
Химическая технология неорганических веществ
..pdfтвора приводит при нагревании к кристаллизации твердого гидрокарбоната, который образует на поверхностях теплообмена инкрустации в виде слоя Na2CO3, обладающего низкой теплопроводностью и резко ухудшающего процесс теплопередачи.
Для предотвращения инкрустаций во вращающихся содовых печах процесс кальцинации проводят с использованием ретурного либо безретурного способа.
При ретурном способе перед подачей в печь влажный гидрокарбонат натрия смешивают с нагретым карбонатом натрия (готовым продуктом – ретуром) в таком соотношении, чтобы вся свободная вода была связана химически с образованием троны по реакции
NaHCO3 + Na2CO3 + 2H2O = |
|
= NaHCO3 Na2CO3 2H2O + 21,9 кДж. |
(3.13) |
Образование новой твердой фазы – троны – предотвращает налипание твердых продуктов на стенки теплопередающих поверхностей. В дальнейшем при нагревании смеси гидрокарбоната натрия и троны происходит их разложение.
Количество ретурной соды определяют из соотношения
R = Wг/Wсм – 1,
где R – расход ретурной соды, кг/кг;
Wг – влажность гидрокарбоната натрия, %;
Wсм – приведенная влажность смеси, %.
При безретурном способе кальцинации вращающаяся содовая печь снабжается специальным устройством для забрасывания влажного гидрокарбоната натрия на слой горячего твердого материала, находящегося в печи на расстоянии 6–8 м от загрузочного конца печи.
Для кальцинации используют два типа вращающихся печей: содовые печи с огневым наружным обогревом топочными газами и паровые кальцинаторы с обогревом паром высоких параметров.
Технологическая схема отделения кальцинации, работающего по ретурной схеме и снабженного паровыми кальцинаторами, представлена на рис. 25.
91
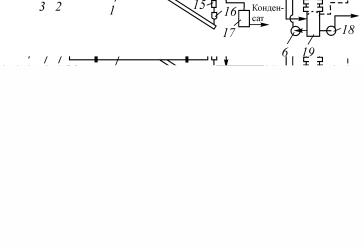
Рис. 25. Технологическая схема отделения кальцинации: 1 – паровой кальцинатор; 2 – питающий смеситель; 3, 15 – ячейковые питатели; 4, 8, 9, 10, 14, 16 – транспортеры; 5 – вибропитатель; 6 – бункер; 7 – сбрасыватель; 11 – циклон; 12 – коллектор газа; 13 – сепаратор; 17 – сборник конденсата; 18 – центробежные насосы; 19 – сборник; 20 – холодильник газа дистилляции; 21 – редукционная охладительная установка; 22 – промыватель газакальцинации; 23 – сборник
Влажный гидрокарбонат натрия с помощью ленточного транспортера 10 подается в бункер 6 вибропитателя 5 и затем транспортером 4 через ячейковый питатель 3 направляется в смеситель 2. Сюда же подается ретурная сода с транспортера 8 и сода, выделяемая из газов в циклоне 11. Из питающего смесителя масса поступает в паровой кальцинатор 1. Из парового кальцинатора сода выгружается через ячейковый питатель 15 и затем с помощью системы транспортеров 16, 8, 9 и 14 направляется на склад.
Газы, выходящие из содовой печи, проходят сухую очистку от воды в циклоне 11 и затем мокрую очистку в коллекторе газа, в который насосом 18 из сборника 19 качается слабая жидкость. Жидкая фаза отделяется от газа в сепараторе 13 и возвращается в сборник 19.
Газовая фаза поступает в верхнюю часть холодильника газа дистилляции 20, из нижней части которого газ направляется в промыва-
92
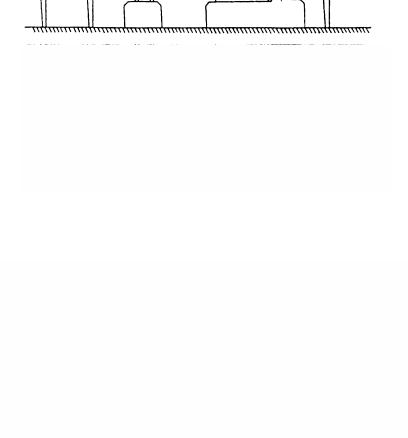
тель газа содовых печей 22, орошаемый промывной жидкостью из сборника 23. Слабая жидкость из сборника 19 насосом 18 перекачивается на малую дистилляцию. Промытый газ содовых печей идет на смешение с газом известковых печей, на компримирование и далее на карбонизацию.
Основное оборудование отделения кальцинации представлено на рис. 26 и 27.
