
9562
.pdf
ет гипотезе плоских сечений ( гипотезе Бернулли) , после интегрирования получаем:
σ = N / A,
где A − площадь поперечного сечения стержня.
В сечениях, близких к месту приложения внешних сил, гипотеза Бернулли на-
рушается: сечения искривляются, и напряжения в них распределяются неравномерно.
По мере удаления от сечений, в которых приложены силы, напряжения выравниваются,
и в сечениях, удаленных от места приложения сил на расстояние, равное наибольшему из размеров поперечного сечения, напряжения можно считать распределенными по се-
чению равномерно. Это положение, называемое принципом СенВенана, позво-
ляет при определении напряжений в сечениях, достаточно удаленных от мест приложе-
ния внешних сил, не учитывать способ их приложения, заменять систему внешних сил статически эквивалентной системой.
Рис. 35
Высказанное предположение о равномерном распределении нормальных напря-
жений в поперечном сечении справедливо для участков, достаточно удаленных от мест:
резкого изменения площади поперечного сечения (рис. 35в); скачкообразного измене-
ния внешних нагрузок; скачкообразного изменения физико-механических характери-
стик конструкций.
Нормальные напряжения при сжатии определяют так же, как и при растяжении,
но считают отрицательными.
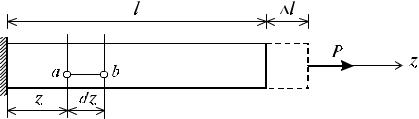
В инженерных сооружениях встречаются растянутые или сжатые элементы,
имеющие отверстия. В сечениях с отверстием определяют осредненные нормальные напряжения по формуле:
σ = N / Aнт,
где Ант − площадь поперечного сечения нетто с учетом ослабления.
2. Деформации и перемещения. Закон Гука
Рассмотрим однородный стержень с одним концом, жестко заделанным, и дру-
гим - свободным, к которому приложена центральная продольная сила Р (рис. 2). До нагружения стержня его длина равнялась l - после нагружения она увеличилась на Δℓ
(рис. 36). Величину Δℓ называют абсолютной продольной деформацией (абсолют-
ным удлинением) стержня. В большинстве случаев оно мало по сравнению с его первоначальной длиной l (∆l<<l).
Рис. 36
Если в нагруженном стержне напряженное состояние является однородным, т.е.
все участки стержня находятся в одинаковых условиях, деформация остается одной и той же по длине стержня и равной
ε = Δℓ / ℓ
Величина ε называется относительной продольной деформацией.
Если же по длине стержня возникает неоднородное напряженное состояние, то для определения его абсолютного удлинения необходимо рассмотреть бесконечно ма-
лый элемент длиной dz (рис. 36). При растяжении он увеличит свою длину на величину dz и его относительная деформация составит:
ε = dz / dz

В пределах малых деформаций при простом растяжении или сжатии закон Гука
записывается в следующем виде (нормальные напряжения в поперечном сечении
прямо пропорциональны относительной линейной продольной деформации ):
σ = Е ε,
Величина Е представляет собой коэффициент пропорциональности, называемый
модулем упругости материала первого рода (модуль продольной упругости). Его ве-
личина постоянна для каждого материала. Он характеризует жесткость материала, т.е.
способность сопротивляться деформированию под действием внешней нагрузки, опре-
деляется экспериментальными исследованиями материала конструкции.
В поперечных направлениях стержень деформируется, возникают поперечные дефор-
мации ε’ . Отношение относительной поперечной деформации ε' к относительной про-
дольной деформации ε, взятое по модулю, есть для каждого материала величина посто-
янная и называется коэффициентом Пуассона:
g = ee¢ .
3. Деформации участков стержня и перемещения сечений. Условие жесткости
Из формул следует:
DL = |
N |
. |
|
||
L |
A × E |
Отсюда получим формулу для определения абсолютного удлинения (или укорочения)
участка стержня длинойL :
DL = N × L .
E × A
В формуле произведение Е×А называется жесткостью бруса при растяжении или сжатии, которая измеряется в кН, или в МН.
