
773
.pdf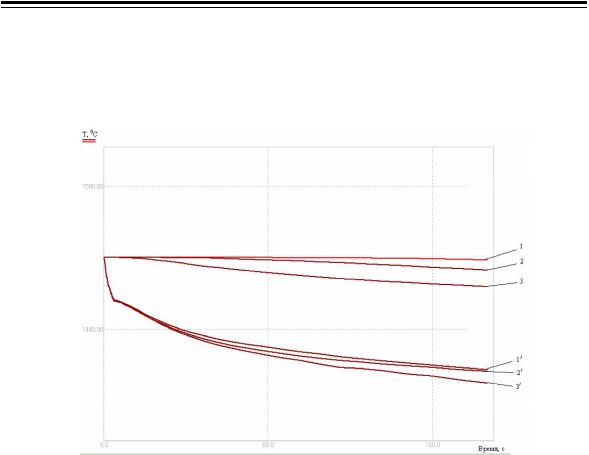
Н.М.Чернов,К.А.Медведев
Изменение температуры расплава в любой точке можно представить в виде графика. Пример графического представления охлаждения расплава в металлоприемнике при начальной температуре стали в точке 1, равной 1470 °С, приведен на рис. 4.
Рис. 4. Изменениетемпературы сталипо сечениюметаллоприемника в контрольных точках при начальнойтемпературе расплава 1470 °С
Методика моделирования направленного затвердевания отливки представлена на рис. 5 при начальной температуре формы 550 °С и температуре расплава на входе в форму 1470 °С.
В табл. 3 показана температура стали в характерных точках отливки при начальной температуре расплава на входе в форму 1470 °С.
По результатам моделирования определяется продолжительность затвердевания отливки, которая составляет 68 с.
Продолжительность выдержки отливки под давлением приняли равной 1,5 мин, т. е. больше продолжительности ее затвердевания.
По результатам моделирования определили толщину слоя затвердевшей стали от дна металлоприемника в момент затвердевания отливки, которая равна 12,69 мм. Поэтому минимальную величину пресс-остатка приняли равной 30 мм.
Таблица 3
Температура стали в характерных точках КФ при начальной температуре расплава 1470 °С
Kонтрольная точка |
Температура после 30 с от начала заливки, °С |
Температура после 68 с от начала заливки, °С |
1 |
1446,06 |
1299,24 |
2 |
1428,98 |
1287,40 |
3 |
1309,37 |
1155,35 |
4 |
1308,28 |
1128,37 |
5 |
1240,89 |
1045,27 |
Температура металла перед выпуском из печи tвып принимается по данным компьютерного моделирования на основе оптимизации температуры расплава на входе в форму, т. е. в точке 0:
191
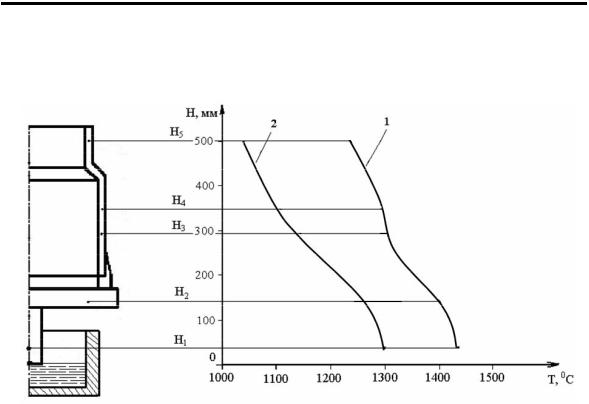
Вестник СГУПСа. Выпуск 17
tвып = tвх + t, |
(4) |
где t — потери температуры металла при переливе его из печи в ковш, а затем в металлоприемник.