Рис. 26. Содовая печь: 1 – топка; 2 – барабан печи; 3 – горелка; 4 – стальные ролики; 5 – подшипники; 6 – загрузочная камера; 7 – забрасыватель; 8 – ободы; 9 – опорные бандажи; 10 – коническая царга; 11 – цепь; 12 – венцовая шестерня; 13 – горловина; 14 – выгрузной шнек
Рис. 27. Паровой кальцинатор: 1 – смеситель; 2 – торцевое уплотнение; 3 – барабан; 4 – венцовая шестерня; 5 – обод; 6 – теплоизоляция; 7 – оребренные греющие трубы; 8 – трубная решетка; 9 – кольцевая камера; 10 – выгрузная камера
93
Безретурная огневая содовая печь (см. рис. 27) имеет цилиндрический стальной барабан 2, помещенный в топку 1 и снабженный на загрузочном и выгрузном концах цилиндро-коническими горловинами. Загрузочная камера 6 снабжена забрасывателем 7 и штуцером выхода газа. В выгрузной части размещается шнек 14. На цилиндрических частях горловин крепятся опорные бандажи 9 и венцовая шестерня 12. Барабан печи бандажами располагается на роликовых опорах 4. Привод барабана во вращение осуществляется от электродвигателя через редуктор и венцовую шестерню.
Уплотнение с неподвижной загрузочной камерой – сальниковое, с выгрузной частью – торцевое.
В табл. 15 представлены характеристики применяемых содовых
печей.
Таблица 15
Характеристики применяемых содовых печей
Показатель |
Печи с огневым нагревом |
Паровые |
|||
безретурная |
ретурная |
кальцинаторы |
|||
|
|||||
Тип смесителя |
– |
двух- |
одно- |
двух- |
|
|
|
вальный |
вальный |
вальный |
|
Производительность, |
|
|
|
|
|
т/сут |
150 |
150 |
300 |
600 |
|
Диаметр барабана, м |
2,5 |
2,65 |
2,6 |
3,0 |
|
Длина барабана, м |
24 |
27 |
20 |
30 |
|
Поверхность теплооб- |
|
|
|
|
|
мена, м2 |
173 |
177 |
1280 |
2780 |
|
Расход топлива или па- |
|
|
|
|
|
ра, т/т |
122 |
112 |
1,7 |
1,54 |
|
Частота вращения, |
|
|
|
|
|
об/мин |
4 |
5 |
7 |
7 |
|
Температура соды на |
|
|
|
|
|
выходе, °С |
160 |
150 |
200 |
200 |
|
Мощность привода, |
|
|
|
|
|
кВт |
75 |
95 |
75 |
132 |
|
|
94 |
|
|
|
Внутри стального цилиндрического барабана 3 размещены три ряда оребренных греющих труб 7, закрепленных в трубных решетках 8. Трубные решетки с помощью фланцевых соединений крепятся к барабану печи. Барабан снабжен закрепленными на нем бандажами 5 и венцовой шестерней 4. С концов барабана с помощью торцевых уплотнений 2 присоединены смеситель 1, кольцевая 9 и выгрузная 10 камеры. Наружная стенка барабана снабжается теплоизоляцией 6.
Отделение обжига известняка
Назначение отделения обжига известняка в производстве соды заключается в получении диоксида углерода и извести. В дальнейшем диоксид углерода используется для карбонизации аммонизированного рассола, а из извести в процессе гашения водой получают известковую суспензию, которую применяют для регенерации аммиака из фильтровой жидкости в отделении дистилляции. В результате обжига известняка в шахтных известково-обжигательных печах образуется газ, содержащий 40–42 % СО2 и известь, содержащая 80 % свободного оксида кальция.
Теоретические основы процесса обжига известняка. Разложе-
ние карбоната кальция при обжиге осуществляется по эндотермической реакции
СаСО3 = СаО + СО2 – 178 кДж. |
(3.14) |
Для того чтобы сместить равновесие реакции в сторону конечных продуктов, необходимо увеличение температуры. Как показывают расчеты, равновесное давление диоксида углерода над карбонатом кальция становится равным парциальному давлению СО2 в газе печи обжига при температуре 80 °С. Поэтому при температуре, которая поддерживается в печи обжига равной 1100–1200 °С, равновесие реакции полностью смещено в правую сторону.
Скорость процесса разложения известняка зависит в основном от температуры. Так как обжигу подвергают куски известняка размерами от 40 до 120 мм, а подвод необходимого для процесса тепла осуществляется за счет горения кокса, находящегося в шихте, в печи
95
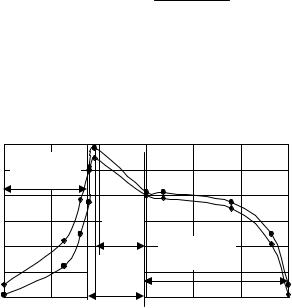
всегда существует разница между температурой газа и твердого материала. Решающее влияние на скорость разложения известняка оказывает скорость продвижения зоны высоких температур к центру кусков известняка. Это, в свою очередь, определяется скоростью процесса теплопередачи.
