
книги / Основы технологии машиностроения. Методы обработки заготовок и технологические процессы изготовления типовых деталей машин
.pdf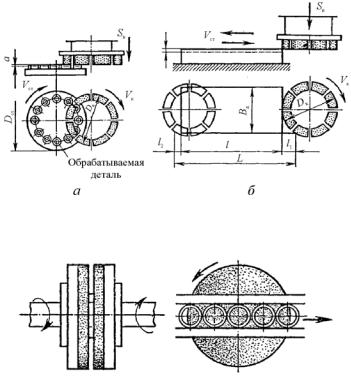
Рис. 5.13. Схемы плоского шлифования торцом круга:
а– на станках с круглым столом; б – на станках
спрямоугольным столом
Рис. 5.14. Схема плоского шлифования на двусторонних станках
При многопроходном шлифовании стол станка полу- чает быстрое вращение (15–20 м/мин); вертикальную пода- чу шлифовального круга (на врезание) осуществляют пе- риодически на один или несколько оборотов стола. При глубинном шлифовании стол станка медленно вращается (от 0,5 до 3,0 м/мин), и за один оборот стола снимают весь припуск.
Независимо от того, производится шлифование тор- цом или периферией круга, различают обдирочное, черно- вое, чистовое и тонкое шлифование.
121
5.4.3. Обдирочное шлифование
Обдирочное шлифование плоскостей может быть пред- варительной или окончательной операцией, если не требуется высокой точности и чистоты обработки. Припуск для обди- рочного шлифования должен быть меньше, чем для фрезе- рования и строгания.
Обдирочное шлифование плоскостей применяется в том случае, когда наличие твердой корки (литейной или штамповочной) на поверхности детали или высокая твер- дость материала затрудняют либо делают невозможным фрезерование или строгание.
5.4.4. Черновое шлифование
Черновое шлифование осуществляют при скорости вращения круга порядка 30 м/с, продольной подаче от 10 до 30 м/мин и глубине шлифования 0,02–0,04 мм. В каче- стве СОЖ используют эмульсию или 4%-й водный содо- вый раствор.
При черновом шлифовании достигается точность об- работки 8–9-го квалитета и шероховатость поверхности Ra = 1,25…2,5 мкм. Припуск составляет порядка 0,7 мм.
5.4.5. Чистовое шлифование
Чистовое шлифование осуществляют при скорости вращения круга порядка 30 м/с, продольной подаче от 10 до 30 м/мин и глубине шлифования 0,01–0,02 мм. В качестве СОЖ используют эмульсию или 4%-й водный содовый рас- твор. При этом достигается точность обработки 6–7-го ква- литетов и шероховатость поверхности Ra = 0,32…1,25 мкм.
Припуск составляет порядка 0,3 мм.
122
5.4.6. Тонкое (отделочное) шлифование
Тонкое шлифование осуществляют при скорости вра- щения круга порядка 30–35 м/с, продольной подаче от 8 до 12 м/мин и глубине шлифования 0,005–0,01 мм с выхажи- вающим проходом без врезания (глубина шлифования равна нулю). В качестве СОЖ используют эмульсию или 4%-й водный содовый раствор. При этом достигается точность обработки 4–5-го квалитета и шероховатость поверхности Ra = 0,08…0,32 мкм. Припуск составляет порядка 0,05 мм.
5.5. Притирка плоских поверхностей
Притирку (доводку) выполняют свободным абрази- вом или пастами с помощью плоских притиров путем при- жима с определенным усилием обрабатываемой поверхно- сти заготовки к плоской поверхности притира и перемеще- ния заготовки относительно притира, при котором снима- ется тончайший слой металла – до 0,02 мм.
Целью притирки является получение плотного или герметичного разъемного и подвижного соединения. Точ- ность притирки до 0,002 мм.
Доводка служит для получения не только требуемых форм и шероховатости поверхности, но и заданных разме- ров с допуском по 5–6-му квалитету точности.
Плоские поверхности притирают после чистового шлифования, хонингования, фрезерования, протягивания, шабрения.
Существует ручная и машинная притирка (доводка). Ручная доводка подразделяется на предварительную,
среднюю, чистовую, отделочную и зеркальную.
Предварительная ручная доводка обеспечивает точ-
ность 7–8-го квалитета и шероховатость поверхности
Ra = 0,32…1,25 мкм. Припуск от 0,015 до 0,025 мм.
123
Средняя ручная доводка обеспечивает точность 6–7-го квалитета и шероховатость поверхности Ra = 0,16…0,32 мкм.
Припуск 0,01–0,015 мм.
Чистовая ручная доводка обеспечивает точность 5–6-го квалитета и шероховатость поверхности Ra = 0,04…0,16 мкм.
Припуск 0,005–0,01 мм.
Отделочная ручная доводка обеспечивает точность 5-го квалитета и шероховатость поверхности Ra = 0,01…0,04 мкм.
