
книги / Технология автоматизированного производства лопаток газотурбинных двигателей
..pdf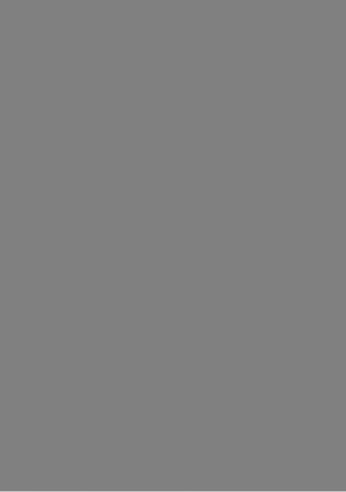
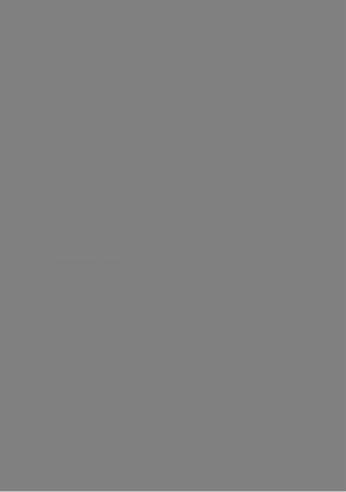
Использование такого оборудования дает возможность значительно сократить цикл технологической подготовки новых изделий (примерно с 2...3 мес до 2...3 нед). Сам же цикл производства турбинных и сопловых лопаток с 1,5.. .2 мес сокращается до 1.. .2 нед.
Для условий единичного и мелкосерийного производств применение данной технологии наиболее целесообразно, причем обработка детали за один установ (когда это возможно) или с небольшим числом переустано вок на единых базах существенно повышает точность обработки благо даря исключению погрешности установки детали.
Рассмотренная технология и соответствующие ей технологические мощности должны быть внедрены на каждом предприятии, изготовляю щем лопатки турбины. Данные мощности составляют технологический минимум предприятия, так как позволяют изготовить в соответствии с требованиями чертежа лопатку турбины любой конструкции. При этом технологический цикл изготовления мотокомплекта из 100... 120 шт. де талей не превышает одной недели, а сроки технологической подготовки сведены к минимуму.
При увеличении потребности выпуска лопаток эта технология усту пает место более мелким операциям, производимым на специальном оборудовании по технологиям, описанным ранее.
Глава 3
ГРУППОВЫЕ ТЕХНОЛОГИИ ОБРАБОТКИ ЛОПАТОК КОМПРЕССОРА
3.1.ОБЩИЕ ВОПРОСЫ
Лопатки компрессора характеризуются большим разнообразием конструкций, широким диапазоном типоразмеров и применяемых мате риалов.
Все многообразие типоразмеров лопаток компрессора целесообраз но разделить на группы по следующим конструктивно-технологическим признакам:
-по длине пера, мм: до 80; 80... 150; 150...300; 300...600; > 600;
-по материалу: коррозионно-стойкие стали, титановые, жаропроч ные и алюминиевые сплавы;
-по конструкции хвостовика: типа ласточкин хвост, шарнирный, призматический и цилиндрический (поворотные лопатки статора);
-по наличию антивибрационных полок.
Перо лопаток компрессора имеет сложную пространственную фор му с профилями сечений, изменяющимися по длине лопатки. Сечения профиля пера лопаток развернуты по его длине друг относительно друга на углы до 90° (рис. 3.1 и 3.2).
Поверхности спинки и корыта пера лопатки могут быть:
-линейчатые, представляющие собой прямые линии, которые пере мещаются в пространстве по определенному закону;
-сложнофасонные, получающиеся при движении какой-либо кри вой по криволинейной образующей.
Точность изготовления пера лопаток обеспечивается при:
•допустимом отклонении точек профиля пера спинки ДПСи корыта ДПКот теоретического положения в пределах 0,06...0,4 мм в зависимости от длины хорды Ь\
•допустимом развороте профилей сечений (допуск на угол закрутки пера Озак) в пределах ±(8... 10)' в зависимости от длины хорды Ь;
•допустимом смещении профилей пера от теоретического положе ния в направлении оси X в пределах 0,1...0,4 мм, в направлении оси У в пределах 0,1.. .0,2 мм в зависимости от длины хорды Ъ\
•отклонении длины хорды АЬ в пределах ±(0,2.. .0,5) мм;
а) |
б) |
в) |
г) |
Рис. 3.1. Примеры конструкций лопаток компрессора:
а- с хвостовиком типа ласточкин хвост; б - с антивибрационными полками;
в- с шарнирным хвостовиком; г - с трапецеидальным хвостовиком
Рис. 3.2. Конструктивные элементы рабочих лопаток компрессора, определяющие точность их изготовления:
а - перо лопатки; б - хвостовик типа ласточкин хвост; в - кольцевой трапецеидальный хвостовики; г - шарнирный хвостовик
•отклонении профилей входной ДПВХи выходной ДПВЫХкромок в пределах 0,03...0,2 мм.
