
книги / Основы технологии машиностроения. Методы обработки заготовок и технологические процессы изготовления типовых деталей машин
.pdfботку, которая несколько снижает достигнутую точность и шероховатость поверхности. Тем не менее при изготов- лении точных зубчатых колес шевингование применяют до термической обработки с тем, чтобы свести к минимуму ошибки механической обработки.
Одним из основных преимуществ шевингования явля- ется возможность ограничиваться нарезанием зубьев на зу- бофрезерных станках (с последующим шевингованием), не прибегая к чистовому нарезанию на зубодолбежных стан- ках. Шевингование червячных шестерен осуществляют спе- циальным инструментом – шевер-червяком (рис. 9.22, в).
Шлифование зубьев зубчатых колес увеличивает точ-
ность незакаливаемых, а в особенности закаливаемых зуб- чатых колес, которые деформируются во время термиче- ской обработки. Шлифование прямых и спиральных зубьев с эвольвентным профилем наружных и внутренних зубча- тых венцов производится: методом копирования при по- мощи фасонного шлифовального круга с эвольвентным профилем рабочей поверхности; методом обкатки.
Первый метод шлифования зубьев – метод копирова- ния – реализуется на специальных зубошлифовальных стан- ках. Станки, работающие по методу копирования, произво- дят шлифование кругом, профиль которого соответствует впадине зубьев, аналогично дисковой модульной фрезе. Ра- бочая поверхность круга заправляется особым копироваль- ным механизмом (пантографом) по шаблонам при помощи трех алмазов (рис. 9.23, а). Круг шлифует две эвольвентные стороны двух соседних зубьев, переход от эвольвентной по- верхности к основанию (дну) впадины и основание (дно) впадины. При шлифовании зубьев с выкружкой основание (дно) впадины не шлифуется. Для зубчатых колес с различ- ными модулями и разным количеством зубьев необходимо иметь отдельные шаблоны для заправки шлифовального круга. Зубошлифовальные станки, работающие по методу
211
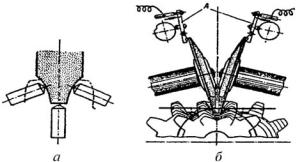
Рис. 9.23. Зубошлифование: а – заправка тремя алмаза- ми рабочего профиля шлифовального круга, работаю- щего методом копирования; б – обработка двумя та- рельчатыми шлифовальными кругами методом обкатки
копирования одним профильным кругом, применяются в массовом, крупносерийном, а иногда – и в среднесерийном производстве.
При шлифовании зубчатых колес с большим количе- ством зубьев по методу копирования имеет место значи- тельный износ шлифовального круга и потеря им формы профиля. Поскольку станки, работающие по методу копиро- вания одним профильным шлифовальным кругом, не имеют механизма компенсирующего износ круга, при последова- тельном шлифовании зубьев между первым и последним зубьями возникает значительная накопленная погрешность. Для уменьшения накопленной погрешности, вызываемой износом шлифовального круга, рекомендуется деление про- изводить не на один зуб, а на некоторое количество зубьев, выражаемое простым числом (3, 5, 7, 11, 13, 17, 19, 23 и т.д.). В этом случае изнашивание шлифовального круга не будет давать большой накопленной ошибки между соседними зубьями. Достигаемая при этом погрешность по шагу будет составлять 0,010–0,015 мм.
Станки, работающие по методу копирования (ти- па 5860, 5861), с использованием в качестве СОЖ эмуль-
212
сии, получили довольно широкое распространение благо- даря высокой производительности по сравнению со стан- ками, работающими по методу обкатки. На станках, рабо- тающих по методу копирования, можно шлифовать пря- мые и спиральные зубья цилиндрических и конических зубчатых колес с наружным и внутренним зацеплением. Однако точность обработки на станках, работающих про- фильным шлифовальным кругом, не превышает 7–8-й степени точности, а шероховатость поверхности составля- ет Ra = 0,6…1,3 мкм. Обработка производится при скоро- сти шлифования Vкр = 30…32 м/с и при продольной пода-
че Sпр = 5…15 м/мин.
Второй метод шлифования зубьев – метод обкат- ки – менее производителен, но дает большую точность (до 0,0025 мм); шлифование производится одним или двумя шлифовальными кругами.
