
книги / Методы нанесения покрытий
..pdfДовольно широко используется совместное нанесение двух и более металлов, в результате чего получаются покрытия из сплавов (Cu-Zn – латунь, Cu-Sn – бронза, сплавы Fe-Ni, Ni-Sn, Sn-Zn, Sn-Pb, Co-N1, Ag-Re). Возможно получение покрытий одновременно тремя компонентами (Fe-Ni-Cr), обеспечивая получение слоя, близкого по составу к известной нержавеющей стали типа 12Х18Н10.
В общем случае покрытия из водных растворов чаще всего получают из тех металлов, которые легко вытесняются из растворов. Такие металлы располагаются в нижней части электрохимического ряда напряжений:
Au-Pt-Pd-Ag-Cu-H-Pb-Sn-Ni-Co-Fe-Cr-Zn-Mn-Al-Mg.
Слева от водорода располагаются электроположительные, а справа – электроотрицательные элементы. Химическим путем без наложения разности потенциалов от внешнего источника принципиально возможно нанесение покрытий тем металлом, который является более электроположительным элементом по отношению к металлу основы. В других случаях вытеснение вещества покрытия из раствора и его осаждение на поверхности более электроположительного вещества возможно лишь при наложении на электролит разности потенциалов от внешних источников.
Простейшим вариантом получения химически осажденных покрытий является контактно-обменное отложение металлов на металлах в виде тонких пористых слоев. Такие покрытия оказываются возможными в соответствии с положением металлов основы и наносимого вещества в вышеуказанном электрохимическом ряду напряжений. Каждый вышестоящий металл вытесняет из раствора ниже его стоящий, т.е. более электроположительный (более благородный). Например, на железе самопроизвольно осаждаются: кобальт, никель, олово, свинец, медь, ртуть, серебро, золото. Этот процессидетпомеханизму обменныхреакций, например:
Fe + CuSO4 = Сu + FeSO4.
101
Эту реакцию можно наглядно пронаблюдать на лабораторной работе как одну из характерных легкореализуемых, однако качество получаемого покрытия медью при этом достаточно низкое, т.к. образуется обычно пористый, плохо сцепленный с основой слой. Высококачественные химические покрытия получают путем восстановления металлов из их растворов в виде легко разлагающихся химических соединений. Роль восстановителей играют активные соединения, содержащие углерод, водород, фосфор, бор. Наибольшее значение имеет химическое осаждение никеля.
9.2. Методы газофазного осаждения
Широкое распространение получил метод осаждения металлических и неметаллических материалов из газовой фазы, сопровождающийся химическими реакциями. Использование различных разновидностей метода дает возможность создавать большую гамму покрытий.
В ходе технологического процесса осаждения из газовой фазы между газами происходит химическая реакция, в результате которой образуется твердое вещество, осаждаемое на поверхности изделия, предназначенного для покрытия и находящегося в контакте с этими газами.
Осаждение из газовой фазы можно проводить как путем гетерогенной реакции на поверхности покрываемого изделия, так и гомогенной реакции в газе. Как правило, основным параметром при этом является температура.
Метод состоит в том, что газовую смесь, содержащую пары летучих компонентов, пропускают над нагретой поверхностью, где происходит реакция восстановления или термической диссоциации с образованием металла того или иного соединения. Схема процесса осаждения из газовой фазы представлена на рис. 9.2.
102
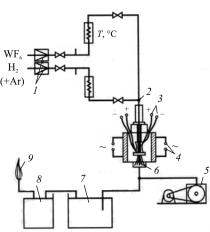
Рис. 9.2. Схема процесса осаждения из газовой фазы
В зависимости от типа используемой реакции и назначения процесса технологические установки могут конструктивно значительно отличаться, за исключением основных узлов. Примеры возможных реакций и условия, при которых они протекают, приведены ниже:
MoSi2 + 2SiCl4+4H2 1000–1400° → MoSi2 8НС1.
2NbCl5 + 2C 1800–2500°→ 2NbC + 5Cl2.
TiCl4 + 4H2+C 1400–1600°→ TiC + 4HCl.
WF6 + 3H2 500–800°→ WG + 6HF.
Ni(CО)4 150–300°→ Ni+4CO.
2A1C13 + 3H2 + 3CO2 1300–1600°→ Al2O3 + 6HC1 + 3CO.
Mo(CO)6 600–800°→ Mo + 6CO.
4BC13 + CH4 + 4H2 1500–1800°→ B4C + 12HC1.
