
книги / Процессы обработки заготовок. Хонингование
.pdfРекомендации по выбору скорости хода хонинговальной головки вдоль оси отверстия приведены в табл. 3.4.
Таблица 3.4
Рекомендации по выбору скорости возвратно-поступательного движения хонинговальной головки в зависимости
от длины ее хода вдоль оси отверстия
Длина хода хонинговальной |
Скорость перемещения хонинговальной |
головки вдоль оси отверстия, мм |
головки вдоль оси отверстия, м/с |
Менее 50 |
От 0,08 до 0,10 |
От 50 до 100 |
От 1,30 до 0,20 |
От 100 до 150 |
От 0,20 до 0,27 |
Свыше 150 |
От 0,27до 0,30 |
Скорость вращения хонинговальной головки зависит от скорости ее возвратно-поступательного движения вдоль оси отверстия и от материала детали. Рекомендации по выбору скорости вращения хонинговальной головки (Vвр) при обработке заготовок из разных материалов в зависимости от скорости ее возвратно-поступатель- ного движения (Vпр) приведены в табл. 3.5.
Число режущих брусков в хонинговальной головке, как правило, выбирают максимальным. Наиболее эффективно исправляют исходные погрешности геометрической формы отверстия хонинговальные головки с четным числом диаметрально расположенных по окружности хонинговальных брусков. В этом случае хонинговальные бруски работают попарно, шток радиальной подачи хонинговальных брусков разгружается от одностороннего действия радиальных сил, отжимающих хонинговальную головку. Отношение режущей поверхности хонинговальных брусков (их протяженность вдоль окружности отверстия) к обрабатываемой поверхности должно составлять от 0,5 до 0,6 при хонинговании гладких отверстий и от 0,8 до 1,0 при хонинговании шлицевых отверстий. Для деталей малой жесткости это отношение необходимо выбирать максимальным.
71
Таблица 3.5
Рекомендации по выбору оптимального отношения Vвр/Vпр при хонинговании отверстий заготовок из разных материалов
Материал заготовки |
Характер хонингования |
Vвр/Vпр |
|
||
Чугун |
Предварительное |
От 3 до |
6 |
||
Окончательное |
От 4 до 10 |
||||
|
|||||
Сталь сырая |
Предварительное |
От 1,5 |
до |
3,0 |
|
Окончательное |
От 2,5 |
до |
5,0 |
||
|
|||||
Сталь закаленная |
После ХТО |
От 3до 5 |
|||
После шлифования |
От 5 |
до |
7 |
||
|
|||||
Бронза |
Однократное |
От 10 |
до |
16 |
При обработке глухих отверстий необходимо предусматривать канавку для выхода (перебега) хонинговальных брусков. Если обрабатываются многорядные отверстия и они расположены близко одно к другому, то следует применять хонинговальную головку с длинными абразивными брусками, чтобы при входе в обрабатываемое отверстие они направлялись одним или двумя предшествующими отверстиями. Для отверстий, отстоящих одно от другого на близком расстоянии, применяют хонинговальные головки с многорядным расположением абразивных брусков.
При обработке шлицевых отверстий следует применять хонинговальные головки с шириной хонинговальных брусков, в 2–3 раза превышающей ширину паза.
Радиальное давление брусков не следует увеличивать более 1,4 МПа при работе алмазными брусками и более 1,0 МПа при использовании абразивных брусков. Желательно чтобы хонинговальный станок имел двухступенчатую систему разжима хонинговальных брусков: в начале операции (первые 2–5 с), когда бруски работают по поверхности отверстия с грубой шероховатостью, радиальное давление должно составлять от 0,3 до 0,4 МПа с последующим автоматическим переключением на повышенное давление.