Распространен способ шлифования зубьев методом обкатки с двумя тарельчатыми шлифовальными кругами, расположенными один по отношению к другому под углом 30 и 40° (15 и 20° к вертикальной плоскости) и образующих как бы профиль расчетного зуба (профиль исходной режу- щей рейки), по которому происходит обкатка зубчатого колеса (рис. 9.23, б). В процессе работы шлифуемое зубча- тое колесо перемещается в направлении, перпендикуляр- ном своей оси, одновременно поворачиваясь вокруг этой оси. Помимо этого шлифуемое зубчатое колесо имеет воз- вратно-поступательное движение вдоль своей оси, что обеспечивает шлифование профиля зуба по всей его длине.
Шлифование зубьев высокоточных зубчатых колес производится на отечественных станках типа 5851, 5853 и на импортных станках фирмы МААГ (Швейцария), рабо- тающих двумя тарельчатыми шлифовальными кругами. Эти станки работают без применения СОЖ и имеют специальное устройство А, компенсирующее износ шлифовальных кругов
213
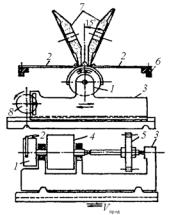
(см. рис. 9.23, б). Это устройство работает автоматически в процессе шлифования. Обработка на этих станках про- изводится следующим образом. Зубчатое колесо или на- бор зубчатых колес устанавливаются на оправке, которая крепится в центрах бабок, расположенных на подвижной каретке 3 на столе станка (рис. 9.24). Стол станка совер- шает возвратно-поступательные движения в продольном направлении (движение подачи) Vпрод. Стальные ленты 2 закреплены одной стороной на барабане ролика обката 1, а другой стороной прикреплены к столу станка 6. Карет-
ка 3, на которой установлены
делительный механизм 4, оп- |
||
равка с |
зубчатым |
колесом |
и барабан |
ролика обката 1, |
|
совершает |
быстрые |
возврат- |
но-поступательные |
движения |
|
в поперечном направлении. |
||
Ленты 2, закрепленные на |
||
барабане ролика обката 1, при |
||
наличии возвратно-поступа- |
||
тельного |
движения |
каретки |
воспроизводят обкаточные дви- |
Рис. 9.24. Схема работы зу- |
жения зубчатого колеса по ис- |
|
бошлифовального станка |
||
ходной режущей рейке шли- |
||
типа МААГ (Швейцария) |
||
фовальных кругов. Установка |
||
|
длины поперечного хода каретки 3 производится за счет регулирования радиуса кривошипа 8. Автоматический по- ворот зубчатого колеса на один зуб производится после одно- , двукратного прохождения зубчатого колеса под шлифовальными кругами. Припуск на шлифование со- ставляет от 0,1 до 0,2 мм на толщину зуба и снимается за два прохода и более. Тарельчатые шлифовальные круги 7
214
шлифуют зубья узкой полоской в 2–3 мм, поэтому силы резания и нагрев детали незначительны, что повышает точность шлифования, но снижает производительность.
Станки для зубошлифования, работающие методом обкатки двумя тарельчатыми шлифовальными кругами, снабжены устройством, компенсирующим изнашивание шлифовальных кругов в процессе правки их алмазами. Та- кие устройства обеспечивают постоянство положения ра- бочей кромки шлифовального круга при его износе, что достигается автоматическим перемещением шпинделя вме- сте с кругом вдоль оси на величину износа от шлифования
иправки. Обработка производится при скорости шлифова- ния Vкр = 30…32 м/с с числом качаний каретки 40–250 в минуту (в зависимости от типоразмера зубчатого колеса)
ипродольной подаче 0,5–2,5 мм на одно качание каретки. На станках типа МААГ стабильно достигается 4–5-я
степень точности зубчатых колес и шероховатость поверх- ности Ra = 0,1…0,8 мкм. В особых условиях обработки (при температуре воздуха в цехе 20±0,2 ° С) на станках типа МААГ может быть достигнута 3-я степень точности. Шли- фовальные круги 7 на этих станках могут быть установле- ны с нулевым углом, то есть оси шлифовальных кругов бу- дут располагаться в горизонтальной плоскости, образуя нулевой профиль исходной режущей рейки. При таком расположении шлифовальных кругов (с нулевым профилем исходной режущей рейки) возможно шлифование только зубьев с выкружкой (попытки обработки зубьев без вы- кружки приводят к поломке шлифовальных кругов).
