
книги / Основы технологии машиностроения. Методы обработки заготовок и технологические процессы изготовления типовых деталей машин
.pdf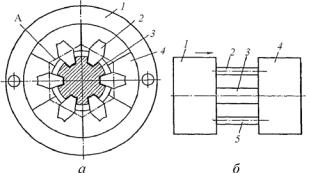
шлицевой вал поворачивают, так что шлифовальный круг обрабатывает впадины постепенно, одну за другой. Обычно вал поворачивается автоматически после каждого двойного хода стола. Этот способ менее производительный, чем пер- вый, но, как правило, позволяет достичь более высокой точности и уменьшить шероховатость шлифованных по- верхностей.
Для повышения производительности второго способа две операции объединяют в одну путем применения станков, на которых шлицы шлифуются одновременно тремя шлифо- вальными кругами, установленными на одном шлифоваль- ном шпинделе. Один шлифовальный круг шлифует впадину, а два других – боковые поверхности шлицев (рис. 10.5, в).
Накатывание шлицев валов без нагрева детали осуще-
ствляется роликами, имеющими профиль, соответствующий форме поперечного сечения шлицев. Вращающиеся на осях ролики (диаметр до 100 мм) по одному на каждый шлиц расположены радиально в сегментах 4 массивного корпуса 1 накатной головки (рис. 10.6, а). При передвижении головки по детали 3 свободно вращающиеся ролики 2, вдавливаясь
Рис. 10.6. Схемы накатывания шлицев вала: а – схема накатной головки для шлиценакатного станка; б – схема расположения накатной головки, зажимного патрона и обрабатываемой детали на шлиценакатном станке
231
вповерхность вала, образуют на ней шлицы, соответствую- щие по форме профилю ролика 2. Все шлицы накатываются одновременно без вращения детали.
На специальных станках для накатывания шлицев (рис. 10.6, б) накатная головка 1 размещается на салазках, для которых направляющими служат валы 2 и 5, соеди- няющие две массивные стойки. Салазки перемещаются приводом от гидравлического цилиндра, расположенного
взадней стойке. В передней стойке находится гидравличе- ский зажимной патрон 4, в котором закрепляется обраба- тываемая деталь 3. Каждый ролик независимо регулируется на требуемую высоту. Головка как самостоятельный узел снимается со станка, не нарушая расположения роликов. На смену роликов затрачивается 5–10 мин, на наладку ро- ликов по высоте – около 30 мин. На таких станках наи- большее число накатываемых шлицев – до 18, а наимень- шее – 6 (на валах диаметром 16 мм). Продольная подача составляет 0,5–0,9 мм/мин при обильной подаче в зону об- работки сульфофрезола или масла индустриального И-20А. Получаемая точность шлицев по шагу 0,04 мм, отклонение от прямолинейности не превышает 0,04 мм на 100 мм длины.
Процесс накатывания весьма производителен, так как все шлицы накатываются одновременно, при малых затра- тах времени, с достаточно высокой точностью.
Протягивание и строгание шлицев вала осуществля-
ется на протяжных и строгальных станках с применением специальных приспособлений.
Для протягивания сквозных шлицев применяется специальная протяжка с ножами, профиль режущей части которых соответствует форме шлица. Каждый шлиц протя- гивается поочередно с помощью делительного устройства при обильной подаче в зону резания сульфофрезола или
232
веретенного масла. При протягивании несквозных шлицев используется блочная протяжка, в которой режущие зубья имеют независимое взаимное перемещение в радиальном направлении (рис. 10.7). В корпусе 1 блока устанавливают- ся по скользящей посадке ножи 2 прямоугольного сечения. Форма режущей части ножа соответствует профилю шлица. Каждый нож имеет независимое перемещение вдоль паза блока. Прижимная планка 3 регулирует зазор, необходи- мый для скольжения ножей в блоке. Ползуны 6 соединяют- ся с ножами тягой 7, оси роликов 5 закреплены в ползунах 6, пружины 4 при помощи тяги 7 прижимают ролики к копир- ной линейке. В конце хода каждого ножа копир отводит ро- лик и выводит нож из обрабатываемой детали. Ножи затачи- ваются в специальном приспособлении комплектно. Обра- ботка производится с применением в качестве СОЖ суль- фофрезола или масла индустриального И-20А.
Процесс изготовления шлицев на валах строганием (шлицестроганием) аналогичен процессу долбления зубьев зубчатых колес с помощью многорезцовой головки. В этом случае все шлицы также обрабатываются одновременно набором профильных резцов, число которых равно числу впадин обрабатываемого шлицевого вала. Обрабатываемая деталь, расположенная вертикально, движется возвратно- поступательно. При каждом ходе вверх она входит внутрь неподвижной резцовой головки, в радиальных пазах кото- рой размещены резцы. Все резцы одновременно нарезают шлицы, получая радиальную подачу на двойной ход обра- батываемой детали. При обратном ходе детали (вниз) резцы в головке отходят в радиальном направлении, во избежание трения задних поверхностей резцов об обрабатываемую поверхность.
