
книги / Процессы обработки заготовок. Хонингование
.pdfХонингование конусных ступенчатых отверстий выполняют крайне редко. Более целесообразно как с технической, так и с экономической точек зрения применять отделочное растачивание.
Контрольные вопросы по разделу 4
1.На каком оборудовании производят хонингование коротких конусных отверстий?
2.На каком оборудовании производят хонингование конусных отверстий большой (более 2000 мм) протяженности?
3.Какие СОТС применяют при хонинговании конусных отвер-
стий?
4.Какие движения придают хонинговальным брускам при хонинговании коротких конусных отверстий?
5.Почему нецелесообразно хонинговать конусные ступенчатые отверстия?
6.Какую экономическую точность и шероховатость поверхности можно получить при хонинговании коротких конусных отверстий и конусных отверстий протяженностью более 2000 мм?
121
5. ХОНИНГОВАНИЕ ПЛОСКИХ ПОВЕРХНОСТЕЙ
Первые упоминания о плоском хонинговании как о производительном и точном методе обработки закрытых кольцевых поверхностей взамен методам отделочной обработки свободным абразивом (доводки) в отечественных открытых литературных источниках относятся к началу 80-х годов XX века.
Важнейшей особенностью плоского хонингования является применение алмазных хонинговальных брусков, имеющих высокую стойкость и сохраняющих в течение длительного времени плоскостность предварительно доведенной поверхности режущего диска. Во избежание задиров обрабатываемой поверхности и для облегчения удаления продуктов резания целесообразно применять узкие хонинговальные бруски шириной от 4 до 6 мм и подавать СОТС непосредственно в зону резания, например, по специальным каналам (отверстиям) в хонинговальном диске.
Для обеспечения равномерного износа хонинговальных брусков и равномерного съема материала с обрабатываемой поверхности режущие зерна должны совершать сложные движения, причем след каждого зерна не должен повторяться в течение всего цикла обработки детали.
При выборе режимов обработки при плоском хонинговании (зернистости, связки, концентрации алмазоносного слоя хонинговальных брусков, величины окружной скорости, давления хонинговальных брусков и состава СОТС) можно пользоваться рекомендациями по хонингованию отверстий.
На Стерлитамакском заводе синтетического каучука имени 50-летия Башкирской АССР была разработана и внедрена установка для плоского хонингования кольцевых поверхностей запорной арматуры.
На Стерлитамакском станкостроительном заводе имени В.И. Ленина был спроектирован и изготовлен станок модели 3893. На нем можно осуществлять алмазное хонингование плоских за-
122
крытых кольцевых поверхностей в корпусах задвижек запорной арматуры и корпусах вентилей диаметром от 50 до 250 мм.
На рис. 1.6 приведены внешний вид и кинематическая схема станка 3893, а на рис. 1.7 – планетарный редуктор этого станка. Описание конструкции и принципа работы станка мод. 3893 и планетарного редуктора приведены в п. 1.2 настоящего пособия. Следует отметить, что благодаря планетарному движению диска с алмазными брусками каждое зерно описывает кривую в форме циклоиды, обеспечивая условие, при котором след каждого зерна не повторяется в течение всего цикла обработки.
Однако кроме упомянутых выше плоских кольцевых поверхностей задвижек запорной арматуры в машиностроении применяют целый ряд деталей с плоскими поверхностями, к которым предъявляются высокие требования по точности изготовления и шероховатости обработанной поверхности (точность формы и размеров по 5-му и 6-му квалитету и шероховатость поверхности Ra 0,32 мкм).
К таким деталям относятся клинья с открытой плоской поверхностью клиновых задвижек. В состав клиновых задвижек входят клин и закрывающий механизм.
Клин является наиболее нагруженной деталью клиновой задвижки.
Клинья изготавливают из заготовок двух видов – кузнечной поковки или штамповки.
При использовании штамповки, как правило, сокращается расход металла и уменьшается трудоемкость механической обработки.
