
773
.pdf
|
|
|
|
|
|
|
|
|
В.М.Тихомиров |
|||
|
Результаты анализа геометрии трещины и расчета КИН |
|
|
|
|
|||||||
|
|
|
Радиус |
N , |
l |
|
|
|
|
|
|
|
Номер |
Положение |
Размер |
кривизны |
N , |
KI, |
|
|
|
Приведенный |
|||
этапа |
точки |
трещины |
фронта |
цикл |
мм/цикл |
|
|
|
|
|
|
|
МПа м |
|
КИН k, м |
||||||||||
|
|
l, мм |
трещины, |
|
||||||||
|
|
|
|
|
|
|
|
|
|
|
||
|
|
|
мм |
|
|
|
|
|
|
|
|
|
|
|
|
|
|
|
|
|
|
|
|
|
|
1 |
в панели |
14,2 |
|
|
|
4,77 |
|
|
|
1,85 |
|
|
2 |
в панели |
17,2 |
10,55 |
|
|
5,16 |
|
|
|
2,00 |
|
|
3 |
в панели |
20,0 |
10,55 |
100000 |
2,80 10–5 |
5,15 |
|
|
|
2,00 |
|
|
4 |
в панели |
22,6 |
9,96 |
85000 |
3,06 10–5 |
5,25 |
|
|
|
2,04 |
|
|
5 |
в панели |
24,8 |
9,68 |
70000 |
3,14 10–5 |
5,38 |
|
|
|
2,09 |
|
|
6 |
в панели |
28,5 |
8,11 |
65000 |
3,23 10–5 |
5,50 |
|
|
|
2,14 |
|
|
7 |
в панели |
30,0 |
8,06 |
39000 |
3,84 10–5 |
5,38 |
|
|
|
2,09 |
|
|
8 |
в панели |
31,4 |
8,06 |
39000 |
3,59 10–5 |
5,42 |
|
|
|
2,11 |
|
|
9 |
в панели |
32,9 |
8,52 |
33000 |
4,54 10–5 |
5,60 |
|
|
|
2,18 |
|
|
10 |
в панели |
34,4 |
9,27 |
24000 |
6,25 10–5 |
5,92 |
|
|
|
2,30 |
|
|
11 |
в панели |
35,7 |
10,23 |
22000 |
6,52 10–5 |
6,46 |
|
|
|
2,51 |
|
|
в ребре |
|
10,23 |
22000 |
5,91 10–5 |
5,92 |
|
|
|
2,30 |
|
|
|
|
|
|
|
|
|
|
||||||
12 |
в панели |
37,7 |
10,77 |
18000 |
1,00 10–4 |
6,38 |
|
|
|
2,48 |
|
|
в ребре |
|
10,85 |
18000 |
7,22 10–4 |
6,22 |
|
|
|
2,42 |
|
|
|
|
|
|
|
|
|
|
||||||
13 |
в панели |
39,0 |
12,00 |
12000 |
1,08 10–4 |
6,74 |
|
|
|
2,62 |
|
|
в ребре |
|
11,95 |
12000 |
1,02 10–4 |
6,31 |
|
|
|
2,45 |
|
|
|
|
|
|
|
|
|
|
||||||
14 |
в панели |
40,9 |
10,87 |
11000 |
1,55 10–4 |
7,46 |
|
|
|
2,90 |
|
|
в ребре |
|
9,70 |
11000 |
1,27 10–4 |
7,74 |
|
|
|
3,01 |
|
|
|
|
|
|
|
|
|
|
||||||
15 |
в панели |
43,0 |
8,48 |
9000 |
2,33 10–4 |
8,29 |
|
|
|
3,22 |
|
|
в ребре |
|
8,60 |
9000 |
1,67 10–4 |
8,29 |
|
|
|
3,22 |
|
|
|
|
|
|
|
|
|
|
||||||
16 |
в панели |
45,2 |
7,50 |
8000 |
2,50 10–4 |
9,20 |
|
|
|
3,57 |
|
|
в ребре |
|
7,55 |
8000 |
2,25 10–4 |
9,06 |
|
|
|
3,52 |
|
|
|
|
|
|
|
|
|
|
||||||
17 |
в панели |
47,4 |
7,35 |
5000 |
4,40 10–4 |
9,54 |
|
|
|
3,71 |
|
|
в ребре |
|
7,25 |
5000 |
3,20 10–4 |
9,62 |
|
|
|
3,74 |
|
|
|
|
|
|
|
|
|
|
||||||
18 |
в панели |
54,7 |
7,25 |
3500 |
20,86 10–4 |
15,66 |
|
|
|
6,09 |
|
|
в ребре |
|
7,25 |
3500 |
15,14 10–4 |
13,95 |
|
|
|
5,42 |
|
|
|
|
|
|
|
|
|
|
