
773
.pdf
В.А.Аксенов,А.С.Ильиных
эпицентром зарождения усталостных дефектов, не даст им развиться в серьезные повреждения.
Восстановительное шлифование, осуществляемое в три и более проходов при малой скорости рельсошлифовального поезда, является достаточно медленным и дорогим процессом улучшения служебных свойств рельсов, к которому следует прибегать для формирования геометрического профиля сильно изношенных рельсов.
Применение в процессе шлифования последнего технологического прохода позволит получить на поверхности катания рельсов приемлемый уровень шероховатости и тем самым повысить долговечность рельсов.
Сочетание предупредительного шлифования с восстановительным даст возможность увеличить срок службы рельсов и сократить общие расходы на содержание пути.
Таким образом, внедрение предложенных рекомендаций в практику эксплуатации железных дорог России позволит продлить долговечность рельсов, повысить безопасность движения поездов и получить значительный экономический эффект.
Литература
1.Шлифование — эффективный способ восстановления железнодорожных рельсов / В.А.Аксенов,В.А.Шаламов,С.В.Щелоков,А.С.Ильиных,В.В.Райт,А.Б.Чаплыгин// Теория, технологияиоборудованиедляпроизводства абразивногоинструмента:Сб.науч.тр. Челябинск, 2003. С. 85–89.
2.Ильиных А.С., Тихомирова Л.Б., Тепляков С.И. Экспериментальная оценка влияния параметровкачестваповерхностинахарактеристикиусталостногоразрушениярельсов// Вестн.
СГУПСа. 2005. №11. С. 63–69.
221
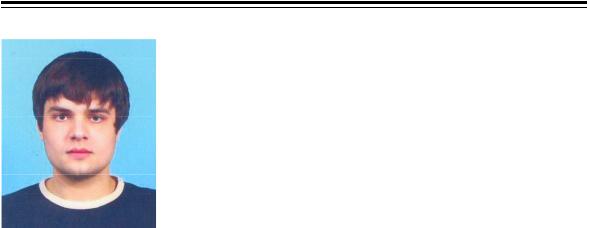
Вестник СГУПСа. Выпуск 17
Ольховиков Сергей Эдуардовичродился в 1983 г. В 2005 г. с
отличиемокончилСГУПС поспециальности«Экономикаиуправлениенапредприятии(строительство)».Обучаетсяваспирантуре. Работаетзаведующимкомпьютернымклассомиведетпедагогическуюдеятельностьнакафедре«Технология,организацияиэкономика строительства».ПроходиткурсыпереподготовкикадровСГУПСапо программе «Система менеджмента качества». Автор 5 печатных работ.
УДК 625.1:658.5
С.Э. ОЛЬХОВИКОВ
ОСОБЕННОСТИ ОРГАНИЗАЦИИ СООРУЖЕНИЯ ЖЕЛЕЗНОДОРОЖНОГО ПОЛОТНА В УСЛОВИЯХ БЛИЖНЕГО СЕВЕРА
Рассматриваются особенности организации строительства железных дорог в сложных условиях восточных районов России и обосновывается ряд ключевых решений.
Расширение масштабов добычи дефицитных ресурсов определяет все большее смещение транспортного строительства в северные районы. Это иллюстрируют, например, Генеральная схема развития сети автомобильных дорог России, строительство нефте- и газопроводов и других коммуникаций. Исследования ИЭОПП СО РАН показали, что назрела необходимость строительства СевероРоссийского транспортного коридора, включающего железную и автомобильную дороги.
Трасса Северосиба (восточной части этого коридора) приходится на зону Ближнего Севера. С позиции строительства и хозяйственного освоения районов тяготения Ближний Север отличается сложными природно-климатическими, транспортно-географическими и инженерными условиями. Это удаленность территорий от экономически развитых районов и транспортных коммуникаций, слабая их заселенность, продолжительная и суровая зима, ограниченная, преимущественно сезонная транспортная доступность, отсутствие развитой инфраструктуры.
