
книги / Основы технологии машиностроения. Методы обработки заготовок и технологические процессы изготовления типовых деталей машин
.pdf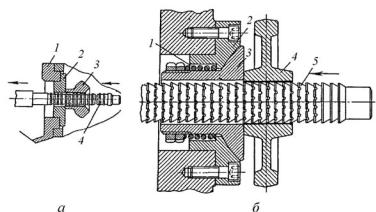
Типы хвостовиков зависят от того, каким способом крепится протяжка в патроне станка.
Отечественные протяжные станки развивают тяговую силу до 10 000 кгс (98 кН) при рабочей скорости поряд- ка 13 м/мин, 40 000 кгс (390 кН) при рабочей скорости по- рядка 6,8 м/мин, 100 000 кгс (980 кН) при рабочей скоро-
сти 0,3–3,7 м/мин.
Практически все отечественные станки снабжены гидравлическим приводом подач, что обеспечивает спо- койный и равномерный ход протяжки. При протягивании деталь устанавливают на жесткую или шаровидную опору (рис. 4.12). На жесткую опору устанавливают детали, у ко- торых обеспечена перпендикулярность торца к оси отвер- стия (см. рис. 4.12, а). Если торец не подрезан (например, поверхность торца после литья) или при обработке не обес- печена перпендикулярность оси отверстия детали к торцу, то применяют шаровидную опору (см. рис. 4.12, б).
Рис. 4.12. Установка деталей при протягивании: а – на жест- кой опоре: 1 – лобовая часть, 2 – опорная шайба, 3 – обраба- тываемая деталь, 4 – протяжка; б – на шарнирной опоре: 1 – пружина, 2 – опорная шайба, 3 – шаровая опора,
4 – обрабатываемая деталь, 5 – протяжка
91
Отверстия протягивают на горизонтальных и верти- кально-протяжных станках при скорости резания 3–15 м/мин. Подача на зуб 0,02–0,1 мм. В настоящее время на ряде пере- довых предприятий применяют скоростное протягивание со скоростью резания до 25 м/мин.
Припуски под протягивание цилиндрических отвер- стий составляют 0,5–1,5 мм на диаметр.
В качестве СОЖ применяют сульфофрезол, масло индустриальное И-20А или 20%-й раствор эмульсола в воде
сдобавлением 4 % мыла.
4.2.Обработка отверстий абразивным инструментом
4.2.1. Шлифование отверстий
Внутреннее шлифование сквозных и глухих цилин- дрических отверстий из чугунов, сталей, жаропрочных сплавов обеспечивает точность 6–7-го квалитета и шеро- ховатость поверхности Ra = 0,15…1,25 мкм. Обработку отверстий производят на шлифовальных станках: при вращающейся детали, закрепленной в патроне станка; при неподвижной детали на станках с планетарным движени- ем шпинделя; при вращающейся незакрепленной детали на бесцентрово-шлифовальных станках.
Диаметр шлифовального круга обычно принимают равным 0,8…0,9 диаметра отверстия.
4.2.1.1.Шлифование при вращающейся детали, закрепленной в патроне станка
Наиболее распространен первый способ обработки
спродольной или поперечной подачей (рис. 4.13).
Взависимости от свойств обрабатываемого материа- ла и вида операции скорость резания при шлифовании из- меняется от 25 до 100 м/с.
92
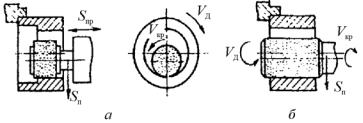
Рис. 4.13. Схема шлифования отверстий: а – с продольной подачей; б – с поперечной подачей
Продольная подача выражается в долях ширины шли- фовального круга Вкр и принимается Sпр = (0,2…0,3) Вкр мм/об при чистовом шлифовании, а при черновом шлифовании
Sпр = (0,6…0,8) Вкр мм/об.