Уравнение кинетики, которое описывает процесс термического разложения твердого вещества, когда он лимитируется подводом тепла, имеет следующий вид:
1−(1−α)2 / 3 −2 / 3α = 2(Т∆гН−ТRт2) λ τ,
где α – степень разложения; Тг – температура газовой фазы; Тт – температура твердого вещества; λ – коэффициент теплопередачи; ∆Н – энтальпия разложения; R – начальный эффективный радиус твердых частиц. Изменение температуры газовой фазы и твердого материала по высоте слоя в шахтной печи представлено на рис. 28.
|
1200 |
|
|
|
|
|
|
|
1000 |
Зона охлаж- |
|
|
|
|
|
|
|
дения |
|
|
|
|
|
|
800 |
|
|
|
|
|
|
°С |
600 |
|
Зона |
|
|
|
|
|
разло- |
|
|
|
|
||
, |
|
|
|
|
|
||
|
|
|
|
|
|
||
Т |
|
|
|
|
|
|
|
|
|
жения |
|
Зона нагрева- |
|
|
|
|
400 |
|
|
|
|
||
|
200 |
|
Зона |
|
ния шихты |
|
|
|
|
|
|
|
|
||
|
|
горения |
|
|
|
|
|
|
|
|
|
|
|
|
|
|
0 |
|
|
|
|
|
|
|
0 |
4 |
8 |
12 |
16 |
20 |
24 |
h, м
Рис. 28. Изменение температуры T, °С газа (круглые точки) и материала (квадратные точки) по высоте слоя h, м
Как видно из рис. 28, температура газовой фазы по мере прохождения её через слой твердого материала возрастает сначала за счет теплообмена с горячим твердым материалом, затем она резко повы-
96
шается в зоне горения кокса и, наконец, понижается за счет отдачи тепла более холодной шихте в верхней части печи. Твердый материал, двигаясь в противоположном движению газа направлении, нагревается сначала за счет теплообмена с горячими газами, а затем за счет тепла, которое выделяется в зоне горения кокса. Большая часть тепла при этом затрачивается на разложение карбоната кальция. После выхода из зон разложения и горения твердый материал охлаждается в нижней части печи встречным потоком более холодного воздуха.
Для обеспечения оптимального режима обжига необходимо, чтобы верхние границы зон горения кокса и обжига совпадали. Это обеспечивается выбором оптимального размера кусков кокса и равномерностью его распределения в шихте.
В случае смещения зоны горения вверх (слишком мелкий кокс, повышенная влажность известняка) повышается температура выходящих из печи газов, увеличивается количество тепла, уносимого газами. Вследствие нарушения общего баланса тепла печи уменьшается количество тепла, затрачиваемого на разложение, снижаются степень разложения и концентрация диоксида углерода в газе.
При смещении зоны горения кокса вниз возрастает температура выгружаемой извести. Это также приводит к снижению степени разложения карбоната кальция и уменьшению концентрации диоксида углерода в обжиговом газе.
Значительное смещение границы зоны горения вверх может привести к проскоку кислорода, слишком большое смещение этой границы вниз – к появлению в извести несгоревшего кокса.
Для процесса обжига большое значение имеет соотношение между размерами кусков кокса и известняка. Как установлено экспериментально, это соотношение должно быть в пределах от 1:1 до 1:2.
Чаще всего используемый для обжига известняка кокс имеет размеры кусков 30–80 мм, а известняк – 40–120 мм.
В используемом для обжига известняке ограничивается содержание примесей. Наиболее вредными для обжига примесями
97
являются оксиды железа и алюминия и сульфат кальция. Именно примеси Fe2O3 и Al2O3 в процессе обжига могут привести к образованию легкоплавких соединений с оксидом кальция.
Сульфат кальция и оксид магния, который образуется при наличии в сырье карбоната магния, понижают температуру образования жидкой фазы. Появление в процессе обжига расплава снижает скорость разложения карбоната кальция, усиливает взаимодействие шихты с футеровкой печи и может привести к образованию крупных спеков («козлов»).
Примесь оксида кремния в известняке оказывает меньшее, но также отрицательное влияние вследствие связывания части извести в реактивное состояние. Суммарное содержание примесей в известняке не должно превышать 2–3 %.
Технологическая схема и оборудование процесса обжига из-
вестняка. На предприятиях, производящих соду, как правило, имеется цех обжига известняка, состоящий из отделений шихтоподготовки, обжига и гашения извести.
