
книги / Методы расчета ресурса работы элементов машин
..pdfЗдесь индексы А и В означают, что символ является характеристикой обобщенных или частных условий эксплуатации станка, индексы «р» и «х», что символ является характеристикой рабочего или холостого хода суппорта.
Таким образом, проведение испытаний на износ материалов по методу физико-статистического моделирования позволяет получить полную характеристику скорости изнашивания в виде закона ее
распределения f , что необходимо для прогнозирования изменения выходных параметров машины.
1.11.Программные испытания металлорежущих станков
Вкачестве примера рассмотрим программные испытания металлорежущих станков, которые являются типичным представителем высокоразвитых автоматизированных прецизионных машин.
Необходимый уровень качества станка определяется в первую очередь требованиями к точности обработанных изделий, включая точность размеров, формы, взаимного расположения обработанных поверхностей, а также их шероховатость и волнистость.
Точность обработки зависит от всех компонентов технологической системы – технологической машины (станка), инструмента, заготовки, приспособления, от их технического уровня и качества. Сохранение точностных показателей станка во времени определяет его параметрическую (технологическую) надежность.
Металлорежущий станок является основным компонентом технологической системы. Для установления номенклатуры его выходных параметров необходимо оценить, какую долю вносит станок
впогрешность обработки и как с позиции точности должны быть назначены его основные показатели.
Анализ процессов формообразования при обработке изделий на станках различного технологического назначения позволяет сделать вывод, что основными выходными параметрами станка должны быть характеристики точности осуществления заданных движений узлов, несущих инструмент и заготовку, т.е. формообразующих узлов станка.
31

Под руководством А.С. Проникова [14] были проведены обширные исследования параметрической надежности станков различных типов и их формообразующих узлов, а также разработаны частные методики для программных испытаний и сертификации станков.
Вкачестве примера в табл. 4 приведены результаты программного испытания для шпиндельной бабки расточного станка при ее поступательном перемещении.
Выходные параметры оценивают возможность станка по полу-
чению точности размера (Х1) и конусообразности обработанного отверстия (Х2), расстояния между обработанными отверстиями (Х3)
ишероховатости поверхности (Х4).
Втабл. 4 указаны принятые размеры области работоспособно-
сти Хmax. Они учитывают, что на точность размера обработанного отверстия основное влияние оказывает вращательное движение шпинделя, поэтому на долю поступательного движения принято 30 % общего допуска. Конусообразность зависит от точности поступательного движения шпиндельной бабки, а точность позиционирования – от точности фиксации стола по отношению к шпиндельной бабке после его перемещения на заданную координату. Шероховатость обработанной поверхности связана с амплитудой высокочастотных колебаний на частотах, которые выявляются при спектральном анализе процесса колебаний станка.
При обработке результатов испытания для каждого из установленных выходных параметров определяются: размер области со-
стояний Хi, наибольшее значение выходного параметра, среднее значение (математическое ожидание) параметра Хiср и его дисперсия
(среднее квадратическое отклонение i ).
Эти параметры получают в результате применения статистических методов обработки результатов испытания. При определении наибольшего значения параметра Хi не учитываются случайные выбросы и оценивается достоверность полученного значения. Величина Хi необходима для непосредственного расчета запаса надежности
Kн X i max , а Хiср и i могут быть использованы для оценки воз-
X i
можности обработки более точных деталей.