В работе [5] предложено полные кинетические диаграммы усталостного разрушения алюминиевых сплавов и сталей от порогового КИН Кth до критического Kfc описывать следующей зависимостью:
l |
K |
|
K |
m |
|
|
|
max |
th |
|
|||
|
C |
|
|
. |
(6) |
|
N |
K |
K |
||||
|
fc |
|
max |
|
При этом показатель степени m для разных материалов изменяется незначительно и имеет среднее значение 1,65 (± 5 %). Также был введен параметр а, который непосредственно связан со значением степени m:
201
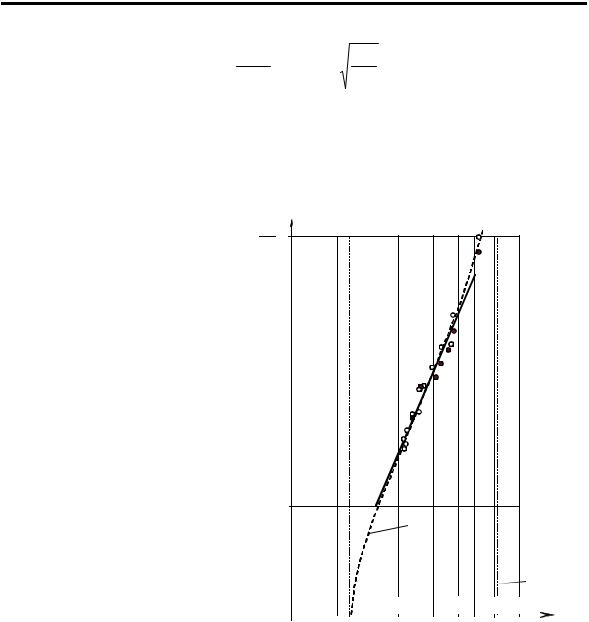
Вестник СГУПСа. Выпуск 17 |
|
|
|
|
|
|
|
|
|
|||
|
|
|
a m |
p 1 |
lg p |
|
Kfc |
|
|
|
|
|
|
|
|
p 1 |
p |
K |
. |
|
|
|
(7) |
||
|
|
|
|
|
|
|
|
|
|
|||
|
|
|
|
|
|
|
th |
|
|
|
|
|
|
Для различных металлов он оказался практически постоянным a 1,61. |
|||||||||||
Обработка данных для исследуемой панели показала, что при K = 2,27 МПа∙м1/2, |
||||||||||||
K |
|
|
|
|
|
|
|
|
|
th |
|
|
|
= 16,0 МПа∙м1/2 имеем С =4,56•10–4; m =1,71; а =1,58, что согласуется с |
|||||||||||
fc |
|
|
|
|
|
|
|
|
|
|
|
|
показателями, приведенными в работе [5]. |
|
|
|
|
|
|
||||||
|
На рис. 9 представлена кинетическая диаграмма усталостного разрушения |
|||||||||||
сплава Д16Т, построенная по результатам эксперимента. Прямая 1соответствует |
||||||||||||
обработке экспериментальных |
|
|
|
|
|
|
|
|
|
|||
данных по формуле (5), кри- |
l |
|
|
|
|
|
|
|
||||
|
|
|
|
|
|
|
|
|
||||
вая 2 — аппроксимация с по- |
N |
|
|
|
|
|
|
|
||||
мм/цикл |
|
|
|
|
|
|
|
|||||
мощью зависимости (6). Чер- |
10-3 |
|
|
|
|
|
|
|
||||
ными точками отмечены дан- |
|
|
|
|
|
|
|
|
|
|||
ные, соответствующиераспро- |
|
|
|
|
|
|
|
|
|
|||
странениюусталостнойтрещи- |
|
|
|
R=0,2 |
|
|
|
|
||||
ны через ребро. |
|
|
|
|
|
|
|
|||||
|
По результатам проведен- |
|
|
|
|
|
|
|
|
|
||
ного расчетно-экперименталь- |
10-4 |
|
|
|
|
|
|
|
||||
ного анализа развития устало- |
|
|
|
|
|
|
|
|
|
|||
стной трещины в монолитной |
|
|
|
|
|
|
|
|
|
|||
панели при |
ее циклическом |
|
|
|
1 |
|
|
|
|
|
||
растяжении |
можно сделать |
|
|
|
|
|
|
|
|
|||
следующие выводы: |
|
|
|
|
|
|
|
|
|
|||
|
1. Геометрия фронта тре- |
10-5 |
|
|
|
2 |
|
|
|
|||
щины хорошо может быть |
|
|
|
|
|
|
|
|
||||
спрогнозирована только во |
|
|
|
|
|
|
|
|
|
|||
внутренних точках трехмерно- |
|
|
|
|
|
|
|
|
Kfc |
|||
го тела, так как известные |
|
|
|
|
|
|
|
|
||||
способы не дают точного зна- |
|
0 |
|
|
5 |
|
10 |
15 20 |
||||
чения КИН в точках фронта |
|
2,5 K |
