
книги / Машины для строительства, ремонта и содержания автомобильных дорог. Асфальтобетонные и цементобетонные заводы
.pdfМикропроцессорная система управления автоматически производит запуск механизмов установки в заданной технологической последовательности, производит вентилирование сушильного барабана, розжиг горелки, в определенное время включает подачу материалов, нагревает их до нужной температуры, выполняет 100%-ный контроль всех механизмов установки. После ввода установки на рабочий режим компьютер автоматически регулирует температуру каменных материалов, соотношение топлива и воздуха, разрежение в сушильном барабане. Высокая точность взвешивания и дозирования обеспечивается за счет применения «упреждения», автоматического контроля и корректировки по дозированию каждого замеса.
Переход с одного рецепта на другой происходит без остановки работы, при этом оператор выбирает новый рецепт из базы, установка дорабатывает необходимое количество замесов и система начинает производить дозирование согласно новому рецепту.
Благодаря применению частотных преобразователей предварительное дозирование начинается еще в агрегате питания, состоящем из четырех или пяти бункеров по 9 м3 каждый. На всех бункерах установлены решетки негабарита и вибраторы.
Между конвейерами устанавливается виброгрохот негабарита, позволяющий удалять материал крупнее 40 мм.
Вуправлении сушильного барабана применен частотный преобразователь, который позволяет выполнять плавный пуск и регулировать обороты в процессе работы, подбирая оптимальный температурный режим. Модернизирована внутренняя часть сушильного барабана, более качественными материалами теплоизолирован сушильный барабан.
Всистеме пылеочистки предусмотрены тканевые фильтры фирмы «Номекс» с удельным весом 500 г/м2. На выходе из дымовой трубы выбросы не превышают 10−20 мг/м3, что является показателем европейского уровня.
Грохот может комплектоваться плетенными либо штампованными си-
тами.
На второй стадии дозирование происходит в дозаторах каменных ма-
териалов, минерального порошка, пыли и битума, которые изготовлены с применением современных тензометрических систем, обеспечивающих высокую точность дозирования.
С помощью инфракрасного датчика система контролирует температуру готового асфальта на выходе из смесителя.
Вконструкции применена пневматика фирмы CAMOZZI (Италия).
Вагрегате минерального порошка (V = 23 м3) использован фильтр итальянского производства, что позволило добиться качественной очистки воздуха, который выходит из емкости при ее заполнении.
81
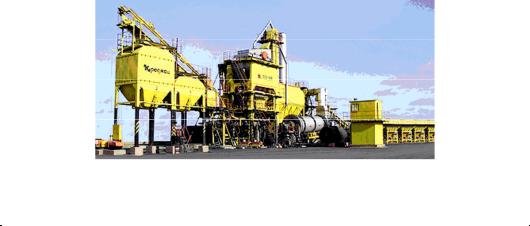
Для контроля уровня минерального порошка и пыли, каменных материалов в конструкции установки применены сигнализаторы верхнего и нижнего уровней итальянского производства фирмы WAM.
В конструкции используются комплектующие ведущих мировых производителей.
Агрегат пыли с собственным элеватором позволяет не только производить дозирование пыли, но и в случае применения очень запыленных исходных материалов часть уловленной пыли (при необходимости) удалять в автотранспорт.
Для возможности изготовления щебеночно-мастичного асфальтобетона в составе завода поставлен агрегат целлюлозной добавки, обеспечивающейдозирование и выдачу вмешалку гранулированныхцеллюлозныхдобавок.
Установка ДС-168
Производительность данной модели − 130−160 т/ч. Асфальтосмесительная установка ДС-168 (рис. 5.5) характеризуется повышенным объемом агрегата питания и бункером агрегата минерального порошка, имеет четыре битумных цистерны и вместительный агрегат готовой смеси, рассчитанный на 100 т. Установка является оптимальным выбором для проведения дорож- но-строительных работ больших объемов.
