
книги / Процессы обработки заготовок. Хонингование
.pdf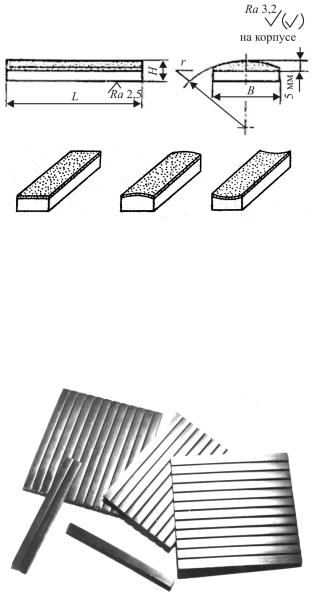
Рис. 1.22. Форма алмазных брусков по СТ СЭВ 24–75 (ГОСТ 25594–83)
При чистовом (отделочном) хонинговании применяют эластичные хонинговальные бруски на связках, содержащих каучук. Эластичные хонинговальные бруски изготавливают в виде блоков, которые затем разрезают на отдельные бруски. Внешний вид блоков и отдельных эластичных алмазныхбрусковприведен нарис. 1.23.
Рис. 1.23. Блоки и отдельные эластичные алмазные бруски
51
Эти бруски применяют при отделочном хонинговании для обеспечения низкой шероховатости обработанной поверхности при обработке чугуна, сталей, алюминиевых сплавов и ряда других материалов.
Эльборовые бруски – содержат режущие зерна из синтетического сверхтвердого материала – эльбора (боразона). Эльбор имеет вид монокристалла с большим числом отдельных вершин, образующих режущую поверхность. При износе происходит скалывание отдельных частей зерен и образование новых режущих кромок. Кристаллы эльбора без примесей прозрачны, а при наличии примесей могут иметь коричневый, желтый или красный цвет. Твердость эльбора близка к твердости алмаза, а термостойкость значительно (примерно в 2 раза) выше, чем у алмаза. Кроме того, кристаллы эльбора обладают высокой устойчивостью при воздействии на них агрессивных сред.
Хонинговальные эльборовые бруски по конструкции аналогичны алмазным брускам, а их характеристика содержит те же параметры. Эльборовые бруски, их формы и размеры регламентиро-
ваны ГОСТ 28734–90.
Для промышленного применения производят эльбор (боразон) трех марок: БО – обычной прочности, БП – повышенной прочности, БВ – высокой прочности.
Зерна эльбора классифицируют аналогично алмазным порошкам, но при обозначении зернистости эльбора добавляют буквенный индекс Л.
В зависимости от размера зерен, методов их получения и контроля порошки эльбора разделены на три группы: шлифзерно – зернистость от Л 315/250 до Л 200/160; шлифпорошки – зернистость от Л 160/125 до Л 50/10; микропорошки – зернистость от ЛМ 40/28 до ЛМ 5/3.
Первые две группы получают путем просеивания, а порошки третьей группы – с использованием жидкости и контролем зернового состава микроскопическим методом.
52
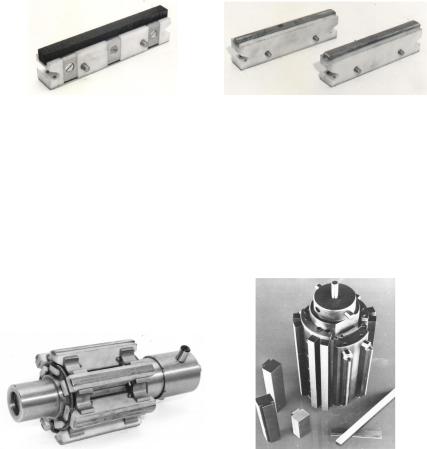
Хонинговальные бруски закрепляют в колодках хонинговальных головок несколькими способами. Наиболее часто применяют приклеивание хонинговальных брусков к колодкам. Возможно механическое крепление хонинговального бруска на колодке (рис. 1.24, а) или крепление хонинговального бруска на колодке путем запрессовки его в колодку из пластической массы (рис. 1.24, б).
а |
б |
Рис. 1.24. Крепление хонинговального бруска: а – механическое; б – на колодке путем запрессовки его в колодку из пластической массы
Установка колодок с хонинговальными брусками в корпус головки показана на рис. 1.25 (удержание от выпадения с помощью пружин).
