
741
.pdf
смеси, прокаленной при температуре 800 ºС. Образец испытывают на стандартном копре, а выбиваемость (А) определяют по формуле
À = nGh,
где n — число ударов копра; G — масса груза, кг; h — высота падения груза, м.
Долговечность (Д) — способность смеси сохранять свои свойства при многократном нагреве, т.е. ее пригодность к повторному использованию после взаимодействия с залитым в форму металлом:
Ä= σò 100,
σî
где σт — предел прочности при сжатии смеси после трехкратного нагрева до температуры заливки и охлаждения до комнатной температуры; σо — предел прочности при сжатии свежеприготовленной смеси.
Гидравлические свойства
Влажность (В) — важнейшее свойство формовочных и стержневых смесей, определяющее значение ряда других свойств и оказывающее прямое воздействие на качество отливок.
Влажность в процентах определяют по потере массы образца — Мо после тепловой сушки при температуре 105–110 ºС до постоянной массы образца — М (~ 2 ч):
 = |
Ì |
î |
− Ì |
100 . |
|
Ì |
î |
||
|
|
|
Пористость — отношение объема пустот к объему смеси. Формовочные смеси имеют пористость 25–30 %.
Газопроницаемость — важнейшее свойство форм, влияющее непосредственно на качество отливок и характеризующее способность смеси пропускать газы. Газопроницаемость определяют путем пропускания воздуха через стандартный образец испытываемой смеси и рассчитывают по формуле
Ê = Vh ,
Fpτ
где К — коэффициент газопроницаемости; V — объем воздуха, прошедшего через образец, см3; h
— высота образца, см; F — площадь сечения образца, см2; р — давление воздуха перед входом в образец, Па; τ — продолжительность прохождения воздуха через образец, мин.
Газотворность — это свойство смесей выделять газы при нагреве, характеризуется количеством газа, выделившимся во время выдержки 1 г смеси при температуре 1000 °С. Газотворность смесей зависит от влажности и содержания органических добавок. Чем выше газотворность, тем вероятнее образование газовых раковин в отливках. Для стальных отливок газотворность смеси не должна превышать величины 15 см3/г.
Механические свойства
Твердость — свойство уплотненной смеси сопротивляться деформированию при внедрении в нее шарикового или ножевого наконечника твердомера. Твердость сырых форм определяют шариковым твердомером, а сухих и упрочненных форм — твердомером с ножевым наконечником. Величина твердости соответствует показаниям шкалы прибора.
Прочность формовочной смеси в сыром состоянии определяют на стандартных образцах на сжатие (рис. 3.4, а), а упрочненных — на разрыв (рис. 3.4, б).
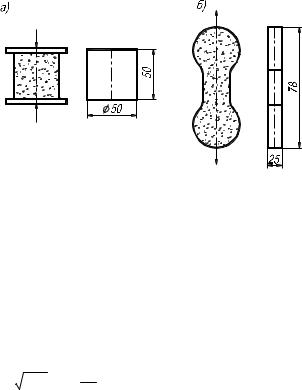
Рис. 3.4. Схемы испытаний прочности стандартных образцов: а — сырых на сжатие; б — упрочненных на разрыв
Прочность на разрыв стандартных образцов — восьмерок после сушки и отверждения различных формовочных смесей составляет: 0,2–0,3 МПа песчано-глинистых; 0,8–1,0 МПа песчано-масляных; 0,5–1,5 МПа песчано-смоляных.
Теплофизические свойства
К теплофизическим свойствам литейных форм относятся: теплопроводность, кВт/м· ºС; удельная теплоемкость — с, кДж/кг; теплоаккумулирующая способность b, кДж/(м2·с½ · ºС) и температуропроводность — а, м2/с, при этом
b = λñρ , а = λ ,
ñρ
где ρ — плотность формовочной смеси, кг/м3.
Плотность песчано-глинистых смесей составляет 1600–1700 кг/м3; теплоемкость сырой смеси — 1050–1200 Дж/(кг·К), сухой 750–850 Дж/(кг·К); теплопроводность изменяется в широких пределах — 0,014…0,4 Вт/(м · ºС).
3.8. Приготовление формовочных и стержневых смесей
Приготовление смесей включает подготовку исходных формовочных материалов, дозирование компонентов, подачу их в определенной последовательности в смеситель и перемешивание всех составляющих до получения однородной массы.
