
773
.pdf
Е.О.Юркова,О.А.Шаламова,Е.В.Самойлова
несоответствий и оценки тяжести последствий для пути, а также устранение установленных отклонений или уменьшение степени их влияния на качество. Такого рода анализы процессов основаны на теоретических знаниях экспертов и их практическом опыте.
При принятии решений всегда существует риск ошибочного выбора, т. е. неверный вклад в достижение цели, обусловленный неправильным шагом. Поскольку риск — вероятность потерь, он означает возможное негативное отклонение от направления, ведущего к цели.
Для оценки технологического процесса шлифования рельсов в пути FMEA-анализ проводился в определенном порядке [1]. Была сформирована рабочая группа, состоящая из экспертов. Перечислены все операции технологического процесса. Для каждой операции определены виды потенциальных дефектов. Затем установлены потенциальные причины возникновения этих дефектов и потенциальные последствия для пути.
В ходе этой работы для каждой операции технологического процесса был рассчитан коэффициент риска RPZ:
RPZ = А•В•Е,
где А — параметр частоты возникновения дефекта; В — параметр тяжести последствий для потребителя; Е — параметр вероятности обнаружения дефекта.
Значения коэффициентов А, В и Е оцениваются по рекомендациям ГОСТ Р51814.2–2001 по 10-балльной шкале.
Результаты рассчетов вносятся в таблицу, фрагмент которой для двух операций технологического процесса показан в табл. 1.
Таблица 1
Фрагмент таблицы, составленной в процессе FMEA-анализа технологии шлифования рельсов в пути
Операция |
Потенциальныйдефект |
Потенциальная причина |
Потенциальные последствия |
А |
В |
Е |
RPZ |
|
|
|
|
|
|
|
|
1. Предварительное |
1. Большая погрешность |
1. Низкая квалификация |
Неверное назначение режимов |
|
|
|
|
сканирование |
сканирования |
персонала |
шлифования |
4 |
4 |
6 |
96 |
фронта работ |
2. Отсутствие результатов |
2. Отказ системы |
|
||||
|
|
|
|
|
|||
|
сканирования |
сканирования |
|
|
|
|
|
2. Выбор |
Несоответствие |
1. Низкая квалификация |
1. Снижение производительности |
|
|
|
|
ремонтного |
ремонтного профиля |
персонала |
шлифования |
4 |
5 |
4 |
80 |
профиля рельса |
эксплуатационным |
2. Отсутствие |
2. Необоснованно большойсъем |
|
|
|
|
|
требованиям пути |
требуемого ремонтного |
металла с головкирельса |
4 |
5 |
6 |
120 |
|
|
профиля для данных |
3. Несоответствие геометрической |
|
|
|
|
|
|
условийэксплуатации |
формы обработанного поперечного |
|
|
|
|
|
|
|
профиля рельса эксплуатационным |
|
|
|
|
|
|
|
требованиям пути |
6 |
6 |
4 |
144 |
Далее были выбраны операции со значениями коэффициента RPZ более 100…120, которые считаются операциями с повышенным риском. Если же значение коэффициента RPZ в среднем для данного процесса выше 100, то «узкими местами» являются переходы.
При анализе техпроцесса шлифования рельсов в пути были выявлены две операции с коэффициентом риска более 100 ед. Во-первых, это операция выбора ремонтных профилей рельсов, для которой коэффициент риска RPZ составил 144 ед. Во-вторых, операция назначения режимов шлифования — RPZ составил
180 ед.