Припуск 0,0025–0,005 мм.
Зеркальная ручная доводка обеспечивает точность 4-го квалитета и шероховатость поверхности Ra < 0,01 мкм. При-
пуск 0,001–0,0025мм.
При ручной доводке существенную, если не основ- ную, роль играет квалификация рабочего и культура произ- водства в целом.
Машинная притирка (доводка) плоских поверхностей осуществляется на специальных плоско-доводочных стан- ках с использованием плоских, как правило, чугунных при- тиров и специальных приспособлений.
Существуют станки для односторонней плоской до- водки и станки для одновременной доводки двух парал- лельных плоскостей заготовки, установленной между дву- мя плоскими притирами.
При односторонней доводке на рабочую поверх- ность притира наносят пасту ГОИ соответствующей зер- нистости. Затем к поверхности притира посредством спе- циального прижимного устройства заготовку или заготов- ки, установленные в кассете, прижимают к рабочей по- верхности притира. Кассете с заготовками сообщают медленное (от 2 до 5 об/мин) вращение (ось кассеты пер- пендикулярна рабочей плоскости притира и не совпадает с центром притира). Притиру сообщают рабочее движение в горизонтальной плоскости по заданной траектории (кру- говой, конхоидной, циклоидной или растровой – в виде
124
фигуры Лиссажу с большим периодом повторений траек- тории) со скоростью 15–40 м/мин. Усилие прижима заго-
товки 0,05–0,3 МПа.
Притирка на станках, движение притира которых осуществляется по круговой, конхоидной или циклоидаль- ной траектории, обеспечивает точность деталей 6–8-го ква- литета с шероховатостью поверхности Ra = 0,08…0,32 мкм. Использование станков, у которых притир совершает рабо- чее движение по растровой траектории (абразивные зерна каждый раз проходят по новой траектории, не повторяя траекторию движения предыдущего зерна), позволяет дос- тичь точности 4–5-го квалитета и шероховатости поверхно-
сти Ra = 0,04…0,16 мкм.
Припуск для предварительной машинной притирки равен 0,010–0,025 мм, а для окончательной – 0,005–0,010 мм.
5.6. Полирование плоских поверхностей
Полирование плоских поверхностей производят ана- логично полированию поверхностей вращения. Припуск под полировку не оставляют. Шероховатость поверхности достигает Ra = 0,04…0,32 мкм.
5.7. Шабрение плоских поверхностей
Шабрением называется операция по снятию (соскаб- ливанию) с поверхности заготовки очень тонких слоев ме- талла специальным режущим инструментом – шабером.
Цель шабрения – обеспечить плотное прилегание со- прягаемых поверхностей и герметичность (непроницае- мость) подвижных соединений. Для получения поверхно- сти высокого качества последовательно выполняют черно- вое, получистовое и чистовое шабрение.
Шабрением обрабатывают прямолинейные поверхно- сти, например направляющие станин прецизионных станков.
125
Шабрение как окончательный процесс обработки не- закаленных поверхностей широко применяется в станко- строении и инструментальном производстве.
Это объясняется особыми качествами полученной шабрением поверхности, которые состоят в следующем:
–в отличие от шлифованной или полученной при- тиркой абразивами поверхности шаброванная поверхность более износостойка, потому что не имеет шаржированных остатков абразивных зерен, ускоряющих процесс износа;
–шабренная поверхность лучше смачивается и доль- ше сохраняет смазывающие вещества благодаря наличию так называемой разбивки этой поверхности, что также по- вышает ее износостойкость и снижает коэффициент трения;
–шабренная поверхность позволяет использовать са- мый простой и наиболее доступный метод оценки ее каче- ства по числу пятен прилегания на единицу площади.
Шабрение можно выполнять: 1) вручную; 2) механическим способом.
Первый способ требует больших затрат времени при высокой квалификации исполнителя, но обеспечивает вы- сокую точность и качество обработанной поверхности.
Второй способ осуществляется с помощью специаль- ных станков, на которых шабер получает возвратно-посту- пательное движение; при этом требуется меньше времени, однако качество обработки оставляет желать лучшего.
Ручным шабрением за один проход шабера снимают слой металла толщиной от 0,005 до 0,07 мм и достигают отклонения от плоскостности 0,003–0,01 мм. Количество пятен на один квадратный дюйм шабреной поверхности
составляет более 30. Припуск под шабрение составляет в зависимости от размера плоскости 0,1–0,5 мм.
126
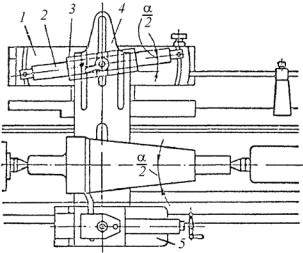
6. МЕТОДЫ ОБРАБОТКИ КОНУСНЫХ ПОВЕРХНОСТЕЙ
6.1. Обработка наружных конусных поверхностей
Обработка наружных конусных поверхностей с обра- зующей достаточно большой протяженности производится точением на станках токарной группы тремя методами:
1)точением с помощью конусных линеек;
2)точением методом настройки кинематических цепей;
3)точением при смещенном заднем центре. Обработка конуса по конусной линейке (рис. 6.1) осу-
ществляется следующим образом.
