
книги / Основы технологии машиностроения. Методы обработки заготовок и технологические процессы изготовления типовых деталей машин
.pdf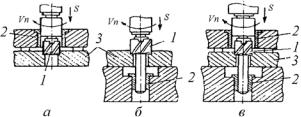
линдрической направляющей (см. рис. 4.5, а). Нижнее на- правление осуществляется втулкой 2, расположенной под деталью 3 (рис. 4.5, б). Двойное направление зенкера ре- комендуется применять при обработке отверстий диамет- ром свыше 25 мм (см. рис. 4.5, в).
Рис. 4.5. Направление зенкера в кондукторных втулках: а – верхнее; б – нижнее; в – двойное
Для того чтобы исключить погрешность оси отвер- стия, связанную с биением оси шпинделя станка относи- тельно оси направляющих втулок, зенкер со шпинделем станка обычно соединяют посредством шарнира.
Припуск под зенкерование равен примерно 0,1 диа- метра отверстия.
Зенкерование отверстия после литья или штамповки обеспечивает 13-й квалитет точности, а после сверления или чернового растачивания – 11–12-й квалитет, шерохо- ватость поверхности Rz = 10…25 мкм.
4.1.3. Развертывание отверстий
Развертывание – это основной способ обработки от- верстия 8–9-го квалитета точности (при обработке двумя развертками достигают 5–7-го квалитета точности) с шеро- ховатостью поверхности Ra = 0,15…2,5 мкм в материале твердостью HRC ≤ 40.
Инструмент – развертка – отличается от зенкера большим числом зубьев и меньшими углами в плане.
81
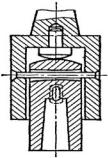
Развертки делятся на ручные и машинные и изготов- ляются цельными и раздвижными. Ручные развертки име- ют длинные зубья и длинную коническую часть, называе- мую заборной. Машинные цельные развертки применяются для отверстий диаметром до 30 мм.
Для отверстий диаметром более 30 мм в целях эко- номии режущего инструментального материала применя- ются насадные развертки. Развертки раздвижные применя- ются для диаметров от 25 до 100 мм. Большое распростра- нение имеют развертки со вставными ножами, применяе- мые для диаметров от 35 до 150 мм.
Необходимым условием достижения высокой точно- сти обработки является равномерность снимаемого при- пуска и строгое совпадение оси развертки с осью обраба- тываемого отверстия. Развертка во время работы должна свободно устанавливаться по отверстию или иметь точное направление.
В зависимости от требуемой точности развертывание производится одной или двумя развертками.
При работе чистовыми развертками на токарных и револьверных станках применяются качающиеся оправки (рис. 4.6), которые компенсируют несовпадение оси отвер-
стия и направления развертки. Развертка направляется кондук-
торными втулками с нижним, верхним или двойным направлением.
Для обработки отверстий диамет- ром от 25 до 500 мм могут быть исполь- зованы самоцентрирующиеся развертки, называемые «плавающими» развертками (рис. 4.7), которые предназначены для
Рис. 4.6. Качаю- |
удаления очень тонкого слоя стружки. |
|
щаяся оправка |
||
Ввиду того, что эти развертки на- |
||
для чистовых |
||
правляются самим отверстием, они не мо- |
||
разверток |
||
82 |
|
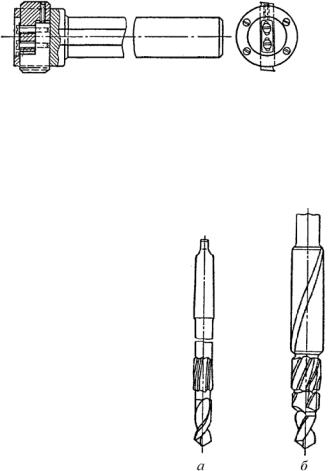
Рис. 4.7. Самоцентрирующаяся (плавающая) развертка
гут выправить кривизну и положение оси, но дают чистую поверхность и точный диаметр отверстия. Износ плавающих пластин компенсируется их регулировкой.