233
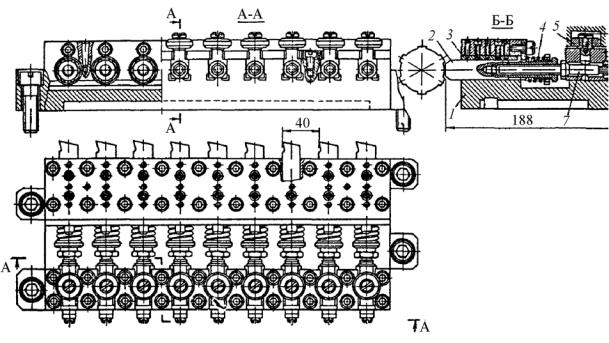
234
Рис. 10.7. Блочная протяжка для протягивания несквозных шлицев
Процесс шлицестрогания производителен и может быть применен в крупносерийном и массовом производстве при большом выпуске одинаковых деталей, так как для ка- ждого числа шлицев должен быть изготовлен комплект специальных резцов. Наиболее выгодно применять его для обработки шлицев под последующее шлифование.
Специальные шлицестрогальные автоматы модели МА-4В могут быть использованы как автономно, так и в составе автоматических линий. Главное движение, движение подачи и движение отвода резцов осуществля- ются гидравлическим приводом. На этих станках можно обрабатывать валы с глухими и сквозными шлицами диа- метром от 25 до 60 мм при длине прорезаемой впадины от 70 до 350 мм и наибольшей глубине 3,5 мм. Скорость рабочего хода 22 м/мин, обратного – 28 м/мин, диапазон подач бесступенчатый от 0,03 до 0,15 мм/дв. ход. Номинальная сила тяги 3000 кгс (30 кН).
Весьма производительным методом обработки шли- цев вала является одновременное долбление всех впадин шлицев специальной многорезцовой головкой, аналогичной многорезцовой головке для долбления зубчатого колеса.
Обработка шлицевых поверхностей в отверстиях
втулок, зубчатых колес и других деталей производится обычно протягиванием.
Сначала отверстие и торец обрабатывают предвари- тельно (сверлением и зенкерованием с подрезкой торца), потом отверстие протягивается круглой протяжкой, а затем – шлицевой протяжкой. Шлицевые отверстия до 50 мм обыч- но протягиваются одной комбинированной протяжкой.
Если деталь с отверстием подвергается термической обработке (например, закалке), то цилиндрическая поверх- ность отверстия, которая сопрягается с дном впадины шли-
235
цев вала, шлифуется на внутришлифовальном станке (при центрировании по внутреннему диаметру шлицев вала).
Протягивание винтовых шлицев отверстий отличает- ся от протягивания обычных отверстий тем, что в процессе работы движение режущих кромок зубьев протяжки долж- но осуществляться по винтовой линии, что достигается со- четанием поступательного и вращательного движений, ко- торое может быть достигнуто двумя способами. Первый способ – оба движения сообщаются протяжке при непод- вижной детали. Второй способ – поступательное движение сообщают протяжке, а вращательное – детали.
236
11. СПЕЦИАЛЬНЫЕ МЕТОДЫ ОБРАБОТКИ
Наряду с обработкой заготовок резанием, сопровож- дающимся снятием стружки, применяется ряд специальных методов обработки без снятия стружки. Использование этих методов повышает производительность и точность обработ- ки, а также увеличивает прочностные свойства деталей.
Специальные методы обработки можно разделить на методы обработки давлением в холодном состоянии
ифизико-механические методы обработки.
11.1.Обработка давлением в холодном состоянии
Кобработке заготовок давлением в холодном состоя- нии относятся: калибрование отверстий шариком и оправ- кой; редуцирование; обработка поверхностей гладкими роликами и алмазным выглаживанием; давильные работы; накатывание рифлений; упрочнение поверхностей шарика- ми; дробеструйная обработка.
Калиброванию подвергают поверхности гладких ци- линдрических отверстий, а также отверстия с фасонным поперечным сечением.
Короткие цилиндрические отверстия калибруют на прессах, проталкивая гладкую оправку (рис. 11.1, б, в) или шарик (рис. 11.1, а) через обрабатываемое отверстие с натягом (иногда этот процесс называют дорнованием отверстий).
При калибровании возникает пластическая деформа- ция металла, в результате которой незначительно увеличи- вается диаметр обрабатываемого отверстия, повышается твердость и снижается шероховатость поверхности.