|
Рис. 5.5. Асфальтосмесительная установка ДС-168 |
|
|
Модификации установки ДС |
|
ДС-1683 |
на жидком топливе с микропроцессорной системой управления |
|
ДС-16863 |
на природном газе с микропроцессорной системой управления |
|
ДС-16837 |
на жидком топливе с микропроцессорной системой управления |
|
с рукавными фильтрами |
||
|
||
ДС-168637 |
природном газе с микропроцессорной системой управления |
|
с рукавными фильтрами |
82
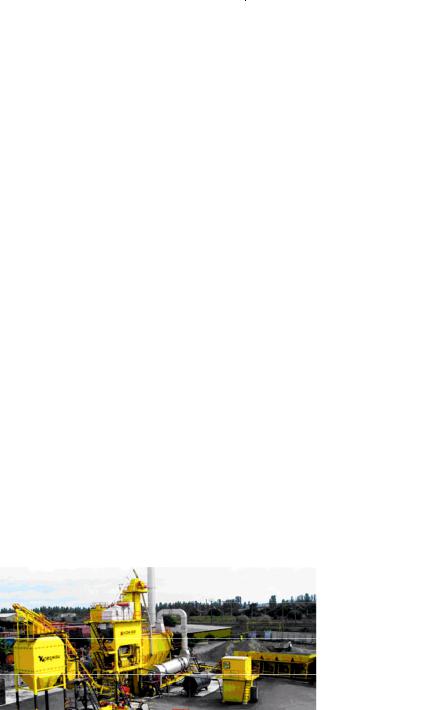
Основные параметры и технические характеристики установки ДС
Производительность номинальная при влажности |
160 |
||
исходных материалов (песка и щебня) до 3 %, т/ч |
|||
|
|||
Вместимость бункеров агрегата питания, м3 |
5 16 = 80 |
||
Вместимость бункеров агрегата готовой смеси, т |
30 + 70 = 100 |
||
Вместимость бункеров агрегата минерального |
2 32,5 = 65 |
||
порошка, м3 |
|||
Вместимость цистерн для битума, м3 |
4 30 = 120 |
||
Тип дозаторов |
весовые на тензодатчиках |
||
Максимальная масса замеса, кг |
2200 |
||
|
|
рукавный фильтр или |
|
Тип пылеулавливающего устройства |
комбинированный: сухой |
||
(циклоны), мокрый (скруб- |
|||
|
|
||
|
|
бер «Вентури») |
|
Удельный расход топлива для приготовления одной |
|
||
тонны смеси: |
5,5–9,5 |
||
– |
при работе на жидком топливе, кг |
||
6,3–10,8 |
|||
– |
при работе на природном газе, м3 (присоединитель- |
||
ное давление газа 0,3 кгс/см2) |
|
||
Установленная мощность электрооборудования, кВт |
400 |
||
Габаритные размеры, м (длина, ширина, высота), max |
55,0×42,5×19,0 |
5.2.2. Асфальтосмесительные установки КДМ
Стационарная асфальтосмесительная установка КДМ-201
Стационарная асфальтосмесительная установка КДМ-201 (рис. 5.6) – одна из последних разработок специалистов ОАО «Кредмаш», зарекомендовавшая себя как мощный комплекс производительностью 80−110 т/ч. В модели собраны все преимущества ранее выпускаемых стационарных установок и добавлены многие инновации, в числе которых увеличение объема бункеров для горячих каменных материалов и наличие агрегата пыли.
Рис. 5.6. Стационарная асфальтосмесительная установка КДМ-201
83
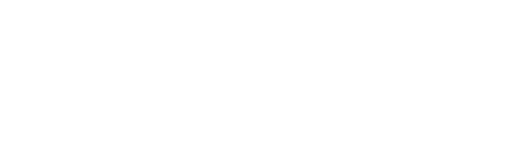
|
Модификации установки КДМ |
|
|
КДМ-2013 |
на жидком топливе с микропроцессорной системой управления |
КДМ-20163 |
на природном газе с микропроцессорной системой управления |
КДМ-20137 |
на жидком топливе с микропроцессорной системой управления |
|
и рукавными фильтрами |
КДМ-201637 |
на природном газе с микропроцессорной системой управления |
и рукавными фильтрами |
Основные параметры и технические характеристики КДМ-201
Производительность номинальная при влажности исход- |
110 |
||
ных материалов (песка и щебня) до 3 %, т/ч |
|||
|
|||
Производительность при влажности исходных материа- |
|
||
лов до 5 % приготовлении мелкозернистых и песчаных |
80 |
||
смесей, т/ч |
|
||
Вместимость бункеров агрегата питания, м3 |
5 8 = 40 |
||
Вместимость бункеров агрегата готовой смеси, т |
70 |
||
Вместимость бункеров агрегатаминерального порошка, м3 |
32,5 |
||
Вместимость бункера агрегата пыли, м3 |
23 |
||
Вместимость цистерн для битума, м3 |
3 30 = 90 |
||
Тип дозаторов |
весовые |
||
на тензодатчиках |
|||
|
|
||
Максимальная масса замеса, кг |
1500 |
||
|
|
рукавный фильтр или |
|
Тип пылеулавливающего устройства |
комбинированный: сухой |
||
(циклоны), мокрый |
|||
|
|
||
|
|
(скруббер «Вентури») |
|
