
книги / Методы нанесения покрытий
..pdfкотором распыленные частицы металлической жидкости этой же струей доставлялись на покрываемую поверхность, где при ударе об нее образовывали слоистые покрытия.
Этот метод характеризуется рядом недостатков: он малопроизводителен, требует громоздких устройств для расплавления металла, его подачи в зону распыления, применения неэффективно использующих тепло установок для калориферного нагрева воздуха и др.
Наносимые покрытия при такой организации технологического процесса слабо сцепляются с покрываемой поверхностью, имеют большое количество дефектов, что обусловлено окислением распыляемых частиц покрываемой поверхности при воздействии на них высокотемпературного воздушного факела, содержащего кислород, а также окислением поверхности каждого наносимого слоя при многослойном нанесении покрытия.
Более совершенным способом газотермического напыления является способ газопламенного покрытия, при котором для создания необходимых температурных условий получения расплава распыляемого материала используется теплота, выделяющаяся при сжигании смеси горючий газ–кислород в газопламенной горелке. При этом напыляемый материал в виде порошка или проволоки подается в наиболее высокотемпературную зону пламени горелки, где он расплавляется, распыляется или разогревается в необходимой степени; увлеченные струей факела распыленные частицы с большой скоростью доставляются на покрываемую поверхность, где они формируют покрытие.
Важнейшим преимуществом такого метода является возможность создания контролируемого состава газопламенной струи, которая при избытке углеводородов в пламени может обеспечивать создание нейтральной или восстановительной атмосферы, защищающей распыляемые частицы жидкости или порошковый материал покрытия от окисления, улучшая качество покрытия. За счет этой атмосферы происходит и защита от окисления покрываемой поверхностииформирующихсяслоевпокрытия.
61
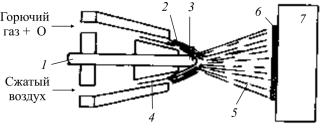
Этот способ не требует специальных устройств для предварительного расплавления металла, исключает применение стационарных установок для нагрева воздуха. Установки газопламенного напыления компактны и высокопроизводительны, в связи с чем получили очень широкое применение во всех отраслях промышленности.
Конструктивно они чаще всего выполняются в виде ручного «пистолета», который по своему существу представляет собой газовую горелку, снабженную дополнительно устройством непрерывной подачи в зону горения (в высокотемпературную зону факела) проволоки распыляемого материала или каналами для подачи порошка. На рис. 8.6 приведена схема газовой горелки для распыления металлической проволоки (прутка) из напыляемого материала.
Рис. 8.6. Схема установки для газопламенного распыления проволоки (прутка) из напыляемого материала: 1 – проволока (пруток);
2– пламя, образующееся при сгорании горючего газа, например ацетилена; 3 – оплавляющийся конец проволоки или прутка; 4 – воздушный поток
в горелке; 5 – поток распыленных частиц; 6 – покрытие; 7 – покрываемое изделие
Из приведенной схемы (см. рис. 8.6) виден принцип действия установки для газопламенного распыления, не требующий дополнительного разъяснения. Образующееся покрытие формируется по месту попадания основного потока частиц в факеле газовой горелки. Для получения покрытия на больших поверхностях и деталях сложной конфигурации горелку перемещают
62
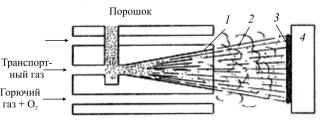
относительно покрываемой поверхности. При этом образование равномерного слоя формируемого покрытия достигается путем механизации процесса перемещения горелки и регламентирования скорости этого перемещения.
На рис. 8.7 приведена конструкция горелки для распыления порошков, в которой раздельно решены задачи организации газовых потоков, обеспечивающих транспортировку напыляемых порошков, сжигаемых газов, обеспечивающих их нагрев и формирующих покрытие.
