
книги / Основы технологии машиностроения. Методы обработки заготовок и технологические процессы изготовления типовых деталей машин
.pdfОбычно зубчатые колеса средних и крупных модулей предварительно обрабатывают на зубофрезерных станках, а чистовая обработка производится на зубодолбежных станках за один или (реже) два хода.
Предварительное нарезание зубьев средних и круп- ных модулей на зубофрезерных станках более производи- тельно, чем зубодолбление. При нарезании зубьев с моду- лем менее 2 мм более производительными и точными яв- ляются зубодолбежные станки.
Следует отметить, что быстроходные зубодолбежные станки с числом ходов долбяка от 600 до 700 в минуту об- ладают достаточно высокой производительностью.
Производительность зубодолбления резко повышает- ся при совмещении чернового и чистового зубонарезания за счет применения комбинированных долбяков. Комбини- рованные долбяки производят последовательное черновое
ичистовое нарезание зубьев за один оборот. У таких дол- бяков часть зубьев имеет заниженную толщину, они вы- полняют черновое нарезание профилей зубьев. Другая часть зубьев удаляет оставшийся припуск при чистовом нарезании. На долбяке предусмотрен участок со срезанны- ми зубьями, который позволяет снимать и устанавливать заготовки без отвода шпинделя с долбяком. Следует отме- тить, что комбинированные долбяки пригодны для нареза- ния зубчатых колес только с определенным числом зубьев. Их целесообразно применять только на заводах массового
икрупносерийного производства. Комбинированные дол- бяки пригодны только для нарезания зубчатых колес с ма- лым числом зубьев, так как число зубьев этих долбяков должно быть равно удвоенному числу зубьев нарезаемого зубчатого колеса.
На рис. 9.7 приведены схемы зубодолбления: цилин- дрических колес внутреннего зацепления с прямыми зубь- ями (см. рис. 9.7, а); цилиндрического зубчатого венца на-
181
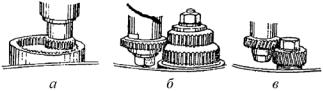
ружного зацепления с прямыми зубьями в блочном зубчатом колесе с двумя венцами разных диаметров (см. рис. 9.7, б) расстояние между которыми составляет от 4 до 6 мм; ци- линдрического зубчатого колеса наружного зацепления с винтовыми зубьями (см. рис. 9.7, в).
Рис. 9.7. Примеры зубодолбления цилиндрических колес:
а– внутреннего зацепления с прямыми зубьями,
б– наружного зацепления с прямыми зубьями;
в– наружного зацепления с винтовыми зубьями
При нарезании спиральных зубьев шпиндель с за- крепленным на нем долбяком совершает возвратно- поступательное и винтовое движения на следующих ре-
жимах: черновое долбление при |
V = 12…18 м/мин, |
Sкр = 0,25…0,5 мм/дв. ход.; чистовое |
долбление при |
V = 20…30 м/мин, Sкр = 0,15…0,3 мм/дв. ход.
Зубодолбежные станки обеспечивают 7–8-ю степень точности и шероховатость поверхности Ra = 1,0…2,5 мкм (СОЖ – масло индустриальное типа И-20А).
Существенным преимуществом зубодолбления по сравнению с зубофрезерованием является то, что оно по- зволяет производить обработку зубчатых венцов в блочных зубчатых колесах с двумя, тремя и более венцами разного диаметра и с расстоянием между соседними венцами 4–6 мм (для выхода долбяка вполне достаточно 2–4 мм).
Как было указано выше, цилиндрические зубчатые ко- леса наружного зацепления с прямым, косым и винтовым зубьями можно нарезать на зубострогальных станках с при-
182
менением долбяков в виде гребенок (реек), которые изготов- лять и затачивать проще, чем долбяки в виде шестерен.
Зубострогальные станки для нарезания зубчатых ко- лес гребенками работают по методу обкатки. При наре- зании косых зубьев суппорт с гребенкой повертывается на угол наклона зуба.
