
741
.pdfТипы термопреобразователей для измерения температуры жидких металлов
|
|
|
|
Диапазон измерений, |
|
|
|
|
|
|
ºС |
|
термопреобра- |
зователя |
Материалы |
|
|
Тип |
термопреобразователя |
кратковременный |
длительный |
||
|
|||||
|
|
|
|
|
|
|
|
|
Вольфрам–рений (5 % |
|
|
|
|
|
рения) |
|
|
|
ТВР |
Вольфрам–рений (20 % |
2500 |
0–2200 |
|
|
|
|
рения) |
|
|
|
|
|
ВР 20/5 |
|
|
|
|
|
|
|
|
ТПР |
|
Платино–родий (30 % родия) |
|
|
|
|
Платино–родий (6 % родия) |
1800 |
300–1600 |
||
|
|
|
ПР 30/6 |
|
|
|
ТПП |
|
Платино–родий (10 % родия) |
1600 |
0–1300 |
|
|
Платина |
|||
|
|
|
|
|
|
|
ТХА |
|
Хромель–алюмель |
1300 |
–200–1000 |
|
ТХК |
|
Хромель–копель |
800 |
–200–600 |
Таблица 7.3
Пирометры для измерения температуры жидкого металла
|
Диапазон |
|
|
|
Тип |
измерений, |
Погрешность |
Примечание |
|
|
оС |
|
|
|
|
|
|
Величина поправки, оС |
|
Оптический |
1200–2000 |
30 % |
(1200–1300) – 100 |
|
ОППИР-017 |
1400–130 |
|||
|
|
|||
|
|
|
1500–150 |
|
Радиационный |
|
|
|
|
РАПИР с |
400–2500 |
3 % от верхнего |
Вторичный прибор |
|
телескопом ТЕРА- |
предела |
КСП — 2, 3, 4 |
||
|
||||
150 |
|
|
|
|
ФЭП-4М |
|
± 1 % от |
|
|
Объективы с |
800–1300 |
Большие габариты, |
||
фокусным |
верхнего предела |
стационарность |
||
850–1400 |
||||
расстоянием |
шкалы |
установки |
||
|
||||
100, 125, 152, 200 |
|
|
|
Перед погружением термоэлемента в жидкий металл его защищают чехлом из огнеупорного
материала.
Контроль температуры жидкого металла производят в процессе плавки и перед выпуском металла из печи в ковш. Непрерывность контроля жидкого металла осуществляют путем установки термопары в футеровку печи.
Основным методом контроля химического состава литейных сплавов является спектральный с использованием оптических квантометров ДФС-36 и других типов. Содержание углерода в сталях и чугунах определяется с помощью экспресс-анализатора типа АН-7529.
Содержание кислорода в меди определяют методом металлографического анализа. Растворенный в жидкой меди кислород при затвердевании раствора выделяется и, взаимодействуя с медью, образует эвтектику Cu – Cu2O. При увеличении × 200 в поляризованном свете закись меди приобретает рубиновый цвет. Металлографический метод позволяет определить содержание кислорода до 0,01–0,15 %.
Более точно определяют содержание газов методом восстановительного вакуумного плавления, например, на приборе С-911М. Точность определения кислорода 0,001–0,0003 %.
Содержание газов определяют также методом плавления в токе инертного газа и методом спектрального анализа.
Широко используются экспресс-методы определения содержания кислорода с помощью приборов, измеряющих ЭДС расплава. При увеличении содержания кислорода в расплаве ЭДС падает.
Термографические методы химического анализа основаны на записи кривой охлаждения сплава. Контроль фазового состава сталей мартенсито-аустенитного класса в процессе плавки производят путем заливки и быстрого охлаждения проб и замера магнитной индукции холодных проб на приборе ИФСС-1 (МКЛ) конструкции ВИАМ. По показаниям прибора корректируется фазовый состав стали таким образом, чтобы в отливке содержание аустенита составляло 25–30 %.
При заливке проб с последующим термостатированием их при 268 ºС и замере индукции «горячей» пробы можно установить наличие δ-феррита. Прибор показывает «0» при отсутствии δ- феррита.
Для контроля качества металла по ходу плавки заливают различного типа технологические пробы.