32
Таблица 4
Оценка начального уровня надежности станка по результатам испытаний
Выходной |
Характе- |
Требова- |
Область |
Область состояний |
|
Запас |
Приме- |
||||
параметр |
ристика |
ния к точ- |
работо- |
по результатам |
надежно- |
чание |
|||||
станка |
параметра |
ности |
способно- |
испытаний |
сти Kн = |
|
|||||
|
|
изделия |
сти Ximax, |
Xi |
Xiср |
σi |
= |
|
Xi max |
|
|
|
|
|
мкм |
|
|
|
|
|
|
|
|
|
|
|
|
|
|
|
Xi |
|
|||
|
|
|
|
|
|
|
|
|
|
||
X1 = Xp |
Размах |
Допуск на |
X1max = 30 |
0,017 |
0,015 |
0,002 |
|
1,75 |
|
Допус- |
|
|
траекто- |
диаметр |
(30 % от |
|
|
|
|
|
|
|
тимо. |
|
рий |
(0,1 мкм) |
допуска) |
|
|
|
|
|
|
|
Необ- |
X2 = tgβ |
Наклон |
Конус- |
X2max = 25 |
0,02 |
0,015 |
0,001 |
|
1,25 |
|
ходим |
|
|
траекто- |
ность |
(50 % от |
|
|
|
|
|
|
|
прогноз |
|
рий |
(0,05 мм |
допуска) |
|
|
|
|
|
|
|
ресурса |
|
|
на длине |
|
|
|
|
|
|
|
|
|
|
|
100 м) |
|
|
|
|
|
|
|
|
|
X3 = X |
Точность |
Расстоя- |
X3max = 75 |
0,111 |
0,070 |
0,007 |
|
0,9 |
|
Необ- |
|
|
позицио- |
ние между |
(75 % от |
|
|
|
|
|
|
|
ходимо |
|
нирования |
осями |
допуска) |
|
|
|
|
|
|
|
повы- |
|
|
(±0,1 мм) |
|
|
|
|
|
|
|
|
шать |
|
|
|
|
|
|
|
|
|
|
|
точ- |
|
|
|
|
|
|
|
|
|
|
|
ность |
|
|
|
|
|
|
|
|
|
|
|
пози- |
|
|
|
|
|
|
|
|
|
|
|
циони- |
|
|
|
|
|
|
|
|
|
|
|
рования |
X4 = aW |
Амплиту- |
Шерохо- |
X4max = 30 |
0,27 |
0,22 |
0,03 |
|
1,1 |
|
Близко |
|
|
да высо- |
ватость |
(90 % от |
|
|
|
|
|
|
|
к пре- |
|
кочастот- |
(Ra = 0,32 |
допуска) |
|
|
|
|
|
|
|
дель- |
|
ных коле- |
мкм) |
|
|
|
|
|
|
|
|
ному |
|
баний |
|
|
|
|
|
|
|
|
|
|
|
|
|
|
|
|
|
|
|
|
|
|
При отсутствии запаса надежности (Kн < 1) необходимо определять вероятность выхода параметра за заданные границы, т.е. вероятность безотказной работы по данному параметру.
Для параметров, у которых Kн < 1, требуется разработка мероприятий по изменению конструкции соответствующего узла или требований к качеству его изготовления для сужения области состояний по данному параметру.
33
Анализ полученных характеристик начального уровня параметрической надежности (см. табл. 4) показывает, что точность позиционирования при перемещении стола станка не удовлетворяет установленным требованиям (Kн < 1) и необходима доработка этого узла.
Для улучшенного варианта механизма позиционирования (более точная шариковая винтовая пара в системе привода) получили меньшие размеры области состояний и соответственно Kн = 1,2.
Изменение начальных параметров станка с течением времени связано с медленно протекающими процессами и в первую очередь с износом базовых элементов. Для оценки этих изменений необходимо осуществить прогнозирование параметрической надежности испытываемого объекта.
Результаты расчета изменения регламентированных выходных параметров Х1, Х2 и Х3 на основе линейной модели параметрического отказа приведены в табл. 5. Эти изменения связаны с износом направляющих шпиндельной бабки и ходового винта стола. Параметр X4 aw практически не будет изменяться при износе направляющих
и при данном прогнозе не учитывался. Значения xср и x для каж-
дого из параметров получены на основании испытаний на износ методом физико-статистического моделирования и путем расчета скорости изменения регламентированных параметров траектории при износе направляющих. Расчет вероятности безотказной работы
станка P t проведен по каждому из параметров при длительности
работы станка t 1 год и t 10 лет с учетом двухсменной работы станка и коэффициента загрузки 0,8. Начальные значения выходных параметров взяты из табл. 4 по результатам программных испытаний. Рассматриваемые выходные параметры можно считать независимыми, поэтому вероятность безотказной работы всей системы оп-
ределялась как P t P1P2 P3 . По результатам расчета и испытаний
построена функция надежности – изменение вероятности безотказной работы системы во времени (рис. 6).
