
книги / Методы нанесения покрытий
..pdf– трудности, связанные с построением кристаллической решетки наносимого слоя, а именно: замедленная диффузия по поверхности адсорбированных частиц или адсорбированных ионов, затруднения при внедрении этих атомов в кристаллическую решетку, при образовании двумерных и трехмерных зародышей слоя; как видно, этот вид торможения связан с третьим этапом электрокристаллизации, он носит название кристаллиза-
ционного перенапряжения.
Другими причинами затруднений (торможений) при электрокристаллизации могут явиться такие, которые так жестко не связаны с той или иной стадией процесса электрокристаллизации. Они могут оказать влияние на торможение всех или нескольких стадий,
иих роль будет зависеть от уровня такого затруднения и их физи- ко-химической природы. Такими затруднениями процессов электрокристаллизации могут явиться пассивационное перенапряжение
(перенапряжение ингибирования) и химическое перенапряжение.
Пассивационное перенапряжение обусловлено прочной адсорбцией посторонних частиц, находящихся на покрываемой поверхности, и трудностями, связанными с необходимостью их удаления споверхности. В ряде случаев их не удается полностью устранить с поверхности, и тогда они сохраняются в структуре образующегосяпокрытия, снижаяегокачество.
Химическое перенапряжение обусловлено замедленным протеканием одной из химических реакций, свойственной рассматриваемому виду покрытия. Если из всей цепочки химических реакций, развивающихся при нанесении покрытия, хотя бы одна из них окажется медленно протекающей, то именно она становится той стадией процесса, которая будет определять кинетику формирования слоя и производительность процесса. Для преодоления торможений процессов электрокристаллизации, связанных как с конкретными ее стадиями, так и пассивными
ихимическими перенапряжениями, используют приложение дополнительной разности потенциалов к электролизному пространству. Величина применяемой разности потенциалов для тех или иных процессов, получения покрытий становится важ-
91
нейшим технологическим параметром покрытия, который не может изменяться в очень широком интервале значений. При недостаточной величине разности потенциалов процесс либо не идет вообще, либо протекает с очень малыми скоростями. Однако чрезмерное увеличение разности потенциалов приводит к опережающему развитию той или иной стадии, расстраивая процесс, что также может приостановить его развитие или будет приводить к грубым нарушениям строения слоя, а следовательно – к ухудшению его качества.
Формирование покрытия при электрокристаллизации, как любой кристаллизационный процесс, происходит путем образования зародышей и последующего их роста.
Согласно второму закону термодинамики и его следствию изменениевнутреннейэнергиисистемыприфазовыхпереходах, втом числе образовании и росте слоя покрытия, сопровождается теплообменоммеждуформирующимсяслоемивнешнейсредой. Поэтому характер роста слоя во многом определяется условиями и направлением этого теплообмена, а также числом одновременно реализуемых межатомных связей, возникающих при присоединении к слою каждого очередного атома. Осаждение покрытия происходит не одновременно по всей поверхности, а лишь на активных, быстро растущих участках. Остальная часть поверхности является как бы пассивной. При этом сначала на вершинах углов, ступеньках, других дефектах поверхности возникают плоские (двумерные) зародыши, которые затем относительно быстро растут, образуя новый слой за счетприсоединениякграниновыхструктурныхэлементов.
Таким образом, формирование слоя покрытия происходит не непрерывно, а периодическими слоями, поскольку скорость осаждения наносимого вещества на покрываемую поверхность при образовании плоского зародыша значительно меньше скорости роста такого зародыша путем присоединения дополнительных атомов к грани слоя.
На рис. 9.1 показаны позиции присоединяющихся атомов при образовании и росте слоя, а также последовательность их присоединения при росте покрытия по толщине.
92
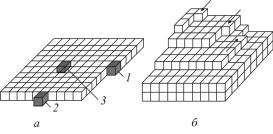
Рис. 9.1. Характер формирования атомных плоскостей при образовании зародышей покрытия и их послойном росте: а – атомные позиции в растущем слое покрытия в порядке убывания скорости присоединения (1 → 2 → 3);
б – направления (указаны стрелками) и очередность роста плоских слоев покрытия
На рис. 9.1, а показано, что наиболее легко присоединяется новый атом к растущему покрытию в поз. 1, где он имеет наибольшее число соседей-атомов и, следовательно, наибольшее количество одновременно реализуемых межатомных связей. Вэтой позиции атом и удерживается наиболее прочно, исключая его обратный переход вионную внешнюю среду. В этой связи в первую очередь реализуются и направления роста слоя так, как указано стрелками нарис. 9.1, б. Меньшееколичествоатомов-соседейи, следовательно, меньшее число одновременно реализуемых атомов-связей может иметь атом в поз. 2. Наиболее вероятен рост слоя путем «обегания» присоединяющимися атомами «островка» плоского зародыша слоя, последовательным их присоединением по всему периметру до тех пор, поканезаполнитсявесьатомныйслой.