Для выявленных операций с целью уточнения значения коэффициента RPZ проводится факторный анализ, который сводится к оценке влияния шести факторов Исикава на составляющие коэффициента RPZ, т. е. на коэффициенты
171
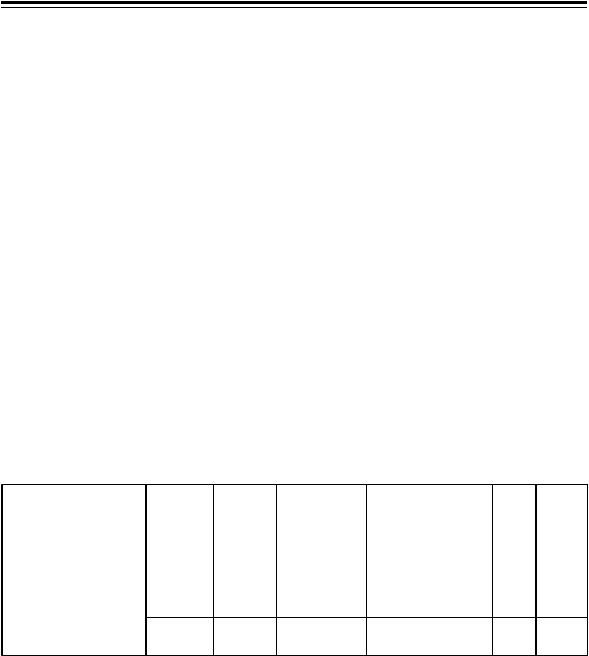
Вестник СГУПСа. Выпуск 17
А, В и Е. Для этого с целью определения весовых коэффициентов аi, bi, ei внутри каждой группы параметров А, В и Е проводится их попарное сравнение. Весовые коэффициенты отражают значимость каждого из параметров группы по отношению к другим параметрам.
При проведении факторного анализа, с одной стороны, требуется максимальное абстрагирование от конкретной реализации исследуемого объекта, но, с другой стороны, функции объекта приходится рассматривать в связи с их конкретными реализациями, в частности, чрезвычайно затрудняется оценка степени влияния каждой функции на работоспособность объекта в целом. Для вычисления относительной важности каждой функции предварительно производится экспертная оценка значимости всех функций, сводящаяся к определению степени влияния каждой из функций на другие.
Возможны различные варианты проведения экспертной оценки значимости функций. К числу наиболее доступных относится метод парных сравнений. При его использовании строится матрица, на пересечении строки и столбца которой фиксируется:
2 — если фактор Фi более значим, чем Фj; 1 — если фактор Фi равнозначен с Фj;
0 — если фактор Фi менее значим, чем Фj.
Вид матрицы парных отношений для одного из коэффициентов показан в табл. 2.
Таблица 2
Парные отношения для коэффициента А
Факторы |
Kвалификация |
Методика |
Kонтролируемость |
Использование |
Фактор |
Фактор |
|
|
персонала |
исполнения |
|
специальных технических |
среды |
материала |
|
|
|
|
|
средств контроля |
|
|
|
Kвалификация персонала |
1 |
2 |
1 |
1 |
0 |
2 |
|
Методика исполнения |
0 |
1 |
0 |
0 |
0 |
2 |
|
Kонтролируемость |
1 |
2 |
1 |
2 |
0 |
0 |
|
Использование специальных |
1 |
2 |
0 |
1 |
0 |
2 |
|
технических средств контроля |
|||||||
|
|
|
|
|
|
||
Фактор среды |
2 |
2 |
2 |
2 |
1 |
2 |
|
Фактор материала |
0 |
0 |
2 |
0 |
0 |
1 |
Аi( Ai = 36) |
5 |
9 |
6 |
6 |
1 |
9 |
Вес фактора ai |
0,14 |
0,25 |
0,17 |
0,17 |
0,03 |
0,25 |
Кроме весов по 10-балльной шкале определяются значения факторов Аn, Вn, и Еn. Уточненные значения коэффициентов получаются перемножением весов факторов на их значения.
Независимо от условий эксплуатации рельсов при обработке задается только один ремонтный профиль, в то время как геометрия поперечного профиля головки рельса зависит в значительной степени от эксплуатационных условий пути. Это требует использования ряда ремонтных профилей, позволяющих учитывать эксплуатационные требования различных участков пути. Для операции «Выбор ремонтного профиля рельса» предлагается корректировочное мероприятие, которое заключается в замене существующего ряда ремонтных профилей на более рациональный, обеспечиввающий экономию снимаемого слоя металла и наилучшие условия контактирования рельса с колесом.
