
741
.pdf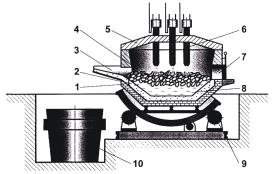
Плавка стали в дуговых печах состоит из следующих операций: заправка, загрузка шихты, плавление, доводка металла, раскисление и выпуск при заданной температуре жидкого металла в ковш.
К плавке необходимо подготовить шихтовые и шлакообразующие материалы, а к выпуску металла из печи — ковш.
Заправка — это операция восстановления поврежденных и оплавленных мест пода и откосов ванны печи и сливного желоба.
В процессе плавки под откосы ванны печи разъедаются металлом и шлаком, а стенки и столбики загрузочного окна оплавляются. Заправка производится после каждой плавки путем очистки от остатков шлака и металла углублений в подине и нанесения на эти места заправочной массы — магнезитового порошка при основной футеровке и кварцевого песка или молотого кварцита при кислой.
Рис. 9.1. Дуговая трехфазная плавильная печь:
1 — кирпичная кладка; 2 — набивная масса; 3 — желоб; 4 — шихта; 5 — свод; 6 — электроды; 7 — рабочее окно; 8 — жидкий металл; 9 — поворотный механизм; 10 — ковш
Загрузка печей емкостью 0,5 т производится вручную, а более 1,5 т — с помощью корзин с откидным дном. Для этого печи имеют механизм подъема и поворота свода. Правила загрузки шихты: под электроды укладывают куски электродного боя и известняк — это необходимо для обеспечения стабильного горения дуги в начальный момент; мелкие куски шихты (более 50 %) и стружку укладывают на под печи; крупные куски укладывают под электроды; средние куски и оставшуюся мелочь — сверху; известняк или известь — 1,5–2 % и около 1,0–1,5 % железной руды дают сразу в металлозавалку при основной футеровке печи для образования шлака.
Плавление шихты. В первые 10–15 мин рекомендуется пониженная мощность расплавления, пока не проплавятся колодцы в слое шихты; затем плавку ведут на максимальной мощности; за 30 мин до полного расплавления всей шихты частично снижают мощность; в конце расплавления устанавливают минимальную мощность для поддержания необходимой температуры жидкого металла.
Доводка металла, раскисление и выпуск из печи при заданной температуре определяются маркой стали и футеровкой печи.
В литейном производстве для плавки углеродистых и низколегированных сталей применяют преимущественно печи с кислой футеровкой, а для высоколегированных — только печи с основной футеровкой.
Преимущество печей с основной футеровкой заключается в том, что кроме выплавки высоколегированных сталей в них можно плавить углеродистые и низколегированные стали на некондиционной с повышенным содержанием вредных примесей и загрязненной шихте.
Особенности плавки углеродистой и низколегированной стали
вдуговых печах с кислой футеровкой
Впечах с кислой футеровкой можно получать сталь с меньшим содержанием FeO и газов, так как в кислом шлаке, содержащем 45–60 % SiО2, окислы FeO и MnO почти полностью связаны в силикаты. В результате возможен только переход FeO и MnO из металла в шлак. Для снижения вязкости шлака в процессе плавки дают железную руду, поэтому в случае скачивания окислительного шлака возможно удаление части фосфора. Кремний в кислой печи не угорает, а содержание углерода регулируют путем окисления его железной рудой.
После наводки нового шлака приступают к легированию и раскислению стали.
Никель, медь, ферромолибден обычно вводят в металлозавалку, а легкоокисляющиеся элементы вводят после расплавления шихты в жидкий металл. Феррохром вводят в расплав подогретым до температуры ~700 ºС.
После расплавления легирующих добавок производят предварительное раскисление стали ферромарганцем в количестве, обеспечивающем его заданное содержание в стали.
Окончательное раскисление производят при выпуске металла из печи на желобе или в ковше. Углеродистые стали раскисляют 0,1 % Al от веса жидкого металла, а низколегированные — комплексными раскислителями — силикокальцием, лигатурами Р3М и др.
Плавка стали в дуговой электропечи с основной футеровкой методом переплава
В качестве шихтовых материалов применяют отходы и возврат собственного производства высоколегированных сталей.
Расчет шихты производят достаточно точно с учетом угара элементов для данной печи и конкретной марки стали на основе опытных плавок.
При переплаве высоколегированных отходов общий угар металла составляет 3,3–10 %, а угар легирующих элементов будет разный: Si ~ 5 %; Mn ~ 20–30 %; Cr ~ 15 %.
