
книги / Процессы обработки заготовок. Хонингование
.pdf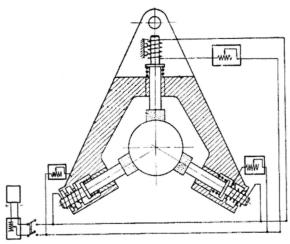
ловке с хонинговальными брусками сообщают продольное перемещение вдоль образующей наружной поверхности со скоростью от 1,66 до 1,00 м/с. В качестве СОТС, как правило, используют смесь из 75–85 % керосина и 15–25 % индустриального масла И-20А.
Впроцессе хонингования станок периодически выключают
иконтролируют размеры детали. При достижении заданных чертежом размеров деталь открепляют и снимают со станка.
Хонингование конических наружных поверхностей вращения,
как правило, осуществляют инструментом с постоянным давлением хонинговальных брусков на обрабатываемую поверхность, а хонингование с нормированной подачей хонинговальных брусков на врезание (с дозированным перемещением брусков) обычно не применяют в связи с высокой трудоемкостью изготовления и сложностью эксплуатации инструмента.
На рис. 2.3 приведена одна из конструкций хонинговальных головок для обработки с постоянным давлением хонинговальных брусков на наружную поверхность вращения заготовки.
Рис. 2.3. Хонинговальная головка с постоянным давлением на наружную поверхность вращения заготовки
61
Хонинговальной головкой подобного типа можно обрабатывать наружные поверхности вращения (как цилиндрические, так и конические) на станках с вращением детали и возвратно-поступательным перемещениемхонинговальнойголовкивдоль осидетали.
Хонинговальная головка выполнена в виде многобрусковой плавающей головки с механическим приводом прижима хонинговальных брусков в виде электромагнитов, сердечники которых жестко связаны с хонинговальными брусками, катушки-соленоиды, последовательно соединенные с подстроечным реостатом, подключены к общему регулируемому источнику. Для упрощения конструкции хонинговальной головки в механизме прижима хонинговальных брусков к обрабатываемой поверхности вместо электромагнитов можно использовать тарированные пружины.
При хонинговании наружных поверхностей вращения с постоянным давлением хонинговальных брусков на обрабатываемую поверхность скорость резания устанавливают от 0,33 до 3,33 м/с, а давление брусков – от 0,3 до 1,35 МПа.
Хонинговальным брускам сообщают продольное перемещение вдоль образующей наружной поверхности со скоростью от 0,03 до
1,66 м/с.
В качестве СОТС, как правило, используют смесь из керосина (от 75 до 85 %) и индустриального масла И-20А (от 15 до 25 %).
После 2–5 минут хонингования станок выключают, контролируют размеры и снимают деталь.
Хонингование с дозированной подачей на врезание несколько снижает производительность труда по сравнению с хонингованием с постоянным давлением хонинговальных брусков на обрабатываемую поверхность, но при этом существенно повышается точность обработки.
Хонингование с дозированным перемещением хонинговальных брусков на врезание обеспечивает точность 6–7-го квалитета и шероховатость поверхности по параметру Ra от 0,16 до 0,63 мкм.
Тонкое хонингование с дозированной подачей хонинговальных брусков на врезание обеспечивает точность 4–5-го квалитета и шероховатостьповерхностипопараметруRa от0,04 до0,16 мкм.
62
Следует отметить, что хонингование наружных поверхностей вращения значительно уступает процессу шлифования по производительности труда, но обеспечивает более высокое качество поверхностного слоя (отсутствие прижогов и трещин).
Процесс хонингования наружных поверхностей вращения обеспечивает производительность труда, равную процессу суперфиниша, но шероховатость поверхности после суперфиниша значительно меньше, чем после хонингования.
Еще одним из существенных недостатков процесса хонингования наружных поверхностей вращения является отсутствие специального оборудования (хонинговальных станков) для хонингования наружных поверхностей вращения.
Хонингование наружных поверхностей вращения применяют крайне редко. Значительно чаще для окончательной (финишной) обработки наружных поверхностей вращения используют тонкое точение, суперфиниш или тонкое (отделочное) шлифование.
Контрольные вопросы по разделу 2
1.Какие движения сообщают детали и хонинговальной головке при хонинговании наружных поверхностей вращения?
2.Можно ли хонинговать наружные поверхности вращения при неподвижной детали?
3.Какие СОТС применяют при хонинговании наружных поверхностей вращения?
4.Каковы преимущества и недостатки хонингования наружных поверхностей по сравнению со шлифованием и по сравнению с суперфинишем?