Отделение шихтоподготовки оснащается системой ленточных конвейеров для транспортировки кокса и известняка, бункерами, питателями и электровесами, ленточным конвейером для транспортировки шихты в ковши скипового подъемника.
Отделение обжига включает в себя обжиговые печи, скиповые подъемники для подачи шихты в приемную воронку загрузочного устройства печи, конвейер для транспортирования извести, дутьевые вентиляторы для подачи воздуха. Для очистки обжигового газа используют систему, состоящую из трубы Вентури, циклонакаплеуловителя и электрофильтра.
Отделение гашения извести состоит из гасителя извести барабанного типа, системы вибрационных сит для отделения мелких и крупных твердых отходов гашения от слабой и крепкой известковой суспензии. Слабая известковая суспензия возвращается в гаситель. Мелкие отходы гашения промываются водой и одновременно измельчаются в шаровой мельнице и после смешения с частью дистиллерной жидкости удаляются в шламохранилище. Крепкая извест-
98
ковая суспензия с концентрацией 190–220 н.д. активного СаО подается на дистилляцию.
На современных содовых заводах используют шахтные печи производительностью 450 т/сут (в пересчете на известь, содержащую 85 % СаО) с диаметром цилиндрической части 6,2 м. Цилиндрическое сечение шахты печи в зоне охлаждения извести постепенно переходит в квадратное. Общая высота печи 27 м, полезная – 24 м. Степень обжига – 90 %, расход условного топлива (на 1 т извести, содержащей 85 % СаО) – 139 кг, 100%-ного известняка – 1744 кг. Печь футеруется огнеупорным шамотным кирпичом.
Загрузочное устройство печи двухклапанное с поворотным лотком и отбойниками. Выгрузочное устройство представляет собой четырехсекционный валковый выгружатель. Под выгружателем устанавливается бункер, снабженный трехкамерным шлюзовым затвором. Воздух, используемый при обжиге, подается по двум трубопроводам в бункер разгрузочного устройства. Процесс загрузки шихты
ивыгрузки извести автоматизирован.
3.3.4.Направления совершенствования технологии кальцинированной соды аммиачным методом
Переработка вторичных минеральных ресурсов
Основным вторичным минеральным ресурсом производства кальцинированной соды является дистиллерная жидкость (ДЖ), со-
держащая 10–14 % СаСl2 и 5–7 % NaCl.
Возможны два направления использования дистиллерной жидкости: переработка ДЖ с получением хлорида кальция и использование ее для закачки в нефтяные скважины.
Разработана технология получения хлорида кальция из дистиллерной жидкости. Она включает две ступени трехкорпусной прямоточной выпарки. На выпарку направляется осветленная дистиллерная жидкость. На стадии осветления получают шлам, который направляется на производство известкового мелиоранта. После первой ступени выпарки получают 18%-ный раствор СаСl2. Упаренный раствор после
99
осветления поступает на вторую ступень выпарки, где раствор концентрируется до 38 % CaCl2. При этом в твердую фазу выделяется основная масса NaCl. После сгущения в отстойнике суспензия NaCl поступает в центрифугу. Твердый хлорид натрия может отправляться потребителям либо возвращается на производство соды.
Осветленный 38%-ный раствор хлорида кальция подается в ва- куум-кристаллизационную установку (ВКУ). В ВКУ раствор концентрируется до 40 % и из него выделяется остальной хлорид натрия. После отделения хлорида натрия 40%-ный раствор CaCl2 направляется в выпарной аппарат, где упаривается до состояния плава (72 % CaCl2). Плав кристаллизуется на барабанном кристаллизаторе, получающийся чешуйчатый хлорид кальция подают в закалочный барабан, затем – в барабан охлаждения. Чешуйчатый продукт (78 % CaCl2) отправляется на склад готовой продукции.
Затраты на 1 т продукта составляют: пар – 16,4 ГДж, электроэнергия – 410 МДж.
Подготовка для закачки в нефтяные скважины включает отстой в накопителе «белое море», разбавление водой, карбонизацию газом известковых печей, отстой.
Преимущества этого способа использования дистиллерной жидкости – снижение потребности нефтепромыслов в свежей воде; увеличение нефтеотдачи скважин; исключение затрат тепла на выпарку; использование накопителя «белое море».
Перспективы развития производства
1.Внедрение малоотходных комплексов по производству кальцинированной соды.
2.Внедрение современного оборудования (колонны с дырчатыми противоточными и перекрестно-точными контактными элементами, пластинчатые КХДС, эффективные ВФ, паровые кальцинаторы).
3.Создание системы карбонизационная колонна – гидроциклон – центрифуга (снижение влажности NaHCO3).
4.Внедрение современных способов коррозионной защиты оборудования из чугуна и стали (исключение применения титана
инержавеющих сталей).
100