Врезультате разного угара элементов для получения заданного химического состава стали в шихту вводят по расчету чистые металлы или ферросплавы.
Впроцессе плавления происходит окисление шихты и переход окислов металлов в шлак, а также интенсивное дымообразование. Бурый дым представляет собой взвешенные в атмосфере печи и уносимые вентиляцией в дымовую трубу газы и твердые частицы железа, окислов железа,
кремния, кальция, марганца. Размер твердых частиц дыма 0,05–1,0 мкм. Максимальное количество пыли в отходящих газах в начале плавления может составлять 0,045–0,1 г/м3. Для снижения окисления шихты в печь в процессе плавления вводят известь, шамот и плавиковый шпат.
Врезультате сокращается дымообразование. После расплавления всей шихты скачивают окисленный шлак и наводят новый, а иногда шлак не скачивают, а раскисляют его молотыми графитом, ферросилицием или порошкообразным алюминием. В результате раскисления шлака происходит восстановление легирующих элементов, а шлак приобретает белый цвет.
При плавке методом переплава без скачивания шлака необходимо применять шихтовые материалы с низким содержанием серы и фосфора.
Предварительное раскисление стали производят в электропечи ферромарганцем, ферросилицием и алюминием в количестве ~ 0,03–0,05 % от жидкого металла, а окончательное раскисление производят в ковше комплексными раскислителями — силикокальцием или церийсодержащими лигатурами.
Плавка стали в дуговой электропечи с основной футеровкой по технологическому процессу с окислением состоит из окислительного и восстановительного периодов.
По технологическому процессу с окислением выплавляют углеродистые, низколегированные и высоколегированные стали для получения высоких механических свойств за счет низкого содержания серы, фосфора, неметаллических включений, кислорода, водорода и азота.
Содержание углерода в шихте должно быть на 0,45–0,50 % выше заданного. Так как процесс плавки ведется с окислением, в качестве шихты используют углеродистый стальной лом и передельный чугун. Так, для выплавки шарикоподшипниковой стали в состав шихты вводят 30 % передельного чугуна.
Окислительный период начинается с процесса плавления шихты. Окисление шихты кислородом, содержащимся в газовой фазе рабочего пространства печи, происходит по реакциям:
Fe + ½ O2 = FeO;
Si + O2 = SiO2;
Mn + O2 = MnO;
C + O2 = CO2;
C + ½ O2 = CO.
В результате плавления образуется расплав металла и шлака. Расплав металла скапливается на подине печи, шлак находится над поверхностью жидкого металла, тем самым отделяет расплав от газовой атмосферы печи.
Шлак образуется в результате окисления элементов металлической шихты, разъедания материала футеровки и за счет растворения в нем извести, шамотного порошка и железной руды,
вводимой в печь для интенсификации окислительных процессов, а также плавикового шпата, вводимого в печь для снижения вязкости шлака.
В результате физико-химических процессов, происходящих при выплавке стали, шлак имеет в разные периоды плавки различный химический и минералогический состав.
Свойства шлака определяются его основностью, т.е. отношением процентного содержания оксида кальция к процентному содержанию кремния в шлаке, поверхностным натяжением, вязкостью и межфазным натяжением.
После образования слоя шлака над поверхностью металла кислород газовой фазы реагирует с закисью железа, содержащейся в шлаке:
3FeO + ½O2 = Fe3O4.
Образующаяся Fe3O4 растворяется в шлаке и при контакте с расплавом металла образует закись железа:
Fe3O4 + Fe = 4FeO.
FeO растворяется в расплаве и окисляет элементы стали:
FeO + С = СO + Fe;
FeO + Si = SiO2 + Fe;
FeO + Mn = MnO + Fe.
Окисление углерода — одна из важнейших реакций окислительного периода. В результате образования СО происходит «кипение» металла, способствующее выравниванию температуры расплава, удалению из него газов (азота и водорода) и неметаллических включений.
Окисление фосфора. Дефосфорация
Во время окислительного периода поверхность металла покрыта оксидами железа, поэтому окисление фосфора преимущественно происходит по реакции
2 P + 5 FeO = P2O5 + 5 Fe.
P2O5 переходит в шлак с образованием фосфатов: P2O5 + 3 FeO = 3 FeO · P2O5;
3 FeO · P2O5 + 4 CаO = 4 CaO · P2O5 + 3 FeO.
Необходимыми условиями для процесса дефосфорации являются: достаточное количество (~ 15 %) FeO в шлаке, что достигается загрузкой железной руды в печь в количестве 2–3 % от веса металлической шихты; высокая основность шлака — 2,5–2,8 %, для чего в печь вводят известняк в количестве 1,5–2 % от веса металлозавалки. Железную руду и известняк вводят вместе с шихтой или после начала плавления.