При изготовлении хвостовиков лопаток необходимо соблюдать сле дующие требования:
1)для хвостовиков типа ласточкин хвост:
•размеры посадочных поверхностей по седьмому квалитету и до пуск на угол посадочных поверхностей ±8';
•точность расположения хвостовика относительно профиля пера
±0,15 мм;
•допустимое смещение основания хвостовика относительно выход ной кромки ±0,1 мм;
2) для шарнирного хвостовика:
•точность изготовления отверстия под штифт по шестому квалитету;
•отклонение от перпендикулярности к оси от этого отверстия отно сительно оси лопатки > 0,05 мм на длине 100 мм.
Условия работы лопаток ротора компрессора заставляют предъяв лять к материалам, из которых они изготовляются, требования сохране
ния прочности при температуре до 600 °С и высокой коррозионной стой кости. Для их изготовления широкое применение находят титановые сплавы.
Главное преимущество этой группы материалов перед другими кон струкционными сплавами состоит в том, что высокие механические ха рактеристики и коррозионная стойкость сочетаются в них с малой плот ностью. Титановые сплавы по удельной прочности превосходят боль шинство жаропрочных сталей при температуре 500 °С, что дает большую экономию массы. В эксплуатационных условиях они обладают высокой коррозионной стойкостью в разных климатических условиях и в 3 %-ном растворе поваренной соли.
Теплопроводность титана, равная 7,5 Вт/(м • °С), в 5 раз меньше, чем железа, и в 14 раз меньше, чем алюминия. Во столько же раз ниже и его температуропроводность.
Титановые сплавы удовлетворительно деформируются в горячем состоянии, после чего заготовки нуждаются в отжиге. Эти сплавы обла дают высокой термической стабильностью и не охрупчиваются при дли тельной эксплуатации под напряжением в условиях нагрева до 400.. .550 °С, удовлетворительно обрабатываются различным лезвийным и абразивны инструментом.
3.1. Химический состав титановых сплавов, используемых при изготовлении лопаток компрессора
Марка |
|
|
|
Химический состав, % |
|
|
|||
сплава |
|
А1 |
Mo |
Сг |
Si |
Fe |
С |
Zr |
|
|
|
||||||||
ВТЗ-1 |
5,5... |
7,0 |
2,0...3,0 |
0,8...2,3 |
0,14 |
...0,4 |
0,2...0,7 |
|
|
ВТ8 |
6,0 |
|
|
|
0,2 |
|
|
|
<0,5 |
7,3 |
2,8 3,8 |
|
0,4 |
<0,3 |
< 0,1 |
|
|||
|
5,8 7,0 |
|
|
|
|
|
0,8 2,5 |
||
ВТ9 |
|
|
0,2... |
0,35 |
<0,25 |
|
Наибольшее распространение получили сплавы марок ВТЗ-1, ВТ8, ВТ9, ВТ20. Химический состав и механические характеристики титано вых сплавов приведены в табл. 3.1 и 3.2.
3.2.Механические характеристики титановых сплавов
|
Темпера |
Предел |
Относи |
Относи |
Ударная |
Предел |
|
Марка |
тура ис |
тельное |
тельное |
длитель |
|||
прочности |
удлине |
вязкость |
ной проч |
||||
сплава |
пытания, |
сужение |
|||||
ав, МПа |
ние S, |
ак, кДж/м2 |
ности С|, |
||||
|
Т,°С |
|
% |
\|/, % |
|
МПа |
|
|
|
|
|
|
|||
|
20 |
1000... 1200 |
10 |
30 |
3,0 |
|
|
ВТЗ-1 |
400 |
750 |
|
|
|
680 |
|
|
450 |
650 |
|
|
|
650 |
|
|
20 |
1000... 1200 |
9 |
30 |
|
|
|
ВТ8 |
450 |
750 |
|
|
|
650 |
|
|
500 |
650 |
|
|
|
500 |
|
ВТ9 |
20 |
1050...1250 |
9 |
30 |
|
|
|
500 |
700 |
|
|
|
600 |
||
|
|
|
|
4 — 3991
Кроме титановых сплавов для изготовления лопаток компрессора ранее широко применялись коррозионно-стойкие стали: 13Х14НВФРА, 1Х12Н2ВРФ и ХН35ВТЮ-ВД, а также различные алюминиевые сплавы. Но даже их низкая стоимость и хорошая обрабатываемость по сравнению с титановыми сплавами не позволяют их использовать в современных напряженных конструкциях ГТД [16].