По сравнению со среднероссийскими условиями здесь сильно, нередко в 2– 3 раза и более, возрастает стоимость ипродолжительностьстроительства. Всвязи с заболоченностью местности, отсутствием либо недостаточной распространенностью кондиционных грунтов особое значение приобретает сооружение земляного полотна — сроки и стоимость его возведения. Для поиска эффективных решений полезно обратиться к прошлому опыту строительства — прежде всего к опыту строительства железных дорог Тюмень—Сургут—Уренгой, Сургут—Нижне- вартовск, БАМа и других линий. Здесь мы остановимся на проблеме организации строительства железнодорожного полотна.
Исторический экскурс позволяет выделить 2 периода и соответственно 2 принципиальных подхода к организации строительства железнодорожного полотна:
•до 50–60-х гг.;
•последующий период до настоящего времени.
222

С.Э.Ольховиков
Для первого, в особенности довоенного периода, были характерны большая доля ручного труда, легкие технические средства и преимущественно гужевой транспорт. Они обуславливали линейную (нередко на широком фронте) организацию работ и использование дешевых дорог постройки временного типа.
В раннее, довоенное время зимой строительство нередко прерывалось. В послевоенное время (40–60-егг.) работы организовывались следующим образом: зимой осуществлялась частичная передислокация мехколонн; летом сооружалась притрассовая автовремянка; пользуясь ею, обустраивались по трассе временные поселки строителей и последовательно-параллельно выполнялись подготовительные и основные работы.
Условия движения по временной притрассовой автодороге, как правило, были сложными, скорости движения автомобилей низкими. Поездка рабочих на объект и обратно нередко занимала до половины смены и более. Работы велись в одну — полторы смены. Простои техники были велики. Производительность труда и темпы сооружения земляного полотна низкие, как и качество жизни строителей и их семей. Примером такой организации строительства являются железные дороги Ивдель—Обь, Тавда—Сотник, частично — Хребтовая—Усть- Илимская и др.
Для послевоенного периода характерен достаточно интенсивный переход к механизированному производству работ и индустриальным методам строительства. С 60-х гг. быстро нарастает грузоподъемность автосамосвалов. Это приходит в противоречие с прежней практикой строительства железной дороги на основе притрассовой автовремянки. Специальные исследования показали целесообразность и эффективность строительства категорийной притрассовой автодороги. Начиная с проекта железной дороги Тюмень—Сургут—Уренгой это постепенно входит в практику линейного строительства и сопровождается переходом — частичным либо полным — к вахтовой организации труда.
Определилась и организационная схема строительства притрассовой автодороги, других подготовительных и основных работ. В реализации объектного потока по сооружению притрассовой автомобильной дороги выделились три специализированных этапа:
•сооружение автозимника — обеспечение сквозного проезда и передислокации строительных подразделений. Развитие первоочередных работ подготовительного периода (ноябрь — январь);
•создание однополосной автодороги шириной 4,5–5,5 м с разъездами — круглогодичный проезд со скоростью до 25 км/ч при интенсивности движения до 50 авт./сут (ноябрь — апрель);
•сооружение двухполосной автодороги по проекту — обеспечение работ основногопериода строительства. Круглогодичныйпроезд автомобилейс расчетными скоростями и пропускной способностью (май — октябрь) [3].
Подготовительные работы по трассе железной дороги состоят в разбивке и закреплении оси трассы автомобильной дороги, строительстве временных поселков строителей, подготовке основания земляного полотна, передислокации строительных подразделений, организации сквозного проезда вдоль трассы для доставки механизмов, подачи элементов конструкций малых искусственных сооружений. Комплекс работ по подготовке (освоению) территории строительства заключается в расчистке полосы отвода — срезке кустарника, рубке леса,
223

Вестник СГУПСа. Выпуск 17
корчевке пней, а также выполнении осушительных работ. Сплошная вырубка леса и кустарника на перегонах производится в пределах расположения автозимника и земляного полотна самой дороги. Древесину используют для изготовления строительных конструкций, а порубочные остатки (сучья, хворост) для устройства автомобильной дороги.
