
книги / Принципы технологии основного органического и нефтехимического синтеза.-1
.pdfнаправляется вскруббер 4для нейтрализации кислот щелочью. После нейтрали зации этилбензол возвращается в реактор /. Туда же подается этилбензол из ко лонны 10. Газы выводятся из системы. Оксидат из нижней части колонны /, со держащий около 10 % гидропероксида, направляют в ректификационную ко
лонну 3 для концентрирования. Концентрирование гидропероксида проводят при глубоком вакууме. Несмотря на большие затраты энергии, этот процесс луч ше проводить на установке двойной ректификации. При этом на первой колон не отгоняется часть этилбензола при более низком вакууме, а во второй колонне при более глубоком вакууме отгоняется остальная часть этилбензола с примеся ми. Дистиллят этой колонны возвращается в первую колонну, а в кубе получает ся концентрированный (до 90 %) гидропероксид, который направляется на эпоксидирование. Предварительно оксидат охлаждается в теплообменнике 5 исходным этилбензолом. В колонне 3 отгоняется этилбензол с примесями ки слот, поэтому верхний продукт также направляется в скруббер 4. Из куба колон ны 3 сконцентрированный гидропероксид поступает в колонну эпоксидирования 6. (Эпоксидирование можно также проводить в каскаде реакторов.) В ниж нюю часть колонны подается катализаторный раствор из куба колонны 9. Туда же проводится подпитка свежим катализатором. Свежий и возвратный (из ко лонны 7) пропилен также подается в нижнюю часть колонны. Продукты реак ции вместе с катализаторным раствором выводят из верхней части колонны и направляют в ректификационную колонну 7для отгонки пропилена. Газы вы водят из верхней части колонны и из системы для утилизации или сжигания. Ку бовый продукт колонны 7поступает в ректификационную колонну <?для выде ления в качестве дистиллята продуктового оксида пропилена. Кубовая жидкость колонны ^поступает в колонну 9 для отделения продуктов синтеза от катализа-
торного раствора. Катализаторный раствор из куба колонны возвращается в ко лонну эпоксидирования 6, а верхний продукт поступает в ректификационную колонну 10 для отделения этилбензола от метилфенилкарбинола и ацетофено на. Смесь метилфенилкарбинола (МФК) и ацетофенона подается в испаритель 11, в котором с помощью перегретого пара испаряются и отделяются отсмол метилфенилкарбинол и ацетофенон. Смесь паров, перегретая до 300 °С, поступает в реактор 7Jдля дегидратации метилфенилкарбинола. В этом реакторе частично проходит дегидратация. Так как реакция дегидратации является эндотермиче ской, то прежде чем продукты дегидратации поступают в другой реактор (реак тор 15), продукты дегидратации перегреваются в теплообменнике 14.
Конверсия метилфенилкарбинола после двух реакторов достигает 90 %. Продукты дегидратации охлаждаются водой в холодильнике 16 и поступают во флорентийский сосуд 17, в котором органический слой отделяется от водного. Верхний углеводородный слой поступает в ректификационную колонну 18дпя отделения стирола от ацетофенона. Ацетофенон затем гидрируется на отдель ной установке в метилфенилкарбинол, который поступает в отделение дегидра тации.
Селективность процесса по оксиду пропилена составляет 95— 97 %, а выход стирола достигает 90 % по этилбензолу. При этом из 1 тпропиленоксида получа ется 2,6—2,7 т стирола.