Подготовка исходных формовочных материалов
Песок перед приготовлением смеси сушат, просеивают и охлаждают. Отработанную песчаноглинистую смесь перед употреблением подвергают магнитной сепарации, разрыхлению, просеиванию и охлаждению. После переработки ее используют для приготовления формовочных смесей в количестве 50–95 %.
Регенерация отработанных жидкостекольных и смоляных смесей включает очистку зерен песка от пленки связующего и удаление пылевидных фракций.
Применяют гидравлический, термический и механический методы регенерации. Выбор способа зависит от применяемого связующего материала и величины затрат на регенерацию.
Высокое качество регенерата обеспечивается гидравлическим методом для жидкостекольных и цементных смесей и термическим — для смоляных смесей.
Механический метод требует меньших затрат. Применим для любых смесей, однако качество регенерации этим методом ниже. Поэтому при приготовлении смесей его используют не более чем в 50 % случаев.
Глину в формовочную смесь вводят в виде порошка или готовят глинистую суспензию.
Добавки перед употреблением дробят и размалывают в шаровых мельницах до порошкообразного состояния.
Приготовление формовочных смесей производят в катковых чашечных смесителях — бегунах (рис. 3.5) или в лопастных смесителях (рис. 3.6).
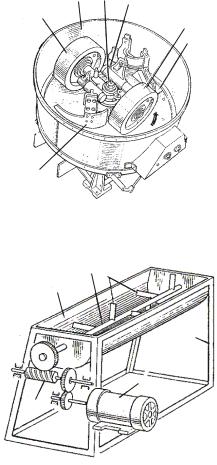
1 2 3
7
4
5
6
Рис. 3.5. Смеситель катковый (бегуны):
1 — чаша; 2 — вертикальный вал; 3 — ось катков; 4, 7 — катки; 5, 6 — плужки
23
1
4
5
6
Рис. 3.6. Смеситель лопастной:
1 — емкость; 2 — вал; 3 — лопасти; 4 — рама; 5 — электродвигатель; 6 — редуктор
Катковые чашечные смесители (бегуны) применяют для приготовления песчано-глинистых смесей, так как в них обеспечивается равномерное обволакивание зерен песка глиняной пленкой.
Чем тоньше пленка глины, тем выше качество смеси и меньше расход связующего при одной и той же прочности формовочной смеси.
Увеличение количества связующего материала отрицательно сказывается на качестве отливок: снижается газопроницаемость форм, увеличивается их газотворная способность, ухудшаются условия труда и регенерируемость смесей.
Приготовление жидкостекольных, смоляных и масляных смесей производят в лопастных смесителях, так как в отличие от глины жидкое стекло, масло и смоляные связующие легко обволакивают зерна песка тонкой пленкой.
В автоматизированном производстве применяют также шнековые смесители непрерывного действия.
Выбор смесителя определяется живучестью смеси и объемом производства.
Для улучшения формуемости песчано-глинистые смеси обрабатывают в аэраторах (лопастных разрыхлителях) или в дезинтеграторах (дисковых разрыхлителях) с помощью штифтов или пальцев, закрепленных на дисках.
Контрольные вопросы
1.Классификация формовочных материалов.
2.Свойства формовочных песков.
3.Классификация связующих материалов.
4.Назовите вспомогательные формовочные материалы.
5. Объясните процесс приготовления формовочных и стержневых смесей.
Глава 4. Изготовление стержней
4.1. Устройство стержня
Требования к стержню
Стержень после заливки формы металлом подвергается действию высоких температур и механических нагрузок при усадке отливки, поэтому к ним предъявляются более высокие требования по качеству, чем к форме.
Качество стержней определяется их прочностью, огнеупорностью, газопроницаемостью, податливостью, низкой гигроскопичностью и хорошей выбиваемостью.
Огнеупорность. Для изготовления стержней применяют в основном свежие формовочные материалы и материалы высокой огнеупорности: обогащенный кварцевый песок, хромистый железняк, магнезит.
Высокая прочность стержней достигается применением в качестве связующих материалов жидкого стекла, металлофосфатов, термоактивных смол. Для повышения прочности стержней их армируют металлическими каркасами.
Стержни должны обладать минимальной газотворной способностью и высокой газопроницаемостью. Для вывода газов из стержня в сторону знака в них выполняют газоотводные каналы.
