
Химическая технология неорганических веществ
..pdf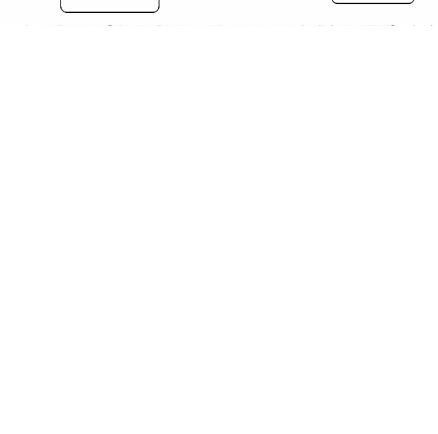
2 NaHCO3 т = Na2CO3 т + СО2 г + H2O г. |
(3.2) |
Фильтровую жидкость направляют на стадию дистилляции, т.е. |
|
регенерацию содержащегося в ней аммиака и углекислого газа: |
|
NH4HCO3 р-р = NH3 г + СО2 г + Н2О г; |
(3.3) |
2NH4Cl р-р + Са(ОН)2 = CaCl2 + 2NH3 г + 2Н2О г. |
(3.4) |
|
|
|
|
|
|
|
|
|
|
|
|
|
|
|
|
|
|
|
|
|
|
|
|
|
|
|
|
|
|
|
|
|
|
|
|
Рис. 15. Принципиальная схема производства кальцинированной соды аммиачным способом
71
Для выделения связанного аммиака используют известковое молоко, получаемое при гашении извести:
СаО + Н2О = Са(ОН)2. |
(3.5) |
Выделение аммиака и углекислого газа осуществляют путем нагревания растворов паром при температуре 74–114 °С.
После выделения аммиака и углекислого газа со стадии дистилляции удаляется дистиллерная жидкость, содержащая CaCl2 · NaCl (на 1 т соды 1 т CaCl2 и 0,5 т NaCl).
Необходимые для производства соды углекислый газ и известь получают путем обжига известняка при температуре 1200 °С:
СаСО3 т = СаО т + СО2 г. |
(3.6) |
При этом одновременно получают обжиговый газ, содержащий
40 % СО2.
3.3.3. Теоретические закономерности и практическая реализация отдельных стадий производства соды
Отделение аммонизации солевого рассола
Теоретические основы процесса аммонизации. В отделение ам-
монизации поступают очищенный от примесей (соединений кальция
имагния) рассол и газы, держащие аммиак и углекислый газ, отделений дистилляции, карбонизации и фильтрации.
На абсорбцию поступает с газами дистилляции 460 кг/т аммиака, 260 кг/т углекислого газа и 140 кг/т водяного пара. Из отделения карбонизации – 75 кг/т аммиака, 70 кг/т углекислого газа и 40 кг/т водяного пара. С воздухом фильтров в отделение аммонизации приходит 4 кг/т аммиака.
Движущая сила процесса поглощения аммиака и углекислого газа рассолом определяется температурой, составом газов, давлением
иравновесным давлением аммиака и СО2 над аммонизированным рассолом, определяемым составом и температурой раствора.
Равновесное давление аммиака pNH3 над растворами определяет-
ся по уравнению
72

lg pNH3 |
= − |
1750 |
+ n lg N +C, |
(3.7) |
|
|
T |
|
|
где Т – температура, К; N – концентрация аммиака, н.д. (нормальные деления, 1 н.д. = 201 кг-экв/м3); n и С– коэффициенты, зависящие от концентрации СО2 в растворе (табл. 12).
Таблица 12
Зависимость равновесного давления аммиака от содержания диоксида углерода в аммонизированном рассоле
(Т = 340 К, N = 100 н.д.)
