
741
.pdf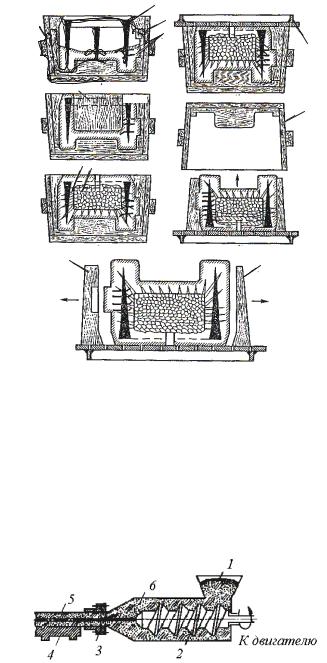
а) |
г) |
1 |
|
|
|
|
|
|
|
|
2 |
|
|
3 |
7 |
|
|
|
|
б) |
4 |
а) |
|
|
д) |
|
г) |
|
|
|
8 |
в) |
5 6 |
б) |
|
|
|
в) |
д) |
|
е) |
9 |
10 |
|
||
|
|
е)
Рис. 4.11. Изготовление крупного стержня по неразъемному ящику
4.5. Машинные способы изготовления стержней
При машинных способах изготовления стержней механизируются трудоемкие операции засыпки и уплотнения смеси, кантовки ящика и извлечение из него стержня, при этом достигается повышенная точность стержней и качество уплотнения.
Прессование стержней на мундштучных машинах (рис. 4.12) применяют для изготовления стержней постоянного профиля (цилиндрических, овальных, прямоугольных, многогранных): смесь 6 подается в приемную емкость 1 и шнеком 2 через мундштук 3 стержень заданного профиля выдавливается и поступает на плиту 4; на плите 4 стержень 5 отрезают на требуемую длину и помещают в сушило.
Рис. 4.12. Схема стержневой мундштучной машины
Изготовление стержней на прессовых машинах показано на рис. 4.13. На верхнем столе 3 машины монтируют половины ящиков 4, а на нижний стол 1 вторые половины ящиков 2, наполняют их смесью, укладывают каркасы 6, устанавливают наполнительную рамку 5 и заполняют ее смесью; смесь руками уплотняют в рамке и снимают ее (рис. 4.13, а); включают прессовый механизм, в процессе прессования избыток смеси выдавливается в желобок по разъему ящика (рис. 4.13, б); стол возвращается в исходное положение (рис. 4.13, в), стержень извлекают из нижних половинок ящика и направляют на сборку или в сушило.
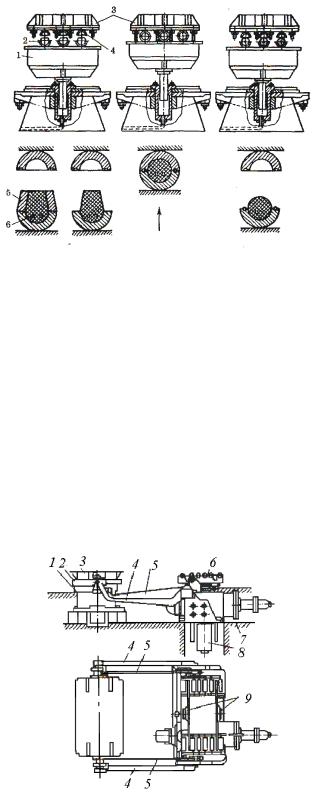
|
|
|
|
в) |
а) |
б) а) |
в) б) |
Рис. 4.13. Изготовление стержней на прессовой машине
Стержни, изготовленные на прессовых машинах, имеют высокую прочность, поэтому простые по конфигурации стержни устанавливают в форму сырыми и для их изготовления используют формовочные смеси.
Прессование не получило широкого применения ввиду неравномерности уплотнения по сечению сложных стержней и в связи с требованиями высокой прочности стержневых ящиков, способных выдержать высокие давления.
На встряхивающих машинах с перекидным или поворотным столом изготавливают средние, реже крупные стержни в мелкосерийном, серийном и массовом производстве. Применяют в основном формовочные машины с перекидным столом, реже с поворотным.