Пробы в виде брусков позволяют визуально определить загазованность сплава, и по излому можно определять в сталях содержание углерода. В чугунах по структуре излома можно определить тип чугуна — белый, серый, ферритный и т.д.
Для определения газосодержания в алюминиевых сплавах используют метод заливки проб — лепешек из стержневой смеси или вакуум-проб конической формы, заливаемых в металлическую форму.
Качество модифицирования алюминиевых сплавов оценивают по излому клиновой пробы. Склонность чугуна к отбелу определяется заливкой клиновых проб в стержневые формы с
металлической плитой.
Таким образом, при плавке сплавов контролируют их химический состав, структуру, содержание газов и заливают образцы для определения механических свойств.
7.5.Шихтовые материалы
Вкачестве основных шихтовых материалов применяют:
–первичные, получаемые из руд, которые являются основой или легирующим компонентом сплава, — железо, чугун, алюминий, медь, магний и др.;
–вторичные, получаемые из отходов и лома черных и цветных металлов, — чушки вторичных цветных металлов и готовых сплавов.
Ферросплавы — сплавы железа с другими химическими элементами, применяемые для легирования и раскисления железоуглеродистых сплавов: феррохром, ферромарганец, ферросилиций
идр., получаемые из руд в ферросплавных печах или домнах.
Лигатуры — сплавы, состоящие из основного одного или нескольких легирующих компонентов, являющихся летучими и тугоплавкими: алюминий – бериллий, алюминий – марганец, медь – фосфор, никель – магний, железо – кремний – магний – церий и др.
Лом черных и цветных металлов и сплавов — детали машин, рельсы, трубы и т.д.
Отходы собственного производства — литники, выпоры, прибыли, бракованные отливки, стружка и т.п.
В литейном производстве отходы собственного производства подразделяют на используемые и неиспользуемые.
Неиспользуемые отходы литейного производства в приготовлении литейных сплавов не применяют, их сдают на переработку.
Металлозавалка — это масса основных шихтовых материалов Мш, необходимых для получения годной отливки с литниково-питающей системой.
Годной отливкой (годным литьем) называется отливка, отвечающая требованиям технических условий и сдаваемая из литейного цеха на продажу.

Массой отливки (черной массой) Мо называется масса отливки с учетом припусков на механическую обработку. Литники и прибыли в массу отливки не включают.
Массой литой детали (чистой массой) Мд называется масса готовой детали, изготовленной из отливки.
Выходом годных отливок Г, %, называется отношение массы годных отливок к массе металлозавалки, выраженное в процентах.
Безвозвратными потерями называются неизбежные потери металла при производстве отливок: угар, потери металла при газовой и электродуговой резке, унос металла со шлаками и фильтрами.
При расчете шихты необходимо знать массу шихты с учетом безвозвратных потерь и количество собственного возврата.
Методика расчета шихты
Для расчета шихты необходимы следующие данные: химический состав сплава и шихтовых
материалов, угар отдельных элементов сплава и количество возврата собственного производства.
Расчет шихты ведут на 100 кг готового сплава и принимают оптимальный состав сплава, а
затем рассчитывают необходимое количество элемента, которое нужно ввести в сплав с учетом
угара, данные заносят в таблицу. Пример расчета шихты для выплавки бронзы Бр05Ц5С5
приведен в табл. 7.4.
Таблица 7.4
Пример расчета шихты для выплавки бронзы БрО5Ц5С5
Химический состав сплава, % |
Sn |
Zn |
Pb |
Cu |
Всего |
Содержание компонентов в сплаве |
5 |
5 |
5 |
85 |
100 |
Масса компонентов на 100 кг сплава |
5 |
5 |
5 |
85 |
100 |
Угар, % |
1 |
2 |
2 |
1 |
– |
Угар, кг |
0,05 |
0,1 |
0,1 |
0,85 |
1,1 |
Расчетная масса шихты, кг |
5,05 |
5,1 |
5,1 |
85,85 |
101,1 |
Содержание в возврате (40 %), кг |
2,0 |
2,0 |
2,0 |
34 |
40 |
Содержание свежих металлов (60 %), кг |
3,05 |
3,10 |
3,10 |
51,35 |
61 |
Объем возврата в шихте принимают из условия его полного использования на основе расчета его количества, образующегося в производстве.
