
книги / Монтаж компрессоров, насосов и вентиляторов
..pdfпроизводить в определенной последовательности путем одно временной затяжки симметрично расположенных пар гаек (попарная сборка) либо диаметрально расположенных гаек (рис. 6).
Ответственные соединения до заданного усилия затягива ют постепенно, в несколько "обходов”.
"Обход"........................................................ |
Усилие затяжки, Рэ |
первый............................................................................................ |
0,5 |
второй............................................................................................. |
0,7 |
третий, четвертый......................................................................... |
1 |
Усилие затяжки контролируют одним из следующих спо собов: по моменту закручивания, удлинению болта (шпиль ки), углу поворота гайки, числу ударов гайковерта.
Для сборки резьбовых соединений применяют инстру мент, ручные машины и специальные устройства.
3.2. Сборка зубчатых передач
Для зубчатых цилиндрических и конических, а также червячных передач установлено 12 степеней точности, к каж дой из которых предъявлены нормы по кинематической точ ности колеса, плавности его работы и контакту зубьев. Кине матическая точность регламентирует полную погрешность уг ла поворота зубчатых колес за оборот. Плавность работы ко леса -- величина составляющих полной погрешности угла по ворота зубчатого колеса, многократно повторяющихся за обо рот. Нормы контакта зубьев определяют точность соблюдения относительных размеров пятна контакта сопряженных зубьев колес в передаче. Независимо от степени точности колес и пе редач установлены нормы бокового зазора.
Наиболее типичные погрешности при сборке зубчатых пе редач и методы их устранения:
недостаточный зазор в зубьях по всему венцу. Требуется замена колес (если все зубья на одном или обоих колесах выполнены полнее) или перепрессовка втулок корпуса и их расточка (если расстояние между осями колес меньше про ектного);
2. Нормы контакта зубьев в цилиндрических передачах, %, не менее
Степень |
По высоте |
По длине |
Степень |
По высоте |
По длине |
точности |
|
|
точности |
|
|
3 |
65 |
95 |
8 |
40 |
50 |
4 |
60 |
90 |
9 |
30 |
40 |
5 |
55 |
80 |
10 |
25 |
30 |
6 |
50 |
70 |
11 |
20 |
25 |
7 |
45 |
60 |
|
|
|
со to
3. Допуски на монтаж глобоидных червячных передач |
|
|
Показатель |
Допуск, мкм, при межосевом расстоянии, мм |
|
|
от 315 до 630 |
от 630 до 1250 |
|
1 |
|
Предельные смещения средней плоскости червяка |
75 |
100 |
То же, колеса |
75 |
100 |
Предельные отклонения межосевого расстояния в передаче |
75 |
100 |
Перекос осей в передаче |
45 |
60 |
Пятно контакта на витке зуба колеса, %, не менее: |
80/70* |
80/70* |
по высоте |
||
по ширине |
45/25* |
45/25* |
Пятно контакта на витке червяка, %, не менее: |
60/40* |
60/40* |
по длине |
* До черты —для степени точности '*7”, после черты —для степени точности ,f8”.
увеличенный зазор по всему венцу. Дефект устраняют аналогично первому случаю (в обратном порядке);
неравномерный зазор в зубьях. Находят наименьший за зор» расцепляют колеса и» повернув одно из них на 180°» сно ва сцепляют. Если зазор не выравнялся» то определяют» ка кое из колес подлежит замене;
биение торцов зубьев (перекос колеса на валу). Запрессо вывают новую втулку и растачивают ее.
Боковой зазор в крупных зубчатых передачах большого модуля проверяют путем прокатывания между зубьями свин цовых проволочек (3—4 шт.), устанавливаемых по длине зу- *ба. Диаметр проволочек составляет 1,4—1,5 величины боково го зазора. Каждую проволочку смазывают техническим вазе лином и в виде П-образной скобки надевают на зуб. Толщину сплющенных частей проволочек с обеих сторон зуба измеря ют микрометром, что в сумме и дает боковой зазор. Одновре менно определяют непараллельность и перекос осей. Наличие зазора может быть так же проверено прокаткой между зубья ми полоски писчей бумаги —отсутствие на ней разрывов сви детельствует о наличии зазора.
Плавность хода колеса определяют, провертывая собран ную передачу динамометрическим ключом.