Дальнейший рост слоя по толщине требует появления нового плоского зародыша в следующей атомной плоскости (поз. 3). Атомы, присоединяющиеся к растущему слою покрытия, имеют наименьшее число атомов соседей по сравнению с поз. 1 и 2 и наименьшее количество одновременно реализуемых межатомных связей. Из этого следует, что появление нового атомного слоя происходит с большими затруднениями по сравнению с ростом уже образовавшегося плоского двумерного зародыша. Это дает право говоритьопериодичности послойногоростаслоя.
93
В большинстве случаев, однако, возникновение нового плоского зародыша может произойти еще до окончательного заполнения атомами предыдущего плоского атомного слоя. Вэтом случае при росте слоя покрытия в нем могут одновременно на разных (последовательных) атомных слоях иметь место растущие плоские зародыши (см. рис. 9.1, б). Это в конечном случае может привести к образованию ступенчатого фронта кристаллизации слоя и в неоптимальных условиях проведения покрытия– копережающему росту слоя в виде вершин «игл» и «дендритов», обеспечивающих значительнуюшероховатостьслоя.
Образование нового плоского зародыша на поверхности предыдущего атомного слоя происходит достаточно благоприятно втом случае, если такая поверхность не содержит посторонних адсорбированных атомов, что достигается тщательной подготовкой исходной поверхности изделия перед покрытием и использованием чистых по примесям растворов электролитов, исключающих попадание на поверхность посторонних примесей из раствора. Если же поверхность пассивирована, например, если на ней присутствует окисная пленка, то образующийся зародыш слоя может быть только трехмерным, т.е. не связанным атомными связями спокрываемой поверхностью. Зарождение такого зародыша требуетзначительнобольшегозапасасвободнойэнергии.
Работа образования двумерного зародыша преимущественно определяется уровнем краевого натяжения, характеризующего избыток свободной энергии по краям растущего зародыша, тогда как для образования трехмерного зародыша она определяется необходимостью образования полной поверхности, ограничивающей образующийся кристалл.
Это свидетельствует о более легком формировании покрытия на уже имеющейся чистой подложке по сравнению со свободным формированием нового зародыша, не базирующегося на подложке (образование зародыша атомного слоя покрытия на загрязненной поверхности). Одним из интересных случаев формирования и роста слоя покрытия является непрерывное наслоение атомных плоскостей по винтовой линии при наличии на внешней атомной плос-
94
кости выхода винтовой дислокации. Такой физический дефект кристаллического строения характеризуется наличием на внешней атомной поверхности ступеньки, которая при присоединении атомов не исчезает, как краевая ступенька, а непрерывно перемещается по винтовой атомной плоскости, формируя характерный винтовой рельеф на поверхности покрытия. В этом случае рост слоя происходит без заметного перенапряжения. Физические дефекты поверхности облегчают формирование слоя, обеспечивая непрерывное увеличение толщины слоя без значительного пересыщения растворов и требуемых перенапряжений по электрическим характеристикам процесса и в большинстве случаев увеличивают сцеплениеслояспокрываемой поверхностью.
Роль пассивирования катода при формировании покрытия. Основные технологические параметры электрохимических способов получения покрытий
Формирование слоя при электрокристаллизации, включающей образование зародышей покрытия на поверхности и их рост, как было показано выше, может контролироваться рядом факторов, важнейшим изкоторыхявляетсяпассивированиеповерхности.
Пассивирование катода происходит за счет адсорбции активными участками его поверхности посторонних молекул, органических и неорганических веществ, гидроокисей металлов, водорода, образующихся при погружении в электролит покрываемых изделий, продуктов взаимодействия металла изделия с электролитом, с кислородом воздуха и т.п. Рост покрытий могут задерживать и адсорбированные на поверхности катода атомы металла, если скорость их выделения из растворов выше, чем скорость их присоединения к растущему атомному слою покрытия.
Блокирование некоторой части поверхности чужеродными веществами приводит к увеличению истинной плотности тока, в результате чего оказывается возможным образование новых зародышей на менее активных участках поверхности. При этом формирование слоя потребует более высокого перенапряжения.
