
книги / Технология автоматизированного производства лопаток газотурбинных двигателей
..pdfА о© У
А
Рис. 3.27. Схема движений инструмента и заготовки при фрезеровании профиля пера (вариант 2)
Вращательное движение координат С\ и Сг синхронизировано, что позволяет исключить деформации скручивания заготовки. Более того, закрепление заготовок одновременно со стороны хвостовика и пера ло патки с помощью специальных технологических бобышек дает возмож ность существенно повысить жесткость заготовки и уменьшить ее де формации под действием сил резания. Такую кинематику движений ин струмента и заготовки обеспечивают обрабатывающие центры фирмы 81агга§Ьеске11, например станок НХ-151 (рис. 3.28).
Рис. 3.28. Принципиальная схема станка для круговой обработки лопатки:
1 - шпиндельные бабки круговой подачи заготовки; 2 - суппорт углового перемещения фрезой головки; 3 - фрезерная головка; 4 ...6 - вертикальный, продольный и поперечный суппорты станка соответственно; 7 - станина
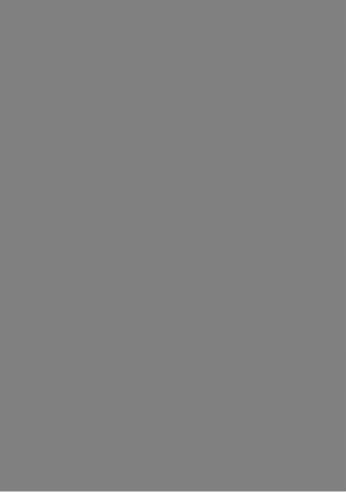
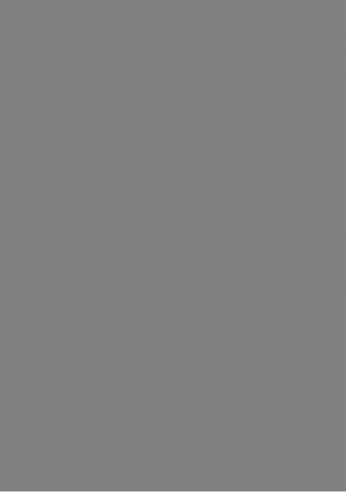
Рис. 3.32. Схемы к расчету деформации лопатки при круговом фрезеровании
Это обусловлено тем, что каждая точка, образующая профиль спин ки пера, характеризуется своим положением нормали: Ы\, А), Nj и т.д. При этом для обеспечения постоянства значений эффективных радиусов ре жущей кромки /?тах и Лт|Пугол наклона у оси фрезы к нормали обрабаты ваемой поверхности должен быть отличным от нуля, что возможно, если нормалям М, А), М,- отвечают соответственно положения осей О], О,, 0¡ и т.д. В этом случае значения Ят(Потличны от нуля, что исключает процес сы пластического деформирования, подмятия металла вершиной инстру мента. Данное условие удается выполнить только при пятикоординатной обработке лопаток компрессора.
2. Осуществление процесса резания на режимах, обеспечивающих постоянное значение деформации лопатки независимо от положения фрезы на обрабатываемой поверхности детали.
Это условие вытекает из развития первого и заключается в разра ботке алгоритма изменения условий резания, гарантирующего деформа цию детали в пределах допуска на ее изготовление (рис. 3.32).
Перо лопатки формируется в процессе его фрезерования концевой фрезой 4. В случае обработки пера поперечными строками (рис. 3.32, а) лопатка вращается вокруг оси 2, а фреза перемещается при прохождении каждой строки в направлениях У и А"с подачей 5. После одного полного поворота детали вокруг оси I фреза смещается в продольном направле нии на ширину строки и процесс резания возобновляется.
Каждое сечение обрабатываемой поверхности пера лопатки, напри мер У-е, характеризуется размером а,. При прохождении фрезой строки в сечении а, постоянно изменяется расстояние между ее режущей частью и осью вращения детали, т.е. изменяется размер Ъ, последовательно при нимая значения Ьп, Ь& Ьа (рис. 3.32, а, б, в).
В результате изменения этих расстояний непрерывно изменяются углы наклона оси фрезы у] относительно нормалей т.е каждому ново му положению нормали обрабатываемой поверхности N 1, N2, N2 отвечает свой угол наклона - соответственно у,ь уа, ув- При этом действительные радиусы режущей поверхности сферической части фрезы /?, соответст венно равны к\, Я2, Я3.
