
книги / Методы нанесения покрытий
..pdfВакуумное термическое напыление используется как для получения тонких декоративных покрытий (прутки, ювелирные изделия, зеркала, декоративная отделка пластмассовых деталей автомобилей и тонирование стекол и др.), где толщина наносимого слоя составляет несколько десятых долей микрометра, так
идля получения толстых коррозионно-стойких и износостойких покрытий. При этом толщины покрытий, полученных в результате длительного напыления, достигают нескольких десятков
идаже сотен микрометров. Качество покрытий определяется рядом контролируемых и регулируемых технологических параметров, таких как температура и время, скорость конденсаций
ифизико-химические свойства материала покрытия и подложки, толщина образующегося покрытия и др.
Кроме того, оно зависит от ряда неконтролируемых и труднорегулируемых факторов, таких как возможность взаимодействия паров наносимого вещества с остаточными газами в вакуумной камере, характер взаимодействия материала покрытия с материалом тигля, характер поверхностного натяжения формирующегося покрытия с поверхностью основы и т.д. Свойства покрытия, прочность сцепления его с основой зависят от условий формирования первых слоев осадка и изменения температуры подложки по мере формирования покрытия.
Вакуумные покрытия можно получить на установках периодического, полунепрерывного и непрерывного действия. Установки периодического действия предназначены для получения покрытий на единичные изделия либо партии изделий при мелкосерийном и массовом производстве, когда непрерывные процессы оказывается невозможным осуществить из-за конструк-
тивных особенностей обрабатываемых деталей |
или в связи |
с технологическими трудностями организации |
производства. |
При выполнении покрытий в установках периодического действия детали загружаются в вакуумную камеру, производят откачку воздуха до требуемой степени вакуума, нагрев и испарение напыляемого материала, и после получения покрытия заданной толщины камеру разгерметизируют и разгружают.
41
Полунепрерывный процесс используют для нанесения материала на листы или ленту с порулонной загрузкой в агрегат, где рулон, установленный в вакуумной камере, перематывают, протягивая его над испарителем. После разгерметизации камеры рулон извлекают на воздух.
Вустановках непрерывного действия изделие (лист, лента) протягивается сквозь вакуумную камеру в непрерывном режиме без разгерметизации с помощью специальных вакуумношлюзовых устройств. При этом реализуется в наиболее полном масштабе высокая производительность процессов вакуумного термического напыления. Она определяется возможностью осуществления интенсивного испарения металлов с помощью мощных источников тепловой энергии, в качестве которых используют электронно-лучевые испарители. В таких устройствах применяются электронные пушки с аксиальным сфокусированным пучком, а также с ленточным плоским пучком электронов; отклонение электронных пучков производится с помощью магнитных систем. В необходимых случаях электродный пучок может быть направлен на различные объекты, например, на различные навески напыляемых веществ, на разные тигли, установленные внутри камеры, обеспечивая таким образом поочередное испарение и нанесение на покрываемую поверхность различных веществ и, как следствие, получение слоистых композиционных материалов. В установках с двухлучевыми испарителями оказывается возможным одновременно наносить два различных вещества, получая покрытия из сплавов.
Вусловиях осуществления полунепрерывных или непрерывных режимов покрытия можно наносить на перемещающуюся лен-
ту со скоростью 1–8 м/с. Мощность установок достигает 1 МВт иболее. При этом испарение достигает существенных скоростей – до 20–50 г/с. Металлические конденсаты, получаемые методом термического напыления в вакууме при хорошей подготовке поверхности, прочно сцепляются со сталью при следующих температурах подложки: цинк и кадмий – при 100–120 °С, свинец– 150– 200 °С, алюминий– 200–300 °С, хромититан– 500 °С.
42
Кроме высокой производительности процесса вакуумного термического напыления, важнейшим преимуществом этого вида покрытий является полное исключение водородной хрупкости, свойственной многим другим процессам. Для получения качественного покрытия небходимо соблюдение вакуумной гигиены и чистоты рабочего места, в связи с чем улучшаются са- нитарно-гигиенические условия труда, повышается культура производства. Недостатками процесса являются необходимость предварительного нагрева защищаемой поверхности для получения надежного сцепления покрытия с основой, низкий коэффициент использования испаряемого металла и трудность получения однородного по толщине покрытия на деталях сложной конфигурации.