95
При применении достаточно высокого перенапряжения на электродах электролизной ванны пассивирование активных участков поверхности может быть преодолено. В этом случае слой начнет формироваться вновь с этих активных участков.
Кинетика формирования покрытия, образующаяся структура слоя и его качественные и количественные характеристики во многом определяются состоянием исходной поверхности, наличием и числом физических и химических дефектов на ней, соотношением числа активных и пассивных микроучастков, уровнем ее пассивации чужеродными атомами, а также значениями применяемых электрических режимов, обеспечивающих преодоление пассивационных явлений при нанесении покрытий.
Перед нанесением большинства химических или электрохимических покрытий следует удалять пассивирующие поверхность оксидные пленки либо пленки других веществ, пассивирующих покрываемую поверхность, что необходимо для получения достаточной прочности сцепления покрытий с поверхностью, достижения равномерности покрытия и стабилизации режимов ведения процесса. Однако для достижения этих же целей при нанесении некоторых видов покрытий специально проводят предварительное пассивирование поверхности. При этом имеется в виду, что образующаяся в контролируемых условиях тончайшая равномерная пассивная пленка при последующем погружении в основной электролит, используемый для нанесения покрытия, быстро восстанавливается, и поверхность покрываемой детали становится очень активной, поскольку вслед за восстановлением пассивной пленки сразу же, без перерыва, начинается нанесение металла покрытия. При этом повышается сцепление слоя покрытия с покрываемой поверхностью и снижается пористость покрытия.
Размеры кристаллов в электролитических осадках определяются соотношением скоростей образования кристаллических зародышей и их роста при формировании покрытия, что вбольшей мере зависит от диффузионного массопереноса веществ и пассиваци-
96
онных явлений на поверхности. Чем больше относительная скорость образования зародышей, тем более мелкозернистыми должны быть осадки, и наоборот, медленное развитие процессов кристаллизации чаще всего приводит к получению грубозернистых осадков. Поскольку для образования кристаллических зародышей требуется более высокое перенапряжение, чем для продолжения их роста, то условия электролиза, способствующие перенапряжению, будут обеспечивать получение более мелкозернистых осадков. Таким образом, факторы, влияющие на катодную поляризацию, влияютинаструктуру образующихсяосадков.
К таким факторам относятся: состояние поверхности; природа и концентрация ионов выделяемого металла; плотность тока, температура электролита; наличие в электролите специальных добавок органических и неорганических веществ.
Ход нанесения и свойства образующегося слоя также зависят от вида и состава электролита, в том числе: от природы и концентрации ионов металлов; вида анионов; содержания в составе электролита кроме основных ионов металлов других веществ, кислот и щелочей; концентрации водородных ионов; добавок органических веществ.
Основными технологическими параметрами электрохимических способов нанесения покрытий являются: плотность тока; температура электролита; использование приема перемешивания электролита; использование приема наложения переменного электрического тока либо реверсирование постоянного тока.
Плотность тока является определяющим технологическим параметром электрохимических способов нанесения покрытий. Повышение плотности тока обычно способствует получению более мелкозернистых осадков. При повышении плотности тока существенно увеличивается скорость выделения металлов из растворов и, соответственно, скорость роста толщины слоя (скорость осаждения). Однако при очень больших плотностях тока образуются рыхлые осадки в виде дендритов и отдельных частиц, образующих агрегаты, непрочно связанные между собой и с покрываемой поверхностью. Поверхность покрытия оказы-
97
вается очень шероховатой, исчезает блеск. При чрезмерном увеличении плотности тока усиливается выделение водорода вместе с ионами металла, что охрупчивает образующийся слой, а в ряде случаев – и изделия в целом, в связи с легким диффузионным взаимодействием ионизированного водорода с основным материалом покрываемого изделия. Большие плотности тока могут привести к уменьшению выхода металла по току.
Второй важнейший технологический параметр электрохимических покрытий– температура электролита. В пределах рекомендуемых интервалов повышение температуры способствует получению более крупнозернистых осадков, компенсируя обратное влияние плотности тока. Повышение температуры электролита допускает использование более высоких значений плотности тока, увеличивая производительность технологических процессов, скорость осаждения, выход по току и улучшая качество покрытий. Повышение температуры электролита уменьшает и концентрацию водорода, выделяющегося на катоде вместе с атомами металла, снижаястепеньохрупчиванияпокрытия.