Гребенки изготавливают трех типов в зависимости от модуля и характера обработки: обдирочная – для черново- го нарезания зубьев; отделочная – для чистового нарезания зубьев; шлифовочная – для зубьев, которые после нарезания будут шлифоваться. Обдирочные гребенки изготавливаются меньшей ширины, чем отделочные; после обдирки остается припуск на отделку до 0,5 мм на сторону.
Нарезание зубьев гребенками обеспечивает 7–8-ю сте- пень точности и шероховатость поверхности Ra = 1,2…2,5 мкм. Однако ввиду меньшей производительности по сравнению с нарезанием круглыми долбяками и червячными фрезами нарезание зубьев гребенкой применяется редко.
Нарезание цилиндрических зубчатых колес методом зуботочения является относительно новым методом, пред- назначенным для нарезания прямых и косых зубьев на зу- бофрезерных станках с помощью круглого долбяка, ис- пользуемого в качестве многорезцового инструмента.
Зацепление инструмента с обрабатываемым зубча- тым колесом рассматривается как зацепление двух винто- вых зубчатых колес, при котором происходит продольное скольжение поверхностей зубьев, являющихся в данном случае движением, осуществляющим процесс резания.
На зубофрезерном станке вместо червячной фрезы устанавливается долбяк под углом β (рис. 9.8) к оси заго- товки. Углы долбяка и заготовки подбираются таким обра- зом, чтобы разность между углами винтовой линии инст- румента и заготовки не была равна нулю.
183
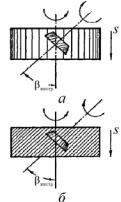
Нарезание прямых зубьев производится косозубым долбяком (см. рис. 9.8, а), а нарезание косых зубьев с углом наклона 45° – пря- мозубым долбяком (см. рис. 9.8, б). Производительность этого метода в 2–4 раза выше, чем зубофрезерова- ния однозаходной червячной фрезой.
Основными недостатками зу- боточения являются необходимость иметь оборудование высокой точ- ности и жесткости и недопусти- мость возникновения при зуботоче- нии вибраций.
Накатывание цилиндрических зубчатых колес произ-
водится без удаления такого объема материала, как при ре- зании. Отходы металла не превышают 2–4 % от массы за- готовки.
Зубья с модулем до 1,5 мм накатываются в холодном состоянии, а более 1,5 мм – в горячем.
Накатывание зубчатых колес в холодном состоянии
является одним из высокопроизводительных методов об- работки.
Накатывание зубчатых венцов в 15–20 раз имеет большую производительность по сравнению с зубофрезе- рованием и обеспечивает высокое качество поверхностей зуба, что способствует повышению износостойкости зубьев зубчатых колес.
Основным условием обработки зубчатых колес нака- тыванием в холодном состоянии является достаточная пла- стичность материала заготовки. Этому условию удовлетво- ряют алюминиевые и медные сплавы (за исключением
184
бронз некоторых марок), а также нержавеющая сталь неко- торых марок при соответствующей предварительной тер- мической обработке.
Накатывание зубьев достаточно часто осуществляют в два этапа: на первом этапе производят предварительное накатывание зубчатыми валиками (роликами), а на втором этапе окончательное накатывание выполняют калибрую- щими валиками (роликами). В процессе накатывания зубь- ев поверхностные слои металла сильно упрочняются, при- чем упрочнение распространяется на значительную глуби- ну. Для предотвращения износа зубонакатного инструмен- та – зубчатых и калибрующих валиков (роликов), а также для уменьшения уровня напряжений в поверхностных сло- ях металла заготовки целесообразно между операциями предварительного и окончательного накатывания выпол- нять промежуточную операцию термической обработки заготовки – отжиг.
В производстве применяют несколько схем накаты- вания зубчатых колес: одним накатником; двумя накатни- ками без заборной части; двумя накатниками с заборной частью; тремя накатниками; двумя рейками.