Для полноты удаления фосфора выполняют следующие технологические приемы: скачивание полностью или на 80 % шлака, образованного в процессе расплавления шихты, что предупреждает возможность восстановления фосфора и перехода его в металл; периодическое введение в печь порций руды и извести и скачивание шлака. Практически к концу окислительного периода можно получить сталь с содержанием Р < 0,005 %.
Влияние температуры
При выплавке низкоуглеродистой стали с содержанием углерода 0,1–0,2 % влияние температуры незначительно. Однако при выплавке средне- и высокоуглеродистых сталей повышение температуры стали снижает скорость дефосфорации: при температуре 1530 ºС содержание фосфора в стали составляет 0,027 %, а при 1475 ºС — 0,005 %. Поэтому для увеличения степени удаления фосфора плавку ведут на пониженной мощности печи.
В конце окислительного периода подачу железной руды в печь прекращают, когда содержание углерода в металле становится на 0,25–0,30 выше заданного в готовой стали, и скачивают окислительный шлак. После этого повышают температуру металла и наводят новый шлак из извести и плавикового шпата, при этом «кипение» металла продолжается 30–60 мин («безрудное кипение»), в результате FeO в шлаке снижается до 0,5–1,0 %.
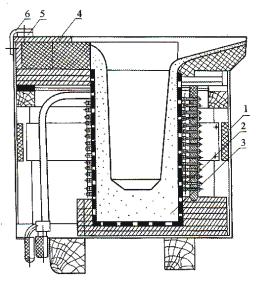
Восстановительный период, обессеривание и диффузионное раскисление
Для удаления серы необходимо хорошо растворимое в металле соединение FeS перевести в MnS с меньшей растворимостью в железе:
Fe S + Mn = Mn S + Fe.
Шлак должен иметь основность 2–3 при низком содержании FeO (~ 0,5 %). Для обессеривания требуется высокая температура металла и восстановительная среда. Для этого на поверхность шлака дают порошкообразные материалы с активными раскислителями: C, Al, Si.
Процесс обессеривания основан на переводе соединений FeS и MnS в нерастворимые соединения CaS:
FeS + CaO = CaS + MnО;
MnS + CаO = CaS + FeО.
Для раскисления шлака применяют углерод, кремний, алюминий и карбид кальция.
В результате восстановления Fe, Mn и Si из шлака переходят в металл, соответственно в шлаке снижается содержание SiO2, FeO, MnO, что способствует переходу окислов из металла в шлак.
Процесс удаления из металла окислов железа, марганца и т.д. и восстановления их в шлаке порошкообразными раскислителями получил название диффузионный метод раскисления.
9.3. Плавка стали в высокочастотных индукционных тигельных печах
Конструкция индукционной плавильной тигельной печи показана на рис. 9.2.
Рис. 9.2. Индукционная плавильная печь:
1 — каркас печи; 2 — индуктор; 3 — футеровка; 4 — верхняя плита; 5 — электроизоляционная прокладка; 6 — прижим
При выплавке углеродистых и низколегированных сталей применяют кислую, а высоколегированных сталей основную футеровку тигля.
Индукционные плавильные печи являются наиболее приемлемым агрегатом для плавки стали в литейном производстве благодаря следующим преимуществам: получение однородного по химическому составу металла с низким содержанием углерода, газов и неметаллических включений; легкость регулирования температурного режима плавки; низкий угар легирующих элементов; простота обслуживания и возможность выплавки разных по химическому составу сталей в одной печи в зависимости от потребности.
Особенность индукционной плавки — низкая активность шлака из-за низкой температуры на поверхности металла. Основная роль шлака в индукционной печи — защита металла от окисления и насыщения его газами.
При плавке стали в индукционных печах происходит интенсивное разрушение футеровки в результате электромагнитного перемешивания металла и продукты износа тигля непосредственно попадают в расплав. Наиболее интенсивно изнашивается основная футеровка при выплавке высоколегированных сталей.
