
книги / Основы технологии машиностроения. Методы обработки заготовок и технологические процессы изготовления типовых деталей машин
.pdfТехнологический процесс, построенный по принципу дифференциации операций, состоит из большого числа простых операций, выполняемых на универсальных, специ- альных или специализированных станках относительно простой конструкции и высокой надежности.
Достоинства дифференциации операций в первую очередь связаны с возможностью отделения сложной и точ- ной чистовой обработки, требующей высокой квалификации рабочих и высокоточных станков, от предварительной не- точной обработки, которая может быть осуществлена про- стейшими и высокопроизводительными способами на про- стых и дешевых станках рабочими средней квалификации.
Степень дифференциации зависит от типа производ- ства. В массовом и крупносерийном производстве может быть экономически целесообразным построение техноло- гического процесса из большого числа простейших опера- ций, выполняемых в едином ритме на простых станках, связанных конвейером. В условиях среднесерийного про- изводства принцип дифференциации используется на пере- менно-поточных линиях групповой обработки.
1.3.4. Структура технологических операций
Производительность технологических операций в зна- чительной степени зависит от их структуры, определяемой количеством заготовок, одновременно устанавливаемых
вприспособлении или на станке (одно- или многоместная обработка), количеством инструментов, используемых при выполнении операции (одно- или многоинструментальная обработка), последовательностью работы инструментов при выполнении операции.
Последовательное вступление инструментов в работу или последовательное расположение нескольких заготовок
вприспособлении по направлению движения подачи харак- теризует структуру операции с последовательной обработкой.
31
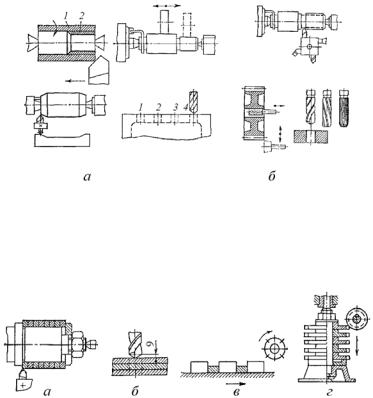
Схемы одноместной последовательной обработки представлены на рис. 1.1.
Рис. 1.1. Схемы одноместной последовательной обработки: а – одноинструментальная обработка; б – многоинстру- ментальная обработка
Схемы многоместной последовательной одноинстру- ментальной обработки представлены на рис. 1.2.
Рис. 1.2. Схемы многоместной одноинст- рументальной обработки
При параллельном расположении обрабатываемых за- готовок в приспособлении (то есть заготовки расположены перпендикулярно к направлению движения подачи) и при одновременной обработке нескольких поверхностей одной или нескольких заготовок формируется структура операции с параллельной обработкой. Схемы одноместной параллель- ной обработки приведены на рис. 1.3.
32
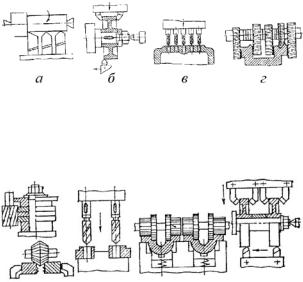
Рис. 1.3. Схемы одноместной параллельной многоинструментальной обработки
Схемы многоместной параллельной обработки пред- ставлены на рис. 1.4.
Рис. 1.4. Схемы многоместной многоинструментальной обработки
При многоместной обработке заготовок, располо- женных в приспособлении рядами вдоль и поперек движе- ния подачи, операция характеризуется как операция с па- раллельно-последовательной обработкой.
Схемы многоместной параллельно-последовательной обработки представлены на рис. 1.5.
Многоместные схемы обработки дают возможность совмещения как основного, так и вспомогательного вре- мени, за счет чего обеспечивается повышение производи- тельности.
Многоместная параллельно-последовательная обра- ботка с раздельной установкой заготовок не только дает возможность совмещать время установки заготовок с ос- новным временем, сокращая общие затраты вспомогатель- ного времени, но и позволяет осуществить частичное со- вмещение основного времени переходов.
33
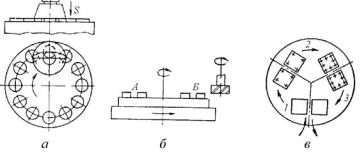
Рис. 1.5. Схемы многоместной параллельно-последовательной обработки: а – с одновременной; б, в – с раздельной установкой заготовок: а – плоское шлифование заготовок; б – фрезерование на поворотном столе со сменой группы заготовок; в – обработка на вертикальном полуавтомате (1 – позиция загрузки;
2 и 3 – позиции обработки заготовок)
Наибольшую производительность обработки обеспе- чивает многоместная параллельно-последовательная обра- ботка с непрерывной установкой и сменой обрабатываемых заготовок на станке.