103
Деталь 3, предназначенная для покрытия, нагревается в реакционной камере 6 нагревателями 4 до температуры, при которой газ (илисмесьгазов), поступающаяизсмесителя2, разлагается, твердое вещество осаждается на детали, а летучие вещества удаляются с помощью насоса 5 через охладительную камеру 7 и емкостьпоглотитель8. Неиспользуемыйводороддогораетвфакеле9.
Преимуществом метода осаждения из газовой фазы является не только получение покрытий из металлов и соединений с теоретической плотностью и толщиной от нескольких микрон до 1–2 мм, но и возможность нанесения материалов как на различные основы (металлы, пластмассы, графит, стекло и т.д.), так
ина изделия сложной формы.
Кчислу научных задач, решение которых связано с разработкой технологических процессов осаждения газофазных покрытий, относятся следующие:
–разработка механизма кристаллизации покрытия из газовой фазы;
–физико-химические закономерности процессов осаждения;
–исследование структуры полученных покрытий;
–исследование свойств и эксплутационных характеристик покрытий.
Следует подчеркнуть: при рассмотрении конкретных систем решению подлежат самые разные задачи.
Решение вышеперечисленных научных проблем разберем на примере газофазного процесса осаждения вольфрама из газовой смеси гексафторида и водорода, получившем широкое использование на практике.
В основу процесса положена простая реакция:
WF6 +3H2 → W +6HF.
Исследование кинетических закономерностей предусматривало экспериментальное изучение скоростей осаждения вольфрама в зависимости от режимных параметров процесса – температуры и содержания в смеси гексафторида вольфрама, водородаифтористоговодорода.
104
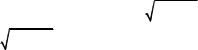
Исходя из концепции слабой адсорбции гексафторида вольфрама на поверхности Р. К. Чужко предложил адсорбцион- но-ударный механизм роста вольфрамового осадка, который был положен в основу вывода кинетического уравнения для рассматриваемого случая. Согласно упомянутому механизму водород находится на поверхности в хемосорбированном состоянии, а следовательно, в атомарном виде, а гексафторид вольфрама испытывает с реакционной поверхностью практически соударение. При этом на неоднородной поверхности имеется контролируемая полоса теплот адсорбций, qн = 167 кДж/моль, определяющая скорость процесса в целом. Выделяя эту полосу теплот адсорбции как энергетически однородную, будем исходить из протекания реакции в идеальном адсорбированном слое или на квазиоднородной поверхности, что позволяет использовать закон действующих поверхностей Ленгмюра.
Тогда обобщенное выражение для скорости осаждения νw (мм/ч) гетерогенного реагирования гексафторида вольфрама с водородом в присутствии фтористого водорода будет иметь вид
|
k0 exp |
−Ek (RT )−1 PWF |
a0H PH |
|
exp qH (2RT )−1 |
|
|
|||
νw = |
|
|
|
6 |
|
2 |
2 |
|
|
, |
|
|
|
|
|
|
|
|
|||
|
1+ a0H2 PH2 |
exp qH (2RT )−1 |
|
+ a0H2 |
exp qHF (2RT )−1 |
PHF |
|
|||
|
|
|
|
|
|
|
|
|
|
|
где неизвестные константы: k0 – константа скорости реакции, Еk – энергия активации процесса, qHF – теплота адсорбции фтористого водорода на вольфраме; – a0H2 ,qHF ,qH – предэкспонен-
циальные множители, определяемые из экспериментальных данных, PH2 , PHF , PWF6 – соответственно парциальные давле-
нияводорода, фтористоговодородаигексафторидавольфрама. Наличие экспериментальных данных по скоростям осажде-
ния вольфрама в отсутствие фтористого водорода и при различных его содержаниях в газовой смеси, их сравнительный анализ с помощью математической обработки и графоаналитическое
105

построение этих данных [8] позволили определить такие важные характеристики, как энергия активации Еа = 67 кДж/моль, теплота адсорбции фтористого водорода на вольфраме qHF = = 150 кДж/моль, а затем и значения предэкспоненциальных множителей k0 = 334 103 мм/кПа ч) и а0 = 5,42 10–10 кПа–1.