Встряхивающая машина с перекидным столом (рис. 4.14) состоит из встряхивающего механизма 1 с плитой 2, на которой лежит перекидной стол 3. После уплотнения стержня в ящике стол поворачивается на 180º рычагами 4 и тягами 5, приводимыми в движение горизонтальным гидроцилиндром 7, и устанавливается на приемный рольганг 6. Подъем и опускание рольганга осуществляется вертикальным гидроцилиндром 8. Строго вертикальная установка стержневого ящика на приемный рольганг обеспечивается двумя нивелировочными брусками 9 с пневматическим приводом.
Рис. 4.14. Встряхивающая машина с перекидным столом
Схема извлечения стержня на встряхивающих машинах с поворотным столом показана на рис. 4.15. На поворотном столе 1 машины жестко закреплен ящик 2. После уплотнения смеси на стержень 3 устанавливается сушильная плита 4, которая крепится к стержневому ящику, и стол поворачивается на 180º. Поднимается приемный стол 5 до соприкосновения с сушильной плитой, затем она отсоединяется от корпуса ящика и приемный стол опускается. После этого поворотный стол возвращается в исходное положение, а плиту 5 со стержнем направляют на сушку.
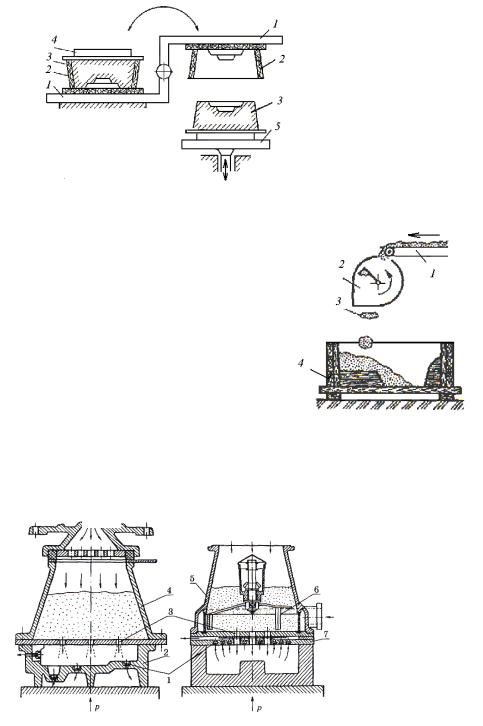
Рис. 4.15. Схема извлечения стержней с помощью поворотно-вытяжной машины
Пескометный способ уплотнения стержней показан на рис. 4.16. Смесь по транспортеру 1 поступает в головку пескомета 2, из которой пакет смеси 3 с большой кинетической энергией выбрасывается в стержневой ящик 4. Этот способ применяют для изготовления средних и крупных стержней. Для равномерного уплотнения смеси головку пескомета перемещают вдоль и поперек стержневого ящика. Иногда совмещают уплотнение пескометом и ручное уплотнение стержневой смеси пневматической трамбовкой.
Пескодувное уплотнение стержней показано на рис. 4.17: сжатый воздух, поступая в пескодувную головку 4, давит на слой смеси, фильтруется через ее поры и, захватывая частицы смеси через вдувные отверстия 3, заполняет полость ящика 2; отработанный воздух удаляется через вентиляционные венты 1 в стержневом ящике (рис. 4.17, а) или через венты 1, расположенные в надувной плите 7, пескодувной головки (рис. 4.17, б).
а) |
а |
б) |
б |
|
Рис. 4.17. Схема пескодувного уплотнения смеси: а — с нижней вентиляцией; б — с верхней
Рис. 4.16. Схема уплотнения пескометом
Для разрыхления смеси в некоторых конструкциях машин в пескодувных головках устанавливают механическую мешалку 6.
Рекомендуемый объем резервуара пескодувной головки должен составлять 2,5–3,0 объема стержневого ящика — Vящ. V = (2,5… 3,0)Vящ. Высота слоя смеси над вдувной плитой резервуара должна быть не ниже 150–200 мм. Влажность смесей не должна превышать 2,5–3,3 %.
При использовании смесей, имеющих сырую прочность до 0,01 МПа, вдувные отверстия должны быть диаметром 10–12 мм, а для смесей с прочностью выше 0,05 МПа необходимо увеличить их диаметр до 25–30 мм.
Отношение суммарного живого сечения вент в стержневом ящике 4 с нижней вентиляцией или в надувной плите 7 с верхней к суммарному сечению вдувных отверстий должно быть 0,8–1,0.