Недостающее количество шихты восполняется свежими материалами. В данном примере необходимо приобрести олова — 3,05 кг, цинка — 3,1 кг, свинца — 3,10 и меди — 51,35 кг.
Определенное расчетом количество шихты увеличивают до емкости тигля или ванны печи. При емкости печи 500 кг необходимо приготовить шихту:
возврат — 40 · 5 = 200 кг; олово — 3,05 · 5 = 15,25 кг; цинк — 3,1 · 5 = 15,5 кг; свинец — 3,1 · 5 = 15,5; медь — 51,85 · 5 = 259,25.
Всего на одну плавку требуется 525,5 кг металлической шихты, для раскисления которой необходимо
525,5 · 0,1 = 0,5255 кг фосфористой меди.
100%
Общий вес металлозавалки составит
525,5 + 0,52 = 526,02 кг.
В отдельных случаях проводят проверочный расчет шихты на количество вредных примесей, внесенных в сплав шихтовыми материалами.

Контрольные вопросы
1.Опишите технологический процесс плавки литейных сплавов.
2.Какие взаимодействия происходят при плавке металлов?
3.Какие происходят взаимодействия жидких металлов с материалами тиглей и футеровкой плавильных печей?
4.Как контролируют температуру жидкого металла и его качество?
5.Какие применяют шихтовые материалы и как рассчитывают шихту?
Глава 8. Плавка чугуна
8.1. Основные сведения о чугунах
Чугуны — это сплавы железа с углеродом (~ от 2,0 % С до 6,67 % С).
Общий углерод Собщ — это общее содержание углерода в чугуне, определяемое химическим анализом:
Собщ = Сгр + Ссв,
где Сгр — свободный углерод — включения в виде графита; Ссв — углерод связанный или находится
втвердом растворе в химических соединениях, карбидах (например, цементит Fe3C).
Вкаком виде находится углерод, зависит от условий охлаждения и химического состава чугуна. При медленном охлаждении или при нагреве чугуна происходит распад цементита с выделением углерода в виде графита. Этот процесс получил название графитизации чугуна и характеризуется степенью графитизации СГ. Графитизация происходит в две стадии:
на I стадии СГ изменяется от 0 до 1,
Ñãð
СГ = ; Ñîáù − Ññâ
на II стадии СГ изменяется от 1 до 2,
СГ = 2 – Ññâ .
Ñãð
Железо с углеродом образуют твердые растворы с ограниченной растворимостью — феррит и аустенит.
Содержание углерода ~ 4,3 % соответствует эвтектическому составу чугуна, при этом образуется ледебурит (аустенит + цементит) или аустенито-графитовая эвтектика. После эвтектоидного превращения в структуре чугуна будут присутствовать феррит и перлит.
Чугуны классифицируют в зависимости от общего содержания углерода на эвтектические ~ 4,3 %, С, доэвтектические — до 4,3 % С и заэвтектические — св. 4,3 % С.
Доменные чугуны, используемые для изготовления отливок, кроме углерода содержат постоянные элементы: кремний, марганец, — и примеси: серу, фосфор, которые различным образом влияют на структурообразование чугунов, а также легирующие добавки, вводимые для изменения тех или иных их свойств.
По степени влияния на процесс графитизации химические элементы: Si, Al, C, Ti, Ni, Cu, P, Zr, [Nb] W, Mn, Cr, V, S, Mg, Ce, Te, B до ниобия включительно, — являются графитизирующими, а после ниобия — антиграфитизирующими.
Кремний и фосфор оказывают сильное влияние на положение эвтектической точки чугуна. Это влияние характеризуется углеродным эквивалентом Сэ и степенью эвтектичности Sэ:
Сэ = С + 0,3 (Si + P); Sэ = |
|
Ñ |
. |
|
− 0,3(Si+ P) |
||
4,3 |
|
По виду высокоуглеродистой фазы (цементит, графит + цементит) чугуны классифицируют на белые (БЧ), половинчатые, отбеленные (ОЧ) и графитизированные: серые (СЧ, рис. 8.1), вермикулярные (ЧВГ, рис. 8.2), ковкие (КЧ, рис. 8.3), высокопрочные с шаровидной формой графита (ВЧШГ, рис 8.4).