Подставляя полученные кинетические и адсорбционные константы в уравнение общего вида (1), получим кинетический закон роста вольфрамового осадка с учетом ингибирующего действия фтористого водорода:
|
|
6,34 102 exp |
|
16,5 |
P |
P |
|
|
|
|
|
||
|
|
|
|
|
|
RT |
WF6 |
H2 |
|
|
|
|
|
νw = |
|
|
|
|
|
|
|
|
|
|
|
. |
|
|
10−5 P |
|
83,5 |
|
+ 5,42 10−10 exp |
150 |
|
|
|||||
1+1,9 |
exp |
P |
|||||||||||
|
|
H2 |
|
|
|
|
|
|
|
RT |
|
HF |
|
|
|
|
|
RT |
|
|
|
|
|
|
|
|
Для описания микроструктуры газофазного вольфрама используется методика, разработанная для сталей. Согласно этой методике определяются тип структуры и величина зерна в баллах, причем больший балл зерна соответствует меньшему линейному размеру.
В зависимости от величины и формы зерна структура вольфрама подразделяется на ветвистую, столбчатую и смешан-
ную. Ветвистая |
структура состоит из зерен, вытянутых |
в направлении от |
поверхности роста к рабочей поверхности |
(рис. 9.3, а). У столбчатой структуры размер зерна в направлении, перпендикулярном поверхности роста покрытия, превышает размеры в продольном сечении (рис. 9.3, б). Однако часто наряду с крупными вытянутыми кристаллами, близкими по форме к столбчатым, присутствуют более мелкие равноосные зерна. В таких случаях структура характеризуется как смешанная (рис. 9.3, в). Комплексной характеристикой газофазного вольфрама является микротвердость. Микротвердость вольфрамового осадка находится в пределах 3800–6000 МПа.
106
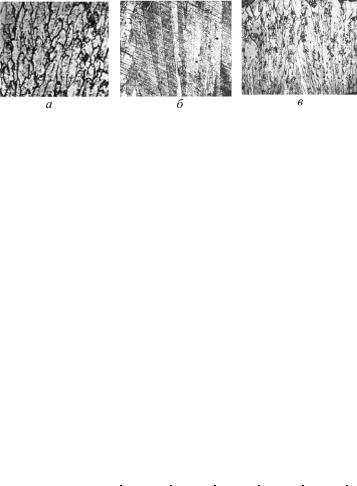
Рис. 9.3. Типы структур газофазного вольфрама: а– ветвистая; б– столбчатая; в– смешанная
Исследование физико-механических свойств газофазного вольфрама проводилось по современным методикам с применениемотечественногоиимпортногооборудования, длячегоизготавливались специальные образцы для исследований. Небольшой разброс свойств фторидного вольфрама объясняется различием его структур и химической чистоты. Приведенные в табл. 9.1 физикомеханические характеристики относятся к фторидному вольфраму, полученному поописанномувышетехнологическомупроцессу с применением следующих исходных продуктов: гексафторид вольфрама ТУ-02-542–84; водород марки «Б», ГОСТ 3022–80; аргон чистый, высшийсорт, газообразный, ГОСТ 10157–79.
Основные физико-механические свойства газофазного вольфрамаприведенывтабл. 9.1.
Таблица 9 . 1
Основныефизико-механическиесвойствагазофазноговольфрама
Характеристика |
|
|
Температура, °С |
|
|
||||
20 |
500 |
1000 |
1500 |
2000 |
2500 |
3000 |
|||
|
|
||||||||
1. Модуль упруго- |
4,1 |
4,0 |
3,65 |
3,5 |
3,3 |
– |
– |
||
сти Е 10–5, МПа |
|||||||||
2. Модуль |
сдвига |
1,6 |
1,5 |
1,4 |
1,3 |
1,2 |
– |
– |
|
У 10–5, МПа |
|
||||||||
3. Коэффициент |
0,28 |
0,29 |
0,3 |
0,3 |
0,3 |
– |
– |
||
Пуассона |
|
||||||||
|
|
|
|
|
|
|
|
||
4. Средний темпера- |
|
|
|
|
|
|
|
||
турный коэффици- |
4,3 |
4,6 |
5,0 |
5,4 |
5,7 |
6,3 |
– |
||
ент линейного рас- |
|||||||||
|
|
|
|
|
|
|
|||
ширения α10–6, К–1 |
|
|
|
|
|
|
|
||
|
|
|
|
107 |
|
|
|
|
|
|
|
Окончание |
табл. 9 . 1 |
||||
|
|
|
|
|
|
|
|
|
Характеристика |
|
|
Температура, °С |
|
|
|||
20 |
500 |
1000 |
1500 |
2000 |
2500 |
3000 |
||
|
||||||||
5. Удельная тепло- |
|
|
|
|
|
|
|
|
емкость С, |
1,34 |
1,4 |
1,46 |
1,58 |
1,62 |
1,7 |
1,78 |
|
Дж/(кг°С) |
|
|
|
|
|
|
|
|
6. Теплоемкость λ, |
154 |
135 |
118 |
102 |
98 |
93 |
88 |
|
Вт/(м К) |
|
|
|
|
|
|
|
|
7. Температуропров |
225 |
160 |
120 |
110 |
105 |
87 |
70 |
|
одность, а 10–3, м2/ч |
||||||||
8. Удельное элек- |
|
|
|
|
|
|
|
|
тросопротивление |
5,3 |
– |
– |
– |
– |
– |
– |
|
γ106, Ом см |
|
|
|
|
|
|
|
|
9. Предел прочности |
|
|
|
|
|
|
|
|
при растяжении σр, |
250– |
200–300 |
90–150 |
25–50 |
– |
– |
– |
|
Мпа; при сжатии σс, |
400 |
|
|
|
|
|
|
|
МПа |
|
|
|
|
|
|
|
Таким образом, описанный процесс восстановления гексифторида вольфрама водородом является весьма перспективным и нашел широкое применение в различных областях техники.
