
книги / Методы расчета ресурса работы элементов машин
..pdf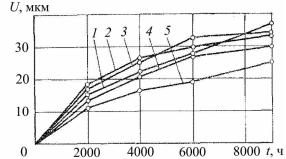
Рис. 7. Средний износ верхних горизонтальных граней направляющих от наработки станков: 1–5 – условные номера станков
Таблица 9
Значения средних износов верхних горизонтальных граней направляющих станины
№ |
Средний износ, мкм, |
Средняя скорость изнашивания, |
||
п/п |
при наработке, ч |
мкм, на 1000 ч при наработке, ч |
||
1 |
2000 |
9000 |
2000 |
9000 |
2 |
11,8 |
33,8 |
5,9 |
3,76 |
3 |
11,9 |
34,1 |
5,95 |
3,79 |
4 |
14,8 |
32,8 |
7,40 |
3,65 |
5 |
10,05 |
29,1 |
5,00 |
3,24 |
6 |
9,9 |
24,2 |
4,95 |
2,69 |
Как показали исследования, наибольшая скорость изнашивания направляющих станины ср 5,5 мкм на 1000 ч наблюдается в пер-
вые 2000 ч работы автоматов. Это период макроприработки, в течение которого износ направляющих наблюдается в отдельных местах. После наработки Т = 2000 ч направляющие изнашиваются по всей длине. Средняя опытная скорость в этот период ср 3,4 мкм на
1000 ч. Оценка среднего квадратического отклонения рассеивания средней скорости изнашивания определена по уравнению
41
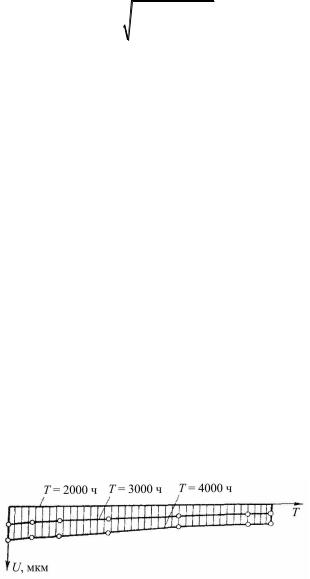
|
n |
ср |
иi ср 2 , |
|
i 1 |
где иi – скорость изнашивания направляющих i-го станка в соответствующем периоде наработки; ср – средняя скорость изнашивания
направляющих всех станков в соответствующем периоде. Рассеивание скорости изнашивания для периодов наработки
Т = 2000 и 9000 ч соответственно ср 1,05 мкм на 1000 ч, ср
= 1,5 мкм на 1000 ч. Средняя опытная скорость изнашивания направляющих станины за период макроприработки и нормального износа
|
|
|
|
5,5 |
3,4 |
|
о.ср |
ср |
ср |
|
4,45 мкм на 1000 ч. |
||
|
2 |
2 |
|
|||
|
|
|
|
|
Чтобы установить закономерность процесса изнашивания по кривым износа, необходимо учесть износы за период макроприработки Т = 2000 ч и построить эпюры последующего износа направляющих.
Эпюра износа направляющих станины одного станка за вычетом износов за период макроприработки показана на рис. 8. Форма изношенной поверхности представляет собой трапецию с большей ординатой со стороны шпинделя. Таким же образом определены скорости изнашивания и их рассеивание для направляющих каретки рассматриваемого сопряжения.
Рис. 8. Кривые износа горизонтальных граней направляющих после макроприработки
42

При известных скоростях и форме изношенной поверхности основных сопряжений станка можно на основании расчетных схем определить погрешности обработки, а исходя из условий требуемой точности – допустимые износы этих сопряжений. Износы по соответствующим граням сопряжения направляющих станины и каретки, отнесенные к 1000 ч работы станков, составляют:
U1 2(I) 9,5 мкм – износ сопряжения со стороны шпинделя по
передним горизонтальным граням;
U1 2(II) 7,1 мкм – износ сопряжения со стороны шпинделя по задним горизонтальным граням;
U1 3 3,7 мкм – износ сопряжения со стороны шпинделя по вертикальным граням;
U1 2(I II) 6,5 мкм – износ сопряжения со стороны маховичка
поворота вспомогательного вала по передним и задним горизонтальным граням.
