
Химическая технология неорганических веществ
..pdfколонн (ПГКЛ-1). Сюда же поступает газ из КЛПК и осадительных колонн. В ПГКЛ-1 улавливается аммиак, отдутый карбонизующим газом из КЛПК. Однако основное назначение этого аппарата – более глубокое, чем в КЛ, извлечение СО2 из карбонизующего газа, что, кроме повышения общей степени использования СО2 в процессе, способствует снижению выдувания из КЛ аммиака. Более полному выполнению ПГКЛ-1 своих технологических функций способствует снижение температуры жидкости в нем. При этом снижается равновесное давление NH3 и СО2 над жидкостью, а следовательно, увеличивается эффективность их поглощения. С этой целью в некоторых схемах предусматривается охлаждение рассола перед подачей в ПГКЛ-1 до 35–38 °С встроенных холодильников. Содержание диоксида углерода в жидкости, выходящей из ПГКЛ-1, обычно составляет 60–66 н.д. Однако с целью повышения производительности КЛ и снижения выдувания из них аммиака иногда рекомендуют увеличивать концентрацию СО2 до больших значений. Такой режим называют глубокой предкарбонизацией и осуществляют его путем вдувания в ПГКЛ-1 газа известковых печей.
За время прохождения жидкости через ПГКЛ-1 ее температура повышается на 5–8 °С. Для дополнительного охлаждения жидкости после ПГКЛ-1 предусматривается теплообменник 2, откуда жидкость поступает в осадительную карбонизационную колонну 5. В нижнюю часть колонны подается смешанный газ (первый ввод), содержащий диоксид углерода 70–80 об. %, а в среднюю часть – газ известковых печей (второй ввод). Газ из осадительной карбонизационной колонны направляется в ПГКЛ-1, а суспензия – в отделение фильтрации.
Нормы технологического режима отделения карбонизации следующие:
Содержание СО2 в жидкости, выходящей из колонны предварительной карбонизации, не выше 60 н.д. В жидкости из промывателя газа колонн 60–76 н.д. Температура жидкости на входе в карбоколонну 42–46 °С, содержание в выходящей суспензии общего аммиака 92–97 н.д. хлорид-иона не менее 95 н.д. Прямой титр суспензии 23– 27 н.д., температура выходящей суспензии не выше 32 °С.
81
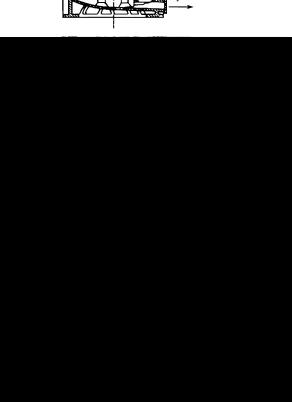
Для карбонизации применяют карбонизационные колонны, представляющие собой аппарат диаметром 3 м и высотой 28 м. Он состоит из чугунных царг (бочек), между которыми устанавливают пассетные контактные элементы – тарелки. В нижней половине колонны между контактными элементами устанавливают холодильные царги с холодильными трубками, изготовленными из нержавеющей стали. Общая поверхность теплопередачи холодильных царг 1344 м2 при производительности 230 т/сут.
Рис. 20. Карбонизационная колонна с перекрест- но-точными контактными элементами: 1– абсорбционная царга; 2 – прекрестно-точная тарелка; 3 – холодильная царга
82
В последнее время разработаны и применяются карбонизационные колонны с перекрестно-точными контактными элементами
(рис. 20).
Абсорбционная зона снабжена 17 царгами 1, в холодильной зоне установлены 8 холодильных царг 3.
Отделение фильтрации гидрокарбонатной суспензии
Процесс фильтрования используется для отделения кристаллов гидрокарбоната натрия от маточного раствора (фильтровая жидкость). Кристаллы NaHCO3 направляются в отделение кальцинации,
афильтровая жидкость – в отделение дистилляции для регенерации аммиака.
Влажный гидрокарбонат должен иметь следующие характеристики: влажность – 13–18 %; содержание хлорида натрия – не более
0,4 %; общего NH3 – не более 0,8 %.
