
741
.pdf
Таблица 12.1
Температура заливки песчаных форм, ºС
|
Алюминие |
|
|
|
|
|
Сплав |
вые |
Бронза |
35 Л |
35 ХГСЛ |
Г13Л |
|
|
сплавы |
|
|
|
|
|
|
|
|
|
|
|
|
Толщина стенок |
720–780 |
1150–1180 |
1550–1590 |
1530–1570 |
1430–1450 |
|
6–20 мм |
||||||
|
|
|
|
|
||
|
|
|
|
|
|
|
Толщина стенок |
690–700 |
1100–1130 |
1520–1530 |
1510–1520 |
1420–1430 |
|
свыше 30 мм |
||||||
|
|
|
|
|
||
|
|
|
|
|
|
Для того, чтобы обеспечить требуемую температуру заливки сплава, его необходимо нагреть в печи до более высокой температуры с учетом потерь тепла при выпуске металла из печи в ковш и потерь тепла в ковше.
Потери тепла при выпуске из печи происходят на желобе печи и в падающей в ковш струе сплава, при этом основное количество тепла отводится излучением, интенсивность которого зависит от степени черноты жидкого металла и разности температур расплава и окружающей среды в четвертой степени. Снижение температуры сплава при выпуске из печи составляет: для стали 30–60 ºС, для бронзы и чугуна 10–30 ºС. Потери тепла излучением при заливке алюминиевых и магниевых сплавов сравнительно невелики.
Скорость заполнения формы металлом теоретически рассчитывают из условия обеспечения ламинарного режима течения расплава в полости формы или с учетом допустимой турбулентности.
Заполняемость отливки без образования дефектов будет обеспечена при средней фактической скорости подъема металла в форме υф, которая должна быть больше некоторой минимально допустимой υф min.
Начальную скорость подъема металла в форме υф нач для алюминиевых сплавов, в зависимости от толщины стенки δотл, можно определить по формуле А.А. Лебедева, см/с:
υф нач = 3,0...4,2 .
Необходимо, чтобы при этом υф нач ≤ υф min.
Минимально допустимая скорость подъема металла в форме зависит от относительной длины отливки Ζ/Rотл, где Ζ — путь, пройденный металлом от входа в форму на всю ее длину l, или ширину
В, или до места соединения с встречным потоком, — в этом случае Ζ = |
l |
или Ζ = |
Β |
, м; Rотл = δотл/2, и |
|
|
|||
2 |
2 |
|
температуры заливки алюминиевого сплава и колеблется в пределах 0,05–0,25 м/с. Например, для алюминиевых сплавов при температуре заливки 680 ºС и отношении Ζ/Rотл = 150 υф min = 0,25 м/с.
Допустимая минимальная скорость подъема металла для отливок из стали, в зависимости от
толщины стенки отливки, должна быть: |
|
|
||
δотл, мм |
5–10 |
10–40 |
40–60 |
60 |
υф min, см/с |
2,0–3,0 |
1,0–2,0 |
0,7–1,0 |
0,4–0,7 |
Продолжительность заливки литейных форм τ определяют по эмпирическим формулам. Для сложных по конфигурации тонкостенных отливок массой до 500 кг
τ = S G , для средних и крупных отливок
τ = S3Gδ ,
где G — масса отливки с литниками, кг; δ — преобладающая толщина стенки отливки, мм; S — коэффициент, зависящий от толщины стенки отливки. Значения коэффициента S равны:
δ, мм до 10 20 40 св. 80
S1,0 1,35 1,5 1,7
Техника заливки форм непосредственно влияет на качество отливок. При заливке форм необходимо обеспечить минимальное окисление металла и снижение его температуры. Для этого заливку следует вести короткой плотной струей металла, не допуская ее разрыва и разбрызгивания.
Перед заливкой форм из носковых ковшей необходимо снимать шлак с поверхности металла.
Литниковые чаши и воронки в процессе заливки должны быть наполнены. Не допускается прерывание струи металла.