34
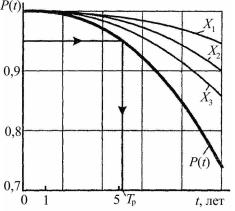
Таблица 5
Оценка параметрической надежности станка
Входнойпараметр |
Область |
Область работоспособности |
X |
н |
Резуль- |
t = 1 год t = 10 лет |
,лет |
||||
a0 = Xicp, |
σа = |
надежностиЗапас K |
γхcp |
|
σх |
Среднийресурс параметрупо Т |
|||||
|
состояний по |
|
мкм |
|
таты |
Расчет P(t) |
ср |
||||
|
результатам |
|
, ТУ |
|
прогноза |
|
|||||
|
|
|
|
и |
|
|
|
||||
|
испытаний |
|
по |
|
расчета |
|
|
|
|||
|
|
|
|
max |
|
|
|
|
|
|
|
|
мкм |
σi |
|
|
|
|
|
|
|
|
|
|
|
|
|
|
|
|
|
|
|
|
|
X1 |
15 |
2 |
33 |
|
1,75 |
0,45 |
0,80 |
0,9999 |
0,95 |
20 |
|
X2 |
15 |
1 |
25 |
|
1,25 |
0,40 |
0,22 |
0,9999 |
0,90 |
16 |
|
X3 |
50 |
4 |
75 |
|
1,20 |
2,00 |
0,23 |
0,9999 |
0,86 |
13 |
|
|
|
|
|
|
|
|
|
|
|
|
Среднийресурс параметрупо Т |
Показатели параметрической |
Вероятность |
|
|
лет |
|||||||
|
надежности станка |
|
безотказной |
0,9997 |
0,730 |
12= |
|||||
|
|
|
|
|
работы P(t) |
|
|
ср |
|||
|
|
|
|
|
|
|
|
|
|
|
|
Рис. 6. Функция параметрической надежности для расточного станка
35
Эти зависимости являются полной характеристикой параметрической надежности системы и позволяют численно оценить показатели надежности, в том числе и ресурс по точности. Проведенные расчеты по прогнозированию показателей надежности и анализ результатов программного испытания позволяют указать наиболее эффективные методы повышения надежности и выявить слабые места конструкции.
В результате испытания должен быть получен аттестат или сертификат, являющийся официальной характеристикой и документом, удостоверяющим качество и работоспособность машины, в первую очередь по ее выходным параметрам.
Табл. 4 и 5 иллюстрируют содержание основных граф аттестата (или сертификата) на примере металлорежущего станка.
Проведение исследовательских испытаний машин для оценки их качества и надежности является одним из ответственнейших этапов освоения новых моделей.
При таких испытаниях должна быть проверена результативность принятых при проектировании конструктивных решений, указаны наиболее эффективные пути достижения требуемого уровня качества и надежности и дана гарантия того, что данная модель после внесения соответствующих исправлений может быть серийно изготовлена.
Рассмотрев общие модели формирования отказа и потери машиной работоспособности, методы расчета и прогнозирования параметрической надежности изделий, теории расчета сопряжений и механизмов на износ, методы исследования технологической надежности оборудования, можно сказать, что до настоящего момента не производился расчет показателей надежности с учетом всех действующих на процесс старения факторов.
1.12. Исследование технологической надежности токарно-револьверных автоматов модели 1Б118
Действие вредных процессов, протекающих с различной скоростью, изменяет точностные параметры станка, что приводит к отказам по точности. Испытания станков на технологическую надеж-
36

ность выявляют динамику изменения точностных параметров станка при эксплуатации [17].
Значения суммарной погрешности обработки , резерва точности т и критериев технологической надежности P t определялись для следующих условий: межналадочный период Tмн 90 , 60
и 30 мин; диаметр 16 мм с допусками 50, 60 и 70 мкм, наработка станками составляла 1000, 2000, 3000 и 4000 ч. Полученные результаты испытания приведены в табл. 6–8. Из этих таблиц видно, что в процессе эксплуатации по мере роста наработки происходит постепенное уменьшение точности работы автомата. Резерв точностит уменьшается и при некоторых значениях наработки становится
равным нулю. С этого момента начинается снижение коэффициента технологической надежности, и, так как появляется вероятность выхода обрабатываемого размера за шестисигмовую зону рассеивания, естественно, что время работы станка до предельного состояния по точности зависит от допуска на размер.