Поперечная подача Sпоп круга при чистовом шлифо- вании равна 0,003–0,015 мм/дв. ход стола, а при черно- вом – 0,05–0,075 мм/дв. ход стола. Глубина резания при чистовом шлифовании равна 0,005–0,015 мм, а при черно- вом – 0,015–0,04 мм. Длина продольного хода стола опре- деляется по формуле: при шлифовании на проход
L = L0 – (0,2…0,4) Bкр,
при шлифовании в упор
L = L0 – (0,4…0,6) Bкр,
где L – длина продольного хода стола, мм; L0 – длина шлифуемой поверхности, мм; Bкр – ширина шлифовально- го круга, мм.
При черновом шлифовании вращающейся детали, за- крепленной в патроне, получают точность 8–9-го квалитета и шероховатость Ra = 0,16…1,25 мкм; при чистовом шли- фовании – 6–7-го квалитета и Ra = 0,08…0,32 мкм.
93
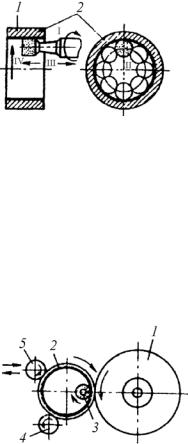
4.2.1.2. Планетарное шлифование отверстий
При этом способе шлифования (рис. 4.14) шпиндель шлифовального станка имеет четыре движения:
–вращение круга вокруг своей оси 1;
–планетарное движение по окружности внутренней поверхности детали, неподвижно закрепленной на столе станка II;
–возвратно-поступатель- ное движение вдоль оси дета-
ли III;
–поперечное перемеще- ние (поперечная подача) IV.
Эта схема шлифования применяется для обработки
Рис. 4.14. Схема планетарно- |
корпусных деталей. |
го шлифования отверстий |
Точность обработки и ше- |
|
роховатость с планетарным |
движением шпинделя соответствует при черновом шлифо-
вании 7–8-му квалитету и Ra = 0,16…1,25 мкм; при чисто- вом шлифовании – 6–7-му квалитету и Ra = 0,08…0,32 мкм.
4.2.1.3. Бесцентровое шлифование отверстий
При этом способе шлифования деталь поддерживается тремя роликами (рис. 4.15). Один ролик 1 является ведущим
|
и |
создает вращательное |
|
|
движение детали 2 относи- |
||
|
тельно шлифовального кру- |
||
|
га 3, который вращается |
||
|
вокруг собственной оси. |
||
|
|
Верхний |
нажимной |
|
ролик 5 прижимает деталь 2 |
||
Рисс. 4.15. Схема бесцентрового |
к |
ведущему |
ролику 1 |
и третьему опорному роли- |
|||
шлифования отверстий |
|
|
|
94 |
|
|
|
ку 4. Деталь, зажатая между тремя роликами, имеет скорость ведущего ролика. При смене деталей зажимной ролик 5 от- водят влево, освобождая деталь 2.
Точность обработки при бесцентровом шлифова- нии по диаметру соответствует 6–7-му квалитету, Ra = 0,16…1,25 мкм, а концентричность и параллель- ность осей внутреннего и наружного диаметров достига-
ет 0,003 мм.
4.2.2. Хонингование отверстий
Хонингование (перекрестное шлифование брусками) применяется для обработки предварительно развернутых, расточенных или шлифованных сквозных и глухих цилин- дрических отверстий.
Обработка осуществляется хоном – инструментом (рис. 4.16), имеющим абразивные или алмазные бруски. Хон совершает одновременно вращательное и возвратно- поступательное движения.
Бруски в процессе обработки раздвигаются (радиаль- ная подача). Раздвижение брусков в радиальном направле- нии осуществляется механическим, гидравлическим или пневматическим устройством. Давление брусков на по- верхность детали 0,1–4,0 МПа. Существуют также конст- рукции хонинговальных головок с механическим дозиро- ванным раздвижением брусков (см. рис. 4.16, а).
