
книги / Основы технологии машиностроения. Методы обработки заготовок и технологические процессы изготовления типовых деталей машин
.pdfшлифовальном станке коническим шлифовальным кругом большого диаметра (800 мм и более).
Этот метод обеспечивает высокую производитель- ность. Таким кругом можно получить разные профили чер- вяка путем его перемещения в горизонтальной плоскости. Шлифование производится при трех движениях: вращении круга, медленном вращении червяка и поступательном пе- ремещении круга на величину одного шага (хода для мно- гозаходных червяков) за один оборот изделия. Для отделки витков червяков ответственных передач применяют при- тирку червяков чугунными или фибровыми притирами, имеющими форму червячного колеса. В качестве абразивно- го материала применяют микропорошки с маслом, а для по- лучения низкой шероховатости поверхности – пасты ГОИ.
Эвольвентный червяк (см. рис. 9.17, б) представляет собой как бы цилиндрическое зубчатое колесо с эвольвент- ной поверхностью. В сечении червяка плоскостями, пер- пендикулярными оси основного цилиндра, получаются эвольвенты, от которых червяк и получил свое название. Эвольвентный червяк можно рассматривать как цилиндри- ческое зубчатое колесо с малым числом спиральных зубьев, имеющих большой наклон.
Эвольвентные червяки нарезают на токарных станках
сраздельной обработкой каждой стороны витка двумя рез- цами 1 и 2, профили режущих кромок которых совмещаются
сдвумя плоскостями, расположенными касательно к поверх- ности основного цилиндра с двух сторон (см. рис. 9.17, б). По мере увеличения диаметра основного цилиндра уста- новка резцов выше и ниже центра вызывает определенные трудности вследствие изменений углов резания, поэтому при нарезании эвольвентных червяков применяют про- фильные резцы, соответствующие контуру нормального
201
сечения впадины червяка с установкой плоскости профиля нормально к ее оси.
Если червяк правый, то левую сторону боковой по- верхности витков нарезают резцом, поднятым над осью,
аправую – опущенным. При левом червяке оба резца соот- ветственно меняют местами. Указанным способом эволь- вентные червяки нарезают редко ввиду неблагоприятных условий резания резцами, поднятыми или опущенными по отношению к осевой линии. Такие червяки обычно фре- зеруют фасонными дисковыми или пальцевыми фрезами,
атакже фрезами-улитками (рис. 9.18, б); шлифуют их пло- ской стороной тарельчатого шлифовального круга. В круп- носерийном и массовом производстве архимедовы и эволь- вентные червяки нарезают обкаточными дисковыми резца-
ми, подобными зуборезным долбякам (см. рис. 9.18, в), на специальных станках. Подача осуществляется инстру- ментом в осевом направлении заготовки червяка при вра- щении червяка и резца.
Червяк с прямосторонним профилем в нормальном сечении витка называют конволютным (см. рис. 9.17, в). Нарезают его резцами, расположенными нормально к боко- вым поверхностям витка.
Нарезание глобоидальных червяков требует приме- нения специальных устройств на зубофрезерных станках. Предварительное фрезерование глобоидального червяка производится за один или два прохода с припуском от 0,3 до 0,5 мм на толщину витка. Окончательное нарезание осуществляется универсальной или специальной многорез- цовой головкой. После нарезания витков глобоидальный червяк обычно подвергают термообработке с последующим шлифованием опорных шеек и витков. Отделку глобои- дальных червяков осуществляют притиркой либо обкаткой закаленным роликом.
202
9.5.Чистовая обработка зубчатых колес
Сувеличением быстроходности машин возникла на- стоятельная необходимость в бесшумно работающих зуб- чатых колесах. Шум, вызываемый зубчатыми колесами, часто обусловлен ненормальными условиями работы зуб- чатой передачи, влекущими за собой ее ускоренное изна- шивание. Шум вреден для человеческого организма. Весь комплекс причин возникновения шума при работе зубча- тых колес изучен недостаточно полно, но в основном про- блема шума зубчатых передач связана с точностью и каче- ством изготовления элементов зубчатых колес.