Заливку следует прекращать после появления металла в выпорах и прибылях. Для получения плотных отливок рекомендуется производить доливку жидкого металла в прибыль. Эту операцию следует периодически повторять, при этом доливку металла в прибыль можно производить только на незатвердевшую поверхность. Если на поверхности прибыли образовалась тонкая корка металла, ее следует пробить ломиком и только после этого производить доливку жидкого металла из ковша.
После заполнения всего объема прибыли ее поверхность следует присыпать горелой землей или экзотермической смесью. Горелой землей также следует присыпать поверхность заполненных литниковых чаш и выпоров.
При заливке крупных форм эффективно поджигать газ, выделяющийся из формы по разъему, в выпоры или через отверстия в стенках опоки.
Контрольные вопросы
1.Классификация способов заливки форм и типов литниковых систем.
2.Особенности проектирования и расчета литниковых систем.
3.Опишите технологические режимы и технику заливки форм.
4.Как рассчитать скорость заполнения формы металлом?
Глава 13. Охлаждение отливки в песчаной форме
13.1. Процессы формирования отливки в песчаной форме
После заполнения формы начинается охлаждение металла, в процессе которого формируются кристаллическая структура и свойства отливки.
Процесс перехода макроскопического объема жидкого металла в твердое состояние в результате отвода тепла от отливки в литейную форму принято называть затвердеванием.
Процесс формирования микроструктуры отливки при переходе жидкого металла в твердое агрегатное состояние называют кристаллизацией. При затвердевании в песчаной форме все промышленные металлы и сплавы имеют кристаллическое строение.
При охлаждении металла в литейной форме происходят усадочные процессы: изменение размеров отливки, формирование пористости внутренних напряжений и усадочных раковин.
С начала заполнения песчаной формы жидким расплавом до выбивки отливки в ней происходят сложные физико-химические и механические процессы, которые определяют качество поверхности литого изделия, величину внутренних напряжений.
Таким образом, формирование отливки в песчаной форме определяется тепловыми, кристаллизационными, усадочными и физико-химическими процессами и их взаимодействием.
13.2. Тепловое взаимодействие отливки с формой
Песчаная форма является средой, в которую отливка отдает тепло. Толщина формы δф во много раз больше толщины отливки δ, поэтому все тепло, выделяемое отливкой при охлаждении, аккумулируется формой, при этом происходит нагрев формы на глубину δпф.
Начальная температура металла отливки равна температуре заливки tз, а начальная температура формы tф равна температуре воздуха tв в помещении литейного цеха.
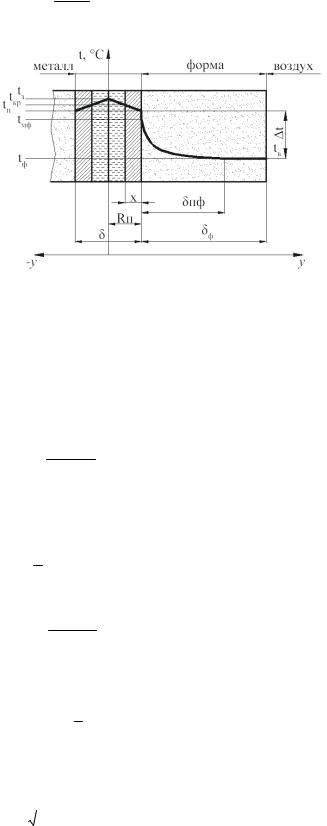
По истечении некоторого времени после заливки металл начинает затвердевать со стороны формы, в результате образуется слой твердого металла x. На границе с жидким металлом температура корки равна температуре кристаллизации tкр, а на границе с формой ее температура равна tп (рис. 13.1).
Для сплавов, затвердевающих в интервале температур, принимают
tкр = të + tc . 2
Поверхность формы на границе с отливкой нагревается до температуры tпф.