Таким образом, рассмотренная технология представляет сложную систему, включающую множество рециклов по этилбензолу, пропилену и катализатору. Эти рециклы приводят, с одной стороны, к увеличению затрат энергии, а с дру гой — позволяют вести процесс в безопасных условиях (при низкой концентра
231
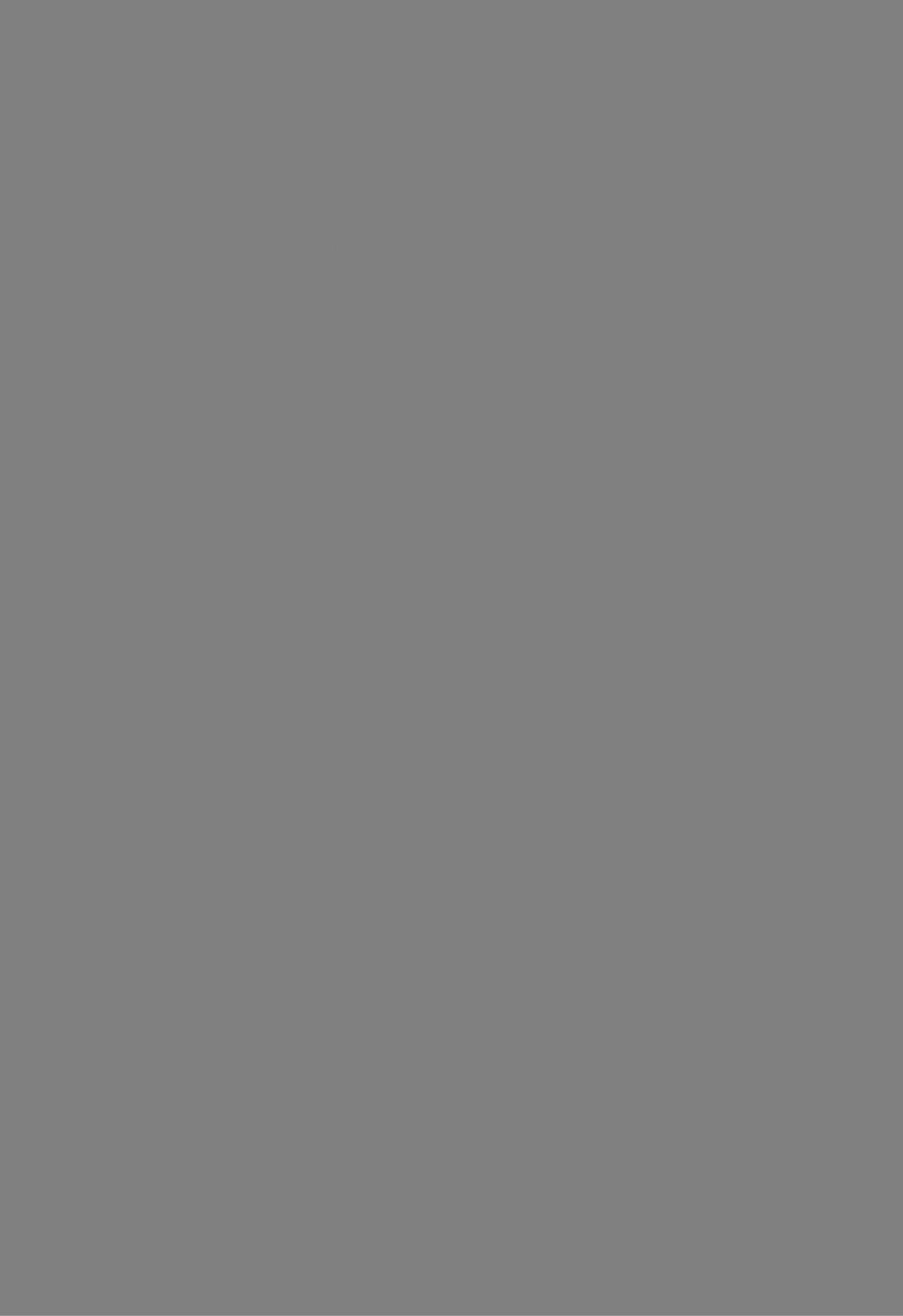
остальных стадий (рецикл по катализаторному раствору стадии эпоксидирования 6— 7— 8 — 9— 6 ; рецикл по возвратному этилбензолу 10— 5— 1) . Данная техно
логия из-за многостадийности требует реализации в полной мере принципа пол
ноты выделения продуктов из реакционной массы, поскольку именно чистые со единения, поступающие на каждую изстадий химического превращения, обеспе чивают высокие показатели процесса в целом. Экзотермичный характер процессов окисления и эпоксидирования дает возможность использовать полу чаемые на этих стадиях энергоресурсы (пар) для процессов разделения и тем са мым обеспечить реализацию принципа полноты использования энергии системы.
В целом разработанное и реализованное в нашей стране технологическое реше ние обладает высокой эффективностью.
