
книги / Процессы обработки заготовок. Хонингование
.pdf3.2. Хонингование цилиндрических отверстий большой протяженности
При хонинговании глубоких цилиндрических отверстий большой протяженности (до 12 000 мм) используют специальные головки, отличающиеся от обычных количеством брусков и наличием дополнительных направляющих устройств в корпусе. Такие хонинговальные головки в зависимости от их длины и диаметра имеют 2, 3 и более рядов брусков. В каждом ряду от 4 до 16 брусков в зависимости от диаметра хонингуемого отверстия.
Финишную обработку многорядной хонинговальной головкой глубоких отверстий большой протяженности (до 12 000 мм) и диаметром от 100 до 200 мм (рис. 1.16), конструкция которой описана в п. 1.3.1 настоящего пособия, производят в два этапа.
Предварительную обработку отверстия такой хонинговальной головкой осуществляют крупнозернистыми, а окончательную обработку – мелкозернистыми хонинговальными брусками.
На замену хонинговальных брусков (или на смену хонинговальной головки с брусками меньшей зернистости) затрачивается значительное время.
Кроме того, при работе даже крупнозернистыми брусками одной и той же зернистости наблюдается затухание съема металла.
Отечественной и зарубежной промышленностью освоен выпуск хонинговальных головок, позволяющих производить обработку одновременно крупнозернистыми и мелкозернистыми хонинговальными брусками.
Однако при работе такими хонинговальными головками с брусками разной зернистости и с одинаковой протяженностью хонинговальных брусков вдоль оси головки на обработанной поверхности отверстия остаютсяучастки, необработанныемелкозернистымибрусками.
Эти участки имеют более грубую шероховатость по сравнению с остальной обработанной поверхностью отверстия, и на них наблюдается значительный эффект затухания съема металла, что приводит к некоторому снижению производительности обработки.
91
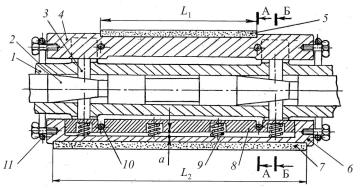
Помимо этого, в хонинговальных головках известных конструкций подпружиненные мелкозернистые хонинговальные бруски при входе в отверстие и при выходе из него подвергаются повышенному размерному износу вследствие их установки на размер, значительно превышающий размер обрабатываемого отверстия.
Это влечет за собой необходимость частой замены изношенных мелкозернистых брускови снижаетпроизводительностьобработки.
В Пермском научно-исследовательском технологическом институте была разработана конструкция хонинговальной головки, лишенная указанных выше недостатков.
На рис. 3.10 представлен продольный разрез хонинговальной головки, позволяющей устранить эффект затухания съема материала и обеспечивающей максимальную производительность обработки при одновременном достижении высокой точности и шероховатости поверхности отверстия.
Рис. 3.10. Продольный разрез хонинговальной головки
Следует отметить, что хонинговальная головка разработанной конструкции может быть изготовлена как однорядной (рис. 3.10), так и многорядной (2- или 3-рядной).
Хонинговальная головка состоит из корпуса 1, в котором размещен шток 2 с разжимными конусами, воздействующими через толкатели 3 на колодки 4 с крупнозернистыми брусками 5, предна-
92
значенными для предварительного хонингования. Колодки 6 с мелкозернистыми брусками 7, предназначенными для окончательного хонингования посредством размещенных в пазах колодок 6 подвижных вставок 8 и упругих элементов 9, кинематически связанных с толкателями 3 и разжимными конусами штока 2. Колодки 4 и 6 удерживаются в осевом направлении штифтами 10, а в радиальном направлении кольцевыми пружинами 11.