При этом матрица может иметь различные виды структуры: феррита — Фе; перлита пластинчатого — Пт1; перлита зернистого — Пт2; троостита — Тр; бейнита — Б; мартенсита — М (рис. 8.5).
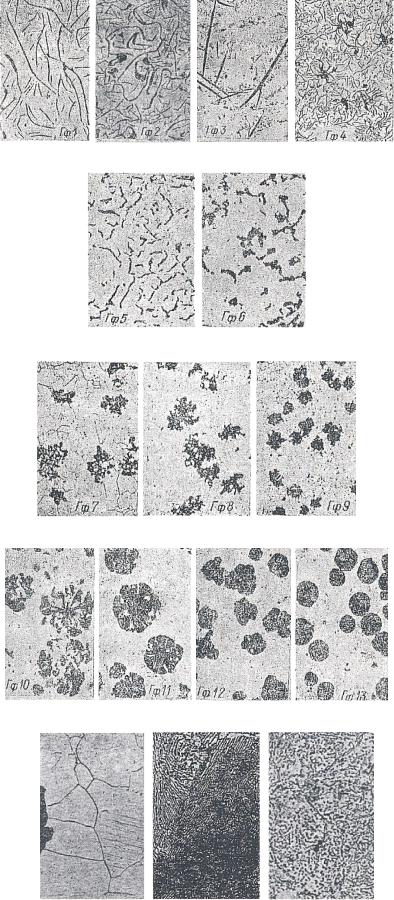
Рис. 8.1. Пластинчатая форма графита
Рис. 8.2. Вермикулярная форма графита
Рис. 8.3. Форма графита в ковких чугунах
Рис. 8.4. Шаровидная форма графита в высокопрочных чугунах
Фе |
Пт1 |
Пт2 |
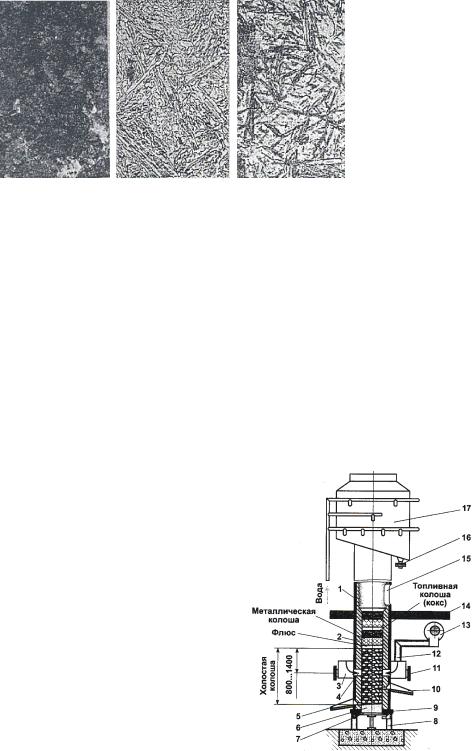
Тр |
Б |
М |
Рис. 8.5. Основные типы металлической основы чугунов:
Фе — феррит; Птl — перлит пластичатый; Пт2 — перлит зернистый; Tр — троостит; Б — бейнит; М — мартенсит
Маркировка чугунов
Вчертежах на литые детали в марке серых и высокопрочных чугунов цифра означает минимальное для данной марки значение предела прочности при растяжении в кг/мм2. Например:
СЧ10 — означает «чугун серый, имеющий предел прочности не менее 10 кг/мм2 (100 МПа)»;
ВЧ60 — означает «чугун высокопрочный с шаровидной формой графита, должен иметь прочность не менее 60 кг/мм2 (600 МПа)».
Вчугунах КЧ после букв указывают две пары цифр: первая — это предел прочности при разрыве в кг/мм2; вторая — относительное удлинение в процентах. Например:
КЧ37-12 — означает «ковкий чугун и имеет предел прочности при разрыве 37 кг/мм2 (370 МПа) и относительное удлинение 12 %».
8.2. Устройство и работа коксовой вагранки
Вагранка — это шахтная печь, предназначенная для плавки чугуна из металлической шихты. По виду топлива вагранки бывают коксовые, коксогазовые и газовые.