По этой формуле определяется абсолютная деформация L , если на участке продоль-
ная сила постоянна. В случае, когда на участке продольная сила переменна, она опре-
деляется по формуле:
L
DL = ∫ N(x)dxE × A ,
0
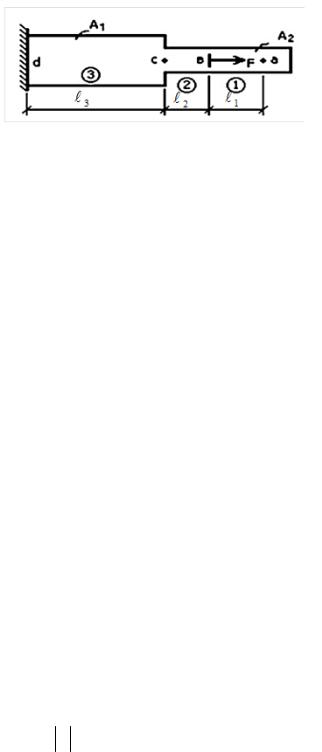
где N(х) – функция продольной силы по длине участка.
Определим горизонтальное перемещение точки а оси бруса (рис. 37) – u a: оно равно абсолютной деформации части бруса аd, заключенной между заделкой и сечени-
ем, проведенным через точку, т.е. ua = Lad.
Рис. 37
В свою очередь удлинение участка аd состоит из удлинений отдельных грузо-
вых участков 1, 2 и 3:
Lad = L1 +ΔL2 +ΔL3 .
Продольные силы на рассматриваемых участках: N2 = N3 = F.
L1 = 0; |
DL2 |
= |
F ×L2 |
; |
|
DL3 |
= |
F ×L3 |
. |
||||
|
|
||||||||||||
|
|
|
|
|
E × A2 |
|
|
E × A3 |
|||||
Тогда ua |
= DLad |
= |
F ×L2 |
+ |
F ×L3 |
. |
|
|
|
|
|||
E × A2 |
|
|
|
|
|
||||||||
|
|
|
|
|
|
E × A3 |
|
|
|
|
Аналогично можно определить перемещение любого сечения бруса и сформу-
лировать следующее правило:
перемещение любого сечения j стержня при растяжении– сжатии определяется как сумма абсолютных деформаций n грузовых участков, заключенных между рас-
сматриваемым и неподвижным (закрепленным) сечениями, т.е.
i =n
u j = ∑ L i .
i =0
Условие жесткости бруса запишется в следующем виде:
u max ≤[u],
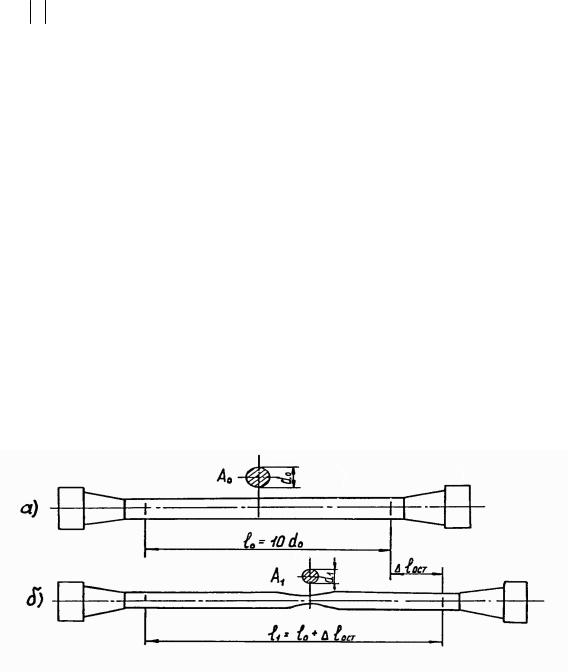
где u max – наибольшее значение перемещения сечения, взятое по модулю из эпюры перемещений; [u] – допускаемое значение перемещения сечения для данной конструк-
ции или ее элемента, устанавливаемое в нормах.
4. Физико-механические свойства металлов
Испытания образцов на растяжение проводятся с целью экспериментального оп-
ределения механических характеристик материалов . Наиболее распространенными в настоящее время являются испытания цилиндрических и плоских образцов в условиях одноосного растяжения.
Широкому применению этого вида испытаний способствует относительная простота их осуществления, так как имеется большой парк разрывных и универсальных испытательных машин (например, УММ-20 или МИ-40КУ). Испытание на растяжение заключается в плавном деформировании закрепленного в захватах испытательной ма-
шины образца из исследуемого материала до наступления его разрушения. При этом специальные приборы фиксируют зависимость абсолютного удлинения образца от прикладываемой к нему продольной растягивающей нагрузки.