Для прогнозирования изменения резерва точности т и коэффициента резерва точности Kт с течением времени из-за износа основ-
ных сопряжений необходимо произвести расчеты по определению формы изношенной поверхности этих сопряжений и, применяя расчетные схемы, определить влияние их износов на точность обработки.
Сравнительные данные о форме изношенной поверхности рассмотрены для основного сопряжения направляющие станины–на- правляющие каретки револьверного суппорта.
Выполняем расчеты по определению износа направляющих. Если учесть настройку автомата на обработку постоянной детали, то уравнение кривой распределения ходов имеет вид
y x L1 .
Пути трения для обратных и рабочих ходов вычислены для одной детали за рассматриваемый период Т = 2000 ч. Коэффициент износостойкости K определим по эпюре износа из уравнения
43

K FSRH a ,
где FH – площадь, ограниченная кривой износа, мкм см , FH 676 ; а – ширина направляющих, см, a 1,7 ; S – путь трения каретки за период работы станка 2000 ч, S 10,4 ; R – реакция на направляющих (при длине каретки l0 33,2 см и среднем давлении на горизонтальных гранях p 1,185 кГ/см2 ), R 66,4 кГ.
Получены следующие значения коэффициентов износостойкости: для направляющих станины K1 3, 2 , для направляющих карет-
ки K2 3,4 (материал направляющих и каретки – чугун МСЧ 32).
Износы направляющих станины и каретки по граням определены как сумма износов от рабочих и обратных ходов каретки при соответствующих эпюрах значений давления при наработке Т = 2000 ч.
Наибольшая и наименьшая скорости изнашивания направляющих станины, каретки и сопряжения на 1000 ч работы станка определены из уравнений
|
U ; |
|
|
U1 2 |
, |
|
|
|
|||||
|
T |
|
1 2 |
|
T |
|
|
|
|
|
|||
где U – износ направляющих; U1 2 |
– износ сопряжения. |
|||||
Скорости изнашивания направляющих станины находят из сле- |
||||||
дующих уравнений: |
|
|
|
|
|
|
1 U1 |
9,53 |
4,65 мкм на 1000 ч; |
||||
2 |
2 |
|
|
|
|
|
1 U1 7,2 |
3,6 |
мкм на 1000 ч. |
||||
2 |
2 |
|
|
|
|
|
Скорости изнашивания направляющих каретки находят из |
||||||
уравнений |
|
|
|
|
|
|
2 U2 |
14,48 |
7,2 мкм на 1000 ч; |
||||
2 |
2 |
|
|
|
|
|
44 |
|
|
|
|
|
|
2 U2 9,51 4,5 мкм на 1000 ч.
2 2
Скорости изнашивания сопряжения находят из уравнений
|
|
|
|
|
|
|
|
|
|
|
9,53 |
14,48 |
|
|
|||
|
U1 2 |
|
U1 |
U2 |
|
|
|
|
|||||||||
1 2 |
|
|
|
|
|
|
|
|
|
|
|
|
|
|
12 |
мкм на 1000 ч; |
|
|
2 |
|
|
|
2 |
|
|
2 |
|
||||||||
|
|
|
|
|
|
|
|
|
|
|
|
|
|
||||
|
|
|
|
|
|
|
|
|
|
|
|
7,2 |
9,51 |
|
|
|
|
|
|
U1 2 |
|
U1 |
U2 |
|
8,3 |
мкм на 1000 ч. |
|||||||||
|
|
|
|
|
|||||||||||||
1 2 |
2 |
|
|
|
2 |
|
|
2 |
|||||||||
|
|
|
|
|
|
|
|
|
|
|
|
|
|
|
Средняя скорость изнашивания направляющих станины по верхним горизонтальным граням
ср.р |
1 1 |
|
4,65 3,6 |
4,12 |
мкм на 1000 ч. |
|
2 |
2 |
|||||
|
|
|
|
Средняя опытная скорость изнашивания направляющих станины по этим граням о.ср 4,45 мкм на 1000 ч. Скорости изнашива-
ния, полученные разными путями, очень близки по значению. Скорость изнашивания в период макроприработки 5,5 мкм
на 1000 ч выше средней опытной о.ср 4,45 мкм на 1000 ч в период
нормального изнашивания.
