
книги / Основы технологии машиностроения. Методы обработки заготовок и технологические процессы изготовления типовых деталей машин
.pdf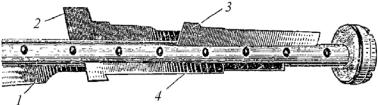
Если необходим второй проход, то каретку суппорта отводят вручную в исходное положение и после замены копира первого прохода на копир второго прохода повто- ряют цикл обработки.
С применением лепестковых копиров (рис. 7.6) мо- жет быть осуществлена как многопроходная обработка данной заготовки, так и обработка различных по конфигу- рации заготовок без замены копира, при этом каждой новой форме поверхности будет соответствовать свой шаблон ле- песткового копира.
Рис. 7.6. Общий вид лепесткового копира
Лепестковый копир представляет собой набор из пло- ских шаблонов 1, 2, 3, 4 (в масштабе 1 : 1 с контуром обра- ботки), закрепленных на оправке, устанавливаемой в цен- трах гидравлического суппорта. При применении лепестко- вых копиров обычный универсальный токарный станок, снабженный гидравлическим копировальным устройством, оснащается механизмом для ускоренного возврата каретки суппорта в исходное положение (обгонной муфтой), меха- низмами включения и выключения гидравлического суппор- та и поворота лепесткового копира. Если необходимо обес- печить передачу движения в масштабе или конструктивной связи между расположенными в разных плоскостях подвиж- ными узлами, применяют сочетание копиров с рычажными механизмами.
141
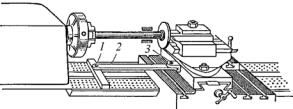
Сферические выпуклые и вогнутые поверхности можно обрабатывать также при помощи штанг или пласти- нок, заменяющих собой копиры.
На рис. 7.7 показано обтачивание сферической голов- ки клапана путем шарнирного соединения суппорта с непод- вижной осью 1 и осью 3 при помощи штанги 2, длина кото- рой соответствует радиусу сферы головки клапана. Попе- речная подача суппорта производится вручную, причем суп- порт одновременно перемещается вдоль станины станка, и при этом резец описывает окружность требуемого радиуса.
Рис. 7.7. Обтачивание сферической головки клапана
Фасонные поверхности можно обрабатывать на токар- но-револьверных станках, гидрокопировальных станках и на станках с ЧПУ. Применение станков с ЧПУ позволяет обта- чивать фасонные поверхности любой сложности (по конфи- гурации) с высокой точностью и малой шероховатостью по- верхности. При этом чем сложнее профиль фасонной по- верхности, тем эффективнее применение станков с ЧПУ.
7.3. Обработка внутренних фасонных поверхностей растачиванием и сверлением
Фасонные поверхности на токарных станках обраба- тывают фасонными зенкерами и развертками, установлен- ными в задней бабке станка. Кроме того, при растачивании могут быть использованы фасонные резцы либо растачива- ние может производиться нормальными расточными рез- цами на станках с ЧПУ.
142
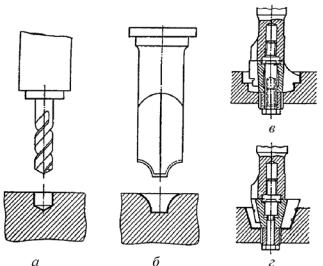
Сверление и растачивание фасонных поверхностей на сверлильных и координатно-расточных станках в большин- стве случаев осуществляется специальным фасонным инст- рументом (рис. 7.8).
Рис. 7.8. Обработка внутренних фасонных поверхностей: а, б – сверление фасонного отверстия в два перехода; в, г – растачивание специальными фасонными резцами
Фасонное отверстие предварительно сверлят спираль- ным сверлом, причем если диаметр отверстия превышает 15 мм, его сначала сверлят сверлом диаметром 10–12 мм, а затем последовательно рассверливают до требуемого диа- метра набором сверл (см. рис. 7.8, а).
Окончательно фасонную поверхность отверстия формируют путем сверления фасонным перовым сверлом
(см. рис. 7.8, б).
Растачивание фасонных поверхностей отверстий (рис. 7.8, в, г) осуществляется специальными фасонными расточными резцами.
143
7.4. Обработка фасонных поверхностей фрезерованием
Замкнутые фасонные поверхности деталей типа дис- ков и незамкнутые прямолинейно-фасонные поверхности чаще всего обрабатывают фрезерованием на станках с ЧПУ, на универсальных станках по разметке или на гидрокопиро- вальных станках с копирными устройствами. Обработка производится обычно при двух движениях, одно из которых получается от соответствующей механической подачи стан- ка, а второе – от копира; к последнему все время прижимает- ся ролик, жестко связанный с частью станка, которой сооб- щается подача; можно работать и с ручной подачей.
Основным движением является продольная подача прямоугольного стола или вращение круглого стола.