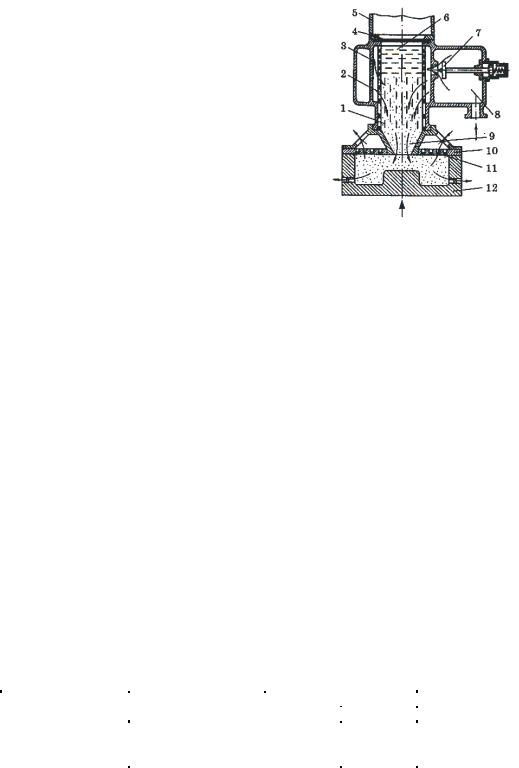
Пескострельное уплотнение стержневой смеси показано на рис. |
|
4.18. Смесь из бункера 5 поступает в пескострельную головку 3 при |
|
открытом шибере 4. После его закрытия сжатый воздух из ресивера |
|
8 через вдувной быстродействующий клапан 7, горизонтальные 6 и |
|
вертикальные 1 прорези входит во внутреннюю полость гильзы 2, |
|
отделяя смесь от нее. Истечение смеси через насадку 9 начинается |
|
через 0,02–0,07 с после открытия клапана 7. Предварительное |
|
заполнение смесью ящика заканчивается до достижения |
|
максимального давления воздуха. Уплотнение смеси обеспечивается |
|
за счет перепада давлений в пескострельном аппарате и стержневом |
|
ящике. |
|
Отработанный воздух удаляется через венты 11 во вдувной плите |
|
10 и стержневом ящике 12. |
|
Пескострельный способ изготовления стержней получил |
|
широкое применение по сравнению с другими методами. |
Рис. 4.18. Схема пескострельного |
Контрольные вопросы |
уплотнения смеси |
|
1.Какие требования предъявляются к стержню? Виды стержней и их классификация.
2.Конструктивные элементы стержней.
3.Что относится к стержневой оснастке?
4.Классификация способов изготовления стержней.
5.Машины для изготовления стержней.
Глава 5. Технология литейной формы
5.1. Технологический процесс ручной формовки
Подготовка технологической оснастки заключается в проверке исправности опок, моделей и инструмента. После установки модели и опоки на подмодельную плиту производят припыливание моделей или нанесение разделительного покрытия.
Уплотнение слоя смеси в опоке. На модель сначала наносят слой облицовочной смеси, уплотняя ее вручную вокруг модели, затем насыпают слой наполнительной смеси от 50 до 150 мм и уплотняют его ручными или пневматическими трамбовками.
Уплотнение смеси начинают от стенок опок, чтобы не повредить модели, а затем уплотняют весь объем опоки с избытком. Излишек смеси срезают металлической линейкой заподлицо с краями опок. При уплотнении смеси необходимо следить за тем, чтобы не сместить отъемные части, холодильники и элементы литниковой системы.
Требования к плотности форм зависят от массы отливки, вида сплава, высоты падения струи расплава, типа формы (сырая или сухая).
Ориентировочная плотность форм по твердомеру приведена в табл. 5.1.
Таблица 5.1
Плотность форм по твердомеру
Масса отливки, кг |
Высота формы, мм |
Твердость, ед. |
||
Верх формы |
Низ формы |
|||
|
|
|||
≤ 100 |
500 |
75–80 |
80–85 |
|
100–1000 |
1000 |
80–90 |
85–95 |
|
1000–5000 |
2000 |
85–90 |
90–95 |
|
75000 |
2000 |
90–95 |
95–100 |
Наибольшую плотность должен иметь слой формы около модели, а далее она должна быть меньше. В этом случае создаются условия для выхода газов из формы.
Плотность сухих форм больше плотности сырых на 25 %.