Таблица 6 Результаты испытаний автоматов модели 1Б118 при Tмн 90 мин
Диаметр |
Наработка, ч |
|
т , мкм |
P t |
Kт |
||
и допуск |
, мкм |
||||||
|
|
10,61 |
|
|
|||
|
|
100 |
39,4 |
0,999 |
1,27 |
||
16 мм |
1000 |
47,03 |
3,0 |
0,999 |
1,06 |
||
2000 |
55,2 |
–5,2 |
0,987 |
0,91 |
|||
50 |
мкм |
||||||
3000 |
68,84 |
–18,84 |
0,764 |
0,725 |
|||
|
|
||||||
|
|
4000 |
83,3 |
–33,3 |
0,386 |
0,60 |
|
|
|
100 |
39,4 |
20,61 |
0,999 |
1,52 |
|
16 мм |
1000 |
47,03 |
3,0 |
0,999 |
1,27 |
||
2000 |
55,2 |
4,8 |
0,999 |
1,07 |
|||
60 |
мкм |
||||||
3000 |
68,84 |
–8,84 |
0,979 |
0,88 |
|||
|
|
||||||
|
|
4000 |
83,3 |
–23,3 |
0,725 |
0,715 |
|
|
|
100 |
39,4 |
30,6 |
0,999 |
1,78 |
|
16 мм |
1000 |
47,03 |
23,0 |
0,999 |
1,49 |
||
2000 |
55,2 |
14,8 |
0,999 |
1,27 |
|||
70 |
мкм |
||||||
3000 |
68,84 |
1,16 |
0,999 |
1,02 |
|||
|
|
||||||
|
|
4000 |
83,3 |
–13,3 |
0,949 |
0,845 |
37

Таблица 7 Результаты испытаний автоматов модели 1Б118 при Tмн 60 мин
Диаметр |
Наработка, ч |
|
т , мкм |
P t |
Kт |
||
и допуск |
, мкм |
||||||
|
|
15,70 |
|
|
|||
|
|
100 |
34,30 |
0,999 |
1,46 |
||
16 мм |
1000 |
39,75 |
10,25 |
0,999 |
1,26 |
||
2000 |
48,37 |
1,63 |
0,999 |
1,03 |
|||
50 |
мкм |
||||||
3000 |
59,80 |
–9,80 |
0,945 |
0,84 |
|||
|
|
||||||
|
|
4000 |
71,80 |
–21,80 |
0,684 |
0,7 |
|
|
|
100 |
34,30 |
25,70 |
0,999 |
1,75 |
|
16 мм |
1000 |
39,75 |
20,25 |
0,999 |
1,51 |
||
2000 |
48,37 |
11,63 |
0,999 |
1,24 |
|||
60 |
мкм |
||||||
3000 |
59,80 |
0,20 |
0,999 |
1,005 |
|||
|
|
||||||
|
|
4000 |
71,80 |
–18,06 |
0,940 |
0,835 |
|
|
|
100 |
34,30 |
35,70 |
0,999 |
2,04 |
|
16 мм |
1000 |
39,75 |
28,0 |
0,999 |
1,76 |
||
2000 |
48,37 |
21,63 |
0,999 |
1,45 |
|||
70 |
мкм |
||||||
3000 |
59,80 |
10,20 |
0,999 |
1,17 |
|||
|
|
||||||
|
|
4000 |
71,80 |
–1,8 |
0,994 |
0,975 |
Таблица 8
Результаты испытаний автоматов модели 1Б118 при Tмн 30 мин
Диаметр |
Наработка, ч |
|
т , мкм |
P t |
Kт |
||
и допуск |
, мкм |
||||||
|
|
19,89 |
|
|
|||
|
|
100 |
31,11 |
0,999 |
1,67 |
||
16 мм |
1000 |
35,37 |
14,63 |
0,999 |
1,41 |
||
2000 |
42,56 |
7,44 |
0,999 |
1,18 |
|||
50 |
мкм |
||||||
3000 |
53,10 |
–3,1 |
0,994 |
0,94 |
|||
|
|
||||||
|
|
4000 |
63,40 |
–13,4 |
0,892 |
0,79 |
|
|
|
100 |
31,11 |
29,89 |
0,999 |
1,99 |
|
16 мм |
1000 |
35,37 |
24,53 |
0,999 |
1,70 |
||
2000 |
42,56 |
17,44 |
0,999 |
1,41 |
|||
60 |
мкм |
||||||
3000 |
53,10 |
6,9 |
0,999 |
1,13 |
|||
|
|
||||||
|
|
|
|
–3,4 |
|
|
|
|
|
4000 |
63,40 |
0,997 |
0,955 |
||
|
|
100 |
31,11 |
39,89 |
0,999 |
2,33 |
|
16 мм |
1000 |
35,37 |
34,63 |
0,999 |
1,98 |
||
2000 |
42,56 |
27,44 |
0,999 |
1,64 |
|||
70 |
мкм |
||||||
3000 |
53,10 |
16,9 |
0,999 |
1,32 |
|||
|
|
||||||
|
|
4000 |
63,40 |
6,6 |
0,999 |
1,1 |
38
С течением времени суммарная погрешность обработки
увеличивается вследствие медленно протекающих процессов. Возрастание погрешности обработки и уменьшение резерва точно-
сти т за межналадочный период есть результат протекания процес-
сов средней скорости, в первую очередь размерного износа инструмента. Износ инструмента ведет к увеличению погрешностей обработки в пределах межналадочных периодов.