1.4. Исходные данные для проектирования технологических процессов механической обработки деталей машин
При проектировании технологического процесса ме-
ханической обработки исходными данными являются размер и срок выполнения производственной программы, состав- ленной на основании общей производственной программы завода, рабочие чертежи и технические условия изготовле- ния и приемки детали (изделия).
При проектировании технологических процессов не- обходимо учитывать общую производственную обстановку (состав и степень загрузки оборудования, обеспеченность предприятия инструментами, приспособлениями, квалифи- цированной рабочей силой и т.п.), а также располагать нор-
34
мативными, справочными и руководящими материалами и каталогами оборудования и технологической оснастки.
Размер и содержание производственной программы
(программного задания) завода и программы по выпуску конкретных деталей для отдельных цехов и участков зависит от установленного объема выпуска изделий, то есть от коли- чества изделий определенных наименований, типоразмера и исполнения, изготавливаемых или ремонтируемых пред- приятием или его подразделением в течение планируемого интервала времени.
Чертежи должны включать: рабочие чертежи дета- лей выпускаемых изделий; сборочные чертежи узлов и от- дельных механизмов (агрегатов); чертежи общих видов из- делий. К чертежам прилагаются: спецификации деталей по каждому изделию, описание конструкций и, если возмож- но, рисунки или фотографии изделий.
На рабочих чертежах, необходимых для проекти- рования технологических маршрутов обработки деталей на металлорежущих станках, должны быть указаны: мате- риал детали, вес (масса), марка материала; обозначения шероховатости после обработки; допуски на точность об- работки; вид термической обработки.
На сборочных чертежах и общих видах должны быть указаны: конструктивные зазоры; допуски на размеры, оп- ределяющие взаимное расположение деталей; особые тре- бования, касающиеся сборки соединений или монтажа все- го изделия.
В спецификациях деталей по каждому изделию должны быть указаны:
–наименования всех деталей (включая покупные);
–количество деталей на одно изделие;
–для нормализованных деталей – обозначение стан-
дарта.
35
Описание конструкции изделий должно давать пра- вильное и полное представление об их работе, назначении и функциях отдельных частей и их взаимодействии.
Технические условия на изготовление и сдачу деталей или изделий определяют требования, предъявляемые к де- талям и к изделию в целом.
1.5. Общие правила разработки технологических процессов и основные принципы составления технологических маршрутов механической обработки заготовок
Весь комплекс работ по технологической подготовке производства регламентирован ГОСТ Р 50995.3.1–96, кото- рый действует совместно с ГОСТ Р 50995.0.1–96, ГОСТ Р 15.000–94, Р 50–54–93–88, Р 50–297–90, ГОСТ 3.1404–86, ГОСТ 3.1122–84, ГОСТ 3.1105–84, ГОСТ 3.1502–82, ГОСТ 3.1118–82, ГОСТ 3.1109–82, ГОСТ 3.1107–81, ГОСТ 3.1102–81, ГОСТ 3.1001–81.
Разработку технологического процесса выполняют
вследующей последовательности:
–анализ исходных данных;
–определение типа производства;
–определение класса детали и выбор в качестве ана- лога действующего типового или группового технологиче- ского процесса;
–выбор исходной заготовки и методов ее изготовления;
–выбор технологических баз;
–составление технологического маршрута обработки;
–разработка технологических операций;
–нормирование технологического процесса;
–определение требований техники безопасности;
36
–расчет экономической эффективности технологиче- ского процесса;
–оформление технологической документации. Прежде чем приступить к проектированию техноло-
гического процесса механической обработки, необходимо тщательно изучить сборочный чертеж изделия и (или) ра- бочий чертеж детали с соответствующими техническими условиями изготовления.
Кроме того, необходимо изучить и такие дополни- тельные условия проектирования, как наличие или отсутст- вие оборудования, на котором предполагается осуществить изготовление проектируемого изделия; возможности при- менения совершенных видов исходных заготовок, прогрес- сивного инструмента и приспособлений и т.п.
Проектирование технологических процессов пред- ставляет собой сложную многовариантную задачу, для ре- шения которой необходимо составить несколько возмож- ных конкурирующих вариантов обработки.