8.3. ПРОИЗВОДСТВО ОКСИДОВ ОЛЕФИНОВ ПРЯМЫМ ОКИСЛЕНИЕМ ОЛЕФИНОВ
Оксиды олефинов используют при промышленном производстве поверхно стно-активных веществ, пластификаторов, антифризов и полиуретанов. В про мышленном масштабе освоено производство оксидов этилена и пропилена. На получение оксида этилена в мире расходуется 16—20 % всего производимого этилена. Суммарные мировые мощности в 1995 г. составили около 12 млн т/год. Производство оксида этилена является одним из наиболее динамично разви вающихся. Так, в США в 1992 г. мощности по производству этого продукта со ставили 2800 тыс. т/год, а в 1995 г. — уже 3975 тыс. т/год. В Японии — соответст венно 600 и 880 тыс. т/год.
Структура потребления оксида этилена и этиленгликоля, производимого на его основе, представлена в табл. 8.4.
Исторически первым способом получения оксида этилена был хлоргидринный метод, основанный на гипохлорировании этилена хлорноватистой кисло той в водных растворах хлора:
С12 + Н20 г* НОС1 + HCI
СН2=СН2 + НОС1 -> СН2С1СН2ОН
СН2=СН2 + С12 + Н20 -> СН2С1СН2ОН + НС1
Второй стадией процесса являлось омыление кислых растворов этиленхлоргидрина концентрированными растворами едких щелочей:
СН2С1СН2ОН + 1/2Са(ОН) 2 -» СН2 - СН2 + 1/2СаС12 + Н20
V
Технология позволяла использовать разбавленные этиленсодержащие газо вые смеси, имела простое аппаратурное оформление. Наряду с оксидом этилена в качестве побочного продукта получали 1 ,2 -дихлорэтан:
СН2=СН2 + С12 -> СН2С1- С Н 2С1
Причем его количество 200 кг на 1 т оксида этилена позволяло говорить о со вместном получении двух целевых продуктов в ходе одного технологического процесса.
Т а б л и ц а 8.4. Структура потребления оксида этилена и этиленгликоля
Оксид этилена |
% |
Этиленгликоль |
% |
Моноэтиленгликоль |
58,4 |
Полиэфирные волокна |
55,2 |
Этоксилаты |
17,5 |
Антифризы |
18,1 |
Ди- и триэтиленгликоли |
6,9 |
Упаковочный материал на основе |
|
Этаноланины |
5,6 |
полиэтилентерефталата |
11,0 |
Гликолиевые эфиры |
4,1 |
Полиэфирная пленка |
5,9 |
Полиолы |
2,7 |
Другие |
9,8 |
Полиэтиленгликоли |
1,4 |
|
|
Другие |
3,4 |
|
|
Тем не менее использование этой технологии практически прекращено. Это связано с использованием хлора и едких щелочей, а также с образованием боль шого количества сточных вод, содержащих наряду с растворами солей значи тельное количество хлорорганических соединений (дихлорэтан, хлорекс). Про мышленное значение хлоргидринная технология имеет еще только для получе ния оксида пропилена.
В настоящее время оксиды олефинов производятся в основном рассмотрен ным ранее способом гидроперекисного эпоксидирования, а также прямым окислением этилена. Единственным известным в настоящее время катализато ром прямого окисления олефинов в соответствующие оксиды является актив ное серебро.
Теоретические основы процесса. В качестве катализатора на всех производст вах оксидов олефинов используют серебро с промотирующими и структурооб разующими добавками, нанесенное на пористый корундовый носитель в виде
шариков или колец. Реакция |
|
|
СН2=СН2 + 1/202 |
—> С2Н40 + 121,5 кДж/моль |
(8.6) |
сопровождается полным окислением этилена |
|
|
СН2=СН2 + 3 0 2 -> |
2С 02 + 2Н20 + 1383 кДж/моль. |
(8.7) |
При более высоких температурах проявляется реакция полного окисления оксида этилена
С2Н40 + 2,502 —> 2С 02 + 2Н20 + 1257 кДж/моль.
Значительное число исследований, посвященных выяснению механизма окисления олефинов в оксиды олефинов, к сожалению, до настоящего времени не привело к единому мнению. Один из широко известных механизмов этого процесса предложен М.И. Темкиным и Н.В. Кульковой. В соответствии с ним по мере увеличения адсорбции кислорода на серебре образуется поверхностный оксид — сначала Ag20 , а затем Ag20 2 и менее устойчивый Ag20 3, которые обра
зуют одну поверхностную фазу переменного состава. При этом серебро в этой фазе оказывается одновременно как одновалентным (Ag20), так и трехвалент ным (Ag20 3), т.е. (Ag20 2) или (Ag,Ag,l0 2). Предполагается, что именно этот оксид серебра адсорбированный на поверхности участвует как в реакции (8.6), так и в
реакции (8.7).