|
7,5 |
12,5 K |
,МПа.м1/2 |
||||||
|
|
|
||||||||||
трещины, которые близко ле- |
|
|
|
th |
|
|
I |
|
||||
|
|
|
|
|
|
|
|
|
||||
жат к поверхности тела. |
Рис.9. Кинетическая диаграмма для сплава Д16Т |
|||||||||||
|
2. Усталостная трещина, |
|
|
|
|
|
|
|
|
|
||
очевидно, стремится занять такое положение, которое максимально выравнивает |
||||||||||||
поле напряжений, что согласуется с гипотезой Черепанова [6]. Однако не всегда |
||||||||||||
по фронту усталостной трещины реализуются равные условия нагружения, так |
||||||||||||
называемый равновесный фронт (КИН КI |
= const). |
При |
распространении |
|||||||||
трещины в монолитной панели (см. рис. 2) видно, что при приближении к ребру |
||||||||||||
жесткости скорость роста трещины имеет разную величину в каждой точке |
||||||||||||
фронта. После прорастания трещины через точку сопряжения ребра с плоско- |
||||||||||||
стью панели скорости точек фронта выравниваются, и равновесный фронт имеет |
||||||||||||
место вплоть до разрушения панели. |
|
|
|
|
|
|
|
|||||
|
3. Кинетические диаграммы, построенные по данным испытаний элементов |
|||||||||||
конструкций, хорошо согласуются с результатами известных испытаний стан- |
||||||||||||
дартных образцов, а также учитывают влияние остаточных напряжений, |
||||||||||||
которые всегда имеются при изготовлении и меняются в процессе эксплуатации |
||||||||||||
конструкции. |
|
|
|
|
|
|
|
|
|
|
||
202 |
|
|
|
|
|
|
|
|
|
|
|
|

В.М.Тихомиров
Литература
1.МаксименкоВ.Н.,ЦендровскийА.В.Оценкаусталостнойпрочностиворебренных панелях
//Динамика и прочность элементов авиационных конструкций. Новосибирск:Изд-во НЭТИ, 1987. С. 113–118.
2.Тырин В.П. Применение метода голографической интерферометрии для определения
коэффициента интенсивности напряжений // ПМТФ. 1990. Т. 30. № 1. С. 155–158.
3.Тихомиров В.М.Аналитические зависимостидля определенияперемещений поверхности разреза вплоских итрехмерных телах // Экспериментально-расчетныеметоды исследования задач прочности: Сб. науч. тр. СГУПСа. Новосибирск, 2003. С. 9–33.
4.ГуревичС.Е.,ЕдидовичЛ.Д.Оскоростираспространениятрещины ипороговых значениях КИН впроцессе усталостного разрушения // Усталость и вязкость разрушенияметаллов. М.:
Наука, 1978. С. 36–79.
5.Ярема С.М. Исследование роста усталостных трещин и кинетические диаграммы усталостного разрушения // ФХММ. 1977. Т. 13. № 4. С. 3–23.
6.Черепанов Г.П. Механика хрупкого разрушения. М.: Наука, 1974. 640 с.