В качестве материала применяют высокопрочные вязкие стали. Технологический процесс механической обработки клина состоит более чем из двух десятков станочных и ручных (слесарных) операций. При этом для финишной (отделочной) обработки плоскостей клина обычно применяли доводку или шлифование. Эти процессы финишной обработки обеспечивают задаваемые конструктором высокую точность формы и низкую шероховатость обработан-
ной плоской поверхности.
Однако в процессе доводки происходит шаржирование абразивом плоских поверхностей клина. Это в процессе эксплуатации
123
клиновой задвижки приводит к повышенному износу плоских поверхностей деталей задвижки, сопрягаемых с плоскими поверхностями клина, что влечет за собой нарушение герметичности задвижки со всеми вытекающими из этого последствиями. Кроме того, процесс доводки весьма трудоемок и требует высокой квалификации рабочего-доводчика.
Процесс шлифования обеспечивает более высокую производительность по сравнению с процессом доводки. Однако шлифование сопровождается возникновением высокой температуры (выше температуры структурных превращений – точка Ас1, а иногда выше температуры фазовых превращений – Ас3) в зоне обработки, способствующей возникновению на прошлифованных поверхностях клина дефектов в виде прижогов, микротрещин и высокого уровня внутренних остаточных напряжений. Наличие на обработанных плоских поверхностях поименованных выше дефектов шлифования существенно снижает эксплуатационные характеристики клина, в том числе по параметру износостойкости, что приводит к нарушению герметичности клиновой задвижки.
Одним из направлений совершенствования финишной обработки плоских поверхностей командных деталей является применение в качестве отделочной операции процесса плоского хонингования.
Процесс хонингования является наиболее предпочтительным, так как обеспечивает достаточно высокую производительность обработки, сопоставимую с производительностью процесса шлифования, и вследствие относительно небольшого количества тепла, выделяющегося при обработке, не вызывает появления прижогов, микротрещин и высокого уровня внутренних остаточных напряжений.
Во избежание задира обрабатываемой поверхности заготовки, для облегчения удаления из зоны обработки продуктов хонингования и повышения производительности процесса при хонинговании необходимо применять специальные СОТС.
В процессе хонингования можно применять СОТС на основе керосино-масляной смеси или на водной основе.
124
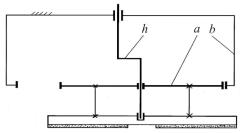
Хонингование позволяет получить достаточно высокую точность обработки (5–6-й квалитет) и низкую шероховатость поверхности (Ra 0,32 мкм).
Процесс хонингования, как правило, применяют при обработке глубоких отверстий, а процессу хонингования плоских поверхностей уделяется значительно меньше внимания.
Для реализации процесса хонингования плоских поверхностей клиньев задвижек было спроектировано, изготовлено и испытано в производственных условиях специальное устройство, его кинематическая схема приведена на рис. 5.1.
Рис. 5.1. Кинематическая схема устройства для хонингования плоскостей клиньев
Хонинговальные бруски устанавливают и закрепляют на нижнем торце диска. Во избежание задира обрабатываемой поверхности и для облегчения удаления продуктов хонингования целесообразно применять относительно узкие хонинговальные бруски шириной от 4 до 6 мм.