Выбор схемы накатывания в значительной степени зависит от длины образующей зуба. Практикой установле- но, что накатывание зубчатых колес небольшой ширины отдельными заготовками целесообразно осуществлять дву- мя накатниками без заборной части, а зубчатых колес большой ширины или собранных в пакет на оправку не- скольких заготовок – двумя накатниками с заборной ча- стью. Заборная часть обеспечивает постепенное проникно- вение зубьев накатников в металл заготовки и заполнение металлом заготовки впадин между зубьями накатников без изменения межцентрового расстояния осей накатников. Накатникам сообщают принудительное вращение совмест-
185
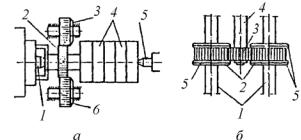
но с заготовкой. Зубчатые колеса можно накатывать на то- карных станках с продольной подачей (рис. 9.9, а) и на специальных стендах (рис. 9.9, б).
Рис. 9.9. Методы накатывания зубьев цилиндриче- ских зубчатых колес: а – на токарном станке;
б – на специальном стенде
При накатывании зубьев на токарном станке в перед- нем 1 и заднем 5 центрах станка устанавливается оправка, получающая вращение от шпинделя станка. На оправке ус- танавливаются заготовки 4 и делительное зубчатое коле- со 2, находящееся в зацеплении с двумя или тремя накат- никами 3 и 6, закрепленными на суппорте станка. При вы- ходе из зацепления с делительным колесом 2 накатники 3 приводятся во вращение зубьями накатанной части загото- вок 4. Для образования симметричного профиля зубьев на- катывание производится сначала в одном, а затем в обрат- ном направлении с ускоренным обратным вращением шпинделя. Накатники 3 и 6 представляют собой зубчатые колеса с модулем, равным модулю накатываемого колеса. Накатники имеют заборную часть для постепенного вне- дрения в металл обрабатываемых заготовок.
При накатывании зубьев на специальных стендах (см. рис. 9.9, б) инструментом служат зубчатые валики 2, с обеих сторон которых надеваются дисковые ограничи- тели 5, препятствующие вытеснению металла в осевом
186
направлении и образованию облоя. Валики 2 вращаются на шпинделях 1. Заготовка 3 закрепляется на оправке 4 и приводится во вращение зубьями валиков 2. Головка зуба валика образует ножку, а ножка валика – головку зуба зуб- чатого колеса, что обуславливает размеры элементов зубча- того валика: головку зуба принимают равной 1,2 модуля, а ножку – равной модулю. Накатывание производится при использовании в качестве СОЖ масла, например масла ин- дустриального И-12А.
Накатывание зубчатых колес в холодном состоянии обеспечивает точность 7–9-й степени и шероховатость по- верхности Rа = 0,32…1,25 мкм.
Накатывание зубчатых венцов в горячем состоянии
производится на специальных стендах (см. рис. 9.9, б) ана- логично накатыванию в холодном состоянии. Отличие со- стоит в том, что за 20–30 секунд до накатывания зубчатого венца поверхностные слои заготовки нагреваются токами высокой частоты до температуры порядка 1200 °С.
Точность зубчатых колес после накатки в горячем со- стоянии соответствует 9–10-й степени точности и шерохо- ватость поверхности Rа = 0,63…2,5 мкм.
Накатывание зубчатых венцов в горячем состоянии существенно повышает износостойкость и изгибную проч- ность зубчатых колес.
Закругление зубьев производится для облегчения со- единения зубчатых колес, предназначенных для коробок пе- редач и других зубчатых колес, переключающихся на ходу. Закругление торца зубьев производится на специальных зу- бозакругляющих станках при помощи пальцевых фрез мето- дом копирования (рис. 9.10, а). В процессе работы пальцевая фреза вращается и одновременно перемещается по дуге с возвратно-поступательным движением, огибая кромку зуба
187

Рис. 9.10. Закругление зубьев цилиндрических зубчатых колес: а – пальцевой фрезой; б – пустотелой фрезой
обрабатываемого колеса, которая периодически отводится в осевом направлении, поворачивается вокруг оси на один зуб и подводится к фрезе. Время обработки каждого торца зуба от 1 до 3 с. Производительность можно повысить за счет применения пустотелой фрезы (рис. 9.10, б).
