
741
.pdf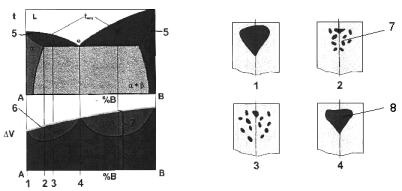
2-я и 3-я зоны разделены границей питания. В пределах температур tп – tс в результате затвердевания изолированных небольших объемов металла образуется усадочная пористость.
Усадочной пористостью называют скопление мелких пустот, образующихся при затвердевании в результате усадки небольших изолированных объемов металла.
Вмомент времени τ4 (поз. 4 на рис. 13.8) образуется слой твердого металла, а остальной объем
вцентре отливки находится в двухфазной области. Температура по оси отливки равна температуре ликвидус.
По сечению двухфазной области сплав опускается на небольшую высоту.
Вмомент времени τ5 затвердевает весь объем металла в форме. В отливке образуются пустоты
—усадочная раковина в верхней части отливки и усадочная пористость по оси отливки. Усадочная раковина имеет форму усеченного конуса. Между отливкой и формой образуется зазор.
Виды усадочных пустот в отливках, в зависимости от типа сплава, показаны на рис. 13.10.
а) |
б) |
|
Рис. 13.10. Виды усадочных пустот в отливках в зависимости от типа сплава:
а — диаграмма состояний (1, 2, 3, 4 — металлы и сплавы; 5 — линии температуры начала линейной усадки сплава (tнлу);
6 — кривая изменения объемной усадки сплавов;
7 — рассеянная пористость; 8 — концентрированная раковина); б — виды усадочных пустот (1 — чистый металл (tкр =const);
2 — сплав, кристаллизующийся в интервале температур; 3 — сплав (tкр = tsol); 4 — эвтектический сплав (tкр = tе))
Усадочные деформации и внутренние напряжения
Усадочные деформации — это изменение размеров и конфигурации отливки от момента заливки формы до ее полного охлаждения.
Внутренние напряжения возникают в результате торможения усадочных деформаций.
Усадочные деформации зависят от свойств сплава и формы, конфигурации отливки, ее размеров и массы.
Виды усадочных деформаций, в зависимости от конфигурации отливки и ее массы, показаны на рис. 13.11.
Механическое или термическое торможение формы усадки отливки приводит к тому, что фактическая усадка отличается от значений, приводимых в справочной литературе. Линейные размеры отливки могут отличаться от расчетных, что приводит к браку отливок по размерной точности.
Внутренние напряжения возникают в отливках в результате неравномерного охлаждения различных ее элементов и при торможении формой свободной усадки сплава.
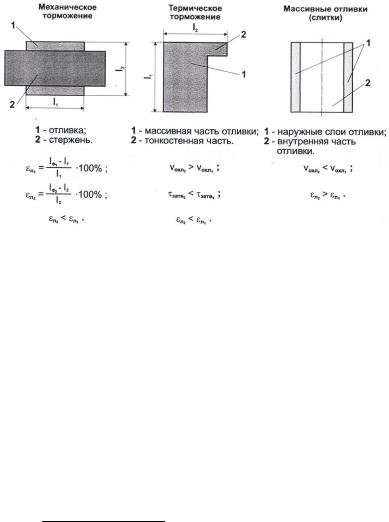
Рис. 13.11. Виды усадочных деформаций отливок
Внутренние напряжения подразделяют на временные и остаточные.
Временными называют напряжения, действующие в отливках в течение некоторого времени. Если напряжения вызывают упругие деформации, то после полного охлаждения отливки они снимаются. Внутренние напряжения могут привести к пластической деформации и короблению отливки.
Остаточными называют напряжения, возникающие в отливках после пластической деформации, полного охлаждения и выравнивания температуры. Они имеют обратный знак по сравнению с временными, вызывающими пластическую деформацию при высоких температурах.
Временные внутренние напряжения, возникающие при охлаждении отливки, подразделяют на
усадочные, фазовые и термические.