Процесс плавки в индукционных печах состоит из следующих операций: подготовка шихты, расчет и навеска ее на плавку; подготовка шлакообразующих смесей; подготовка печи к плавке; загрузка и расплавление шихты; раскисление стали и выпуск ее в ковш при температуре, необходимой для заливки деталей.
Подготовка шихтовых материалов
Возврат собственного производства сортируется по маркам сталей и плавкам, а затем подвергается дробеструйной или дробеметной очистке.
Железо 003–008 ЖР, сталь 09, прокат легированных сталей разрезаются на куски длиной не более высоты тигля печи ~ 300–500 мм, которые по плавкам обрабатываются в дробеметных установках до полной очистки ржавчины и загрязнений.
Никель и медь электролитические разрезаются на куски размером 100×200 мм и прокаливаются при температуре ~700 ºC. Для ответственных марок сталей электролитические никель и медь, содержащие водород в количестве 1,5–3,0 см3/100 г, прокаливают в вакуумных печах.
Ферросплавы и лигатуры прокаливают при температуре до 700 ºC.
Алюминий и магний для раскисления переплавляют и заливают бруски размерами по дозе, необходимой для раскисления (100 или 200 г).
Известняк прокаливают при температуре 900–1100 ºС, а затем хранят в порошкообразном состоянии в термошкафах при температуре ~200 ºС непосредственно у плавильных печей.
Плавиковый шпат дробят на куски и хранят в сухом месте.
Магнезитовый порошок прокаливают при температуре 700–900 ºС. Его добавляют в шлак для увеличения вязкости (сгущения шлака).
Очистка, прокалка и хранение шихтовых материалов, исключающих попадание влаги в жидкий металл, позволяют получить концентрацию водорода в производственных плавках в пределах 0,55…2,3 см3/100 г. Такое количество водорода не оказывает влияния на образование пористости в стальных отливках и не приводит к снижению механических свойств стали.
Порядок загрузки шихты и режим плавки в печах
сосновной футеровкой
Вначальный период плавки в индукционных печах шихтовые материалы не защищены от контакта с атмосферой воздуха, поэтому они будут насыщаться газами , находящимися в ней.
Для уменьшения интенсивности окисления шихты и насыщения ее газами в период предплавления необходимо сокращать продолжительность расплавления, для чего следует: загружать шихту в предварительно подогретую печь; производить максимально плотную укладку шихты; так как в индукционных печах невозможно загрузить в тигель всю садку, то вначале необходимо загружать наиболее компактную шихту и шихтовые материалы, менее склонные к поглощению газов; после укладки на дно тигля мелкой шихты ее следует присыпать известью, чтобы уже первые порции жидкого металла были покрыты шлаком.
Для сокращения периода предплавления необходимо сначала прогреть шихту на пониженной мощности печи, а затем расплавление вести на максимальной мощности преобразователя. При этом необходимо использовать источники тока для печи емкостью 160 кг мощностью не менее 160 кВт, предпочтительнее — 320 кВт.
При плавке низкоуглеродистой хромо-никелевой стали сначала следует загружать в тигель 008 ЖР, медь, никель, ферромолибден, а после наплавления достаточного количества жидкого металла, покрытого слоем шлака, вводить подогретый феррохром в жидкий металл под слой шлака. Шлак хорошо защищает сталь от насыщения газами. При выдержке жидкой стали под слоем шлака при температуре 1600 ºС после расплавления всей шихты в течение 1 ч концентрация азота увеличивается с 0,061 % до 0,063 %, а после трехчасовой выдержки до 0,064 %.
После расплавления всей шихты и наплавления металла до верхнего витка индуктора сразу же снижают мощность печи, снимают весь шлак периода наплавления и наводят новый свежеобожженной известью с добавкой плавикового шпата.
Подвижный расплав шлака разъедает футеровку печи, поэтому в него добавляют магнезитовый порошок, затем дают выдержку металла под слоем шлака при выключенной печи.
Врезультате отстаивания расплава без электромагнитного перемешивания неметаллические соединения оксидов всплывают и связываются в шлаке в устойчивые соединения.
После отстоя металла поднимают его температуру, производят предварительное раскисление высоколегированных сталей ферромарганцем, ферросилицием и алюминием, а затем за 5–10 мин до выпуска металла из печи производят окончательное раскисление лигатурой ФС30Р3М30, что позволяет получать в сталях содержание кислорода 0,003–0,016 %.
Контрольные вопросы
1.Охарактеризуйте стали для изготовления отливок.
2.Опишите процессы плавки стали в дуговых печах.