Податливость стержней обеспечивается применением органических связующих материалов, теряющих прочность при высоких температурах, и введением в состав смеси древесных опилок, асбестовой крошки и т.п.
Гигроскопичность стержней должна быть минимальной, особенно при формовке по-сырому. Впитывание влаги стержнем — нежелательное явление из-за образования газовых дефектов и
выброса металла из формы при заливке («кипение металла»).
Выбиваемость стержней зависит от типа связующего. Жидкостекольные и песчано-глинистые смеси в результате спекания трудно удаляются, а песчано-смоляные в результате разупрочнения при заливке легко удаляются из полостей отливок.
Виды стержней
По конструктивному признаку стержни могут быть неразъемные, сборные, объемные, облегченные и оболочковые.
Неразъемные изготавливают в одном ящике и устанавливают в форму без дополнительных стержней.
Сборные получают сборкой из нескольких стержней. Собранный пакет устанавливают в форму как единый стержень. Способы соединения сборных стержней в единый пакет следующие: наложение одного стержня на другой; склеивание формовочными клеями; скрепление стяжками, болтами и другими способами; заливка в специальные отверстия в стержнях жидкого металла.
Объемные стержни выполняют сплошными.
Облегченные стержни изготавливают с внутренними полостями, которые заполняют недефицитными материалами, имеющими низкую газотворность: шлак, сухая отработанная смесь; бой стержней.
Оболочковые стержни имеют внутри открытые полости, которые в дальнейшем перед или после установки в форму засыпаются сухой отработанной смесью или другими негазотворными материалами. Толщина стенок оболочковых стержней составляет 6–12 мм.
По назначению стержни подразделяют на центровые, наружные, литниковые, подкладочные и вспомогательные.
Центровыми называют стержни, выполняющие внутренние полости деталей, а наружными — наружные поверхности отливок.
Литниковые — это стержни, предназначенные для выполнения элементов литниковой системы и оболочки прибылей: чаши, воронки, фильтровальные сетки, прибыльные и выпорные надставки, разделительные пластины для прибылей.
Подкладочные стержни служат опорами для крупных стержней или для упрочнения отдельных мест формы, испытывающих большое гидростатическое давление металла.
По конфигурации и условиям работы стержни делят на пять классов или групп сложности:
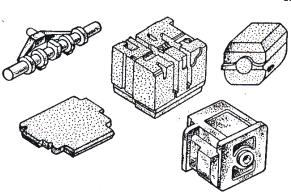
–к I классу относятся стержни сложной конфигурации, с тонкими сечениями и небольшим количеством тонких знаков, вывод газов через которые затруднителен. Они предназначены для образования в отливках необрабатываемых полостей с высокими требованиями к чистоте и шероховатости поверхности. Это ленточные и центровые стержни двигателей внутреннего сгорания, центровые стержни полостей гидроаппаратуры и т.п. Такие стержни должны обладать высокой прочностью, огнеупорностью и газопроницаемостью, низкой газотворной способностью
ихорошей выбиваемостью;
–к V классу относятся стержни средних и крупных размеров, образующие в крупных, простых по конфигурации отливках большие полости. Они имеют устойчивые знаки. Это центровые стержни корпусных деталей, которые должны обладать хорошей прочностью, газопроницаемостью и податливостью.
На рис. 4.1 показаны примеры стержней I, II, III, IV и V классов.
I |
II |
III |
IV |
V |
Рис. 4.1. Классы сложности стержней
По объему и массе стержни разделяют на четыре группы (табл. 4.1).
По характеру производство стержней может быть единичным, мелкосерийным, серийным, крупносерийным и массовым.
Таблица 4.1
Группы стержней по объему и массе
Группа |
Объем |
Масса стержней, кг |
Габариты стержневых |
|
стержней |
стержней, дм3 |
ящиков, мм |
||
Мелкие |
До 1,6 |
До 2,5 |
От 200×160×100 до |
|
1,6–6,3 |
2,5–10,0 |
630×400×400 |
||
|
||||
Средние |
6,3–16,0 |
10,0–25,0 |
от 630×400×400 до |
|
16,0–40,0 |
25,0–63, |
1600×1000×600 |
||
|
||||
Крупные |
40,0–100,0 |
63,0–160,0 |
Свыше 1600×1000×600 |
|
100,0–250,0 |
160,0–400,0 |
|||
|
|
|||
Особо |
Свыше 250,0 |
Свыше 400 |
|
|
крупные |
|
|||
|
|
|
Конструктивные элементы стержней
Знаки стержней служат для устойчивого крепления стержня в форме и вывода газов из него при заливке форм расплавом. По расположению в форме различают горизонтальные и вертикальные (верхние и нижние) знаки.