5.Какую точность и шероховатость поверхности обеспечивает хонингование наружных поверхностей вращения?
63
3. ХОНИНГОВАНИЕ ЦИЛИНДРИЧЕСКИХ ОТВЕРСТИЙ
Финишную обработку цилиндрических отверстий можно осуществлять за счет применения развертывания, протягивания, дорнования, хонингования, доводки или полирования.
Хонингование исправляет исходные погрешности геометрической формы отверстий и существенно повышает их размерную точность, уменьшает шероховатость поверхности, увеличивает несущую способность, сохраняет микротвердость и структуру поверхностного слоя и увеличивает в поверхностном слое остаточные сжимающие напряжения.
Процесс хонингования является наиболее предпочтительным, так как обеспечивает достаточно высокую производительность, не вызывает местных изменений в структуре материала заготовки вследствие относительно небольшого количества тепла, выделяющегося при обработке, и позволяет получить высокую точность
инизкую шероховатость поверхности обработанного отверстия.
Внастоящее время существует возможность хонинговать как цилиндрические отверстия диаметром до 300 мм и протяженностью до 12000 мм, так и конические отверстия диаметром до 300 мм
ипротяженностью до 8000 мм.
Впроцессе хонингования необходимо сохранить положение оси обрабатываемого отверстия после предшествующей операции механической обработки. Это условие определяет способ крепления инструмента и заготовки (детали).
На рис. 3.1 показаны пять основных схем крепления инструмента и заготовки.
Первый способ с жестким креплением хонинговальной головки
иплавающим креплением заготовки в приспособлении (рис. 3.1, а) значительно упрощает конструкцию хонинговальной головки и не требует точного центрирования обрабатываемой заготовки относительно оси шпинделя станка. Конструкция зажимного приспособления также значительно упрощается, так как заготовка не зажима-
64

ется, а только ограничивается от поворота, вызываемого крутящим моментом. При «плавающем» положении заготовки почти полностью исключаются деформации, возникающие при ее зажиме, что повышает геометрическую точность хонингуемого отверстия.
Этот способ можно применять для заготовок, у которых верхняя и нижняя плоские опорные поверхности параллельны друг другу и перпендикулярны оси хонингуемого отверстия.
а |
б |
в |
г |
д |
Рис. 3.1. Схемы установки и закрепления заготовки и инструмента при хонинговании
Второй способ, предусматривающий жесткое крепление хонинговальной головки и обрабатываемой заготовки в плавающем приспособлении (см. рис. 3.1, б), можно применять для обработки мелких и средних заготовок, имеющих одну плоскую опорную поверхность, перпендикулярную оси отверстия.
При хонинговании отверстий относительно малого диаметра и большой глубины (при отношении длины отверстия к его диаметру более 2,5), а также при хонинговании на станках с малой жесткостью шпинделя следует применять одноили двухшарнирное креп-
65
ление хонинговальной головки на шпинделе станка и жесткое крепление обрабатываемой заготовки.
Третий способ предусматривает одношарнирное крепление хонинговальной головки на шпинделе станка (см. рис. 3.1, в), если обеспечивается точное центрирование заготовки (при несоосности шпинделя станка и обрабатываемого отверстия в пределах от 0,03
до 0,05 мм).
Четвертый способ (см. рис. 3.1, г) предусматривает двухшарнирное крепление хонинговальной головки на шпинделе станка и жесткое закрепление заготовки. Его применяют при несоосности шпинделя станка и отверстия заготовки более 0,05 мм.
Пятый способ рекомендуется использовать при обработке глубоких особо точных отверстий, где весьма трудно обеспечить соосность шпинделя станка и отверстия заготовки. Этот способ (см. рис. 3.1, д) предусматривает двухшарнирное соединение хонинговальной головки и применение «плавающего» крепления обрабатываемой заготовки, что существенно усложняет реализацию процесса хонингования, в связи с чем этот способ не нашел широкого применения в промышленном производстве.
В настоящее время существуют вертикально-хонинговальные станки для обработки цилиндрических отверстий протяженностью до 2000 мм и горизонтально-хонинговальные станках для обработки цилиндрических отверстий протяженностью до 12000 мм. Следует отметить, что, возможно, если это потребуется, создание вертикально- и горизонтально-хонинговальных станков для обработки цилиндрических отверстий большей протяженности.
