
741
.pdfII группа — сплавы на основе системы Al – Si – Cu: АК 5М (АЛ 5), АК 5Мч (АЛ 5 – 1), АК 5М2, АК 5М7, АК 6М2, АК 8М (АЛ 32), АК 5М4, АК 8М3, АК 8М3ч (ВАЛ 8), АК 9М2, АК 12М2, АК 12ММгН (АЛ 30), АК 12М2МгН (АЛ 25), АК 12М2,5Н2,5 (ВКЖЛС-2), где М — медь; цифры после буквы указывают среднее содержание меди в сплаве; Мг — магний; Н — никель.
III группа — сплавы на основе системы Al – Cu: АМ 5 (АЛ 19), АМ 4,5 Кд (ВАЛ 10), где Кд — кадмий.
IV группа — сплавы на основе системы Al – Mg: АМг 4К1,5М, АМг 5К (АЛ 13), АМг 5Мц (АЛ28), АМг 6л (АЛ 23), АМг 6лч (АЛ 23 – 1), АМг 10 (АЛ 27), АМг 10ч (АЛ 27 – 1), АМг 11 (АЛ 22), где Мц
—марганец.
V группа — сплавы на основе алюминия, прочие компоненты: АК 7Ц9 (АЛ 11), АК 9Ц6, АЦУМг
(АЛ 24), где Ц — цинк.
Сплавы, предназначенные для литья изделий пищевого назначения, маркируют дополнительно буквой П. В них массовая доля свинца должна быть не более 0,15 %, мышьяка — не более 0,015 %, цинка — не более 0,3 %, бериллия — не более 0,0005 %.
Для всех групп сплавов в скобках приведены старые обозначения марок сплавов, действующие до 1993 г.
В конструкторско-технологической и нормативной документации на отливки из алюминиевых сплавов приняты следующие сокращенные обозначения способов литья: 3 — литье в песчаные формы; В — литье по выплавляемым моделям; К — литье в кокиль; Д — литье под давлением; О
—литье в оболочковые формы; ПД — литье с кристаллизацией под давлением (жидкая штамповка); М — сплав подвергается модифицированию.
Условные обозначения в документации видов термической обработки отливок из алюминиевых сплавов: Т1 — искусственное старение без предварительной закалки; Т2 — отжиг; Т4 — закалка; Т5
—закалка и кратковременное (неполное) искусственное старение; Т6 — закалка и полное искусственное старение; Т7 — закалка и стабилизирующий отпуск; Т8 — закалка и смягчающий отпуск.
Различают алюминиевые сплавы в чушках (металлошихта) и в отливках.
Калюминиевым сплавам в отливках предъявляются требования в зависимости от объема контроля. Группа контроля указывается в технических требованиях на поле чертежа отливки или литого изделия.
КI группе контроля относятся отливки, контроль механических свойств которых осуществляется выборочно на образцах, вырезанных из тела контрольных отливок с одновременным испытанием механических свойств на отдельно отлитых образцах от каждой плавки или поштучным испытанием на образцах, вырезанных из прилитых к каждой отливке заготовок, а также поштучным контролем на плотность (рентген-просвечивание).
Ко II группе относятся отливки, механические свойства которых определяют на отдельно отлитых образцах или на образцах, вырезанных из прилитых к отливке заготовок, и по требованию завода-потребителя на образцах, вырезанных из отливок (выборочно), а также поштучным или выборочным контролем плотности отливок методом рентген-просвечивания. Для отливок II группы контроль на плотность не производят.
КIII группе относят отливки, у которых контролируют только твердость.
По условиям работы отливки подразделяют на три группы: общего, ответственного и особо ответственного назначения.
Контроль плотности алюминиевых отливок производят на наличие литейных дефектов и пористости. Пористость алюминиевых сплавов оценивают по диаметру пор и их количеству (табл. 11.1, рис. 11.1, где приведены эталоны пористости алюминиевых сплавов).