Усадочные напряжения, возникающие в отливках при охлаждении в форме в результате торможения формы, σм равны:
αã (tâ − tñð )
σм = 1/ Εì +1/ Εô Fì / Fô ,
где tср — температура отливки в определенный момент времени; tв — температура на границе выливаемости; Ем, Еф — модули упругости металла и формы; Fм, Fф — моли площади сечений отливки и формы.
Если внутреннее напряжение выше предела прочности металла, при определенной температуре σв(t) возникнут трещины, т.е. при условии:
σм < σв(t).
Трещины классифицируют на горячие и холодные.
Горячие трещины имеют черную окисленную поверхность и значительное расхождение между краями. Они образуются в период затвердевания отливки.
Холодные трещины имеют блестящую поверхность обычно с цветом побежалости и незначительным расхождением между краями. Они образуются при низких температурах (ниже 700 ºС для стали и чугуна).
Для устранения горячих трещин следует увеличивать податливость форм; упрочнять слабые места в отливках путем установки холодильников, ребер жесткости, конструирования плавных переходов от тонких сечений к толстым; устранять выступающие части в отливках за счет изменения их конструкций; снижать температуру и скорость заливки; снижать в сплавах содержание вредных примесей, например серы, фосфора, водорода; подводить металл в тонкие части отливки для выравнивания скорости охлаждения тонких и толстых частей.
Для снятия внутренних напряжений в отливках применяют отжиг или высокий отпуск.
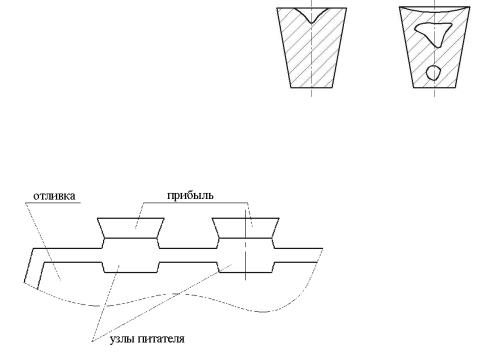
13.8. Устранение усадочных пустот в отливках. Прибыли и холодильники
Усадочные раковины в отливках могут быть открытыми и закрытыми.
Слои металла, разделяющие отдельные усадочные раковины и закрывающие раковины сверху, называют мостами.
Процесс перемещения жидкого металла внутри затвердевающей отливки называют питанием.
Основным средством устранения усадочных раковин является прибыль, которую располагают над местом образования усадочной раковины в верхней части отливки. В процессе затвердевания отливки прибыль составляет с ней единое целое, поэтому в ней сосредотачивается усадочная раковина, т.е. прибыль является источником питания затвердевающей отливки жидким металлом.
Прибыль также ослабляет образование пористости в отливке и служит сборником загрязнений, всплывающих из жидкого металла в процессе затвердевания.
Отливки сложной конфигурации состоят из конструктивных элементов: стенок, ребер, бобышек, фланцев и т.д., — различной толщины, в которых возможно образование усадочных раковин при затвердевании (рис. 13.12).
Для устранения раковин в массивных частях отливки ее разбивают на несколько обособленных узлов питания, над каждым из которых устанавливают прибыль (рис. 13.13).
а) |
б) |
Рис. 13.12. Виды усадочных раковин: а — открытая; б — закрытая
Отливка |
Прибыль |
Узлы питания
Рис. 13.13. Разделение отливки на узлы питания
Организация питания отливки или отдельных ее узлов основана на принципе направленного затвердевания.
Для отливок, затвердевающих в вертикальном положении, — цилиндров или плит — принцип направленного затвердевания формулируется следующим образом: каждый вышележащий слой затвердевающей отливки служит для питания нижележащего.
Для выполнения этого принципа отливка или отдельный узел питания должны быть конструктивно выполнены с уклонами.