203
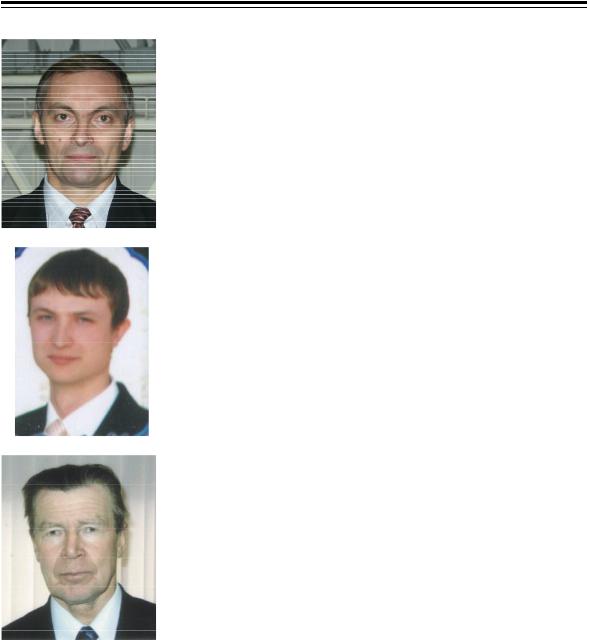
Вестник СГУПСа. Выпуск 17
БахтинСергей Анатольевич— профессор,кандидат техническихнаук,профессоркафедры«Мосты»Сибирскогогосударственного университетапутей сообщения, выпускник факультета«Мосты и тоннели» НИИЖТа1974г.
Вестунг Илья Альфредович — инженер производственно-тех- нического отдела ООО «Опора», выпускник факультета «Мосты и тоннели»Сибирскогогосударственногоуниверситетапутейсообще-
ния2007г.
Пыринов Борис Владимирович — доцент, кандидат техничес-
кихнаук,главныйспециалистпроизводственно-техническогоотдела
ООО «Опора», выпускник факультета «Мосты и тоннели» НИИЖТа
1955г.
УДК 624.21.011.1:674.028.9
С.А. БАХТИН, И.А. ВЕСТУНГ, Б.В. ПЫРИНОВ
РАЗРАБОТКА НОВОГО КОМБИНИРОВАННОГО ПРОЛЕТНОГО СТРОЕНИЯ МОСТОВ ИЗ КЛЕЁНОЙ ДРЕВЕСИНЫ ПОД ПЕШЕХОДНУЮ НАГРУЗКУ
Для повышения архитектурной выразительности пешеходных путепроводов при строительстве многоуровневых развязок в больших городах предлагается новое комбинированное пролетное строение: пологая деревянная клеёная арка с металлической затяжкой.
Одной из важнейших проблем современных больших городов является строительство многоуровневых развязок с выразительными архитектурными решениями, способных с минимальными затратами обеспечить движение постоянно растущего потока автотранспорта.
204
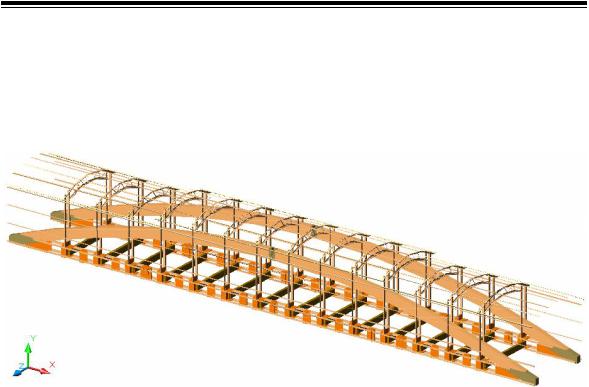
С.А.Бахтин,И.А.Вестунг,Б.В.Пыринов
Одним из фрагментов решения данной проблемы может стать предлагаемое пролетное строение пешеходных путепроводов комбинированной конструкции
«деревянная клеёная арка с металлической затяжкой» индустриального изготовления пролетом 32,4 м и шириной пешеходной дорожки 3 м, обеспечивающее перекрытие 6–8 полос автомобильного движения (рис. 1).