Значительно реже колодки с хонинговальными бруска устанавливают в корпусе хонинговальной головки посредством ласточкиного хвоста (рис. 1.26).
Рис. 1.25. Установка колодок |
Рис. 1.26. Установка колодок |
с брусками в хонинговальной |
с хонинговальными брусками |
головке |
с ласточкиным хвостом |
53
1.4. Состав СОТС, используемых при хонинговании
1.4.1. Составы СОТС, применяемые при хонинговании
Состав СОТС необходимо выбирать с учетом характеристик обрабатываемого материала и хонинговальных брусков и требований к качеству обработанной поверхности.
Хонингование происходит при большой площади контакта поверхности хонинговальных брусков с обрабатываемой поверхностью заготовки. При обработке без применения СОТС резко возрастает сила трения, а на обрабатываемой поверхности возникают задиры. Это обусловливает недопустимость обработки хонингованием без применения СОТС.
СОТС при хонинговании выполняет смазывающее, охлаждающее и вымывающее действие (удаление микрочастиц срезанного материала и отходов хонинговального бруска), что должно снижать трение и предотвращать адгезионное схватывание абразивных частиц с обрабатываемым материалом заготовки.
Охлаждающие свойства СОТС при хонинговании не так важны, как при шлифовании, в связи с тем, что хонингование происходит при относительно низких температурах порядка 50 °С.
Основная задача СОТС при хонинговании – проникать непосредственно в зону контакта хонинговальных брусков с обрабатываемой поверхностью заготовки и за счет вымывающего действия обеспечивать снижение трения и предотвращение адгезионного схватывания режущих зерен с материалом заготовки.
Наилучшей проникающей и вымывающей способностью обладает керосин, но его пары легко воспламеняются, что делает невозможным его применение в качестве СОТС при хонинговании из-за требований пожарной безопасности. Для снижения вероятности возгораний с учетом требований пожарной безопасности в настоящее время при хонинговании широко применяют в качестве СОТС не керосин, а керосино-масляные смеси. Наиболее широко используют СОТС на основе керосина с добавлением 10–25 % минерального масла (например, масла индустриального И-20А), олеиновой кислоты ли-
54
бо скипидара. Однако добавка в керосин минеральных масел снижает производительность процесса хонингования и полностью не исключает опасностивозгоранияпаровкеросина и возникновения пожара.
Поэтому уже на протяжении более четырех десятилетий ведутся работы по созданию СОТС, не содержащих керосина, но обеспечивающих такие же производительность и качество поверхности. В качестве заменителей керосино-масляных смесей предлагают использовать водные растворы и водно-масляные эмульсии следующих составов, % по массе:
1-й состав СОТС:
–натриевое жидкое стекло – 3–6 %, нитрит натрия – 0,3–0,5 %, сульфит натрия – 0,2–0,4 %, вода – остальное;
–хлорированный парафин – 8 %, тринатрийфосфат – 0,5 %, триэтаноламин – 2 %, нитрит натрия – 4 %, неионогеновый смачиватель – 3,5 %, вода – остальное.
2-й состав СОТС: продукт взаимодействия гидроксида натрия
сжирными кислотами в среде оксиэтилированных 6 и 10 молями оксида этилена моноизононилфенолов – 0,2 %, триэтаноламин – 0,3 %, сода кальцинированная – 0,05–2,5 %, тринатрий-фосфат – 0,05–2,5 %, бактерицидная присадка – 0,1–2,5 %; противопенная присадка – 0,001–1,0 %, вода – остальное.
3-й состав СОТС:
–триэтаноламин – 0,4–1,2 %, бура – 0,2–0,6 %, этиленгликоль –
0,15–0,45 %, глицерин – 0,15–0,45 %, вода – остальное;
–сульфатное мыло – 0,6–1,0 %, легированное масло – 0,9– 1,5 %, этиленгликоль – 0,75–1,25 %, триэтаноламиновое мыло олеи-
новой кислоты – 0,22–0,37 %, смачиватель ОП-7 – 0,15–0,25 %,
моющее средство «Лабомид-205» – 0,15–0,25 %, триэтаноламин –
0,22–0,37 %, вода – остальное.