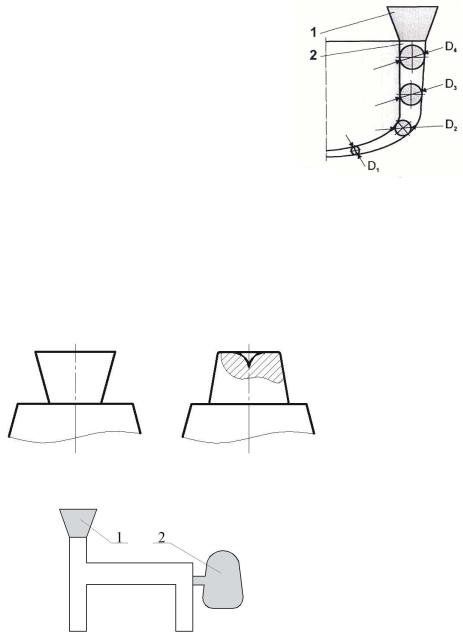
Принцип направленного затвердевания проверяют методом выкатывания шарика или методом вписанной окружности. Сущность метода заключается в том, что при выкатывании шарика в сторону прибыли его диаметр должен постоянно расширяться или диаметры вписанных в тело отливки окружностей должны увеличиваться в направлении к прибылям (рис. 13.14).
Принцип направленного затвердевания справедлив также для горизонтально расположенных отливок или узлов питания, в этом случае диаметры вписанных окружностей должны увеличиваться в сторону расположения прибылей.
Классификация прибылей
Прибыли для отливок разделяют по следующим признакам:
– способу формовки — открытые и закрытые (рис. 13.15);
Рис. 13.14. Метод вписанной окружности:
D1 < D2 < D3 < D4;
1 — прибыль; 2 — стенка отливки
– расположению относительно питаемого узла (прямого действия, устанавливаемые к верхней поверхности отливки или узла питания, и отводные, устанавливаемые сбоку от питательного узла, рис. 13.16);
а) |
б) |
Рис. 13.15. Прибыли:
а — открытые; б — закрытые
Рис. 13.16. Прибыли: 1 — прибыль прямого действия; 2 — отводная прибыль
–геометрической форме: круглые (цилиндрические, шаровые, полушаровые, кольцевые, полукольцевые), плоские (прямоугольные, квадратные) и фигурные;
–условиям охлаждения: обычные (оформляемые тем же материалом, что и отливка), теплоизолированные (оформляемые менее теплопроводным материалом, чем отливка), обогреваемые экзотермическими смесями или внешним источником теплоты (электрическим, газовым, химическим);
–способу использования давления: обычные (в которых не принимают мер по созданию давления), с атмосферным, газовым и воздушным давлением;
–способу отделения: отрезаемые и отбиваемые (когда между отливкой и прибылью устанавливают разделительные пластины, рис. 13.17);
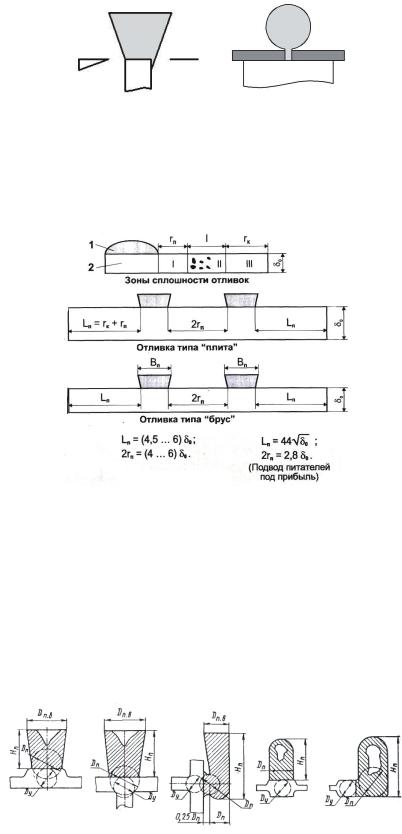
1 |
2 |
Рис. 13.17. Прибыли: 1 — отрезаемая прибыль; 2 — отбиваемая прибыль
– по числу питаемых узлов: групповые и индивидуальные.