Характеристика вакуума при напылении
Получение покрытий в вакууме определяется условиями течения и последовательностью физико-химических процессов, определяющих механизмы и кинетику конкретных покрытий. Такими процессами являются: испарение (распыление) материала покрытия; направленный массоперенос в виде потока атомов или ионов материала покрытия на поверхность изделия; соударение атомов (ионов) в потоке с поверхностью с последующей их адсорбцией или десорбцией на этой поверхности; поверхностная диффузия адсорбированных атомов к местам предпочтительного образования зародышей покрытия: миграция и коалесценция зародышей, их рост до срастания и образования сеточных поверхностных структур; срастание островков и сеточных структур в сплошную плёнку; рост сплошной пленки и образование покрытия необходимой толщины.
Испарение вещества, перенос атомов во внешней среде к покрываемой поверхности, формирование покрытия и его свойства во многом зависят от степени вакуума в рабочей камере. В зависимости от соотношения среднего расстояния, которое проходят атомы покрытия в потоке массопереноса между двумя
43
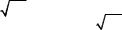
последовательными столкновениями с атомами среды 1 и расстояния L от испарителя до покрываемой поверхности, различают три степени вакуума: низкий вакуум при l < L; средний вакуум при l = L; высокий вакуум при l > L.
В условиях низкого вакуума каждый атом до образования покрытия многократно сталкивается с молекулами окружающего газа, поэтому их перемещения хаотичны. При этом поток пара непрерывно перемешивается, обеспечивая получение равномерных по толщине покрытий на протяжении большой длины и ширины покрываемой поверхности.
В высоком вакууме атомы, двигаясь без столкновения с атомами внешней среды по прямым линиям, обеспечивают получение неоднородных покрытий, толщина которых оказывается сильно зависящей от формы и плотности потока испаряемых атомов. При этом по оси атомных потоков испаренного вещества обычно формируются наиболее толстые слои, а по периферии потока – более тонкие. В этом случае для получения качественных однородных покрытий целесообразно осуществлять перемещение изделия относительно потока частиц либо перемещать поток с помощью управляющих магнитных систем. В среднем вакууме могут наблюдаться явления, характерные как для низкого, так и для высокого вакуума. Оценку уровня вакуума можно сделать, определив величину l:
|
|
|
l =i (n0 Q |
2 |
|
2π) = |
kT |
||
|
|
|
|
|
, |
||||
|
|
|
|
(P Q2 2π) |
|||||
где |
n = |
P |
– число молекул в единице объема (число Лошмидта); |
||||||
kT |
|||||||||
|
0 |
|
|
|
|
|
|
k – постояннаяБольцмана; Q – эффективный диаметрмолекулы. При нормальных условиях в одном кубическом сантиметре
любого газа содержится h = 2,687–1019 молекул. Анализ приведенного выражения показывает, что при указанных «нормальных условиях», т.е. при комнатной температуре и атмосферном давлении, величина l составляет порядка 1 мкм. Понижение
44

давления до 1 Па увеличивает эту величину примерно до 1 мм, а до 0,001 Па – до 1000 мм. Соответственно, эта величина растет пропорционально повышению абсолютной температуры. Однако изменение температуры не может быть столь значительным, как давление, в связи с чем влияние ее на строение потока испаряющихся атомов и характер осаждения на покрываемую поверхность значительно меньше, чем давления.
Формирование покрытия в вакууме
Формирование покрытий в вакууме неразрывно связано с развитием таких элементарных явлений, как испарение наносимого вещества и его конденсация на покрываемой поверхности.
Испарение веществ при нагревании может происходить из жидкого или твердого состояний. В случае испарения из твердого состояния вещества процесс называется сублимацией.
При испарении с поверхности жидкости, имеющей температуру (Т), атом переходит в пар, если его энергия колебаний равна или больше энергии связи (Е) с ближайшими соседями. Вероятность испарения Pu может быть определена как
P =v exp −E ,
u kT
где ν – частота колебания атомов на поверхности.
В высоком вакууме скорость испарения определяется уравнением Лэнгмюра
1
m = 4,4 10−4 P M 2 ,
T
где m – масса вещества, испаряемого с поверхности образца в единицу времени; М – молекулярная масса испаряемого вещества; Т – температура испарения; Р – давление насыщенного пара.