ССО |
, |
|
|
pNH , |
ССО |
, |
|
|
pNH , |
2 |
|
n |
C |
3 |
2 |
|
n |
C |
3 |
н.д. |
|
мм рт. ст |
н.д. |
|
мм рт. ст |
||||
|
|
|
|
|
|
||||
0 |
|
1,13 |
5,67 |
602,5 |
40 |
|
1,83 |
2,15 |
2,5 |
10 |
|
1,25 |
5,36 |
512,9 |
50 |
|
4,13 |
3,40 |
2,65 |
|
|
|
|
|
|
|
|
|
|
20 |
|
1,38 |
5,08 |
489,8 |
60 |
|
436,5 |
354,8 |
316,2 |
|
|
|
|
|
|
|
|
|
|
30 |
|
1,55 |
4,73 |
478,6 |
|
|
|
|
|
|
|
|
|
|
|
|
|
|
|
Присутствие СО2 в растворе снижает равновесное давление аммиака над раствором и способствует его поглощению. В газе, который поступает на абсорбцию, парциальное давление аммиака примерно 58,5 кПа (440 мм рт. ст.).
Концентрация хлорида натрия в очищенном рассоле составляет 106 н.д., а в аммонизированном она снижается до 88–90 н.д. за счет снижения плотности раствора и разбавления конденсирующимися парами воды.
Соотношение NH3:NaCl должно быть 1,1–1,15, следовательно, концентрация аммиака в аммонизированном рассоле должна быть
101–104 н.д. или реально 100–106 н.д.
Пусть N = 100 н.д. и концентрация СО2 в растворе 40 н.д., тогда в уравнении (3.7) n = 1,83; С = 4,13. Отсюда lg рNH3 = −1750T + 7,79.
73
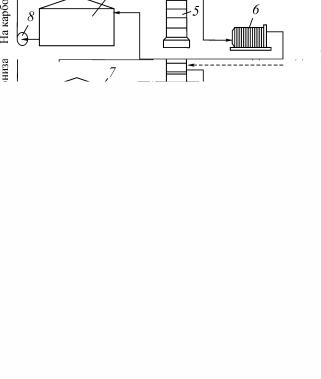
Если рNH3 = 440 мм рт. ст., то Т = 340 К (или 67 °С). Следовательно, температура в нижней части абсорбера должна быть ниже 67 °С, а температура газа на входе – не ниже 55 °С, т.к. при более низкой температуре возможно выделение твердых углеаммонийных солей.
Технологическая схема отделения аммонизации представлена на рис. 16.
Рис. 16. Технологическая схема отделения аммонизации: 1 – промыватель воздуха фильтров; 2 – первый промыватель газа абсорбции; 3 – второй промыватель газа колонн; 4 – абсорбер; 5 – емкость; 6 – пластинчатый холодильник; 7 – сборник аммонизированного рассола; 8 – насос
74
Очищенный рассол центробежными насосами подают в напорный бак (на схеме не показан), откуда он самотеком поступает в промыватель воздуха фильтров (20 %) и во второй промыватель газа колонн (остальные 80 %). Через промыватель воздуха фильтров воздух просасывается вакуум-насосами, расположенными в отделении компрессии. Рассол из аппарата 1 поступает в промыватель газа абсорбции 2. Через него вакуум-насосами просасываются газы из абсорбера 4. После аппарата 2 они смешиваются с газами содовых печей и направляются в промыватель газа содовых печей. В первом промывателе газа колонн 3 происходит улавливание рассолом аммиака и СО2 из газов отделения карбонизации, после улавливания газы через сепаратор выбрасываются в атмосферу.
Рассол из аппаратов 2 и 3 поступает в абсорбер, где он насыщается аммиаком и диоксидом углерода из парогазовой смеси отделения дистилляции. В нижней части абсорбера отводится тепло, выделяющееся в процессе абсорбции, путем охлаждения водой в труб- но-решетчатых контактных элементах. Далее газы абсорбции направляются в аппарат 2, а рассол после охлаждения в пластинчатом холодильнике направляется в сборник 7.