3.Как готовятся шихтовые материалы для плавки стали в высокочастотных индукционных тигельных печах?
4.Какой порядок загрузки шихты и режим плавки в печах с основной футеровкой?
Глава 10. Плавка медных сплавов
10.1. Плавка чистой меди
Чистую медь используют при литье теплопроводящих изделий — фурм доменных печей и кислородных конверторов и токопроводящих деталей электрических машин.
Медь как литейный материал имеет низкие литейные свойства: плохую жидкотекучесть, большую линейную усадку ~ 2,1 %, большую объемную усадку ~ 11 %, высокую склонность к трещинообразованию и поглощению газов.
Все примеси снижают электропроводность меди и ее технологические и эксплуатационные свойства. К наиболее вредным примесям относятся висмут, свинец и кислород.
Висмут практически не растворим в твердой меди и располагается по границам зерен. При нагреве изделий выше 270 ºС прослойки висмута оплавляются и вызывают разрушение деталей при нагрузках, а при содержании более 0,001 % Bi медь становится хрупкой при холодной обработке.
Свинец вызывает красноломкость меди при нагреве выше 400 ºС.
Медь с кислородом при его содержании более 0,005 % образует эвтектику Cu – Cu2O, располагающуюся по границам зерен, хрупкие включения которой существенно снижают ее пластичность и делают склонной к «водородной болезни» — образованию трещин при работе в восстановительной атмосфере.
Растворимость водорода в жидкой меди составляет 6–8 см3/100 г и зависит от содержания в ней кислорода. Кислород снижает растворимость водорода в жидкой меди. Водород является вредной примесью, так как при затвердевании, выделяясь из пересыщенного раствора, вызывает образование газовой пористости и охрупчивание меди.
Плавку меди необходимо производить в индукционных высокочастотных печах с графитовым тиглем емкостью до 200–500 кг. В качестве шихты применяют катодную медь, возврат собственного производства, медный лом и переплав медной стружки и проводов.
Подготовка меди заключается в ее разрезке на куски, удобные для загрузки, очистки от загрязнений. Катодную медь обязательно прокаливают в открытой или в вакуумной печи при температуре 500–700 ºС, при этом удаляется ~80 % водорода и ~16 % кислорода от его исходного состояния.
Загрузку шихты производят в нагретый докрасна (~900 ºС) тигель, на дно которого загружают ¼ часть покровного флюса: прокаленного древесного угля, карбюризатора или графита. В процессе загрузки и плавления постоянно добавляют флюс, чтобы жидкий металл все время был закрыт слоем флюса. Углеродный флюс и графитовый тигель способствуют раскислению меди.
Вначале плавку следует вести на пониженной мощности печи, ~30 % для подогрева всей шихты, а затем переходить на максимальную мощность. После расплавления всей шихты температуру расплава поддерживают на пониженной мощности в пределах 1150–1210 ºС.
Повышение температуры выше 1200–1210 ºС недопустимо из-за увеличения растворимости водорода и интенсивного окисления меди при контакте с атмосферой воздуха. При температуре расплава ниже 1150–1160 ºС снижается жидкотекучесть меди.
Раскисление меди
По механизму действия раскислители подразделяют на поверхностные и объемные. Объемные раскислители вводят погружением в расплав. Углерод — наиболее эффективный раскислитель меди. Он восстанавливает окись и закись меди, а углекислый газ удаляется при этом из расплава.
Раскислителями меди являются P, Li, K, Sr, Al, Mg, Ba, Cr. Они связывают кислород в оксиды, которые трудно удалить, и медь загрязняется неметаллическими включениями.
Эффективным раскислителем является CaC2. Его вводят в расплав колокольчиком в составе флюса: 50 % CаС2, 35 % СаО и 15 % Na2CO3, — c наложением вибрации на тигель с жидкой медью в течение 20 мин. Образующийся жидкий шлак всплывает на поверхность металла, и медь не загрязняется неметаллическими включениями.
Вакуумная плавка чистой меди
При выплавке меди в вакуумных индукционных печах всю порцию шихты загружают в графитовый тигель и начинают откачку воздуха из печного пространства до 1–50 Па. В качестве шихты применяют катодную медь и возврат собственного производства.
Нагрев шихты ведут с небольшой скоростью ~20–60 ºС/мин, так как основное количество газов удаляется в интервале 500–1000 ºС и в момент плавления.