Рис. 5. Изменение температуры стали в зависимости от высоты в характерных точках отливки при начальнойтемпературе расплава 1470 °С:
1 — через 30 с после начала заливки; 2 — через 60 с в момент затвердевания отливки
Опытные работы показали эффективность применения системы компьютерного моделирования LVMFlow для установления гидродинамических режимов, уточнения величины пресс-остатка, сечения питателей и определения температурных параметров процесса ЛВМКД.
Характеристика отливки, параметры и режимы процесса ЛВМКД, по которым произведено изготовление опытной партии корпусов, приведены в табл. 4.
Таблица 4
Характеристика отливки, параметры и режимы процесса ЛВМКД
Наименование |
Значение |
Масса модели, кг |
4,4 |
Масса модели литниковой системы, кг |
0,86 |
Масса модельного блока, кг |
5,26 |
Температура запрессовки модельного состава в пресс-форму, °С |
56–58 |
Температура выплавления модельного состава, °С |
120–130 |
Масса керамической формы, кг |
15,4 |
Температура прокалки KФ, °С |
950–980 |
Температура выпуска металла из печи, °С:для стали 12Х18Н9ТЛ |
1600–1610 |
для стали 10Х18Н11БЛ |
1590–1600 |
Температура нагрева контейнеров, металлоприемников и пуансонов после облицовки |
|
жидкостекольной смесью, °С |
300–500 |
Давление рабочей жидкости под поршнем гидроцилиндра при кристаллизации отливки, МПа |
3,5–4,0 |
Величина пресс-остатка, мм |
40–50 |
Продолжительность заливки, с |
7–8 |
Выдержка кристаллизующегося расплава под давлением, с |
90 |
Температура нагрева ковша, °С |
800–900 |
Линейная усадка сталей в процессе осуществления ЛВМKД, % |
1,8–2,0 |
Отливки ЛВМКД отличаются от ЛВМ отсутствием характерного для сталей 12Х18Н9ТЛ и 10Х18Н11БЛ дефекта поверхности «питтинга» и повышенным
192
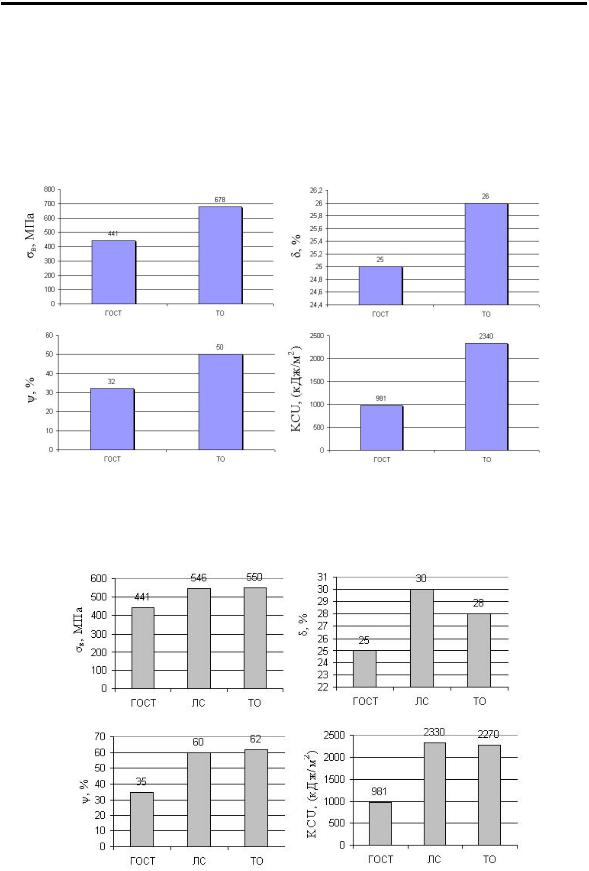
Н.М.Чернов,К.А.Медведев
уровнем механических свойств образцов из стали 12Х18Н9ТЛ и плотности. Плотность образцов из стали 12Х18Н9ТЛ одинакового химического состава, залитых из одной плавки методом ЛВМ, составляет 7800 кг/м3, а ЛВМКД —
8100 кг/м3.