Плотность форм для литья легких сплавов меньше, чем для тяжелых цветных и черных металлов.
Вентиляционные каналы в форме накалывают при помощи душников — заостренных прутков диаметром 3–6 мм из расчета 4–5 наколов на 1 дм2 площади опоки, при этом они не должны доходить до модели на 3–4 мм.
Нанесение разделительного покрытия по разъему формы производят для того, чтобы не происходило прилипания формовочной смеси верха и низа полуформ.
Упрочнение выступающих частей в верхней полуформе производят простановкой крючков из расчета расстояния между ними 70–100 мм и с расстоянием между концами крючков и моделью 5–20 мм. Крючки и крестовины опок необходимо смочить глиной. При формовке по-сырому иногда вместо крючков применяют деревянные колышки — солдатики.
Извлечение модели из формы производят после расталкивания модели путем постукивания по ней деревянным молотком или слесарным молотком по подъемам.
Отделка форм. После удаления модели из формы проверяют ее твердость и исправляют поврежденные места.
Упрочнение рабочих поверхностей сухих форм производят литейными шпильками или гвоздями у питателей с шагом 25–35 мм, верхних горизонтальных участков с шагом 50–75 мм, нижних и вертикальных 25–100 мм. Выступы (болваны) укрепляют шпильками через 50–75 мм. Частоту прошпиливания сырых форм увеличивают в два раза.
Крупные формы перед сушкой окрашивают в два слоя и подкрашивают после сушки неостывшие (60–70 ºС) еще один раз.
Режимы сушки форм приведены в табл. 5.2.
Таблица 5.2
Режимы сушки форм из песчано-глинистых смесей
Размер опок в свету, м |
Температура |
Продолжительность |
|
сушки, ºС |
сушки, ч |
||
|
|||
От 0,5×0,6 до 1,2×1,8 |
400 |
6–8 |
|
От 1,2×1,9 до 3,0×2,0 |
400 |
8–12 |
|
От 3,5×2,0 до 5,5×3,0 |
450 |
16–24 |
|
От 5,0×3,5 до 5,5×4 |
450 |
24–36 |
|
Свыше 5,5×4,0 |
450 |
36–48 |
Сборка форм. Перед сборкой сухих форм необходимо проверить глубину просушенного слоя, при необходимости исправить повреждения, подкрасить и подсушить.
Подготовка стержней к сборке заключается в проверке их качества, размеров по шаблонам и комплектности.
Стержни устанавливают в заданной последовательности, строго контролируя точность установки знаков. При установке стержней с одним знаком устанавливают жеребейки.
В технологической документации, а также в технологической карте на изготовление стержня указывается его номер, который означает последовательность его установки в форму.
Положение каждого стержня в форме и стержней относительно друг друга строго контролируется шаблонами и мерками.
При невозможности проверки стенки отливки мерками производят предварительную установку стержней на глиняные конусы (маяки) или валики, имеющие высоту на 3–5 мм больше тела отливки. После сжатия верхнего стержня или верхней полуформы измеряют придавление конуса или валика, таким образом проверяется толщина тела отливки. На место маяков устанавливаются жеребейки высотой, равной высоте сдавленного конуса или валика, и производится окончательная установка стержня.
После установки стержня заделываются подъемы формовочной смесью с подсушкой и зазоры в знаках асбестовым шнуром, сырой формовочной смесью или пастой. Затем проводят очистку полуформ от комочков формовочной смеси и песчинок формовочными крючками с последующей продувкой форм сжатия воздухом или с помощью эжекторов и пылесосов.
Перед тем, как накрыть верхнюю полуформу по периметру отливки, в нижней полуформе сырых форм гладилкой делают подрезку, а в сухих формах прокладывают асбобитумный или глиняный жгут. Таким образом предотвращается утечка металла при заливке по разъему форм.
Верхнюю опоку в строго горизонтальном положении опускают на нижнюю с помощью центрирующих штырей и устанавливают литниковые чаши. Полуформы скрепляют между собой скобами, болтами с клином или на верхнюю полуформу устанавливают груз. Этим заканчивается сборка форм.
При заливке алюминиевых и магниевых сплавов груз не устанавливают и не скрепляют опоки друг с другом.
