
книги / Технология автоматизированного производства лопаток газотурбинных двигателей
..pdf2.3.3. Качество поверхностного слоя хвостовиков лопаток турбины при глубинном шлифовании
Оно оценивается прежде всего по характеру и величине остаточных напряжений первого рода, степени и глубине наклепа, шероховатости, т.е. по характеристикам, определяющим эксплуатационные показатели детали.
Многочисленные исследования качества поверхностного слоя, фор мируемого при шлифовании лопаток из жаропрочных сплавов, показали, что величины и формы эпюр остаточных напряжений определяются не равномерными пластическими деформациями поверхностного слоя под действием сил резания и упругопластическими деформациями, обуслов ленными неравномерным тепловым расширением материала в поверхност ном слое.
Сравнение эффективности использования того или иного способа обработки проводили в условиях обработки при одной и той же произво дительности, т.е. на режимах, обеспечивающих одинаковый удельны“ объем металла в единицу времени.
На рис. 2.27...2.29 приведены кривые распределения остаточных напряжений первого рода при обычном шлифовании, фрезеровании и глубинном шлифовании.
О |
20 |
40 |
60 |
80 Л, мкм |
Рис. 2.27. Эпюры остаточных напряжений в поверхностном слое при маятниковом шлифовании сплава ХН62МВКЮ-ВД:
1 - врезанием; 2 - с поперечной подачей
Рис. 2.28. Эпюры остаточных напряжений при фрезеровании сплавов:
1 - ЖС6К; 2 -ХН77ТЮР-ВД
Обычное (маятниковое) шлифование проводилось кругом 25А40ПСМ 27К5 на следующих режимах: ук = 35 мм/с; уд = 26 м/мин; *5/= 0,05 мм/дв.ход; с поперечной подачей £п = 1 мм/ дв.ход. Фрезерова ние: Уф = 8 м/мин; уд = 80 мм/мин; Я, = 0,2 мм. Глубинное шлифование:
круг 24А10ПВМ2 12К5; ук= 30 м/с; уд = 50 мм/мин; / = 1,5 мм.
<Уост> МПа
Рис. 2.29. Эпюры остаточных напряжений при глубинном шлифовании сплавов:
1 - ЖС6К; 2 - ХН77ТЮР-ВД; 3 - ВТЗ
2.3. Сравнительные характеристики поверхностного слоя, сформированного при фрезеровании и глубинном шлифовании
Материал |
|
Фрезерование |
Глубинное шлифование |
||||
Степень |
Глубина |
Шерохо |
Степень |
Глубина |
Шерохова |
||
детали |
|||||||
наклепа, |
наклепа, |
ватость |
накле |
наклепа, |
тость |
||
|
% |
мкм |
Яа, мкм |
па, % |
мкм |
Яа, мкм |
|
ЖС6К |
37 |
100 |
2,5...6 |
17,7 |
38,4 |
0,63... 1,25 |
|
ХН77ТЮР-ВД |
17,5 |
80,5 |
2,5...6 |
14 |
45,3 |
0,63... 1,25 |
Из представленных эпюр следует, что только глубинное шлифова ние обеспечивает гарантированное получение в поверхностном слое де талей сжимающих напряжений. Это и служит основной предпосылкой к внедрению данного процесса в производство.
Характерной чертой формирования остаточных напряжений при глубинном шлифовании является идентичность их распределения неза висимо от колебаний режимов шлифования и изменения марки шлифуе мого материалаГДаже химический состав титановых сплавов и предрас положенность их к структурным изменениям не влияют на характер эпю
ры напряжений по глубине измененного слоя.
Распределение сжимающих напряжений происходит в более тонком слое, чем при фрезеровании, что свидетельствует о меньшей глубине проникновения пластических деформаций. Это подтверждается и резуль татами исследований, приведенных в табл. 2.3.
Из данной таблицы следует, что глубина и степень наклепа, шерохо ватость при шлифовании значительно меньше, чем при фрезеровании.
Все это положительно сказывается на эксплуатационных характери стиках деталей, работающих в условиях высоких температур. Оценка влияния усредненных показателей качества поверхностного слоя позво ляет оценить повышение предела циклической прочности деталей на 25... 32%.
Наряду с традиционными методами исследования поверхностного слоя по величине и степени наклепа, а также величине и характеру рас пределения остаточных напряжений использовался метод внутреннего трения [3].