Неплохо зарекомендовала себя в условиях машиностроительного производства хонингования закаленных стальных заготовок СОТС следующего состава, % по массе:
триэтаноламин (ТУ 2423-168-00203335–2007)................. 1,0–5,0 нитрид натрия (ГОСТ 19906–74) ..................................... 0,25–1,0 глицерин (ГОСТ 6259–75) ................................................ 0,25–1,0
55
хлористый кальций (ГОСТ 450–77)................................... |
0,5–2,0 |
смачиватель НБ (ГОСТ 6867–77).............................................. |
0,5 |
вода................................................................................... |
90,5–95,7 |
На некоторых предприятиях машиностроения |
для усиления |
моющего действия СОТС в эту смесь рекомендуют добавить 0,25– 0,6 % нафтенового мыла (ГОСТ 13302–77).
Для хонингования абразивными брусками заготовок из чугуна
применяют СОТС из следующих компонентов, % по массе: |
|
тринатрийфосфат (ГОСТ 201–76).................................... |
0,25–0,6 |
нитрид натрия (ГОСТ 19906–74) ............................................ |
0,25 |
кальцинированная сода (ГОСТ 10689–75)......................... |
0–0,25 |
бура (ГОСТ 8429–77) ........................................................... |
0–0,25 |
Водные растворы и водно-масляные эмульсии, используемые при хонинговании в качестве СОТС, существенно уступают СОТС на керосино-масляной основе по обеспечению качества обработки
ипроизводительности процесса хонингования.
Внастоящее время разработана и находится в стадии исследований СОТС из очищенной фракции сернистой нефти с температурой вспышки 270–350 °С, по эффективности (по мнению авторов разработки) не уступающая керосино-масляной смеси, но менее агрессивная и огнеопасная. Эта СОТС после гидрированной или адсорбированной очистки имеет температуру вспышки в открытом тигле не ниже 125 °С, в то время как хонингование осуществляется при более низких температурах (50–100 °С).
1.4.2.Очистка СОТС и способы ее подачи
взону хонингования
Для стабильного получения требуемой шероховатости поверхности (особенно при отделочном хонинговании) необходимо обеспечить тщательную очистку СОТС от отходов процесса – частиц абразива или алмаза, металла, связующих материалов. При очистке СОТС увеличивается срок службы насосов для подачи жидкости, приспособлений, хонинговальных головок и хонинговальных станков.
56
В настоящее время применяют различные способы очистки СОТС: отстаивание, магнитная сепарация, фильтрация и центробежная сепарация.
Каждый из поименованных выше способов очистки имеет свои недостатки. Например, магнитная сепарация не обеспечивает удаление продуктов износа хонинговального бруска и стружки некоторых материалов. В отстойниках на дно баков осаждаются только крупные частицы, а мелкие попадают в рабочую зону насоса и брусков.
Необходимо использовать комбинированные средства очистки СОТС. Наиболее надежную и достаточно качественную очистку СОТС обеспечивает центробежная сепарация. Однако даже после этой очистки очень желательно осуществлять тонкую очистку СОТС путем фильтрации через бумажный фильтр (бумажное полотенце).
Хонингование должно сопровождаться обильной подачей СОТС в зону обработки. Подача СОТС в зону хонингования свободно падающей струей под давлением 0,03–0,1 МПа (т.е. под действием силы тяжести) является неэффективной. Наиболее целесообразно осуществлять подачу СОТС при хонинговании напорной струей под давлением порядка 2,5 МПа со скоростью порядка 40 м/с. В целях уменьшения разбрызгивания рекомендуется разветвлять поток СОТС: часть потока направлять в виде тонкой напорной струи, а часть – свободным поливом. При подаче СОТС высоконапорной струей наблюдаются следующие недостатки: трудность обеспечения нужного направления струи СОТС; необходимость тщательной очистки СОТС во избежание засорения сопла; оснащение станка специальной насосной станцией; сильное разбрызгивание СОТС. При хонинговании глубоких отверстий считается перспективной подача СОТС импульсным (ударным) методом с частотой от 10 до 13 Гц и давлением до 1,0 МПа, что повышает производительностьобработкиот2 до2,5 раз.
1.5. Виды процесса хонингования, применяемые на отечественных предприятиях машиностроения
В настоящее время известны и достаточно успешно применяются на отечественных предприятиях машиностроения следующие виды процесса хонингования:
57
–хонингование цилиндрических и конических наружных поверхностей вращения;
–хонингование короткихи глубоких цилиндрическихотверстий;
–хонингование коротких и глубоких конических отверстий;
–хонингование ступенчатых конических отверстий;
–хонингование конических поверхностей отверстий, расположенных в глубине от наружной поверхности детали;
–хонингование плоских поверхностей;
–хонингование поверхностей зубьев зубчатых колес (зубохонингование).