Горизонтальные знаки делают цилиндрическими, а вертикальные — коническими или пирамидальными.
Знаки стержней выполняют с зазорами, а острые кромки форм — с закруглениями для удобства сборки и для того, чтобы при установке стержня не разрушить форму.
Для обеспечения строго заданного положения стержня в форме знаки выполняют с фиксаторами (рис. 4.2).
При отсутствии верхнего знака для того, чтобы стержень не всплыл при заливке, нижний выполняют с пояском, т.е. размер знака принимается больше размеров окна в отливке, чтобы сила
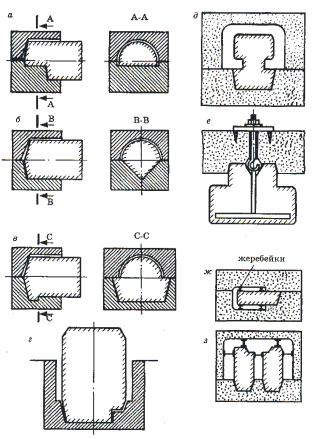
давления жидкого металла на поясок была больше силы выталкивания стержня из расплава (рис. 4.2, д).
Иногда стержни, не имеющие нижнего знака, подвешивают к ребрам верхней опоки (рис. 4.2,
е).
В случае, когда с помощью знаков нельзя обеспечить устойчивость стержня в форме, применяют опорные (рис. 4.2, ж) или распорные жеребейки (рис. 4.2, з).
а) |
д) |
|
б) |
е) |
в)
|
|
ж) |
|
|
|
||
г) |
з) |
|
|
|
|
|
Рис. 4.2. Виды фиксаторов стержней
Арматура (каркасы) служит для обеспечения прочности стержней и должна удовлетворять следующим требованиям: не препятствовать усадке отливки, для чего между каркасом и внешним контуром стержня должен быть достаточный слой смеси; не мешать устройству вентиляционных каналов и не препятствовать выходу газов из стержня, для чего листовые и трубчатые каркасы должны иметь отверстия; легко удаляться из отливки при выбивке; быть удобной в работе, чтобы каркас можно было быстро и точно установить в стержневой ящик и чтобы он не препятствовал набивке стержня.
Каркасы классифицируют по способу изготовления на проволочные, литые, сварные, разборные (рис. 4.3); по материалам — на чугунные, стальные, комбинированные и из синтетических материалов. Для изготовления проволочных каркасов применяют только отожженную проволоку.
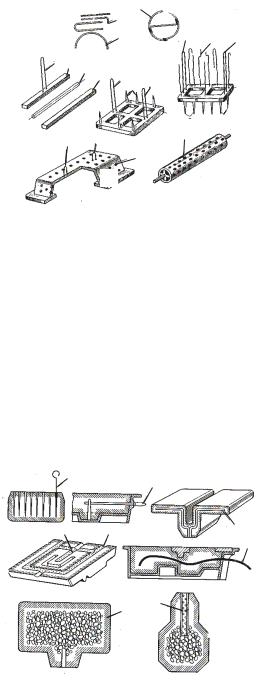
|
а) |
|
|
|
|
|
|
4 |
4 |
|
|
|
|
|||
|
|
|
|
|
|
|
|
|
|
|
|
|
|
|
||
|
|
|
|
|
|
|
|
|
4 |
|
|
|
2 |
4 |
2 |
|
б) |
|
в) |
|
|
|
|
|
|
|
|
а) |
|
|
|
|
|
|
|
г)2 |
1 |
1 |
1 |
|
|
|
|
|
|
|||||
|
|
|
|
|
|
|
|
|
|
|||||||
|
|
|
|
|
|
|
2 |
3 |
|
2 |
|
|
|
|||
|
|
|
|
|
|
|
|
|
|
|
||||||
|
|
|
|
|
|
|
|
|
|
|
|
|||||
|
|
|
|
|
|
|
|
|
|
|
|
|
|
|
||
д) |
|
б) |
|
|
|
2 |
2 |
|
|
|
|
в) |
1 |
|
г) |
|
|
|
|
|
|
|
|
|
|
||||||||
|
|
|
|
|
|
|
|
|
|
|||||||
|
|
|
|
|
|
|
|
|
|
|||||||
|
|
|
|
|
|
|
|
|
|
|||||||
|
|
е) |
|
|
1 |
|
|
|||||||||
|
|
|
|
|
|
|
|
|
||||||||
|
|
|
|
|
|
|
|
|
|
|
|
|
||||
|
|
|
|
|
|
|
|
|
|
|
|
|
|
|
||
|
|
|
|
|
|
|
|
|
|
|
|
|
|
|
е)
д)
Рис. 4.3. Каркасы стержней:
а — проволочные; б — планки; в — рамочный литой; г — комбинированный; д — коробчатый; е — трубчатый с вентиляционными отверстиями;
1 — основание; 2 — подъемы; 3 — торцы; 4 — проволока
Вески (подъемы) служат для перемещения, отделки и установки стержней в форму. Вентиляция стержней служит для направленного в сторону знаков вывода газов, образующихся
в результате заливки форм.