Рис. 8.7. Схема газовой горелки для нанесения покрытий путем распыления порошков: 1 – инжекционное сопло горелки, разгоняющее частицы порошка; 2 – пламя; 3 – покрытие; 4 – покрываемое изделие
В рассматриваемой горелке порошок для напыления подается из бункерного устройства горелки самонасыпью в газовый канал, обеспечивающий разгон частиц порошка продувкой через инжекционное сопло горелки 1. В качестве транспортирующего газа может быть использован горючий или нейтральный газ (в зависимости от вида покрытия). Организация горения осуществляется путем подачи горючей газовой смеси (чаще всего ки- слородно-ацетиленовой) через внешний газовый канал горелки, охватывающий поток напыляемых частиц. Частицы, проходя сквозь пламя 2 на выходе из горелки, разогреваются и, ударяясь о напыляемую поверхность изделия 4, образуют слой покрытия 3.
При напылении пластмасс с использованием исходных порошковых материалов приходится организовывать три раздельных газовых потока (рис. 8.8).
63
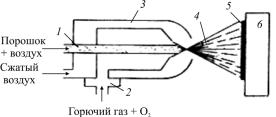
Рис. 8.8. Схема горелки для напыления порошковых покрытий из пластмасс: 1 – канал подачи порошка с помощью воздушного потока; 2 – камера смешения горючей смеси, переходящая далее в канал для подачи ее в зону горения на выходе из сопла; 3 – дополнительный канал для подачи сжатого воздуха, организующий поток 4 разогретых порошковых пластмассовых частиц и доставку их к формируемому покрытию 5; 6 – изделие
Такая организация газовых потоков обусловлена необходимостью строгого дозирования количества подаваемых порошков и контролируемой технологически температурой нагрева порошков при достаточно высоких скоростях частиц в потоке после их разогрева.
8.5.Особенности детонационного напыления
Вряду газотермических методов покрытий одно из ведущих мест отводится детонационным покрытиям. В литературе, посвященной рассматриваемому методу, отмечается, что детонационные методы по ряду показателей (в частности, по уровню износостойкости получаемых покрытий, адгезии к подложке) опережают почти все методы газопламенных покрытий. Образующиеся слои обладают минимальной пористостью и газопроницаемостью. Эти методы позволяют получать покрытия путем внедрения в покрываемую поверхность твердых окисных и карбидных частиц без их оплавления, а также получать композиционные покрытия, например порошковыми смесями твердых сплавов, которые формируются внедрением без оплавления карбидов вольфрама и титана, оплавлением и растеканием кобальтовой связки, что обеспечивает высокую износостойкость покрытия, его прочностные показатели и качественную адгезию покрытия с покрываемой поверхностью.
64
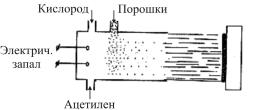
Действительно, при газопламенном напылении область его применения ограничивается максимальной температурой в зоне интенсивного горения ацетилено-кислородной смеси порядка 2850 °С, что не позволяет достаточно хорошо покрывать поверхность тугоплавкими металлами и оксидами, температура плавления которых может значительно превышать указанные температуры. Кроме того, скорости движения частиц в газовом потоке имеют ограниченные величины, что не позволяет частицам достичь высоких кинетических энергий, необходимых для внедрения в покрываемую поверхность.
Детонационный метод покрытия основан на принципе работы огнестрельного оружия (пушки), в стволе которого осуществляется взрыв горючей смеси. При этом наносимому порошковому веществу придается большая кинетическая энергия, расходуемая потоком разгоняющихся частиц для их внедрения в поверхность покрываемого материала.
На рис. 8.9 приведена схема устройства (пушки) для детонационного напыления порошками поверхности изделия.
Для реализации единичного акта работы установки при нанесении покрытий рассматриваемым методом должна быть выполнена цепь последовательных операций, включающая: заполнение камеры (ствола пушки) рабочей газовой смесью (ацетилен и кислород); подачу порции порошка; включение электрического разряда, зажигающего рабочую смесь и вызывающего ее взрыв и разгон в стволе частиц порошка; образование единичного покрытия при столкновении потока порошковых частиц с покрываемой поверхностью; продувку камеры азотом.