234
Исходя из этих представлений предполагается следующий механизм:
Ag2O r +С 2Н4 - |
—>Ag20 MC+С ,Н 40 |
(8.8) |
|||||
Ag20 r + C 2H4 - |
- ^ A g 2OC,H4Ow,c |
(8.9) |
|||||
Ag2O f +С |
2 |
Н |
4 |
- |
- ^ A g C rc +СН СНО |
(8.10 ) |
|
|
|
|
2 |
3 |
Образование продуктов полного окисления происходит за счет окисления ацетальдегида
CH3CHO + 5Ag2O r — ^->2 СО, + 2H |
20 + 5 A g 2CTc |
(8.1 1 ) |
|
AgjO^ 0 + 0 2 - ^ - > A g 20 “c |
|
(8.12) |
|
Ag20 “c +Ag20 “c — »Ag20 “c |
(8.13) |
||
Ag2C 2H40 aj,ct==f=^Ag20 “c +C 2H40 |
(8.14) |
||
Ag20 r + C 2H40 t= ^ = TAg20 2C |
2H40 anc |
(8.15) |
|
Ag20 f c +H 20 t = ^ A g 20 2H |
20 |
MC |
(8.16) |
Ag20 “c + C 0 2 f c ^ A g 20 2C 0 |
“c |
(8.17) |
В данном случае Ag2 0 wc представляет собой промежуточную частицу по
верхностного соединения и соответствует вакантному месту на поверхности ка тализатора.
Стадия (8.10) состоит из нескольких быстрых стадий. Последние четыре ста дии описывают равновесие между продуктами в паровой фазе и адсорбирован ными на поверхности. В адсорбированном состоянии они могут закрывать ката литически активные центры и тормозить целевую реакцию. В соответствии с ме ханизмом реакций (8.8)—(8.17) скорость основной реакции (8.6) описывается
как
w1 |
(8.18) |
Для побочной реакции (8.7):
(8.19)
где
_ кхкх+6АТ2 PC2W4
(1 + ^ 4РС2Н4о) +(1 + ^SPC2H 4O + ^ ьР н 2о + ^ тРсо2)• (8.20)
2*3 Ро>
При низких концентрациях этилена (ниже нижнего предела взрываемости):
w1 |
к\ Рс2н4 |
( 8. 21) |
1 +/:/?с2н4о
Наоборот, при высоких (выше верхнего предела взрываемости) концентра циях этилена:
(£, / L)p0, |
( 8. 22) |
w, --------------- - |
1 + Ki pCiHt0
Таким образом, в зависимости от условий проведения скорость реакции мо жет иметь первый порядок по этилену и нулевой по кислороду [см. выражение (8.2 1 ) | или первый порядок по кислороду и нулевой по этилену [см. выражение
(8.22) 1.
В целом можно говорить о некотором общем виде уравнения, описывающе го скорость реакции окисления этилена:
w=k'Pc!HtPo2 |
/ 0 + * > с 2н4о)> |
(8.23) |
|
где кажущиеся порядки по исходным реагентам составляют от 0 до 1 (по экспе
риментальным данным пх= 0 -г- 0,45, п2 —0,55 + 1).
Значительный вклад в исследование процесса получения оксида этилена на серебряных катализаторах внесли М.И. Темкин, А.К. Аветисов, Б.Б. Чесноков.
Российскими исследователями в НИИ «Синтез» совместно с Институтом катализа СО РАН разработана технология приготовления высокоэффективного катализатора парциального окисления этилена. Как правило, селективность се ребра без добавок не превышает 45—50 %, в то же время она зависит в основном от наличия на поверхности электроотрицательных (хлор, сера, селен) и электро положительных (цезий, рубидий, калий) элементов. При использовании амин ного метода приготовления серебряных катализаторов удалось добиться равно мерного осаждения на поверхность пор носителя мелкодисперсных кристаллов серебра (0 ,8—1,5 тыс. А), содержащих промотирующие и структурообразующие
добавки. Влияние такого рода добавок представлено на рис. 8.11—8.12. Так как селективность существенно зависит от присутствия С1 на поверхно
сти и его постоянного уноса, в ходе эксплуатации катализатора требуется посто янная подпитка исходной смеси микроколичествами хлора. Его источником могут служить дихлорэтан или винилхлорид.