Улучшение качества зубчатых колес, способствую- щее уменьшению шума, достигается: нарезанием зубчатых колес с точностью, выражаемой сотыми и тысячными до- лями миллиметра; термической обработкой с применением цианирования и газовой цементации, дающих значительно меньшую деформацию зубьев зубчатых колес, чем цемен- тация в твердом карбюризаторе и закалка; применением рациональных способов окончательной чистовой обработ- ки зубьев, позволяющих достигнуть точности зубчатых ко- лес до 2–3 мкм; использованием специальных высокопроч- ных малодеформируемых в процессе термической и хими- ко-термической обработки сплавов, в первую очередь вы- сокопрочных сталей, и неметаллических материалов (пластмасс, текстолита и др.).
Помимо стремления усовершенствовать способы окончательной обработки зубьев изыскиваются способы заглушения шума путем подбора конфигурации коробок скоростей, применения гибких зубчатых колес из специ- альных сортов стали, зубчатых колес из неметаллических материалов.
Причины шума заключаются не только в низком ка- честве обработки зубьев, но и в неудовлетворительной
203
сборке зубчатых передач, неточности изготовления корпу- сов и валиков, деформации валиков, несущих зубчатые колеса, условиях смазки и т.д.
Окончательная чистовая отделка зубьев производится следующими способами: обкаткой; шевингованием; шли- фованием; притиркой и приработкой.
Обкаткой называется процесс получения гладкой по- верхности зубьев незакаленного зубчатого колеса путем вращения его между тремя вращающимися закаленными зубчатыми колесами (эталонами), точность которых дости- гает ±5 мкм. При этом достигается некоторое исправление небольших погрешностей в форме зуба. Обкатка осуществ- ляется при обильной подаче масла в зону контакта зубьев эталонных колес с зубьями обкатываемого колеса. Как пра- вило, в результате обкатки точность повышается примерно на одну степень (до 5–9-й) в зависимости от точности зуб- чатого колеса перед обкаткой.
Шевингованием (бреющим резанием) называется процесс чистовой отделки незакаленного зубчатого колеса, заключающийся в снятии (соскабливании) очень мелких волосообразных стружек, благодаря чему значительно ис- правляются эксцентриситет начальной окружности, ошиб- ки в шаге, в профиле эвольвенты и в угле подъема винто- вой линии.
Шевингование (или, иначе говоря, шевинг-процесс)
производится двумя способами.
По первому способу шевингование выполняется при помощи специального инструмента, называемого шевером.
Шевер представляет собой режущее зубчатое колесо (диско- вый шевер) с прорезанными на боковых поверхностях каж- дого зуба канавками глубиной порядка 0,8 мм. Эти канавки образуют режущие кромки, которые соскабливают волосо- образную стружку. На рис. 9.19 представлены общий вид и схемы шевингования. Дисковые шеверы по ГОСТ 8570–80
204
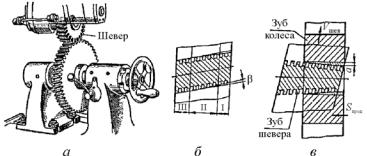
Рис. 9.19. Шевингование цилиндрического зубчатого колеса дисковым шевером: а – общий вид; б, в – схемы шевингования за один проход
изготавливают с уголом наклона винтовой линии зубьев
взоне делительной окружности 5, 10 и 15° (при модуле до 1,75 мм) и 5 и 15° (при модуле 2–8 мм). Оправка с обраба- тываемым зубчатым колесом (см. рис. 9.19, а) закрепляется
вцентрах стола станка; шевер располагается над зубчатым колесом под углом для внешнего зацепления 10–15° и для внутреннего зацепления – около 3°, образуя с колесом как бы винтовую пару со скрещивающимися осями. Крутящийся шевер вращает обрабатываемое зубчатое колесо, которому придают осевое возвратно-поступательное перемещение, называемое продольной подачей (Sпр = 0,15…0,3 мм на один оборот зубчатого колеса); при этом шевер равномерно со- скабливает стружку по всей ширине зуба. Помимо враще- ния и осевого движения обрабатываемого зубчатого коле- са для равномерного снятия стружки по всему профилю зуба стол станка имеет вертикальное перемещение подачи Sв = 0,025…0,04 мм на один ход стола. После окончания каждого хода стола шевер получает вращение в обратную сторону и обрабатывает другую сторону зуба. Для предвари- тельной обработки число ходов составляет от 4 до 6, для окончательной – 2…4.