Рис. 13.1. Схема распределения температуры в охлаждающейся отливке и песчаной форме в процессе затвердевания металла
Толщину затвердевшей части стенки отливки x, в зависимости от времени τ, можно определить на основе следующих допущений: температура жидкого металла постоянна по сечению и равна температуре кристаллизации tкр; металл кристаллизуется при постоянной температуре tкр; затвердевание отливки ограничено одной плоской поверхностью, т.е. рассматривается полупространство с координатой y, перпендикулярной к поверхности отливки; тепловые характеристики металла остаются постоянными; теплопередачи в жидком металле не происходит, а в твердой части она подчиняется уравнению Фурье, при этом температура распределена по линейному закону:
dQ = λ (têð − tô )dτ . x
Выделяющаяся теплота кристаллизации при затвердевании слоя dx равна: dqкр = ρL dx.
При перемещении границы затвердевания на dx от твердого слоя отводится теплота
dqтв = 1 ñρ(têð − tô )dx . 2
Количество тепла, которое должна аккумулировать форма, равно:
dqф = λ (têð − tô )dτ . x
Уравнение теплового баланса для отливки и формы:
dqкр + dqтв = dqф.
Толщина затвердевшего слоя металла х подчиняется закону квадратного корня:
х = К τ ,
где К — коэффициент затвердевания, см/с1/2.
Коэффициент затвердевания отливки в песчаной форме определяют по формуле:
К = |
2 |
|
bô (têð − tô |
) |
||
|
|
|
|
|
, |
|
|
|
|
ρòL |
|
||
|
π |
|
||||
|
|
|
|
|
где ρт — плотность твердого металла.
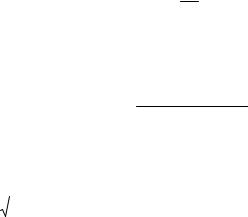
Из анализа последних трех уравнений следует, что скорость затвердевания отливки определяется теплофизическими свойствами металла и формы, т.е. коэффициент затвердевания зависит от теплоаккумулирующей способности песчаной формы bф.
Экспериментальные значения коэффициента затвердевания различных сплавов в песчаной форме приведены ниже:
Сплав |
Сталь |
Чугун |
Медные сплавы |
К |
0,10–0,16 |
0,07–0,09 |
0,22 |
13.3. Стадии охлаждения отливки
По технологическому циклу изготовления отливки продолжительность ее охлаждения занимает значительное время — от долей часа до сотен часов в зависимости от конфигурации, размеров и массы.
В литейных цехах крупного чугунного и стального литья 50 % производственных площадей занимают формы с охлаждающимися отливками.
Процесс охлаждения металла отливки можно разделить на четыре стадии, отличающиеся интенсивностью и характером отвода тепла.
1-я стадия. Охлаждение жидкого металла от температуры заливки до температуры кристаллизации или ликвидус сплава.
2-я стадия. Затвердевание отливки. При затвердевании отливки выделяется теплота кристаллизации, величина которой будет зависеть от природы металла.
3-я стадия. Охлаждение затвердевшей отливки до температуры выбивки ее из формы.
4-я стадия. Охлаждение отливки после выбивки из формы. Отливка отдает тепло в окружающую среду, в основном излучением и небольшую долю — конвекцией.
На первой, второй и третьей стадиях основная доля тепла от отливки в форму передается теплопередачей (контактный теплообмен) и небольшая часть тепла — излучением через открытые поверхности прибылей, выпоров и литниковой чаши.
От температуры заливки до температуры выбивки все тепло, выделяемое отливкой, воспринимает песчаная форма.
Продолжительность каждой стадии охлаждения будет определяться теплофизическими свойствами металла и песчаной формы, а также конфигурацией отливки и ее массой.
Интенсивность охлаждения какого-либо тела пропорциональна поверхности, приходящейся на единицу объема.
Для оценки общей продолжительности затвердевания тел различной формы применяют понятие приведенной толщины стенки.