Конструкция хонинговального станка и технологическая оснастка должны обеспечивать цикл хонингования отверстия в следующей последовательности:
–введение хонинговальной головки в отверстие;
–включение подачи СОТС;
–быстрое выдвижение хонинговальных брусков до касания
поверхности отверстия после введения хонинговальной головки в отверстие;
66
–включение вращения и продольного перемещения хонинговальной головки в соответствии с установленными режимами обработки;
–подача хонинговальных брусков с малым радиальным давлением от 0,2 до 0,4 МПа для снятия исходной шероховатости поверхности за 2–3 двойных хода хонинговальной головки;
–подача хонинговальных брусков с рабочим давлением от 1,2 до 1,5 МПа для удаления припуска по гладкой поверхности;
–выключение вращения и продольного перемещения хонинговальной головки и подачи СОТС после достижения заданного диаметрального размера отверстия;
–быстрый отвод хонинговальных брусков перед выводом хонинговальной головки из обработанного отверстия.
При высоких требованиях к шероховатости поверхности после удаления основного объема припуска необходимо осуществить выхаживание (от 2 до 3 двойных ходов хонинговальной головки) при малом радиальном давлении (от 0,2 до 0,4 МПа) хонинговальных брусков.
При хонинговании маложестких тонкостенных деталей (типа гильз) для лучшего исправления отклонения от круглости отверстия целесообразно хонингование вести не с радиальным давлением хонинговальных брусков на обрабатываемую поверхность отверстия,
ас принудительной дозированной радиальной подачей хонинговальных брусков.
Если основная цель операции хонингования сводится к исправлению погрешностей формы отверстия (ГОСТ 24642–81, 24643–81, ГОСТ 2.308–2011), величину припуска устанавливают по разности между исходной и заданной точностью формы отверстия.
После установления общей величины припуска назначают число операций (переходов), распределяя припуск по операциям (переходам) и подбирая характеристику хонинговальных брусков для каждой из операций (переходов). Обработка за несколько операций (переходов) вызвана невозможностью обеспечить интенсивный съем материала заготовки и одновременно получить поверхность
67
с малой шероховатостью хонинговальными брусками одной и той же характеристики. Большой припуск при хонинговании можно снять крупнозернистыми хонинговальными брусками, которые, удаляя материал заготовки, сохраняют шероховатость поверхности, необходимую для самозатачивания хонинговальных брусков. Поэтому основной объем припуска должен быть снят на первой операции (переходе). На чистовых операциях (переходах) припуск должен быть достаточным лишь для удаления шероховатости, полученной на первой операции (переходе). Шероховатость поверхности в пределах от 1,25 до 0,32 мкм по параметру Ra надежно обеспечивается одной операцией (переходом) в серийном и массовом производстве, для получения меньшей шероховатости поверхности хонингование необходимо осуществлять за 2–3 операции (перехода).
В табл. 3.1 приведены рекомендации по выбору припуска, если точность геометрической формы отверстия обеспечивается предыдущей обработкой и необходимо лишь уменьшить шероховатость поверхности.
Таблица 3.1
Выбор припуска при хонинговании отверстий в зависимости от требуемой шероховатости поверхности
Шероховатость поверхности, мкм |
Рекомендуемая величина |
|
исходная |
требуемая |
припуска, мкм |
Rz 10–40 |
Ra 0,63–2,5 |
30–40 |
Rz 10–20 |
Ra 0,32–1,25 |
25–30 |
Ra 0,32–1,25 |
Ra 0,16–0,63 |
15–20 |
Ra 0,16–0,63 |
Ra 0,08–0,32 |
10–15 |
Ra 0,08–0,32 |
Ra 0,04–0,08 |
5–10 |
Рекомендации по выбору припуска и числа операций (переходов) при хонинговании приведены в табл. 3.2.