205
Припуск на шевингование принимается равным 0,03– 0,06 мм на сторону зуба, зависит от модуля зубчатого коле-
са и составляет: |
|
|
|
|
модуль, мм.............. 2 |
3 |
4 |
5 |
6 |
припуск, мм ............ 0,03 |
0,04 |
0,05 0,055 |
0,06. |
|
Шевингование повышает точность |
относительно |
предварительной обработки зубьев примерно на 1–2 степе- ни и обеспечивает 5–8-ю степень точности. Исправление погрешностей зубчатых колес шевингованием представле- но в табл. 9.1.
Т а б л и ц а 9 . 1
Данные, характеризующие исправление погрешностей зубчатых колес шевингованием
|
Величины погрешностей, мм |
|||
Наименование погрешности |
до шевин- |
после шевингования |
||
для прямых |
для косых |
|||
|
гования |
|||
|
зубьев |
зубьев |
||
|
|
|||
Суммарная ошибка межцентрово- |
0,06–0,1 |
0,025 |
0,02 |
|
го расстояния |
||||
|
|
|
||
Радиальное биение |
0,05–0,07 |
0,01–0,02 |
0,01 |
|
Отклонение профиля |
0,04–0,08 |
0,01–0,02 |
0,01 |
|
Отклонение направления зуба |
0,05 |
0,015 |
0,01 |
|
Накопленная погрешность шага |
0,05–0,07 |
0,03–0,04 |
0,03 |
|
Неравномерность окружного ша- |
0,04–0,05 |
0,015–0,02 |
0,01–0,015 |
|
га между двумя зубьями |
||||
|
|
|
Шевингование за один проход находит распростране-
ние для чистовой отделки зубчатых колес средних модулей шеверами специальной конструкции. Зубья таких шеверов имеют три группы зубчиков (см. рис. 9.19, б): заборные I, режущие II и калибрующие III. Боковые поверхности левой и правой сторон заборной и режущей частей зубьев шевера составляют с соответствующими боковыми поверхностями калибрующей части углы β.
206
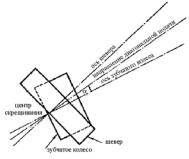
Такая конструкция шевера позволяет снимать весь припуск за один рабочий и один обратный (калибрующий) ход стола, осуществляемый при постоянном расстоянии между осями шевера и колеса. Шеверы для удаления всего припуска за один рабочий и один обратный ход выпуска- ются отечественными инструментальными заводами. В ря- де случаев специальные шеверы можно изготовить путем перешлифовки стандартных шеверов шириной 20–25 мм. При этом заборная и режущие части должны иметь не ме- нее 4 режущих кромок каждая.
Производительность обработки при шевинговании за один проход увеличивается в 2–3 раза благодаря сокраще- нию количества циклов и исключению радиальных пере- мещений стола с обрабатываемым колесом, неизбежных при шевинговании стандартными шеверами. Стойкость та- ких шеверов в 3 раза выше стойкости стандартной конст- рукции благодаря увеличению числа режущих кромок, од- новременно задействованных в работе, и уменьшению на-
вингования с диагональной |
|
||||
подачей |
предусматривает |
Рис. 9.20. Схема шевингования |
|||
поступательное |
перемеще- |
||||
с диагональной подачей: |
|||||
ние обрабатываемого зубча- |
|||||
1 – ось шевера; 2 – направление |
|||||
|
|
|
|
||
того колеса не параллельно |
диагональной подачи; |
||||
его оси, а под углом α, рав- |
3 – ось зубчатого колеса; |
||||
4 – центр скрещивания; |
|||||
грузки на каждую из них. |
|
||||
Кроме |
того, |
калибрующие |
|
||
зубчики не участвуют в сре- |
|
||||
зании основного |
припуска |
|
|||
(см. рис. 9.19, в). |
|
|
|||
Достаточно |
широко |
|
|||
используемый |
метод ше- |
|
ным 35–40° (рис. 9.20). |
5 – зубчатое колесо; 6 – шевер |
|
|
|
207 |
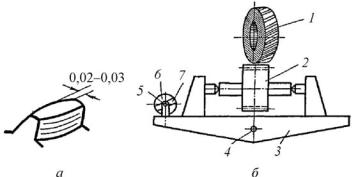
Вследствие этого уменьшается длина хода, и число проходов можно принять меньшим, чем при обычном ше- винговании (с продольной подачей), что в целом значи- тельно сокращает время обработки. Время шевингования одного зуба с модулем 2–3 мм при продольной подаче со- ставляет 2–3 с, а при диагональной подаче – около 1 с.
