
книги / Технология автоматизированного производства лопаток газотурбинных двигателей
..pdfБолее прогрессивным способом выполнения данных операций явля ется их осуществление на токарных станках с противошпинделем, на пример серии МТ фирмы Mori Seiki (Япония), серии G фирмы Index (Германия), серии TNC фирмы Traub (Германия) и др. Указанные станки имеют противошпиндель с мощностью привода, составляющей 80...90 % от мощности главного привода. Это позволяет в процессе обработки пе реустанавливать деталь и обрабатывать противоположную сторону.
Такие "способности" станков особенно важны в том случае, когда жесткость заготовки невелика. Благодаря наличию противошпинделя возникает технологическая возможность постоянной автоматической переустановки заготовки и симметричного (равномерного) снятия при пуска с каждой стороны заготовки.
Кроме того, данные станки имеют приводной инструмент в револь верной головке, а станки серии МТ фирмы Mori Seiki - во фрезерной го ловке. Вращающий момент привода такого инструмента составляет ~ 100 Н м, что более чем достаточно для выполнения небольших фрезер ных или сверлильных операций (переходов).
После предварительной обработки часть крыльчаток, прежде всего из титановых сплавов, подвергают термообработке - стабилизирующему отпуску.
4.3.МЕХАНИЧЕСКАЯ ОБРАБОТКА ПРОТОЧНОЙ ЧАСТИ
КРЫЛЬЧАТОК
Обработка проточной части лопаток открытых и полузакрытых крыльчаток осуществляется фрезерованием на пятикоординатных много целевых фрезерных центрах с горизонтальным и вертикальным располо жением шпинделя. В НПО "Сатурн" для этих целей используются станки мод. C600U/C800U фирмы Hermle (Германия); UCP710 фирмы Mikron (Швейцария); SX-051, ZT-1000 фирмы Starragheckert (Швейцария) (рис. 4.2).
Крыльчатка монтируется на планшайбу станка на установочную ба зу в виде торца заготовки (базы 1...3), ориентируется в радиальном на правлении по отверстию заготовки с помощью оправки, проходящей че рез ось планшайбы (направляющие базы 4\ 5) и прижимается к торцу планшайбы упором, например гайкой (опорная база б). Такой вид опор ной базы приемлем, если угловое положение заготовки не имеет значения для обработки. Если положение заготовки в угловом положении должно быть жестко задано, то в качестве опорной базы используют отверстие в ступице крыльчатки, а как установочный элемент приспособления - ци линдрический палец (фиксатор).
Рис. 4.2. Схемы базирования и обработки крыльчатки на пятикоординатном обрабатывающем центре с вертикальным
расположением шпинделя
Фотографии рабочей зоны станка, представленные на рис. 4.3, дают полное представление о показанной выше схеме базирования и закрепле ния полузакрытой крыльчатки компрессора при обработке ее проточной части.
Кинематика станка должна обеспечивать следующие перемещения (см. рис. 4.2): заготовка /, установленная на стол II, имеет возможность вращения вокруг оси В на 360°, а также может поворачиваться на качалке III вокруг оси С на угол ±110°; при этом инструмент IV способен пере мещаться вдоль осей X, Y, Z.
Несколько иная схема используется при обработке крыльчаток на машинообрабатывающем центре мод. SX-051 фирмы Starragheckert (рис. 4.4).
Станок имеет горизонтальное расположение шпинделя, который может перемещаться по осям X, Y, Z. Деталь находится на поворотном столе станка, имеющем вертикальную ось вращения (координата В). На столе размещена шпиндельная бабка изделия (ось С). Все координаты управляются одновременно, что позволяет на данном станке осуществ лять объемную обработку криволинейных поверхностей. Однако такая схема менее предпочтительна, чем предыдущая, так как здесь деталь кре пится консольно, причем сила резания не всегда совпадает с силой закре пления детали.
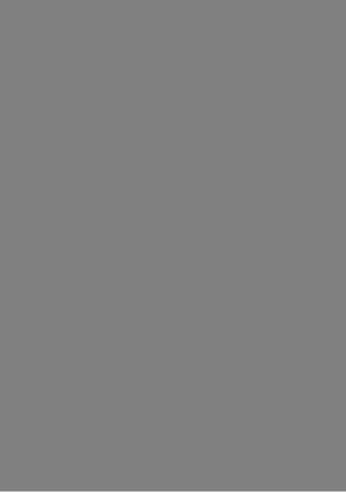
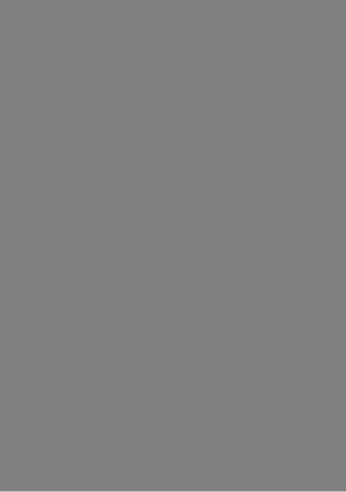
Рис. 4.5. Компоновочная схема крупногабаритного машинообрабатывающего центра с горизонтальным расположением шпинделя
ной головки (до 37...50 кВт) предопределяют возможность обработки на таких станках деталей значительных габаритных размеров и массы.