Оценить эффективность использования различных типов ремонтных профилей и влияние их на производительность технологического процесса можно по
172
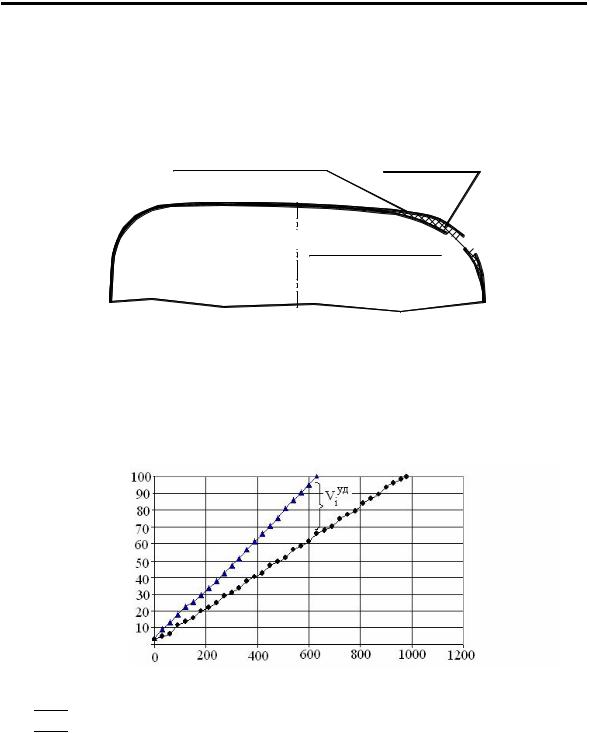
Е.О.Юркова,О.А.Шаламова,Е.В.Самойлова
значениям удельного съема металла, необходимого для формирования каждого типа ремонтных профилей. Площадь, заключенная между фактическим поперечным профилем, полученным в результате измерения, и ремонтным профилем, по значению равняется удельному съему металла. На рис. 1 показано наложение двух профилей для прямого участка пути.
Фактический профиль |
Удельный |
|
съем металла |
Ремонтный профиль
Рис. 1. Наложениеремонтного профилярельса на фактический поперечныйпрофиль рельса
В литературе [2] приводятся зависимости потери металла от наработки рельсов, которые были построены по результатам анализа значений удельного съема металла, снимаемого при использовании различных рядов ремонтных профилей, как это показано на рис. 2.
Потеряметалла, %
Значение тоннажа, млн т брутто
—при использованииремонтных профилей,применяющихся внастоящее время;
—при использованиипредлагаемого ряда ремонтных профилей
Рис. 2.Потеря металла при использовании различных рядовремонтных профилей
По данным, полученным в результате исследований, определено, что для прямого участка пути рельсов Р65 средняя экономия удельного объема металла на одну рельсовую нить при замене рядов ремонтных профилей составила 4•10–5 м2/м. При этом снижается интенсивность износа абразивного инструмента и повышается производительность технологического процесса шлифования рельсов примерно на 20 %.
Таким образом, замена рядов ремонтных профилей позволила снизить коэффициент RPZ со 144 до 97,39.
173

Вестник СГУПСа. Выпуск 17
Замена используемых шлифовальных кругов Лужского абразивного завода на круги с повышенной износостойкостью Челябинского абразивного завода для проведения операции «Назначение режимов шлифования» позволила снизить коэффициент RPZ со 180 до 92,5.
Стоимость абразивного круга производства Челябинского завода в 1,6 раза меньше, притом что срок его службы примерно в 4 раза продолжительнее. Соответственно, за 1 ч шлифовки изнашивается 20 % круга обычной производительности и 5 % нового круга (это в 4 раза меньше), что сокращает стоимость одной машино-смены рельсошлифовального поезда. Годовой экономический эффект от внедрения новых кругов достигается за счет повышенной стойкости абразивного инструмента и выигрыша в цене [3].
После проведения FMEA, с целью подтверждения экономической эффективности проведенного анализа и принятыхкорректировочных мероприятийрассчитан экономический эффект, который составил более 10 млн р./год при эксплуатации одного рельсошлифовального поезда.