Результаты испытаний механических свойств образцов из стали 12Х18Н9ТЛ, полученных методом ЛВМКД, и их сравнение проиллюстрированы на рис. 6, а из стали 10Х18Н11БЛ — на рис. 7.
а) |
б) |
в) |
г) |
Рис. 6. Сравнение значений механических свойствобразцов из стали 12Х18Н9ТЛ:
а — предел кратковременной прочности; б — относительное удлинение; в — относительное сужение; г — ударная вязкость;
ГОСТ — значение в соответствии с ГОСТ 977-88; ТО — термообработанные, полученные методом ЛВМКД
а) |
б) |
в) |
г) |
Рис. 7. Сравнение значений механических свойствобразцов из стали 10Х18Н11БЛ:
а — предел кратковременной прочности; б — относительное удлинение; в — относительное сужение; г — ударная вязкость;
ГОСТ — значение в соответствии с ГОСТ 977–88; ЛС — в литом состоянии, полученные методом ЛВМКД;ТО — термообработанные, полученныеметодом ЛВМКД
193

Вестник СГУПСа. Выпуск 17
Отливки из сталей 12Х18Н9ТЛ и 10Х18Н11БЛ соответствуют требованиям нормативной документации на поковки и сварно-штампованные узлы для энергомашиностроения, а себестоимость серийного изготовления одной литой детали «корпус» в два раза ниже штампосварного варианта.
Результаты проведенной работы показали, что ЛВМКД относится к перспективным технологическим процессам в производстве тонкостенных изделий сложной конфигурации с повышенными требованиями к качеству литья из коррозионно-стойких сталей аустенитного класса.
Литература
1.Способлитьяповыплавляемыммоделямскристаллизациейподдавлением/В.И.Томилов, Н.М. Чернов, Ю.А. Караник, В.Н. Гречко. Патент РФ № 2048954 27.11.95. Бюл. № 33.
2.Чернов Н.М.,Гречко В.Н. Исследованиегидравлической прочности оболочковых форм
//Литейное производство. 1995. № 6. С. 24–25.
3.Литьеповыплавляемыммоделям/ В.Н.Иванов,С.А.Казеннов,Б.С.Курчманидр.;Под общ. ред. Я.И. Шкленника,В.А. Озерова. 3-е изд.,перераб. идоп. М.: Машиностроение, 1984. 408 с.
4.ЧерновН.М.,ИгнатовА.И.,ГречкоВ.Н.Литьеалюминиевыхзаготовокповыплавляемым моделям с кристаллизацией под давлением // Литейное производство. 1995. № 2. С. 12–13.
194
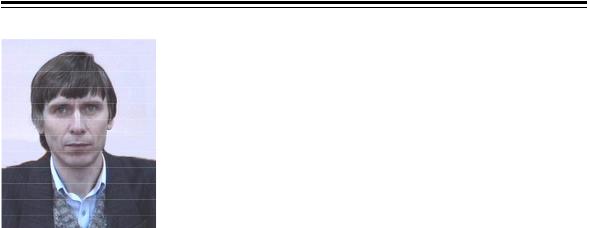
В.М.Тихомиров
Тихомиров Виктор Михайлович родился 27 ноября 1954 г. в
г.Барнауле.В1977г.окончилсамолетостроительный факультет Новосибирскогоэлектротехническогоинститутапоспециальности «Динамикаипрочностьлетательныхаппаратов»ибылнаправленпо распределению наработу инженером в НИЛ прочности НИИЖТа.
Общийнаучно-педагогическийстажВ.М.Тихомировасоставляет 28 лет. В 1984 г. он окончил заочную аспирантуру при кафедре «Строительнаямеханика».