Для плоской стенки R |
= |
δ |
, для цилиндра R |
= |
1 |
R , для сферы R |
= |
1 |
R . |
|
|
|
|||||||
ï |
|
2 |
ï |
|
2 |
ï |
3 |
|
|
|
|
|
|
|
|
Закон квадратного корня для приведенных толщин будет иметь вид:
2
τ = K .
Rï
13.4. Продолжительность охлаждения отливки
Для первой стадии продолжительность охлаждения определяется уравнением, с:
τ |
|
ñ ρ V |
(t |
çàë |
− t |
êð |
) |
2 |
= |
1 1 o |
|
|
|
, |
|||
1 |
|
1,13bô Fo(têð − tçàë ) |
||||||
|
|
|
|
|
|
|
|
|
где с1, ρ1 — теплоемкость и плотность жидкого металла, Дж/(кг·ч), кг/м3; Vo, — объем отливки, м3; tкр
|
(t |
ë + tñ ) |
|
— температура кристаллизации, ºС; Fо — |
|
|
|
|
2 |
|
||||
= |
|
|
|
|
|
|
площадь |
поверхности |
отливки, |
м |
; |
|||
|
2 |
|
|
|||||||||||
|
|
|
|
|
|
|
|
|
|
|
|
|||
|
|
|
|
|
|
|
|
Дж/(м2·с1/2 · |
ºС), λ |
|
|
|||
bф= |
|
ρ |
ñ λ |
ô |
|
— теплоаккумулирующая способность |
формы, |
ô |
— |
|||||
|
|
|
|
ô ô |
|
|
|
|
|
|
|
|
теплопроводность формы.
Для второй стадии продолжительность затвердевания определяется из уравнения:
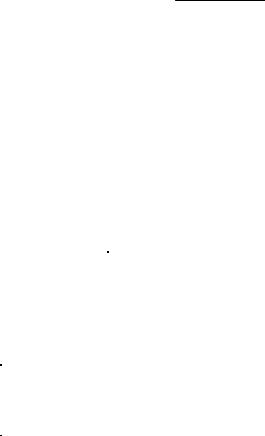
|
|
ρ2LVo |
|
2 |
|
τ |
2 = |
|
|
|
, |
1,13b (t |
− t |
|
|||
|
|
) |
|||
|
|
ô |
êð |
ô |
где L — теплота кристаллизации, Дж/кг; ρ2 — плотность твердого металла при температуре солидус, кг/м3.
Для третьей стадии продолжительность охлаждения определяется из уравнения:
Ñ |
ρ |
2 |
(t |
êð |
− t |
âûá |
) 2 |
||
î |
|
|
|
|
|
||||
τ3 = |
1,13b |
(t |
− t |
) |
, |
||||
|
|
ô âûá ô |
|
|
|||||
|
|
|
|
где tвыб — допустимая температура выбивки отливки из формы, ºС. Общее время охлаждения отливки в форме:
τо = τ1 + τ2 + τ3.
Рекомендуемые температуры выбивки отливок из черных сплавов не должны превышать следующих значений:
Неответственные крупные детали простой конфигурации |
600–700 ºС |
|
|
|
|
Небольшие детали простой конфигурации, к которым не |
400–500 ºС |
|
предъявляют требований по точности |
||
|
||
|
|
|
Ответственные детали сложной конфигурации |
200–300 ºС |
|
|
|
|
Отливки из легированных малотеплопроводных сталей |
150–200 ºС |
|
ответственного назначения |
||
|
||
|
|
После выбивки скорость охлаждения отливки резко возрастает. Продолжительность стадии охлаждения отливки после выбивки до температуры 50 ºС зависит от ее массы, температуры выбивки и наличия стержней (табл. 13.1).