Удельный расход топлива для приготовления одной |
|
||
тонны смеси: |
5,5–9,5 |
||
– |
при работе на жидком топливе, кг |
6,3–10,8 |
|
– |
при работе на природном газе, м3 |
|
|
Мощность нагревателя жидкого теплоносителя, ккал/ч |
300000 |
||
Установленная мощность электрооборудования, кВт |
312 |
||
Габаритные размеры (длина, ширина, высота), м, max |
45,5×39,0×18,7 |
Конструкция асфальтосмесительных установок позволяет выполнять следующие операции технологического процесса:
• предварительное дозирование влажных каменных материалов в агрегате питания, дистанционное изменение подачи каменных материалов из кабины оператора;
84
•просушивание и нагрев каменных материалов до рабочей температуры в сушильном барабане и подачу их к грохоту смесительного агрегата;
•сортировку нагретых каменных материалов на четыре фракции (0−5; 5−10; 10−20; 20−40 мм), временное хранение их в «горячем» бункере вместительностью 19 м3, дозирование и выдачу их в смеситель;
•трехступенчатую очистку выходящих из сушильного барабана дымовых газов от пыли в предварительной системе очистки, циклонах сухой пылеочистки и в мокром пылеуловителе − скруббере «Вентури» (эффективность пылеулавливания составляет 99,7−99,85 % в зависимости от вида применяемых материалов) или очистку в рукавных фильтрах − выбросы пыли составляют при этом не более 20 мг/м3;
•использование уловленной пыли путем подачи ее в отсек «пыли» бункера емкостью 26 м3, позволяющий временно хранить пыль, производить весовое дозирование и подачу в смеситель, а также, при необходимости, выгружать уловленную пыль в технологический автотранспорт для дальнейшей утилизации;
•прием минерального порошка из автоцементовозов, дозирование
ивыдачу в смеситель;
•прием битума из битумовозов (или склада битума), временное хранение, мягкий нагрев его в битумных цистернах жидким теплоносителем (маслом) или огневой нагрев в нагревателе битума, дозирование и подачу его в смеситель;
•обогрев битумных коммуникаций, нагрев битума и топлива горячим маслом, нагретым в нагревателе жидкого теплоносителя;
•подачу смеси скиповым подъемником в бункер агрегата готовой смеси или выдачу непосредственно из смесителя в автотранспорт.
В установках обеспечено:
•автоматизированное и дистанционное весовое дозирование каменных материалов, битума, минерального порошка и пыли, их перемешивание
ивыдача в бункер готовой смеси или автотранспортное средство;
•контроль и регулирование температуры каменных материалов на выходе из сушильного барабана, контроль температуры каменных материалов в «горячем» бункере, температуры битума, топлива и готовой смеси;
•автоматическое или дистанционное управление всеми основными механизмами;
•мягкий пуск и остановка скипового подъемника, сушильного бара-
бана.
85
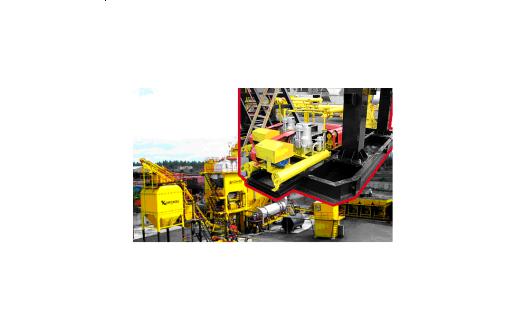
• управление всей установкой централизованно и осуществляется с пульта управления, размещенного в кабине оператора. Кабина оператора оборудована кондиционером и громкоговорящей связью. Блочный принцип изготовления повышает заводскую готовность узлов и позволяет значительно сократить сроки монтажа установки. Применение микропроцессорной системы управления обеспечивает наиболее оптимальный, экономичный режим работы установки, повышает культуру производства и безотказность работы оборудования. При этом вся информация, в том числе и о возможных неисправностях, выводится на дисплей.