В.М.Тихомировпринималучастиевработенад17научно-иссле- довательскимитемами.НаучнаядеятельностьВиктораМихайловича восновномсвязанассовершенствованиемэкспериментальныхметодовмеханикитвердогодеформируемоготела.С1993г.онявляется руководителем НИЛ прочности. В 1995 г. защитил кандидатскую
диссертацию.РешениемВАК от1997г.В.М.Тихомировуприсвоенозваниедоцента.В2004г. онзащитилдокторскуюдиссертацию.
ПорезультатамисследованийВ.М.Тихомировымопубликованоболее70научно-методичес- кихтрудов.
УДК 620.178.311.6
В.М. ТИХОМИРОВ
РАСЧЕТНО-ЭКСПЕРИМЕНТАЛЬНЫЙ АНАЛИЗ РАЗВИТИЯ УСТАЛОСТНОЙ ТРЕЩИНЫ В МОНОЛИТНОЙ ПАНЕЛИ С РЕБРАМИ
Вработе представлено исследование развития усталостной трещины в панели с ребрами при
еециклическом нагружении. Зафиксирована скорость роста трещины и форма ее фронта на каждом этапе испытаний вплоть до разрушения.
Разработана методика расчета коэффициентов интенсивности напряжений (КИН) для трещин с криволинейным фронтом. Создана численная модель панели с растущей трещиной, граничные условия в которой определялись на основе экспериментально измеренных перемещений берега усталостной трещины.
Проведен анализ скорости роста трещины при ее развитии через ребро панели. Определены значения КИН в характерных точках фронта трещины на каждом этапе ее продвижения. Построена диаграмма разрушения в виде зависимости скорости роста трещины от размаха КИН.
Во всех известных исследованиях предполагается, что для материалов с высоким уровнем прочности (сталь, алюминиевые и титановые сплавы) скорость роста трещины не зависит от вида напряженного состояния. Однако даже при однородном растяжении тонких пластин фронт усталостной трещины не прямолинейный из-за различной степени стеснения деформаций по ширине пластины, от плоского напряженного состояния на поверхности до плоской деформации во внутренних точках. В таких переходных зонах развитие усталостных трещин не изучено. Мало исследовано влияние на скорость роста и геометрию трещин подкрепляющих элементов типа ребер, а также поля остаточных напряжений, вызванных технологией изготовления и режимом эксплуатации элементов конструкций.
В данной работе проведено экспериментально-расчетное исследование развития усталостной трещины в монолитной панели с двумя ребрами при ее циклическом растяжении.
195
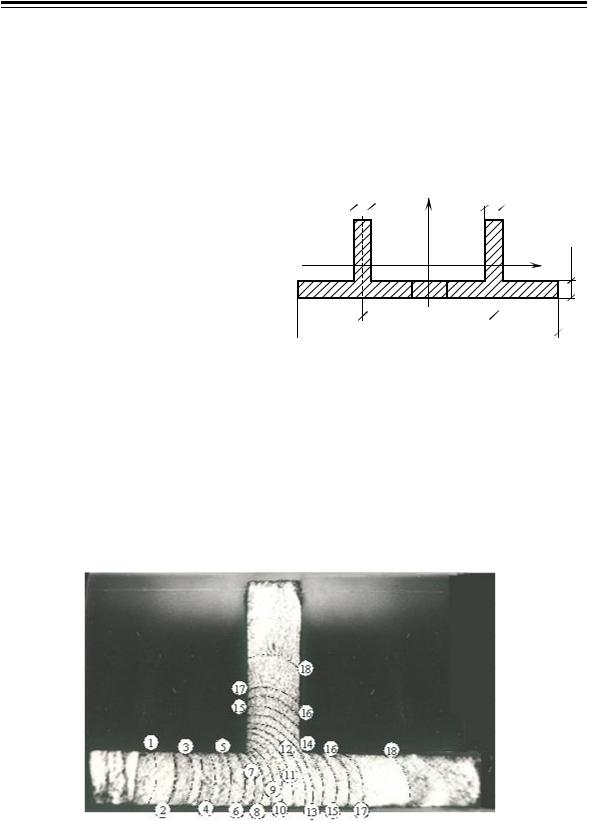
Вестник СГУПСа. Выпуск 17
Циклические испытания панели
В конструкции летательных аппаратов широко применяются монолитные оребренные панели. Расчет долговечности таких элементов с учетом развития магистральных усталостных трещин — достаточно сложная проблема. В основном рассматриваются бесконечные панели с ребрами малой величины, где отсутствует влияние границ, а разрушенный подкрепляющий элемент моделируется с помощью двух ребер, выходящих на кромки разреза [1]. На рис. 1
представлена геометрия поперечного |
8,4 |
|
y |
8,4 |
|