Вентиляцию стержней выполняют следующими способами: при помощи прямого душника или металлических прутков, вынимаемых через стенки ящика, или путем наколов в знаках со стороны набивки стержня (рис. 4.4, а, б); при помощи витой стальной стружки или покрытых воском жгутиков из соломы, хлопчатобумажной ткани или древесной стружки (рис. 4.4, в, г); при помощи прорезных каналов по разъему стержня (рис. 4.4, г); при помощи колодцев или полостей в крупных стержнях, заполняемых шлаком (рис. 4.4, е, ж).
а) |
б) |
|
|
|
|
|
|
|
|
|
|
||||||
|
|
в)1 |
|
|
|
2 |
|||||||||||
|
|
|
|
|
|
|
|
|
|
|
|
|
|||||
|
|
|
|
|
|
|
|
|
|
|
|
|
|
|
|||
|
|
|
|
|
а) |
Наколы |
б) |
|
3 |
||||||||
|
|
|
|
|
|
||||||||||||
г) |
|
|
|
|
4 |
|
|
в) |
|||||||||
|
|
|
|
|
д) |
|
|
|
|
|
|
|
|||||
|
|
|
|
|
|
|
|
|
|
|
|
|
|
|
|
5 |
|
|
|
|
|
|
|
|
|
|
|
|
|
|
г) |
|
|||
|
|
|
|
|
|
|
|
|
|
|
|
|
|
|
д) |
||
|
|
|
|
|
|
|
|
|
|
|
|
|
|
|
|||
|
|
|
|
|
|
|
|
|
|
|
|
|
|
|
|||
е) |
|
|
|
|
|
|
ж) |
|
|
|
|
|
|
|
|||
|
|
|
|
|
|
|
|
|
|
|
|
|
|
|
|
||
|
|
|
|
|
|
|
|
|
|
|
|
|
|
|
|||
|
|
|
|
|
|
|
|
|
|
|
|
7 |
|||||
|
|
|
|
|
|
|
|
|
|
|
|
|
|
|
|||
|
|
|
|
|
|
|
|
|
|
|
|
|
|
|
6 |
|
|
|
|
|
|
|
|
|
|
|
|
|
|
|
|
|
|||
|
|
|
|
|
|
|
|
|
е) |
|
|
|
|
|
ж) |
||
|
|
|
|
|
|
|
|
|
|
|
|
|
|
|
|
|
|
Рис. 4.4. Способы выполнения вентиляционных каналов
4.2.Стержневая оснастка
Кстержневой оснастке относятся: стержневые ящики и шаблоны, контрольные шаблоны, сушильные плиты и драйеры; кондукторы для зачистки и сборки стержней.
Стержневые ящики
При изготовлении небольшого количества стержней применяют деревянные ящики, при крупносерийном и массовом производстве — металлические и пластмассовые ящики (рис. 4.5).
Металлические стержневые ящики изготавливают из алюминиевых сплавов, чугуна и стали. Конструктивной особенностью ящиков для изготовления стержней на пескодувно-пескострельных
машинах является наличие отверстий — вент для выхода воздуха (рис. 4.6). Наружный диаметр вент 6–20 мм, ширина прорезей составляет 0,2–20 мм (рис. 4.7). Кроме вент по разъему ящика выполняют вентиляционные щели глубиной 0,15–0,20 мм.