Вкрупносерийном и массовом производстве доста- точно часто применяют комбинированные инструменты. Такими инструментами явля- ются сверло – зенкер, сверло – развертка, сверло – зенкер – развертка (рис. 4.8).
Машинное развертыва- ние можно производить на то- карных, револьверных, свер- лильных и фрезерных станках.
Вавтомобилестроении
итракторостроении широко ис-
пользуют специальные много- шпиндельные головки для од- новременной обработки боль- шого количества отверстий.
Отверстия 7–8-го квали- тета точности обрабатыва- ют одной разверткой, а 5–6-го квалитета точности – двумя развертками.
В качестве СОЖ при развертывании обычно исполь- зуют масло индустриальное И-12А.
83
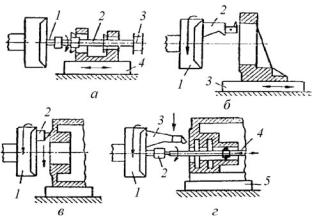
4.1.4. Растачивание отверстий
Растачивание применяется для обработки отверстий, предварительно полученных сверлением или зенкеровани- ем. Допускается растачивание отверстий, которые были изготовлены методом литья, ковки или прошивки.
Растачивание осуществляется на токарных, расточ- ных, агрегатных, координатно-расточных и специальных станках. Растачивание производится при вращении детали (токарные станки), при вращении расточной борштанги (горизонтальные, вертикальные, координатные, агрегат- ные многошпиндельные станки). Для обработки деталей на агрегатных станках используются многолезвийные, комбинированные и сборные инструменты, заранее уста- новленные на требуемый размер. Отверстия диаметром 50–200 мм и длиной 75–200 мм обрабатываются на верти- кальных станках, отверстия, имеющие протяженность больше 200 мм, и отверстия меньших диаметров – на го- ризонтальных станках.
Горизонтально-расточные станки служат для сверле- ния, зенкерования и растачивания отверстий (рис. 4.9).
Рис. 4.9. Схемы основных видов работ, выполняемых на горизонтально-расточном станке
84
На рис. 4.9, а показано растачивание двух концен- тричных отверстий резцами, закрепленными на борштанге 2, которую приводит во вращение шпиндель 1 и поддерживает люнет 3 задней стойки. При обработке заготовки стол 4 пе- ремещается параллельно оси шпинделя (продольная подача). Этот способ применяется в случае, когда расположенные соосно растачиваемые отверстия имеют значительную длину и возможен прогиб борштанги 2.
На рис. 4.9, б показано растачивание отверстия боль- шого диаметра с помощью резца, закрепленного в резце- держателе 2, который укреплен на планшайбе 1. Продоль- ная подача заготовки осуществляется движением стола 3, а радиальная подача резца – радиальным перемещением резцедержателя на планшайбе. Этим способом можно рас- тачивать отверстия большого диаметра, но сравнительно малой длины.
На рис. 4.9, в показана обработка «летучим» суппор- том торца заготовки после растачивания отверстия. В дан- ном случае заготовка неподвижна и стол не перемещается. Планшайба 1 вращает резцедержатель 2 с закрепленным резцом, который перемещается радиально, обрабатывая тор- цовую поверхность заготовки. Эта операция часто встреча- ется при обработке больших несимметричных поверхностей.
На рис. 4.9, г показан пример совместной работы шпинделя 2 и планшайбы 1. Одновременно растачивается отверстие резцом, закрепленным на борштанге 4, и обраба- тывается торец заготовки резцом, закрепленным в резце- держателе 3. Заготовка вместе со столом 5 неподвижна.
На рис. 4.10 приведены две основные схемы растачи- вания на горизонтально-расточном станке при помощи борштанги.