9.2. Обработка червячных зубчатых колес
При нарезании червячных зубчатых колес ось чер- вячной модульной фрезы устанавливается перпендикуляр- но оси обрабатываемого колеса и точно по центру ширины венца. Нарезать червячные зубчатые колеса можно тремя способами: способом радиальной подачи; способом тан- генциальной подачи; комбинированным способом.
Нарезание червячных колес способом радиальной по-
дачи более распространено, чем другие способы. При этом способе (рис. 9.11, а) фреза 1 и нарезаемое зубчатое колесо 2 вращаются; скорости вращения их рассчитываются так, что- бы за один оборот фрезы зубчатое колесо повернулось на число зубьев, равное числу заходов червяка.
В отличие от нарезания зубчатых колес суппорт с фре- зой стоят на месте, стол же с укрепленным на нем зубчатым
188
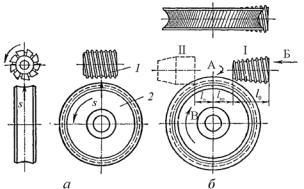
Рис. 9.11. Зубонарезание червячных зубчатых колес червячными фрезами: а – способом радиальной подачи; б – способом тангенциальной подачи: I и II – соответст- венно начальное и конечное положение фрезы
(червячным) колесом осуществляет горизонтальную пода- чу S на глубину зуба по направлению к фрезе, то есть в ра- диальном направлении.
В зубофрезерных станках, работающих по методу об- катки, которые предназначены для нарезания зубчатых ко- лес большого диаметра, горизонтальная подача осуществ- ляется не столом с заготовкой, а стойкой, несущей суппорт с фрезой.
Способ радиальной подачи применяется для нареза- ния червячных зубчатых колес к однозаходным и реже – двухзаходным червякам.
Способ тангенциальной подачи применяется главным образом для нарезания червячных зубчатых колес к много- заходным червякам; он выполняется при помощи специ- ального суппорта, позволяющего осуществлять тангенци- альную (то есть по касательной к зубчатому колесу) подачу фрезы (рис. 9.11, б).
189
Стрелка А указывает вращение червячной фрезы, стрелка Б – подачу фрезы по касательной линии к зубчато- му колесу, стрелка В – вращение зубчатого колеса. Нареза- ние зубчатого колеса заканчивается, когда все зубья фрезы перейдут за ось зубчатого колеса.
При нарезании способом тангенциальной подачи по- лучается более правильный профиль, но стоимость фрезы, работающей способом тангенциальной подачи, значитель- но выше стоимости фрезы, работающей способом радиаль- ной подачи, и, кроме того, требуется наличие специального суппорта.
Нарезание червячных зубчатых колес комбинирован-
ным способом применяется при нарезании единичных нор- мализованных червячных зубчатых колес, для которых изго- товление червячных фрез экономически не оправдывается.
Нарезание производится последовательно двумя рез- цами: черновым и чистовым; резец закрепляется в оправке (рис. 9.12, а), представляя собой как бы однозубую фрезу. Чистовой резец изготавливается точно по профилю, а чер- новой уже чистового, благодаря чему остается припуск, примерно равный 0,5 мм на сторону зуба. Черновой резец врезается на установленную глубину с радиальной подачей, после чего чистовой резец дорезает зуб с тангенциальной подачей.
Резцы (черновой 1 и чистовой 2) можно менять; часто оба резца закрепляют на одной оправке (рис. 9.12, б) на определенном расстоянии один от другого.
Нарезание червячного глобоидального колеса обычно состоит из двух операций: предварительного нарезания при радиальной подаче и чистового нарезания при круговой подаче с точно заданным осевым расстоянием.
190