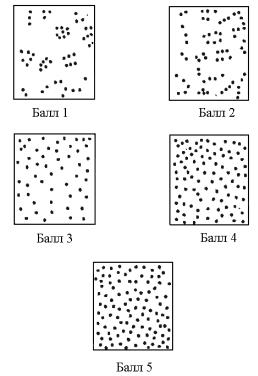
Таблица 11.1
Шкала пористости алюминиевых сплавов
Номер эталона |
Диаметр пор, мм |
Количество пор на 1 см2, шт. |
|
1 |
До 0,1 |
До 5 |
|
2 |
До 0,1 |
До 8 |
|
» 0,2 |
»2 |
||
|
|||
3 |
До 0,3 |
До 12 |
|
» 0,5 |
» 3 |
||
|
|||
4 |
До 0,5 |
До 14 |
|
» 1,0 |
» 6 |
||
|
|||
|
До 0,5 |
До 15 |
|
5 |
» 1,0 |
» 8 |
|
|
Св. 1,0 |
» 2 |
Рис. 11.1. Эталоны пористости алюминиевых сплавов
Допустимый балл пористости отливок указывается в технических требованиях чертежа
отливки.
Механические свойства алюминиевых отливок зависят от способа литья, режима термической обработки и модифицирования, которые также указываются в технических требованиях на отливки.
Благодаря низкой плотности и хорошим технологическим свойствам отливок из алюминиевых сплавов объем их производства ежегодно растет.
11.2. Плавка алюминиевых сплавов
Плавку алюминиевых сплавов производят в пламенных или электрических отражательных
печах, индукционных тигельных печах высокой и промышленной частоты, индукционных
канальных печах и электрических тигельных печах сопротивления.
Для разливки мелких деталей сплав готовят в плавильной печи, а затем жидкий металл
переливают в раздаточные печи.
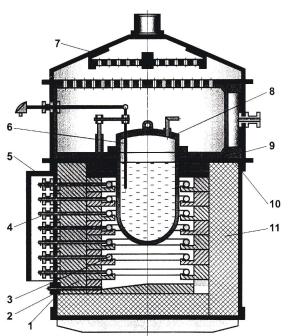
В раздаточных печах сплав повторно рафинируют, модифицируют, а затем из них производят разливку. В качестве раздаточных печей применяют тигельные электрические печи сопротивления, устройство которых показано на рис. 11.2.
В литейных цехах с небольшим объемом производства плавку и разливку алюминиевых
сплавов ведут в одной и той же печи, для чего наиболее подходящими являются тигельные
электропечи сопротивления.
В качестве шихтовых материалов для плавки применяют: первичные чушки алюминия и силумина, лом алюминия, возврат собственного производства, стружку и лигатуры. В литейном производстве лом и стружку алюминиевых сплавов предварительно переплавляют и разливают в чушки.
Шихтовые материалы: чушковые сплавы и лигатуры, — подвергают травлению в растворах едкого натрия или прокаливают.
Качественная подготовка шихты для приготовления литейных алюминиевых сплавов позволяет значительно снизить брак отливок.
При плавке в атмосфере воздуха алюминий окисляется кислородом воздуха и парами воды.
Рис. 11.2. Тигельная электрическая печь сопротивления:
1 — стальной кожух; 2 — футеровка; 3 — нагревательные элементы; 4 — клеммы; 5 — клеммная коробка; 6 — термопара; 7 — кожух вентиляционный; 8 — крышка печи; 9 — тигель плавильный;
10 — опорная плита; 11 — теплоизоляционный слой
Расплав чистого алюминия покрывается слоем оксидной плены γ — Al2О3, которая не растворяется в жидком алюминии и хорошо защищает расплав от дальнейшего окисления и наводораживания. Толщина слоя плены зависит от температуры расплава. Чем выше температура, тем толще слой плены.
Легирующие элементы влияют на процессы окисления алюминиевых сплавов и на плотность покровной плены, т.е. на ее газопроницаемость и, следовательно, на скорость окисления и наводораживания расплава.