Устройство коксовой вагранки показано на рис. 8.6. Шахта печи обрамлена стальным кожухом — 1, футерованным внутри шамотным или динасовым кирпичом — 2. Распределительная коробка 3 служит для подвода воздуха к фурмам 4. Слив чугуна производят через желоб 5. Лещадь 6 заформовывают смесью перед каждой плавкой. Шахта вагранки имеет откидное днище 7, опорные колонны 8 и подовую плиту. Шлак выпускают через желоб 10. В зависимости от диаметра вагранки имеют 6–10 фурм.
Наблюдение за работой ведут через смотровые окна 11. Воздух в распределительную коробку подают посредством трубопровода 12 от вентилятора 13.
Для обслуживания вагранки имеется шихтовая площадка 14 и загрузочное окно 15. Рукава 16 предназначены для
удаления шлама, который осаждается в мокром
Рис. 8.6. Устройство коксовой вагранки
пылеосадителе 17.
Вагранки строят: с подогревом воздуха, без подогрева воздуха, с обогащением воздуха кислородом, с одним или двумя рядами фурм.
Воздухонагреватели или рекуператоры подогревают теплом отходящих из вагранок газов или сжиганием дополнительного топлива.
Жидкий чугун выпускают в ковш, копильники или миксеры.
Копильники бывают стационарными и передвижными поворотными — миксерами с индукционным или газовым обогревом жидкого чугуна.
Ремонт и подготовка вагранки к плавке заключаются в полной или частичной замене футеровки шахты. Толщина футеровки из шамотного кирпича для вагранок без водяного охлаждения кожуха составляет 120–180 мм. Верхняя часть шахты в районе загрузочного окна выполняется из чугунных кирпичей.
Взоне фурм и горна текущий ремонт производят после каждой плавки. После ремонта шахты закрывают дно вагранки и набивают подину формовочной смесью.
На подину укладывают дрова, загружают часть холостой колонии и производят розжиг кокса дровами или газовой горелкой. После того, как кокс у рабочего окна разгорелся, горелки переставляют в фурмы и следят, чтобы он равномерно разгорался по всему сечению шахты.
После розжига первой порции холостой колоши загружают вторую. Розжиг завершается продувкой воздухом холостой колоши и замером ее высоты, которая должна быть на 800–1400 мм выше уровня фурменного пояса. После этого заделывают рабочее окно.
Продолжительность розжига холостой колоши составляет 3–4 ч.
Перед подачей дутья заделывают чугунную летку глиной, а шлаковую — формовочной смесью. Загрузку первого столба шихты производят так, чтобы масса металлозавалки первых четырех-пяти колош была на 20 % меньше, а количество стального лома в ней было в 1,5–2,0 раза больше расчетной
величины. В пятую колошу загружают двойную порцию кокса.
Дутье в вагранку подается сразу после загрузки первого столба шихты. При этом рекомендуется давление воздуха до появления первых капель чугуна у фурм устанавливать на 40–50 % меньше оптимального значения.
Взависимости от конструкции вагранки при ее нормальной работе первый выпуск металла можно производить через 15–40 мин после появления первых капель чугуна у фурм. При выпуске чугуна кратковременно уменьшают давление воздуха во избежание выброса металла после открытия летки.
Управление работой вагранки в период плавки заключается в своевременном выпуске чугуна и шлака, поддержании постоянного уровня столба шихты в бесперебойной подаче дутья.
Загрузку вагранки производят наклонными скиповыми подъемниками. В ковш подъемника загружают все компоненты шихты: металл, флюсы, кокс и ферросплавы.
Длительность плавки в коксовых вагранках составляет от одной-двух смен до пяти-шести суток, в зависимости от потребности в чугуне и принятого режима работы литейного цеха.
Окончание плавки начинают с прекращения загрузки шихты и постепенного снижения давления дутья в фурменной коробке. Затем выпускают весь металл и шлак, открывают откидное днище.
Остатки золы и шлака кокса самопроизвольно проваливаются из шихты на пол цеха между опорными колоннами. После остывания внутреннего пространства шахты приступают к ремонту вагранки и подготовке ее к следующей плавке, как правило, это делают через сутки.