Обрабатываемая деталь 3 устанавливается на столе станка 1. Осевая подача резца при работе по первой схеме осуществляется путем перемещения шпинделя (см. рис. 4.10, а);
85
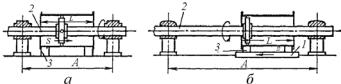
Рис. 4.10. Схемы растачивания на горизонтально-расточном станке: 1 – стол станка; 2 – борштанга; 3 – опоры (подшипники)
расстояние между подшипниками А может лишь незначи- тельно превышать длину растачиваемого отверстия L. Осевая подача при растачивании по второй схеме может осуществ- ляться также приведением в движение стола 1 (см. рис. 4.10, б), на котором расположена обрабатываемая деталь 3. В этом случае необходимо, чтобы выполнялось условие А > 2L.
При таком способе растачивания бó льшая точность может быть достигнута при отсутствии прогиба борштан- ги 2 (скалки, несущей инструмент); прогиб возникает при большом расстоянии между подшипниками, большом сече- нии стружки и недостаточной жесткости борштанги.
Работа на горизонтально-расточных станках в серий- ном производстве ведется обычно по кондукторам и шаб- лонам. В единичном производстве изготовление кондукто- ров не окупается, поэтому отверстия растачивают по раз- метке или методом координат. Разметка в ряде случаев не обеспечивает требуемой в современном машинострое- нии точности расстояний между осями, когда допуски вы- ражаются сотыми долями миллиметра. Метод координат дает возможность достичь такой точности. Этот метод со- стоит в том, что положение осей отверстий определяется перемещением детали (реже – инструмента) по осям коор- динат на расстояния, измеряемые штангенциркулем, инди- катором, мерными плитками и т.п.
Метод координатного растачивания, а также метод растачивания по разметке имеют низкую производитель-
86
ность и требуют высокой квалификации рабочего, в то вре- мя как при работе по кондуктору можно использовать труд рабочих менее высокой квалификации и достичь при этом более высокой производительности. Отверстия растачива- ют пластинчатыми резцами, расточными блоками и голов- ками. Расточной блок состоит из корпуса и вставных рез- цов, установленных на требуемый размер. Блок крепится к борштанге, имеющей переднее направление. В ряде слу- чаев борштанга шарнирно соединяется со шпинделем и базируется на двух опорах.
При координатном растачивании на координатно- расточных станках положение осей растачиваемых отвер- стий задается двумя размерами (координатами), которые от- считываются от базисных установочных плоскостей детали.
Установка оси шпинделя расточного станка осуще- ствляется с помощью градуированных линеек и нониусов, имеющихся на станке, или с помощью специальных вкла- дышей, регулируемых по размеру соответствующих ко- ординат.
Перед растачиванием проверяют правильность уста- новки детали на столе станка индикатором, закрепленным на шпинделе станка, затем устанавливают шпиндель в ну- левое положение с помощью ловителя, вставляемого в ко- нец шпинделя станка, с проверкой щупом. После этого можно начать растачивание, предварительно совместив ось шпинделя и ось растачиваемого отверстия.
Координатное растачивание повышает точность меж- центровых расстояний и их соосность, упрощает обработку и увеличивает производительность.
Расточка отверстий с точно координированными осями в корпусных деталях производится на координатно- расточных станках, в том числе с программным управлени- ем, оснащенных оптическими системами отсчета по шкале с точностью ±0,002 мм.
87
Растачивание отверстий в стальных деталях произво- дится в таких режимах: скорость резания 100–250 м/мин, продольная подача 0,05–0,3 мм/об, глубина резания 0,05– 0,3 мм, а в деталях из цветных металлов и сплавов ско- рость резания 500–1000 м/мин, продольная подача – от 0,05 до 0,3 мм/об, глубина резания 0,05–0,4 мм.
4.1.5. Тонкое растачивание отверстий
Тонкое растачивание производится на прецизионных расточных одно- или многошпиндельных вертикальных и/или горизонтальных станках моделей 2А710, 2705, 2706, 2714, 2А715, и др.
Эти станки имеют повышенную жесткость и вибро- устойчивость; на них также можно сверлить, зенкеровать, развертывать, подрезать торцы, нарезать резьбу и протачи- вать канавки.