Перебег головки на сторону lп составляет 12–15 мм
(см. рис. 4.16, б).
Для обработки отверстий с прерывистыми поверхно- стями, например отверстия со шпоночной канавкой или шлицевого отверстия, используют хонинговальные головки (см. рис. 4.16, в) с размещением абразивных брусков не па- раллельно оси головки, а под углом α = 15…30°.
Головка состоит из корпуса 4, в котором шток 2 ввер- нут в шток 6, соединенный с четырьмя колодками 8, несу-
95
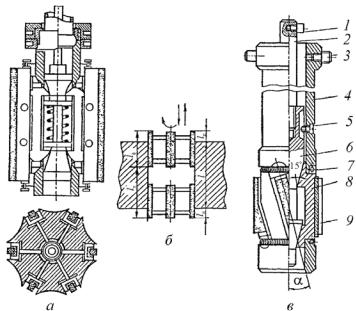
Рис. 4.16. Хонинговальная головка: а – конструкция; б – схема для определения длины перемещения; в – головка
для хонингования шлицевого отверстия
щими абразивные бруски 9. На штоке имеются два усечен- ных конуса под углом 15°. Для предохранения от выпадения колодок 8 из корпуса 4 служат две пружины 7.
Хонинговальная головка закрепляется в шпинделе станка с помощью шпилек 1 и 3. Шуруп 5 препятствует то- му, чтобы шток 6 провертывался.
Расположение абразивных брусков под углом 15…30° обеспечивает постоянное перекрытие шпоночных пазов не менее чем двумя брусками одновременно. Режущие зерна хонинговальных брусков изготавливают из электро- корунда, карбида кремния, эльбора или алмаза.
Процесс хонингования осуществляется с СОЖ, вы- полняющей смазывающее, охлаждающее и вымывающее действие. При обработке чугуна в качестве СОЖ исполь-
96
зуют керосин с добавкой 10–15 % масла индустриально- го И-20А, а для стали – смесь из масла индустриально-
го И-20А (12–25 %) и керосина 75–88 %.
Для отверстий диаметром 25–500 мм величина при- пуска составляет 0,02–0,20 мм для чугунных деталей и 0,01–0,08 мм – для стальных деталей.
Хонингование производят на горизонтальных и вер- тикальных одно- и многошпиндельных станках. Хонинго- вальная головка вращается со скоростью 60–75 м/мин для чугуна и бронзы и 45–60 м/мин – для стали; скорость воз- вратно-поступательного движения головки 12–30 м/мин.
Хонингование устраняет овальность, конусность, бочкообразность и обеспечивает точность 6–8-го квалите- та и шероховатость поверхности Ra = 0,16…0,63 мкм. Тонкое хонингование обеспечивает точность 5–6-го ква- литета и шероховатость поверхности Ra = 0,04…0,16 мкм.
Хонингование является одним из самых распростра- ненных способов финишной обработки глубоких отвер- стий, например труб артиллерийских стволов.
4.2.3. Притирка (доводка) отверстий
Притирка – отделочная абразивная обработка, обес- печивающая точность размеров 5–6-го квалитета и шерохо- ватость поверхности Ra = 0,01…0,16 мкм.
Инструментом служит притир, представляющий со- бой разрезную втулку, создающую давление на стенки от- верстия при помощи пружин (рис. 4.17).
Для достижения высокой точности 4-го квалитета, а иногда и точнее (овальность и конусность 1–2 мкм), ис- пользуют притиры с дозированным изменением диаметра притира.
Корпус притира в этом случае изготавливается в виде разрезной втулки с внутренней поверхностью в виде кону- са, надетой на ответный конус штока. При перемещении
97
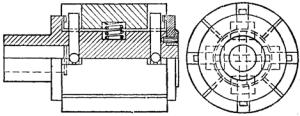
Рис. 4.17. Чугунный притир
штока вдоль оси притира разрезная втулка упруго дефор- мируется, изменяя диаметр корпуса притира.