Рис. 6.1. Схема обработки конуса на токарном станке с помощью конусной линейки
На кронштейне 1 установлена линейка 2, которая может быть повернута на заданный угол (равный половине угла α при вершине обтачиваемого конуса). По конусной линейке 2 перемещается ползун 3, связанный с поперечной
127
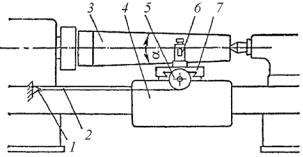
кареткой 5 жесткой тягой 4. Поперечная каретка освобож- дена от винта поперечного суппорта. При движении про- дольной каретки 5 по направляющим станины станка пол- зун 3, перемещаясь по линейке 2, через тягу 4 заставляет поперечную каретку вместе с резцом следовать по направ- лению конусной линейки 2 под заданным углом α/2.
Отсутствие конусных линеек на токарных станках не препятствует обработке конусов. Использование настроен- ных кинематических цепей позволяет посредством неслож- ного приспособления обрабатывать конусы (рис. 6.2).
Рис. 6.2. Схема обработки конуса методом настроенной кинематической цепи
Для этого достаточно установить на винт суппорта 7 поперечной подачи вместо маховика барабанчик 5 и, при- крепив к его поверхности гибкий металлический трос 2, навить один конец троса на поверхность барабанчика 5; другой конец троса 2 необходимо закрепить в неподвиж- ном упоре 1.
При продольном перемещении слева направо суппор- та 4 продольной подачи винта (от ходового винта) барабан- чик 5 благодаря натяжению троса 2 начнет поворачиваться и вращать ходовой винт поперечной подачи. Резец 6 будет обрабатывать на заготовке 3 наружный конус с заданным
128
углом (каждому углу конуса будет соответствовать бара- банчик строго определенного диаметра). Погрешность вы- полнения угла конуса будет зависеть от соотношения диа- метров барабанчика 5 и троса 2. Чем больше эта величина, тем точнее выполнение угла конуса.
Для обеспечения принудительного движения резца 6 при перемещении суппорта 4 в обоих направлениях (слева направо и справа налево) необходимо к наружной цилинд- рической поверхности барабанчика 5 прикрепить два ме- таллических троса 2, свободные концы которых присоеди- нить к станине станка.
Конец одного троса 2 необходимо присоединить к ста- нине станка слева от суппорта 4 (как показано на рис. 6.2), а конец другого троса – справа от суппорта 4 (на рис. 6.2 не показано).
Конусы с малым углом при вершине (до 10–12°) на за- готовках, имеющих центровые отверстия и установленных в центрах (передний и задний) станка, можно обрабатывать точением при смещении заднего центра станка в горизон- тальном направлении.
Обработка конусов с большим углом при вершине (более 12°) и относительно малой протяженностью обра- зующей (до 250 мм) производится точением на токарных станках за счет поворота верхних салазок поперечного суп- порта с резцедержателем и закрепленным в нем резцом на заданный угол, равный половине угла при вершине об- рабатываемого конуса.
Продольная подача в направлении, параллельном образующей конуса, обеспечивается перемещением верх- них салазок.
Обработку конусов с протяженностью менее 50 мм можно обеспечить применением широких резцов с перед-
129
ним углом, в плане равном половине угла при вершине об- тачиваемого конуса. При этом резцу сообщают перемеще- ние на врезание поперечным суппортом станка.
Кроме того, обработку наружных конусных поверх- ностей с любыми углами при вершине обтачиваемого кону- са любой протяженности можно производить на токарных станках с ЧПУ. Обработку наружных конусных поверхно- стей, к которым предъявляются повышенные требования по точности и шероховатости поверхности, можно произ- водить на кругло-шлифовальных станках.
Шлифование длинных конусов с малым углом при вершине (до 12°) производят в центрах методом продоль- ной подачи периферий или торцом шлифовального круга при повороте стола станка на заданный угол, равный поло- вине угла при вершине шлифуемого конуса.
Шлифование коротких конусов (протяженность кону- са менее высоты шлифовального круга) производят в цен- трах периферией шлифовального круга методом врезания при повороте шпиндельной бабки (оси шлифовального круга) на угол, равный половине угла при вершине шли- фуемого конуса.
Для обработки конусной поверхности на станках, ось шпинделя шлифовального круга которых параллельна оси центров, рабочую поверхность шлифовального круга необ- ходимо править под углом, равным половине угла при вершине шлифуемого конуса, и шлифование производить методом врезания.
При особо высоких требованиях к чистоте обработки конусной поверхности ее можно подвергнуть суперфинишу или полированию.
130