68
Таблица 3.2
Выбор припуска и числа операций (переходов) при хонинговании отверстий в зависимости от исходного
допуска формы и шероховатости поверхности
Допуск формы |
Шероховатость |
|
|
Ожидаемый |
||||
Номер |
При- |
результат хонин- |
||||||
отверстия, мкм |
поверхности, мкм |
|||||||
|
|
|
|
опера- |
пуск |
гования, мкм |
||
|
|
|
|
ции |
на опе- |
допуск |
шерохо- |
|
исход- |
требуе- |
исход- |
требуе- |
(пере- |
рацию, |
формы |
ватость |
|
ный |
мый |
ная |
мая |
хода) |
мкм |
отвер- |
поверх- |
|
|
|
|
|
|
|
стия |
ности Ra |
|
100–150 |
4–5 |
|
|
1 |
150–100 |
15–20 |
0,63–2,5 |
|
Rz |
|
2 |
20–30 |
6–10 |
0,16–0,63 |
|||
|
|
|
3 |
12–15 |
4–5 |
0,08–0,32 |
||
50–90 |
3–4 |
10–40 |
|
1 |
80–120 |
10–18 |
0,63–2,5 |
|
|
|
2 |
15–25 |
5–9 |
0,16–0,63 |
|||
|
|
|
Ra |
3 |
8–12 |
3–4 |
0,08–0,32 |
|
|
|
|
1 |
50–70 |
8–12 |
0,63–1,25 |
||
|
|
Ra |
0,04–0,32 |
|||||
25–40 |
|
2 |
12–15 |
4–б |
0,16–0,63 |
|||
2–3 |
1,25–2,5 |
|
||||||
|
|
3 |
6–12 |
2–3 |
0,08–0,32 |
|||
|
|
|
||||||
12–15 |
|
|
|
1 |
20–35 |
5–9 |
0,16–1,25 |
|
|
Ra |
|
2 |
10–12 |
2–3 |
0,08–0,32 |
||
|
|
|
||||||
5–12 |
1–2 |
0,63–2,5 |
|
1 |
15–20 |
2–4 |
0,16–0,63 |
|
|
|
2 |
4–6 |
1–2 |
0,04–0,16 |
|||
|
|
|
|
При хонинговании точных отверстий в настоящее время широко применяют алмазные, эльборовые и борозоновые хонинговальные бруски на металлической связке.
Рекомендации по выбору зернистости хонинговальных алмазных брусков даны в табл. 3.3.
Скорость перемещения (скорость хода) хонинговальной головки обычно выбирают в зависимости от длины хода инструмента, которая равна протяженности отверстия плюс два перебега (по одному перебегу с каждой стороны сквозного отверстия).
69

Таблица 3.3
Выбор зернистости хонинговальных алмазных брусков
взависимости от допуска формы отверстия заготовки
иготовой детали
Допуск формы |
|
Шероховатость |
Рекомендации |
|||
Номер |
по зернистости брусков |
|||||
отверстия, мкм |
операции |
поверхности |
при обработке |
|||
|
|
(перехода) |
после хонинго- |
|
|
|
|
|
закаленной |
|
|||
заготовки |
детали |
вания Ra, мкм |
чугуна |
|||
|
|
|
|
стали |
|
|
|
|
1 |
0,63–2,5 |
А 200/160 |
А 160/125- |
|
|
|
|
|
|
125/100 |
|
50–100 |
4–5 |
2 |
0,16–0,63 |
АС 63/50– |
АС 50/40– |
|
50/40 |
40/28 |
|||||
|
|
|
|
|||
|
|
3 |
0,08–0,32 |
АС 40/28– |
АС 20/14– |
|
|
|
20/14 |
14/7 |
|||
|
|
|
|
|||
|
|
1 |
0,63–2,5 |
А 200/100– |
А 160/125– |
|
|
|
160/125 |
125/100 |
|||
|
|
|
|
|||
50–90 |
3–4 |
2 |
0,16–0,63 |
АС 50/40– |
АС 50/40– |
|
40/28 |
40/28 |
|||||
|
|
|
|
|||
|
|
3 |
0,08–0,32 |
АС 28/20– |
АС 20/14– |
|
|
|
20/14 |
14/7 |
|||
|
|
|
|
|||
|
|
1 |
0,32–1,25 |
АС 100/80– |
АС 80/63– |
|
|
|
63/50 |
63/50 |
|||
|
|
|
|
|||
25–40 |
|
2 |
0,16–0,63 |
АС 63/50– |
АС 50/40– |
|
|
40/28 |
40/28 |
||||
|
|
|
|
|||
|
2–3 |
3 |
0,08–0,328 |
АС 28/20– |
АС 20/14– |
|
|
20/14 |
14//7 |
||||
|
|
|
|
|||
|
|
1 |
0,16–1,25 |
АС 63/50– |
АС 63/50– |
|
12–15 |
|
40/28 |
40/28 |
|||
|
|
|
||||
|
2 |
0,08–0,32 |
АС 20/14– |
АС 20/14– |
||
|
|
|||||
|
|
14/7 |
14/7 |
|||
|
|
|
|
|||
|
|
1 |
0,16–0,63 |
АС 40/28– |
АС 40/28– |
|
6–12 |
1–2 |
14/7 |
14/7 |
|||
|
|
|||||
2 |
0,04–0,32 |
АС 14/7– |
АС 14/7– |
|||
|
|
|||||
|
|
7/5 |
7/5 |
|||
|
|
|
|
70