В процессе испытаний измеряются сила, действующая на образец, и удлинение его расчетного участка. Результатом испытаний является графическая диаграмма
растяжения.
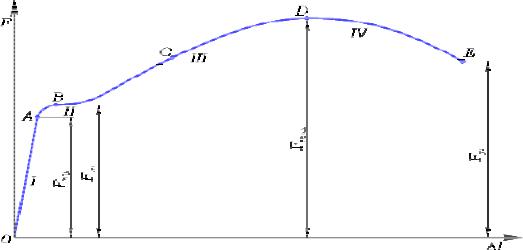
Рис.38. Диаграмма растяжения образца из малоуглеродистой стали
Как видно из рисунка, диаграмма имеет четыре характерных участка:
I - участок пропорциональности;
II - участок текучести;
III - участок самоупрочнения;
IV - участок разрушения.
Рассмотрим подробнее процесс построения диаграммы (рис. 38).
В самом начале испытания на растяжение, растягивающая сила F, а следова-
тельно, и деформация l стержня равны нулю, поэтому диаграмма начинается из точки пересечения соответствующих осей (точка О).
На участке I до точки A диаграмма вычерчивается в виде прямой линии. Это го-
ворит о том, что на данном отрезке диаграммы, деформации стержня l растут пропор-
ционально увеличивающейся нагрузке F. На этом участке выполняется закон Гука – математическая линейная зависимость между напряжениями и деформациями: ε Е = σ,
где Е – модуль упругости (Юнга) равный тангенсу угла наклона прямого участка диа-
граммы к оси абсцисс.
После прохождения точки А диаграмма резко меняет свое направление и на уча-
стке II начинающемся в точке B линия какое-то время идет практически параллельно оси l, то есть деформации стержня увеличиваются при практически одном и том же значении нагрузки. Этот участок диаграммы называется площадкой текучести. В этот момент в металле образца начинают происходить необратимые изменения. Перестраи-
вается кристаллическая решетка металла. При этом наблюдается эффект его самоуп-
рочнения.

После повышения прочности материала образца, диаграмма снова "идет вверх" (участок III) и в точке D растягивающее усилие достигает максимального значения. В
этот момент в рабочей части испытуемого образца появляется локальное утоньшение,
так называемая "шейка", вызванное нарушениями структуры материала (образованием пустот, микротрещин и т.д.).
Рис.39. Стальной образец с "шейкой"
Вследствие утоньшения, и следовательно, уменьшения площади поперечного сечения образца, растягивающее усилие необходимое для его растяжения уменьшается,
и кривая диаграммы "идет вниз".
В точке E происходит разрыв образца. Разрывается образец в сечении, где была образо-
вана "шейка"
По диаграмме также можно определить величину упругих и остаточных деформаций в любой момент процесса испытания.
Для получения непосредственно механических характеристик металла образца диаграмму растяжения необходимо преобразовать в диаграмму напряжений.
Пределом пропорциональности σпц, называется максимальное напряжение, при кото-
ром выполняется закон Гука. При достижении нагрузкой некоторой величины в образ-
це появляются остаточные деформации.
Пределом упругости σупр называют максимальное напряжение, при котором не возникают остаточные деформации. Принято считать за максимальное то напряже-
ние, при котором в испытуемом образце появляются деформации 0,05%.
Предел пропорциональности, предел упругости, модуль упругости и коэффициент поперечной деформации характеризуют упругие свойства материала.
Предел текучести материала σт – наименьшее напряжение, при котором деформа-
ция увеличивается без заметного увеличения нагрузки. Если после возникновения те-
кучести продолжать увеличивать действие нагрузки, наступает разрушение.
Пределом прочности (временным сопротивлением) σв называют напряжение,
соответствующее максимальной нагрузке, предшествующей разрушению образца. При отсутствии площадки текучести (что характерно для диаграмм растяжения большинст-
ва материалов, после предварительной пластической деформации) определяют услов-
ный предел текучести 0,2σв называется технический предел прочности. Условным пределом текучести напряжение, при котором остаточная (пластическая) деформация составляет 0,2 %. Условный предел текучести определяется аналогично пределу упру-
гости.
Еще одна важная характеристика материала – это оценка интенсивности де-
формации εи, где применяют такие понятия как: относительная продольная деформа-
ции εпр, приходящиеся на единицу длины или ε′ относительная поперечная, приходя-
щаяся на единицу параметра сечения (высота, ширина). Продольная и поперечная де-
формации связаны соотношением (закон Пуассона) μ = ε′/εпр, где μ – коэффициент Пуассона – постоянная материала в пределах упругости.