Рис. 8.9. Схема устройства для детонационного способа нанесения покрытий порошками
65
При этом единичный слой может оказаться различной структуры и толщины. Преимущественно толщина единичного слоя оказывается равной 5–6 мкм. Образующееся покрытие при единичном акте оказывается неравномерно распределенным по поверхности, в связи с чем покрытия детонационным методом осуществляют многократным чередованием указанных циклов в автоматическом режиме работы установки, которая работает с частотой чередования цикла операций 3–4 раза в секунду с перемещением покрываемой поверхности относительно ствола пушки в соответствии с формой и протяженностью поверхности. Общую длительность нанесения покрытия определяют исходя из требуемого количества наносимых слоев по толщине покрытия. В большинстве случаев эта толщина должна быть порядка 0,25–0,30 мм.
Рассматривая механизмы формирования слоя этим методом, можно увидеть, что выделение основной доли энергии взрыва
горючей смеси происходит в |
стволе, где она преобразуется |
в энергию сжатия продуктов |
реакции, образовавшихся при |
взрыве, а также в тепловую энергию, разогревая продукты детонации и вводимую в ствол навеску напыляемых порошков. Эффект детонации при взрыве, разгоняя частицы, возбуждает в них высокий уровень кинетической энергии, которая, в свою очередь, преобразуется при соударении частиц с покрываемой поверхностью в энергию их внедрения в эту поверхность и частично – в тепловую энергию, разогревая основу. Кроме того, разогрев основы может осуществляться за счет омывания ее газообразными горячими продуктами детонации, однако разогрев основы за счет всех факторов оказывается не очень сильным. Обычно температура детали оказывается не выше 200 °С. Поэтому основа детали при покрытии практически не деформируется и не подвергается другим физическим изменениям.
В качестве основных недостатков метода часто отмечают следующие: относительно низкая производительность процесса; высокая себестоимость детонационных покрытий; небезопасность детонационного метода и высокий уровень шума.
66
Однако в специальной литературе утверждается, что производительность процесса может быть увеличена в сотни раз путем использования многоствольных напылительных устройств.
Высокую себестоимость детонационного напыления связывают в основном с использованием дорогостоящих порошковых напылительных материалов на основе карбида вольфрама и кобальта. Как показали многочисленные исследования, высокую работоспособность имеют покрытия, полученные с использованием порошков оксида алюминия и других недефицитных веществ, что снижает себестоимость покрытия.
Специалисты также считают, и это подтверждается достаточно большим производственным опытом использования детонационных установок, что при наличии достаточно мощной вентиляции в помещениях и при выполнении обычных мер техники безопасности метод детонационного напыления безопасен.
Единственное, что серьезно ограничивает применение данного способа, – высокий уровень шума. Это требует разделения рабочего помещения на напылительную часть, где непосредственно получают покрытие, и на операторскую, где расположен пункт управления установкой.
8.6.Электродуговой и индукционный методы нанесения покрытий
Применение электрической энергии для нагрева распыляемого материала в напылительных устройствах существенно расширяет возможности способа, поскольку при таком методе нагрева практически не существует предела получаемых температур и распылять оказывается возможным самые тугоплавкие материалы. На рис. 8.10 представлена схема распыления металлической проволоки дуговым электрометаллизатором.
Как видно из представленной схемы, проволока из электропроводящего материала расплавляется электрической дугой. К наконечникам аппаратов с помощью роликов (на рисунке не показаны) подают две проволоки 1 диаметром 1,0–2,5 мм, через
67
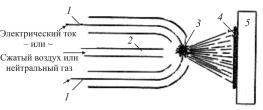
которые пропускают ток. При встрече проволок между их концами возникает электрическая дуга 3, в которой и происходит плавление этих проволок. Образующаяся капля жидкого металла непрерывно распыляется подающимся через центральный канал 2 нейтральным газом или сжатым воздухом.
Рис. 8.10. Схема распыления проволоки в электродуговом металлизаторе: 1 – две распыляемые проволоки; 2 – канал для подачи газа;
3 – электрическая дуга; 4 – формирующееся покрытие; 5 – изделие
Питание электродуговых металлизаторов осуществляют как переменным, так и постоянным током. Обычно при использовании переменного тока электрическая дуга горит неустойчиво и сопровождается значительным шумом. При этом качество покрытия ниже, чем при напылении постоянным током.