Технологическая схема и аппаратура отделения фильтрова-
ния (рис. 21). Суспензия из карбонизационной колонны по трубопроводам поступает в напорную емкость 1. Из напорной емкости по общему трубопроводу она распределяется по вакуум-фильтрам 2 и подается в корыта вакуум-фильтров. После разделения суспензии фильтровая жидкость через сепаратор 4 направляется в сборник 6,
авоздух из сепаратора проходит через промыватель воздуха фильтров 11 и вакуум-насосом выбрасывается в атмосферу. Осадок на
фильтре проходит несколько стадий обработки (предварительную сушку, промывку, основную сушку и съем с поверхности барабана с помощью ножа, регенерацию фильтровой перегородки). Избыток суспензии из корыт вакуум-фильтров и напорной емкости собирается в буферном сборнике 7, откуда насосом качается в емкость 1.
Технические характеристики фильтра БС-5,6-1,8/1 следующие: поверхность фильтрования 5,6 м2, длина барабана 1 м, угол погружения барабана в суспензию 130 °С, число оборотов барабана 1–3 об/мин, производительность 180 т/сут.
83
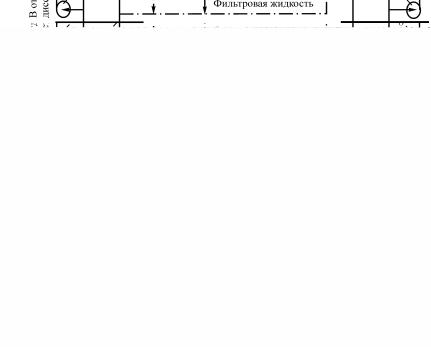
Рис. 21. Схема отделения фильтрации: 1 – емкость; 2 – вакуум-фильтры; 3 – дроссельные заслонки; 4 – сепараторы; 5, 8, 10 – насосы; 6 – сборник фильтровой жидкости; 7 – буферный сборник; 9 – сборник промывной жидкости; 11 – промыватель воздуха фильтров
Фильтрование суспензии осуществляется через фильтрующую ткань и слой осадка (в среднем 6 мм), остающегося на фильтре после срезания основной его части ножом.
В процессе фильтрации неизбежны потери гидрокарбоната натрия из-за частичного растворения при промывке и прохода мелких частиц через фильтровальную перегородку.
Важнейшей характеристикой является влажность гидрокарбоната натрия, т.к. она определяет выход готового продукта и затраты на испарение воды при кальцинации.
84
Отделение дистилляции в производстве кальцинированной соды
Теоретические основы процесса дистилляции. В отделении дис-
тилляции осуществляется регенерация аммиака и диоксида углерода из жидкости, образующейся при фильтрации суспензии гидрокарбоната натрия (фильтровая жидкость), а также из жидкостей, образующихся в других отделениях производства при промывке газов и аппаратов (слабые жидкости).
В основе дистилляции лежат процессы перевода связанного аммиака в свободное состояние, разложения соединений полусвязанного аммиака и выделения в газовую фазу летучих компонентов – аммиака, диоксида углерода и воды.
Процессы выделения аммиака и диоксида углерода осуществляются в дистилляционной колонне, состоящей из дистиллера (ДС), теплообменника дистилляции (ТДС) и конденсатора – холодильника газа дистилляции (КХДС). Отгонка осуществляется при постепенном нагревании фильтровой жидкости движущимися противотоком паром и парогазовой смесью.
При постепенном нагревании фильтровой жидкости в КХДС и ТДС протекают экзотермические реакции разложения находящихся в растворе гидрокарбоната и карбоната аммония и происходит выделение аммиака и диоксида углерода в газовую фазу:
NH4HCO3 = NH3 + CO2 +H2O – 239 кДж/кг; |
(3.8) |
(NH4)2CO3 = 2NH3 + CO2 + H2O – 972 кДж/кг. |
(3.9) |
После удаления из раствора летучих компонентов при температуре 95–98 °С жидкость из ТДС поступает в реактор-смеситель, где при подаче известковой суспензии происходит разложение связанного аммиака:
2NH4Cl + Ca(OH)2 = CaCl2 + 2NH3 + 2H2O + 218 кДж. (3.10)
Отгонка основного количества аммиака из жидкой фазы осуществляется в дистиллере путем подачи в нижнюю часть острого пара.