Так, станок мод. М-НТ 1250/5Т фирмы МН1 позволяет обрабатывать детали диаметром до 1500 мм и массой до 2000 кг. При этом величина вращающего момента на шпинделе составляет порядка 2700 Н м. Соот ветственно, на таком станке обрабатывают крыльчатки для двигателей очень большой мощности (60 МВт и более).
Одновременно частота вращения шпинделя на любом станке для об работки крыльчаток должна регулироваться в широких пределах, обеспе чивая оптимальную скорость резания при выполнении различных пере ходов. Число переходов и, соответственно, используемого при этом ин струмента могут быть значительными. Как правило, обработка проточ ной части включает в себя технологические переходы предварительной, чистовой и окончательной обработки лопаток.
При этом определяющую роль в достижении требуемой точности играет схема снятия припуска. Она диктует такой порядок постепенного удаления металла с заготовки, при котором она постоянно остается в
Рис. 4.6. Схема снятия припуска с моноколеса
уравновешенном состоянии [6, 13]. Так, суммарный припуск заготовки, равный сумме припусков, удаляемых в каждом межлопаточном про странстве, снимается строками на этапах черновой и чистовой обработки (рис. 4.6).
Припуск на черновом этапе удаляется следующим образом.
1. На первом проходе фрезы в каждом межлопаточном пространстве удаляется припуск глубиной /1 и шириной В. При этом значения и В устанавливаются исходя из связи между величиной деформации межло паточного пространства АВ, шириной образующегося паза В и коэффи циентом ослабления сечения заготовки в месте образования пера К = (И -ЬУЪ. Это соотношение определяется на основе расчетной схемы, представленной на рис. 4.7.
Рис. 4.7. Расчетная схема деформации межлопаточного пространства при первом переходе предварительной обработки
Заготовка в виде кольца высотой Л имеет в наружном поверхност ном слое остаточные напряжения ао, обусловленные предшествующей обработкой. Глубина их залегания равна 50. При фрезеровании в заготов ке паза шириной В на глубину гх > 80 происходит перерезание слоя ме талла толщиной 80 с распределенными в нем остаточными напряжения ми. При этом нарушается уравновешенность сил в материале кольца (за готовки), появляются силы F и моменты М, приложенные к границам паза глубиной и и шириной В, что приводит его к деформации на вели чину ЛВ.
Исходя из этих представлений, относительные величины деформа ции ДВ, ширина В и глубина и прорезаемого паза связаны соотношением вида
(4.1)
где Е - модуль упругости обрабатываемого материала, МПа.
Из данной зависимости следует, что с уменьшением коэффициента ослабления межлопаточного пространства моноколеса К = (А - /()/Л отно сительная деформация межлопаточного пространства АВ/В увеличивает ся. При гх = 0 и К = 1 отношение АВ/В = 0, при К -> 0 оно стремится к своему максимальному значению. В этом случае необходимым условием обеспечения требуемой точности является назначение такой глубины резания при которой величина отношения АВ/В не превышает задавае мых значений.
После определения соотношения между В и АВ выполняется про резание всех пазов моноколеса, причем в целях уменьшения деформации удаление припуска в каждом межлопаточном пространстве осуществля ется по условиям симметрии, т.е. каждый новый паз прорезается диамет рально по отношению к прорезанному изначально. В этом случае длины поверхностей заготовки, перерезаемых двумя следующими одна за дру гой строками фрезы, одинаковы. Соответственно, и их напряженные со стояния равнозначны.
В результате обработки каждого межлопаточного пространства мо ноколеса на глубину /1 удаляется деформированный слой заготовки, ха рактеризующийся остаточными напряжениями ао и глубиной их залега ния 80. При этом по дну межлопаточного пространства шириной В фор мируется новый деформированный слой с величиной остаточных напря жений <У\ и глубиной залегания 8] (рис. 4.8).