сечения панели, которая изготовлена |
|
|
|||
|
|
|
|
||
из алюминиевого сплава Д16Т со сле- |
|
|
|
|
|
дующими механическими характерис- |
|
|
|
z |
8,4 |
тиками: модуль продольной упругос- |
|
|
|
||
|
|
|
|
||
|
|
|
|
|
|
ти Е = 70000 МПа; коэффициент |
|
|
|
|
|
|
|
|
|
|
|
Пуассона = 0,3; условный предел |
|
|
|
|
|
|
|
|
|
|
|
текучести 0,2 = 240 МПа; предел |
|
65,6 |
|
|
|
|
|
|
|
|
|
|
|
130 |
|
|
|
прочности в = 480 МПа. |
|
|
|
|
|
|
|
|
|
|
|
В процессе циклическогорастяже- |
Рис. 1. Геометрия поперечного сечения панели |
||||
ния в панели из острого центрального |
надреза длиной 20 мм зародилась и развивалась усталостная трещина. Параметры циклического нагружения поддерживались гидравлическим пульсатором
ГРМ-1: Pmax = 50 кН; Pmin = 10 кН; частота нагружений — 600 цикл/мин (10 Гц). Для того чтобы зафиксировать поэтапное изменение геометрии фронта трещины
при распространении ее через тело панели, применялся способ перегрузки. Для этого максимальная нагрузка на некоторое время повышалась на 20 % (до Pmax = = 60 кН). Таким образом, было зафиксировано на разных стадиях испытаний восемнадцать положений усталостной трещины (рис. 2). Перегрузка в момент достижения трещины положения № 18 вызвала разрушение панели.
Рис.2. Видизлома панелис зафиксированнымифронтами усталостнойтрещины на восемнадцатиэтапах испытаний
Усилие на панель передавалось через шарнирные захваты. Однако в сечении, где распространялась усталостная трещина, наблюдалось внецентренное (относительно оси z, см. рис. 1) растяжение, параметры которого контролировались четырьмя симметрично расположенными тензорезисторами.
196

В.М.Тихомиров
На каждом этапе испытаний после перегрузки испытательная машина останавливалась и при статическом нагружении, используя метод голографического муара, проводили измерения перемещений берегов усталостной трещины. Для этого на исследуемую поверхность панели наносился металлизированный растр с частотой f = 850 линий/мм. В коллимированном пучке монохроматического света на фотопластинке, прикрепленной непосредственно на образец (рис. 3), регистрировалась голограмма. Источником света являлся гелий-неоно- вый лазер с длиной волны излучения = 632,8 нм.
Коллимированный |
P |
пучок света |
Образец |
|
|
|
Клеевой слой |
|
Металлизированный |
|
растр |
|
Фотопластинка |
P
Рис. 3. Схема записи голограмм
Величина перемещения в направлении, перпендикулярном плоскости трещины, определялась по следующей зависимости [2]:
|
1 |
n |
n |
, |
(1) |
|
|||||
|
2f |
1 |
2 |
|
|
|
|
|
|
|
где n1 и n2 — порядки полос, зафиксированные на картине полос интерференции (рис. 4, б) при восстановлении голограммы с двух симметричных направлений, которые соответствуют первому дифракционному порядку. Здесь вершина трещины находится в начале координат ( , r). В этой точке начинается темная полоса интерференции нулевого порядка (n = 0).