Таблица 13.1
Время охлаждения отливок после выбивки
Масса отливки, кг |
До 100 |
100–500 |
500–1000 |
1000–5000 |
|
Температура выбивки, ºС |
600 |
500 |
400–500 |
300–400 |
|
Время охлаждения, ч: |
|
|
— |
— |
|
без стержней |
До 2 |
3–4 |
|||
12–18 |
18–36 |
||||
со стержнями |
До 5 |
7–8 |
|||
|
|
13.5. Кристаллизация отливок в песчаной форме
Кристаллизация промышленных металлов и сплавов в песчаной форме происходит без переохлаждения в центре отливки. Переохлаждение фиксируется только на фронте кристаллизации и составляет 0,01–0,1 ºС в зависимости от природы сплава, его чистоты, конфигурации и массы отливки.
Форма и размер зерна определяются скоростью охлаждения. При литье в песчаные формы образуются зерна округлой формы. На поверхности отливки образуется корка мелких округлых зерен и ближе к центру они укрупняются.
В сплавах, образующих твердые растворы, кристаллы имеют форму дендритов, скорость роста осей первого порядка выше, чем второго, а второго выше, чем третьего. В тонких стенках дендриты могут иметь игольчатую форму. В некоторых марках сталей границы между дендритами не выявляются или выявляются неотчетливо, т.е. отсутствуют четкие границы, характерные для зерен округлой формы. Дендриты срастаются между собой окончаниями ветвей второго порядка.
При кристаллизации сплавов с эвтектическим или перетектическим превращением вначале выделяются первичные кристаллы твердого раствора, а затем формируются зерна эвтектики или перетектики.
При эвтектической кристаллизации образуются две кристаллические формы. Когда обе фазы кристаллизуются, одновременно образуются пластинчатые формы. Одна из структурных составляющих в эвтектических сплавах может иметь форму стержней, шариков, иголок. При литье в песчаные формы эвтектики имеют аномальное строение.

Распределение температуры по сечению отливки зависит от теплофизических свойств кристаллизующегося металла, материала формы и конфигурации детали (рис. 13.2). В различных по толщине стенках отливок кристаллизация расплава происходит с разной скоростью.
Рис. 13.2. Схема кристаллизации отливки в песчаной форме:
а— изменение температуры расплава по сечению формы;
б— ход кристаллизации расплава в форме τ1 < τ2 < τ3 < τ4; 1 — перегрев металла; 2 — переохлаждение расплава;
3 — последовательная кристаллизация; 4 — охлаждение металла
Кристаллическое строение металла в песчаной форме зависит от скорости охлаждения, температуры заливки и методов рафинирования и модифицирования и раскисления.
При кристаллизации в отливках возникает химическая неоднородность — ликвация.
Различают дендритную ликвацию в пределах одного дендрита (внутридендритная), междендритную и зональную ликвацию в пределах отливки в целом, которая проявляется в виде ликвационных пятен, может быть внеосевой и располагаться по оси отливки (рис. 13.3).
а) |
б) |
|
|
|
|
|
|
|
Рис. 13.3. Виды ликвации в отливках: а — зональная ликвация
(1 — ликвационное пятно; 2 — внеосевая ликвация; 3 — осевая ликвация); б — дендритная ликвация
(1 — внутридендритная; 2 — междендритная)
Ликвация происходит в результате того, что примеси в сплаве (например, S, P, O, C) имеют растворимость в жидком сплаве больше, чем в твердом.
Неметаллические включения, присутствующие в структуре отливок после кристаллизации, по химической природе подразделяют на окислы компонентов сплава и сульфиды.