Рис. 1. Разработанноепролетное строение(деревоплита прохожей части иостекление не показаны)
К достоинствам данного пролетного строения можно отнести: «стремительность» арки (отношение стрелы подъема пологой арки к пролету 1 : 11); внешнюю «безраспорность» конструкции благодаря балке-затяжке; минимальную строительную высоту, равную при «езде понизу» высоте поперечной балки — 0,6 м; малый собственный вес; удобство монтажа и минимум трудозатрат на него (пространственный монтажный блок составляет полпролета и имеет массу всего 19,4 т — см. рис. 4); индустриальность изготовления и технологичность узлов соединения металлических и деревянных элементов и т.д.
Внастоящее время во многих странах, в том числе и в России, находит широкое применение клеёная древесина. Это новый передовой материал, обладающий малой плотностью, относительно высокой удельной прочностью и жесткостью, эстетичностью,химическойстойкостью, легкой обрабатываемостью, достаточной долговечностью при соответствующей обработке. Кроме того, широкое применение этого материала обусловлено постоянным возобновлением запасов древесины.
ВНовосибирске существует фирма «СТИЛВУД», которая занимается изготовлением конструкций из клеёной древесины по современной технологии,
втом числе криволинейных, для различных сооружений. Но конструкции ограничены некоторыми размерами, а в частности, длиной элементов (до 18–20 м).
Для статического расчета выбранной комбинированной конструкции были построены линии влияния внутренних усилий и деформаций, выявлены невыгодные загружения постоянной и временной нагрузками (рис. 2). Необходимо было подобрать такие загружения, при которых возникали максимальные нормальные, касательные и приведенные напряжения в арке, работающей на сжатие с изгибом и в балке-затяжке, работающей на растяжение с изгибом.
205
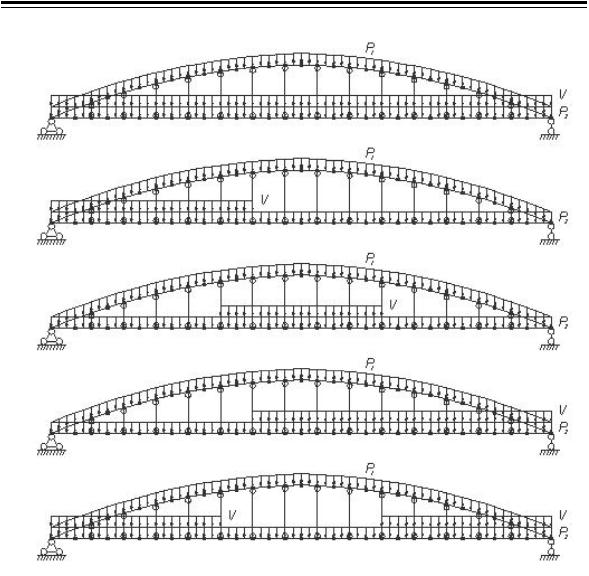
Вестник СГУПСа. Выпуск 17
а)
б)
в)
г)
д)
Рис. 2. Загруженияпролетного строения:
а— определение максимальных продольных усилий вконструкции; б— определениеМmax,0.25;
в— определение Мmax,0.5; г — определение Мmin,0.25; д – определение Мmin,0.5
По полученным результатам были запроектированы поперечные сечения основных элементов, в частности, клеёная арка представляет собой криволинейный стержень постоянного сечения (600 280 мм — высота по фасаду 1 : 54 от пролета). Балка-затяжка состоит из четырех уголков минимального сечения L100 100 10, объединенных планками.
Наибольшие проблемы возникли при проверке устойчивости сжатой арки, которая выполнялась в пространственной постановке при помощи программного обеспечения SCAD. Из-за действия подвесок в вертикальной плоскости арка имеет существенные запасы по устойчивости. Но в горизонтальной плоскости только совместный учет пространственного характера работы подвесок, поперечных балок и каркаса остекления, играющего роль верхних поперечных связей (см. рис. 1), позволил получить приемлемые коэффициенты запаса:
•первое сочетание (постоянная нагрузка плюс полная пешеходная) — 1,25;
•второе сочетание (постоянная нагрузка плюс полная ветровая) — 2,42;
•третье сочетание (постоянная нагрузка плюс 0,8 пешеходной плюс 0,25 ветровой) — 1,39.