Проектирование питания отливки прибылями заключается в определении узлов питания, количества прибылей с учетом радиуса их действия и радиуса действия торцевого эффекта и выборе рациональной конструкции прибыли (рис. 13.18, 13.19).
Рис. 13.18. Определение количества прибылей:
rп — радиус действия прибыли; rк — радиус действия края отливки;
I, III — зоны плотного строения отливки; II — зона усадочной пористости
Места образования усадочных раковин определяют методом вписанных окружностей или методом проведения изотерм — изосолидов.
Определение количества прибылей для отливок типа плит или «брус», расположенных горизонтально, поясняется рис. 13.18.
Выбор рациональной конструкции прибыли основан на том, что она должна быть резервуаром жидкого металла на весь период затвердевания отливки. Наивыгоднейшей конфигурацией прибыли является цилиндр (рис. 13.19).
Рис. 13.19. Тепловые узлы отливок с прибылями
На выбор оптимальной конструкции прибыли влияют следующие факторы: конфигурация отливки; способ формовки; характер производства; затраты на подготовку производства; затраты на отделение прибыли от отливки и т.д.
Методы расчета прибылей основаны на следующих положениях:
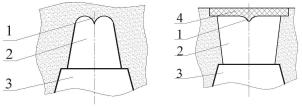
–продолжительность затвердевания прибыли должна быть больше продолжительности затвердевания питаемого узла;
–объем прибыли должен быть достаточным для компенсации усадки жидкого металла при затвердевании;
–усадочная раковина не должна выходить за пределы прибыли и достигать ее шейки.
Методы расчета прибылей для стальных отливок можно подразделить на три основные группы: с помощью таблиц и графиков, построенных на основе практических данных; на основе эмпирических и полуэмпирических формул; теоретические.
Все существующие методы в основном дают близкие результаты, поэтому часто используют расчет размеров прибыли в зависимости от размеров питаемого узла на основе соотношений, полученных в результате обобщения различных методов (теоретических или эмпирических).
Расчеты размеров прибыли на основе соотношений с размерами питаемого узла просты и удобны, в то же время они удовлетворяют основным требованиям к ее работе, т.е. обеспечивают достаточный объем прибыли для компенсации усадки и требуемую продолжительность ее затвердевания.
Отношение сечения цилиндрической прибыли к сечению питаемого узла должно быть следующим: для открытых прибылей Дп/Ду = 1,05…1,10, а для закрытых Дп/Ду = 0,96…1,00.
Высоту прибыли выбирают из соотношения Нп/Дп = 0,3…1,0.
Для плоских прибылей отношение длины прибыли lп к ее ширине Вп рекомендуется принимать следующее:
lп/Вп ≥ 2,5.
Для цилиндрических прибылей, устанавливаемых на плоские плиты, необходимо обеспечить соотношения
Нп/Дп = 3,0…3,5.
Методы повышения эффективности работы прибылей постоянно совершенствуются и весьма многообразны. К ним относятся:
–доливка открытых прибылей жидким металлом;
–засыпка верхней поверхности открытых прибылей песком или экзотермической смесью;
–газовый или электрический подогрев прибылей;
–применение теплоизолирующих облицовочных смесей или оболочек для увеличения продолжительности затвердевания прибыли;
–применение атмосферного, газового или механического давления на металл в прибыли.
Для закрытых прибылей весьма эффективно применение атмосферного давления. Устройство обычных закрытых прибылей с атмосферным давлением показано на рис. 13.20, а.
Для повышения эффективности работы закрытых прибылей предложена конструкция расширяющейся вверх закрытой прибыли, которая показана на рис. 13.20, б.
а) |
б) |
Рис. 13.20. Конструкция обычной (а) и расширяющейся кверху закрытой прибыли (б) с атмосферным давлением:
1 — выступ в форме; 2 — прибыль; 3 — отливка; 4 — стержень, перекрывающий верхнюю поверхность прибыли
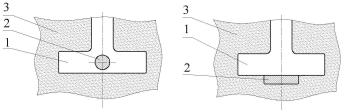
Холодильники применяют, в основном, для устранения усадочных пустот в тепловых узлах отливок, когда нет возможности установить на них прибыль.