Являясь весьма «гибким», процесс позволяет изготавливать самые разнообразные изделия сложной формы (стержни, тигли, клапана, трубы и др.), а также наносить покрытия различного назначения. Следует, однако, отметить, что при всех достоинствах газофазных процессов их система улавливания и нейтрализации отходящих газов требует доработки и улучшения с целью сведения до минимума загрязнения окружающей среды, что позволит отнести эти процессы к экологически чистым.
БИБЛИОГРАФИЧЕСКИЙ СПИСОК
1. Кудрявцев Н.Т. Электролитические покрытия металлами / Н.Т. Кудрявцев. – М.: Химия, 1979. – 352 с.
2. РойхИ.Л. Нанесение защитных покрытий в вакууме / И.Л. Ройх, Л.Н. Колтунова, С.Н. Федосов. – М.: Машиностроение, 1976. – 368 с.
3.БартеневС.С. Детонационные покрытия / С.С. Бартенев, Ю.П. Федько, А.И. Григорьев. – Л.: Машиностроение, 1982. – 278 с.
4.Кудинов В.В. Нанесение покрытий напылением / В.В. Кудинов, Г.В. Бобров // Теория, технология и оборудование. – М.: Металлургия, 1992. – 327 с.
5.Борисов Ю.С. Плазменные порошковые покрытия / Ю.С. Борисов, А.Л. Борисова. – Киев: Техника, 1986. – 223 с.
6.Данилин Б.С. Применение низкотемпературной плазмы для нанесения тонких пленок / Б.С. Данилин. – М.: Машино-
строение, 1989. – 362 с.
7.МрочекЖ.А. Основы технологии формирования многокомпонентных вакуумных, электродуговых покрытий / Ж.А. Мрочек, Б.А. Эйзнер, Г.В. Марков. – Минск: Наукаитехника, 1991. – 96 с.
8.БелыйА.В. Структура и методы формования износостойких поверхностных слоев / А.В. Белый, Г.Д. Карпенко, Н.К. Мышкин. – М.: Машиностроение,1991. – 208 с.
9.Фторидный процесс получения вольфрама / А.И. Красов-
ский[идр.]. – М.: Наука, 1981. – 260 с.
10.Синани И.Л. Газофазный процесс получения вольфрама: учеб. пособие / И.Л. Синани; Перм. гос. техн. ун-т. – Пермь, 1994. – 64 с.
11.Биронт В.С. Нанесение покрытий / В.С. Биронт; Академия цветных металлов и золота. – Красноярск, 1994. – 160 с.
12.Пузряков А.Ф. Теоретические основы технологии плазменного напыления / А.Ф. Пузряков;. МГТУ им. Н.Э. Баумана. –
М., 2003. – 358 с.
109
Учебное издание
Синани Игорь Лазаревич, Федосеева Елена Михайловна, Береснев Герман Александрович
МЕТОДЫ НАНЕСЕНИЯ ПОКРЫТИЙ
Учебное пособие
Корректор Л.С. Лыкова
–––––––––––––––––––––––––––––––––––––––––––––––––
Подписано в печать 2.07.2008. Формат 60×90/16.
Усл. печ. л. 6,75.
Тираж 100 экз. Заказ № 162/2008.
–––––––––––––––––––––––––––––––––––––––––––––––––
Издательство Пермского государственного технического университета.
Адрес: 614990, г. Пермь, Комсомольский пр., 29, к. 113.
Тел. (342) 219-80-33.