При проверке норм контакта зубьев (табл. 2) зубья мень шего колеса покрывают тонким слоем лазури и поворачива ют зубчатую пару, после чего осматривают следы прилегания на зубьях большого колеса. Основная причина непра вильного прилегания — непараллельность и перекос осей от верстий в корпусе или те же погрешности в узле ’’зубчатое колесо —вал”.
При пятне контакта по высоте и длине зуба в пределах 10—15% зубья припиливают и шабрят, а при более удовлет ворительном контакте зацепление прирабатывают (притира ют) абразивными пастами. Примерный состав притирочной пасты: солидол — 30, олеиновая кислота - 2, стеарин — 10, абразивный порошок —58%.
Глобоидные передачи (табл. 3) значительно сложнее в из готовлении и монтаже, чем передачи с цилиндрическим чер вяком.
3.3. Сборка подшипников
На монтаже, как правило, приходится собирать подшип ники скольжения разъемного типа. При этом необходимо обеспечить выполнение следующих требований: проверить на личие отверстий и канавок с плавно закругленными кромка-
Рис. 7. Схема проверки верхнего зазора между вкладышем и валом
а}, Л2 * в}. <*2 *’ места укладки свинцовой прово локи на разъеме подшипника; Cj, С2 - места укладки свинцовой проволоки на валу
ми для подвода смазки (совпадение маслоподводящих отвер стий корпуса ц вкладышей с допуском 0,2—0,5 мм); шерохо ватость поверхностей вкладышей должна быть не ниже 5-го класса чистоты; плотное (без отслоений) прилегание баббито вого слоя к основному металлу вкладыша; прилегание вкла дышей к основанию и крышке по площади не менее 70%; совпадение маркировки вкладышей с сопрягаемыми деталя ми; углубление фиксирующих штифтов относительно рабочей поверхности вкладыша не менее чем на 1—2 мм; плотное прилегание стыков верхнего и нижнего вкладышей, а также вкладышей к шейкам установленного вала с точностью, ука занной в чертеже (шейка вала должна оставлять следы кра ски на поверхности вкладыша, ограниченной дугой не менее 60°; точность прилегания для нагруженных вкладышей со ставляет 5—12 пятен, для ненагруженных — 4—6 пятен на квадрате 25x25 мм); наличие диаметральных зазоров между вкладышем и валом; наличие натяга между крышкой и вер хним вкладышем; равномерность и плотность затяжки бол тов' в собранном подшипнике.
Верхний зазор между валом и вкладышем проверяют сле дующим образом (рис. 7). Отрезки свинцовой проволоки диа метром на 0,2—0,3 мм больше возможного зазора закладыва ют в нескольких местах между вкладышем и шейкой вала (проволоку слегка смазывают маслом). После этого крышку подшипника затягивают гайками. Проволока при этом де-
Диаметр |
|
|
Зазор, мм |
Диаметр |
|
|
Зазор, мм |
шейки |
min |
| |
max |
шейки |
min |
| |
max |
вала, мм |
вала, мм |
||||||
90 |
0,25 |
|
0,35 |
400 |
0,5 |
|
0,65 |
100 |
0,25 |
|
0,35 |
225 |
0,5 |
|
0,65 |
115 |
0,25 |
|
0,35 |
255 |
0,5 |
|
0,65 |
125 |
0,25 |
|
0,35 |
305 |
0,75 |
|
0,9 |
150 |
0,25 |
|
0,5 |
355 |
0,75 |
|
0,9 |
175 |
0,38 |
|
0,5 |
400 |
0,75 |
|
0,9 |
формируется, толщина образовавшихся пластинок будет ха рактеризовать зазоры в местах установки проволоки, мм:
д 1 = СХ - (ах + bj)/2 ; д 2 = С2 - (а2 + Ь2)/2,
где а^, Д2* ^1» &2* с1* с2 " толЩины сплющенных проволок.
Аналогичным способом определяют натяг между крыш кой и верхним вкладышем.
Верхний зазор во вкладышах указывают в чертежах. При отсутствии этих сведений следует руководствоваться табл. 4.
Боковые зазоры между валом и нижним вкладышем оп ределяют пластинчатым щупом. Осевой зазор (между галте лями вала и торцом вкладыша) проверяют щупом или инди катором часового типа при крайних смещениях вала (0,1—0,8 мм) вдоль его оси.