Основные параметры технологического режима абсорбера сле-
дующие: |
|
– жидкость на входе: температура 20–30 °С, прямой |
титр |
15020 н.д., содержание СО2 2–5 н.д.; |
|
– газ на выходе: температура 30–40 °С, разрежение |
330– |
350ГПа;
–газ на входе: температура 58–60 °С, разрежение 85–130 ГПа;
–жидкость на выходе: температура 60–65 °С;
–жидкость после пластинчатого теплообменника: температура
28–32 °С, прямой титр 100–106 н.д., содержание СО2 31–41 н.д., содержание хлор-иона не менее 89 н.д.
В отделении аммонизации применяют колонные аппараты с контактными элементами колпачкового типа. В последние годы разработан и применяется абсорбер с решетчатыми и трубнорешетчатыми контактными элементами (рис. 17). Абсорбер снабжен
75
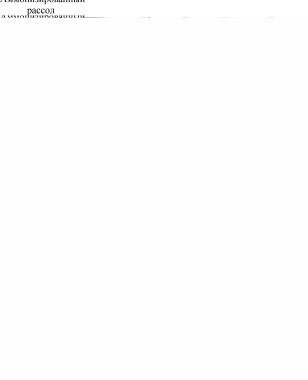
распределительной тарелкой, четырьмя противоточными решетчатыми тарелками и 12 противоточными трубно-решетчатыми тарелками. Тарелки абсорбера изготавливаются из титана марки ВТ1-0.
Рис. 17. Абсорбер с трубно-решетчатыми тарелками: 1 – распределительное устройство; 2 – противоточная решетчатая тарелка; 3 – противоточный трубно-решетчатый контактный элемент; 4 – перераспределительная тарелка; 5 – штуцер
Отделение карбонизации аммонизированного рассола
На стадии карбонизации протекают процессы абсорбции СО2 аммонизированным рассолом и кристаллизация бикарбоната натрия. В общем виде эти процессы описываются уравнением (3.1). Количе-
76
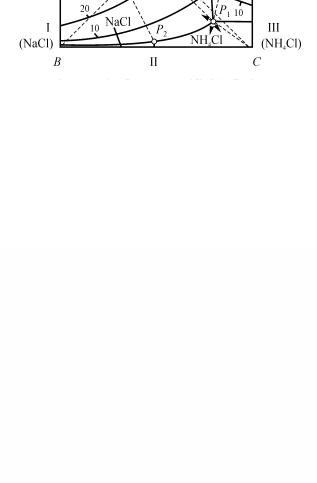
ство абсорбированного углекислого газа характеризуется степенью карбонизации Rс, т.е. отношением количества поглощенного СО2 [CO2 общ.] к общему содержанию аммиака в жидкой фазе
[NH3 общ.].
Rc = [CO[2 ]+ 2 [NH3] св] 100 ,
NH3 общ
где [СО2], [NH3 св.], [NH3 общ.] – концентрации СО2, связанного и общего аммиака в жидкой фазе.
При Rс = 200 % процесс может быть описан уравнением
NaCl р-р + NH4HCO3 р-р = NaHCO3 т + NH4Cl р-р.
В условиях производства Rс = 187–190 %.
Равновесие в системе при степени карбонизации 200 % может быть рассмотрено с помощью диаграммы состояния четырехкомпонентной взаимной системы солей NaCl – NH4HCO3 – H2O. Безводная проекция изотермы данной системы имеет вид, который представлен на рис. 18.
Рис. 18. Диаграмма растворимости четырехкомпонентной системы NaCl – NH4HCO3 – H2O при 15 °С
77
Одной из характеристик производства кальцинированной соды является степень использования Na, т.е. доля натрия, перешедшего из сырья в конечный продукт. В табл. 13 представлена зависимость степени использования Na (UNa) от температуры.
Таблица 13
Влияние температуры на UNa в точке Р1
Темпера- |
Состав раствора в точке Р1, н.д. |
UNa, % |
|||
тура, °С |
[Cl общ.] |
[NH3 общ.] |
[NH3 св.] |
[CO2 общ.] |
|
0 |
96,8 |
80,0 |
71,2 |
19,2 |
73,6 |
15 |
105,0 |
97,2 |
82,8 |
28,8 |
78,8 |
30 |
113,8 |
112,6 |
95,0 |
35,2 |
83,5 |
|
|
|
|
|
|
Таким образом, для достижения большего выхода гидрокарбоната натрия с точки зрения статики необходимо поддерживать наибольшую степень карбонизации, оптимальную температуру, соотношение [Cl общ.]/[NH3], отвечающее точке Р1 при соответствующей температуре.