Копиры представляют собой ведущую деталь копи- ровального устройства, очертания которой определяют тра- екторию движения режущего инструмента, соответствую- щую профилю обрабатываемой поверхности.
Системы управления процессом копирования подраз- деляют на системы прямого и непрямого действия.
При прямом действии контакт копировального роли- ка (пальца) и копира обеспечивается весом груза, силой гидравлического давления или силой сжатия пружины.
При использовании системы непрямого действия ко- пировальный ролик находится в соприкосновении с копи- ром под действием незначительной силы, измеряемой де- сятками граммов. В этой системе копировальный ролик является промежуточным подвижным элементом, незначи- тельные перемещения которого, измеряемые в сотых долях миллиметра, в виде команд передаются в специальные уси- лительные устройства, которые воздействуют на исполни- тельные механизмы и перемещают режущий инструмент и обрабатываемую заготовку.
144
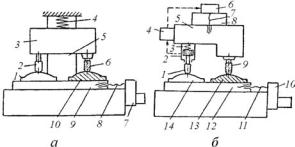
Принципиальные схемы копировальной обработки по системе прямого и непрямого действия приведены на рис. 7.9.
Рис. 7.9. Принципиальные схемы копирования: а – прямого действия; б – непрямого действия
При копировальной обработке по системе прямого действия с механическим управлением (рис. 7.9, а) стол 9 перемещается ходовым винтом 8 от редуктора 7. На столе 9 установлены копир 1 и заготовка 10. При движении палец 2 совместно с бабкой 3 под действием копира 1 сжимает пружину 4 и перемещается в вертикальном направлении по стойке 5. Фреза 6, имеющая форму и размеры пальца 2, при перемещении совместно с бабкой обрабатывает заго- товку, придавая ей форму копира. Работа пружины 4, сила которой больше, чем вертикальная слагающая от силы ре- зания на фрезе, обеспечивает постоянный контакт между пальцем и копиром.
При копировальной обработке непрямого действия с гидравлическим, пневматическим или электронным управ- лением (см. рис. 7.9, б) стол 12 с копиром 14 и заготовкой 13 перемещается от редуктора 10 через ходовой винт 11. При этом палец 1 под действием копира 14 перемещается в кор- пусе 2, соединенном с бабкой 5. Пружина 3 обеспечивает постоянный контакт между пальцем и копиром. Незначи- тельное перемещение пальца можно увеличить, используя электронные, гидравлические, пневматические или другие
145
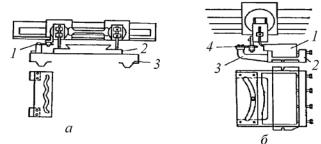
устройства. Это усилие происходит в аппарате 4, который затем сообщает команду двигателю 6; последний через ре- дуктор и ходовой винт 7 перемещает по стойке 8 бабку 5. Соответственно фреза 9 обрабатывает заготовку по профи- лю копира.
Объемное фрезерование по копиру или по специаль- но изготовленной модели производится на специальных копировально-фрезерных станках. Однако наибольший эф- фект по точности, шероховатости поверхности и экономич- ности при объемном фрезеровании достигается при работе на станках с ЧПУ.
7.5. Обработка фасонных поверхностей строганием
Строгание фасонных поверхностей обычно произво- дится по копиру (рис. 7.10).
Строгание стружечных канавок (см. рис. 7.10, а) на направляющих поверхностях детали 2 производится при помощи копира 1, установленного на столе 3 продольно- строгального станка.
Рис. 7.10. Строгание фасонных поверхностей по копиру: а – стружечных канавок; б – вогнутой поверхности
Строгание вогнутой поверхности (см. рис. 7.10, б) на детали 1 осуществляется при помощи копира 4, закреплен- ного на кронштейне 3 приспособления 2, установленного на столе станка.
146
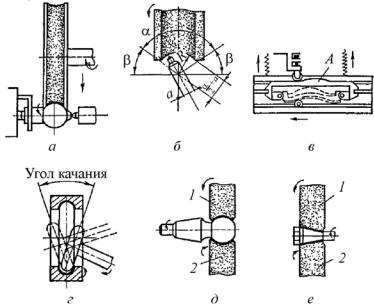
7.6. Обработка фасонных поверхностей шлифованием
Шлифование фасонных поверхностей производится фасонными шлифовальными кругами (рис. 7.11, а, б), а также при помощи копиров (рис. 7.11, в, г), по которым перемеща- ются обрабатываемые заготовки или шлифовальный круг.
Рис. 7.11. Схемы шлифования фасонных поверхностей: а – фасонным кругом с поперечной подачей; б – профили- рование шлифовального круга по радиусу; в – вогнутой по- верхности по копиру; г – беговой дорожки шарикоподшип- ника; д и е – на бесцентрово-шлифовальных станках
При обработке на бесцентрово-шлифовальных стан- ках (рис. 7.11, д, е) фасонная поверхность обрабатывается между шлифовальным 1 и ведущим 2 кругами.