Cu, Si, Mn в небольших количествах не снижают защитных свойств плены алюминия γ — Al2О3, а при значительном содержании изменяют ее химический состав и защитные свойства. Оксидная плена при этом будет состоять из твердых растворов оксидов кремния, марганца, меди с оксидом алюминия и шнипелей.
K, Na, Ni, Ba, Ca, Sr, Mg, Zn при незначительном содержании образуют на поверхности рыхлые оксидные плены, способствующие окислению Al и наводораживанию сплава.
При содержании магния более 1 % окисная плена почти полностью состоит из оксида магния. Бериллий и лантан значительно снижают окисление и наводораживание алюминиевых сплавов
за счет образования плотной покровной плены.
Перемешивание расплава в процессе плавки приводит к нарушению целостности оксидной плены и способствует замешиванию ее в расплав, т.е. загрязнению его оксидными включениями. При плавке алюминиевых сплавов в чугунных тиглях происходит загрязнение расплава железом.
Склонность алюминиевого сплава к поглощению водорода зависит от его легирования. Медь и кремний уменьшают растворимость водорода в алюминии. Mg, Ti, Zr, Li, Na, Ca, Ba, Sr увеличивают растворимость водорода в алюминии. Большое количество водорода может быть внесено также непрокаленными шихтовыми материалами.
Алюминиевые сплавы склонны к образованию газовой пористости вследствие того, что растворимость водорода в твердом алюминии значительно ниже его растворимости в жидком расплаве.
Для того чтобы предупредить образование пористости в отливках, например, в сплаве с 7 % Si, содержание водорода в расплаве не должно превышать 0,15 см3/100 г.
При плавке алюминиевые сплавы от окисления и насыщения водородом защищают газообразными фторидами — SiF4, BF3, SF6 или покровными флюсами. Для большинства сплавов, кроме магниевых, служит флюс 45 % NaCl; 55 % KCl. Для алюминиево-магниевых сплавов применяют флюс MgCl2 · KCl.
Хорошо защищает алюминиевые сплавы от окисления и насыщения водородом микролегирование их бериллием и лантаном.
11.3.Рафинирование алюминиевых сплавов
Влитейном производстве, в отличие от металлургического, рафинирование производят только с
целью снижения содержания водорода и неметаллических включений, для чего широко
применяются следующие способы рафинирования: хлоридами, обработка газом, фильтрация.
Рафинирование хлоридами заключается в погружении в расплав до дна тигля порошков хлоридов или таблеток. В результате их взаимодействия с алюминием образуется газообразный хлорид алюминия, пузырьки которого, поднимаясь на поверхность расплава, увлекают за собой неметаллические частицы. Внутрь пузырьков дифундирует растворенный водород. Таким образом происходит рафинирование сплава от неметаллических включений и водорода.
Вкачестве порошкообразных хлоридов применяют C2Cl6 и прокаленный MnCl2. Таблетки для рафинирования «Дегазер» и другие содержат смеси солей. MnCl2 вводят в расплав в количестве ~ 0,1 % при температуре 700–730 ºС, гексахлорэтан — в количестве ~ 0,3 % при 740–750 ºС, таблетки «Дегазер» — в количестве ~ 0,5 % при 720–750 ºС.
Эффективно рафинирование сплавов фторцирконатом калия ~ 0,1 % при 730 ºС и таблетками углекислотных солей: BaCO3, SrCO3, Na2CO3 и др.
Рафинирование флюсами. Для сплавов, не содержащих магний, применяют флюс 35 % КCl, 50 % NaCl, 15 % Na2SiF6. Для сплавов, содержащих магний, 60 % MgCl2 · KCl; 40 % CaF2. Универсальный рафинирующий и модифицирующий флюс для сплавов системы Al – Si: 45 % NaCl; 15 % Na3AlF6; 40 % NaF.
Флюсы предварительно переплавляют и в колокольчике вводят в расплав при непрерывном перемешивании. Расход флюса 0,5–1 %, температура расплава 720–750 ºС. После выдержки 30–45 мин снимают шлак и разливают сплав.