Важными, относящимися к первоочередным, являются работы по осушению территории строительства. Осушительные работы состоят из устройства сети водоотводных канав и дренажей. Без осушения района работ невозможно обеспечить прочность и устойчивость земляного полотна и других сооружений, а в ряде случаев невозможно производить сами работы [1].
Важным достоинством хорошей автодороги (альтернативный вариант) является отсутствие больших колебаний в скорости движения в различное время года. Для хороших дорожных условий характерны:
а) повышение среднегодовой технической скорости движения в 2–3 раза; б) небольшие колебания между наибольшими и наименьшими среднемесяч-
ными скоростями — не более 6–8 км/ч; в) в неблагоприятное время года (дожди, распутица) превышение скорости
в общем в сравнении с наиболее высокими скоростями базового варианта [2]. Категорийная притрассовая автодорога представляет эксплуатационную ценность, поскольку пригодна для оказания услуг не только строителям
железной дороги, но и отраслям народного хозяйства и населению. Автодорога выступает фактором, улучшающим условия проживания в
Сибири, способствует повышению ее притягательности.
Притрассовая автодорога, по существу, дополняет железную дорогу, составляет с ней единую транспортную коммуникацию. На нее целесообразно передавать короткопробежные перевозки. Известна высокая эффективность полимагистралей за счет взаимодействия совмещаемых видов транспорта. При этом перевозочные расходы могут снижаться на 35–40 %, а эксплуатационные — от
10 до 20–25 % [3].
Подход с использованием категорийной притрассовой автодороги был выработан и использован при строительстве железных дорог, таких как Тюмень— Сургут—Уренгой, БАМ, и по настоящее время является актуальным.
Литература
1.Сибирь на пороге нового тысячелетия / Отв. ред. В.В. Кулешов. Новосибирск: Изд-во ИЭиОПП СО РАН, 1998.
2.Строительствожелезныхдорог:Учеб.пособиепокурсам«Организацияипланирование строительногопроизводства», «Строительствожелезных дорог»/ Под ред. В.И.Грицыка. М., 1999.
3.Ткаченко В.Я., Матвиенко В.С. Организация железнодорожного строительства: Учеб. пособие.Новосибирск, 2000.
224
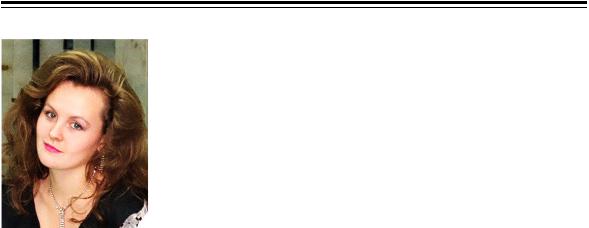
А.В.Банул
БанулАленаВикторовнаокончилав1999г.сотличием Сибирскийгосударственныйиндустриальныйуниверситетвг.Новокузнецкепоспециальности«Промышленноеигражданскоестроительство». В2003 г.— аспирантуруСГУПСа поспециальности «Строительные материалыиизделия».
УДК 666.973.2
А.В. БАНУЛ
СОСТАВ, СВОЙСТВА И ТЕХНОЛОГИЯ ПОЛУЧЕНИЯ БЕСКЛИНКЕРНЫХ ВЫСОКОПРОЧНЫХ ШЛАКОЩЕЛОЧНЫХ БЕТОНОВ
В статье приводятся оптимальные составы полученного высокопрочного шлакощелочного бетона, его свойства и технология получения. Установлено влияние добавок и технологических параметров на активность шлакощелочного вяжущего.