Процессы различной скорости протекают одновременно. Основное влияние на изменение погрешностей обработки, резерва точности и критериев технологической надежности при эксплуатации станков оказывают медленно протекающие процессы. Они увеличивают все составляющие погрешности и снижают критерии техноло-
гической надежности. Значения коэффициентов Kт и P t зависят от допуска на размер, а значение погрешности обработки явля-
ется функцией времени (наработки). Когда значение суммарной погрешности достигает значения допуска на неточность парамет-
ра , т.е. , то коэффициент резерва точности достигает предельного значения (Kт 1) .
Суммарная погрешность с ростом Tмн увеличивается, а ре-
зерв точности |
т |
уменьшается. Влияние медленно протекающих |
||
процессов тм |
с |
увеличением |
Tмн возрастает (при |
Tмн 15 мин |
тм 0,000 45 |
мкм/ч, а при Tмн |
90 мин тм 0,0028 |
мкм/ч). Повы- |
|
шение скорости |
влияния медленно протекающих процессов |
с увеличением межналадочного периода следует объяснить увеличением сил резания при затуплении резца, а следовательно, и более интенсивным изнашиванием сопряжений.
Основной причиной быстрого выхода показателей точности за допустимые пределы является износ сопряжений: фиксатор–втулка фиксатора, направляющие станины–направляющие каретки револьверного суппорта и др.
39
1.13. Влияние медленно протекающих процессов на технологическую надежность автоматов
В большинстве случаев основное значение в потере автоматами точности и виброустойчивости имеют величина и форма изношенной поверхности. Зная среднюю скорость изнашивания и ее рассеивание, можно определить степень влияния износов отдельных сопряжений автомата на потерю им точности, а также время работы станка с требуемыми показателями точности и вероятность безотказной работы при данной наработке.
Рассмотрим на примере износа сопряжения направляющие станины–направляющие каретки револьверного суппорта погрешности размера и формы обрабатываемой детали от наработки [17]. Определение износа и формы изношенной поверхности этого сопряжения проводилось в производственных условиях на пяти автоматах. Перед пуском станков в эксплуатацию на гранях направляющих станины и каретки по определенной схеме были нарезаны лунки. Местный износ направляющих определялся замером лунок. Проверки производили через 2000 ч работы станков (время календарное). Средний износ Uср направляющих по отдельным граням
для данного станка и по наработке определился как среднее линейных (местных) износов по всем лункам на соответствующей грани с помощью уравнения
Uср 1 n Ui , n i 1
где n – количество лунок на грани.
Семейство реализации случайной функции среднего износа горизонтальных граней направляющих станины за весь период показано на рис. 7. По виду реализаций можно полагать, что период макроприработки направляющих станины длится до 2000 ч работы станков.
Значения средних износов верхних горизонтальных граней направляющих станины для каждого станка в отдельности при наработке Т = 2000 и 9000 ч приведены в табл. 9.
40