Литература
1.ГОСТ Р 51814.2–2001. Метод анализа видов и последствий потенциальных дефектов.
2.Аксенов В.А.,Юркова Е.О. Ремонтныепрофили длярельса Р65// М-лы всерос. науч.- практ. конф. ученых транспортных вузов, НИИ, инженерных работников и представителей академической науки «Актуальные проблемы Транссиба на рубеже веков». Хабаровск, 2000.
С. 230–233.
3.АксеновВ.А.,ШаламовВ.А.,ЮрковаЕ.О.ПовышениепроизводительностиРШПза счет рационализации параметровтехнологического процесса шлифования рельсовв пути// Новые технологии—железнодорожному транспорту:подготовка специалистов,организацияперевозочного процесса, эксплуатация технических средств. Омск, 2000. С. 334–336.
4.Бабич М.А., Гришина Т.Г. Управление качеством на современных предприятиях. М.:
СТАНКИН, 2004. 457 с.
174
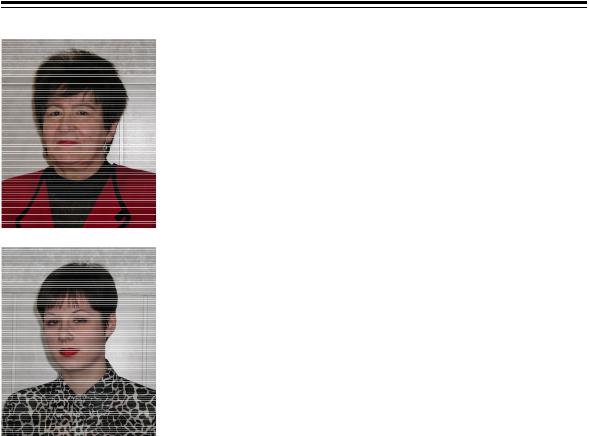
Л.Б.Тихомирова,О.В.Болотова
Тихомирова Людмила Борисовна — кандидат технических наук,профессоркафедры«Технологиятранспортногомашиностроенияиэксплуатациямашин»Сибирскогогосударственногоуниверситетапутейсообщения.В1963г.окончилаНовосибирскийэлектротехническийинститут.С1970работаетвСГУПСе.Имеет230печатных работ,втомчисле2монографии.
БолотоваОльгаВикторовнаокончилаСибирскийгосударственный университет путей сообщения в 2000 г. В 2003 г. защитила диссертационнуюработу насоискание ученойстепени кандидата техническойнаук.Внастоящеевремядоценткафедры«Технология транспортногомашиностроенияиэксплуатациямашин».Имеетболее 20печатныхработ.
УДК 625.143:620.17
Л.Б. ТИХОМИРОВА, О.В. БОЛОТОВА
ИЗМЕНЕНИЕ НАПРЯЖЕННО-ДЕФОРМИРОВАННОГО СОСТОЯНИЯ И СТРУКТУРЫ ГОЛОВКИ РЕЛЬСА В ПРОЦЕССЕ ЭКСПЛУАТАЦИИ
Рассмотрено изменение физико-механических свойств и структуры головки рельсов в процессе эксплуатации.
В процессе эксплуатации под воздействием колес подвижного состава происходит непрерывное изменение физико-механических свойств рельсов. Для выявления природы изменения свойств рельсов, определяющих их эксплуатационные качества, нами проводились физико-механические и структурные исследования.
Влияние длительности эксплуатации на физико-механические свойства материала головки рельса проследили по результатам измерения микротвердости новых рельсов и рельсов с различной эксплуатационной наработкой, металлографический анализ структуры осуществляли методом оптической микроскопии.