На наружную цилиндрическую поверхность корпуса притира наносятся перекрещивающиеся пазы. Притиры изготавливают из чугуна, мягкой стали, латуни, меди и других материалов, более мягких, чем материал обраба- тываемой детали.
На поверхность притира наносится паста или суспен- зия на основе корунда, карбида кремния, карбида бора (зернистостью М2–М3), алмаза (зернистостью 1–100 мкм).
В качестве связующих материалов в пастах приме- няют стеарин, парафин, вазелин, олеиновую кислоту и дру- гие составляющие. Состав связующих материалов паст, как правило, выбирают, основываясь на существующих реко- мендациях и производственном опыте.
Притир совершает вращательное (Vвр = 15…50 м/мин) и возвратно-поступательное (Vп = 10…25 м/мин) движения с удельным давлением 0,2–0,5 МПа или работает с дозиро- ванной подачей разжимного конуса.
98
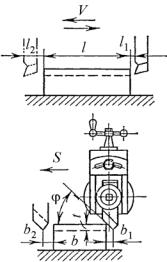
5. МЕТОДЫ ОБРАБОТКИ ПЛОСКИХ ПОВЕРХНОСТЕЙ
При обработке плоских поверхностей применяют строгание, долбление, фрезерование, протягивание, шли- фование, полирование, притирку (доводку) и шабрение.
5.1. Строгание и долбление плоских поверхностей
Обработку производят на продольно- или поперечно- строгальных станках (последние называются шепингами) одним резцом или несколькими резцами.
При строгании на продольно-строгальных станках стол с закрепленной на нем обрабатываемой заготовкой (или заготовками) совершает возвратно-поступательное движе- ние; подача в поперечном направлении (поперечная подача) придается резцу путем перемещения резцового суппорта, которое осуществляется прерывисто после каждого рабочего хода. Стружка снимается во время хода стола в одном на- правлении, то есть во время рабочего хода. Обратный – холостой – ход совершается со скоростью, в 2–3 раза большей, чем скорость рабоче- го хода, тем не менее потеря времени при холостых ходах делает строгание менее произ- водительным способом обра- ботки, чем другие способы (на- пример, фрезерование).
Схема строгания плос- кости представлена на рис. 5.1.
На поперечно-строгаль- ных станках возвратно-посту- пательное движение имеет ре-
99
зец, который закреплен на суппорте ползуна. Обрабатывае- мая заготовка, закрепляемая на столе станка, получает попе- речную подачу благодаря прерывистому перемещению сто- ла в поперечном направлении после каждого рабочего хода.
Продольно-строгальные станки изготавливают одно- стоечными и двухстоечными, с одним, двумя, четырьмя и более (до 12) суппортами.
Одностоечные строгальные станки применяют для заготовок, которые не помещаются полностью на столе станка и свешиваются с него.
Продольно-строгальные и поперечно-строгальные стан- ки применяют в единичном, мелкосерийном и серийном производствах вследствие их универсальности, простоты управления, достаточной точности обработки и меньшей стоимости по сравнению с фрезерными станками.
Работа на строгальных станках не требует сложных приспособлений и инструментов. Однако этот вид обработки малопроизводителен. Низкая производительность объясня- ется тем, что обработку ведут одним резцом с потерями вре- мени на обратные холостые ходы. Повысить производитель- ность на строгальных станках помогут следующие меры:
–установка нескольких резцов на одной державке, что сокращает число рабочих и холостых ходов и позволяет снимать значительно больший припуск за один проход;
–одновременная работа нескольких суппортов и, сле- довательно, совмещение времени обработки нескольких по- верхностей;
–применение широких резцов и больших подач, спе- циальных установочно-зажимных приспособлений и шаб- лонов для установки резцов при профильном строгании;
–увеличение скорости холостого хода в 2–3 раза по сравнению со скоростью рабочего хода.
100