При использовании постоянного тока дуга горит непрерывно, устойчиво, напыляемый материал получает мелкозернистое строение. Электродуговые металлизаторы характеризуются высокой производительностью процесса. При использовании этого метода обеспечивается более прочное соединение покрытия с основой по сравнению с газопламенным напылением. При использовании двух разнородных проволок или проволоки из сплавов можно обеспечить комплексное покрытие сплавами. Как уже отмечалось, способ электродуговой металлизации позволяет, в отличие от газопламенного напыления, получать покрытия тугоплавкими металлами и сплавами.
Однако у этого метода есть и недостатки. Очень высокие температуры в зоне горения дуги приводят к сильному перегреву распыляемого материала и часто– к его окислению, особенно при ма-
68

лых скоростях подачи проволоки и при использовании в качестве распыляющего газа сжатого воздуха. Большое количество выделяющегося при горении дуги тепла приводит к выгоранию легирующих компонентов (избирательному испарению и окислению), входящих в напыляемый сплав. Например, содержание кремния всталях уменьшается на 40–60 % по сравнению с его исходным содержанием, марганца– на 10–15 %. Поэтому при расчете состава распыляемой проволоки приходится учитывать это явление и легировать ее такими компонентами в большем объеме, чем это требуетсядлянапыляемого слоя.
Индукционный метод распыления
К электрическим методам распыления относится метод высокочастотного индукционного распыления, где нагрев распыляемого прутка (проволоки) осуществляется за счет вихревых токов вмаломобъемераспылителявцентреиндуктора(рис. 8.11).
При реализации данного способа проволока1, непрерывно подающаяся в распылитель с помощью роликов (на рисунке не показаны), плавится под действием сконцентрированных в центре индуктора2 с помощью концентратора3 индуктированных вихревых токов. Частота возбуждаемых в индукторе токов 50 000–70 000 Гц. Распыление осуществляется сжатым воздухом или нейтральным газом, какивдругихраспылительных аппаратах.
Рис. 8.11. Схема распыления проволоки высокочастотным индукционным способом: 1 – проволока; 2 – индуктор; 3 – концентратор; 4 – покрытие; 5 – изделие
69
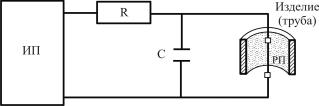
Электроимпульсное нанесение покрытий
Метод основан на импульсном разряде конденсатора через проволоку напыляемого металла. При этом происходит взрывное плавление и распыление проволоки с осаждением частиц расплавленного металла на поверхность изделия. На рис. 8.12 показана принципиальная схема такого способа.
Рис. 8.12. Принципиальная схема электроимпульсного метода напыления: ИП – источник питания; R – резистор; С – конденсатор;
РП – распыляемая проволочка из материала покрытия
При осуществлении способа используют проволочки диаметром от 0,5 до 1,0 мм длиной 20–150 мм. При разряде конденсатора в оптимальном режиме около 40 % массы проволоки превращается в газ, а 60 % – в капли расплавленного металла. Оплавление происходит взрывом. Кинетической энергией взрыва капли отбрасываются на напыляемую поверхность со скоростью несколько сотен метров в секунду. Покрытие образуется частицами 1–2 мкм. Более мелкие частицы, превращаясь в аэрозоли, не участвуют в образовании покрытия. При недостаточной энергии импульса проволока расплавляется без взрыва и покрытие не образуется. При излишней энергии импульса основная масса металла превращается в газ и аэрозоли. Покрытие также не образуется. Поэтому для каждого вида покрытия требуется отработка оптимальных электрических режимов.
Взрыв происходит почти мгновенно. При взрыве из камеры почти полностью вытесняется воздух. Поэтому при осуществлении покрытия практически не происходит окисления поверхности и частиц расплава, что обеспечивает хорошее сцепление покрытия с основой покрываемого материала.
70