Готовый катализатор содержит 11—13 % массовых серебра и обеспечивает при 2 М Па и объемной скорости 5—7 тыс. ч- 1 ввоздушном (5,0 % С2Н4; 5,5 % 0 2) и кислородном (15,0 %С2Н4;6,5 % 02) высокую селективность (80—82 %) и про изводительность (концентрация С2Н40 на выходе из реактора 1 и 1,5 % об. соот
ветственно). Разработанный катализатор «НПП Оксид-Этокс» выпускается катализаторной фабрикой Казанского АО «Органический синтез». Статистиче ские исследования процесса позволили рекомендовать для его проведения труб чатый реактор. При этом в качестве хладагента целесообразно использовать кипящую под давлением 5,5 МПа воду, что обеспечивает более равномерный те плоотвод по сравнению с использованием высококипящих промежуточных хла дагентов. Рекомендуется использовать трубки диаметром 32 мм с длиной слоя катализатора 6,5—7 м для воздушного и 27 мм и 7,5—8 м для кислородного про цессов. Селективность соответственно составляет 78—80 и 80—81 %. Срок служ бы катализатора составляет обычно от двух до пяти лет.
За рубежом в основном применяют катализаторы фирмы «Shell» с содержа нием серебра 12—15 % (вес). Катализаторы обладают достаточной'стабильно стью. За 4—5 лет их селективность снижается на 7—8 %.
2 3 6
Рис. 8.11. Зависимость селективности катали заторов на носителях различной пористой структуры от содержания цезия (удельная поверхность в м2/г и объем пор в см}/г):
/ - 0 ,0 4 6 и 0,40; 2 - 0 ,0 2 6 и 0,23; J — 0,013 и 0,16
Рис. 8.12. Зависимость скорости реакции и>, и селективности S от температуры для се ребряных катализаторов с добавками Cs и С 1 (/), Cs (2), Cl (3 ) и без промотирующих
добавок (4)
Чрезвычайно важное значение для эффективного проведения процесса име ет температурный режим и степень конверсии этилена. При постоянной степе ни конверсии этилена селективность падает с повышением температуры и сте пени конверсии этилена (рис. 8.13).
Это связано с последовательно-параллельным характером образования про дуктов полного окисления:
СН2 =СН 2 |
+ о , |
|
|
,0, |
эСО, + Н ,0 |
г;, к, |
->СН,СН,02kJ г . к |
||||
|
|
2^ п |
|
|
|
сн2 |
=сн2 |
1 о, |
-»С07+ н ?о |
||
|
|
|
г; |
|
|
Выражение для дифференциальной селективности по оксиду олефина имеет
вид
Г\ + 'з
При допущении о равных порядках скоростей реакций парциального и пол ного окисления получим
кх- к 2Рс2иАо |
\ _ к 2 |
/*с2н4о |
(8.24) |
Рс2НА |
* 3 |
Рс2нА |
|
к. +къ |
I+к^/кх |
|
Отсюда очевидно, что подавление побочной реакции полного окисления за счет изменения концентраций исходных реагентов невозможно. Однако кон центрацией целевого продукта можно эффективно контролировать скорость последовательного полного окисления. Действительно, промышленные про цессы мри получении оксида этилена обеспечивают ее концентрацию в реакци-
237
Температура, С |
Степень конверсии, % |
а |
б |
Рис. 8.13. Зависимость селективности образования оксида этилена от температуры (а) и степени конверсии (б)
онных газах на уровне 0,7—1,5 %, что позволяет практически исключить после довательное окисление.
Подавление параллельной реакции полного окисления возможно при сни жении температуры процесса. Это связано с тем, что энергия активации реак ции полного окисления на 21—24 кДж/моль выше, чем для целевого процесса. Следовательно, при снижении температуры £3Д | уменьшается, а дифференци
альная селективность растет.
Таким образом, в промышленности процесс окисления этилена с получени ем оксида этилена проводят на серебряном катализаторе, промотированном, как правило, хлором, серой, цезием. Окисление ведут в кожухотрубных реакто рах со стационарным слоем катализатора, обеспечивая конверсию этилена за один проход 15—25 % и концентрацию оксида этилена на выходе 0,7—1,5 %. Температура 230—250 °С, давление 0,3—3,5 МПа.
Технология производства оксида этилена парциальным окислением этилена.
