
книги / Процессы обработки заготовок. Хонингование
.pdfформы обработанного отверстия не превышает 1 % от величины погрешности формы исходного отверстия, т.е. погрешность формы обработанного отверстия будет соответствовать требованиям 5-го квалитета точности.
Выполнение угла β за пределами диапазона от 5 до 15° приводит к резкому увеличению погрешности формы обработанного отверстия.
Для повышения производительности и точности хонингования необходимо обрабатываемой заготовке и хонинговальной головке
содним подвижным и двумя неподвижными хонинговальными брусками сообщить относительное возвратно-поступательное и вращательное движение, при этом подвижному хонинговальному бруску сообщать радиальное перемещение, вектор которого располагают под углом к оси симметрии неподвижных хонинговальных брусков в направлении, противоположном направлению вращения хонинговальной головки в диапазоне от 5 до 15°.
На рис. 3.8, а представлен продольный разрез хонинговальной головки для реализации предложенного способа, а на рис. 3.8, б – поперечное сечение этой хонинговальной головки, которая состоит из корпуса 1 с одним подвижным хонинговальным бруском 2, закрепленным в колодке 3 и двумя неподвижными опорами, выполненными в виде хонинговальных брусков 4 и 5. Эти хонинговальные бруски установлены относительно друг друга под углом 90°.
Неподвижные хонинговальные бруски 4 и 5 имеют протяженность вдоль оси головки от 1,5 до 2,5 раз больше, чем протяженность вдоль оси головки подвижного бруска 2.
Подвижный хонинговальный брусок 2 и колодку 3 устанавливают под углом β = 9–11° к плоскости симметрии неподвижных брусков 4 и 5 и имеют возможность радиального дозированного перемещения.
Радиальное дозированное перемещение колодки 3 с хонинговальным бруском 2 осуществляется посредством клина разжима 6, размещенного внутри корпуса 1 и взаимодействующего с колодкой 3 и бруском 2 посредством плоских пружин 7 и винтов 8, связанных
скорпусом 1.
81
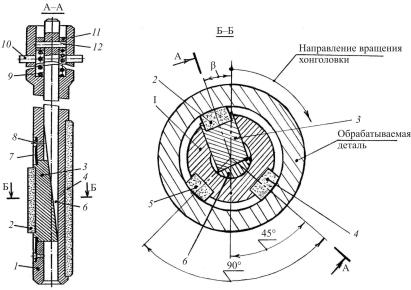
Величина радиального перемещения хонинговального бруска 2 осуществляется при помощи воздействия механизма дозированного перемещения хонинговального станка на клин разжима 6 и перемещения его вдоль оси головки. Хонинговальная головка снабжена возвратной пружиной 9, через кольцо 11 со штифтом 12 воздействующей на клин разжима 6.
а |
б |
Рис. 3.8. Продольный разрез (а) и поперечное сечение (б) хонинговальной головки
Присоединение хонинговальной головки к шпинделю станка осуществляется общеизвестными методами, например, посредством штифтов 10, вводимых в фигурный паз байонетного замка станка.
Зернистость неподвижных хонинговальных брусков 4 и 5 на 2–4 степени меньше зернистости подвижного хонинговального бруска 2, а зернистость хонинговального бруска 4 на 1–2 степени больше зернистости неподвижного хонинговального бруска 5.
82
Обработку необходимо производить на вертикально-хонинго- вальном станке, снабженном механизмом дозированной подачи штока, размещенного в осевом отверстии шпинделя станка.
Использование хонинговальных брусков с различной зернистостью и на различных связках устраняет вероятность возникновения эффекта затухания съема металла, за счет чего увеличивается производительность обработки.
Разная протяженность хонинговальных брусков вдоль оси хонинговальной головки и увеличение их зернистости в направлении вращения хонинговальной головки способствуют уменьшению шероховатости поверхности и повышению точности обработки.
Параметры хонинговальной головки, обеспечивающие достижение наиболее высокой точности и производительности обработки, были подтверждены экспериментально.
Обработка контрольной партии заготовок из стали 38ХНМЮ-А производилась на модернизированном вертикально-хонинговаль- ном станке модели ОФ-38Б с дозированной подачей штока. В качестве СОТС использовали смесь керосина, масла индустриального и олеиновой кислоты (85 % керосина, 12 % масла индустриального И-20А и 3 % олеиновой кислоты).
Обрабатываемые отверстия диаметром 6,35 мм и длиной 120 мм имели исходную погрешность формы (овальность и конусность) в пределах 0,1 мм.