72
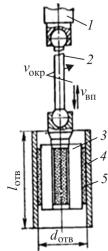
3.1. Хонингование коротких цилиндрических отверстий
Короткое отверстие – это отверстие, протяженность которого вдоль оси соизмерима с протяженностью (длиной) хонинговального бруска. В настоящем пособии под термином «короткое отверстие»
понимается отверстие, у которого протя- |
|
|
женность вдоль его оси не превышает |
|
|
300 мм. Это связано с тем, что протяжен- |
|
|
ность хонинговальных брусков (размер |
|
|
хонинговальных брусков вдоль оси хонин- |
|
|
говальной головки) не должна быть менее |
|
|
50 % протяженности отверстия, а отечест- |
|
|
венная промышленность производит на |
|
|
обезличенного потребителя хонинговаль- |
|
|
ные бруски размером не более 150 мм. |
|
|
Хонингование коротких отверстий |
|
|
осуществляют на вертикально-хонинго- |
|
|
вальных станках. |
|
|
На рис. 3.2 представлена наиболее |
|
|
часто применяемая схема движений хо- |
Рис. 3.2. Схема движений |
|
нинговальной головки при обработке от- |
||
верстия на вертикально-хонинговальных |
при хонинговании |
|
отверстия |
||
станках в заготовке 4. С помощью стерж- |
||
|
||
ня 2 хонинговальная головка 3 посредст- |
|
вом двух шарниров соединена со шпинделем 1 станка, от которого ей сообщаются вращательное и возвратно-поступательное движения.
Разжим (радиальная подача при хонинговании) хонинговальных брусков 5, обеспечивающий съем заданного припуска в отечественных станках, осуществляется автоматически с помощью специального механизма, встроенного в шпиндельную бабку станка, обеспечивая заданное давление на шток хонинговальной головки, конусные поверхности которого воздействуют на колодки хонинговальных брусков, обеспечивая их давление на обрабатываемую поверхность отверстия.
73
Зарубежные вертикально-хонинговальные станки некоторых фирм, например фирмы Sunnen, имеют два специальных механизма. Один механизм автоматически обеспечивает заданное давление на шток хонинговальной головки, конусные поверхности которого воздействуют на колодки хонинговальных брусков, обеспечивая их давление на обрабатываемую поверхность отверстия. Другой механизм обеспечивает дозированное радиальное раздвижение (схождение) хонинговальных брусков на двойной ход шпинделя станка. Хонингование отверстий с автоматическим дозированным радиальным раздвижением хонинговальных брусков обеспечивает точность геометрической формы и размеров обработанного отверстия по 5-му квалитету, а хонингование с автоматически заданным давлением на шток хонинговальной головки обеспечивает 6–7-й квалитет точности.
Для возможности хонингования с дозированным радиальным раздвижением (схождением) хонинговальных брусков на двойной ход шпинделя отечественные вертикально-хонинговальные станки требуют серьезной модернизации.
Процесс хонингования с дозированным радиальным раздвижением (схождением) хонинговальных брусков на двойной ход или через заданное число двойных ходов шпинделя станка можно реализовать на отечественных станках без их модернизации за счет применения ручного механизма раздвижения (схождения) хонинговальных брусков, встроенного в конструкцию хонинговальной головки.
При хонинговании с использованием ручного механизма раздвижения (схождения) хонинговальных брусков, встроенного в конструкцию хонинговальной головки, если припуск под хонингование остается равным припуску под хонингование с обеспечением заданного давления на шток хонинговальной головки, конусные поверхности которого воздействуют на колодки хонинговальных брусков, обеспечивая их давление на обрабатываемую поверхность отверстия, производительность процесса снижается на 12–20 %.
74
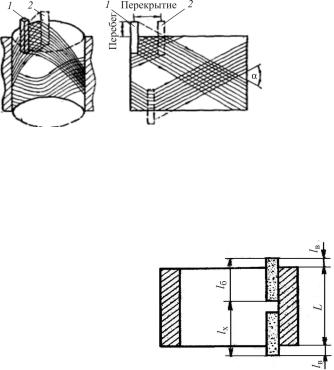
Врезультате совмещения при хонинговании вращательного
ивозвратно-поступательного движений режущие зерна хонинговальных брусков описывают траектории, показанные на рис. 3.3, а на обработанной поверхности образуется характерная сетка рисок.
Рис. 3.3. Траектория движения абразивного бруска при хонинговании: 1 – положение бруска в начале хода; 2 – положение бруска в конце хода; α – угол сетки
На рис. 3.4 приведена схема перемещения хонинговальных брусков при обработке короткого отверстия.
Длину хода хонинговальной головки при обработке коротких отверстий устанавливают равной протяженности отверстия плюс перебег хонинговальных брусков (выход части брусков за пределы отверстия). Обычно перебег хонинговальных брусков за пределы каждой из сторон отверстия составляет 1/3 протяженности хонинговальных брусков.