а) |
|
|
|
б) |
|
|
n |
l = 31,4 мм P= 15кН |
|
|
|||
2,0 |
|
|
|
n2 |
||
|
n1 |
|
|
|||
1,5 |
|
|
|
|
2 |
|
1,0 |
|
|
|
|
|
|
0,5 |
|
- направлениенаблюдения- |
1 |
|||
|
- направлениенаблюдения+ |
r |
||||
|
|
|||||
0 |
|
|
|
|
||
0,2 0,6 |
1,0 |
1,4 |
1,8 r, мм |
|
||
-0,5 |
n1=0 |
|||||
|
|
|
-1 |
-1,0
-2
-1,5 -2,0
Рис. 4. Распределение порядка муаровых полос у вершины трещины
197
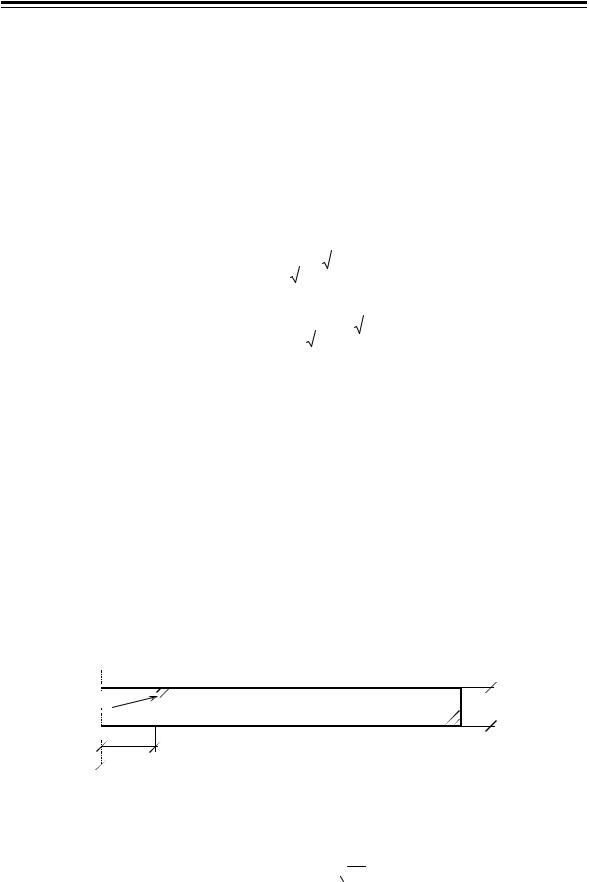
Вестник СГУПСа. Выпуск 17
На рис. 4, a представлено распределение порядков полос интерференции, зафиксированных на восьмом этапе испытаний при статической нагрузкеР= 15 кН.
Определение коэффициента интенсивности напряжений по криволинейному фронту трещины
По перемещениям берега трещины в работе [2] определяется коэффициент интенсивности напряжений (КИН) КI в образцах из тонких листов. Для этого используются известные соотношения перемещений при растяжении пластины с центральной трещиной:
— при плоском напряженном состоянии, которое всегда реализуется на поверхности образца,
r |
2KI |
|
|
|
|
|
|
|
|
2rc r2 ; |
(2) |
||||
|
|
|
|||||
|
E c |
|
|
|
|
||
|
|
|
|
|
|
— при плоском деформированном состоянии
r |
2KI 1 2 |
|
|
|
|
|||
|
2rc r2 , |
(3) |
||||||
|
|
|
|
|||||
E c |
||||||||
|
|
|
|
где с — полудлина трещины; r — расстояние до вершины трещины; Е, — модуль упругости и коэффициент Пуассона материала.