Существует два подхода к организации технологического процесса, которые от личаются типом используемого окислителя — воздух или технический кисло род.
Первая установка мощностью 7000 т/год была пущена в США в 1937 г. фир мой «Карбайд энд Карбон». В 1956 г. при создании такого производства фирма Шелл использовала чистый кислород. В настоящее время, несмотря на одновре менное сосуществование обеих технологий, все крупные установки с мощно стью 50—200 тыс. т/год используют в качестве окислителя кислород.
Главные фирмы-разработчики процесса — «Шелл», «Юнион Карбайд», «Сайентифик Дизайн», БАСФ, «Ниипон Секубай», НИИ «Синтез». Несмотря на разнообразие фирм-разработчиков принципиальные технологические схемы процесса практически не отличаются друг от друга.
Рассмотрим технологическую схему получения оксида этилена с использо ванием в качестве окислителя технического кислорода (рис. 8.14).
Свежий этилен, содержащий промотирующую добавку (C2 H4 CI2 ), предвари тельно очищенный от ацетилена (0,001 % об.), сернистых соединений (0,0001 % об.), высших непредельных углеводородов (0 ,1 % об.), смешивается с рецирку
ляционным потоком при давлении 2,0 МПа, затем в парогазовую смесь вводится кислород. Смесь подогревается отходящими реакционными газами в теплооб-
2 3 8
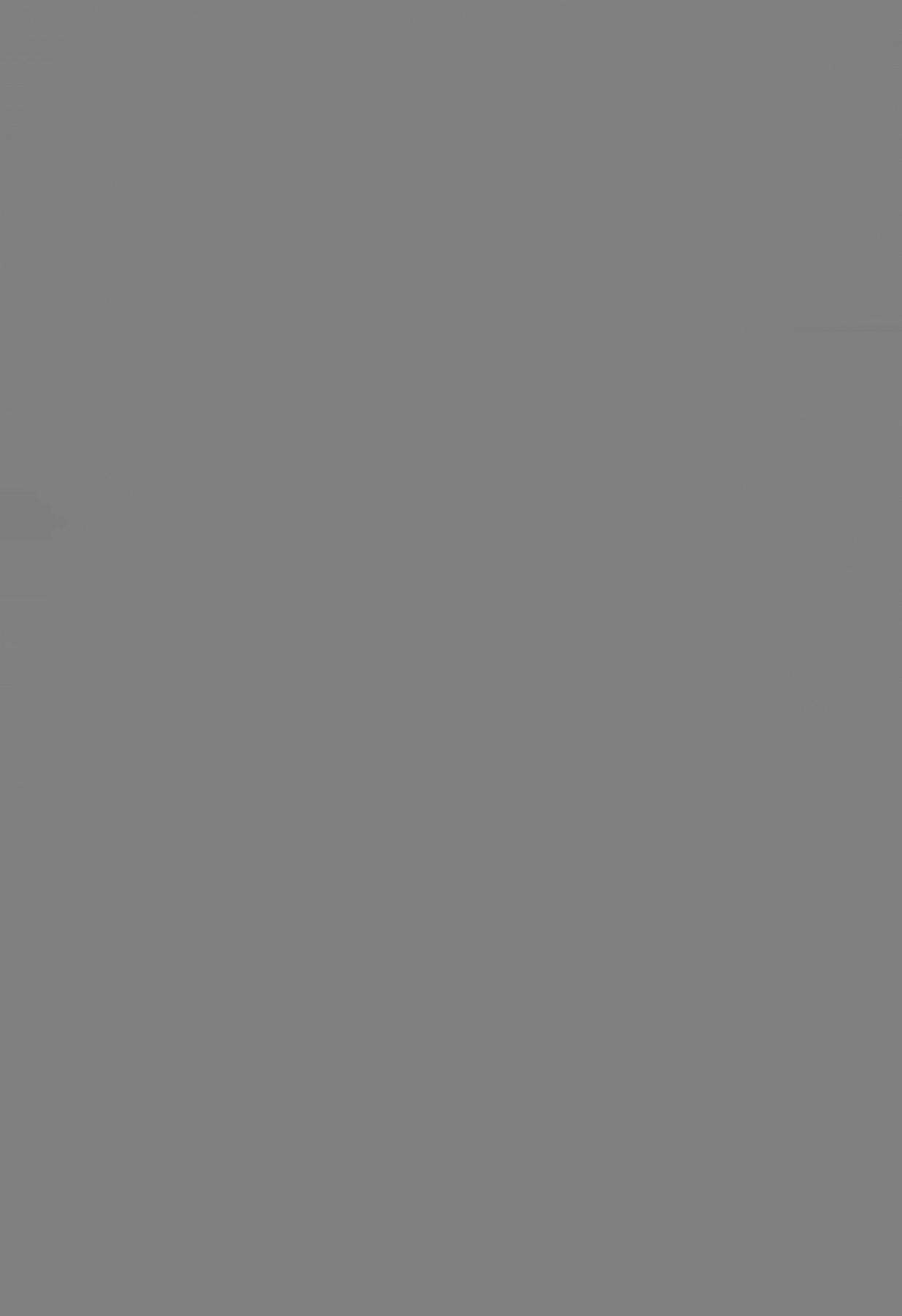
Выходящий из реактора / поток имеет состав, % (об.): этилен — 13—19,5; кислород — 3,5—5,0; оксид этилена — до 1,5; СОг— 10—12; инертные газы (азот, аргон) — 62—72. Реакционные газы охлаждаются исходной смесью в теп лообменнике 2, а затем в водяном холодильнике 4. После этого смесь поступает в абсорбер 6. Так как оксид этилена смешивается с водой влюбых соотношени ях, то в качестве абсорбента используется охлажденная фузельная вода из аппа ратов 9 и П. Раствор оксида этилена из абсорбера бпосле дросселирования на гревается фузельной водой в теплообменнике 2 и поступает в отгонную колонну 9, обогреваемую острым паром. Смесь оксида этилена, углекислого газа и не большого количества паров воды поступает на ректификацию в колонну 10. Трудность разделения низкокипящих СОг и оксида этилена, а также лабиль ность оксида этилена приводит к тому, что эффективность колонны 10не может быть большой. Поэтому в ней осуществляется фракционирование этой смеси. Дистиллят колонны обогащен углекислым газом, но в нем присутствует и неко торое количество оксида этилена. Кубовый продукт — высококонцентрирован ный раствор оксида этилена в воде (с продуктами окисления) поступает на рек тификацию в колонну 12, где в качестве дистиллята выделяют товарную окись этилена. Кубовый продукт колонны 12 представляет собой фузельную воду, за грязненную смолообразующими продуктами, и отводится на очистку.