Экспериментальным путем были установлены рациональные соотношения конструктивных элементов хонинговальной головки:
L1 – L2 = (0,7 – 4,5) |
D1 |
, |
(1) |
|
К |
|
|
где L1 – протяженность вдоль оси хонинговальной головки крупнозернистых хонинговальных брусков, мм; L2 – протяженность вдоль оси хонинговальной головки мелкозернистых хонинговальных брусков, мм; D1 – диаметр окружности, описанной вокруг крупнозернистых хонинговальных брусков, мм; К – количество колодок крупнозернистых хонинговальных брусков.
a = (0,6 – 1,2) Н1, |
(2) |
где a – величина зазора (мм) между подвижной вставкой и дном паза колодки с мелкозернистым хонинговальным бруском; Н1 – высота нового крупнозернистого хонинговального бруска, мм.
D2 – D1 = (1,3 – 1,8) Н2, |
(3) |
где D1 – диаметр окружности, описанной вокруг крупнозернистых хонинговальных брусков, мм; D2 – диаметр окружности, описанной вокруг мелкозернистых хонинговальных брусков, мм; Н2 – высота нового мелкозернистого хонинговального бруска, мм.
Благодаря выполнению условий выражения (1) обеспечивается перекрытие следов обработки крупнозернистых брусков мелкозернистыми брусками. Выполнение условий выражений (2) и (3) обеспечивает постоянное усилие прижима мелкозернистых брусков, независимо величины износа мелкозернистых и крупнозернистых брусков, и исключает возможность резкого роста нагрузки на мел-
93
козернистые бруски при их входе в отверстие и выходе из него. Благодаря этому износостойкость мелкозернистых брусков существенно увеличивается.
Обработку партии специальных труб (с отверстием диаметром100 Н6 и протяженностью 3,8 м) из стали 38ХН2МЮА хонинговальной головкой описанной выше конструкции (рис. 3.10) прово-
дили на горизонтально-хонинговальном станке модели РТ-620 при режимах: nин = 63 мин–1; nдет = 10 мин–1; S = 6 м/мин; t = 0,006– 0,012 мм/дв. ход.
В качестве СОТС использовали смесь керосина (85 %) и масла индустриального И-20А (15 %).
Хонинговальную головку с тремя колодками крупнозернистых хонинговальных брусков АБХ 125×12×3×6 – АСВ 160/125 – 100 % – МС1 и мелкозернистых брусков АБХ 200×12×3×6 – АСЧ 100/80 – 100 % – В2 – 04 устанавливали на шпинделе станка мод. РТ–620 (узел крепления хонинговальной головки со шпинделем станка на рис. 3.10 не показан).
Механизмом разжима станка хонинговальные бруски приводили в исходное положение, при котором диаметры окружностей, описанных вокруг крупнозернистых хонинговальных брусков 5 и мелкозернистых хонинговальных брусков 7, становились меньше диаметра отверстия трубы. После этого хонинговальную головку вводили в отверстие трубы.
Соответствующим механизмом станка перемещали шток 2 в корпусе 1. При этом конусы штока 2, взаимодействуя с толкателями 3, в результате прямого контакта через вставки 8 и упругие элементы 9 раздвигали колодки 4 и 6 с крупнозернистыми 5 и мелкозернистыми 7 хонинговальными брусками.
Когда диаметр окружности, описанной вокруг крупнозернистых хонинговальных брусков 5, становился равным диаметру обрабатываемого отверстия (крупнозернистые хонинговальные бруски соприкасались и поверхностью отверстия), перемещение штока 2 прекращали. При этом диаметр окружности, описанной вокруг мелкозернистых хонинговальных брусков, был равен диаметру об-
94
рабатываемого отверстия и мелкозернистые хонинговальные бруски 7 были прижаты к поверхности обрабатываемого отверстия с усилием от 0,5 до 0,6 МПа, величина которого зависела от жесткости упругих элементов 9.
После этого включали подачу СОТС, трубе сообщали вращательное, а хонинговальной головке вращательное и возвратнопоступательное движение. Устанавливали протяженность осевого перемещения хонинговальной головки, при котором крупнозернистые хонинговальные бруски 5 имели перебег, равный 1/3 их длины.