Влитейном производстве для продувки сплавов газом используют очищенный аргон. Расход газа 0,5–1 м3 на 1 т сплава. Продолжительность продувки 5–20 мин.
Фильтрацию расплава ведут через сетчатые, пенокерамические и зернистые керамические фильтры.
Рафинирование методом вакуумирования производят при остаточном давлении 1330 Па, температуре 720–740 ºС в течение 10–30 мин.
11.4. Модифицирование литейных алюминиевых сплавов
Модифицирование алюминиевых сплавов лигатурами Al – Ti, Al – B или Al – Ti – B производят при температуре 720–750 ºС из расчета содержания 0,05–0,15 % Ti и 0,01–0,02 В.
Доэвтектические и эвтектические Al – Si сплавы модифицируют натрием, которого должно быть в количестве 0,05–0,1 %.
Модифицирование металлическим натрием производят в основном флюсами и редко из-за его большого угара.
Модифицирование двойным флюсом: 67 % NaF; 33 NaCl, — ведут при температуре 780–800 ºС. На поверхность расплава насыпают слой флюса в количестве 1–2 % от массы металла, выдерживают 12–15 мин, затем нарубают корочку флюса и замешивают в расплав на глубину 50–
100мм.
Врезультате реакции 6NaF + Al → Na3AlF4 + 3Na происходит восстановление Na из флюса и растворение его в расплаве. С поверхности расплава удаляют шлак и заливают клиновую пробу на качество модифицирования. Излом модифицированного сплава имеет светло-серый цвет без наличия блестящих включений.
Сплав должен быть разлит в течение 25–30 мин из-за явления потери модифицирующего эффекта.
Для снижения температуры модифицирования вместо двойного применяют тройные составы модификаторов, содержащие натрий.
При модифицировании стронцием эффект модифицирования сохраняется долго — более 2–3 ч. Модифицирование стронцием производят путем введения в расплав лигатуры Al – Sr (5 % Sr) из расчета 0,05–0,07 Sr в сплаве.
Модификаторами длительного действия являются также иттрий и сурьма, которые вводят в
расплав в количестве 0,15–0,3 %. Заэвтектические силумины (более 13 % Si) модифицируют фосфором при температуре 790–825 ºС из расчета 0,05–0,1 Р.
Фосфор вводят в виде лигатуры Cu – P (9–11 % Р) или солевых флюсов, содержащих красный фосфор или фосфорорганические вещества (хлорофос).
11.5. Плавка магниевых сплавов
Чистый магний отличается высокой химической активностью. Он легко окисляется. При
температуре 450 ºС отсутствуют защитные свойства плены и увеличивается скорость окисления.
При температуре 623 ºС в атмосфере воздуха магний воспламеняется.
С водой магний интенсивно реагирует с выделением водорода, который часто является причиной взрывов из-за образования гремучего газа.
Литейные сплавы магния подразделяют на три группы: I — Mg – Al – Zn (МЛ3, МЛ4, МЛ5, МЛ6);
II — Mg – Zn – Zr (МЛ8, МЛ12, МЛ15);
III — сплавы легированные Р3М (МЛ9, МЛ10, МЛ11, МЛ19).
Плавку магниевых сплавов ведут под покровом флюсов или в защитной атмосфере в массовых стальных тиглях. Для плавки применяют индукционные и электрические печи сопротивления.
Стальной толстостенный литой тигель нагревают до 400–500 ºС и загружают в него флюс ВИ 2 в количестве до 10 % от массы шихты.
Состав флюса ВИ 2: 38–46 % MgCl2; 34–40 % KCl; < 10 % CaCl2; 5–8 % BaCl2; 3–5 % CaF2; < 1,5 MgO; влажность не более 3 %.
Флюс расплавляют и небольшими порциями загружают в него подогретые до 150–200 ºС шихтовые материалы.
В качестве шихты применяют первичные чушки магния, алюминия, цинка, готовые магниевые сплавы, возврат собственного производства, различные лигатуры.