Холодильниками называют металлические вставки, устанавливаемые в форму или стержень с целью обеспечения направленного затвердевания или ускоренного охлаждения теплового узла отливки. Холодильники бывают внешние и внутренние (расплавляемые) (рис. 13.21).
а) |
б) |
Рис. 13.21. Внутренние (а) и внешние (б) холодильники: 1 — тепловой узел; 2 — холодильник; 3 — форма
Внутренние холодильники изготавливают из того же сплава, из которого изготавливают отливку. Внешние изготавливают из чугуна, стали или медных сплавов. Для того, чтобы внешний холодильник не расплавился, на него наносят слой огнеупорного покрытия. Толщина внешнего холодильника равна 0,4–1,0 толщины питаемого узла.
Рекомендуются следующие соотношения диаметра холодильника dх и толщины наибольшей стенки dу в зависимости от типа сопряжения стенок:
Тип сопряжения |
L-образный |
T-образный |
X-образный |
Соотношения dх/dу |
~ 0,3 |
~ 0,5 |
~ 0,7 |
Контрольные вопросы
1.Охарактеризуйте процессы формирования отливки в песчаной форме.
2.Как отливка взаимодействует с формой?
3.Перечислите и опишите стадии охлаждения отливки.
4.Как определяется продолжительность охлаждения отливки?
5.Опишите процесс кристаллизации отливок в песчаной форме.
6.Сущность усадочных процессов при охлаждении отливки в песчаной форме.
7.Как устраняются усадочные пустоты в отливках? Для чего применяются прибыли и холодильники?
8.Классификация прибылей.
9.Какие существуют методы расчета прибылей для стальных отливок?
10.Опишите методы повышения эффективности работы прибылей.
Глава 14. Выбивка, обрубка, контроль и доводка отливок до требований технических условий
14.1. Выбивка, обрубка и очистка отливок
Выбивка — это процесс удаления затвердевших и охлажденных до определенной температуры отливок из литейных форм.
Объем и последовательность операций технологического процесса выбивки отливок из литейных форм зависят от их массы и конфигурации, типа сплава и способа формовки.
Целью процесса выбивки является удаление формовочной и стержневой смеси.
При ручной выбивке используются грузоподъемные механизмы и ручной (кувалды, молотки, зубила, стропы) и механизированный инструмент (пневматические молотки, зубила, навесные вибраторы и коромысла, а также вибрационные устройства с отбойными молотками).
К механизированным способам выбивки относятся: вибрационный, галтовка, гидравлический (водопескоструйный); водоструйный (струя сверхвысокого давления); гидроабразивный; электрогидравлический.
При механизированной выбивке отливок из опок применяют вибрационные выбивные решетки, схемы устройства которых показаны на рис. 14.1
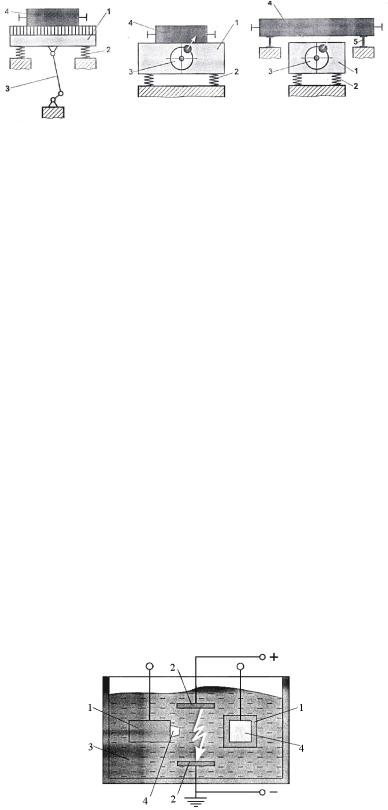
а) |
б) |
в) |
Рис. 14.1. Схемы типовых выбивных решеток:
а— эксцентриковая; б — инерционная; в — ударная инерционная; 1 — решетка; 2 — опорные пружины; 3 — механический привод; 4 — литейная форма; 5 — опорная рама
Для крупногабаритных опок применяются ударные инерционные выбивные решетки.