В хонинговальной головке использовали хонинговальные бруски следующих размеров и характеристик: подвижный брусок
35×3×3×1,5 АС4 60/40 – 100 % – М73 (хонинговальный брусок 2)
устанавливали под углом β = 10° к плоскости симметрии двух неподвижных брусков 60×3×3×1,5 АС6 14/10 – 100 % – М1 (хонинго-
вальный брусок 4) и 60×3×3×1,5 АС6 20/14 – 100 % – М1 (хонинго-
вальный брусок 5).
Подвижный хонинговальный брусок 2 посредством механизма дозированной подачи штока станка выдвигали до обеспечения контакта с поверхностью отверстия всех трех хонинговальных брусков. Затем включали подачу СОТС. Вращение головки с частотой
83
200 мин –1 устанавливали в направлении перемещения оси симметрии подвижного бруска в сторону плоскости симметрии расположения неподвижных брусков, а возвратно-поступательное перемещение осуществляли со скоростью 4 м/мин. Подвижному хонинговальному бруску через каждые два двойных хода хонинговальной головки сообщали радиальное перемещение, равное 0,005 мм.
После 20 периодических дозированных радиальных перемещений подвижного бруска осуществляли 3-5 выхаживающих двойных ходов хонинговальной головки без радиального перемещения подвижного хонинговального бруска. Затем выключали вращение головки, подачу СОТС, уменьшали вылет подвижного хонинговального бруска, обеспечивая зазор между хонинговальными брусками и поверхностью отверстия, и выводили хонинговальную головку из отверстия детали.
Замеры опытной партии обработанных деталей показали, что точность обработанных отверстий соответствовала 5-му квалитету, овальность и конусность не превышали соответственно 0,001 и 0,002 мм, а шероховатость обработанных поверхностей не превышала 0,16 мкм по параметру Ra при одновременном повышении производительности обработки на 12–15 %.
На основании результатов производственных испытаний хонинговальная головка описанной конструкции была рекомендована для использования в серийном производстве.
Хонингование глубоких цилиндрических отверстий диа-
метром более 12 мм и протяженностью до 300 мм деталей из вязких, высокопрочных сталей (марки 38ХНМФА; 38ХН2МЮА; 38ХН3МФА) достаточно часто производят на вертикально-хонинго- вальных станках, выпускаемых отечественным станкостроительным заводом имени В.И. Ленина (г. Стерлитамак).
Эти станки имеют девять ступеней частот вращения шпинделя, систему бесступенчатого регулирования скорости возвратно-посту- пательного движения и давления хонинговальных брусков на обрабатываемую поверхность отверстия. Для очистки СОТС в этих станках используют магнитные сепараторы и отстойники.
84
Процесс хонингования на этих станках можно осуществлять
спеременным давлением штока станка на шток хонинговальной головки, взаимодействующий с колодками хонинговальных брусков, увеличенным на первом этапе цикла хонингования и уменьшенным на втором этапе цикла, что способствует уменьшению шероховатости поверхности.
Однако при этом устранение исходной погрешности формы отверстия (овальность, огранка, конусность, бочкообразность, седлообразность), реализуемой с применением хонинговальной головки, обеспечивающей давление на обрабатываемую поверхность хонинговальных брусков за счет применения механизма давления станка на разжимной шток, на первом этапе цикла хонингования происходит весьма медленно. Это приводит к повышению трудоемкости обработки, т.е. к снижению производительности процесса хонингования. Значительно быстрее устранение исходной погрешности формы отверстия на первом этапе цикла хонингования происходит при использовании хонинговальной головки, работающей
сручной дозированной подачей хонинговальных брусков. Недостатком существующих хонинговальных головок с дозированной подачей хонинговальных брусков является невозможность их применения на втором этапе цикла хонингования.
Внастоящее время разработаны хонинговальные головки для реализации цикла хонингования в два этапа (с ручной дозированной подачей хонинговальных брусков на первом этапе цикла и с давлением хонинговальных брусков, обеспечиваемым автоматически механизмом станка подачи хонинговальных брусков по давлению на втором этапе цикла). Эти хонинговальные головки имеют достаточно простую конструкцию, позволяющую повысить ее надежность, а также точность и производительность обработки.
Хонинговальная головка (рис. 3.9) состоит из корпуса 1, разжимного штока с конусом 2, воздействующего через колодки 3 на хонинговальные бруски 4, которые посредством плоских пружин 5, закрепленных винтами 6 на корпусе 1, прижимаются к конусу 2 разжимного штока.