Зависимость давления насыщенного пара от температуры выражается уравнением Клайперона–Клаузиуса
45
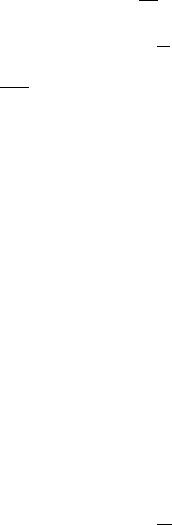
dP |
= |
dнисп |
|
dT |
|
, |
|
T (Vп −Vж ) |
где Vп и Vж – молекулярные объемы пара и жидкости. При Vж
значительно меньше Vп и Vп =kTP получим
lg P = − BA +B ,
dниспk ; В – const.
При повышении давления Р и увеличении вероятности столкновений испарившихся атомов около поверхности, с которой происходит испарение, образуется пограничный слой. При этом дальнейшее испарение резко замедляется, поскольку испаряющийся атом может попасть во внешнее пространство только через пограничный слой путем диффузии в этом слое. Таким образом, улучшение условий испарения может быть достигнуто путем существенного увеличения степени вакуума. Тем более что такой технологический прием, кроме того, уменьшает число атомов остаточных газов в вакуумной камере, повышает степень чистоты процесса нанесения покрытий, улучшает качество покрытия.
Испарению сплавов свойственны некоторые особенности течения процесса в связи с различными физическими свойствами веществ, входящих в состав испаряемого сплава. У большинства сплавов составляющие их вещества (компоненты) имеют различные упругости давления паров при испарении. Поэтому при испарении сплавов состав паров и покрытия отличается от состава исходного материала в испарителе.
Для описания процесса испарения таких материалов используют понятие активности а:
a = P , P0
46
где Р – давление над сплавом паров рассматриваемого компонента; Р0 – то же над чистым веществом.
Коэффициент активности f связывает активность а с молярной концентрацией вещества в сплаве X:
а = fX.
Поэтому при испарении сплавов первым всегда испаряется тот компонент, у которого более высокое давление пара. Из рассмотренного материала следует, что при назначении технологии напыления покрытия сложного состава требуется использовать исходный испаряемый материал, отличный от конечного состава покрытиясучетом различияскоростей испаренияразныхкомпонентов.
Конденсация – явление, по своему содержанию обратное испарению. Образовавшийся в результате испарения или распыления атом вещества покрытия движется во внешней среде под действием сил потоков, обусловленных явлениями диффузии либо накладываемых внешних физических воздействий (электромагнитные поля, электронный луч, плазма и др.).
Встречая на своем пути препятствие (напыляемую поверхность), атом ударяется об основу, попадая при этом в поле сил атомов, расположенных на поверхности основы. После столкновения возможны три варианта поведения атома: атом адсорбируется и остается на поверхности; атом мгновенно отражается от поверхности и переходит вновь во внешнюю среду; атом некоторое время находится на поверхности, а затем ее покидает, т.е. претерпевает повторное испарение.
В образовании покрытия будут участвовать только те атомы, которые остаются на поверхности основы. Вероятность того, что атом образует покрытие, характеризуется коэффициентом конденсации Ак, который представляет собой отношение количества атомов, сконденсировавшихся на поверхности, к общему числу падающих на поверхность атомов. Каждый атом, ударяющийся о поверхность, обменивается с ней энергией. Обмен энергией опреде-
ляетсякоэффициентом термическойаккомодацииАт.
47
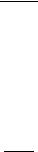
Aт = T1 −T2 ,
T1 −T0
где Т0 – температура поверхности основы; T1 и T2 – средние эквивалентные температуры падающих и отраженных атомов соответственно.
Температуры T1 и Т2 могут быть определены на основе сведений о кинетической энергии падающих и отраженных атомов:
= mV 2
T1,2 3k ,
где m – масса атома; V – средняя скорость атомов; k – константа Больцмана.