Перемещаемая асфальтосмесительная установка КДМ-201М
В отличие от КДМ-201 асфальтосмесительная установка КДМ-201М (рис. 5.7) является перемещаемой. Благодаря производительности 80–110 т/ч, оптимальной вместимости бункеров для готовой смеси, топлива, минерального порошка и горячих каменных материалов данная модель является оптимальной для проведения дорожно-строительных и ремонтных работ любого уровня сложности.
|
Модификации установки КДМ |
|
|
КДМ-2013М |
на жидком топливе с микропроцессорной системой управления |
и комбинированной системой пылеочистки |
|
КДМ-20137М |
на жидком топливе с микропроцессорной системой управления |
|
и рукавными фильтрами |
Рис. 5.7. Перемещаемая асфальтосмесительная установка КДМ-201М
Основные параметры и технические характеристики КДМ-201М
Производительность номинальная при влажности исход- |
110 |
|
ных материалов (песка и щебня) до 3 %, т/ч |
||
|
||
Вместимость бункеров агрегата питания, м3 |
4 8 = 32 |
|
Вместимость бункеров агрегата готовой смеси, т |
72,9 |
86

Вместимость бункеров агрегата минерального порошка, м3 |
32,5 |
|
Вместимость бункера пыли, м3 |
26 |
|
Вместимость цистерн для битума, м3 |
2 30 = 60 |
|
Тип дозаторов (каменных материалов, минирального по- |
весовые на тензодат- |
|
рошка, битума) |
чиках |
|
Максимальная масса замеса, кг |
1500 |
|
|
рукавный фильтр или |
|
|
комбинированный: |
|
Тип пылеулавливающего устройства |
сухой (циклоны), мок- |
|
|
рый (скруббер |
|
|
«Вентури») |
|
Концентрация пыли в очищенном газе на выходе дымовой |
20 |
|
трубы не превышает, мг/нм3 |
||
Удельный расход топлива для приготовления одной тонны |
5,5–9,5 |
|
смеси, кг |
||
|
||
Установленная мощность электрооборудования, кВт |
330 |
|
Время сборки завода, ч |
100 |
|
Время разборки завода, ч |
25 |
|
Габаритные размеры (длина, ширина, высота), м, max |
39,1×34,0×16,8 |
Конструкция асфальтосмесительных установок позволяет выполнять следующие операции технологического процесса:
•предварительное дозирование влажных каменных материалов в агрегате питания;
•просушивание и нагрев каменных материалов до рабочей температуры в сушильном барабане и подачу их к грохоту смесительного агрегата;
•сортировку нагретых каменных материалов на четыре фракции (0−5; 5−10; 10−20; 20−40 мм), временное хранение их в «горячем» бункере, дозирование и выдачу их в смеситель;
•трехступенчатую очистку выходящих из сушильного барабана дымовых газов от пыли в предварительной системе очистки, циклонах сухой пылеочистки и в мокром пылеуловителе − скруббере «Вентури» (эффективность пылеулавливания состовляет 99,7–99,85 % в зависимости от вида применяемых материалов) или очистку в рукавных фильтрах − выбросы пыли составляют при этом не более 20 мг/м3;
•использование уловленной пыли путем подачи ее элеватором в «горячий» бункер;
•прием минерального порошка из автоцементовозов, дозирование
ивыдачу в смеситель;
87
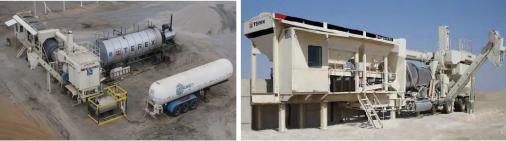
•прием битума из битумовозов (или склада битума), временное хранение и нагрев его в битумных цистернах до рабочей температуры, дозирование и подачу в смеситель;
•выдачу смеси в автосамосвал или подачу ее скиповым подъемником
вбункера готовой смеси;
•обогрев битумных коммуникаций и насосов горячим маслом, нагретым в змеевике нагревателя битума.
Асфальтосмесительные установки являются перемещаемыми и быстромонтируемыми, но имеют почти все преимущества стационарных установок ДС-185.
Сокращение времени монтажа и демонтажа обеспечивается: повышенной монтажной готовностью за счет блочного (модульного) выполнения конструкции, укрупнения узлов и снижения количества болтовых соединений; установкой и проверкой в заводских условиях работы всех комплектующих; выполнением электрических соединений на быстромонтируемых штекерных разъемах; контрольным монтажем блоков и агрегатов установок
взаводских условиях; теплоизоляцией битумопроводов, выполненной в условиях завода; применением конструкции соединений, способствующих быстрому монтажу и демонтажу узлов. Узлы установки приспособлены для
транспортировки на дальние расстояния автомобильным транспортом и трейлерами с низкой платформой или железнодорожным транспортом. Установки монтируются на временной строительной площадке, не требующей выполнения специальных бетонных фундаментов.