После выбивки верхней опоки с отливкой (или без нее) приступают к выбивке нижней опоки без отливки (или с отливкой).
Под действием вибрации формовочная смесь разрушается и удаляется из опоки. Вместе с формовочной смесью удаляются также знаки стержней.
После выбивки отливки охлаждают до комнатной температуры и отправляют на участок выбивки стержней. Удаление стержневой смеси начинается уже в процессе выбивки литейных форм.
Для удаления стержней применяют установки с пневматическими вибраторами. Сущность процесса состоит в том, что отливка прижимается к упору пневматическим приводом и к ней прилагается вибрация, в результате разрушается стержневая смесь и высыпается из полостей отливок.
Удаление стержней из мелких отливок производят в галтовочных барабанах. При галтовке процесс очистки поверхности отливок от пригара совмещен с процессом удаления стержней.
При гидравлической (гидроструйной) очистке с поверхности и внутренних полостей отливок остатки формовочной и стержневой смеси после выбивки удаляются струей воды или водопесчаной смеси.
Давление струи воды для чугунных отливок составляет 11–16 МПа, для стальных 20–25 МПа, а средняя скорость равна 150 м/с.
Применение гидравлической выбивки стержней из отливок ограничено особыми требованиями к прочности стержневой смеси (остаточная прочность должна быть низкой), конструкции каркасов и конфигурации полости отливки (закрытые полости с окнами малого диаметра не допустимы).
Перспективным технологическим процессом выбивки стержней является электрогидравлический, схема которого показана на рис. 14.2.
Рис. 14.2. Схема электрогидравлической выбивки стержней: 1 — отливка; 2 — электрод; 3 — ванна с водой; 4 — стержень
В результате высоковольтного импульсного разряда 50–70 кВ в воде возникают импульсы сверхвысокого давления — 150–200 МПа и более, которые разрушают стержни и пригоревшую к отливке формовочную смесь.
Обрезка — это операция удаления (отделения) литников, прибылей, технологических приливов (перемычек, стяжек) и заливов.
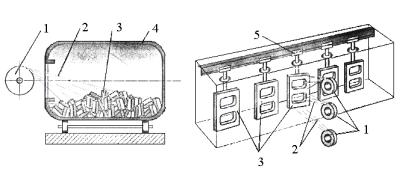
Вручную литниковую систему и прибыли удаляют пневматическими зубилами и молотками, а также слесарными, пневмо- и электромашинами с абразивными кругами.
У чугунных отливок литники и выпоры удаляются в процессе выбивки.
К механизированным способам обрезки литниковой системы и прибылей относятся: механические (ленточно-пильные станки, станки с дисковыми пилами, фрезерные, токарные и карусельные станки); абразивные (абразивно-отрезные станки); газопламенные, газофлюсовые; газоэлектрические (воздушно-дуговой, кислородно-дуговой, плазменно-дуговой, газолазерный).
Выбор способа удаления литниковой системы и прибылей, в первую очередь, зависит от типа и марки сплава. Для алюминиевых сплавов широко применяют обрезку на ленточно-пильных станках, для углеродистых сталей в основном кислородную обрезку прибылей, а для легированных — абразивную.
Очистка поверхности отливок — это процесс удаления пригара с наружных и внутренних поверхностей отливки, остатков формовочной смеси и стержней.
При ручной очистке применяют металлические щетки и механизированный слесарный инструмент, пневмо- и электромашины с абразивными кругами и металлическими шарашками.
Различают следующие способы механизированной очистки: песко- и дробеструйный; дробеметный, галтовка; гидроабразивный, вибрационный, ультразвуковой; химический, электролитический.