Измерения показали, что поверхностные слои металла головки нового рельса имеют отличные от основного металла значения микротвердости. Наибольшей микротвердостью обладает поверхностный слой — 3600–3700 МПа. По мере удаления от поверхности микротвердость снижается и достигает минимального уровня на глубине 0,5–2 мм. При переходе к внутренним слоям металла значение микротвердости стабилизируется и составляет для нового рельса в объемно-за- каленном состоянии 3000–3100 МПа. Такой характер изменения микротвердости по высоте головки рельса в исходном состоянии связан с различием в структуре
175
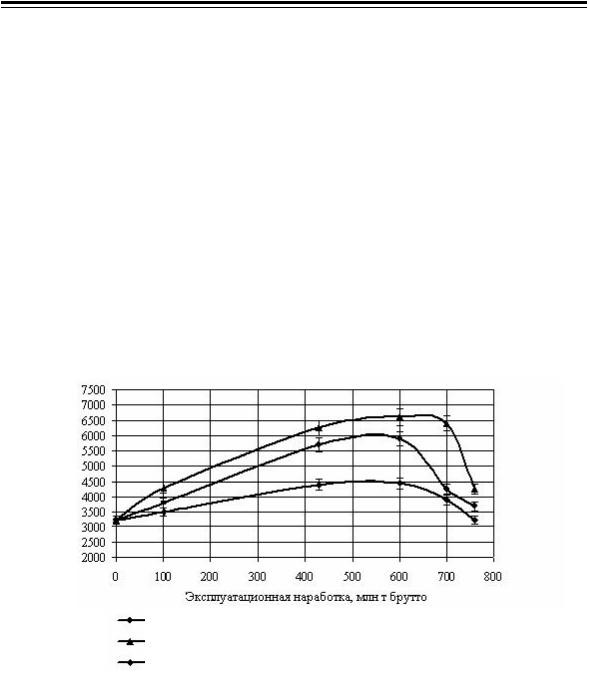
Вестник СГУПСа. Выпуск 17
поверхностных и внутренних слоев. Металлографический анализ показал, что поверхностный слой представляет собой окалину, ниже которой располагается обезуглероженный слой. Эти слои металла головки, обладая пониженными показателями механических свойств, ухудшают эксплуатационные характеристики рельсов. В процессе эксплуатации, с увеличением объема наработки до определенного уровня, в поверхностном слое головки рельсов наблюдалось непрерывное увеличение микротвердости (рис. 1). Так, по рабочей выкружке при наработке 100 млн т брутто микротвердость увеличилась в 1,4 раза, при наработке 430 млн т брутто — в 1,9 раза и при наработке 600 млн т брутто — в 2 раза по сравнению с аналогичными данными для нового рельса. По оси катания микротвердость повышалась менее интенсивно и практически не изменилась по нерабочей выкружке головки рельса. Такое различие в значениях микротвердости по поперечному сечению головки рельса связано с неравномерным распределением нагрузки от колеса на рельс, когда максимальное давление приходится именно на зону рабочей выкружки. Металл в этой области упрочняется наиболее интенсивно и, соответственно,происходитболеезначительное увеличение микротвердости.
Микротвердость Н ,МПа 200
—ось симметрии;
—рабочая выкружка;
—нерабочая выкружка
Рис. 1. Изменение микротвердости в поверхностном слое головки рельса в процессе эксплуатации
При наработке, соответствующей моменту изъятия рельсов из пути, происходит резкое снижение микротвердости в поверхностном слое головки рельса, свидетельствующее о протекании процессов разупрочнения. Падение микротвердости наблюдается сначала по оси катания, после чего начинается разупрочнение рабочей выкружки.
Разупрочнение поверхностного слоя в процессе эксплуатационной наработки подтверждено также данными металлографического анализа (рис. 2). На темплете можно выделить несколько характерных слоев. Первый слой — это разупрочненный металл, в котором отсутствуют следы пластической деформации.