Если падающий атом полностью отдает энергию основе, т.е. T2 = Т0, то Ат = 1 и между ними устанавливается термическое равновесие. Случай этот – крайний, и фактически атом отдает основе только часть энергии, расходуя остальную ее часть на увеличение энергии поверхностных атомов, отрывающихся от поверхности, и на иные процессы рассеивания энергии, поэтому Ат всегда меньше единицы. Однако он никогда не бывает равным нулю, так как в этом случае образование покрытия принципиально исключается.
В результате непрерывной передачи энергии напыляемыми атомами основе она разогревается, ухудшая условия адсорбирования атомов поверхностью, что вызывает необходимость регулирования температуры поверхности при напылении.
Процессы испарения (распыления) и конденсации (адсорбции) атомов являются необходимыми, но недостаточными для характеристики полной картины формирования покрытий при напылении в вакууме.
Из сконденсированных (адсорбированных) атомов на поверхности возникают микроскопические центры новой фазы – зародыши покрытия, которые, образуя отдельные островки, а затем сетчатые структуры, разрастаются до тех пор, пока не заполнят всю поверхность и не сольются в сплошной слой по-
48
крытия. В связи с тем, что начальные этапы формирования покрытия происходят в течение непродолжительного времени, они часто не проявляют себя, а на самых ранних стадиях экспериментально обнаруживаются сразу тонкие (моноатомные) пленки покрытия. Поэтому покрытия, получаемые методами вакуумного напыления, часто называют пленками.
Однако зародыши покрытия образуются по механизмам гетерогенного переноса, поскольку они в первую очередь формируются на дефектах поверхности, в так называемых «потенциальных ямах». Между атомами, скопившимися в таких потенциальных ямах, начинают действовать силы химической связи, которые стремятся сдвинуть (сблизить) эти атомы до положений, определяемых их плотной упаковкой в соответствующей им кристаллической решетке. Сформировавшийся таким образом зародыш покрытия, выросший до размера, обеспечивающего возможность дальнейшего самопроизвольного роста с выделением избытка энергии, является критическимзародышемпокрытия.
В зависимости от соотношения температуры подложки и значения температуры плавления наносимого вещества формирование покрытия будет проходить через кристаллизацию из паровой фазы либочерез образованиежидкойпленкинапыляемого материала.
Процесс формирования твердого кристаллического покрытия путем кристаллизации из газовой фазы мало чем отличается по механизму от образования твердых пленок при осаждении из водных растворов в способах электрохимических и химических покрытий, рассмотренных ранее. Образование же зародышей при конденсации жидкого покрытия на поверхности основы во многом определяется типом взаимодействия между материалом основы
ивозможных пленок на ее поверхности с каплей жидкости, которыйпроявляетсячерез равновесный контактныйуголθ (рис. 8.2).
При химическом взаимодействии происходит смачивание,
изародыши хорошо растекаются по поверхности. В этом случае
краевой угол смачивания θ стремится к нулю угловых градусов. При этом образование зародышей облегчается (см. рис. 8.2, а).
49
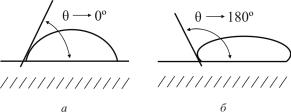
Рис. 8.2. Влияние характера взаимодействия жидкой капли с поверхностью на контактный угол при образовании покрытия
Если смачивания не происходит (cм. рис. 8.2, б), например при наличии на покрываемой поверхности окисных пленок, контактный угол θ стремится к 180°. При этом образование зародыша покрытия затруднено.
Рост зародышей покрытия как при формировании первого моноатомного слоя, так и по толщине образующейся пленки происходит двумя путями: путем прямого захвата атомов из пара; путем присоединения диффундирующих по поверхности адсорбированных атомов.
Последний процесс преобладает при повышении температуры поверхности. Температура поверхности играет большую роль в определении структуры и свойств покрытия, кинетики и механизма его формирования. Эта температура имеет несколько характерных значений:
Ткр – критическая температура основы, выше которой конденсация не происходит, поскольку все падающие атомы отражаются от поверхности. Значение этой температуры ориентировочно совпадает с температурой кипения материала покрытия.
Q1 – температура, выше которой конденсация пара происходит по механизму пар–жидкость, ниже этой температуры – по механизму пар–кристалл. Значение этой температуры примерно равно 2/3 от температуры плавления материала покрытия. Q2 – температура поверхности подложки, ниже которой покрытие формируется в виде аморфного слоя, не имеющего выра-
50