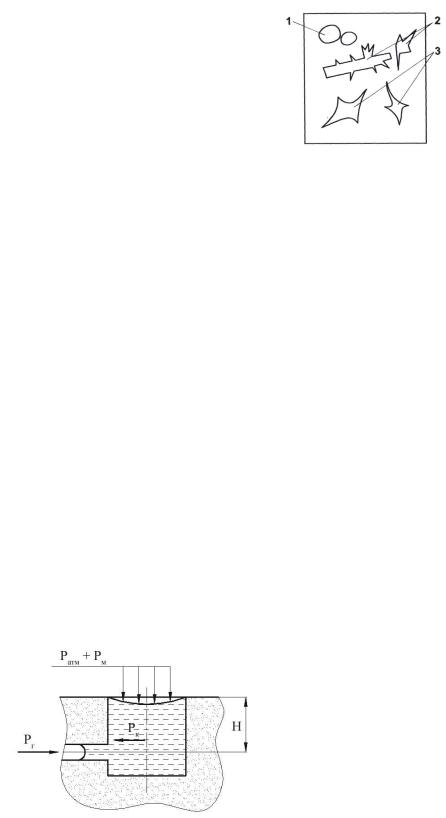
Неметаллические включения делятся на растворимые в жидком сплаве и не растворимые. По форме неметаллические включения бывают округлые, дендритные и пленочные (рис. 13.4). Их размеры колеблются от долей микрона до десятков микрон, поэтому они не успевают всплыть при кристаллизации и остаются в теле отливки.
При кристаллизации отливки в песчаной форме из расплава выделяются растворенные в нем газы, которые могут образовывать пустоты в виде скоплений мелких пузырьков, называемых газовой пористостью, или крупные пузыри — газовые раковины.
Другой причиной газовых раковин и газовой пористости могут быть химические реакции с образованием газообразных продуктов. Например, при кристаллизации нераскисленной стали в результате увеличения концентрации углерода и кислорода вблизи твердой фазы протекает реакция
FeO + C = Fe + CO↑.
Рис. 13.4. Неметаллические включения:
1 — округлые;
2 — дендритные;
3 — пленочные
Неблагополучную литую структуру отливок, затвердевающих в песчаной форме, улучшают различными методами.
Методы управления формированием кристаллического строения отливки разделяют на тепловые, физико-химические, механические и физические.
Ктепловым методам формирования кристаллического строения отливки относятся: снижение температуры заливки и повышение теплоаккумулирующей способности песчаных форм.
Кфизико-химическим методам улучшения литой структуры относятся различные методы модифицирования, раскисления и рафинирования расплавов.
Кмеханическим воздействиям на кристаллизующийся расплав относят: встряхивание, вибрацию форм, обработку расплава ультразвуком или его перемешивание перед заливкой, создание газового или механического давления.
Кфизическим методам относится кристаллизация отливок в магнитных и электрических полях.
13.6. Физико-химические процессы взаимодействия отливки с песчаной формой
На первой стадии охлаждения отливки, когда металл находится в жидком состоянии, возможно его проникновение в поры песчаной формы. В результате прогрева формы на границе с жидким металлом из нее выделяются газы: воздух, пар, газообразные продукты деструкции органических связующих.
Рис. 13.5. Условия проникновения расплава в поры песчаной формы
Условия проникновения расплава в поры песчаной формы (рис. 13.5):
Рг < Рм + Рк + Ратм,
где Рг — давление газов в песчаной форме; Рм = ρж gН — гидростатическое давление металла на уровне поры в форме; Рк =
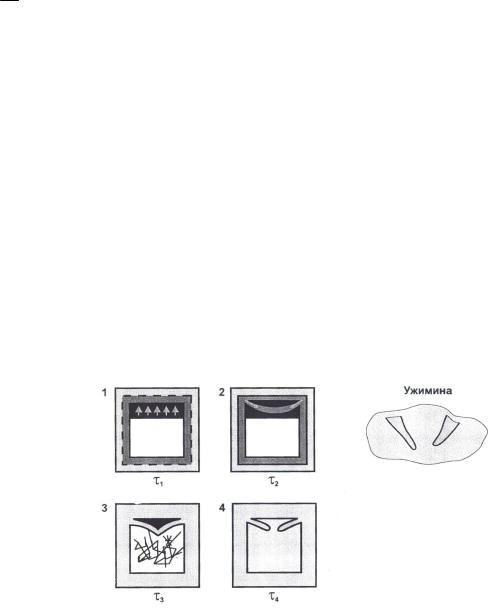
= 2σ cosϑ — капиллярное давление расплава в поре радиусом r, здесь σ — поверхностное r
натяжение расплава; ϑ— угол смачивания расплавом песчаной формы; Ратм — атмосферное давление на поверхность незатвердевшего расплава.