8.3.Физико-химические процессы плавки чугуна
вкоксовой вагранке
Горение топлива происходит в зоне фурм по реакциям:
С+ О2 = СО2 + 393,8 кДж;
С+ ½ О2 = СО + 110, 6 кДж; СО + ½ О2 = СО2 + 283,2 кДж.
Максимальная температура поверхности горящего топлива ~1600 ºС находится на высоте ~300 мм над уровнем фурм при расходе кокса 10 % от металлозавалки и температуре вдуваемого воздуха 450 ºС.
На высоте 600–800 мм над уровнем фурм температура на поверхности горящего кокса составляет ~1400 ºС. Основным продуктом горения является СО2, который поднимается вверх шахты и восстанавливается углеродом кокса:
СО2 + С = 2СО – 172,6 кДж.
Реакция прекращается при температуре на поверхности кокса ~1000 ºС.
Для условий расхода 10 % кокса и температуры воздуха 450 ºС в отходящих газах из вагранки содержится 10–16 % СО и 10–14 % СО2.
Последовательность процесса плавки чугуна в вагранке можно разделить на зоны по высоте шахты:
нагрева шихты до температуры плавления; плавления; перегрева жидкого чугуна; охлаждения металла (горн).
Повысить температуру металла в вагранке можно путем увеличения расхода кокса, объема дутья температуры воздуха, обогащением воздуха кислородом.
Испарение влаги шихты происходит в верхней части шахты.
Диссоциация известняка происходит интенсивно при температуре 900–1000 ºС:
СаСО3 = Са О + СО2.
СО2 удаляется из шахты с отходящими газами, а СаО участвует в процессе шлакообразования.
Шлакообразование. Ввод СаСО3 и образование СаО способствуют образованию подвижного низкоплавкого шлака. В зависимости от футеровки печи состав шлака должен иметь разное соотношение суммы СаО + MgO и SiO2. Это соотношение характеризует основность шлака. Для кислого процесса оно находится в пределах 0,4–0,9, а для основного 1,3–2,0.
Количество шлака зависит от количества вводимого известняка и составляет при кислом процессе 5–8 %, а при основном 8–10 % от массы чугуна. СаО связывает в шлак золу кокса и окислы MnО, FeO, SiO2, Al2O3 и др. Для снижения вязкости шлака и повышения его активности в шахту вагранки добавляют плавиковый шпат CnF2.
Состав шлака в процессе плавки изменяется с повышением температуры металла: в нем уменьшается количество FeO и MnO.
Легирующие элементы Cr, Ni, Cu, Ti, Mo, как правило, вводят в жидкий чугун для стабилизации его химического состава и уменьшения угара этих элементов.
Угар элементов при плавке в вагранке зависит от многих факторов: стабильности состава шихты, дутья, температуры металла.
8.4. Модифицирование чугуна
Модифицирование серого чугуна производят графитизирующими модификаторами для измельчения пластинчатого графита, устранения отбела и образования междендритного графита.
В качестве графитизирующих модификаторов применяют ферросилиций ФС 75, силикокальций, графит черный и разнообразные лигатуры, которые кроме кремния содержат следующие элементы: Al, Zr, Ba, Sr, P3M и др. Для получения перлитной структуры серого чугуна вводят модификаторы: Sn, Sb, N2 и др.
Каждый тип графитизирующего модификатора имеет определенный срок действия, т.е. если разлить металл в формы позднее, то модифицирования сплава не произойдет. Срок действия модификатора составляет 5–15 мин.
Для повышения эффекта модифицирования применяют следующие способы ввода модификаторов: в ковш при заполнении его металлом из печи, на желоб плавильной печи; через промежуточный ковш
— растворитель модификатора, поступающего из дозатора; методом погружения модификатора в ковш; в литниковую чашу специальной конструкции; непосредственно в карман, устроенный в литниковой системе.
Контроль качества модифицирования производят по излому клиновидной пробы, заливаемой через определенный промежуток времени.