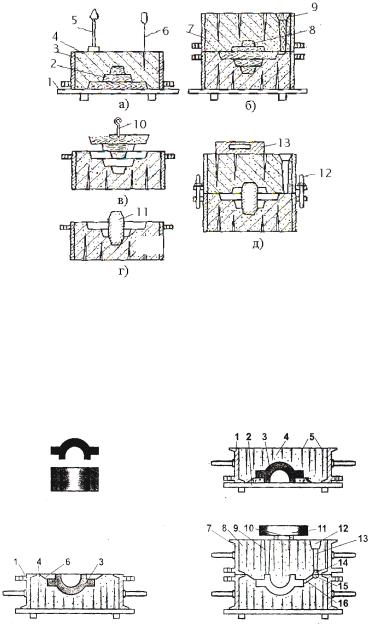
5.2. Разновидности ручной формовки
Формовка по разъемной модели в парных опоках показана на рис. 5.1.
а) |
б) |
|
|
|
|
|
|
|
|
|
|
в) |
д) |
|
г)
Рис. 5.1. Технологический процесс изготовления отливки «крышка» по разъемной модели:
а— изготовление нижней полуформы; б — изготовление верхней полуформы;
в— извлечение модели; г — установка стержня; д — форма, готовая к заливке;
1 — подмодельная плита; 2 — модель низа; 3, 7 — опоки; 4 — формовочная смесь; 5 — трамбовка; 6 — игла (душник);
8 — модель верха; 9 — модель стояка; 10 — подъем; 11 — стержень; 12 — центрирующие штыри; 13 — груз
Формовка с подрезкой по неразъемной модели в парных опоках показана на рис. 5.2.
а) |
б) |
|
а) |
|
б) |
|
|
|
|
|
|
г)
в)
Рис. 5.2. Формовка по неразъемной модели с подрезкой: а — неразъемная деревянная модель; б — изготовление нижней полуформы; в — выполнение подрезки в нижней полуформе; г — собранная полуформа, подготовленная к заливке;
1 — нижняя опока; 2 — подмодельная плита (щиток); 3 — модель; 4 — нижняя полуформа; 5 — наколы; 6 — подрезаемый слой смеси; 7 — опока;
8 — верхняя полуформа; 9 — выпор; 10 — прокладки над грузом; 11 — груз; 12 — литниковая чаша; 13 — стояк; 14 — коллектор (шлакоуловитель); 15 — металлоприемник (зумпф); 16 — питатель
Стопочная формовка. Сущность стопочной формовки заключается в том, что изготовленные формы мелких деталей устанавливают одну на другую в несколько этажей с общими стояком, выпором и литниковой чашей.
Открытая формовка в почве по мягкой постели (рис. 5.3) осуществляется в следующей последовательности:
а — в полу (плацу) цеха выкапывают яму 6 на 200–300 мм больше размера модели, засыпают ее наполнительной смесью 1, на два массивных металлических бруса (двутавра) 10, уложенных по уровню, устанавливают деревянные бруски 11 и между ними засыпают слой облицовочной смеси 2, излишек которой срезают линейкой 12;
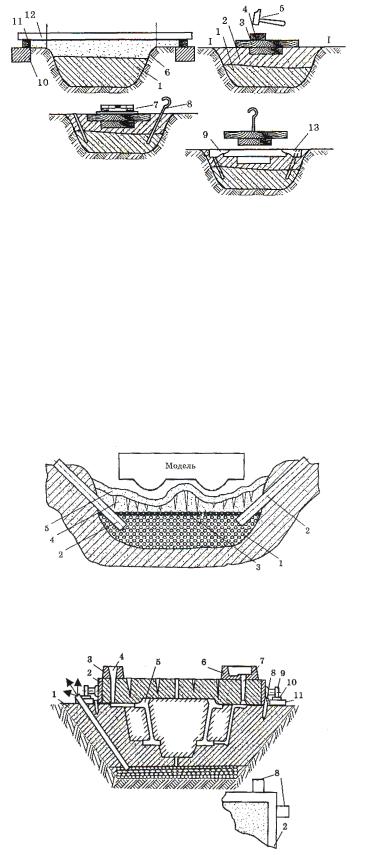
б — после снятия подкладок уплотняют смесь до уровня I–I, затем модель 3 осаживают в смесь 2, ударяя молотком 5 по бруску 4;
в — проверяют горизонтальное положение модели по уровню 7, уплотняют смесь вокруг модели, выравнивают смесь и душником 8 выполняют вентиляционные каналы;
г — извлекают модель и прорезают литниковые чаши 9 и 13.