Режимы тонкого растачивания отверстий в стальных деталях: скорость резания 120–250 м/мин, продольная пода- ча 0,01–0,08 мм/об, глубина резания 0,05–0,10 мм; в деталях из цветных сплавов скорость резания 500–1500 м/мин, про- дольная подача 0,01–0,10 мм/об, глубина резания 0,05–0,1 мм.
Тонкое растачивание обеспечивает точность от- верстий 6–7-го квалитета при шероховатости поверхно-
сти Ra = 0,16…0,25 мкм.
Погрешность формы (овальность, конусность) со-
ставляет 0,003–0,004 мм.
4.1.6. Протягивание отверстий
Протягивание – это процесс обработки цилиндриче- ских (диаметром от 10 до 300 мм), шлицевых, прямоуголь- ных и квадратных отверстий с точностью 5–7-го квалитета и шероховатостью поверхности Ra = 0,08…0,16 мкм.
Перед протягиванием отверстие обрабатывают свер- лением, зенкерованием или растачиванием. Длина протяги-
88
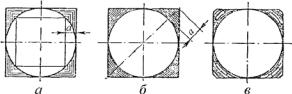
вания отверстия обычно не превышает трехкратной вели- чины его диаметра.
Протягивание – процесс обработки поверхности от- верстия специальным инструментом – протяжкой, зубья которой за один ход снимают весь припуск. На протяжке кроме основных режущих зубьев имеются калибрующие, придающие обрабатываемой поверхности требуемые точ- ность и шероховатость.
Различают три основных схемы протягивания (рис. 4.11).
Рис. 4.11. Схемы протягивания: а – продольная; б – генераторная; в – прогрессивная
По профильной схеме (см. рис. 4.11, а) процесс осу- ществляется протяжками, все зубья которых имеют про- филь, подобный профилю обрабатываемой поверхности, различаясь только размерами, причем каждый зуб последо- вательно снимает слой металла по форме профиля обраба- тываемой поверхности.
По генераторной схеме (см. рис. 4.11, б) процесс осуществляется протяжками, зубья которых имеют пере- менный профиль с дугообразной или прямолинейной фор- мой главной режущей кромки, постепенно переходящей к заданному профилю обрабатываемой поверхности.
По прогрессивной схеме (см. рис. 4.11, в) процесс осуществляется протяжками, у которых все режущие зубья разбиты на группы, обычно по два зуба, причем каждый зуб группы формирует только определенный участок про- филя обрабатываемой поверхности. При этом режущие кромки зубьев перекрывают друг друга.
89
Первая схема применима при протягивании поверхно- стей со снятием тонкого слоя металла по всей ширине обра- ботки. Обработка по корке (литейной, штамповочной и т.п.) не применяется.
Генераторная схема упрощает изготовление протя- жек, так как в этом случае нет необходимости в заточке зу- ба по всему фасонному затылку. Протяжки, использующие генераторную схему, также как протяжки, работающие по профильной схеме, могут формировать поверхность отвер- стия только после предварительной лезвийной обработки (сверления, зенкерования, растачивания и т.п.).
При прогрессивной схеме резания режущие зубья по периметру разделены на отдельные секции. Зубья протяжки срезают металл отдельными участками контура, но толщи- ной в 3–5 раз больше, чем при работе по профильной схе- ме. Прогрессивная схема может применяться для протяги- вания необработанных предварительно лезвийным инстру- ментом поверхностей.
По профилю протяжки подразделяют на плоские, круглые, фасонные. Различают также сборные протяжки со вставными зубьями и наборные, оснащенные пластин- ками из твердого сплава.
Разность высоты двух смежных зубьев определяет толщину слоя металла, снимаемую каждым зубом про- тяжки, или величину подъема на зуб, которая зависит от свойств обрабатываемого материала, материала про- тяжки, жесткости заготовки, формы протягиваемой по- верхности и т.д. Для разделения широкой стружки на по- верхности режущей части зубьев прорезают стружкораз- делительные канавки (от 6 до 12 канавок). Число калиб- рующих зубьев составляет от 3 до 8.
Чем выше требования к точности обработки, тем больше калибрующих зубьев должна иметь протяжка.
90