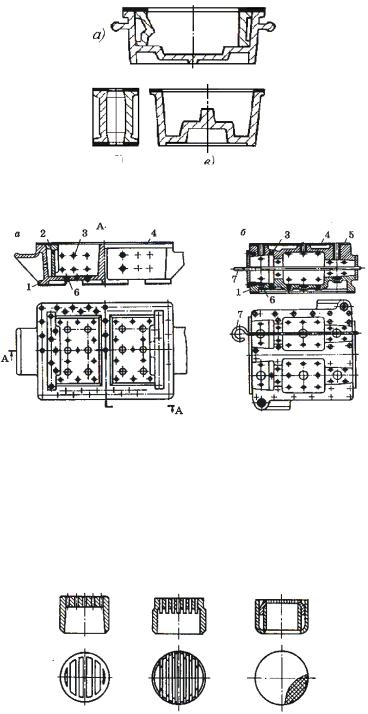
а)
б)
в)
Рис. 4.5. Пластмассовые стержневые ящики
а) |
б) |
|
Рис. 4.6. Стержневые ящики для пескодувных машин:
а— открытый вытряхной ящик; б — закрытый двугнездный ящик
сгоризонтальным разъемом;
1 — корпус ящика; 2 — вкладыш; 3 — венты; 4 — армировка ящика;
5 — вдувная втулка; 6 — бронирующая шайба; 7 — шомпол
а) |
|
а) |
б) |
в) |
|
б) |
|||||
|
в) |
|
|||
|
|
|
|
|
Рис. 4.7. Конструкции вент:
а — литая с щелевыми прорезями; б — изготовленная механической обработкой; в — сетчатая
При изготовлении стержней в горячих ящиках их нагрев осуществляют встроенными нагревателями, в печах или газом.
Сушильные плиты и драйеры
Сушильные плиты бывают плоскими и фасонными, которые называют драйерами (рис. 4.8). Они служат опорой при транспортировке стержней в сушило. Их изготавливают литыми из алюминиевых сплавов или чугуна с ребрами жесткости и отверстиями диаметром 6–10 мм для выхода газов из стержня при сушке.
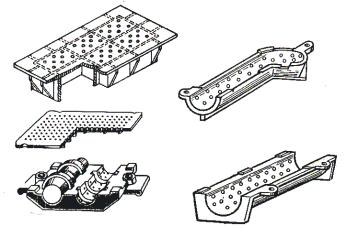
Рис. 4.8. Типы сушильных плит и драйеров
4.3. Классификация способов изготовления стержней
Стержни приобретают некоторую прочность после уплотнения. Насыпная плотность стержневой смеси составляет 900–1100 кг/м3, а после уплотнения 1450–1650 кг/м3. Прочность стержней после уплотнения зависит от состава стержневой смеси. Она недостаточна для того, чтобы предотвратить деформацию стержня при его установке в форму. Необходимую прочность стержень приобретает после сушки или отверждения, поэтому сырые стержни из песчано-глинистой смеси применяют при единичном или мелкосерийном изготовлении отливок.
Различают ручное и механизированное изготовление стержней. При ручном изготовлении стержней все основные операции выполняются вручную. При механизированном изготовлении стержней заполнение стержневого ящика и его разъем, уплотнение смеси производят на машинах, а остальные операции могут выполняться вручную. Засыпка ящика смесью может выполняться и вручную.
По применяемому типу стержневой смеси и характеру упрочнения технологические процессы подразделяют на отверждаемые: тепловой сушкой вне оснастки, т.е. после извлечения стержня из ящика; в нагревательной оснастке; в ненагреваемой холодной оснастке из жидкостекольных смесей с продувкой стержня в ящике углекислым газом; в холодной оснастке из жидких (наливных) самотвердеющих смесей; в холодной оснастке из химически твердеющих (холоднотвердеющих) смесей (ХТС), содержащих в составе отвердитель — катализатор отверждения; самотвердеющие в ящике или твердеющие после продувки стержня газообразным отвердителем.
4.4.Ручное изготовление стержней
Вмелкосерийном и единичном производстве стержней, имеющих форму тел вращения, иногда применяют способ их изготовления по шаблону. Основную массу стержней изготавливают в ящиках.