Модифицирование ковкого чугуна
Химический состав белого чугуна для получения ферритного ковкого чугуна КЧ 36-6, КЧ 33-8, КЧ 35-10, КЧ 37-12: C 2,4…2,9; Si 1,0…1,6; сумма C + Si 3,6…4,2; Mn 0,2…0,6; P до 0,08; S 0,06…0,2; Cr до 0,06. Графитизирующий обжиг проводят в две стадии. Перлитный ковкий чугун (КЧ 45-7, КЧ 50-5, КЧ 55-4, КЧ 60-3, КЧ 65- 3, КЧ 70-2, КЧ 80-1,5) должен иметь следующий химический состав: C 2,4…2,8; Si 1,1…1,4; сумма C + Si 3,6…3,9; Mn 0,3…1,0; P до 0,1; S 0,2…0,6; Cr до 0,08. Графитизирующий отжиг производят при ускоренном проведении второй стадии графитизации.
Отливки из ковкого чугуна должны иметь одинаковую толщину стенок без массивных толстых узлов для исключения образования в их сердцевине структуры серого чугуна (брак по трещинам).
Жидкий чугун модифицируют с целью сокращения продолжительности отжига и стабилизации структуры белого чугуна, т.е. для предупреждения выделения графита при кристаллизации белого чугуна в толстых стенках.
Модификаторы для стабилизации структуры белого чугуна при кристаллизации отливок: висмут; висмут + сурьма или марганец; теллур; теллур + медь или сера; бор + сурьма или бор + сурьма и алюминий; сера + алюминий или алюминий и бор, магний; иттрий и др.
Количество модификатора, вводимого в жидкий чугун, может составлять 0,001–0,5 % от массы расплава. Способ ввода модификаторов в шихту (сера), в ковш — над струей расплава, в литниковую систему.
Параметры модифицирования — это температура расплава и срок выдержки перед заливкой в форму.
Чугун для валков обрабатывают стабилизирующими модификаторами (Те 1…7 г на 1 т чугуна) и графитизирующими модификаторами (ФС 75 + графит + СК) для получения заданной толщины слоя отбела и сердцевины со структурой серого чугуна.
Модифицирование для получения высокопрочного чугуна
сшаровидным графитом
Кэлементам, сфероидизирующим графит при их вводе в жидкий чугун, относятся: Mg, Ca, Ce, Y и др. Р3М. Магний является наиболее эффективным модификатором для получения ВЧШГ. Основной проблемой модифицирования является интенсивное горение чистого магния при вводе его в чугун при атмосферных условиях. Кроме того, необходимо строго следить за временем выдержки металла после его модифицирования до конца заливки. Эффект модифицирования сохраняется непродолжительное время.
Ряд элементов препятствуют процессу сфероидизации графита. Эти элементы называют демодификаторами. Их количество в чугуне не должно превышать в %: Pb — 0,009; Bi — 0,003; Sb — 0,026; As — 0,08; Ti — 0,04; S — 0,13; Al — 0,3.
Действие демодификаторов частично или полностью устраняется введением в чугун элементов-ремодификаторов. К ним относятся церий и другие Р3М.
Химический состав чугуна для получения шаровидного графита модифицированием задают в зависимости от толщины стенки отливки и требуемого значения предела прочности. При этом содержание примесей должно быть не более, в %: Р < 0,1, серы < 0,01–0,02, Cr < 0,05–0,15.
В качестве модификаторов для получения чугуна с шаровидным графитом используют чистый магний и лигатуры.
Количество магния зависит от содержания серы в исходном чугуне, требуемого остаточного содержания магния в модифицированном чугуне и от коэффициента усвоения магния, который определяется опытным путем в зависимости от способа ввода магния в чугун.
Модифицирование чистым магнием — наиболее дешевый способ. Однако для его ввода требуется специальное оборудование. При вводе Mg в чугун в автоклаве его количество и температура жидкого чугуна зависят от давления.
Остаточное количество магния в чугуне должно быть в определенных пределах. При недостатке Mg образуется смешанный графит или вермикулярный графит, а при избытке белый или отбеленный чугун.
Ввод магния в жидкий чугун в составе лигатур
Применяют лигатуры с содержанием магния до 15 % на базе тяжелых металлов Ni, Cu или Fe или более легкие лигатуры, содержащие кроме магния другие элементы, сфероидизирующие графит в чугуне, — Са, Р3М. При вводе магния в составе лигатур стабилизируется степень его усвоения, которая зависит также от температуры жидкого чугуна tж, при которой они водятся.