206
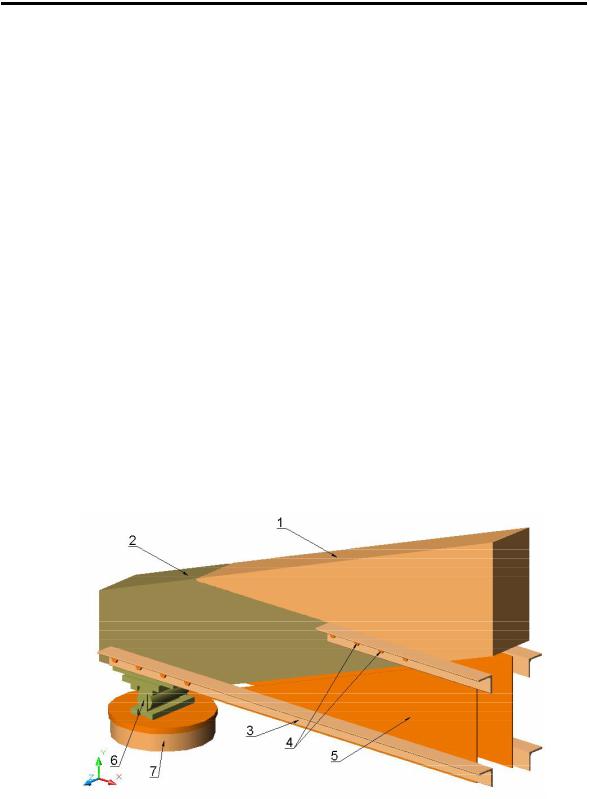
С.А.Бахтин,И.А.Вестунг,Б.В.Пыринов
Одной из важных проблем было конструирование основных узлов пролетного строения, которые, во-первых, должны были обеспечивать стыковку двух материалов — металла и дерева, а во-вторых, учитывать технологию изготовления клеёных конструкций на фирме «СТИЛВУД». Достоинством всех узлов можно считать минимум трудозатрат и максимальную простоту на монтаже. Наиболее интересными и оригинальными можно считать следующие узлы (см. рис. 1, 3 и 4):
•Опорный узел прикрепления арки к балке-затяжке, где происходит передача распора, и который требует постановки всего восьми болтов на монтаже. Для обеспечения надежного соединения, торец арки на заводе наглухо вклеивается в металлический башмак из листового металла толщиной 10 мм (см. рис. 3).
Вместах постановки высокопрочных болтов в заводских условиях в арку вклеиваются металлические трубки наружным диаметром 42 мм и толщиной стенки 8 мм, чтобы воспринять усилия натяжения высокопрочных болтов.
•Центральный узел монтажной стыковки двух половинок арки, так как по технологии заводского изготовления невозможно получить клеёную конструкцию длиной более 18–20 м.
•Узлы монтажных стыков балки-затяжки (в четвертях и середине пролета) и узлы стыковки подвесок с аркой и балкой решены при помощи простейших горизонтальных и вертикальных планок на болтах. Учитывая то, что подвески работают при некоторых сочетаниях нагрузок на сжатие, их конструкция представляет собой комбинированный элемент: два уголкаL100 100 10, объединенных глухими нагелями с вставкой из клеёной древесинысечением 280 100мм.
Рис. 3. Узловое соединение аркии балки-затяжки:
1 — арка; 2 — металлический башмак; 3 — уголки затяжки; 4 — высокопрочные болты; 5 — вертикальные планки; 6 — катковая опорная часть; 7 — опора
Технология сооружения комбинированного пролетного строения предусматривает предварительную сборку металлической балки-затяжки на специально выложенных брусьях и установку половинки арки с опиранием на пятую подвеску, которая поддерживает арку и работает на сжатие. Причем выбор
207
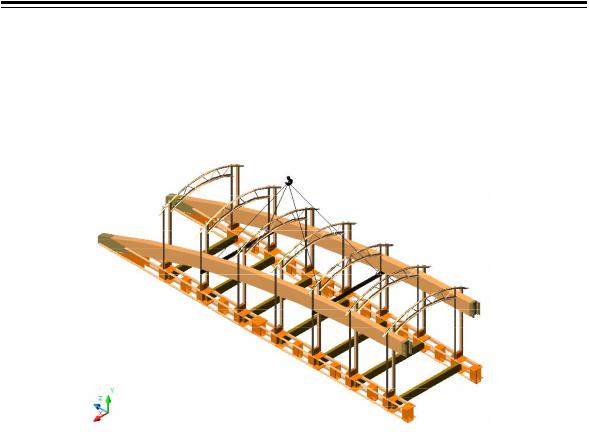
Вестник СГУПСа. Выпуск 17
данной подвески определялся дополнительным расчетом для обеспечения минимальных прогибов половинки арки, что позволит беспрепятственно установить все последующие подвески пролетного строения и состыковать половинки арок.