На автомобильных и тракторных заводах шевинго- ванием иногда образуют зубья, концы которых на 0,02– 0,03 мм тоньше середины, что придает им бочкообразную форму (рис. 9.21, а). Такая форма зубьев обрабатываемого шевером 1 зубчатого колеса 2 получается посредством применения на шевинговальных станках специального качающегося приспособления (рис. 9.21, б).
Рис. 9.21. Шевингование бочкообразного зуба: а – форма бочко- образного зуба; б – шевингование в качающемся приспособле- нии: 1 – шевер; 2 – обрабатываемое зубчатое колесо;
3 – основание; 4 – ось основания; 5 – палец; 6 – диск с наклонным пазом; 7 – наклонный паз
На столе станка устанавливается основание приспо- собления, на оси 4 которого посредством пальца 5 качается плита 3. Палец 5 при продольном передвижении стола пе- ремещается по наклонному пазу 7 диска 6, закрепленного на неподвижном кронштейне и установленного под тре- буемым углом.
208
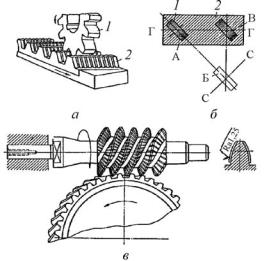
Поскольку шевингование способствует значительному повышению точности зубчатых колес и высокой производи- тельности, его применяют не только в массовом и крупносе- рийном производстве, но и в серийном и даже в мелкосе- рийном.
Если специальных станков для шевингования нет, то можно приспособить вертикально-фрезерный станок с по- воротной фрезерной головкой, обеспечивающей образование угла скрещивания осей шевера и зубчатого колеса.
По второму способу шевингование производится при помощи специального инструмента – шевер-рейки
(рис. 9.22, а), состоящей из отдельных зубьев с канавками, образующими режущие кромки на стороне каждого зуба.
Рис. 9.22. Шевингование шевер-рейкой и шевер-червяком:
а– шевер-рейкой; б – схема скольжения шевер-рейки по зубьям зубчатого колеса; в – шевер-червяком червячного колеса
Впроцессе обработки стол станка с закрепленной на нем шевер-рейкой имеет возвратно-поступательное движение. Так же как и обычный (дисковый) шевер, шевер-
209
рейка изготовляется с наклонными зубьями для обработки зубчатых колес с прямым зубом; для обработки зубчатых колес с косым зубом (с углом наклона около 15°) шевер- рейка имеет прямые зубья, расположенные перпендикуляр- но оси; в том и другом случае образуется винтовое зубчатое зацепление с обрабатываемым зубчатым колесом; для об- работки одного зубчатого колеса необходимо произве- сти 15–20 двойных ходов стола. На рис. 9.22, б показана схема, поясняющая осуществление продольного скольже- ния зубьев шевер-рейки по зубьям зубчатого колеса.
Если обрабатываемое зубчатое колесо 1 свободно ка- тить по шевер-рейке 2 из положения А, то оно должно пе- реместится в положение Б. Но так как зубчатое колесо и шевер-рейка представляют собой как бы винтовую зубча- тую пару со скрещивающимися осями, то колесо передви- гается не в положение Б, а в положение В. В результате создается относительное скольжение зубьев обрабатывае- мого зубчатого колеса и шевер-рейки, определяемое отрез- ком между положениями зубчатых колес Б и В. При этом режущие кромки шевера срезают стружку с поверхности обрабатываемых зубьев колеса.
После каждого хода стола зубчатое колесо перемеща- ется вниз; таким образом, осуществляется вертикальная подача в пределах 0,025–0,04 мм.
Шевингование (дисковым шевером и шевер-рейкой) обычно производят с СОЖ – сульфофрезолом или маслом индустриальным И-20А. По причине высокой стоимости инструмента, плохой вымываемости стружки из зубьев ше- вер-рейки, невозможности обработки бочкообразных зубь- ев шевингование шевер-рейкой не имеет широкого распро- странения.
Шевингование зубьев производится до термической обработки закаливаемых зубчатых колес. Часть зубчатых колес после шевингования поступает в термическую обра-
210