Современное развитие технологии бетона и железобетона неразрывно связано с необходимостью расширения номенклатуры применяемых цементов за счет разработки и внедрения эффективных в современных условиях разновидностей вяжущих, обеспечивающих получение высококачественных изделий. Все большее внимание в России и за рубежом уделяется развитию разработок и производства бесклинкерных и малоклинкерных вяжущих веществ, в значительной мере позволяющих одновременно решать задачи снижения цементоемкости строительства, ресурсо- и энергосбережения, охраны окружающей среды. К таким вяжущим, в полной мере способных конкурировать с портландцементом, относятся шлакощелочные вяжущие (ШЩВ). Высокие эксплуатационные характеристики шлакощелочных бетонов (ШЩБ) (прочность, морозостойкость, водонепроницаемость и т.д.) позволяют использовать их для возведения ответственных конструкций, в том числе и в подземном строительстве.
ШЩВ и ШЩБ известны с 60-х гг. прошлого столетия благодаря работам В.Д. Глуховского и его школы [1]. В настоящее время ШЩБ не находят масштабного применения в строительстве по ряду причин, среди которых и дороговизна наиболее эффективного затворителя ШЩБ — жидкого стекла. Поэтому одно из направлений дальнейшего развития ШЩВ и ШЩБ — поиск и использование более доступных и экономически целесообразных «заменителей» силикатных затворителей.
На базе лаборатории строительных материалов СГУПСа была проведена серия опытов, в результате которых получены высокопрочные бесклинкерные бетоны.
В работе определялись составы шлакощелочного вяжущего на основе гранулированного шлака Западно-Cибирского металлургического комбината Новокузнецка и содержащего 95–96 % углекислого натрия и 4–5 % гидрооксида натрия содощелочного плава Новокемеровского химического комбината [2, 3].
225
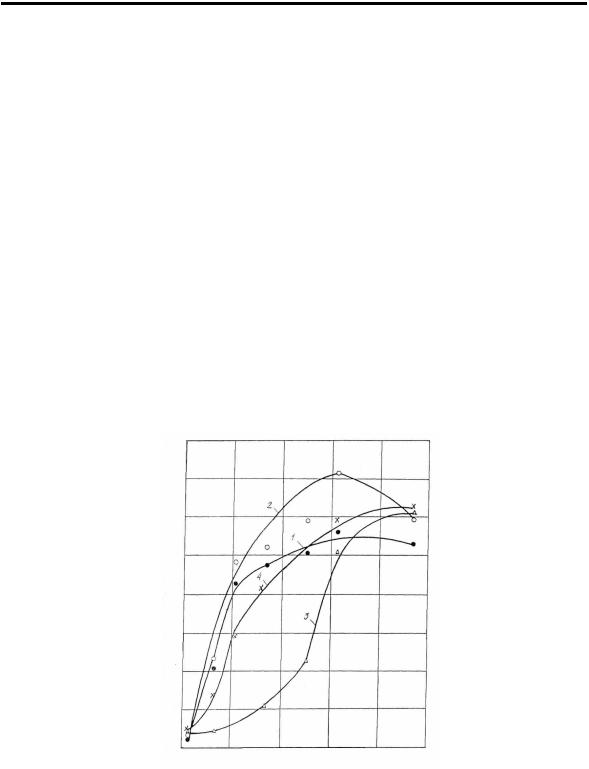


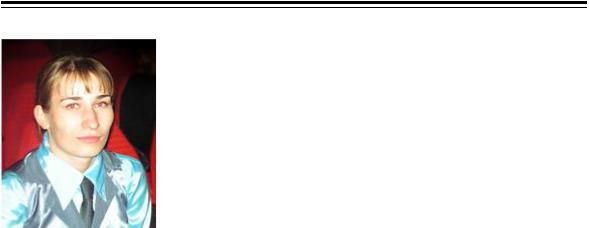