Далеесобираетсяпространственныймонтажныйэлемент—половинапролетно- го строения массой 19,4 т, который был рассчитан на монтажные нагрузки в момент строповки и в момент установки данного блока на временную опору (см. рис. 4).
Рис. 4. Пространственный монтажный блок массой 19,4 т
Сравнение технико-экономических показателей пешеходных путепроводованалогов, построенных в Новосибирске в 2005–2006 гг., показало достаточную перспективность предлагаемой комбинированной конструкции, судя по расходу материалов на 1 м2 проезжей части (таблица).
Расход материалов на 1 м2 проезжей части пешеходных путепроводов-аналогов
Пролетные строения путепроводов-аналогов |
Расход материалов на 1 м2 проезжей части |
||
|
Металл, т |
Железобетон, м3 |
Древесина, м3 |
Металлическая ферма пролетом 44 м по типовому проекту № 723/3 |
0,273 |
0,055 |
— |
Индивидуальная металлическая балка, проектировки ООО «Опора» пролетом 33 м |
0,303 |
0,111 |
— |
Предлагаемая деревянная арка с металлической затяжкой пролетом 34,2 м |
0,155 |
0,042 |
0,27 |
Разработанное комбинированноепролетное строение является определенным вкладом в расширение применения деревянных клеёных конструкций в области мостостроения и в решении современных проблем больших городов.
208
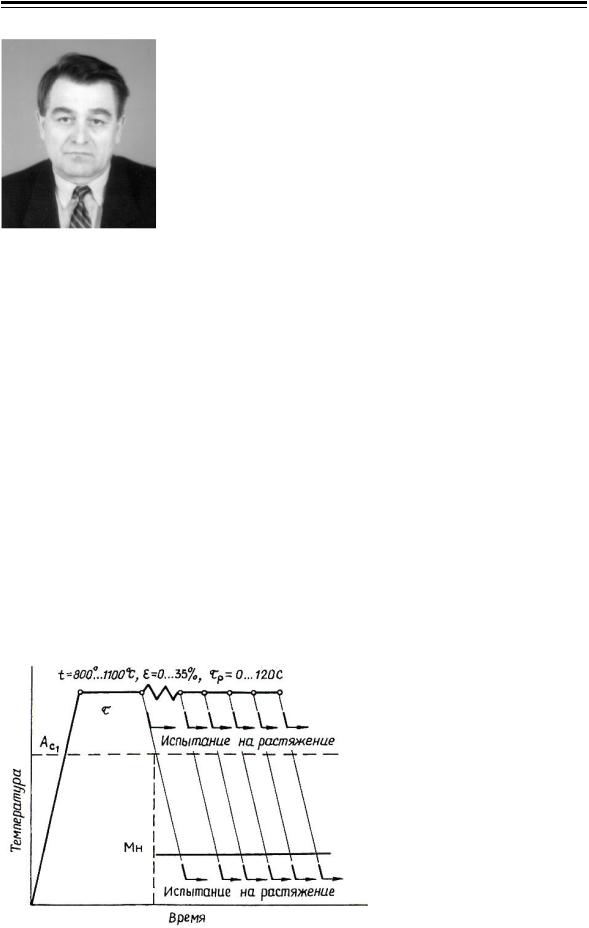
В.В.Решедько
Решедько Владимир Васильевич — кандидат технических наук,доценткафедры«Технологиятранспортногомашиностроенияи эксплуатациямашин»Сибирскогогосударственногоуниверситета путей сообщения.Родился в1945г.В 1968 г.окончил факультет «Механизациясельскогохозяйства»НСХИ.В1977г.окончиласпирантуруНЭТИ(НГТУ). С1978г.и понастоящее времяработаетна кафедре«Технологиятранспортногомашиностроенияиэксплуатация машин»СГУПСа. Имеетболее 70печатных работ.