Для предупреждения отбела в отливках после обработки чугуна магнием производят вторичное модифицирование графитизирующими добавками.
Для получения высокопрочного чугуна с шаровидной формой графита необходимо:
–применять шихтовые материалы с низким содержанием серы или производить обессеривание жидкого чугуна;
–вводить магний в устройствах с погружением под избыточным давлением;
–производить вторичное модифицирование жидкого магниевого чугуна графитизирующими элементами;
–производить модифицирование чугуна комплексными лигатурами, содержащими сфероидизирующие и графитизирующие элементы.
Перспективно применение внутриформенных способов модифицирования. Например, когда модифицирующие вещества помещают в устройствах, расположенных в литниковой системе.
Контрольные вопросы
1.Охарактеризуйте чугун.
2.Опишите устройство и работу коксовой вагранки.
3.Какие происходят физико-химические процессы при плавке чугуна в коксовой вагранке?
4.Методы модифицирования чугуна.
Глава 9. Плавка стали
9.1.Общие сведения о сталях для изготовления отливок
Взависимости от назначения литых деталей и требований к ним стальные отливки подразделяются на три группы (табл. 9.1).
|
|
|
Таблица 9.1 |
|
Требования к литым деталям |
|
|||
|
|
|
|
|
Группа |
Назначение |
Характеристика отливки |
Перечень контролируемых показателей |
|
отливки |
||||
|
|
|
||
I |
Отливки общего |
Конфигурация и размеры деталей |
|
|
определяются конструктивными и |
Внешний вид, размеры, химический состав |
|||
назначения |
||||
|
технологическими соображениями |
|
||
|
|
|
||
II |
Отливки |
Детали рассчитываются на прочность |
Внешний вид, размеры, химический состав, |
|
ответственного |
и работают при статичных нагрузках |
механические свойства: предел текучести или |
||
|
назначения |
прочности и относительное удлинение |
||
|
|
|||
|
Отливки особо |
Детали рассчитываются на прочность |
Внешний вид, размеры, химический состав, |
|
III |
ответственного |
и работают при циклических и |
механические свойства: предел текучести или |
|
прочности; относительное удлинение и ударная |
||||
|
назначения |
динамических ударных нагрузках |
||
|
вязкость |
|||
|
|
|
Группа отливки указывается в штампе чертежа 25Л – «III» или в технических требованиях на поле чертежа — «отливка III группы».
Литейные стали маркируют буквой Л, которую проставляют в конце их обозначения, например, 25 Л или 12 Х18 Н9ТЛ.
Для плавки литейных сталей применяют мартеновские (очень редко) и электрические (в подавляющем большинстве) печи с кислой или основной футеровкой.
Химический состав стали с указанием допустимого содержания вредных примесей и группы отливки являются основными данными для разработки технологии плавки (выбор плавильной печи, состав шихтовых материалов, расчет шихты и т.п.).
Легирующие элементы и примеси в различной степени снижают температуру ликвидус tл стали, ºС:
tл = 1539 – 80C – 30(P + S) – 12Si – 3,5Ni –
– 3(Mn + Mo) – 2V – 1(Cr +W),
где 1539 — температура плавления железа; 80, 30, 12 и т.д. — коэффициенты, показывающие, на сколько градусов снижает температуру плавления железа добавка в сталь 1 % соответствующего элемента — C, P, S …
Литейные свойства сталей значительно хуже, чем чугунов. Температура плавления и температура заливки стали на ~200 ºС выше, чем чугуна, что требует применения более качественных и высокоогнеупорных футеровочных материалов для плавильных печей и формовочных материалов для форм.
Линейная и объемная усадки сталей выше, чем чугунов. Поэтому для питания массивных узлов отливок применяют прибыли, в результате расход жидкого металла на отливки увеличивается более чем в два раза.
9.2. Плавка стали в дуговых электропечах
Электрические дуговые печи (рис. 9.1) широко применяются в литейном производстве благодаря следующим преимуществам по сравнению с кислородными конверторами и мартенами: возможность выплавлять в одной и той же печи разнообразные марки сталей малыми порциями при сравнительно небольшой продолжительности плавки; получение высоколегированных сталей высокого качества с низким содержанием серы, фосфора и неметаллических включений с использованием большого количества легированных отходов.