В настоящее время отечественная промышленность выпускает на обезличенного потреби-
теля хонинговальные бруски длиной от 25 до 150 мм. Эмпирически установлено, что лучшие результаты по точности
геометрической формы отверстия достигаются при хонинговании
75
хонинговальными брусками, длина которых составляет от 0,5 до 0,75 протяженности отверстия (вдоль его оси). При хонинговании коротких отверстий по 7-му квалитету точности допускается применение хонинговальных брусков, длина которых равна протяженности обрабатываемого отверстия.
Геометрическая форма отверстия после хонингования существенно зависит от величины и формы погрешности отверстия до хонингования, величины перебега хонинговальных брусков и времени задержки хонинговальной головки в точках реверсирования воз- вратно-поступательного движения хонинговальной головки.
Увеличение времени задержки хонинговальной головки в точках реверсирования ее возвратно-поступательного движения приводит к образованию седлообразности (корсетности) отверстия. При этом чем больше время задержки инструмента при реверсировании возвратно-поступательного движения хонинговальной головки, тем больше седлообразность отверстия. Кроме того, задержка хонинговальной головки в точках реверсирования возвратно-поступатель- ного движения снижает производительность обработки. В связи с этим организации-производители и наладчики хонинговальных станков как отечественные, так и зарубежные стремятся обеспечить минимальное время задержки инструмента в точках реверсирования возвратно-поступательного движения хонинговальной головки. Как правило, время задержки инструмента в точках реверсирования в современных хонинговальных станках не превышает 1,5 с.
Увеличение перебега от 0,3 до 0,5–0,75 длины хонинговальных брусков также приводит к возникновению седлообразности отверстия. Величина седлообразности увеличивается при увеличении перебега хонинговальных брусков. На рис. 3.5 приведены основные варианты исправления исходной погрешности геометрической формы отверстия заготовки до хонингования за счет настройки хонинговального станка.
При цилиндрической форме исходного отверстия заготовки необходимо установить одинаковый перебег хонинговальных брусков с каждой стороны отверстия. Величина перебега хонинговаль-
76
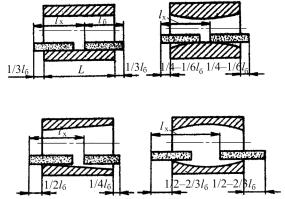
ных брусков должна примерно соответствовать 0,3 длины хонинговальных брусков (см. рис. 3.5, а).
аб
вг
Рис. 3.5. Различные соотношения между размерами отверстий заготовок, длиной хода хонинговальной головки и величиной перебега хонинговальных брусков
Если отверстие до хонингования имеет форму конуса, то отклонение от цилиндричности отверстия можно уменьшить (уменьшить конусность). Для этого необходимо увеличить перебег хонинговальных брусков со стороны меньшего диаметра до 0,5 длины хонинговальных брусков и соответственно уменьшить перебег хонинговальных брусков со стороны большего диаметра до 0,25 длины хонинговальных брусков (см. рис. 3.5, б).
При наличии седлообразности исходного отверстия заготовки перебег хонинговальных брусков следует уменьшить до 0,17–0,25 длины хонинговальных брусков (см. рис. 3.5, в).
В случае бочкообразной формы исходного отверстия заготовки перебег хонинговальных брусков с обеих сторон заготовки следует увеличить до 0,5–0,75 длины хонинговальных брусков (рис. 3.5, г).
Хонингование глубоких высокоточных отверстий протя-
женностью до 300 мм (отношение протяженности отверстия к его диаметру более 5) можно осуществлять на вертикально-хонинго-
77
вальных станках с использованием зарубежного инструмента, например, хонинговальной головкой фирмы Sunnen, показанной на рис. 1.10.
На большинстве машиностроительных заводов финишную обработку сквозных глубоких высокоточных цилиндрических отверстий малых диаметров (менее 11,5 мм) протяженностью до 300 мм осуществляют на отечественном оборудовании после операции сверления ружейными сверлами.
Достаточно распространено хонингование отверстий малых диаметров (от 4,5 до 11,5 мм) с отношением протяженности отверстия к его диаметру более 10 хонинговальной головкой с одним подвижным и двумя неподвижными хонинговальными брусками при вращательном и возвратно-поступательном движении инструмента вдоль оси обрабатываемой заготовки и периодической подачей подвижного хонинговального бруска в радиальном направлении.