Использование приема перемешивания электролита обеспечивает поддержание постоянной концентрации растворов, улучшает качество покрытий. Однако при перемешивании растворов во взвешенном состоянии оказываются частицы шлама, вносимые врастворы с примесями в исходных компонентах, ииные загрязнения, в том числе продукты реакций при электролизе. Такие частицы при перемешивании электролита могут попадать на покрываемую поверхность, ухудшая качество покрытия и его свойства. Поэтому при нанесении покрытия с использованием перемешиванияэлектролитарастворынеобходимотщательнофильтровать.
В практике электрохимических способов нанесения покрытий широко используется применение переменного (периодического)
тока либо реверсирование постоянного тока. Целью этих прие-
мов является улучшение качества некоторых покрытий, получение мелкозернистых полублестящих покрытий и интенсификация процесса их формирования. Это обусловлено тем, что при наложении на постоянный ток переменной составляющей в связи с кратковременностью импульсов переменного тока увеличивается эффек-
98
тивная допустимая величина катодного тока, формирующего покрытие и обеспечивающего заданные характеристики качества слоя. Увеличение плотности тока в соответствии с законом Фарадеяинтенсифицирует процессобразованияпокрытия.
Для различных материалов покрытия возможны различные варианты поведения при нанесении слоя в условиях напряжения периодического тока на основной (катодный) ток покрытия. Металлы, не образующие прочных оксидных пленок, с небольшим сопротивлением электрохимической реакции (медь, цинк, кадмийсвинец и др.) в режиме анодного импульса периодического тока изменяют ход электрохимической реакции, в результате чего в этот момент прекращается рост слоя, а в связи с изменением направления электрического тока он начинает растворяться, причем скорость растворения оказывается выше на гранях, вершинах и других выступающих участках поверхности. Поэтому такой электрический импульс приводит к выравниванию покрытия, создавая блестящий внешний вид покрытия. Кроме того, вследствие частичного растворения ранее образовавшегося слоя вся покрываемая поверхность становится более активной, что способствует очень эффективному продолжению формирования покрытия до следующего анодного импульса электрического тока в межэлектродном пространстве. Для металлов такого типа целесообразно применять достаточно длительный анодный импульс, причем плотность тока ванодномимпульсеможет бытьравнаплотностикатодноготока.
Для легко пассивирующихся металлов, покрывающихся на воздухе и при анодной поляризации прочными окисными пленками, при анодном импульсе одновременно с растворением металла происходит его окисление с образованием пассивирующей оксидной пленки. Поэтому для пассивирующихся металлов обычно применяют прерывание тока или короткий анодный импульс небольшой плотности тока. При этом пассивирование происходит путем появления тонкой оксидной пленки, которая при включении катодного тока быстро растворяется, активизируя поверхность и способствуя эффективному продолжению роста наносимого покрытия.
99
Одним из новейших способов интенсификации процессов формирования электрохимических покрытий является наложение ультразвука на электролизную ванну. Ускорение электрохимических процессов в ультразвуковом поле обусловлено целым рядом причин:
– снижением концентрационной поляризации (на 40– 100 мВ), активированием поверхности, десорбцией различного рода загрязнений с поверхности покрываемого изделия;
– интенсивным перемешиванием электролита под действием «звукового ветра», возникающего вследствие постоянного смещения частиц жидкости в ультразвуковом поле; это обеспечивает даже при интенсивностях ультразвука 2– 3 Вт/см2, соответствующих докавитационным режимам ультразвуковых волн, уменьшение толщины диффузионного слоя до 3–4 мкм, что позволяет существенно увеличить допустимые плотности тока осаждения, уменьшить длительность нанесения покрытия;
– ускорением дегазации электролита под действием ультразвука в связи с облегчением отрыва пузырьков газа, образующегося на электродах, что приводит к уменьшению пористости образующегося покрытия, повышая его механические характеристики, улучшая качество покрытия.
Таким образом, воздействие ультразвука на электроосаждение позволяет существенно улучшить технологию покрытия, повысить скорость осаждения, улучшить блескообразование, снизить пористость слоя.
Основные технологические процессы получения покрытий химическими и электрохимическими методами
Из водных растворов электрохимическими методами получают покрытия поверхности следующими металлами: Ni, Fe, Co, Cr, Cu, Zn, Cd, Sn, Pb, Ag, Pt, Pd, Ru, Ir, In, Ga. Покрытия нано-
сят как на металлические поверхности, так и на неметаллы – графит, стекло, керамику, пластмассы).
100