Плавление катодной меди сопровождается активным газовыделением, которое прекращается через 5–10 мин после полного расплавления шихты. Далее при остаточном давлении 1–10 Па дают изотермическую выдержку расплава при температуре 1350–1400 ºС в зависимости от емкости печи (250–1000 кг) 10–45 мин. В результате производится очистка меди от кислорода и водорода до ~ 1·10-5 %.
В процессе вакуумной индукционной плавки происходит очистка меди только от летучих примесей, например, Mg, Mn и др.
Основное назначение вакуумной плавки в литейном производстве состоит в удалении водорода и кислорода.
При вакуумной плавке заливку форм производят также в вакууме. Печи представляют собой вакуумные плавильно-заливочные установки.
Плавка в защитной атмосфере
Плавка в защитной атмосфере производится в открытых индукционных канальных печах (ИЛК). Слой жидкой меди, как и при обычной плавке, покрывают слоем прокаленного древесного угля, а затем на поверхность металла под крышку дают защитный газ.
Защитный газ получают в газогенераторах сжиганием твердого древесного угля, жидкого или газообразного топлива с последующей его очисткой. Основные компоненты защитного газа, получаемого в генераторах: CO + N2 (CO ~ 20–25 %).
Вкачестве защитной атмосферы применяют также азот и аргон с содержанием кислорода не
более 0,01 %. Применение защитной атмосферы позволяет получать медь с содержанием [О] ~ 4·10-4 % и [Н] ~ 8·10-4 %.
10.2.Плавка латуней
Впроизводстве коррозионностойких литых изделий применяют следующие марки латуней: ЛЦ16К4; ЛЦ40С; ЛЦ23А6Ж3Мц2 (гребные винты); ЛЦ38Мц2С2 (антифрикционные детали); ЛЦ4ОМцЗЖ (гребные винты).
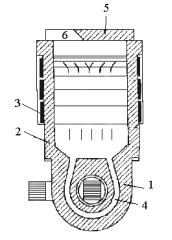
В качестве шихтовых материалов применяют первичные металлы: |
|
|
медь, цинк, свинец, марганец; возврат собственного производства; |
|
|
вторичные готовые сплавы соответствующих марок и латунный лом |
|
|
и стружку. |
|
|
Для плавки латуней применяют индукционные канальные печи |
|
|
(ИЛК). Устройство такой печи показано на рис. 10.1. Ванну печи |
|
|
выкладывают из шамотного кирпича, а канал футеруют кварцевым |
|
|
порошком на связке — борной кислоте 1–2 %. Широко применяются |
|
|
также индукционные тигельные печи. |
|
|
Особенностью плавки латуней является летучесть цинка |
|
|
(температура кипения 907 ºС). Угар цинка может достигать 0,5– |
|
|
5,0 %. Окись цинка не защищает сплав от окисления, поэтому плавку |
|
|
ведут под слоем флюса. |
|
|
Составы флюсов весьма разнообразны. Наиболее известно оконное |
|
|
стекло с добавлением разжижителей — буры, криолита, плавикового |
Рис. 10.1. Индукционная |
|
шпата. Применяют солевые флюсы: 60 % NaCl; 30 % Na2CO3; 10 % |
||
канальная печь для плавки |
||
Na3AlF6. |
||
металла: |
||
Часто применяют прокаленный древесный уголь без или в смеси с |
1 — канальная часть; |
|
покровными солевыми флюсами. |
2 — тигельная часть; |
|
При плавке латуней на дно прогретого тигля загружают |
3 — трехсекционная |
|
древесноугольный карбюризатор ~1 % от веса металлозавалки, медь |
индукционная катушка; |
|
4 — канал; 5 — крышка; |
||
и медный лом. После прогрева шихты в течение 10–15 мин печь |
||
6 — загрузочное отверстие |
||
включают на максимальную мощность, по мере расплавления жидкая |
|
медь должна быть покрыта флюсом. Расплав нагревают до температуры 1150–1200 ºС и раскисляют фосфористой медью из расчета 0,1 % от веса жидкой меди. После этого вводят чушки вторичной латуни, латунный лом, цинк.
Стружку смешивают с флюсом, насыпают на поверхность расплава и после прогрева замешивают в жидкий металл. Таким образом достигается минимальный угар стружки.
Легирующие элементы вводят в расплав или загружают в печь в начале плавки в виде лигатур Cu – Fe, Cu – Mn, Cu – Ni и т.п.
При расчете шихты следует учитывать требуемые эксплуатационные свойства деталей. Если необходимо иметь более высокую пластичность, то при расчете шихты принимают количество меди в ее составе, соответствующее верхнему пределу ее содержания в марке по ГОСТ или ТУ.