Устройство устанавливают на вертикально-фрезерном или вер- тикально-сверлильном станке. В качестве привода водила устройства h используется шпиндель станка. Зубчатое колесо b с внутренним зацеплением устанавливают посредством подшипников качения на верхней части водила h и закрепляют неподвижно относительно корпуса станка. Зубчатое колесо внешнего зацепления a посредством подшипников качения устанавливают на нижней части водила h. Зубчатое колесо внешнего зацепления a вращается
125

относительно водила h совместно с диском с хонинговальными брусками. Необходимое давление хонинговальных брусков на обрабатываемую плоскую поверхность заготовки обеспечивается тарированными пружинами. Для обеспечения равномерного износа хонинговальных брусков и равномерного съема металла с обрабатываемой поверхности режущие зерна хонинговальных брусков должны совершать сложные движения в горизонтальной плоскости, причем след каждого из них не должен повторяться в течение всего цикла обработки. Это условие было учтено при проектировании кинематики устройства для плоского хонингования. Принятая
впредлагаемом устройстве кинематическая схема привода диска с установленными и закрепленными на нем хонинговальными брусками обеспечивает сложную траекторию каждого режущего зерна
вгоризонтальной плоскости, описываемую системой уравнений
|
|
Ri2 ecos2 |
|
|
|
|
|
|
|
|
|
|
|
|
|
|
|
|||||||
X |
|
|
|
|
|
ecos |
|
|
|
|
cos |
|
|
|
|
|
|
|
; |
|||||
|
u |
b |
u |
b |
|
u |
b |
|
||||||||||||||||
|
|
|
|
ah |
|
|
ah |
|
|
|
ah |
|
|
|||||||||||
|
|
|
|
|
|
|
|
|
|
|
|
|
|
|
|
|
|
|
|
|
|
|
||
|
|
|
|
|
|
|
|
|
|
|
|
|
|
|||||||||||
|
Ri2 ecos2 |
|
|
|
|
|
|
|||||||||||||||||
Y |
|
|
|
ecos |
|
|
|
sin |
|
|
|
|
|
, |
|
|||||||||
u |
b |
|
u |
b |
u |
b |
|
|
|
|||||||||||||||
|
|
|
ah |
|
|
|
|
|
|
ah |
|
|
||||||||||||
|
|
|
|
|
|
|
ah |
|
|
|
|
где Ri – текущее расстояние от оси вращения диска с хонинговаль-
ными брусками до единичного зерна; е – эксцентриситет водила (расстояние между осями верхней и нижней частями водила); –
угол поворота диска с хонинговальными брусками; uahb – переда-
точное отношение редуктора устройства.
В зависимости от величины передаточного отношения редуктора устройства uahb траектория движения единичного зерна будет представлять собой кривую, подобную 2-, 3-, 4- или 5-лепестковой «розе» при uahb , равном 2, 3, 4 или 5. На основе графоаналитического исследования траектории движения единичного зерна были установлены рациональные границы передаточного отношения uahb . Пе-
126

редаточное отношение устройства определяется уравнением
ub 1 zb .
ah za
Из условия, что след каждого единичного зерна не должен повторяться в течение всего цикла обработки, в устройстве были приняты следующие параметры передачи: число зубьев Za = 71, Zb = 91, модуль m = 2 мм, эксцентриситет водила h – 20 мм, при этом переда-
точноеотношение передачи составляет uahb 1 |
zb |
1 |
91 |
2,282. |
|
za |
71 |
||||
|
|
|
В этом случае за время обработки одной плоской поверхности заготовки исключается повторение следа движения каждого из единичных зерен.
Производительность процесса хонингования существенно зависит от величины давления хонинговальных брусков на обрабатываемую поверхность. Однако при давлении более 0,3 МПа возникает вероятность задира обрабатываемой поверхности.
Устройство для хонингования плоскостей клиньев клиновых задвижек (сборочный чертеж устройства приведен на рис. 5.2) устанавливают на вертикально-фрезерном станке. Метрический конус или конус Морзе устройства для хонингования плоскостей 1 для передачи крутящего момента от шпинделя станка устанавливают и закрепляют в конусе шпинделя станка.
Фланец конуса устройства 1 посредством пальцев 2 передает крутящий момент валу устройства, состоящему из двух частей с эксцентриситетом е. Этот вал выполняет в устройстве (см. рис. 5.2) функции водила. Верхняя ступень этого вала установлена в корпусе 3 на подшипниках качения 10.
К нижнему торцу корпуса 3 жестко присоединено, например посредством болтового соединения, зубчатое колесо внутреннего зацепления 4.
Верхний торец корпуса 3 жестко связан, например посредством болтового соединения, с корпусом станка, на котором установлено устройство.