Обработку производили с периодической дозированной подачей штока 2 на разжим крупнозернистых брусков 5. Крупнозернистые 5 и мелкозернистые 7 бруски (рис. 3.11) находились в постоянном контакте с обрабатываемой поверхностью отверстия. В процессе заводских испытаний обрабатывали отверстия труб диаметром от 76 до 152 мм (как гладкие отверстия, так и отверстия с винтовыми нарезами шириной 4,7 мм).
Крупнозернистые хонинговальные бруски 5 раздвигали на заданную величину через определенное число двойных ходов хонинговальной головки и производили ими основной съем материала.
Мелкозернистые хонинговальные бруски 7, работая по предварительно хонингованной поверхности отверстия, при каждом проходе окончательно формировали однородный микрорельеф, уменьшали шероховатость и препятствовали процессу затухания съема материала и снижению производительности хонингования.
После достижения требуемого размера обрабатываемого отверстия штоку 2 сообщали перемещение в противоположном направлении. При этом под действием пружин 11 колодки 4 и 6 сближали до выхода крупнозернистых хонинговальных брусков 5 из контакта с обрабатываемой поверхностью отверстия, а мелкозернистые хонинговальные бруски 7 продолжали контактировать с обрабатываемой поверхностью отверстия (рис. 3.12), уменьшая шероховатость обработки.
Через 5–8 двойных ходов хонинговальной головки последовательно выключали вращение детали и хонинговальной головки,
95
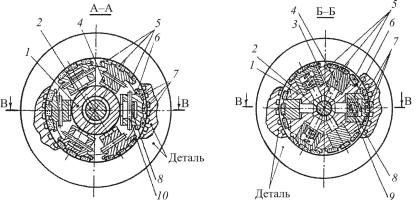
прекращали подачу СОТС, штоку 2 сообщали дополнительное перемещение, при этом под действием пружин 11 колодки 4 и 6 сближали до выхода мелкозернистых брусков из контакта с обработанной поверхностью отверстия, и выводили хонинговальную головку из отверстия.
а |
б |
Рис. 3.11. Поперечный разрез хонинговальной головки: обработка одновременно всеми брусками (а); мелкозернистыми брусками (б)
После этого производили контроль обработанного отверстия по точности и шероховатости.
Производственными испытаниями было установлено, что применение хонинговальной головки позволяет снизить трудозатраты на 16–25 % при стабильном достижении 6-го квалитета точности и шероховатости поверхности менее 0,3 мкм по параметру Ra.
Положительные результаты промышленных испытаний позволили рекомендовать хонинговальную головку описанной выше конструкции для применения в серийном производстве.
96
Контрольные вопросы по разделу 3
1.На каком оборудовании осуществляют хонингование цилиндрических отверстий протяженностью до 400 мм?
2.На каком оборудовании осуществляют хонингование цилиндрических отверстий большой протяженности (до 12 000 мм)?
3.Когда применяют однорядные, а когда многорядные хонинговальные головки?
4.Какие СОТС применяют при хонинговании цилиндрических отверстий?
5.Какую точность и шероховатость поверхности обеспечивает хонингование цилиндрических отверстий?
6.Какие существуют виды окончательной (финишной) обработки, способные полноценно заменить хонингование цилиндрических отверстий большой протяженности (до 12 000 мм)?
97
4.ХОНИНГОВАНИЕ КОНУСНЫХ ОТВЕРСТИЙ
Всовременном машиностроении широкое распространение имеют детали с конусными отверстиями различной протяженности вдоль оси конуса. Короткие конусные поверхности имеют протя-
женность вдоль оси от 0,5 до 200 мм, но встречаются детали,
вкоторых глубокие конусные отверстия имеют протяженность конуса вдоль оси до 8000 мм и более.
Кроме того, встречаются детали с конусными отверстия с двумя и более конусными поверхностями.
Вряде случаев конструкторы предъявляют к выполнению конусных поверхностей повышенные требования по точности, форме и шероховатости поверхности.
Финишную обработку таких отверстий можно осуществлять за счет применения развертывания, тонкого растачивания, хонингования, доводки и полирования.