Однако на рис. 2 видно, что фронт усталостной трещины не прямолинейный. Поэтому для проверки зависимостей (2) и (3) методом конечных элементов был проведен расчет напряженно-деформированногосостояния пластины с центральной трещиной, имеющей криволинейный фронт (рис 5). Фронт трещины имел форму дуги окружности радиусом 10 мм, таким же, как на первых четырех этапах испытаний панели. Размеры конечных элементов вблизи вершины трещины были выбраны следующие 0,25 0,25 0,5 мм. На рис. 6 приведены результаты расчета перемещений берега трещины в срединной плоскости и на краю пластины. Кривая 1 соответствует перемещениям берега трещины, определенным по формуле (2); кривая 3 — по формуле (3); кривая 2 показывает перемещение точек, лежащих на поверхности пластины; кривая 4 соответствует перемещениям точек берега трещины в срединной плоскости пластины. По данным метода конечных элементов была определена величина КИН КI в соответствии с методикой, изложенной в работе [3].
R=10
c=15
8,4
Рис. 5. Среднее сечение пластины при численноммоделировании
Значение КИН, рассчитанное в точке фронта, выходящей на свободную поверхность, на 20 % превысило теоретическую величину КИН для бесконечной
пластины с центральной трещиной (KI c ). Погрешность расчета для
средней точки, в которой реализуется плоская деформация, составила менее 1 %. Для восемнадцати вариантов геометрии трещины (см. рис. 2) был проведен численный анализ напряженно-деформированного состояния конечноэлемент-
198
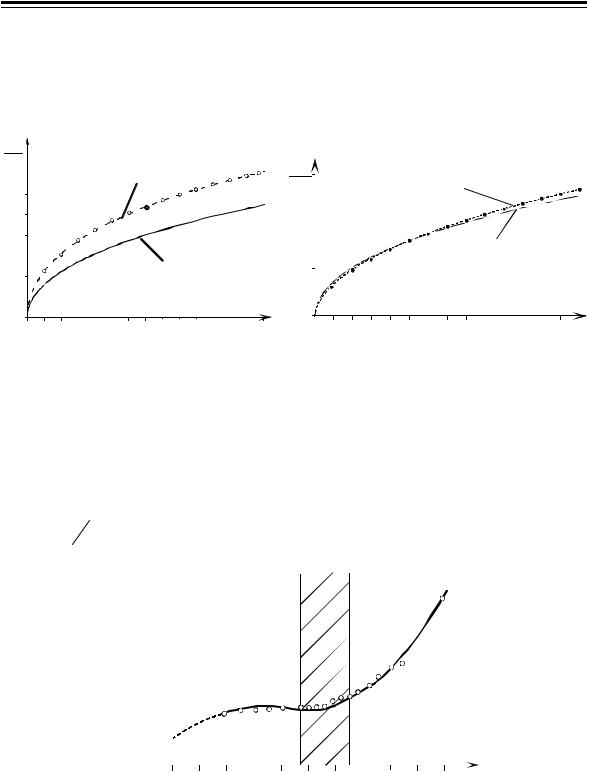
В.М.Тихомиров
ной модели исследуемой панели. С учетом результатов проведенных исследований КИН определялся в точках фронта трещины, лежащих по середине панели или по середине ребра, где реализуется плоское деформированное состояние.