Ниже располагается наклепанный слой с ярко выраженной текстурой. По мере удаления от поверхности темплета текстура становится менее выраженной
176
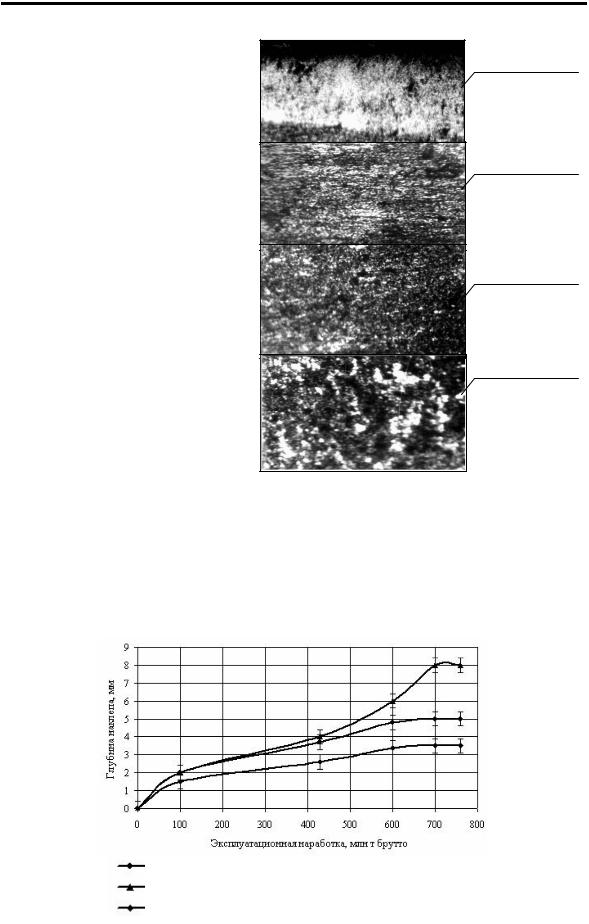
177
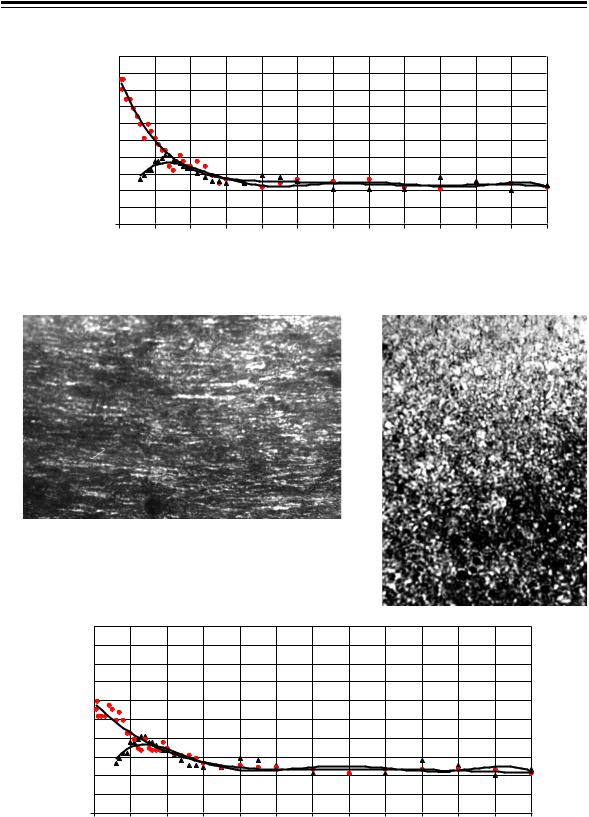
Вестник СГУПСа. Выпуск 17 |
|
|
|
|
|
|
|
|
|
|
|
||
а) |
7000 |
|
|
|
|
|
|
|
|
|
|
|
|
МПа |
|
|
|
|
|
|
|
|
|
|
|
|
|
6500 |
|
|
|
|
|
|
|
|
|
|
|
|
|
6000 |
|
|
|
|
|
|
|
|
|
|
|
|
|
, |
|
|
|
|
|
|
|
|
|
|
|
|
|
|
|
|
|
|
|
|
|
|
|
|
|
|
|
200 |
5500 |
|
|
|
|
|
|
|
|
|
|
|
|
Н |
5000 |
|
|
|
|
|
|
|
|
|
|
|
|
Микротвердость |
|
|
|
|
|
|
|
|
|
|
|
|
|
4500 |
|
|
|
|
|
|
|
|
|
|
|
|
|
4000 |
|
|
|
|
|
|
|
|
|
|
|
|
|
3500 |
|
|
|
|
|
|
|
|
|
|
|
|
|
3000 |
|
|
|
|
|
|
|
|
|
|
|
|
|
2500 |
|
|
|
|
|
|
|
|
|
|
|
|
|
2000 |
|
|
|
|
|
|
|
|
|
|
|
|
|
|
|
|
|
|
|
|
|
|
|
|
|
|
|
|
0 |
1 |
2 |
3 |
4 |
5 |
6 |
7 |
8 |
9 |
10 |
11 |
12 |
|
|
|
|
|
Расстояние отповерхности, мм: |
|
|
|
|||||
|
|
— до шлифования; |
|
— после шлифования |
|
|
|||||||
б) |
|
|
|
|
|
|
|
в) |
|
|
|
|
|
г)
|
7000 |
|
|
|
|
|
|
|
|
|
|
|
|
,МПа |
6500 |
|
|
|
|
|
|
|
|
|
|
|
|
6000 |
|
|
|
|
|
|
|
|
|
|
|
|
|
5500 |
|
|
|
|
|
|
|
|
|
|
|
|
|
200 |
|
|
|
|
|
|
|
|
|
|
|
|
|
|
|
|
|
|
|
|
|
|
|
|
|
|
|
Н |
5000 |
|
|
|
|
|
|
|
|
|
|
|
|
Микротвердость |
4500 |
|
|
|
|
|
|
|
|
|
|
|
|
4000 |
|
|
|
|
|
|
|
|
|
|
|
|
|
3500 |
|
|
|
|
|
|
|
|
|
|
|
|
|
3000 |
|
|
|
|
|
|
|
|
|
|
|
|
|
2500 |
|
|
|
|
|
|
|
|
|
|
|
|
|
|
|
|
|
|
|
|
|
|
|
|
|
|
|
|
2000 |
|
|
|
|
|
|
|
|
|
|
|
|
|
0 |
1 |
2 |
3 |
4 |
5 |
6 |
7 |
8 |
9 |
10 |
11 |
12 |
|
|
|
|
|
Расстояние отповерхности, мм: |
|
|
|
|
||||
|
— после шлифования; |
— после шлифования с последующей наработкой |