Методика прогнозирования потери станками точности может обеспечить проверку эффективности принятых решений на ранней стадии разработки конструкции (что особенно важно при создании единичных деталей), значительно сократить время на получение необходимой информации в решении вопросов повышения надежности станков (что обеспечивает возможность выпуска высоконадежных моделей), дает возможность определить допустимые износы сопряжений, сроки и объемы ремонтов, номенклатуру запасных частей. Вычислив погрешности обработки, применяя расчетные схемы и зная скорости изнашивания, можно прогнозировать потерю станком точности при эксплуатации и оценить вероятность безотказной работы за определенные периоды наработки.
45
Прогнозирование потери станком точности и кратковременные испытания опытных образцов на технологическую надежность позволяют получить численные показатели надежности, т.е. дать объективную оценку показателям качества станка.
1.14. Исследование технологической надежности прецизионных токарных станков
Одной из причин преждевременной потери станками точности является изменение геометрической формы литых базовых деталей. Это изменение может происходить вследствие износа направляющих и из-за коробления деталей. В результате этого искажаются траектории перемещения узлов станка в пространстве, и, кроме того, изменения формы контактирующих поверхностей из-за коробления приводят к ускорению их изнашивания.
Проведенными исследованиями установлено, что коробление станин при благоприятном сочетании факторов невелико.
Длительное сохранение точности, жесткости и виброустойчивости прецизионных станков в значительной степени зависит от износостойкости направляющих станин, которые весьма трудоемки при изготовлении и ремонте.
Основные параметры изнашивания направляющих связаны не только с износостойкостью материалов и конструкцией станин, но и с интенсивностью работы станка, характером технологических процессов обработки, силами резания, количеством и видом абразивов, попадающих на направляющие, т.е. с теми факторами, которые определяются условиями эксплуатации станков. Ввиду этого исследование износа направляющих станков в производственных условиях дает наиболее правильное представление о влиянии отдельных факторов на характер и интенсивность изнашивания и на потерю станком точности.
Кривые износа граней у станка модели 1Е61МТ приведены на рис. 9. Из графиков следует, что теоретические кривые 1 износа граней достаточно точно совпадают с экспериментальными кривыми 2, за исключением грани III [17]. Это можно объяснить тем,
46
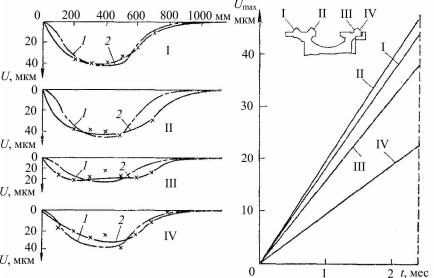
что давление на этой грани создается только в результате прижима каретки к направляющей нижней планкой, а грань имеет выпуклость с центром кривизны впереди станка, поэтому по концам грани давление было больше, что оказало влияние на форму изношенной поверхности.
Рис. 9. Теоретическая 1 и экспериментальная 2 форма изношенных граней и динамика износа граней направляющих
Износ каждой из четырех граней направляющих станины различен по величине. Большему износу подвергалась грань II, грань I изнашивалась в 1,05 раза медленнее, грань IV – в 1,23 раза, а грань III – в 2,05 раза медленнее, чем грань II. Соотношение между износами отдельных граней не сохраняется по длине направляющих, что является следствием неодинакового характера эпюр давления на направляющих.
Исследования показали, что протекание износа во времени в период нормального износа подчиняется линейному закону с некоторыми отклонениями, которые не носят закономерного характера. Таким образом, износ граней направляющих станков, выпускае-
47
мых одним и тем же заводом, одной и той же модели может быть представлен во времени случайной функцией, которая в результате опыта может принять тот или иной конкретный вид, т.е. иметь ту или иную реализацию.
Видим, что в результате экспериментов были получены значения параметров процесса изнашивания граней направляющих то- карно-револьверных автоматов и прецизионных токарных станков. Были проведены обширные исследования технологической надежности этих станков, но конечного результата, т.е. срока службы направляющих при заданных параметрах процесса старения не было получено. Это дает нам возможность использования экспериментальных данных для дальнейших исследований, оценки и расчета ресурса работы.