147
8. МЕТОДЫ ОБРАБОТКИ КРЕПЕЖНЫХ РЕЗЬБ
Резьбовые поверхности по своему назначению под- разделяются на крепежные и ходовые.
Ходовые резьбы прямоугольного, трапецеидального и полукруглого профиля применяют в ходовых винтах, в станочных, сборочных и контрольно-измерительных при- способлениях. Они служат для преобразования вращатель- ного движения в поступательное движение.
Крепежные резьбы служат для соединения и фикса- ции деталей в разборных соединениях. Крепежные резьбы подразделяются на цилиндрические и конические. К ци- линдрическим крепежным резьбам относятся: метрические (нормальные, тугие, плотные), дюймовые, трубные, трапе- цеидальные, упорные (пилообразные) и специальные резь- бы (часовые, круглые, артиллерийские).
Основным видом крепежной цилиндрической резьбы, применяемым в России, является метрическая резьба тре- угольного профиля с углом профиля 60°. Дюймовая резьба треугольного профиля с углом профиля 55° используется при изготовлении запчастей и ремонте зарубежного обору- дования. Применение дюймовых резьб при проектировании нового оборудования ограниченно.
Трубная резьба представляет собой измельченную по шагу дюймовую резьбу с закругленными впадинами. Тра- пецеидальную резьбу применяют в основном в резьбовых соединениях, передающих движение. Резьбу с трапецеи- дальным и прямоугольным профилем в качестве чисто кре- пежной используют крайне редко, только в исключитель- ных случаях.
148
Упорную резьбу применяют в резьбовых соединениях, испытывающих большое одностороннее давление (в винто- вых прессах, специальных нажимных винтах и т.п.), круглую резьбу – в резьбовых соединениях с повышенными динами- ческими нагрузками или в условиях, загрязняющих резьбу.
Часовую резьбу применяют в точном приборострое- нии для резьбовых соединений диаметром менее 1 мм.
Артиллерийские резьбы выбирают для крепления ко- мандных деталей (артиллерийского ствола, казенника и т.п.), работающих в условиях периодических нагрузок пикового характера.
Конические резьбы, как правило, применяют в труб- ных соединениях, если необходимо обеспечить герметич- ность соединения без специальных уплотняющих материа- лов (пряжи с суриком, льняных нитей и т.п.). Наиболее распространенным видом является трубная коническая резьба, профиль которой соответствует профилю трубной цилиндрической резьбы. В ряде изделий, например в на- сосно-компрессорных и бурильных трубах для нефтедобы- чи, используется резьба специального профиля.
На машиностроительных заводах в зависимости от размеров и точности среднего диаметра резьбы, а также объема производства изготовление крепежных резьб про- изводят на токарных, токарно-револьверных, сверлиль- ных, резьбофрезерных, резьбошлифовальных и резьбона- катных станках. Наружные резьбы нарезают резьбонарез- ными резцами, гребенками, плашками, фрезами, резьбо- выми головками, профилированными шлифовальными кругами, резьбонакатными роликами и плашками. Внут- ренние резьбы нарезают метчиками, резцами, фрезами.
149
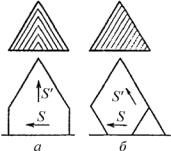
8.1. Нарезание резьб резцами и гребенками
Треугольную резьбу часто нарезают на токарно- винторезном станке или на станке с ЧПУ резьбовыми рез- цами, то есть резцами, заточенными под углом в плане 60° для метрической резьбы и 55° – для дюймовой резьбы. Получение профиля резьбы обеспечивается соответст- вующим профилем резьбового резца, который должен быть заточен достаточно точно, и правильной установки резца относительно заготовки: резец должен быть распо- ложен строго перпендикулярно оси шпинделя станка, так как в противном случае резьба получится косой; кроме того, передняя часть резца должна находиться на высоте центров станка. При другом расположении резьба будет нарезана с неправильным углом.
Нарезание резьбы резцами является малопроизводи- тельным методом обработки, так как формирование полно- го профиля производится за несколько проходов. При наре- зании резьб с крупным шагом применяют две схемы резания:
генераторную и профильную
(рис. 8.1).
Генераторную схему ре- зания применяют при предва- рительном нарезании резьб с крупным шагом (более 3 мм), профильную схему – для чис-
Рис. 8.1. Схема нарезания |
тового нарезания резьбы. |
|
резьбы: а – профильная; |
||
Высокие требования, |
||
б – генераторная |
||
предъявляемые к заточке рез- |
||
|
цов и сохранению правильного профиля, привели к исполь- зованию в производстве не только нормальных резьбовых резцов, но и фасонных резьбовых резцов (рис. 8.2).
150