
книги / Технология автоматизированного производства лопаток газотурбинных двигателей
..pdf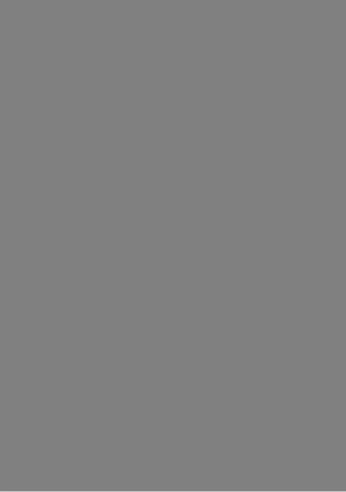
Все эти факторы, с одной стороны, ослабляют поверхностный слой детали, с другой - способствуют тому, что очаг возникновения трещины сдвигается в подповерхностные слои детали. Все это в совокупности с регламентированными знакопеременными нагрузками лопатки и ограни ченным интервалом температур, в которых они действуют (300...400 °С), способствует увеличению циклической прочности лопаток на 20...30 %.
Несмотря на кажущуюся простоту метода, его реализация достаточ но сложна, так как требуется:
1)получить одинаковый по толщине деформированньГ участках лопатки, включая проточную часть и хвостовик.
2)исключить деформации (коробление) лопаток, связанные с после довательным деформированием отдельных участков проточной части лопатки, прежде всего спинки и корыта.
Для снижения этих факторов большое распространение получили гидродробеструйная и гидроабразивная обработка лопаток, где процесс поверхностного упрочнения дробью или абразивом постоянно демпфи руется применением промывочных жидкостей в виде органических или синтетических масел. Эти процессы существенно изменяют цикл пласти ческого деформирования лопаток, загрязняют производство, требуют дополнительных операций промывки деталей.
Вместе с тем, существуют современные дробеструйные установки, которые позволяют жестко регламентировать скорость рабочих тел (дро би); связать перемещение упрочняющего сопла с перемещением проточ ной части лопатки, т.е. гарантировать равномерное перемещение зоны деформации, а также обеспечить одновременную двустороннюю обра ботку спинки и корыта с совпадением пятен обработки с одной и другой сторон.
Такие установки выпускают многие фирмы мира, в частности фир мы Rosier (Германия), Vaporblast (Франция) и др. Выбор той или иной установки определяется геометрическими размерами деталей и объемом их производства. Например, для обработки лопаток длиной до 100... 150 мм целесообразно использовать дробеструйные установки мод. RMBC фир мы Rosier (рис. 3.72).
Работает установка следующим образом. Детали 7 загружаются пар тиями в ленточный сепаратор 4, образующий лоток (провисание между приводными валками) под действием собственной массы и массы загру женных деталей. Дробь б (или абразив) из бункера 2 подается на специ альную турбину 3, вращающуюся со скоростью 100 м/с (не менее).
Рис. 3.72. Схема лотково-ленточной дробеструйной установки мод. НМВС:
1 - рабочая камера; 2 - бункер; 3 - турбина; 4 - ленточный сепаратор; 5 - шнек; 6 - рабочие тела (дробь, абразив); 7- упрочняемые детали
Попадая между лопастями этой закрытой крыльчатки, дробь под действием центробежных сил попадает на детали 7, которые постоянно перемешиваются в сепараторе 4 посредством перемещения ленты, его образующей. В сепараторе 4 выполнены отверстия, позволяющие дроби 6 под действием собственной массы свободно ссыпаться в бункер, откуда она с помощью шнека 5 вновь подается в загрузочный бункер 2.
Установки данного модельного ряда позволяют загрузить детали общей массой 100... 1500 кг; их турбины имеют мощность 1,1...22 кВт, причем число одновременно работающих турбин может быть увеличено до двух. При желании ленточный лоток может быть заменен поворотным столом, что возможно при обработке жестких по конструкции деталей или необходимости их односторонней обработки.
Рис. 3.73. Схема работы установки для очистки дроби:
1 - рабочая среда (дробь, фарфоровые шарики); 2 - заслонка; 3 - сжатый воздух; 4 - выход на фильтр тонкой очистки; 5 - бункер для сбора тяжелых частиц; 6 - отвод грубых тяжелых частиц; 7- бункер очищенных частиц; 8 - патрубки турбины; 9 - сито
Одним из преимуществ установок такого типа является постоянная фильтрация дроби, т.е. отделение расколотых частиц от рабочей среды основной фракции. Поэтому данные установки оснащены устройствами для очистки технологических средств (рис. 3.73).
Работает система очистки следующим образом. Загрязненная рабо чая среда 1 (дробь с металлическими отходами, пылью) попадает в уста новку для очистки и сдерживается во входном патрубке заслонкой 2. За тем порциями при открытии заслонки 2 среда отбрасывается на стацио нарное сито 9. Попадая на него, дробь 1 проходит воздушный поток 5, который уносит более легкие частицы в патрубок фильтра тонкой очист ки 4, а более тяжелые частицы сдувает в бункер для сбора тяжелых час тиц. Дробь 1, оказавшись на сите Р, попадает через него в бункер 7, уже отсортированная по размеру от легких и тяжелых (грубых) примесей.
Функционирует такая система очистки постоянно, что позволяет осуществлять обдувку дробью, имеющей одинаковые размеры, т.е. осво божденной от расколовшихся частиц дроби и посторонних примесей. Наличие этой системы очистки является гарантией равномерного пласти ческого деформирования деталей.
Рис. 3.74. Схема рабочей зоны установки, выпускаемой фирмой УарогЫаз!
Использование установок для обдувки дробью, подобных рассмот ренной выше, целесообразно при обработке достаточно жестких деталей, у которых длина проточной части соизмерима с длиной хорды.