Рис. 4.8. Расчетная схема деформации межлопаточного пространства при втором переходе предварительной обработки
2. На следующем проходе фрезы удаляется припуск глубиной /, на ширину В. При этом, поскольку /, > бь перерезается деформированный слой, характеризующийся остаточными напряжениями Ст|. При перереза нии этого слоя вновь нарушается уравновешенность сил в материале, сформированная на предыдущем проходе заготовки. Возникающая при этом деформация прорезаемого паза АВ, связана с шириной паза В и глу биной перерезаемого слоя соотношением вида
(4.2)
После вычисления по данному соотношению значения в зависимо сти от задаваемого значения ЛВ1осуществляется прорезание всех осталь ных пазов колеса. Затем весь цикл повторяется до тех пор, пока суммар ная глубина прорезаемого паза t не достигнет требуемого значения, по лучаемого суммированием глубин всех проходов фрезы шириной В. В результате прорезания в каждом межлопаточном пространстве пазов ши риной В заготовка моноколеса представляет собой кольцо с выступами и впадинами, по дну которых расположен деформированный слой, сфор мированный при фрезеровании, характеризующемся толщиной 8, и вели чиной остаточных напряжений а, (рис. 4.9).
В+2Ь, |
В+2ЬХ |
I
Рис. 4.9. Расчетная схема деформации межлопаточного пространства при чистовой обработке (фрезерование пера)
3. При чистовой обработке профиля пера лопаток фрезерование ве дется на всю высоту профиля /, значение которой определяет ширину строки. При этом на каждом проходе фрезы увеличивается ширина меж лопаточного пространства В на величину 2Ь\, определяющую глубину снимаемого припуска со стороны спинки и корыта лопатки, возрастает ширина паза, т.е. увеличивается длина деформированного слоя металла заготовки по дну впадины толщиной 5, и нарушается равновесное со стояние заготовки.
Возникающие при этом силы деформации В и моменты М деформи руют образующееся межлопаточное пространство глубиной / и шириной В + 2Ь\ на величину ДЯ,. Соотношение между величиной деформации ДЯ| и шириной образующегося паза после каждого прохода фрезы, форми рующего перо лопатки, определяется выражением вида
(4.3)
После установления величины припуска Ьи снимаемого со стороны спинки и корыта лопаток, в зависимости от задаваемого значения ДЯ1 осуществляется обработка каждого пера, в ходе которой формируются межлопаточные пространства глубиной / и шириной В\ = В + 2Ь\. При этом максимальное отклонение в каждом сечении моноколеса, перпенди кулярного к его оси, равно задаваемой величине деформации ДЯ|.
Затем весь цикл повторяется, т.е. с пера снимается припуск b¡ и т.д., до тех пор, пока размеры межлопаточного пространства по своей ширине не достигнут требуемых значений.
Данная технология обработки моноколес позволяет при их изго товлении обеспечивать одинаковые условия деформирования заготовки при прорезании каждого межлопаточного пространства как при черно вой, так и при чистовой обработке. При осуществлении каждого нового цикла по равномерному удалению слоя металла заготовка принимает равновесное состояние, характеризуемое уравновешенностью ее внут реннего состояния. В конечном счете, это существенно повышает точ ность изготовления моноколес, что позволяет на ряде двигателей исключить операции отделочной обработки, связанные с размерной обработкой.
Наряду с соблюдением описанной технологии обработки моноколес важнейшим аспектом соблюдения технологии является поддержание ре жущего инструмента в одинаковых условиях. При обработке первой и последней лопаток моноколеса режущие характеристики инструмента должны сохраняться одинаковыми. Это обеспечивается путем использо вания при окончательной обработке каждой новой лопатки моноколеса нового инструмента. Таким образом, число режущих инструментов, ис пользуемых при чистовой обработке, должно соответствовать числу ло паток в обрабатываемом колесе.
Предварительная настройка инструмента на размер (длина вылета) осуществляется совместно с используемой оправкой на специальных приборах, например фирмы Nikken (Япония) и др. (рис. 4.10).
Здесь инструмент, помещенный в оправку и представляющий собой инструментальный блок, устанавливают в прибор на посадочный хвосто вик оправки (HSK, SK, Capto). На режущую поверхность инструмента направляют световой луч, под которым оператор перемещает оправку до тех пор, пока режущая кромка не попадет на экране прибора во вписан ный ему размер. Соответствующий длиновой размер инструментального блока вносится в стойку станка.
Балансировку оправок с инструментом, как правило, не проводят, так как обработка крыльчаток из материалов, используемых в производ стве ГТД, ведется с частотой вращения, не превышающей 8000 об/мин; сама инструментальная оправка балансируется при изготовлении, а инст румент изготавляется за один установ, поэтому его ось и ось оправки при установке инструмента на длину не менее трех диаметров сов падают.