а) |
|
б) |
|
E |
|
|
|
KI |
2 |
E |
|
|
KI |
4 |
|
3,0 |
|
||
|
|
|
2,0
2,0 |
3 |
|
1,0 |
|
|
1 |
|
|
1,0 |
|
|
|
|
|
|
|
|
|
|
|
||||
|
|
|
|
|
|
|
|
|
|
|
0 |
0,05 |
0,10 0,15 |
0,20 r/c |
0 |
0,05 |
0,10 |
0,15 |
0,20 r/c |
||
|
|
|
|
Рис.6. Перемещениеберега трещины: |
|
|
|
|||
|
|
а — плоское напряженное состояние; б — плоская деформация |
|
На рис. 7 представлена зависимость приведенного КИН k от характерного размера трещины. Здесь длина трещины l измерялась от оси симметрии панели до расчетной точки фронта усталостной трещины. Приведенная величина КИН k составила:
k |
KI |
, |
(4) |
|
|||
|
н |
|
где н P A — номинальное напряжение; А — площадь поперечного сечения панели.
k, м1/2
6,0
5,0
4,0
3,0
2,0
1,0
0 |
10 |
20 |
30 |
40 |
50 l, мм |
Рис. 7. Результаты численного определения КИН
Заштрихованная область на графике соответствует положению ребра. Для контроля правильности выбранных граничных условий на каждом этапе
нагружения перемещения берега трещины, полученные экспериментально (метод голографической интерферометрии), сравнивались с результатами метода конечных элементов. На рис. 8 сплошной линией показаны данные численного расчета на восьмом этапе испытаний, точками — экспериментально полученные
199
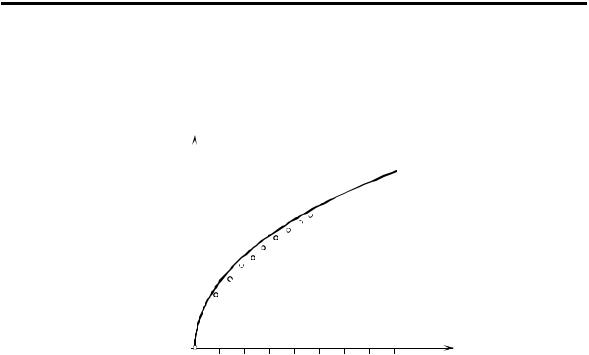
Вестник СГУПСа. Выпуск 17
значения перемещений поверхности усталостной трещины. Максимальное расхождение результатов по всем этапам испытаний составило не более 12 %. Это свидетельствует о правильности выбора граничных условий при проведении конечноэлементных расчетов.
.103, мм
7,0
6,0
5,0
4,0
3,0
2,0
1,0
0 |
0,5 1,0 1,5 2,0 r,мм |
Рис. 8. Зависимость перемещений берега трещины от r
Анализэкспериментальныхрезультатов
В момент разрушения панели, когда Рmax = 60 кН, размер трещины составил 54,7 мм. Эти данные позволили определить критический коэффициент интенсивности напряжений при усталостном разрушении данного элемента конструкции. C учетом результатов расчета КИН (см.рис. 7) было определено его критическое значение: Kfc= 23,5 МПа∙м1/2.
По поверхности излома была изучена геометрия усталостной трещины. На всех стадиях испытаний форма фронта трещины мало отличается от дуги окружности. Только в области угла, при переходе трещины в ребро, кривизна трещины увеличивается. Минимальное значение радиуса 7,25 мм имеет фронт трещины перед разрушением панели, максимальное —12 мм, в зоне соединения панели с ребром. Радиус кривизны фронта, очевидно, зависит от неравномерности поля напряжений, в котором растет трещина.
Анализ поверхности излома панели позволил рассчитать скорость роста усталостной трещины на каждом этапе испытаний (таблица).
Зависимость скорости роста трещины от величины КИН аппроксимируют различными соотношениями [4]. Для сравнения с известными экспериментальными результатами была использована формула Пэриса
l |
C KI m, |
(5) |
|
N |
|||
|
|
здесь N — число циклов нагружения; С и m — постоянные коэффициенты. Обработка экспериментальных данных по методу наименьших квадратов
(исключая результаты на последнем этапе испытаний) позволила вычислить постоянные С и m: C = 4,78•10–8, m = 3,97.
200