Таким образом, испытания на растяжение стального образца дают возможность определить самые важные механические параметры материала необходимые для созда-
ния прочных и надежных конструкций: модуль упругости и коэффициент Пуассона.
5. Метод расчета конструкций по допускаемым напряжениям
Метод допускаемых напряжений. Этот метод расчета строительных конструк-
ций и их элементов основан на предположении, что критерием надежности конструк-
ции будет выполнение следующего условия прочности:
σmax ≤ [σ] ,
где σmax – наибольшее напряжение, возникающее в одной из точек опасного сечения и определяемое расчетом; [σ] – допускаемое (предельное) для данного материала напря-
жение, полученное на основании экспериментальных исследований.
Допускаемое напряжение определяется по формуле:
[σ] = σ0 , n
где σ0 – опасное напряжение; n – коэффициент запаса прочности.

Для пластичных материалов за опасное напряжение σ0 принимается предел те-
кучести σт ; для хрупких материалов – временное сопротивление (предел прочности) σв.
Значение коэффициента запаса прочности, а следовательно, и допускаемого напряжения зависит от многих факторов. Основными факторами, которые влияют на выбор его значения, являются:
1)соответствие механических свойств материала конструкции и отдельно испытанных образцов;
2)учет конкретных условий работы рассчитываемой конструкции;
3)метод определения напряжений (степень точности этого метода);
4)неточность задания внешней нагрузки;
5)долговечность и значимость проектируемого сооружения или машины.
Значения допускаемых напряжений или коэффициентов запаса прочности уста-
навливаются техническими условиями и нормами проектирования. Для строительных сталей значение коэффициента запаса прочности принимается n = 1,4÷1,6; для хрупких материалов n = 2,5÷3,5; для древесины n = 3,5÷6.
6. Расчеты на прочность при центральном растяжении– сжатии
При центральном растяжении-сжатии нормальные напряжения в поперечных сечениях, достаточно удаленных от места приложения сил, постоянны (принцип Сен-
Венана) и определяются по формуле:
σ= N , A
где σ – нормальное напряжение; А – " чистая" площадь поперечного сечения бруса по-
сле вычета возможных ослаблений сечения отверстиями, т.е. А = Аnetto.
Если площадь поперечного сечения бруса постоянна по длине, то условие проч-
ности для пластичного материала имеет вид:
N ≤ A · [σ] или |max σ| = |max N| / A ≤ [σ],
где |max N| – наибольшее значение продольной силы по абсолютной величине берется из эпюры N (сечение, где имеется |max N|, является опасным); [σ] – расчетное сопро-
тивление материала по пределу текучести.
Если брус выполнен из хрупкого материала, т.е. когда расчетные сопротивления на растяжение и сжатие различны [σ]с ≠ [σ]р , то условие прочности имеет следующий вид:
max σр = max Nр / А ≤ [σ]р
|max σс| = |max Nс| / А ≤ [σ]с
где maxNр – наибольшая растягивающая продольная сила (на эпюре N имеет знак
"плюс");
|max Nс| – наибольшая по абсолютной величине сжимающая продольная сила (на эпю-
ре N имеет знак "минус"); [σ]с, [σ]р – расчетные сопротивления материала на сжатие и растяжение по пределу прочности.
Используя условия прочности (6.2) или (6.3), можно решать задачи трех типов: 1-й тип – проверочная задача. Используя все заданные величины и эпюру N, по форму-
лам (6.2) и (6.3) можно проверить прочность бруса. 2-й тип – проектная задача, т.е. подбор сечения бруса.
Приняв |max σ| = [σ], определяем требуемую для этого величину площади Атр
поперечного сечения из формулы:
Атр = |max N| / [σ]
Зная эту площадь, можно определить конкретные размеры сечения заданной фор-
мы.
Для хрупкого материала из формул требуемую площадь сечения находим отдельно:
для растянутой зоны – Ар = |max Nр| / [σ]р
и сжатой зоны – Ас = |max Nс| / [σ]с .
Из полученных значений площадей выбираем большую.
3-й тип – определение несущей способности стержня или определение допускаемой продольной силы.
Приняв |max σ| = [σ] определяем величину наибольшей допускаемой продольной
силы:
– для пластичного материала
[N] = [σ] · A
– для хрупкого материала
[N]р = [σ]р · A