Шлифование зубьев двумя тарельчатыми шлифо- вальными кругами без продольной подачи осуществляется на специальных зубошлифовальных станках, на которых установлены тарельчатые шлифовальные круги большого
215
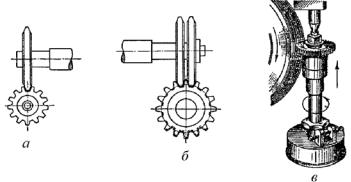
диаметра (700–880 мм), шлифующие зуб по всей длине без возвратно-поступательного движения зубчатого колеса вдоль своей оси. При таком шлифовании основание впади- ны зубчатого колеса образуется не по прямой, а по дуге ок- ружности с радиусом, равным радиусу шлифовального кру- га. На таких станках рекомендуется шлифовать узкие зуб- чатые колеса (с зубьями небольшой длины). Отсутствие продольной подачи, а следовательно, и потери времени на врезание шлифовальных кругов значительно повышает производительность по сравнению методом шлифования двумя тарельчатыми шлифовальными кругами с продоль- ной подачей.
Применяется также шлифование методом обкатки на станках:
– фирмы Найльс (Швейцария) и отечественных стан- ках мод. 5840 и 5841, работающих одним дисковым шли- фовальным кругом (рис. 9.25, а), рабочие поверхности ко- торого заправлены алмазами в виде конуса с углом между двумя конусными поверхностями 40° (угол исходной ре- жущей рейки 20°);
Рис. 9.25. Зубошлифование цилиндрического зубчатого колеса: а – одним шлифовальным кругом; б – двумя шлифовальными кругами; в – червячным шлифовальным кругом
216
–фирмы Эрликон (Швейцария–США) и отечествен- ных станках мод. 5841, работающих двумя дисковыми шлифовальными кругами (рис. 9.25, б), рабочие поверхно- сти которых заправлены алмазами в виде конуса с углом между двумя конусными поверхностями одного шлифо- вального круга 40° (угол исходной режущей рейки 20°);
–фирм Матрикс (Великобритания), Рейсхауэр (Швейцария) и отечественных станках мод. 5832 и 5833, работающих червячным кругом (рис. 9.25, в), имеющим
восевом сечении прямобочный профиль с углом 40° (угол исходной режущей рейки 20°).
На станках типа Найльс кулисе с установленным на ней конусным шлифовальным кругом, представляющим как бы зуб исходной режущей рейки, сообщается посредст- вом кривошипно-шатунного механизма быстрое возвратно-
поступательное перемещение в горизонтальной, а чаще –
ввертикальной плоскости. Шлифуемое зубчатое колесо имеет обкаточное движение. При обкатке в одну сторону производится шлифование одной эвольвентной поверхно- сти одного из зубьев, образующих впадину (по эвольвенте обкатка идет от ножки зуба к его головке), а при обкатке
вдругую сторону производится шлифование эвольвентной поверхности другого зуба этой же впадины. После обра- ботки эвольвентной поверхности зубьев, образующих впа- дину, зубчатое колесо поворачивают на один зуб и произ- водят обработку зубьев следующей впадины. Шлифование, таким образом, обычно происходит за два оборота зубчато- го колеса. Окончательное шлифование осуществляется
на более мягких режимах (с меньшей глубиной резания и меньшей скоростью обката). В процессе шлифования шлифовальный круг автоматически правится, и его режу- щие кромки возвращаются в исходное положение.
217
Простая форма круга и наличие обкатки позволяет получать 6–7-ю степень точности и шероховатость поверх-
ности Ra = 0,15…0,63 мкм.
Обработка на станках этого типа производится с применением СОЖ (обычно используют сульфофрезол или масло индустриальное И-20А) при скорости шлифова- ния Vкр = 30…32 м/с, числе качаний кулисы 15–250 в мину- ту (в зависимости от типоразмера зубчатого колеса) и кру- говой подаче 30–450 мм/мин.
Для увеличения производительности на шпиндель станка 5841 устанавливают два конусных шлифовальных круга (см. рис. 9.25, б).