Окончательный выбор одного из вариантов произво- дится на основании расчетов и сопоставления достигаемых точности, трудоемкости (выражается нормой штучного или штучно-калькуляционного времени), технологической се- бестоимости и срока окупаемости капитальных затрат. Та- кое сопоставление производится как по важнейшим техно- логическим операциям, так и по всему технологическому процессу в целом.
По величине программного задания определяют ко- эффициент закрепления операций, тип производства, необ- ходимые такт и ритм обработки заготовок и разрабатывают рациональный технологический маршрут механической обработки.
37
Основные принципы, используемые при составлении технологического маршрута процесса механической обработки заготовки
При низкой точности исходных заготовок технологи- ческий маршрут начинается с черновой обработки поверх- ностей, имеющих наибольшие припуски. При этом в пер- вую очередь снимается припуск с тех поверхностей, на ко- торых возможны литейные раковины, трещины и другие дефекты, с целью скорейшего отсеивания возможного бра- ка или устранения обнаруженных дефектов заваркой, на- плавкой металла и т.п.
Вдальнейшем технологический маршрут строится по принципу обработки сначала более грубых и затем – более точных поверхностей.
Наиболее точные и (или) легко повреждаемые по- верхности (наружные резьбы, особо точные шлифованные
идоведенные поверхности) выполняют на заключительных этапах технологического маршрута.
Вконце технологического маршрута размещают вто- ростепенные операции (сверление мелких отверстий, наре- зание крепежных резьб, прорезка пазов, снятие фасок и за- усенцев).
При обработке заготовок, подвергающихся термиче- ской обработке, в технологическом маршруте предусмат- ривают дополнительные операции, связанные с особенно- стями термической обработки. (Например, операция мед- нения или операция снятия дополнительного припуска для удаления цементированного слоя на поверхностях, не под- лежащих закалке).
Необходимость выявления брака на первых операци-
ях в некоторых случаях заставляет изменять маршрут обра- ботки заготовки.
38
При назначении технологических баз технолог руко- водствуется принципом совмещения и постоянства баз,
то есть стремится выбрать в качестве технологических баз поверхности или сочетание поверхностей, которые одно- временно являются конструкторскими и измерительными базами, и старается не менять технологические базы в про- цессе обработки.
При вынужденной смене технологических баз и нару- шении принципа их совмещения необходимо произвести перерасчет допусков и технологических размеров заготовки.
Во всех возможных случаях в качестве черновых баз принимаются поверхности, удобные для установки и в даль- нейшем не обрабатываемые. Черновые базы связываются размерами или условиями (параллельность, перпендикуляр- ность) с обрабатываемой при первой операции поверхно- стью или совокупностью поверхностей, которые в дальней- шем используются в качестве технологических баз для по- следующих операций обработки заготовки.
Вцелях уменьшения пространственных отклонений
врасположении технологических баз, используемых при последующих операциях механической обработки, жела- тельно в процессе первой операции, выполняемой от чер- новых баз, произвести обработку всех указанных баз при одном установе заготовки.
Выбор типа станка определяется его возможностью обеспечить выполнение технических требований, предъяв- ляемых к детали в отношении точности ее размеров, формы и шероховатости поверхности. Если по характеру обработ- ки эти требования можно выполнить на различных станках, выбирают тот или иной станок для выполнения данной операции на основе следующих соображений:
– соответствие основных размеров станка габарит- ным размерам обрабатываемой заготовки;
39
–соответствие производительности станка количест- ву заготовок, подлежащих обработке в течение года;
–наиболее полное использование станка по мощно- сти и по времени;
–наименьшая затрата времени на обработку;
–наименьшая себестоимость обработки;
–наименьшая цена станка;
–реальная возможность приобретения того или дру- гого станка;
–необходимость использования имеющихся на пред- приятии станков.
При проектировании рабочего технологического процесса производится конструктивная разработка при- способления с изготовлением рабочих чертежей. Обычно это выполняется в заводских конструкторских бюро при- способлений.
Вединичном и мелкосерийном производстве исполь- зуют универсальные приспособления, которые являются принадлежностями станков (токарные патроны, тиски, дели- тельные универсальные головки, поворотные столы и т.п.).
Вкрупносерийном и массовом производстве приме- няют главным образом специальные приспособления, ко- торые сокращают вспомогательное и основное время об- работки.
Одновременно со станком и приспособлением для каждой операции выбирается необходимый режущий инст- румент и средства измерения, обеспечивающие достижение высокой производительности, требуемой шероховатости, точности обработки и контроля. При выборе инструмента
вединичном и мелкосерийном производстве предпочтение отдается нормализованным режущим и измерительным ин- струментам, выполненным по стандарту или в соответствии
40