Марганец вводят в виде лигатуры Al – Mn (8–10 %) или Mg – Mn (2 %). Цирконий вводят в
виде лигатур Mg – Zn – Zr (6–7 %).
После введения всех составляющих шихты расплав нагревают до 700–720 ºС и производят рафинирование и модифицирование. Затем выстаивают сплав 10–15 мин, заливают пробы на излом и для химического анализа. Готовый сплав разливают по формам, оставляя в тигле расплав
— 20–30 % от емкости тигля, который разливают в изложницы, так как он загрязнен оксидами и флюсом и не пригоден для литья деталей.
Рафинирование магниевых сплавов проводят с целью очистки расплава от неметаллических включений, водорода и железа.
Рафинирование методом отстаивания производят при температуре не ниже 750 ºС в течение 20–30 мин.
Рафинирование методом замешивания флюса. Снимают покровный флюс, и на поверхность расплава насыпают свежий — 1 % от емкости тигля, расплавляют его и замешивают в металл на глубину ⅔ высоты тигля. При замешивании плавными движениями периодически добавляют свежий флюс. Температура расплава при рафинировании 700–720 ºС, продолжительность выдержки 5–7 мин. Последовательность операций: удаление использованного флюса и нанесение свежего; нагрев металла до температуры 750–780 ºС, отстаивание 10–15 мин и снижение температуры расплава до температуры заливки форм. Рафинирование считается законченным, когда поверхность металла имеет зеркально блестящий вид.
Контроль качества рафинирования производят по излому проб. Черные пятна в изломе указывают на загрязнение сплава оксида магния, а флюсовые включения имеют серый цвет.
Для более полного удаления водорода сплав обрабатывают гексахлорэтаном (C2Cl6) или продувают газами: азотом при температуре не выше 680–685 ºС для предупреждения образования нитрида магния; аргоном, хлором, гелием или углекислым газом при температуре 740–760 ºС в течение 15–20 мин.
Рафинирование фильтрацией. Применяют сетчатые фильтры из стали с ячейкой 1×1 мм, зернистые фильтры (магнезитовые, графитовые).
Рафинирование от примеси железа производят присадкой в перегретый расплав (800–850 ºС) марганца, циркония или титана в количестве 0,3–0,4 % от емкости тигля.
После выдержки расплава при температуре 700 ºС в течение 20–30 мин соединения железа оседают на дно тигля и сплав очищается до тысячных долей процента примеси железа.
Модифицирование магниевых сплавов Mg – Zn, Mg – P3M производят цирконием — 0,3–1 % от их массы.
Модифицирование сплавов Mg – Al – Zn осуществляют перегревом рафинированного расплава до 850–925 ºС, выдержкой в течение 10–15 мин, а затем быстрым охлаждением до температуры 680–720 ºС. Модификатором здесь служит соединение FeAl3, которое образуется за счет растворения железа тигля в перегретом расплаве.
При модифицировании сплавов Mg – Al – Zn углеродсодержащими веществами — магнезитом, мрамором, мелом, гексахлорэтаном — измельчение зерна происходит за счет образования мелкодисперсных частиц карбида алюминия, которые служат центрами кристаллизации.
Модифицирование сплавов Mg – Al – Zn – Mn и Mg – Mn производят хлорным железом в количестве 0,5–1 % при температуре 800–830 ºС и выдержке 10–15 мин.
Контрольные вопросы
1.Как подразделяют литейные алюминиевые сплавы по химическому составу?
2.Классификация алюминиевых сплавов в отливках по группам контроля.
3.Опишите процесс плавки алюминиевых сплавов.
4.Особенности рафинирования алюминиевых сплавов.
5.Чем и как модифицируют литейные алюминиевые сплавы?
6.Как производят плавку магниевых сплавов?
Глава 12. Заливка форм
12.1.Классификация способов заливки форм
итипов литниковых систем
Заливка форм — это процесс заполнения литейных форм расплавленным металлом. Различают свободную и принудительную заливку форм под давлением.