После расплавления всей металлозавалки доводят температуру металла до заданной в техпроцессе и выпускают сплав в ковш для заливки форм.
Если проведено раскисление меди фосфористой медью до ввода цинка, латунь окончательно не раскисляют.
Литейные свойства латуней можно улучшить путем регулирования содержания примесей. Добавка алюминия до 0,3 % и кремния до 0,3 % повышает жидкотекучесть латуни ЛЦ40С, при этом сумма примесей алюминия и кремния, равная 0,6 %, не превышает допустимого содержания примесей для данной марки латуни.
Добавка алюминия, но не выше 0,3 % его остаточного содержания в латуни, способствует также снижению угара цинка, пленка алюминия, покрывающая поверхность расплава, тормозит его испарение.
10.3.Плавка оловянистых бронз
Кнаиболее распространенным литейным оловянистым бронзам относятся следующие: Бр О3Ц7С5Н1, Бр О5Ц5С5 (герметичные и антифрикционные детали); Бр О4Ц4С17 (антифрикционные детали); Бр О1ОЦ2 (арматура и гребные винты); Бр О1ОФ1 (узлы трения с повышенным сопротивлением износу, шнековые приводы, венцы червячных колес).
Колокольная бронза содержит 20–22 % олова, не более 1–2 % примесей, остальное — медь. Оловянные бронзы имеют широкий интервал кристаллизации (150–200 ºС), что способствует
образованию в отливках рассеянной усадочной пористости, однако их относят к сплавам с хорошими литейными свойствами.
К наиболее вредным примесям в оловянных бронзах относятся алюминий и кремний. Сотые доли процента этих примесей снижают механические свойства и герметичность отливок.

Для плавки оловянистых бронз, особенно с высоким содержанием свинца, применяют высокочастотные индукционные печи с графитовым тиглем.
Вкачестве шихтовых материалов применяют чистые металлы, возврат собственного производства, лом оловянных бронз, стружку, вторичные готовые сплавы оловянных бронз, лигатуры и раскислители.
Вготовых сплавах оловянных бронз содержание цинка предусмотрено выше, чем требуется в литейной бронзе, на величину угара цинка при плавке.
Подготовка шихты заключается в очистке шихтовых материалов от загрязнений путем прокалки и пескоструйной обработки. Перед плавкой шихтовые материалы следует подогревать до температуры не ниже 150 ºС.
Подготовка тигля. Тигель перед плавкой очищают и подогревают до температуры не ниже 900 ºС.
Загрузка шихты. На дно тигля насыпают прокаленный древесный уголь, 1–2 % от емкости тигля, или древесноугольный карбюризатор, или графитовую крошку. Графитовый порошок хорошо защищает расплав от взаимодействия с атмосферой, но его сложнее снять с поверхности жидкого металла.
После засыпки углеродного флюса включают печь и прогревают флюс, а затем загружают шихтовые материалы с максимально плотной укладкой в объеме тигля.
Виндукционных печах вся металлозавалка не помещается в тигель при первоначальной загрузке, поэтому по мере расплавления шихты периодически производят ее догрузку.
Расплавление шихты вначале производят на пониженной мощности (30–50 %) печи для равномерного прогрева всей первоначальной порции металлозавалки. После этого печь включают на максимальную мощность до конца расплавления всей навески шихты, соответствующей емкости печи.
Зеркало расплава должно быть постоянно покрыто слоем защитного флюса, а продолжительность плавки должна быть минимальной для сокращения потерь металла на угар.
Для оловянистых бронз, содержащих цинк, применяют углеродный флюс с добавлением оконного стекла и буры (0,1–0,2 %).
Влитейном производстве применяют, как правило, плавку на чистых шихтовых материалах с использованием возврата, стружки и лома, суммарное количество которых в металлозавалке может составлять от 20 до 80 % в зависимости от требований, предъявляемых к качеству отливок.
Плавку оловянистых бронз начинают с расплавления меди и ее раскисления фосфором. Потребность фосфора для раскисления в 1,8 раза меньше процентного содержания кислорода в жидком металле.
При плавке в индукционных печах содержание кислорода при температуре 1200 ºС может быть
впределах 01–0,04 %, на что потребуется 0,005–0,02 % фосфора для образования соединения 2CuO2P2O5, которое в жидком виде переходит в шлак. После раскисления жидкой меди в печь загружают отходы, цинк и олово.