85
В смесителе и дистиллере протекает побочная реакция с образованием малорастворимого сульфата кальция:
Na2SO4 + CaCl2 = CaSO4 + 2NaCl – 264 кДж. |
(3.11) |
Для того чтобы кристаллизующийся сульфат кальция не откладывался на внутренних поверхностях дистиллера, а кристаллизовался в виде CaSO4 0,5H2O, температура в смесителе должна быть не ниже 93 °С (93–96 °С). Кроме того, время пребывания суспензии в смесителе (не менее 30 мин) и интенсивное перемешивание должны обеспечивать почти полное выделение CaSO4 0,5 H2O в твердую фазу именно в смесителе.
В современных отделениях дистилляции предусмотрено использование специальных колонн малой дистилляции для переработки слабых жидкостей. В этих колоннах в качестве теплоносителя используется вторичный пар, получающийся в специальных испарителях при снижении давления над выходящей из дистиллера жидкостью.
Таким образом, полное выделение аммиака и диоксида углерода из фильтровой жидкости обеспечивается постепенным ее нагреванием при контакте с парогазовой смесью в КХДС до 70–77 °С, в ТДС – до 95–98 °С и последующее нагревание в ДС – до 110–115 °С путем подачи пара с давлением 0,18–0,20 МПа.
Технологическая схема основной дистилляции представлена на рис. 22.
Фильтровая жидкость из сборника насосом подается в конден- сатор-холодильник газа дистилляции 3, где происходит ее нагревание и одновременное охлаждение парогазовой смеси с конденсацией из нее слабой жидкости. Слабая жидкость выводится из нижней части КХДС и направляется на малую дистилляцию. Выделившийся из фильтровой жидкости газ присоединяется к основному потоку газа и направляется на абсорбцию.
Жидкость из КХДС перетекает в теплообменник дистилляции 2, где при контакте с газом происходит дальнейшее ее нагревание и выделение летучих компонентов. Из ТДС жидкость подается в сме-
86
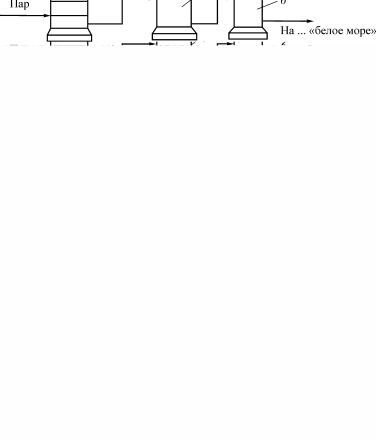
ситель 4, куда поступает также известковое молоко. После смешения и протекания процессов в смесителе жидкая фаза направляется в верхнюю часть дистиллера 1. Из ДС жидкость перетекает в первый испаритель 5 и затем во второй испаритель 6, откуда шламовыми насосами качается в шламонакопитель.
Рис. 22. Технологическая схема отделения дистилляции: 1 – дистиллер; 2 – теплообменник дистилляции; 3 – конденсаторхолодильник газа дистилляции; 4 – смеситель; 5 – первый испаритель; 6 – второй испаритель; 7 – паровой эжектор
87
В нижнюю часть ДС подается пар, а парогазовая смесь из верхней его части поступает в верхнюю часть смесителя и затем в нижнюю часть ТДС. Пар из испарителей используется в колонне дистилляции слабых жидкостей.
Основные показатели технологического режима при дистилляции таковы:
–фильтровая жидкость на входе: температура 28–30 °С; содер-
жание Cl– 89–92, СО2 34–40, прямой титр 24–28 н.д.;
–фильтровая жидкость на выходе из КХДС: температура
70–77 °С; содержание общего аммиака 70–77, СО2 18–22, прямой титр 22–27 н.д.;
–жидкость на выходе из ТДС: температура 95–98 °С; содержание Cl– 80–84, общего аммиака 77–81, прямой титр 20–23, СО2 не более 1 н.д.;
–жидкость на выходе из смесителя: температура 93–94 °С; со-
держание Cl– 63–68, СаО 2–3 н.д.;
–жидкость на выходе из дистиллера: температура 110–115 °С;
содержание Cl– не менее 61, прямой титр не более 0,1 н.д. Давление в нижней части дистиллера 0,15–0,16 МПа.