При обработке цилиндрических зубчатых колес мо- дулем до 7 мм и диаметром до 700 мм широкое распро- странение получил метод шлифования червячными шлифо- вальными кругами (см. рис. 9.25, в) на станках фирм Рейс- хауэр (Швейцария), Матрикс (Великобритания) и на отече- ственных станках мод. 5832, 5833. Правка червячного шлифовального круга с прямолинейным профилем осуще- ствляется многониточными алмазными накатниками (чер- новым и чистовым). Обработка производится при скорости шлифовального круга 30–32 м/с и соответствующей скоро- сти вращения обрабатываемого зубчатого колеса, с про- дольной подачей вдоль направляющей зуба от 0,02 до 0,5 мм на оборот обрабатываемого колеса, в качестве СОЖ используется масло индустриальное И-20А.
Станки этой группы обеспечивают 5–6-ю степень точ-
ности и |
шероховатость поверхности |
Ra = 0,08…0,65 мкм. |
В особых |
условиях обработки (при |
температуре воздуха |
в цехе 20±0,2 ° С) на станках фирмы Рейсхауэр может быть достигнута 4-я, а по некоторым отдельным показателям – 3-я степень точности.
218
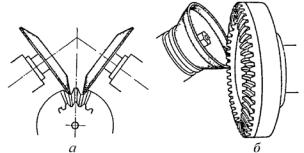
Шлифование прямых зубьев конических зубчатых колес по методу обкатки двумя тарельчатыми кругами про- изводится на станках, сконструированных на базе зубо- строгальных станков (рис. 9.26, а).
Рис. 9.26. Зубошлифование конического зубчатого колеса: а – с прямым зубом; б – с криволинейным зубом
Криволинейные зубья конических зубчатых колес шлифуются на станках фирмы Глиссон (Швейцария–США) чашечным шлифовальным кругом (рис. 9.26, б).
Сечение боковой стороны шлифовального круга долж- но иметь профиль зуба исходной режущей рейки. Чашечный шлифовальный круг, вращаясь со скоростью 30–32 м/с, обка- тывает рабочую поверхность профиля шлифуемого зуба.
Зубохонингование применяется для окончательной отделки поверхности прямых, косых и криволинейных зубьев цилиндрических зубчатых колес; производится с помощью хона – инструмента, имеющего вид геликои- дального зубчатого колеса наружного или внутреннего зацепления. Хон изготовляется из пластической массы, включающей мелкозернистый абразивный или алмазный порошок. Процесс зубохонингования осуществляется на станках внешнего или внутреннего зацепления без же- сткой кинематической связи и заключается в совместной обкатке зубчатого колеса и инструмента. Обкатка сопро-
219
вождается относительным проскальзыванием при наличии радиального давления. Оси изделия и инструмента уста- навливают под углом скрещивания от 15 до 20°.
Обработку производят при постоянном давлении ме- жду зубьями обрабатываемого зубчатого колеса и хона или способом беззазорного зацепления зубчатого колеса и хона при неизменном межцентровом расстоянии. Первый способ обеспечивает изготовление зубчатых колес более высокой точности.
Хонингуемое зубчатое колесо, находясь в зацеплении с хоном (без зазора), совершает реверсируемое вращение (попеременно в обе стороны) и возвратно-поступательное движение вдоль своей оси с частотой 17–220 Гц. Зубохо- нингование производится с окружной скоростью 2–5 м/с
при обильном охлаждении керосином.
Величина припуска при зубохонинговании не должна превышать 5 мкм, ибо при увеличении снимаемого припус- ка происходит искажение профиля эвольвенты: возникает подрез ножки и фланкирование головки зуба. Искажение эвольвенты при зубохонинговании связано с неравномер- ным проскальзыванием по высоте зуба сопряженных про- филей (зубчатого колеса и хона).
После зубохонингования величина шероховатости поверхности по сравнению с исходной уменьшается до 0,02–0,1 мкм, и обеспечивается 6–8-я степень точности. Если припуск менее 0,002 мм и точность зубчатого колеса до хонингования высокая (3–4-й степени), то после хонин- гования точность зубчатого колеса может соответство- вать 4-й степени точности.
Зубохонингование является высокопроизводительным методом окончательной отделки, например, обработка зуб- чатого колеса модулем 2–3 мм и числом зубьев 30–40 произ- водится при обильном охлаждении керосином за 30–40 се- кунд, на хонингование одного зуба требуется от 1 до 1,2 се-
220