Для очистки чугунных и стальных отливок применяют, преимущественно, галтовку в барабанах, пескоструйную обработку в барабанах и камерах, а также дробометную обработку во вращающихся барабанах и камерах (рис. 14.3). Обрубка отливок — это процесс отделения от отливок литниковой системы, заливов по разъему формы и других неровностей поверхности.
Зачистка отливок — это процесс окончательной обработки поверхности отливок перед последующей механической обработкой.
После обрезки литников и очистки отливок на них остаются заливы от газовой резки и заливы металла по разъему формы и знакам стержней, различные наплывы и неровности поверхности, которые необходимо удалить. Все эти операции производятся путем обрубки ударными инструментами или методами зачистки на абразивных кругах.
а) |
б) |
Рис. 14.3. Дробометная очистка отливок:
а— в дробометном барабане; б — в дробометной камере; 1 — метательная головка; 2 — поток дроби; 3 — отливки; 4 — вращающийся барабан; 5 — подвесной конвейер
Технологический процесс обрезки, очистки, обрубки и зачистки отливок, в зависимости от типа сплава, массы отливки и предъявляемых к ней требований, а также в случае необходимости термообработки, будет иметь различные объемы и последовательность операций.
14.2. Дефекты отливок. Методы контроля качества отливок
Качество отливок — это совокупность свойств отливок, обуславливающих их пригодность удовлетворять определенным потребностям в соответствии с назначением.
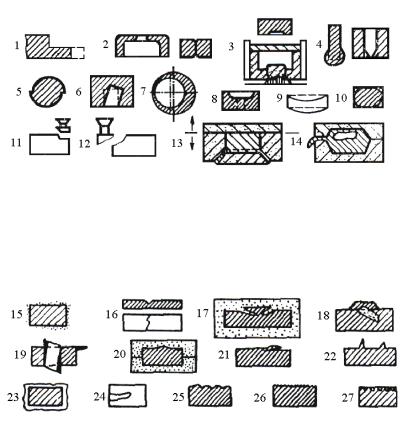
Дефект отливки следует рассматривать как отступление от заданных требований, а контроль качества — это выявление различного вида дефектов.
Дефекты отливок по видам классифицируют на пять групп: несоответствие по геометрии; дефекты поверхности; несплошности в теле отливки; включения; несоответствие по структуре.
Несоответствие по геометрии включает в себя следующие виды дефектов (рис. 14.4): 1 — недолив, 2 — неслитина, 3 — обжим, 4 — подутость, 5 — перекос, 6 — стержневой перекос, 7 — разностенность, 8 — стержневой залив, 9 — коробление, 10 — недолив, 11 — зарез, 12 — вылом, 13
— прорыв металла, 14 — уход металла.
Рис. 14.4. Схематическое изображение дефектов отливок из-за несоответствия по геометрии
Дефекты поверхности (рис. 14.5): 15 — пригар, 16 — спай, 17 — ужимина, 18 — нарост, 19 — залив, 20 — засор, 21 — плена, 22 — просечка, 23 — окисление, 24 — поверхностное повреждение, 25 — складчатость, 26 — грубая поверхность, 27 — газовая шероховатость.
Рис. 14.5. Схематическое изображение дефектов поверхности отливок
Несплошности в теле отливки: 28 — горячая трещина, 29 — холодная трещина, 30 — межкристаллическая трещина (на схеме не показана), 31 — газовая раковина, 32 — ситовидная трещина, 33 — усадочная раковина, 34 — песчаная раковина, 35 — шлаковая раковина, 36 — залитый шлак, 37 — графитовая пористость, 38 — усадочная раковина, 39 — газовая пористость, 40 — рыхлота, 41 — непровар жеребеек, 42 — вскип, 43 — утяжина (ри. 14.6, а);
включения: 44 — металлическое включение, 45 — неметаллическое включение, 46 — королек (рис. 14.6, б);
несоответствие по структуре: 47 — отбел, 48 — половинчатость (рис. 14.6, в).