5.2.3. Асфальтобетонные заводы фирмы Magnum
Завод Magnum 80
Качество асфальтобетонного завода Magnum 80 (рис. 5.8) обеспечивается экономичностью и рентабельностью в комбинации с автоматизированным режимом работы по укладке и строительству дорог.
Рис. 5.8. Асфальтобетонный завод Magnum 80
88
Асфальтобетонный завод Magnum 80 стал более цельным, современным и эффективным. Были внесены определенные инновационные изменения для полного удовлетворения потребностей новых клиентов и расширения сферы использования оборудования.
Завод противоточного типа Magnum 80 был разработан с помощью самого современного компьютерного оборудования и математического моделирования турбулентных потоков с целью предложить значительные преимущества в процессе приготовления асфальтобетонных смесей и увеличить производительность до 80 т/ч.
Супермобильный завод значительно сэкономит время монтажа на месте. Его можно смонтировать и начать работу всего за два дня. Это делает его более практичным и мобильным для применения в этой области.
Работа АБЗ была полностью автоматизирована, что дает возможность оператору осуществлять абсолютный контроль всех процессов и обеспечивать производство асфальтовой смеси очень высокого качества. Основными факторами, влияющими на старение или окисление горячей асфальтобетонной смеси (HMAC), являются температура смеси и степень воздействия кислорода.
Небольшой процент кислорода и низкая температура смешивания повышают срок службы конечного продукта. Ключевым аспектом при приготовлении высококачественного асфальтобетона является смешивание разогретых фракций инертного материала со связующим веществом. На этой стадии в отношении качества смеси можно отметить, что чем меньше кислорода, тем лучше; таким образом, можно не допустить преждевременного старения смеси.
Технические характеристики АБЗ Magnum 80
Производительность, т/ч |
80* |
|
Количество шасси |
1 |
|
Количество осей/шин |
3 оси/12 шин |
|
Загрузочные бункеры |
3 (стандарт)/4 (опция) |
|
Объем бункера, м3 |
7 |
|
Система дозирования |
отдельная система взвешивания с отцентрованным |
|
датчиком веса |
||
|
||
Сушка |
протипоточного типа, диаметр 1,8 м |
|
в самой широкой секции |
||
|
||
Размеры сушильного барабана |
диаметр 1,5 м в самой узкой секции, длина 6,0 м |
89
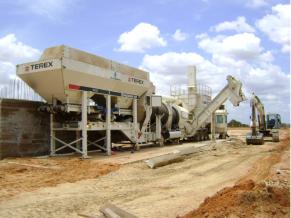
Горелка |
тип Terex CF 04 |
|
Мощность горелки (ккал/ч) |
10.000.000 |
|
Смеситель |
внешний вращательный |
|
|
рукавный фильтр: 288 шт. |
|
Система фильтрации |
гладкий полиэстер (стандарт) − |
|
|
сорта Номекс (опция) |
|
Эффективность |
более 99,9 % |
|
выбросы частиц − менее 50 мг/Н м3 |
||
Элеватор |
драг-конвейер с лопатками зубчатого типа, |
|
предотвращающими расслоение смеси |
||
|
||
Бункер-накопитель |
1 м3 (стандарт) / 10, 25 или 50 м3 (опция) |
|
Кольцо для подачи вторично- |
стандартное исполнение |
|
го материала |
||
|
Примечание.*Производительность АБЗ может меняться в зависимости от следующих факторов: влажность материала, высота местонахождения АБЗ, процент мелких фракций в смеси, температура смеси, теплопроводная способность топлива и удельный вес фракций материала
Завод Magnum 140
Качество асфальтобетонного завода Magnum 140, экономичность и рентабельность в комбинации с автоматизированным режимом работы по укладке и строительству дорог. Асфальтобетонный завод Magnum 140 (рис. 5.9) был детально проанализирован с целью увеличить его производительность, предложить снижение расхода изнашиваемых материалов, а также сделать весь завод и его продукцию более эффективными и практичными.
Рис. 5.9. Асфальтобетонный завод Magnum 140
90