При разработке технологических процессов исходят из обеспечения требуемых точности, формы поверхностей и их относительного располо жения. При этом геометрическая точность изготовления лопаток тесно связана с параметрами качества поверхностного слоя: шероховатостью, величинами и распределением остаточных напряжений, глубиной и сте пенью наклепа, т.е. с теми параметрами, которые во многом определяют сопротивление усталости данных деталей.
Высокие требования к циклической прочности лопаток компрессора обусловливают метод получения заготовок - горячая штамповка. Она может быть изотермической или высокоскоростной, но в любом случае заготовка обладает высокими механическими характеристиками дефор мированного при штамповке материала.
Конструкция лопатки и способ получения заготовки определяют структуру группового технологического процесса. Некоторые из них (наиболее широко применяемые) приведены в табл. 3.3.
Здесь все технологические процессы определены видом заготовки и конструкцией детали.
В первом случае проточная часть лопатки сформирована методом изотермической штамповки окончательно, т.е. в технологическом про цессе проточная часть не подвергается размерной механической обработ ке. Точность изготовления изотермически штампованных лопаток с по следующей термофиксацией 0,05...0,1 мм.
Для ряда конструкций лопаток, используемых в двигателях назем ного применения, эта точность вполне допустима. Для производства та ких лопаток технологический процесс предусматривает только операции механической обработки замка и полировку проточной части с целью получения требуемой шероховатости.
Во втором случае заготовка изготовлена методом горячей штампов ки с припуском 1,0... 1,5 мм на сторону и допуском ^ мм. Конструкция
проточной части обеспечивает к ней свободный доступ профильного ин струмента с обратной кривизной. Такие конструкции предопределяют использование объемной электрохимической обработки при формирова нии проточной части лопаток. Свободный доступ объемных электродов
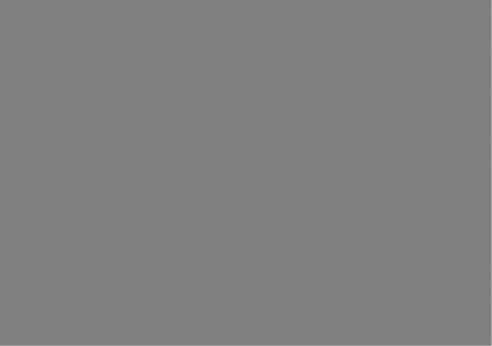
как со стороны спинки, так и со стороны корыта лопатки позволяют в случае выравненных припусков сформировать профиль проточной части лопатки в размер, т.е. без последующей доработки.
В третьем случае наличие антивибрационных полок на проточной части лопатки предопределило использование в качестве основного тех нологического процесса фрезерование проточной части лопатки. При этом наличие антивибрационных полок определяет необходимость фор мирования прямолинейных поверхностей инструментом, имеющим в нужный момент времени очень ограниченную площадь контакта с дета лью (практически точку). Как правило, здесь применяются концевые фрезы со сферической режущей частью.
Вместе с тем, всем приведенным выше технологическим процессам присуще много общих технологических операций, что позволяет провес ти их обобщенный анализ.
3.2.ПОДГОТОВКА ТЕХНОЛОГИЧЕСКИХ БАЗ ЗАГОТОВОК
3.2.1.Входной контроль заготовок
Получаемые заготовки имеют шесть базовых точек, обеспечиваю щих входной контроль заготовок.
Расположение этих точек зависит от конструкции заготовки. Наибо лее распространенные конструкции приведены на рис. 3.3.
В эскизе, показанном на рис. 3.3, а, технологическими базами явля ются три точки на профиле пера (две в сечении А$ и одна в сечении Аг) - установочная база. Опорной базой служит точка 4 на полке замка лопат ки, направляющей - точка 5 на торце хвостовика со стороны входной кромки и точка б на бобышке со стороны профиля пера.
На рис. 3.3, б установочной базой являются три точки на проточной части (1...3); направляющей базой - точки 5 и 6 на технологических бо бышках; опорой - точка 4 на одной из сторон технологической бобышки, расположенной на боковой поверхности замка. В третьем случае (рис. 3.3, в) установочную базу также составляют точки 1...3 на проточ ной части детали; направляющую - точки 5 и б на цилиндрических бо бышках; опорную - точка 4 на торце хвостовика со стороны проточной части.
На заготовительных операциях контролируют профиль пера в сече ниях А | .. .А„. Контроль обычно осуществляют в специальном приспособ лении с помощью жестких шаблонов. На этом этапе проверяют величину