Рис. 4. Микротвердость и структура металла поверхностного слоя головки рельса:
а — микротвердость головки рельса до и после шлифования; б — структура металла головки рельса дошлифования; в —структура металла головки рельса после шлифования; г — микротвердость головки рельса после шлифования и с последующей наработкой
178

Л.Б.Тихомирова,О.В.Болотова
Изменение микротвердости и металлографический анализ металла головок рельсов после профильного шлифования показали, что применяющаяся в настоящее время технология восстановления служебных свойств рельсов приводит к разупрочнению поверхностного слоя, выражающемуся в снижении микротвердости (рис. 4, а) и изменении структуры металла (рис. 4, б, в). Если до шлифования структура металла поверхностного слоя головки рельса имела характерную для наклепа ярко выраженную ориентацию зерен, то после шлифования она приблизилась к структуре исходного объемно-закаленного рельса. Микротвердость поверхностногослоя падает до уровня, соответствующего объемно-закаленному состоянию, вследствие частичного снятия эффекта упрочнения теплом, выделяющимся в процессе шлифования. В этот момент трещины, зародившиеся в процессе эксплуатации, выход которых на поверхность тормозился наклепанным слоем, получат интенсивное развитие, в результате чего значительно снизится долговечность рельсов.
При дальнейшей эксплуатации вновь происходит накопление пластической деформации, возникает наклеп, и микротвердость поверхностного слоя повышается вновь (рис. 4, г).
Таким образом, проведенные исследования показали, что характер распределения микротвердости по профилю головки рельса и структура металла головки рельса определяются эксплуатационно-технологическими факторами.