Длинные отверстия калибруют протягиванием калиб- рующей оправки через обрабатываемое отверстие на про- тяжном станке (рис. 11.1, г). Если обрабатываемой заготовке
237
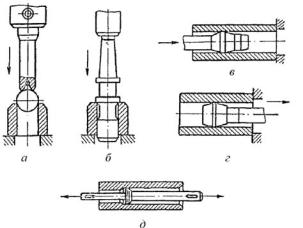
Рис. 11.1. Схемы калибрования отверстий: а – протал- киванием шарика; б и в – проталкиванием оправки;
г– протягиванием оправки; д – протягиванием оправки
свозвратно-поступательным движением
или калибрующей оправке придать дополнительное враще- ние, то можно калибровать участки отверстия, расположен- ные по винтовой линии.
Несквозные отверстия калибруют оправкой, которая совершает возвратно-поступательные движения (рис. 11.1, д).
Калибрование повышает точность от 25 до 35 %,
атакже исправляет погрешности формы в поперечном сече- нии отверстия (погрешности направления оси отверстия ос- таются). Шероховатость поверхности после калибрования во многом зависит от исходной шероховатости и свойств ма- териала заготовки. Поэтому, чтобы достигнуть хороших ре- зультатов, отверстие под калибрование следует растачивать или развертывать, а калибрование производить при обильной подаче сульфофрезола или масла типа И-20А в зону обработ- ки. В этом случае достигается точность 6–7-го квалитета,
ашероховатость поверхности Ra = 0,08…0,63 мкм.
238
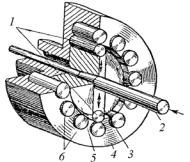
Применяемые для калибрования стальные шарики (шарики подшипников) имеют то преимущество, что срок их использования более продолжителен, так как они имеют практически бесконечное количество калибрующих поя- сков. Кроме того, смещение точки приложения проталки- вающей силы не вызывает их перекоса. Однако область применения шариков ограничивается их стандартными размерами.
Калибрующие оправки изготовляются цельными или сборными с поясками любых размеров.
Для повышения износостойкости калибрующий ин- струмент подвергают хромированию или азотированию, а также применяют наплавку калибрующих поверхностей твердым сплавом.
Редуцирование, или формообразование детали мето- дом обжатия или вытягивания заготовок, является прогрес- сивным методом, обеспечивающим по сравнению с обработ- кой точением и шлифованием увеличение производительно- сти в 5 раз со значительной экономией металла и повышени- ем механических свойств обработанного поверхностного слоя благодаря упрочнению и созданию напряжений сжатия. Этот метод обеспечивает точность 7–8-го квалитета и шеро- ховатость поверхности Ra = 0,08…0, 63 мкм.
Принцип редуциро- вания наружных поверхно- стей заключается в после- довательном обжатии заго- товки (рис. 11.2). Заготовка по мере продвижения вдоль оси деформируется под действием сжимающих сил вращающихся матриц. При этом происходит течение металла заготовки в на-
239
правлении ее движения до тех пор, пока заготовка не будет обжата до размера, соответствующего наименьшему диа- метру желоба матриц. Процесс редуцирования осуществля- ется следующим образом. Шпиндель 5 головки для редуци- рования, вращающейся с определенной скоростью, имеет диаметральный паз прямоугольного сечения, по которому
кцентру и от центра свободно перемещаются бойки с мат- рицами 3. Последние, соприкасаясь во время работы свои- ми рабочими поверхностями с металлом прутка 2, придают заготовке требуемую форму, обжимая и вытягивая ее. На внешних торцах бойков установлены опорные ролики 1. Шпиндель 5 расположен внутри обоймы 4, в отверстиях которой по окружности свободно установлены ролики 6 таким образом, что их боковые поверхности частично вы- ступают из обоймы.
При взаимодействии шпинделя 5 с бойками и матри- цами 3 последние под действием центробежной силы отхо- дят от центра к периферии в тот момент, когда ролики 1 находятся в пространстве между роликами 6, и сходятся
кцентру, когда ролики 1 наталкиваются на ролики 6. При этом матрицы 3 своими рабочими поверхностями приходят в соприкосновение с металлом заготовки, пластически де- формируя его: заготовка обжимается и вытягивается. Стан- ки для редуцирования обеспечивают вращение шпинделя от 150 до 500 об/мин, при этом число обжатий заготовки колеблется от 1000 до 3500 в минуту, а сжимающая сила составляет порядка 200 тонн.
Обкатка поверхностей гладкими роликами заключа-
ется в том, что свободно вращающиеся ролики, прижима- ясь к обрабатываемой поверхности под давлением при обильном охлаждении веретенным маслом, сминают не- ровности и создают упрочненный слой, повышающий экс- плуатационные свойства поверхности детали.
240