Подготовка стержневых ящиков заключается в их осмотре, очистке от остатков стержневой смеси щеткой, кистью, выдуванием воздухом или промывкой водой или керосином, проверке надежности скрепления и отдельных его частей и нанесении разделительных покрытий.
Распространенными разделительными покрытиями для стержней являются: ликоподий, серебристый графит, растворы керосина с маслом, растворы каучука в уайт-спирите, кремнийорганические жидкости.
Уплотнение стержневой смеси производят ручными или пневматическими трамбовками в зависимости от размеров ящика. Степень и равномерность уплотнения стержней имеют важное значение. Недопустимо наличие рыхлых, неуплотненных мест. Твердость песчано-глинистых мелких стержней должна быть 50–60 ед. по шариковому твердомеру, крупных — примерно около 80 ед.
Изготовление стержня в разъемном ящике показано на рис. 4.9. Вначале раздельно трамбовкой 1 уплотняют смесь 2 в двух половинах стержневого ящика. Каркас 3, предварительно смазанный глиняной суспензией, заформовывают в одной половине ящика, а в другой прорезают вентиляционный канал 4. После этого укладывают одну половину ящика на другую и плотно их скрепляют, а затем с торцов знаков подбивают смесь, постукивая деревянным молотком по стенкам ящика. Затем срезают излишки смеси металлической линейкой, со стороны каждого знака выполняют душником наколы и снимают верхнюю половину ящика. На стержень 5 устанавливают драйер 6, кантуют его вместе с
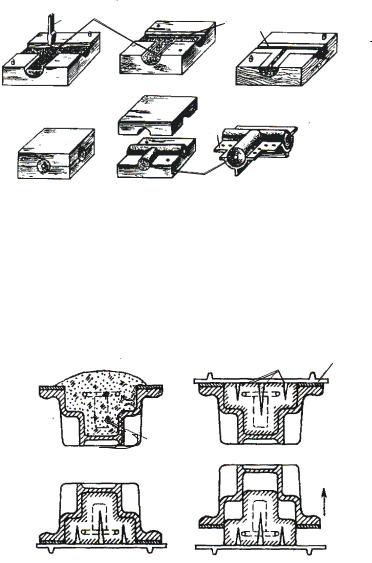
нижней половиной стержневого ящика и снимают половину ящика со стержня. Драйер с лежащим на нем стержнем помещают в сушиле.
а) |
а) |
1 |
2 |
3 |
4 |
|
|
||||
|
|
|
|
|
|
в) |
в) |
|
|
б) |
|
г) |
г) |
|
б) |
|
|||
|
|
|||
|
|
|
6 |
|
|
|
|
|
5
Рис. 4.9. Изготовление стержня в разъемном ящике
Изготовление стержня в вытряхном ящике показано на рис. 4.10. Сначала на дно ящика насыпают тонкий слой смеси, устанавливают каркас 1 и постепенно засыпают и уплотняют весь объем ящика с избытком выше краев (рис. 4.10, а); затем срезают излишек уплотняемой смеси, выполняют вентиляционные каналы 2, устанавливают сушильную плиту 3 (рис. 4.10, б); кантуют ящик вместе с плитой на 180º (рис. 4.10, в); постукивая по боковым стенкам и дну ящика деревянным молотком, снимают его со стержня (рис. 4.10, г); плиту со стержнем помещают в сушиле.
а) |
а |
б) |
б |
2 |
3 |
|
|
|
|
|
|
1
в) |
г) |
г |
|
в
Рис. 4.10. Изготовление стержня по неразъемному вытряхному ящику
Изготовление крупного стержня по вытряхному ящику с отъемными частями показано на рис. 4.11: засыпка и уплотнение слоя смеси 3 в ящике 2 и установка каркаса 1 (рис. 4.11, а); установка деревянного вкладыша 4 и уплотнение смеси до верхнего уровня ящика (рис. 4.11, б); съем вкладыша 4, выполнение наколов 5, засыпка шлака 6, окончательное уплотнение стержня, срез излишка уплотненной смеси заподлицо с верхней плоскостью ящика, выполнение наколов (рис. 4.11, в); установка на верхнюю плоскость ящика сушильной плиты 7 (рис. 4.11, г); кантовка корпуса ящика 8 и съем его со стержня (рис. 4.11, д); извлечение отъемных частей 9 и 10 (рис. 4.11, е); помещение плиты со стержнем в сушило.