В результате проникновения расплава в поры формы образуется механический пригар на поверхности отливок. Если давление газа
Рг > Рм + Рк + Ратм,
газ проникает в жидкий расплав и обычно всплывает в верхнюю часть отливки. Поэтому на первой стадии охлаждения отливки газовые дефекты в них не образуются.
На второй стадии охлаждения отливки, когда образуется корка твердого металла, в которой на начальной стадии затвердевания имеются участки жидкой фазы, газы из формы могут прорвать корку и проникнуть внутрь расплава с образованием газовой пористости или газовых раковин в отливках. Газы из формы могут также деформировать корку твердого металла, что приводит к искажению поверхности отливки.
На этой стадии начинается окисление металла кислородом воздуха, содержащимся в порах формы. Происходит образование окислов FeO, MnO и других, а также взаимодействие их с материалом формы. Образуются легкоплавкие соединения 2FeO SiO2, MnO SiO2 и другие. На поверхности отливки образуется химический пригар.
На первой и второй стадиях охлаждения происходит образование специфических дефектов отливок, изготовляемых в песчаных формах, называемых ужиминами (рис. 13.6).
Рис. 13.6. Образование ужимин на отливках:
1 — испарение и миграция влаги в форме, зона «мокрой» прочности; 2 — тепловое расширение материала формы, отслоение вдоль зоны конденсации влаги; 3 — переход сплава в вязкожидкое состояние; 4 — разрушение отделившегося слоя формы
В конце второй стадии к моменту окончания затвердевания продолжается образование химического пригара. Происходит обезуглероживание поверхностного слоя отливки в результате взаимодействия углерода отливки с окислами формы и кислородом воздуха. Возникает механическое взаимодействие отливки с формой: форма и стержень препятствуют усадке отливки.
На третьей стадии отливка и форма охлаждаются как единое целое. Форма и стержень препятствуют усадке отливки.
На четвертой стадии охлаждения вне формы окисление поверхности отливки может усилиться, увеличивается уровень механического взаимодействия отливки и стержней из-за разных скоростей охлаждения. Может произойти разрушение отливки от внутренних напряжений.
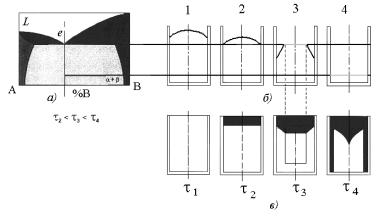
13.7.Усадочные процессы при охлаждении отливки
впесчаной форме
Усадочные процессы — это совокупность процессов сокращения объема и размеров залитого металла при его охлаждении в литейной форме, приводящих к образованию в отливках усадочных пустот (раковин, пористости) и усадочных деформаций.
Схема образования усадочных пустот в отливках, кристаллизующихся при постоянной температуре, показана на рис. 13.7.
а) |
б) |
|
|
|
|
|
|
|
|
|
|
|
|
|
|
в)
Рис. 13.7. Схема образования усадочных пустот в отливках, кристаллизующихся при постоянной температуре:
а — диаграмма состояния с эвтектикой; б — диаграммы распределения температуры по сечению отливки; в — отливка при охлаждении
до комнатной температуры в моменты времени τ1, τ2, τ3, τ4
На первой стадии охлаждения расплава от температуры заливки до температуры кристаллизации в момент времени от τ1 до τ2 (поз. 1 и 2 на рис. 13.7) в результате сокращения объема жидкого металла происходит уменьшение высоты отливки. При этом принято, что все тепло от отливки в форму передается через боковые стенки и дно формы, а теплопередача излучением через верхнюю поверхность отсутствует.
На второй стадии охлаждения происходит затвердевание отливки. В момент времени τз образуется слой твердого металла со стороны дна и боковых стенок формы. Свободно отпускается только слой жидкого металла в центральной незатвердевшей части отливки (поз. 3 на рис. 13.7). При этом начинается сокращение размеров отливки по сечению, и после затвердевания между ней и формой образуется зазор (поз. 4 на рис. 13.7).