Подшипники качения монтируют по двум неподвижным посадкам —внутреннего кольца с валом и наружного кольца с корпусом без специальных креплений, препятствующих проворачиванию.
Основные требования, предъявляемые к собираемым уз лам: тщательная промывка; регулирование радиальных зазо ров между роликами или шариками и наружным кольцом подшипника; контроль цапф валов и посадочных мест в кор пусе подшипника. Запрессовку подшипников осуществляют обычно путем их нагрева (в масляных ваннах или индукци онными нагревателями). При монтаже крупных подшипни ков качения во многих тяжелых машинах применяют гидро прессовый метод, при котором масло подают под давлением в зону контакта сопрягаемых поверхностей вала и подшипни ка, чем обеспечивается полужидкостное трение. Это способст вует снижению коэффициента трения с 0,15 (при сухом тре нии) до 5х10-4.
Надежное соединение подшипника с валом и необходи мый радиальный зазор обеспечиваются путем уменьшения
осевого перемещения подшипника. Однако радиальный зазор в установленном подшипнике не всегда можно измерить. По этому чаще всего проверяют осевой зазор, т.е. осевое переме щение вала с напрессованным внутренним кольцом относи тельно наружного кольца подшипника. Особое внимание не обходимо уделять контролю осевых зазоров в регулируемых подшипниках (радиально-упорные шарико- и роликоподшип ники, двойные упорные шарикоподшипники).
Наиболее распространенные погрешности сборки подшип ников и вызываемые ими дефекты:
Использование при |
сборке |
Резкий шум при работе, |
|||||
ударного инструмента |
вмятины |
нй |
дорожках |
||||
Попадание |
грязи в под |
качения |
|
|
шум, |
||
Неравномерный |
|||||||
шипник |
|
|
повышенный |
износ |
ко |
||
|
|
|
лец и тел качения |
|
|
||
Перекос кольца |
|
Шелушение поперек |
до |
||||
|
|
|
рожек качения |
|
|
|
|
Недостаточный зазор |
|
Металлический шум, пе |
|||||
Поворачивание внутрен |
регрев подшипника |
|
|
||||
Перегрев |
подшипника, |
||||||
него кольца на валу |
|
износ вала под кольцом |
|||||
Чрезмерно тугая насадка |
Трещины по окружности |
||||||
колец |
|
|
|
|
|
|
|
Несоосность |
вала |
и |
Выкрошивание краев ро |
||||
корпуса, |
роликопод |
ликов и |
сопряженных с |
||||
шипника |
|
|
ними поверхностей доро |
||||
|
|
|
жек качения |
|
|
|
3.4. Сборка соединительных муфт
Соосность вертикальных валов (рис. 8) проверяют с по мощью четырех струн, которые подвешивают по осям монти руемого оборудования к хомуту, закрепленному к верхнему цалу. Для измерения расстояния между шейками валов и струнами применяют штихмасы. При проверке вертикально сти с помощью четырех струн валы не проворачивают (повер хность валов в местах замеров должна быть гладкой и без за боин). Результаты точности замеров определяют по формуле Р = [(аг + Ьг) + (с2 + rf2)l - Ка 2 + ь2) + (ci + rfi)L
Неточность измерений при сопоставлении восьми эсер ов не должна превышать 0,02 мм. При превышении этого допу ска замеры производят повторно. Отклонения оси валов от вертикали:
A I =YAX 2 +Ау2,
где ьх и ьу - уклон в направлениях координат х и у.
Рис. 8. Выверка соосности а - вертикальных валов; б -- горизон
тальных валов; /--// - плоскости за меров; 1 - вал прицентровываемый; 2 •• вал базовый; N 1 -4 - подшип
ники
Уклоны Дх = [{а2 - Ь2) [(а; + Ь{)]/2;Ау =[(е2 - Ъ2) - (<?i dx)V2.
Отклонение оси валов от вертикали &10 = И/l, где I —дли на участка валов между точками замеров.