Вместе с тем, большая часть лопаток такому классу не принадлежит и, соответственно, требует иных способов упрочнения. В первую очередь это относится к упрочнению с помощью инжекторных методов подачи дроби. Этот метод позволяет проводить местную обдувку упрочняемой поверхности, размеры которой значительно превышают пятно обдувки. Здесь важно добиться при обдувке равномерного перемещения зоны пла стической деформации по всей упрочняемой поверхности, причем, если последняя имеет переменные кривизну и толщину, нужно обеспечить изменение скорости перемещения зоны пластической деформации в со ответствии с изменениями толщины детали или двустороннюю обработ ку спинки и корыта посредством специальных устройств.
Примером такого устройства является установка фирмы УарогЫав! (рис. 3.74 и 3.75).
Работает установка следующим образом. Оператор устанавливает в рабочую камеру 1 на поворотный стол 2 деталь 3 (лопатку вентилятора). Затем запускает установку по специальной программе, занесенной в сис тему ЧПУ. При реализации этой программы робот 5, расположенный на основании 4, перемещает инжекторные сопла 6. Сопла с помощью специ альной наладки размещаются по обе стороны от проточной части лопатки.
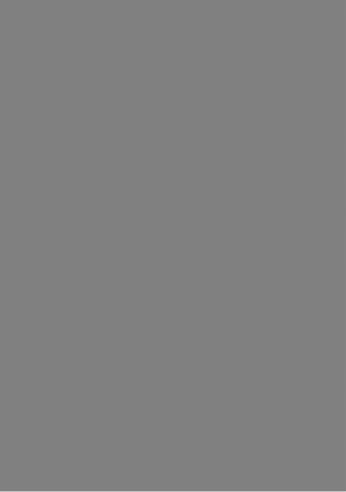

Напыление наносили в три слоя: 1) № + 5 % А1 (производитель по рошка фирма ЭЫгег МеКю); 2) Си + 36 % N1 + 5 % 1п (изготовитель та же фирма); 3) N1 + 20 % С (выпускает порошок фирма "Гипроникель", Рос сия). Толщина каждого слоя 10...50 мкм. Поверхности лопатки, которые не подвергаются плазменному напылению, предварительно изолируют с помощью специальных пленок. Затем деталь устанавливают в приспо собление на некотором расстоянии от излучателя плазменного потока, которое определено в ходе экспериментов по напылению контрольных образцов деталей. Покрытия наносятся в автоматическом цикле.
3.8.2.Операции сварки лопаток компрессора
Современные конструкции лопаток все чаще и чаще включают в се бя сборные конструкции, образованные путем сварки. В первую очередь это относится к приварке поверхностей, которые наиболее быстро изна шиваются в эксплуатации, что, в частности, относится к входной кромке лопаток вентилятора, наиболее подверженной внешним механическим повреждениям, абразивному износу, коррозии. Поэтому у ряда конструк ций таких лопаток входную кромку выполняли в виде носка, устанавли ваемого на проточную часть с помощью заклепок. Это позволяет при ре монте заменить на лопатке только носок и продолжить эксплуатацию де тали. Так, в двигателе мод. ДЗОКУ/КП-154 на лопатках входного направ ляющего аппарата применяют клепаное соединение носка с проточной ча стью. В эксплуатации происходит обрыв заклепок и они попадают в проточ ную часть двигателя, повреждая другие детали. Поэтому в связи с развити ем процессов сварки, в частности электронно-лучевой, в НПО "Сатурн" разработана технология приварки носка вместо клепки (рис. 3.78) [1].
Конструкция свариваемого узла лопатки входного направляющего аппарата (ВНА) состоит из трех деталей: лопатки, носка и технологиче ской планки. При сварке лопатки с носком планку помещают внутрь воз душного канала под стыковое соединение для выведения в нее корня шва. Подготовка свариваемых поверхностей осуществляется в ходе фре зерования кромок лопатки и носка. Шероховатость стыкуемых и приле гающих к стыку поверхностей на ширине > 10 мм должна быть < 3,2 мкм по ГОСТ 2789-73. Механическая обработка лопатки под сварку является операцией, определяющей успешное выполнение процесса сварки. Здесь необходимо обеспечить одинаковую толщину паза под технологическую планку по всей длине входной кромки, а также не допустить тонкой стенки паза (< 3 мм) как со стороны спинки, так и со стороны корыта. Эскиз сборки деталей под электронно-лучевую сварку приведен на рис. 3.79.
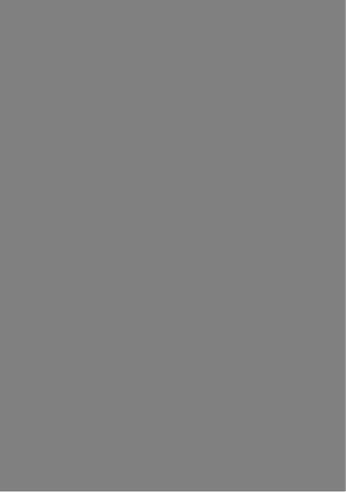
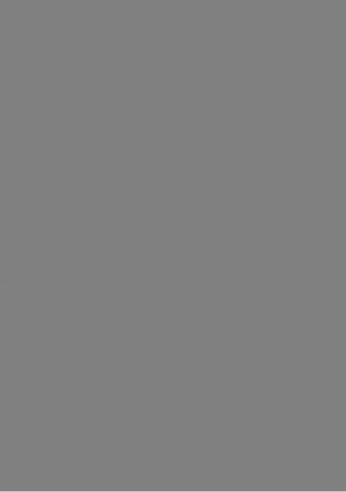