85
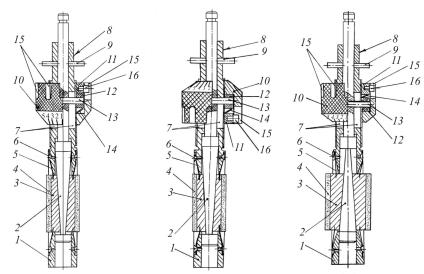
а |
|
б |
|
|
в |
|
Рис. 3.9. Продольный разрез |
хонинговальной головки, |
работающей |
||||
в вертикально-хонинговальном |
станке с |
механизмом |
работы в |
цикле |
||
с переменным |
давлением хонинговальных |
брусков: а |
– |
при |
сжатии |
разжимного штока и снабженной механизмом ручной дозированной подачи с нижним расположением гайки, выполненной в форме стакана; б – при сжатии разжимного штока и снабженной механизмом ручной дозированной подачи с верхним расположением гайки, выполненной в форме стакана; в – при растяжении разжимного штока и снабженной механизмом ручной дозированной подачи с нижним расположением
гайки, выполненной в форме стакана
В корпусе 1 имеется сквозной аксиальный паз 7, посадочное место 8 для установки хонинговальной головки в шпинделе (или переходнике) станка и штифты 9 для установки в пазах байонетного замка. На наружной поверхности корпуса 1 выполнена резьба, на которой расположены гайки 10 и 11, между ними установлена втулка 12 с чекой 13 и упругий элемент 14, например в виде тарельчатой пружины. В боковой стенке гайки 10, выполненной в виде стакана, имеются аксиальные пазы 15. В одном из пазов 15 установлен су-
86
харь 16, связанный с наружной поверхностью гайки 11. Следует отметить, что присоединение сухаря 16 к гайке 11 может быть выполнено любым из известных способов, например посредством винтового соединения.
В качестве упруго элемента 14 может быть использован любой из известных в технике упругих элементов с малой протяженностью в осевом направлении, а в качестве разжимного элемента штока может быть использован не только конус, но и другая поверхность, например клиновая.
Обработку отверстия при помощи описанной выше хонинговальной головки осуществляют следующим образом.
Установленную в шпинделе вертикально-хонинговального станка хонинговальную головку со сведенными колодками 3 с хонинговальными брусками 4 вводят в обрабатываемое отверстие детали. Вращением гайки 10, кинематически связанной посредством паза 15 и сухаря 16 с гайкой 11, осуществляют синхронное вращение гайки 11. Гайки 10 и 11, синхронно перемещаясь в осевом направлении, перемещают втулку 12, которая посредством чеки 13 связана с конусом 2 разжимного штока (или с клиновой поверхностью разжимного штока), и производят разжим колодок 3 с хонинговальными брусками 4. Вращение гайки 10 осуществляют до соприкосновения хонинговальных брусков 4 с поверхностью обрабатываемого отверстия. После этого дальнейшим поворотом гайки 10 с лимбовыми делениями осуществляют дозированный разжим хонинговальных брусков 4 на требуемую величину, включают подачу СОТС, а также вращение и возвратно-поступательное движение шпинделя станка.
Через определенное, заданное технологическим процессом, число двойных возвратно-поступательных ходов хонинговальной головки выключают вращение и возвратно-поступательное движение шпинделя и прекращают подачу СОТС. Поворотом гайки 10 раздвигают хонинговальные бруски на требуемую технологическим процессом величину, включают подачу СОТС, вращение и возврат- но-поступательное движение шпинделя станка. Указанные действия
87
повторяют до устранения исходной погрешности формы отверстия (овальность, огранка, конусность, бочкообразность, седлообразность). После достижения требуемой чертежом точности формы отверстия в пределах допускаемой погрешности включают механизм подачи хонинговальных брусков 4 по давлению станка, который путем создания требуемого осевого усилия на конусе 2 разжимного штока обеспечивает прижим хонинговальных брусков 4 к обрабатываемой поверхности отверстия с требуемым операционным описанием технологического процесса усилием.
Обработку с давлением хонинговальных брусков от механизма давления станка производят до достижения требуемого диаметрального размера отверстия.
По достижении требуемого чертежом диаметрального размера отверстия последовательно:
–выключают вращение и возвратно-поступательное движение шпинделя станка;
–выключают давление на разжимной шток хонинговальной головки, а значит и на хонинговальные бруски 4;
–прекращают подачу СОТС и выводят хонинговальную головку из отверстия.
В качестве финишной обработки цилиндрических отверстий
вдеталях из вязких высокопрочных сталей целесообразно применять алмазное хонингование.