Этот интегральный метод оценки качества поверхностного слоя по зволяет оценивать изменения структуры металла после его механической
обработки. Он основан на исследовании изменения упругих колебаний в различных материалах. Комплексным показателем изменений структуры материала является логарифмический декремент затухания собственных колебаний.
Известны исследования упругих колебаний образцов из стали 20; сплавов ВТЗ-1; ХН77ТЮР-ВД, поверхностный слой которых сформиро ван методами: фрезерования; обычного маятникового и глубинного шли фования. В ходе этих исследований все образцы имели одинаковую гео метрическую форму и размеры, а их поверхностный слой был сформиро ван различными способами резания, сочетание режимов которых обеспе чивало одинаковую удельную производительность [9].
В результате исследований установлено, что у всех материалов наи большее повреждение получил поверхностный слой, сформированный в процессе маятникового шлифования, наименьшее - при глубинном шли фовании. В абсолютном выражении наименьшая величина декремента логарифмических колебаний наблюдается в поверхностном слое детали из никелевого сплава, сформированного глубинным шлифованием.
Эти исследования в дополнение к приведенным выше показали, что глубинное шлифование снижает вероятность появления очагов разруше ния в формируемом поверхностном слое заготовки, т.е. этот метод нано сит наименьшие повреждения детали по сравнению с другими.
2.4.ОБРАБОТКА БАНДАЖНЫХ ПОЛОК И ЛАБИРИНТОВ
2.4.1.Предварительная механическая обработка
Деталь устанавливается. По "елочному" профилю хвостовика (точки 1 ...3) установочная база ориентируется вдоль оси лопатки по точкам на торцах хвостовика и бандажной полки (точки 4, 5) - направляющая база, а также вдоль оси точкой на хвостовике со стороны проточной части (точка 6) - опорная база. В этом положении обрабатываются плоские по верхности бандажной полки (рис. 2.30).
Обработка этих поверхностей может быть двусторонней и совме щаться при использовании фасонного инструмента, как на приведенной технологической схеме, или выполняться поэлементно. В любом случае технологические схемы базирования и закрепления заготовки остаются одинаковыми.
Данные плоскости обрабатываются на плоскошлифовальных стан ках моделей ЗД722, ЗЛ722, ЛШ-220, ЛШ-233 методами маятникового или глубинного шлифования кругами 24А40ПС1 ...С2 6...8К5 на следую-
Рис. 2.30. Технологическая схема обработки плоскостей бандажной полки
щих режимах: скорость круга \ к = 35 м/с; скорость детали \ а > 10 м/мин; подача на врезание 5вр = 0,2 мм/дв. ход.
Ввиду того что обрабатываемые поверхности имеют ограниченные размеры, на указанных режимах возможно снятие значительных припус ков. В процессе маятникового шлифования используют СОЖ, представ ляющие собой водные эмульсии на основе эмульсолов типа ЭГТ5. Одна ко роль этих жидкостей в снижении теплонапряженности процесса не следует преувеличивать.
При технике подачи СОЖ, существующей на обычных плоскошли фовальных станках типа ЗД722 или ЗЛ722, жидкость не попадает в зону резания. В то же время из зоны обработки она достаточно эффективно удаляет продукты изнашивания абразивного инструмента (шлифоваль ный шлам), очищает приспособление.
2.4.2.Наплавка бандажных полок (зигов) специальны
твердыми сплавами
Бандажные полки лопаток турбины, контактирующие друг с другом в процессе эксплуатации, для повышения их износостойкости напаива ются пластинами из более износостойкого материала, чем основной сплав ЖС6К.
Пайка осуществляется с использованием локального источника энергии. В качестве источника для высокотемпературной пайки в вакуу ме применяется дуговой разряд с полым катодом. Неплавящийся катод представляет собой полый цилиндр из титана или вольфрама. Катод име ет внутреннее отверстие диаметром ~2 мм для прохождения через него плазмообразующего газа (аргона), протекающего со скоростью 0,1...
3,0 мг/с. Благодаря этому внутри катода всегда есть условия для обеспе чения необходимой концентрации плазмы [18].
Рис. 2.31. Схема процесса пайки с использованием дугового разряда с полым катодом:
1 - источник питания; 2 ,3 - соответственно напаиваемая деталь и пластина; 4 - полый катод; 5 - вакуумная камера; 6 - охлаждаемая горелка;
7- дроссель подачи аргона
С применением схемы, приведенной на рис. 2.31, можно получить высококачественные паяные соединения с помощью дуговой высокотем пературной пайки в вакууме, если:
-значение падения анодного потенциала близко к нулевому (1...