а) |
б) |
|
а) |
|
б) |
в) |
г) |
|
|
|
|
в) |
|
|
|
|
Рис. 5.3. Формовка по мягкой постели
Формовку в почве по твердой постели подразделяют на открытую и закрытую, когда верх формы перекрывают опокой. Эту разновидность формовки применяют для изготовления крупных отливок массой в несколько тонн или десятков тонн.
Вплацу цеха выкапывают яму и начинают подготовку твердой постели, схема которой показана на рис. 5.4.
Вподготовленную таким образом постель осаживают модель и утрамбовывают вокруг модели формовочную смесь.
Закрытая формовка в почве по твердой постели показана на рис. 5.5.
Формы, изготовленные по мягкой постели, заливают сырыми, а по твердой постели — сначала окрашивают и сушат, затем собирают и после установки груза заливают.
Рис. 5.4. Подготовка твердой постели:
1 — уплотненный слой кокса или кускового шлака; 2 — трубы для вывода газов при заливке; 3 — сетка, перекрывающая слой кокса; 4 — уплотненный слой наполнительной смеси; 5 — облицовочная смесь толщиной 10–20 мм
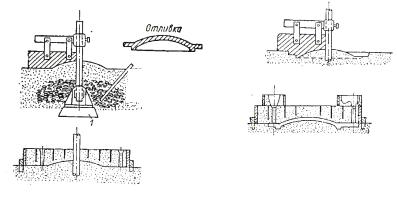
Рис. 5.5. Закрытая формовка в почве по твердой постели (собранная форма): 1 — твердая постель; 2 — верхняя опока; 3 — надставка выпора; 4 — выпор; 5 — верхняя часть детали, формируемая в опоке; 6 — литниковая чаша;
7 — стояк; 8 — колышки для центрирования опоки с низом формы; 9 — цапфы; 10, 11 — доски, подкладываемые перед установкой груза под цапфы, чтобы опока верха не продавила и не разрушила
края нижней полуформы, выполненной в почве
Формовка по вращающимся шаблонам поясняется рис. 5.6, где
а — вокруг приспособления для формовки по шаблону готовится твердая постель, вокруг вала насыпают горку облицовочной смеси, уплотняют и деревянным шаблоном срезают излишек формовочной смеси;
б — снимают шаблон и опорное кольцо, устанавливают опоку, заформовывают ее и центрируют забивкой колышков, таким образом получают верхний контур полости будущей отливки;
в — после съема опоки на вал надевают другой шаблон, с помощью которого удаляют смесь для оформления нижнего контура отливки;
г — снимают шаблон с вала, вытаскивают вал, заполняют отверстие, образованное валом в почве формовочной смесью, окрашивают форму, сушат и собирают, центрируя опоку по колышкам, затем на нее устанавливают литейную чашу, надставку для выпора и груз.
а) |
в) |
|
в)
г)
а)
б) |
|
г) |
|
||
|
|
|
б)
Рис. 5.6. Отливка и последовательность операций формовки по вращающемуся шаблону
5.3. Технология машинной формовки
Изготовление отливок в сырых песчано-глинистых формах является ведущим методом. В развитых странах с его помощью производится 60–78 % всех деталей автомобилестроения, тракторостроения и сельхозмашиностроения.
Машинная формовка позволяет механизировать наиболее трудоемкие и тяжелые операции: уплотнение формовочной смеси в опоке; извлечение модели из полуформы; поворот нижних полуформ и соединение их с верхними.
Машинные способы уплотнения по характеру воздействия на смесь подразделяют на прессовые, динамические и комбинированные.
Прессовые методы уплотнения форм классифицируют: по направлению движения смеси относительно стенок опоки на нижние, верхние и двусторонние; по величине давления прессования на низкие — до 0,3 МПа, средние — 0,3–0,7 МПа, повышенные — 0,7–2,0 МПа, высокие — 2–6 МПа и сверхвысокие выше 5 МПа. По конструкции прессовой головки — плоские и профильные жесткие прессовые плиты, эластичные плиты, решетки, многоплунжерные, роторные и лопастные головки.
Динамические методы уплотнения литейных форм классифицируют на три группы: инерционные — уплотнение гравитационное и встряхиванием; газодинамические — импульсное, пескодувное и пескострельное уплотнение; прессово-динамические — скоростное прессование и прессово-ударное.