Соосность горизонтальных валов определяется центровкой по полумуфтам. Радиальные и торцевые зазоры при центров
ке измеряют при исходном положении 0° и после поворота валов на 90, 180 и 270° в направлении рабочего вращения. При каждом положении полумуфт производят один замер ра диального зазора и два — торцевых зазоров (сверху и снизу или справа и слева) между полумуфтами. Для контроля пра вильности измерений после четырех замеров необходимо ус тановить полумуфты в первоначальное положение (0). Ре зультаты повторных измерений в этом положении должны совпадать с первоначальными, в противном случае следует найти причину отклонения и устранить ее. Результаты изме рений заносят в круговую диаграмму. Правильность измере ния можно проверить, сопоставив суммы результатов, полу ченных при измерении на противоположных сторонах полу муфт. Эти суммы должны быть равны между собой. Допуска емое отклонение не должно превышать 0,02 мм.
Результирующую замеров зазоров по торцу полумуфт в
каждой из четырех точек окружности определяют как сред нюю арифметическую величину в каждом положении валов (сверху, снизу, справа и слева): т *
*.-<< +*.W « - € +0/2; t. - (С + й/2;
^-<£+0 /*-
Полученные замеры по торцу и окружности приводят к нулю путем вычитания из полученных результатов наимень шего зазора.
В случае неудовлетворительных результатов центровки и необходимости перемещения валов в горизонтальной и верти кальной плоскостях определяют величины перемещения (ус ловные обозначения соответствуют рис. 8, б)\
* 1 = ML + l)/dm; уг = Al/dm; х2 = у2 = R/2; х = хх + х2;
У = У\ + У2>х = ML +l)/dm + R/2; у = M /dm + R/2,
где Д e iîj - ^ 2 *• расцентровка валов по окружности; A e Aj - А 2 " рас-
центровка валов по торцу.
3.5. Сборка уплотнений
При наличии избыточного давления или вакуума во внут ренних полостях насосов в местах прохода вала через стенки корпуса применяют особые уплотнительные устройства, на зываемые сальниками или уплотнениями контактного тре ния (рис. 9). При отсутствии или неисправности сальников происходит выброс перемещаемой насосом жидкости наружу
I В О Д А И З Н А П О Р Н О Г О П А Т Р У Б К А
Рис. 9. Сальниковые уплотнения валов насосов а ~ с мягкой набивкой; б •• с мягкой набивкой и водяным уплотнением
(сальники со стороны всасывания насоса); в - охлаждаемый сальник; 1 - корпус насоса; 2 - кольца шнура; 3 - болт; 4 - втулка
на напорной стороне или подсасывание наружного воздуха внутрь насоса на стороне ее всасывания.
Сальник с мягкой набивкой имеет в корпусе цилиндриче скую выточку, заполненную кольцами шнура из мягкого промасленного материала (хлопка, пеньки, асбеста). Нажати ем гаек, навертываемых на болты, втулку сальника плотно загоняют в выточку и, раздавая мягкую набивку в стороны, уплотняют вал. Вследствии трения вала о набивку при работе насоса выделяется некоторое количество теплоты. Для отвода
еечерез сальник подают небольшое количество воды.
Внасосах, подающих жидкость с высокой температурой, может происходить сильный нагрев вала и деталей сальника. Это ведет к быстрому износу набивки и нарушению плотно сти сальника. В таких случаях сальник выполняют с поло-
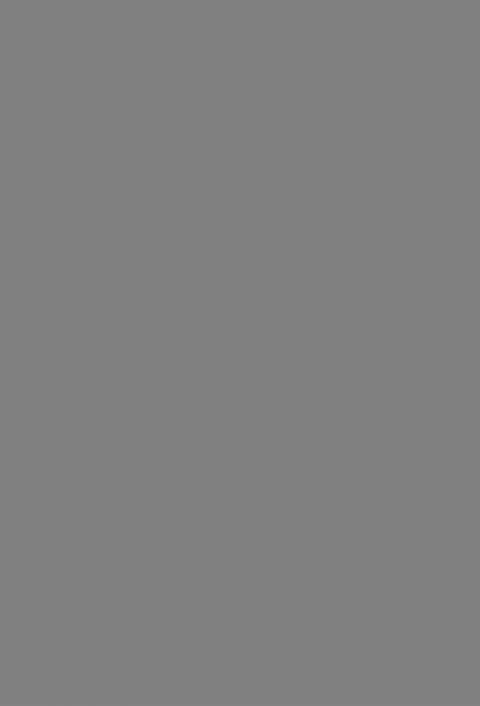