Так как затвердевание металла происходит от стенок формы к центру с постоянным уменьшением сечения жидкой фазы, а свободное опускание уровня металла по высоте формы возможно только в незатвердевшей его части, в верхней части отливки образуется пустота в виде обратного конуса (поз. 4 на рис. 13.7).
Пустоту, образующуюся в отливке в результате усадки жидкого металла, при затвердевании называют усадочной раковиной.
На третьей стадии охлаждения металла в форме происходит сокращение линейных размеров отливки и образование зазора между ней и формой. Возможно образование зазора между отливкой и дном формы, величина которого зависит от массы металла и конфигурации детали.
Схема образования усадочных пустот в отливках, кристаллизующихся в интервале температур, показана на рис. 13.8.
На первой стадии охлаждения металла от температуры заливки tз до температуры ликвидус tл в моменты времени τ1 и τ2 (поз. 1, 2 на рис. 13.8) происходит сокращение его объема и уменьшение высоты отливки.
На второй стадии охлаждения происходит затвердевание отливки.
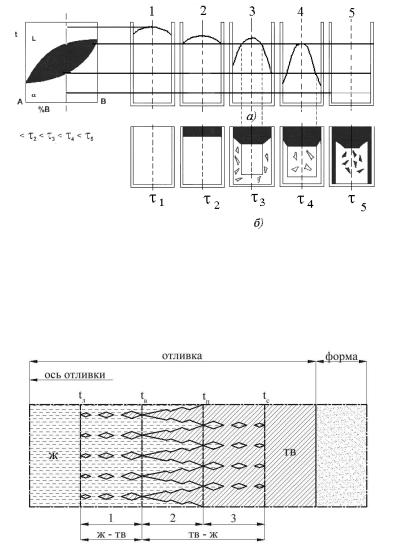
Затвердевание сплавов, кристаллизующихся в интервале температур, отличается от сплавов, кристаллизующихся при постоянной температуре, наличием двухфазной области между жидкой и твердой фазами.
а)
б)
Рис. 13.8. Схема образования усадочных пустот в отливках, кристаллизующихся в интервале температур:
а— диаграммы распределения температуры по сечению отливки
вмоменты времени τ1, τ2, τ3, τ4, τ5; б — отливка при охлаждении до комнатной температуры в моменты времени τ1, τ2, τ3, τ4, τ5
Строение отливки, затвердевающей в интервале температур, показано на рис. 13.9.
Рис. 13.9. Схема строения отливки, затвердевающей в интервале температур: tл, tв, tп, tс — температуры ликвидус, выливаемости, питания и солидус сплава соответственно; Ж, ТВ — жидкая и твердая фазы;
1— зона жидко-твердого состояния; 2, 3 — зоны твердо-жидкого состояния
Вмомент времени τз (поз. 3 на рис. 13.8) со стороны стенок и дна формы образовался двухфазный слой сплава, содержащий жидкую и твердую фазы. У поверхности формы температура сплава равна температуре солидус tс, а на границе между жидкой и твердой фазами его температура равна температуре ликвидус.
Область двухфазного состояния сплавов в интервале температур ликвидус–солидус принято делить на две части (жидко-твердую и твердо-жидкую) и три зоны:
1-я зона — микроскопических перемещений жидкого металла, в пределах которой твердые кристаллы разделены жидкостью, т.е. свободно плавают, и при выливании жидкого остатка удаляются вместе с ним; 1-я зона ограничена температурой ликвидус и температурой выливаемости;
2-я зона — зона локальных перемещений жидкого металла между твердыми кристаллами, образующими связанный скелет (каркас). При выливании жидкого остатка жидкость остается между кристаллами;
3-я зона — зона микроскопических перемещений жидкости в изолированных объемах, разделенных растущими кристаллами.