48
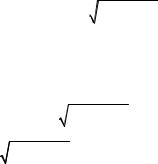
Глава 2. ТЕОРЕТИЧЕСКИЕ ПРЕДПОСЫЛКИ УЧЕТА ОСОБЕННОСТЕЙ РАБОТЫ ЭЛЕМЕНТОВ МАШИН ДЛЯ РАСЧЕТА РЕСУРСА
Для определения ресурса нам необходимо получить расчетную зависимость, т.е. выразить в явном виде ресурс работы T от всех факторов, которые могут оказывать влияние на срок службы. Для этого рассмотрим окончательное выражение (20) для вероятности безотказной работы объекта:
|
U |
max |
a |
|
ср |
T |
|||
P(T ) 0,5 |
Ф |
|
|
0 |
|
|
. |
||
|
2 |
2T 2 |
|
||||||
|
|
|
|
||||||
|
|
|
a |
|
|
|
|
|
Поскольку аргумент функции Лапласа является квантилем, получим
X p |
Umax a0 срT |
; |
(29) |
|
a2 2T 2 |
||||
|
|
|
X |
p |
2 |
2T 2 |
U |
max |
a |
ср |
T. |
(30) |
|
a |
|
|
0 |
|
|
Как рассматривалось ранее, в отдельных случаях мы можем прийти к упрощенным формулам и расчетам, пренебрегая некоторыми величинами, а можем учитывать все факторы.
Возведем обе части уравнения в квадрат:
Xp2 2a Xp2 2T 2 Umax a0 2 2 Umax a0 срT ср2 T 2 . (31)
Переносим все слагаемые в одну часть и делаем дополнительные преобразования:
Xp2 2T 2 |
ср2 T 2 |
2 Umax a0 срT Xp2 a2 |
Umax a0 2 |
0; |
(32) |
|||||
2 |
2 |
|
2 |
2 |
2 |
2 |
Umax a0 |
2 |
0; |
(33) |
Xp |
|
ср T |
|
2 Umax a0 срT Xp |
a |
|
||||
|
|
|
|
|
|
|
|
|
|
49 |
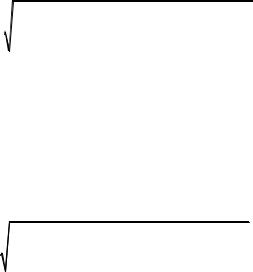
|
U |
max |
a |
|
|
X 2 |
2 |
|
U |
max |
a |
0 |
2 |
|
|||
T 2 2 |
|
|
0 |
|
ср T |
p |
a |
|
|
|
|
0. |
(34) |
||||
|
2 |
|
2 |
|
2 |
|
|
2 |
2 |
|
2 |
|
|
||||
|
Xp |
|
сp |
|
|
X p |
|
сp |
|
|
|
|
Таким образом, мы получили квадратное уравнение относительно T, развернутое решение которого имеет вид
|
|
|
|
|
2 |
|
2 |
2 |
2 |
|
|
|
|
|
|
X p a Umax a0 |
|
|
|||
T |
Umax a0 ср |
|
Umax a0 ср |
|
|
|
. (35) |
|||
|
|
X 2 2 2 |
|
|||||||
|
X 2 2 2 |
|
X 2 2 2 |
|
|
|
|
|
|
|
|
p ср |
p ср |
|
|
|
p ср |
|
|
||
|
|
|
|
|
|
|
|
Мы видим сложную зависимость времени наработки на отказ T от таких параметров, как Umax , Xp , , ср, a , a0 .
В решении уравнения (35) очевидно, что для практических целей приемлемым является условие
2 |
2 |
2 |
Xp |
|
cp . |
В этом случае знаменатель первого члена уравнения получается отрицательным, а вся дробь и решение уравнения положительным:
|
|
|
|
2 |
|
2 |
2 |
|
2 |
|
|
|
|
|
X p a |
Umax a0 |
|
||||
Umax a0 ср |
|
Umax a0 ср |
|
|
. |
|||||
|
|
|
|
|||||||
X 2 2 2 |
|
X 2 2 2 |
|
|
|
|
X 2 2 2 |
|
|
|
p ср |
p ср |
|
|
|
|
p ср |
|
|
||
|
|
|
|
|
|
|
|
Тогда мы также получаем положительное решение путем вычитания из большего члена меньшего.
Приведенная методика расчета позволяет на основании исходной информации о состоянии изделия, возможных условиях его эксплуатации и при оценке интенсивности процессов потери работоспособности (износа) рассчитать ресурс изделия при требуемой вероятности безотказной работы и количественно оценить вес каждого фактора.
50