Следует отметить, что узкоспециализированных хонинговальных станков для хонингования конусных отверстий не создано ни
вРоссии, ни за рубежом.
Хонингование конусных отверстий осуществляют на выпускаемых серийно вертикально-хонинговальных и горизонтально-хонинго- вальных станках с применением специальных хонинговальных головок и/илиспециальных средств техническогооснащения.
4.1. Хонингование коротких конусных отверстий
Хонингование коротких конусных отверстий осуществляют на модернизированных сверлильных, вертикально-фрезерных или на вертикально-хонинговальных станках с выключенным возвратнопоступательным перемещением шпинделя.
Хонинговальную головку устанавливают и жестко закрепляют на шпинделе станка либо связывают вращение хонинговальной головки с вращением шпинделя станка посредством применения со-
98
единения с двумя шарнирами. При этом применяют хонинговальные головки, схематично изображенные на рис. 1.20.
Хонинговальная головка снабжена хонинговальными брусками, расположенными под углом конуса обрабатываемого отверстия.
Протяженность хонинговальных брусков равна протяженности образующей конусного отверстия или незначительно короче.
Хонинговальные бруски в процессе хонингования отверстия совершают возвратно-поступательное движение вдоль образующей конического отверстия. При этом характер возвратно-поступатель- ного движения обеспечивается формой паза пространственного кулачка, имеющего равномерное вращательное движение.
Хонингование коротких конусных отверстий, расположенных непосредственно у поверхности детали, не создает существенных трудностей.
В зависимости от требований конструктора к форме, точности размеров и шероховатости обработанной конусной поверхности применяют абразивные, эльборовые или алмазные бруски, СОТС из керосино-масляной смеси и режимы обработки, аналогичные режимам хонингования цилиндрических отверстий.
Определенные сложности возникают при хонинговании коротких конусных отверстий, расположенных на значительной глубине от поверхности детали. Например, в корпусных деталях первого контура атомных энергетических установок конусные запорные гидравлические клапаны взаимодействуют с узкими уплотнительными поверхностями шириной от 0,7 до 3 мм, расположенными во внутренней полости корпусных деталей на значительном расстоянии (до 465 мм) от торцов корпуса (рис. 4.1).
Корпусные детали энергетических установок, как правило, изготавливают из стали 08Х18Н10Т по ГОСТ 5632–2014 с наплавкой уплотнительной конусной поверхности из кобальтового стеллита В3К (ЦН-2) следующего химического состава: C = 1,6–2,2 %; Si = = 1,5–2,6 %; Cr = 2,5–3,2 %; W = 4,0–5,0 %; Co = 60–65 %; S 0,035 %; P 0,04 %.
99
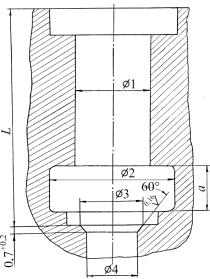
При этом клапанные узлы энергетических установок должны обеспечивать герметичность (полное отсутствие протечек) при давлении парожидкостнойсмеси до110 атмосфер итемпературедо300 °С.
Рис. 4.1. Схема внутренней полости корпуса с горловиной
Размеры внутренних уплотнительных поверхностей, наиболее часто применяемых в корпусных деталях энергетических установок, даны в табл. 4.1.
|
|
|
|
|
Таблица 4.1 |
||
Размеры внутренних поверхностей корпусов с горловиной |
|
||||||
|
|
|
|
|
|
|
|
Наименование |
|
|
Размеры (мм) |
|
|
|
|
конусного |
1 |
2 |
3 |
4 |
L |
|
a |
клапана |
|
||||||
|
|
|
|
|
|
|
|
Ду50 |
60 |
80 |
51,2 |
50 |
275 |
|
50 |
Ду65 |
75 |
100 |
66,5 |
65 |
465 |
|
80 |
Ду80 |
85 |
120 |
82 |
80 |
360 |
|
85 |
100