Изменение углов наклона фрезы и соответствующие им изменения радиусов режущей части изменяют окружные скорости резания, которые соответственно принимают значения \ п, уа. В том случае, когда уве личение угла у] не приводит к изменению радиуса режущей кромки фре зы, т.е. при у, = у„,ах, изменяют в процессе фрезерования величину подачи фрезы ($,, 5/3).
Угол утах отвечает положению фрезы, при котором радиус режущей кромки принимает максимальное значение Ятах. Таким образом, возмож ности регулирования процесса резания с помощью изменения окружной скорости резания фрезы исчерпаны.
Значение угла наклона оси фрезы у, определяющее окружную ско рость резания \ р и подачу Я, при у, = утах, в каждый момент времени уста навливают исходя из условия, что необходимо обеспечить равенство де формации пера лопатки допуску на размеры обрабатываемой поверхно сти. После фрезерования поперечной строки фреза перемещается на ши рину строки в направлении 2 и процесс резания возобновляется. При этом положении фрезы происходит обработка следующего сечения, т.е. 1+ 1.
Для данного сечения, имеющего в плоскости Х 0 2 значения пара метров я,+| и ¿>,+|, моменты инерции при изгибе и кручении соответствен но равны Ул+1, Л,». Эти характеристики лопатки отличны от аналогич ных значений в /-м сечении лопатки. Поэтому при фрезеровании этой
строки значения углов наклона фрезы у|+| и подач 5,+| устанавливают с учетом обеспечения равенства деформаций пера лопатки под действием сил резания не только в данном сечении, т.е. (/' + 1)-м, но и в предыду щем, т.е. 1-м. При этом исходят из того, что изгиб лопатки образуется в результате равнодействующей силы резания Р^ определяемой в каждый момент времени работы фрезы режимами обработки.
Поскольку сечения профиля пера в направлениях Х и Усущественно различаются по моментам инерции пера Ух и причем » У,, то и де формации в направлении У(£,) значительно больше деформаций в направ лении X (/¿), т.е./у » / х. Это позволяет приблизительно определить вели чину деформаций пера лопатки в направлении У:
\ - - j - - |
I2 |
(3.1) |
9 Ш , |
/3 |
где Р\ - равнодействующая сила резания, Н; Е - модуль упругости обра батываемого материала, МПа; Л - момент инерции площади поперечно го сечения пера лопатки относительно оси X, м4; / - длина пера лопат ки, м.
Помимо изгиба лопатки в направлении оси Упроисходит скручива ние профиля пера под действием силы резания Р1вокруг оси 2. Величина деформации, являющейся результатом скручивания, определяется выра жением
Г |
Р‘ Ъ‘ а> |
(3.2) |
кр ‘ |
с л |
' |
где й - модуль сдвига, МПа; Л - момент инерции площади поперечного сечения лопатки при кручении относительно оси 2, м4
Суммарное значение линейных и угловых деформаций пера лопатки
Р(1 Ш х Ъ2а{
( 3 .3 )
о / к /3
где Р1= Срур* 5 / (здесь Ср, х, у - коэффициенты степенных функций си
лы резания от скорости резания и подачи, определенные эксперимен тально).
Для фрезерования титановых сплавов принимают х = 0,15...0,2; у = 0,65...0,7; Ср = (3,1...3,4)104
Соотношение между скоростью резания ур, и углом наклона оси фрезы у, имеет вид
*= 2я пЛф вш у , |
(3.4) |
где и-частота вращения шпинделя, с-1; Яф - радиус фрезы, м.
Точность обработки профиля определяется зависимостью б < КТоп, где АГ = 0,3...0,7 —коэффициент использования поля допуска; Топ - до пуск на операционный размер.
С учетом этого параметры управления процессом обработки можно выразить следующим образом:
У, = агс£ |
1 |
Сф 5,7/3А |
при У» < Утах. |
(3.5) |
2я/гф/1ф |
|
|||
|
|
|
|
|
Если у, = утах, то управление процессом резания осуществляется не |
||||
за счет изменений угла наклона фрезы, а из-за изменения подачи Я: |
|
|||
КГ0ПЕУх(2кХф8ту,У}' |
(3.6) |
|||
|
/ЗСр А |
ПРИ У, = Утах, |
||
|
. |
|
||
- частота вращения фрезы, с 1; |
|
|
||
А |
|
|
£7,6,2 а,- |
(3.7) |
|
|
|
G J / ’
где а„ b¡ - координаты положения режущей кромки фрезы, м.
Данные алгоритмы расчета условий фрезерования используются при создании управляющих программ для обработки компрессорных лопаток на многоцелевых обрабатывающих станках.