Комбинированные методы предусматривают последовательное уплотнение сначала динамическим методом, а потом прессовым, например: встряхивание с подпрессовкой, пескодувнопрессовый, пескодувно-импульсный, уплотнение воздушным потоком с последующим прессованием (Seiatsu — процесс).
Пескометное уплотнение. В нем совмещены два процесса — это заполнение опоки и уплотнение смеси. Ширококовшовые пескометы, у которых ширина ковша ротора и головки равна ширине опоки, обеспечивают высокие производительность и качество уплотнения форм.
На рис. 5.7 приведены схемы машинного уплотнения форм.
Применяют две разновидности машинной формовки: раздельную на двух машинах и изготовление форм на одной машине.
Раздельное изготовление полуформ на двух машинах включает следующие операции: монтаж модельной плиты на стол формовочной машины; очистку моделей и покрытие их разделительным составом; установку верхней или нижней опоки по штырям на модельную плиту; установку моделей стояков и выпоров в верхней опоке; засыпку облицовочной смеси, установку наполнительной рамки; засыпку наполнительной смеси, уплотнение; снятие излишков смеси, выполнение наколов душником; извлечение стояков и выпоров; извлечение моделей; установку стержней и сборку форм.
в) г)
а) б)
Рис. 5.7. Машинное уплотнение форм:
а— верхнего прессования; б — нижнего прессования;
в— встряхиванием; г — пескометом; 1 — стол формовочной машины; 2 — модельная плита; 3 — модель;
4 — формовочная смесь; 5 — опока; 6 — наполнительная рамка; 7 — прессовая колодка; 8 — поршень; 9 — выходное отверстие;
10 — кожух пескомета; 11 — ротор; 12 — транспортер; 13 — лопатка; 14 — метательное окно
На формовочных машинах применяют следующие схемы извлечения моделей из форм: штифтового подъема (рис. 5.8); с протяжной плитой (рис. 5.9); штифтового подъема с протяжной плитой (рис. 5.10); с поворотным столом (рис. 5.11); с перекидным столом (рис. 5.12).
Рис. 5.8. Схема штифтового подъема:
1 — полуформа; 2 — модель; 3 — подъемные штифты; 4 — стол машины
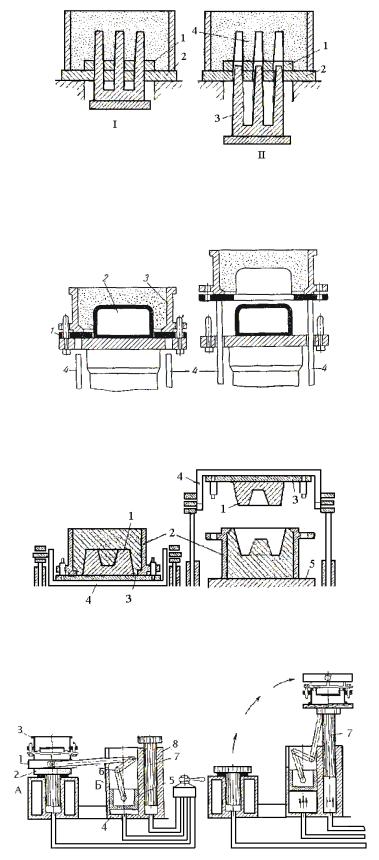
Рис. 5.9. Схема извлечения модели с помощью неподвижной протяжной плиты: I — формовка; II — удаление модели (протяжка);
1 — основное тело модели; 2 — модельная плита; 3 — протягивающиеся (проваливающиеся) ребра; 4 — свисающие болваны полуформы
Рис. 5.10. Схема извлечения модели с помощью протяжной плиты и штифтового подъема:
1 — протяжная плита; 2 — модель; 3 — опока; 4 — штифты
Рис. 5.11. Схема встряхивающей машины с поворотным столом: 1 — модель; 2 — опока; 3 — модельная плита; 4 — поворотный стол;
5 — приемное устройство
В
Рис. 5.12. Схема встряхивающей машины с перекидным столом: А — встряхивающий механизм; Б — перекидной механизм;
В — приемно-вытяжной механизм; 1 — перекидной стол; 2 — встряхивающая плита; 3 — опока;
4 — цилиндр перекидного механизма; 5 — поршень перекидного механизма; 6 — рычаги перекидного механизма; 7 — поршень приемно-вытяжного механизма