Парогазовый поток из верха абсорбера 6 направляется на карбонатную очи стку от СО2 в абсорбер 7. При этом протекает реакция
К2С 0 3 + С 0 2 + Н20 2КНС03
и углекислый газ связывается в гидрокарбонат. Раствор гидрокарбоната подог ревается втеплообменнике и направляется на десорбцию в аппарат 8. Для более эффективной десорбции, как правило, снижают давление до 2—3 атм. Раствор карбоната калия из куба десорбера охлаждают и возвращают насосом (не пока зан) на стадию абсорбции в аппарат 7.
Таким образом, рассмотренная технология обеспечивает постоянство со держания инертных примесей в циркулирующем газе в основном за счет очист ки его от СО2. Практически разница в составах выходящего из реактора парога
зового потока и потока из верхней части абсорбера 7обусловлена отсутствием в нем оксида олефина и снижением концентрации СО2 приблизительно в2 раза.
Существующая технология может быть несколько модифицирована с целью повышения ее эффективности. Во-первых, это относится к замене охлаждения реактора /дифенильной смесью на кипящую воду, что, как показано в работах НИИ «Синтез», существенно снижает вероятность местного перегрева и тепло вого срыва реактора. Во-вторых, целесообразно использовать в колонне 12 обогрев не острым паром, а глухим паром в циркуляционных кипятильниках, что позволит снизить количество отходящих сточных вод.
Более старая технология окисления этилена воздухом не позволяет достичь той же эффективности, что кислородный процесс, и обеспечивает общий выход оксида этилена 60 % по этилену при средней селективности 65 % и суммарной конверсии этилена 90 %. В отличие от кислородного варианта, где необходимые концентрации реагентов поддерживаются в основном за счет хемосорбции СО2
и циркулирующих газов, большое количество инертов, поступающих с воздухом на стадию окисления, делает этот прием экономически неэффективным. Про стая сдувка при одностадийном окислении приводит к значительным потерям этилена, а если отводить эту смесь на разделение — к большим энергозатратам
240