Так, на рис. 3.33 представлены отдельные кадры визуализации управляющих программ. Профили пера компрессорных лопаток из тита новых сплавов обычно фрезеруют при следующих режимах резания: ско рости инструмента \ р > 120 м/мин; подачах продольных и поперечных (в зависимости от способа строчечного фрезерования) £прод/поп ^ 1000 мм/мин; глубине резания / на черновых проходах 0,4...0,5 мм, получистовых 0,2...0,3 мм, окончательных 0,1 мм. Выбор направления строчечного фрезерования определяется схемой ее закрепления (базирования).
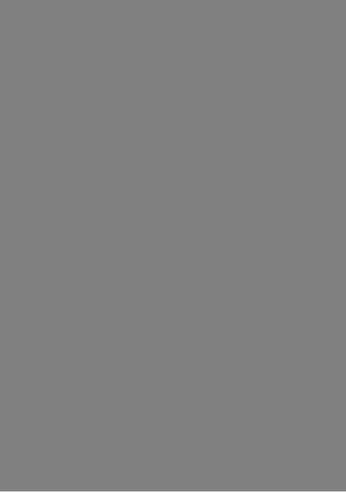
3.4.3. Режущий инструмент для фрезерования проточной части лопаток
К режущему инструменту, используемому при обработке лопаток, предъявляют требования, исходя в целом из двух условий:
1.Компрессорные лопатки - наиболее распространенные детали в ГТД. Их число достигает 1500...2000 шт в каждом изделии. Поэтому первое и самое главное условие, предъявляемое к режущему инструмен ту, - обеспечение высокопроизводительной обработки.
2.Конструкции лопаток предопределяют их малую жесткость в плоскости, перпендикулярной к проточной части. Упругие деформации детали в этой плоскости при фрезеровании обусловливают наличие на последующих операциях значительных припусков, как правило неравно мерных. Это, в свою очередь, требует введения дополнительных опера ций размерного шлифования, полирования, ручной доводки. Поэтому второе условие, предъявляемое к инструменту, - обеспечение высокой точности обработки.
Исходя из этих условий проектируют и изготовляют режущий инст румент, где наряду с общеизвестными принципами расчета инструмента обязательно выполняют следующие принципиальные положения.
1.Режущий инструмент должен иметь твердость, значительно пре вышающую твердость обрабатываемого материала, как правило того или иного титанового сплава. Для их обработки в соответствии с условием обеспечения высокопроизводительной обработки должен использоваться мелкозернистый твердый сплав, например марки ШОР или ОС1025. Применение твердосплавного инструмента позволяет при обработке ти тановых сплавов использовать скорости резания 100...250 м/мин в зави симости от конструкции детали.
2.Режущая поверхность инструмента по линии контакта с заготов кой не должна иметь точек, в которых скорость резания равна нулю или близка к нему. Поэтому при проектировании в режущей части фрезы предусматривают отверстие либо выполняют ее сферической формы. При этом путем наклона фрезы по отношению к нормали в точке касания обрабатываемой поверхности исключают такие зоны застоя, причем по стоянство соблюдения этого условия при обработке гарантируется управляющей программой. Значит, система управления станка должна обеспечивать возможность создания таких программ. Данное условие обычно соблюдается при возможности одновременного управления пя тью координатами.
3.Частота колебаний сил резания (сил, деформирующих деталь) должна быть не менее чем на два порядка выше частоты собственных
Рис. 3.34. Фреза концевая для фрезерования сложных профильных поверхностей при окончательной обработке
колебаний заготовки. В этом случае деталь из-за своей инерционности не успевает деформироваться под действием сил резания.
Это учитывается при расчете числа режущих зубьев и при ограни чениях по диаметру фрезы определяет частоту вращения заготовки. Гео метрия проточной части лопатки, а именно: наличие участков двойной кривизны, малых значений радиусов, переходов от проточной части к хвостовику - вносит ограничения по диаметру режущей части фрезы. Поэтому, как правило, используют фрезы диаметром 2... 10 мм и обра ботку лопаток фрезерованием осуществляют на очень высоких частотах вращения шпинделя: 2000...10000 об/мин.
4. В свою очередь, такие обороты инструмента предопределяют обя зательные условия по равномерности заточки каждой режущей кромки и отсутствию взаимных биений всех поверхностей фрезы, т.е. их точное взаимное расположение. Данное условие диктует необходимость изго товления фрезы за один установ.
Расчет фрез может осуществляться по любой из известных методик, например [1, 2]. Но в каждом случае он должен постоянно оцениваться проектировщиком на соответствие изложенным выше признакам. На рис. 3.34 и 3.35 представлены две типовые конструкции фрез, соответст-