Свободная заливка литейных форм производится с помощью заливочных ковшей. Применяют также свободную заливку форм непосредственно из плавильных печей путем их поворота. При литье в песчаные формы преобладает свободная заливка литейных форм из ковша.
По месту установки форм перед заливкой различают следующие способы: на плацу (полу литейного цеха); стопочную заливку форм, когда они устанавливаются одна на другую и имеют общую литниковую чашу и стояк; заливку форм на конвейерах.
По емкости разливочные ковши подразделяют на ручные для заливки форм одним (до 15 кг) или двумя (до 60 кг) рабочими, монорельсовые и крановые.
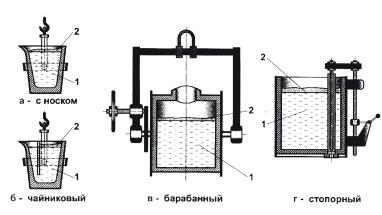
По конструкции различают следующие типы ковшей: заливочные ложки для малых доз металла, конические ковши, чайниковые, барабанные (цилиндрические и грушевидные) и стопорные (рис. 12.1).
Рис. 12.1. Типы крановых разливочных ковшей: 1 — жидкий металл; 2 — шлак
Для заливки легких цветных сплавов применяют нефутерованные ковши, которые изготавливаются из коррозионностойкой стали или титана. Стальные ковши, как правило, окрашивают огнеупорной краской, а титановые применяют без покрытий. Наиболее рационально применение титановых ложек и ковшей — они долговечнее, имеют меньшую массу и не требуют огнеупорной покраски.
Для заливки меди и медных сплавов предпочтительнее пользоваться графитовыми тиглями в качестве ковшей.
Ковши для заливки черных металлов изготавливают из листовой стали. Внутреннюю поверхность ковша, соприкасающуюся с жидким металлом, футеруют огнеупорными материалами. Крупные ковши футеруют огнеупорными кирпичами, а мелкие — набивными огнеупорными массами.
После футеровки ковши сушат, а затем прокаливают при температуре 700–900 ºС, в зависимости от заливаемого сплава.
Металл из плавильных печей выпускают в прокаленный ковш, температура которого должна быть не ниже 700–900 ºС для разливки стали и чугуна.
Температура футеровки ковша имеет важное значение для получения качественных отливок.
При выпуске металла из печи в неподогретый ковш происходит насыщение его газами, а из-за быстрого падения температуры расплава возможен брак отливок по недоливу тонких стенок. Кроме того, на стенках и дне ковша образуется слой застывшего металла (настыль). Образование настыли приводит к потерям металла и снижает стойкость футеровки разливочных ковшей.
При выпуске металла из печи в разливочный ковш в него попадает шлак, который всплывает на поверхность расплава.
Шлак на поверхности жидкого металла в ковше защищает его от окисления и снижает темп падения температуры расплава. Поэтому при заливке форм из чайниковых и стопорных ковшей шлак не снимают с поверхности расплава, так как в форму металл попадает чистым без шлаковых включений.
При заливке форм из носковых и барабанных ковшей необходимо шлак полностью снимать с поверхности металла с тем, чтобы он не попал в форму и не привел к браку отливок по шлаковым включениям.
При заливке цветных сплавов из печей, не имеющих механизма поворота, заполнение ковша расплавом производят методом зачерпывания, т.е. путем погружения ручных ковшей в жидкий металл.
При литье в песчаные формы их заполнение производят посредством литниковой системы.
В зависимости от расположения места подвода металла к отливке различают следующие типы литниковых систем: верхние, боковые, сифонные или нижние, ярусные, комбинированные
или этажные (рис. 12.2).