Основное оборудование отделения дистилляции. В качестве КХДС применяют аппарат, состоящий из прямоугольных бочек, на которых смонтированы трубные решетки. В трубных решетках крепятся холодильные трубки. Материал аппарата – чугун марки С4-24-44. В более современных аппаратах применяют холодильные трубки из алюминия марки АД1 или титановые.
Вкачестве ТДС применяют барботажные, насадочные или комбинированные аппараты. Дистиллер типовой дистилляционной колонны представляет собой барботажный аппарат с 11 одноколпачковыми тарелками (рис. 23).
Новые колонны дистилляции комплектуются щелевыми и дырчатыми противоточными контактными элементами и пластинчатым конденсатором-холодильником (рис. 24).
Втабл. 14 приведена основная характеристика аппаратов дистилляции содового производства.
88
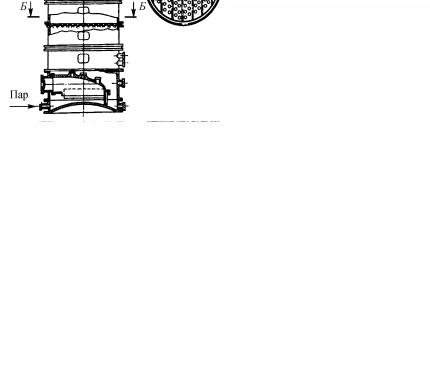
Рис. 23. Дистиллер: 1 – царгаРис. 24. Дистилляционная колонна: 1 – база; 2 – колокол; 3 – днище; распределительное устройство; 2 – кон- 4 – перелив; 5 – планка; 6 – сетактный элемент ТДС; 3 – контактный парационная царга; 7 – брызгоэлемент ДС отбойник; 8 – горловина; 9 – барботажная царга; 10 – штуцер
89
Таблица 14 Характеристика аппаратов дистилляции содового производства
|
ДС |
ТДС |
КХДС |
|||
Параметр |
одно- |
проти- |
много- |
проти- |
трубча- |
пла- |
колпач- |
воточ- |
колпач- |
воточ- |
тый |
стин- |
|
|
ковый |
ный |
ковый |
ный |
|
чатый |
Производитель- |
|
|
|
|
|
|
ность, т/с |
600 |
900 |
600 |
900 |
600 |
900 |
Диаметр, м |
3,0 |
3,0 |
3,2 |
3,2 |
|
|
Размеры сече- |
|
|
|
|
3,0×2,8 |
2,9×2,2 |
ния, м |
|
|
|
|
||
Высота, м |
17,1 |
21,7 |
17,5 |
16,6 |
8,6 |
15,7 |
Поверхность те- |
|
|
|
|
|
|
плообмена, м2 |
– |
– |
– |
– |
300 |
500 |
Отделение кальцинации гидрокарбоната натрия
впроизводстве кальцинированной соды
Вотделении кальцинации протекает термическое разложение гидрокарбоната натрия с образованием конечного продукта – кальцинированной соды и газа, содержащего диоксид углерода.
Основные характеристики готового продукта: содержание карбоната натрия – не менее 99,2 и хлорида натрия – не более 0,5 %; насыпная плотность – 500–550 кг/м3.
При термическом разложении сухого гидрокарбоната натрия протекает следующая эндотермическая реакция:
2NaHCO3 = Na2CO3 + CO2 + H2O – 125,6 кДж. |
(3.12) |
В практических условиях термическому разложению подвергают влажный гидрокарбонат натрия, содержащий следующие компо-
ненты, мас. %: NaHCO3 – 76–80; Na2CO3 – 2–3; NH4HCO3 – 1–2; (NH4)2CO3 – 1; NaCl – 0,2–0,4 и Н2О – 14–18. Наличие в гидрокарбо-
нате натрия влаги в виде насыщенного растворенным NaHCO3 рас-
90