Однако при этом погрешности формы отверстия по овальности, огранке, конусности, бочкообразности и седлообразности находятся в пределах допуска 7–8-го квалитета. Кроме того, производительность обработки относительно низка, что связано с затуханием процесса хонингования (уменьшением интенсивности съема металла по мере увеличения продолжительности хонингования).
При использовании хонинговальной головки, в которой ось подвижного бруска располагают с некоторым смещением относительно плоскости симметрии расположения двух неподвижных хонинговальных брусков, размещенных друг относительно друга под углом 90 %, производительность процесса и точность формы отверстия после хонингования повышаются, но недостаточно существенно. Это связано с тем, что смещение подвижного хонинговального бруска относительно оси симметрии расположения двух неподвижных хонинговальных брусков не регламентировано нормативными техническими документами и достаточно часто их назначение не является оптимальным с точки зрения производительности и точности обработки.
78
Эмпирически установлено, что при хонинговании глубоких отверстий малого диаметра в заготовках из вязких, высокопрочных сталей (марок 38ХНМФА; 38ХН2МЮА; 38ХН3МФА и т.п.) неподвижные хонинговальные бруски необходимо выполнять протяженностью от 1,5 до 2,5 раз большей протяженности подвижного хонинговального бруска. Неподвижные хонинговальные бруски на высокопрочной связке должны иметь зернистость на 2–4 степени мельче зернистости подвижного хонинговального бруска. Зернистость неподвижного хонинговального бруска, размещенного в направлении углового смещения оси симметрии подвижного хонинговального бруска (т.е. расположенного впереди другого неподвижного хонинговального бруска по направлению вращения хонинговальной головки), необходимо выбирать на 1–2 степени крупнее зернистости другого неподвижного хонинговального бруска. Выполнение этих условий позволяет избежать затухания процесса хонингования, что приводит к существенному повышению производительности хонингования.
Эмпирически были установлены оптимальные (с точки зрения достижения наибольшей производительности и точности обработки) угол смещения подвижного хонинговального бруска относительно оси симметрии двух неподвижных хонинговальных брусков и величина его выдвижения в радиальном направлении.
На рис. 3.6 представлен график зависимости S = f(β) выдвижения подвижного бруска от угла β отклонения оси симметрии подвижного хонинговального бруска от плоскости симметрии неподвижных брусков. Следует отметить, что при угле β от 5 до 15° численное значение функции S = f(β) приближается к нулю. Это означает, что подвижный брусок в начальный момент обработки выдвигают на определенную величину, сохраняя ее постоянной до полного устранения исходной погрешности формы отверстия в виде овальности, огранки, конусности, бочкообразности, седлообразности.
На рис. 3.7 представлен график зависимости отношения погрешности формы обработанного отверстия к величине погрешно-
79
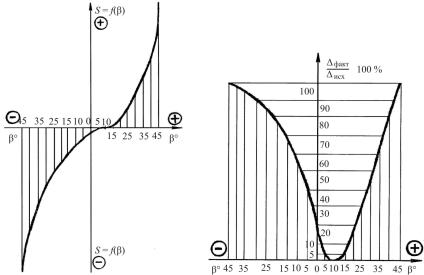
сти формы исходного отверстия от угла β отклонения оси симметрии подвижного хонинговального бруска от плоскости симметрии неподвижных хонинговальных брусков.
Рис. 3.6. График зависимости S = f(β) выдвижения подвижного бруска от угла β отклонения от симметрии подвижного бруска от плоскости симметрии
неподвижных брусков
Рис. 3.7. График зависимости отношения погрешности формы обработанного отверстия к величине погрешности формы исходного отверстия от угла β отклонения оси симметрии подвижного бруска от плоскости симметрии
неподвижных брусков
Из анализа графиков (см. рис. 3.6 и 3.7) следует, что выполнение угла β в диапазоне от 5 до 15° обеспечивает погрешность обработанного отверстия не более 5 % от величины погрешности исходного отверстия.
При выполнении хонинговальной головки с расположением оси симметрии подвижного хонинговального бруска со смещением относительно плоскости симметрии неподвижных хонинговальных брусков под углом β в диапазоне от 9 до 11° величина погрешности
80