Контрольные вопросы по разделу 1
1.Что представляет собой процесс хонингования?
2.Какие существуют виды хонингования?
3.Каковы преимущества хонингования по сравнению с шлифованием?
4.На каких станках (какой группы) производят хонингование наружных поверхностей вращения, отверстий, плоских поверхностей, боковых (эвольвентных) сторон зубьев зубчатых колес?
5.Каковы преимущества и недостатки хонингования с постоянным давлением штока хонинговального станка?
6.Каковы преимущества и недостатки хонингования с дозированным перемещением режущих элементов хонинговальных инструментов?
7.Какие существуют типы хонинговальных головок?
8.Что используют в хонинговальных головках в качестве режущих (хонингующих) элементов?
9.Как различают хонинговальные бруски по материалу режущих зерен?
10.Какие связки применяют в абразивных, эльборовых и алмазных хонинговальных брусках?
11.Какие СОТС применяют при хонинговании?
58
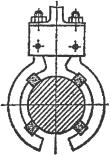
2. ХОНИНГОВАНИЕ НАРУЖНЫХ ПОВЕРХНОСТЕЙ ВРАЩЕНИЯ
Хонингование наружных поверхностей вращения, как цилиндрических, так и конических, производят, как правило, на токарных или суперфинишных станках с выключенным осциллирующим движением, абразивными, алмазными или эльборовыми хонинговальными брусками, закрепленными в разжимных колодках хонинговальной головки (рис. 2.1), установленной на суппорте станка.
Хонингование цилиндрических наружных поверхностей вращения можно осуществлять как с постоянным давлением хонинговальных брусков на обрабатываемую поверхность, так и с нормированной подачей хонинговальных брусков на врезание (с дозированным перемещением брусков). При хонинговании с постоянным давлением хонинговальные бруски прижимают к обрабатываемой поверхности при помощи гидравлических и пневматических устройств и тарированных пружин.
Для повышения точности обработки следует применять хонинговальные головки с механическим дозированным перемещением брусков (нормированной подачей брусков на врезание). Обычно обрабатываемой детали сообщают вращение, а хонинговальной головке – возвратно-поступательное движение вдоль оси вращения детали, но возможны варианты хонингования, при которых деталь неподвижна, а хонинговальной головке придают одновременно вращательное и возвратно-поступательное движения.
К сожалению, хонингование наружных поверхностей вращения с постоянным давлением хонинговальных брусков лишь незна-
59
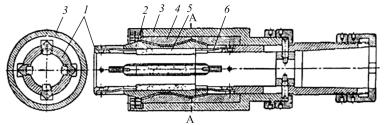
чительно уменьшает, но не устраняет погрешности предшествующей обработки (овальность, конусность, бочкообразность).
Хонингование наружных поверхностей вращения с дозированным перемещением хонинговальных брусков на врезание лишено этого недостатка и практически полностью устраняет погрешности формы (овальность, конусность и бочкообразность), возникшие на операциях, предшествующих хонингованию.
На рис. 2.2 приведена одна из конструкций хонинговальной
головки для хонингования наружных поверхностей |
вращения |
с нормированной подачей хонинговальных брусков на |
врезание |
(с дозированным перемещением брусков). |
|
Рис. 2.2. Хонинговальная головка для обработки наружных поверхностей
В корпусе 1 помещены абразивные бруски 5 в колодках 2. При нажиме на стакан 3 конусы 4 нажимают на конусы колодок 2 с хонинговальными брусками 5 и заставляют их сходиться. Раздвигание колодок 2 производится пружинами 6 при обратном ходе стакана 3. Хонинговальные бруски 5 охватывают обрабатываемую поверхность детали. При обработке на токарных или суперфинишных станках с выключенным осциллирующим движением равномерное вращение придают заготовке (детали), а хонинговальной головке сообщают возвратно-поступательное движение. При этом хонинговальным брускам сообщают радиальную подачу на врезание, как правило, через один возвратно-поступательный ход хонинговальной головки. Скорость вращения на обрабатываемой поверхности устанавливают от 0,33 до 1,66 м/с, а дозированную подачу на врезание на один двойной ход – от 0,005 до 0,015 мкм. Хонинговальной го-
60