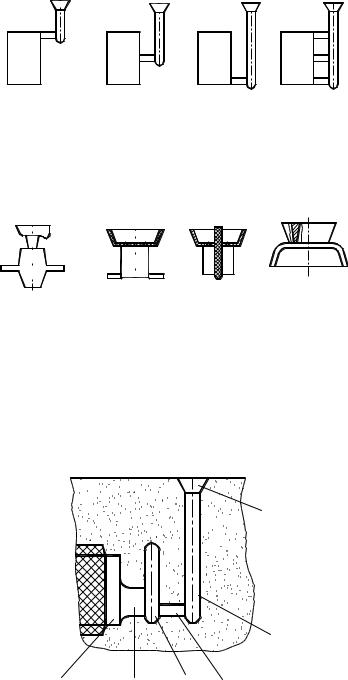
а) |
а)б |
вб) |
г) в) |
|
г) |
|
|
|
|
|
|
|
|
|
|
|
|
Рис. 12.2. Типы литниковых систем по расположению питателей относительно отливки:
а — верхняя; б — боковая; в — сифонная; г — ярусная
Верхние литниковые системы могут быть различного конструктивного исполнения. Схемы некоторых конструкций верхних литниковых систем показаны на рис. 12.3.
а) |
б)а) |
|
|
в) б) |
|
г) в) |
г) |
|
|
|
|
|
|
|
|
|
|
|
|
|
|
|
|
|
|
|
|
|
|
|
|
|
|
|
|
|
|
|
|
|
|
|
|
|
|
|
|
|
|
|
|
|
|
|
|
|
|
|
|
|
|
|
|
|
|
|
|
|
|
|
|
|
|
|
|
|
|
|
|
|
|
|
|
|
|
|
|
|
|
|
|
|
|
|
|
|
|
|
|
|
|
|
|
|
|
|
|
|
|
|
|
|
|
|
|
|
Рис. 12.3. Конструкции верхних литниковых систем: а — простая; б, в — дождевая; г — клиновая
Верхние литниковые системы отличаются простотой конструкции, малым расходом металла и обеспечивают направленность затвердевания отливок.
Вертикально-щелевые литниковые системы применяют для литья из алюминиевых сплавов цилиндрических и коробчатых тонкостенных отливок (рис. 12.4).
Боковые, нижние, ярусные и комбинированные литниковые системы, как правило, имеют несколько горизонтальных щелевых питателей с одним или несколькими шлаковиками на одном или разном уровнях. Иногда применяют заливку через два стояка.
6
5
1 |
2 |
3 |
4 |
Рис. 12.4. Схема вертикально-щелевой литниковой системы: 1 — отливка; 2 — щелевой питатель; 3 — колодец;
4 — горизонтальный питатель; 5 — стояк; 6 — литниковая воронка
12.2. Проектирование и расчет литниковых систем
При проектировании литниковых систем необходимо учитывать конфигурацию отливки, ее размеры и массу, а также свойства сплава и литейной формы.
При литье в песчаные формы скорость потока расплава, поступающего в полость отливки, должна быть минимальной, чтобы не размыть форму, и в то же время достаточной, чтобы обеспечить заполнение протяженных тонких стенок до момента потери металлом жидкотекучести, а при заливке массивных толстостенных отливок — до начала осыпаемости и растрескивания формы под воздействием высокой температуры поднимающегося зеркала жидкого металла. Для этой цели конструкция литниковой системы должна быть разветвленной, металл подводится в несколько
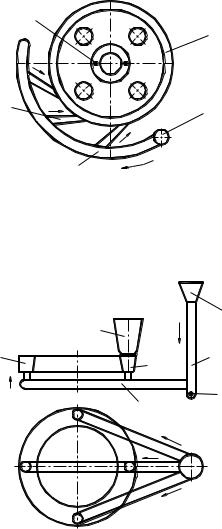
штабелей, направленных тангенсально или по касательной, чтобы струя расплава не ударяла в выступающие части формы или в стержни.
Схема тангенсального подвода питателей к отливке показана на рис. 12.5. Стрелки на рисунке указывают путь движения жидкого чугуна в шлакоуловителе и питателях.
5
1
4 |
2 |
3
Рис. 12.5. Схема литниковой системы для заливки чугунного шкива: 1 — отливка; 2 — стояк; 3 — шлакоуловитель;
4 — питатели (3 шт.); 5 — выпор (2 шт.)