На основании вышесказанного можно сделать вывод, что необходимо проводить корректировку режимов существующего процесса восстановления рельсов шлифованием для снижения степени разупрочнения поверхностного слоя головки рельса, которое является неблагоприятным фактором с точки зрения долговечности рельсов.
Литература
1.Периодичность структурных изменений при ротационной пластической деформации / В.И.Владимиров,Б.К.Барахтин,С.А.Иванов,И.А.Овидько,А.Е.Романов//Физикаметаллов
иметалловедение. 1987. № 6. С. 1185–1191.
2.Тушинский Л.И. Классификация структур сплавов и физико-механических моделей пластической деформации// Структуры объемно иповерхностноупрочненнойстали. Новоси-
бирск, 1984. С. 3–13.
179
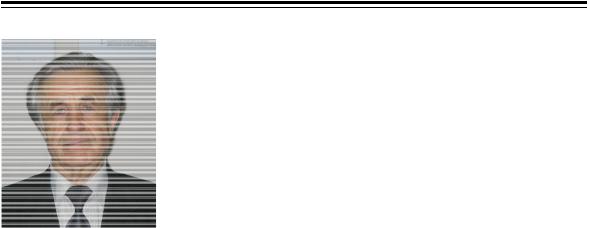
Вестник СГУПСа. Выпуск 17
Привалов Петр Васильевич — доктор технических наук, профессоркафедры«Технологиятранспортногомашиностроенияиэксплуатациямашин»Сибирскогогосударственногоуниверситетапутей сообщения.ОкончилАлтайский сельскохозяйственныйинститутв 1960г.поспециальности«Механизацияпроцессовсельскохозяйственногопроизводства».
Научноенаправление —техническаяэксплуатациямашин,техно- логииисредстватехническогообслуживанияивосстановления.
УДК 629.113.004.5
П.В. ПРИВАЛОВ
ТЕОРЕТИЧЕСКИЕ ОСНОВЫ ФОРМИРОВАНИЯ РЕМОНТНООБСЛУЖИВАЮЩЕЙ БАЗЫ АВТОТРАНСПОРТНЫХ ПРЕДПРИЯТИЙ
Рассматривается методика совершенствования системы технического обслуживания (ТО) машин для формирования специализированной службы ТО.
Повышение эксплуатационной надежности автомобилей обеспечивается как на стадии производства, так и совершенствованием методов технической эксплуатации, что требует создания необходимой технической базы для поддержания машинного парка в исправном состоянии. Если трудоемкость изготовления современного грузового автомобиля равна 120-150 нормо-часов, то трудоемкость ремонтно-обслуживающих воздействий, в зависимости от интенсивности эксплуатации, ежегодно составляет от 700 до 9000 нормо-часов.
Важными элементами решения проблемы управления техническим состоянием машин являются совершенствование технологических процессов и организации ТО и ремонта, рационализация структуры инженерно-технических служб, методов принятия инженерных решений по оснащению рабочих постов технологическим оборудованием. В работе рассматриваются методы проектирования, реконструкции и технологического перевооружения производственно-техничес- кой базы автотранспортных предприятий (АТП) и централизованных производств, гаражей и станций технического обслуживания.
Функционирование технических средств в значительной мере обусловлено постоянно меняющимися составляющими: потоком требований на их работу, трудоемкостью и продолжительностью устранения неисправностей машин, т. е. системой массового обслуживания (СМО). В сфере технической эксплуатации автомобильного парка примерами СМО являются: посты, линии, участки ремонтных мастерских, склады запчастей, топливо- и маслораздаточные колонки АЗС.
Система массового обслуживания состоит из следующих основных элементов [1–3]: входящий поток требований, очередь, обслуживающие аппараты (каналы) и выходящий поток требований. СМО классифицируются по ограничениям на длину очереди (с потерями и без потерь); количеству каналов обслуживания (одно- и многоканальные); типу обслуживающих аппаратов (универсальные и специализированные); порядку обслуживания (одно- и многофазовые, т. е. на одном посту и линии ТО); числу обслуживающих аппаратов (ограниченные и
180