127
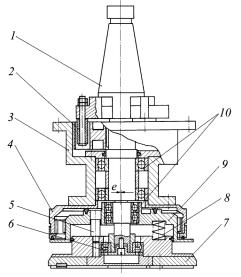
Рис. 5.2. Сборочный чертеж устройства для хонингования плоскостей
На нижней ступени вала – водила устройства, выполненной по отношению к верхней ступени вала с эксцентриситетом е на подшипниках качения, установлено зубчатое колесо внешнего зацепления 9, входящего в зацепление с неподвижным зубчатым колесом внутреннего зацепления 4. На нижнем плече вала устройства в подшипниках качения 6 установлен диск 7, на нижнем торце которого расположены и закреплены хонинговальные бруски. Зубчатое колесо внешнего зацепления 9 имеет возможность вращения на подшипниках качения 10 относительно оси нижнего плеча вала устройства совместно с диском 7 с хонинговальными брусками. Совместное вращение диска 7 и зубчатого колеса внешнего зацепления обеспечивается за счет передачи крутящего момента посредством пальцев 5, установленных в отверстиях диска 7 и зубчатого колеса 9. Давление хонинговальных брусков, установленных и закрепленных на диске 7, на обрабатываемую поверхность заготовки обеспечивается тарированными пружинами 8.
128
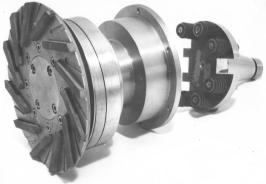
Работает устройство (его внешний вид показан на рис. 5.3) для хонингования плоскостей клиньев клиновых задвижек следующим образом. Устройство устанавливают на вертикально-фрезерном станке, например, модели 6Н80Ш. Конус 1 устройства вставляют в конус шпинделя станка и закрепляют штревелем. Корпус 3 устройства соединяют с корпусом станка, обеспечивая их неподвижность относительно друг друга. На диске 7, например диаметром 160 мм, устройства в двенадцати радиальных пазах прямоугольного сечения закрепляют, к примеру посредством приклеивания, алмазные хонинговальные бруски шириной B = 6 мм и протяженностью
L = 75 мм.
Рис. 5.3. Внешний вид устройства для хонингования плоскостей
Конусу 1 устройства сообщают вращательное движение от шпинделя вертикально-фрезерного станка. Вращение конуса 1 устройства посредством пальцев 2, закрепленных на фланце конуса 1, передает вращение на водило. Нижняя ступень водила с эксцентриситетом e, например равным 5 мм, относительно верхней ступени водила приводит в движение подвижное зубчатое колесо внешнего зацепления 9, которое обкатывается по неподвижному зубчатому колесу внутреннего зацепления 4, жестко закрепленному на нижнем фланце корпуса 3. Вращение зубчатого колеса 9 относительно оси
129
нижней ступени водила передается диску 7 с закрепленными на нем хонинговальными брусками посредством пальцев 5, установленных в цилиндрических отверстиях диска 7 и зубчатого колеса 9. Кроме того, ось диска 7 с закрепленными на нем хонинговальными брусками, установленного на нижней ступени водила посредством подшипников качения 6, получает вращательное движение по круговой траектории с частотой вращения, равной числу оборотов конуса 1 устройства по радиусу, равному величине эксцентриситета e. Включают подачу СОТС и посредством вертикальной подачи станка приводят хонинговальные бруски в соприкосновение с поверхностью обрабатываемой плоскости клина. Необходимое давление хонинговальных брусков, установленных и закрепленных на диске 7, на обрабатываемую поверхность клина обеспечивается тарированными пружинами 8. Кроме того, для обработки поверхности плоскости клина, превышающей диаметр диска 7, столу станка сообщают возвратно-поступательное движение с перебегом, обеспечивающим обработку всей плоскости клина. Обработку производят до получения размера, заданного чертежом. После этого хонинговальные бруски устройства посредством вертикальной подачи станка выводят из соприкосновения с обработанной плоскостью клина и последовательно выключают вращение шпинделя станка и подачу СОТС.
Исследование процесса плоского хонингования с применением описанного выше устройства производили на вертикально-фрезер- ном станке модели 6Н81. Обработку осуществляли на образцах из стали 38ОХНМФА с размерами в плане 130×240 мм. Обработку выполняли на различных режимах с применением различных СОТС и хонинговальных брусков разных характеристик. Применяли 5 разных составов СОТС на керосино-масляной основе и 6 составов СОТС на водной основе.
В результате проведенных испытаний были установлены рациональные условия процесса хонингования плоскостей клина и рекомендованы следующие параметры процесса плоского хонингования.
130