При заливке массивных стальных деталей литниковую систему выполняют из специальных сифонных кирпичей и трубок (рис. 12.6).
|
2 |
|
7 |
1 |
3 |
|
6 |
|
4 |
|
5 |
4
Рис. 12.6. Схема литниковой системы для заливки стальной планшайбы (толщина кольца 300 мм; высота 400 мм):
1 — отливка; 2 — шамотная чаша; 3 — стояк, выложенный из шамотных трубок; 4 — шамотная звездочка; 5 — коллектор из шамотных кирпичей (3 шт.); 6 — питатели из шамотных кирпичей (4 шт.); 7 — прибыль
Металл из стопорного ковша поступает в литниковую систему, выполненную из шамота, и не оказывает воздействия на песчаную форму. При подводе металла в четыре питателя расплав равномерно снизу формы поступает в полость отливки.
Рассредоточенные литниковые системы с подводом металла снизу широко применяются для заливки черных и цветных сплавов.
Схема рассредоточенной нижней литниковой системы с заливкой через два стояка тонкостенных алюминиевых насосных колес показана на рис. 12.7.
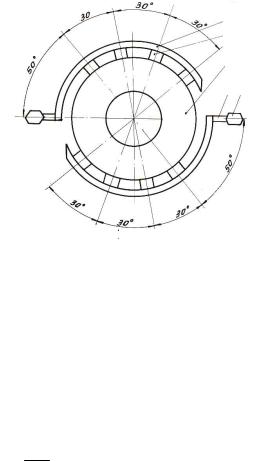
1
2
3
4 5
Рис. 12.7. Схема нижней литниковой системы с заливкой через два стояка алюминиевых насосных колес:
1 — коллектор (2 шт.); 2 — питатель (8 шт.); 3 — отливка; 4 — стояк (2 шт.); 5 — воронка (2 шт.)
При проектировании литниковых систем устанавливают место подвода металла к отливке, количество питателей и тип литниковой системы.
После этого производят расчет литниковой системы и определяют ее размеры. Расчет литниковой системы производят по ее наиболее узкому сечению F. Для отливок из чугуна и стали
наиболее узким сечением является суммарная площадь всех питателей ΣFпит, для алюминиевых сплавов — площадь нижнего основания стояка Fст.
Q F = Kυτ ,
где Q — масса отливки, кг; Кυ — массовая удельная скорость заливки, кг/(с·см2); τ — продолжительность заливки, с.
После определения площади узкого сечения литниковой системы определяют сечения остальных ее элементов по рекомендуемым для каждого сплава соотношениям:
ΣFпит : Fшл : Fст,
где Fшл — площадь шлакоуловителя или коллектора. Например, для чугуна рекомендуются следующие соотношения площади сечений:
ΣFпит : Fшл : Fст = 1,0 : 1,1 : 1,15.
12.3. Технологические режимы и техника заливки форм
Температура заливки форм определяет качество отливки: чистоту поверхности (наличие пригара, ужимин, утяжин поверхностных трещин, пористости); структуру отливки; образование внутренних дефектов; ликвацию; размер зерна; содержание газовых и неметаллических включений; механические и эксплуатационные свойства сплава.
Сплав сохраняет способность течь до температуры нулевой жидкотекучести, т.е. до тех пор, пока не образуется сплошной каркас кристаллов по всему сечению отливки.
Заливку песчаных форм из ковша производят при температуре выше ликвидус сплава с некоторым перегревом для обеспечения заполняемости протяженных тонких стенок отливки.
Температура заливки — это температура, при которой металл поступает в форму. Она равна температуре ликвидус сплава плюс перегрев, необходимый для обеспечения жидкотекучести расплава по каналам и полостям литейной формы. Чем выше перегрев сплава, тем больше его жидкотекучесть и способность заполнять тонкие стенки.
Температуру заливки песчаных форм выбирают в зависимости от типа и марки сплава, конфигурации отливки, ее размеров и массы (табл. 12.1).