Отработку технологии алмазного хонингования цилиндрических отверстий диаметрами от 20 до 125 мм производили при обработке образцов из вязких, высокопрочных сталей (марок 38ХНМФА; 38ХН2МЮА; 38ХН3МФА) на вертикально-хонинговальном станке модели 3К82У, на различных режимах с применением различных СОТС. В качестве инструмента использовали хонинговальные головки описанной выше конструкции с 4, 6 и 8 хонинговальными брусками различных характеристик при обработке отверстий диаметром от 12 до 30 мм и с 6 и более хонинговальными брусками различных характеристик при обработке отверстий диаметром более 30 мм.
88
Эксперименты показали, что в качестве СОТС при алмазном хонинговании можно использовать водный раствор НСК-5, в состав которого входят: натриевые соли кислого гудрона – 30 %; азотнокислый натрий – 2,5 %; тетраборокислый натрий – 2,5 %; триэтаноламин – 2,5 %; остальное вода. Водный раствор НСК-5 обладает хорошими теплоотводящими, смазывающими и антикоррозийными свойствами, но лучшие результаты по параметрам шероховатости поверхности и производительности обработки дает применение в качестве СОТС смеси, в состав которой входят: керосин – 80 %, масло индустриальное И-20А– 15 % иолеиноваякислота – 5 %.
Для усиления моющего действия СОТС целесообразно увеличивать ее подачу и создавать давление от 0,3 до 0,5 МПа.
Для тонкой очистки СОТС целесообразно, помимо магнитных сепараторов и отстойников, использовать бумажные фильтры или центрифуги.
Экспериментально было установлено, что алмазное хонингование целесообразно производить на следующих режимах.
На первом этапе цикла хонингования с дозированной подачей хонинговальных брусков:
–со скоростью резания на хонинговальных брусках (скорость резания зависит от вращения хонинговальной головки) в диапазоне от 0,65 до 1,00 м/с;
–при скорости возвратно-поступательного перемещения хонинговальной головки в диапазоне от 0,15 до 0,40 м/с;
–с периодической ручной радиальной дозированной подачей хонинговальных брусков в диапазоне от 3·10–6 до 10·10–6 м.
На втором этапе цикла хонингования с давлением хонинговальных брусков, обеспечиваемым механизмом станка подачи хонинговальных брусков по давлению:
–со скоростью резания на хонинговальных брусках (скорость резания от вращения хонинговальной головки) в диапазоне от 0,65
до 1,00 м/с;
–при скорости возвратно-поступательного перемещения хо-
нинговальной головки в диапазоне от 0,15 до 0,40 м/с;
89
– с давлением хонинговальных брусков на обрабатываемую поверхность отверстия, плавно изменяющимся от 3,0 до 1,6 МПа на первом проходе цикла и от 1,5 до 0,3 МПа на последнем проходе.
Обработку контрольной партии из 15 заготовок из стали 38ХН2МЮА с отверстием диаметром 32 мм и протяженность 300 мм производили на вертикально-хонинговальном станке 3К82У хонинговальной головкой описанной выше конструкции с 6 хонинговальными брусками 125×8×5×3 АС6 63/50 – 100 % – М73 и подачей СОТС под давлением 0,3 МПа.
В качестве СОТС применяли смесь из 80 % керосина, 15 % масла индустриального И–20А и 5 % олеиновой кислоты.
Обработку на первом этапе цикла хонингования (с дозированной подачей) осуществляли при числе оборотов шпинделя станка, равном 400 об/мин (скорость резания 0,67 м/с), и скорости возврат- но-поступательного перемещения хонинговальной головки, равной 15 м/мин (0,25 м/с). Радиальную дозированную подачу хонинговальных брусков, равную 8 мкм (8·10–6 м), осуществляли вручную через каждые 3 двойных хода хонинговальной головки, повторяя эту процедуру 4 раза.
На втором этапе цикла хонингования включали механизм давления станка на разжимной шток с конусом хонинговальной головки. Обработку производили за 10 двойных ходов хонинговальной головки, плавно уменьшая давление на хонинговальные бруски от 2,0 МПа при первом двойном ходе хонинговальной головки до 0,3 МПа на последнем двойном ходе хонинговальной головки.
За счет уменьшения объема материала, удаляемого на первом этапе цикла хонингования, производительность процесса хонингования (суммарная на первом и втором этапах цикла хонингования) повысилась на 7–10 %.
Контроль отверстий после хонингования показал, что диаметральные размеры отверстий всех деталей опытной партии укладывались в пределы допуска по 5-му квалитету точности. Овальность и конусность отверстий не превышали 2 мкм. Шероховатость поверхности обработанных хонингованием отверстий соответствовала
Ra 0,16 мкм.
90