Реальная величина степени использования Na UNa = 75 % определяется кинетическими факторами.
Достижение максимальной степени карбонизации определяется концентрацией СО2 в исходном газе. Газ содовых печей содержит 80–90 %, газ известковых печей – 33–40 % СО2. Следовательно, недопустимы потери СО2, т.к. это потребует использования большего количества газа известковых печей, что приведет к снижению общей концентрации газа, подаваемого на карбонизацию.
Скорость абсорбции СО2 определяется уравнением
WCO2 = Ka [NH3 своб.]м (pCO2г– рСО2*м),
где Ka – константа скорости абсорбции; [NH3 своб.]м – концентрация аммиака в метастабильном растворе; pCO2г и рСО2*м – парциальное и равновесное давления СО2.
78
Нужно отметить, что рСО2*м должно быть найдено для метастабильного раствора, в котором имеется пересыщение.
Кристаллизация гидрокарбоната натрия осуществляется в две стадии. Для получения крупных кристаллов необходимо, чтобы в карбонизационной колонне в том месте, где образуются первые кристаллы NaHCO3, были созданы условия для образования меньших количеств зародышей (высокая температура, малое пересыщение, а следовательно, и малая скорость поглощения СО2). В тех местах карбонизационной колонны, где происходит рост кристаллов NaHCO3, наоборот, должны быть созданы условия для быстрого роста кристаллов.
Скорость роста кристаллов можно описать следующим уравнением:
Wк = Kк · ([NH3 связ.]р – [NH3 связ.]м),
где Kк – константа скорости роста кристаллов; [NH3 связ.]р и [NH3 связ.]м – концентрации аммиака в реальном и метастабильном растворах.
Оптимальная температура в зоне образования кристаллических зародышей составляет 60–65 °С.
Технологическая схема отделения карбонизации представлена на рис. 19.
Отделение карбонизации комплектуется сериями колонн, причем производительность каждой серии равна производительности абсорбционной колонны. В состав серии входят осадительные карбонизационные колонны 5, первый промыватель газа колонн 3 и теплообменник 2. Периодически каждую из осадительных карбонизационных колонн (КЛ) ставят на промывку, тогда она выполняет функции колонны предварительной карбонизации.
Аммонизированный рассол из сборника аммонизированного рассола (CAP) поступает в колонну предварительной карбонизации (КЛПК), в которую подается также газ известковых печей, полученный при обжиге известняка и содержащий 38–40 % (об.) СО2. В КЛПК одновременно осуществляются промывка колонны от гид-
79
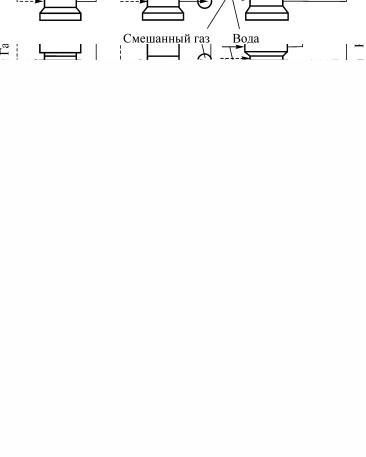
Рис. 19. Технологическая схема отделения карбонизации: 1 – колонна предварительной карбонизации; 2 – теплообменник; 3 – первый промыватель газа колонн; 4 – насос; 5 – осадительная карбонизационная колонна
рокарбоната натрия, осаждающегося на внутренних поверхностях аппарата, и предварительная карбонизация аммонизированного рассола. Из КЛПК жидкость, содержащая 55–60 н.д. диоксида углерода, при температуре 42–46 °С направляется в первый промыватель газа
80