Врасплаве оловянистых бронз кроме Cu2О образуются оксиды цинка и олова. Наличие включений оксидов цинка и олова заметно снижает механические и эксплуатационные свойства бронз.
Для оловянистых бронз фосфор является хорошим раскислителем. Его применяют в виде лигатуры — фосфористой меди, содержащей от 7 до 10 % фосфора. Зная содержание кислорода в расплаве [О], можно определить количество фосфористой меди МФ для раскисления расплава:
МФ = [Î ] |
Q |
, |
|
α |
|||
1,8 |
|
где Q — масса расплава (емкость печи), кг; α — содержание фосфора в лигатуре медь — фосфор, %.
Для раскисления 400 кг расплава бронзы, содержащего 0,04 % кислорода, потребуется фосфористой меди (8 % Р):
МФ = 0,04 400 =1,11 кг. 1,8 8
Так как олово является дорогостоящим металлом, раскисление меди производят перед введением олова. Фосфор с окисью цинка в расплаве бронзы образует жидкий продукт 3ZnO · Р2О5, который легко удаляется из металла в шлак.
Рафинирование меди от водорода производят различными методами: фильтрацией; продувкой осушенными газами — азотом и аргоном; обработкой расплава хлористыми солями — ZnCl2, MnCl2, C2Cl6 в количестве 0,1–0,5 % от массы расплава.
10.4.Плавка безоловянистых бронз
Кнаиболее распространенным литейным безоловянистым бронзам относятся: Бр А9Мц2Л, БрА9Ж3Л, БрА10Ж4Н4Л (судовая арматура, антифрикционные детали); БрС3О (антифрикционные биметаллические со сталью детали дизелей).
Высокосвинцовые бронзы плавят в индукционных печах высокой или промышленной частоты для интенсивного перемешивания расплава. Количество возврата и отходов не должно превышать 50 % массы металлозавалки. Плавку ведут под слоем покрывного углеродсодержащего флюса.
Основной дефект отливок — ликвация по плотности. Чем интенсивнее перемешивание расплава, тем мельче включения свинца и мельче ликвация. Быстрое охлаждение отливок способствует уменьшению ликвации свинца в бронзе.
Плавку алюминиевых бронз ведут в индукционных печах с графитовым тиглем под защитой покровных флюсов. Составы солевых флюсов разнообразны. Эффективно применение углеродосодержащего флюса с добавлением солесодержащих составов, включающих криолит, плавиковый шпат и поваренную соль.
При плавке на чистых шихтовых материалах сначала расплавляют медь, раскисляют ее фосфористой медью, затем в несколько приемов вводят алюминий, после расплавления алюминия вводят железо.
Чем выше содержание алюминия, тем выше прочность и ниже пластичность и литейные свойства бронзы.
Алюминиевые бронзы склонны к пленкообразованию.
При плавке основное внимание уделяют защите расплава от окисления.
Раскисление алюминиевых бронз производят активными раскислителями — магнием, литием 0,5 % и цирконием до 0,2 % от массы расплава.
Рафинирование алюминиевых бронз производят продувкой осушенными газами, фильтрацией или обработкой хлорными солями — С2Cl6, MnCl2.
Модифицирование алюминиевых бронз производят ванадием, вольфрамом, бором, цирконием или титаном в количестве 0,05–0,15 % от массы сплава.
Контрольные вопросы
1.Опишите процессы плавки меди.
2.Охарактеризуйте процесс плавки латуни.
3.Особенности плавки оловянистых бронз.
4.Опишите процесс плавки безоловянистых бронз.
Глава 11. Плавка алюминиевых
имагниевых сплавов
11.1.Общие сведения об алюминиевых литейных сплавах
Литейные алюминиевые сплавы по химическому составу подразделяют на пять групп.
I группа — это сплавы на основе системы Al – Si – Mg: АК 12 (АЛ 2), АК 13, АК 9, АК 9с, АК 9ч (АЛ 4), АК 9пч (АЛ 4 – 1), АК 8л (АЛ 34), АК 7, АК 7ч (АЛ 9), АК 7пч (АЛ 9 – 1), АК 10 Су, где А — означает алюминиевый сплав; К — кремний; цифры после буквы К — среднее содержание кремния в сплаве. Малые буквы означают чистоту сплава по содержанию вредных примесей: ч — чистый; пч — повышенной чистоты; оч — особо чистый; с — селективный, л — литейный сплав.