УДК 621.785
В.В. РЕШЕДЬКО
ТЕРМОПЛАСТИЧЕСКАЯ ОБРАБОТКА В ТЕХНОЛОГИЯХ МАШИНОСТРОИТЕЛЬНОГО ПРОИЗВОДСТВА
Рассмотрен способ изготовления и восстановления деталей из углеродистых сталей термопластической обработкой. Приведены результаты экспериментальных исследований на всех этапах обработки. Способ позволяет осуществлять формообразование с созданием высокого уровня показателей конструктивной прочности при изготовлении и восстановлении деталей.
Горячая пластическая обработка в процессах машиностроительного производства используется сравнительно давно. Все виды, связанные с горячей деформацией при формообразовании элементов и деталей: горячая ковка, осадка, штамповка, профильный прокат, — можно отнести к таким процессам. Горячая пластическая деформация в этом случае применяется при формообразовании с цельюполучения элементов с требуемой точностью поразмерам,форме и расположению поверхностей.
Термопластическая обработка (ТПО) включает нагрев в область аустенита, горячую пластическую деформацию, выдержку горячедеформированного аустенита и последующее охлаждение с разной скоростью (обычно закалка и отпуск) при однократном нагреве заготовки или детали (рис. 1).После выдержки горячедеформированного аустенита возможнадополнительная деформация на 2–7 % с целью повышения плотности дислокаций.
ТПО необходимо рассматривать как конечную стадию термического воздействия в технологическом процессе изготовления или восстановления деталей. После этого могут выполнятьсятолькооперации механической обработки [1].
Принципиальное отличие ТПО от существующих технологических схем зак-
209

Вестник СГУПСа. Выпуск 17
лючается в том, что выполняемые операции «не разорваны» во времени. Режимы формообразования путем горячей деформации и последующей термической обработки являются взаимно определяющими и назначаются с учетом выполнения всего комплекса операций. Режимы каждой операции ТПО не могут быть назначены независимо друг от друга, как это наблюдается в большинстве существующих технологий формообразования и последующей термической обработки (ТО) [2].
Выбор оптимальных режимов ТПО производится с учетом химического состава материала, имеющегося технологического оборудования, требуемой конструктивной прочности и сводится к назначению температуры нагрева и деформации, степени и скорости деформирования, скорости охлаждения детали и др. В общем случае выбор режимов ТПО может быть выполнен по графикам горячего деформирования в истинных координатах [3].
Согласно дислокационной теории упрочнения металлических материалов повышение конструктивной прочности углеродистой стали может происходить несколькими путями [4]:
1)повышением плотности дислокаций и «закреплением» их атомами азота, углерода (атмосферы Сноека, Котрелла и др.);
2)созданием препятствий перемещению дислокаций путем выделения субмикрочастиц упрочняющих фаз (карбидов, карбонитридов);
3)образованием в высокотемпературной области развитой полигональноячеистой структуры аустенита с последующим «наследованием» ее конечными структурами и получением высокого уровня показателей конструктивной прочности [4]. На современном этапе развития теории упрочнения сплавов данный путь является одним из наиболее перспективных.
Реализация упрочнения первым путем наблюдается после ТО. Это приводит
кповышению прочности с одновременным снижением пластичности. ТО реализует частично и второй путь упрочнения. При этом механизме упрочнения происходит сравнительно легкое перемещение менее закрепленных дислокаций, снятие пиковых напряжений и тем самым уменьшение опасности образования и развития хрупких трещин.
При ТПО реализуются все механизмы упрочнения, но в большей степени — третий путь, который обеспечивает одновременно повышение прочности и пластичности [2].
Материалом исследований выбрана углеродистая конструкционная сталь марок: сталь 20, сталь 45, сталь 70 со стандартным химическим составом, а также сталь 70, микролегированная титаном (0,1 % по массе).
Схема ТПО (см. рис. 1) отличается от схемы ТО наличием дополнительной операции — горячей деформации перед закалкой. Температурные режимы нагрева образцов под закалку, деформацию и отпуск оставались во всех случаях идентичными и варьировались в одинаковых пределах. Интервал температур нагрева образцов составлял от 800 °С до 1100 °С через 50 °С. ТПО образцов проводилась на установке, представляющей собой прокатный двухвалковый стан ДУО-300. Прокатный стан позволяет проводить горячую прокатку образцов со степенью деформации до 50 % (по толщине листа) за один проход и со скоростью деформирования порядка 3∙10–2 с–1. После закалки сталь подвергалась отпуску в течение 60 мин. Температурные режимы отпуска варьировались от
200 °С до 450 °С через 50 °С.
210