5 В) и не может быть соизмеримо с потенциалом ионизации аргона;
-площадь торцовой поверхности пластины, где расположены пая ные соединения, в 1,5...2 раза больше площади пятна нагрева, что, как правило, превышает площадь бандажной полки лопатки.
Всвязи с этим площадь бандажной полки увеличивают посредством специального приспособления.
Для напайки обычно применяют пластины из следующих материа лов: ВКНА2; ВЖЛ15; ВЖЛ2. Эти сплавы обладают более высокими твердостью и прочностью по сравнению с материалом лопатки, особенно
вусловиях высоких температур. Обычно используют припои ВПр24 и
ВПр27, которые имеют температуру пайки 1170... 1180 °С, что несколько меньше температуры фазовых превращений основного материала (ЖС6К, ЖС6У). Кроме того, эти припои выпускаются в виде аморфной фольги толщиной 30...60 мкм.
На подготовленные во время предыдущих операций поверхности бандажных полок наносят припой, который вырезают по форме полки (обычно шире на 2...3 мм) и укладывают на нее в два-три слоя. Затем припой прихватывают точечной сваркой. В этом положении на бандаж ную полку лопаток помещают напаиваемую пластину и прижимают ее к полке.
После сборки бандажной полки с напаиваемой пластиной детали за ключают в вакуумную камеру, в которой после откачки воздуха создает ся давление 0,06.. .0,08 Па. Затем при подаче через полый катод аргона со скоростью 0,5... 1,0 мг/с проводят процесс пайки.
Режим при пайке пластин размерами 5x3x1,5 мм из материала ВКНА2 припоем ВПр27 к лопатке из сплава ЖС6К следующий: ток раз ряда 12... 15 А; напряжение 32...34 В; расстояние между катодом и на паиваемой пластиной 20...23 мм; диаметр проходного отверстия в катоде 3,0. ..3,2 мм.
Процесс пайки контролируют визуально по оплавлению припоя, вы ступающего за границы пластины, а также по выдавливанию части при поя из-под пластины и растеканию под ней. После оплавления припоя предусмотрена выдержка полного соединения при температуре пайки в течение 15...20 с.
После пайки лопатки подвергают термообработке в течение 3 ч при температуре 950 °С, места пайки полируют (для удаления остатков при поя), и проводят люминесцентный контроль. В особых случаях, огово ренных требованиями чертежа, одну или несколько лопаток из партии испытывают на срез при температуре 975 °С.
Испытания считают успешными, если разрушение бандажной полки происходит по материалу пластины.
2.4.3.Окончательная обработка бандажной полки
Операции обработки бандажных полок после наплавки аналогичны (по схемам базирования и закрепления, задействованному оборудованию и режимам обработки) операциям, выполняемым на этапе предваритель ной обработки полок под пайку. Существенным отличием является обя зательное использование при обработке напаянных пластин шлифоваль ных кругов из зеленого карбида кремния 63С и 64С; в исключительных случаях допускается применение кругов из хромотитанового электроко рунда 91А и 92А.
2.5.ОБРАБОТКА ЦИЛИНДРИЧЕСКИХ ПОВЕРХНОСТЕЙ
ЛОПАТОК ТУРБИН
2.5.1. Операции шлифования цилиндрических поверхностей лопатки
Их можно выполнять на специальных шлифовальных станках, а также на токарно-лобовых или карусельных токарных станках, при ос нащении их шлифовальными головками, размещенными на суппорте станков. Лопатки собирают в приспособление в виде ложного диска, со ответствующего диску той же ступени турбины, что и обрабатываемые лопатки (рис. 2.32).
Лопатки устанавливают хвостовиком в диск, при этом лопатку фик сируют в шести направлениях. Точки 1...3 определяют ее положение на плоскости (установочная база), боковая поверхность зуба (точки 4, 5) фиксирует ее от поворота относительно оси лопатки (направляющая ба за). Опорной базой является точка 6 на торце, противоположном обраба тываемому. Эта база определяет положение оси лопатки.
С помощью винтов лопатки выжимают в радиальном направлении на максимальный диаметр, который допускает зазор между хвостовиком
Рис. 2.32. Схема базирования лопатки при обработке лабиринтов
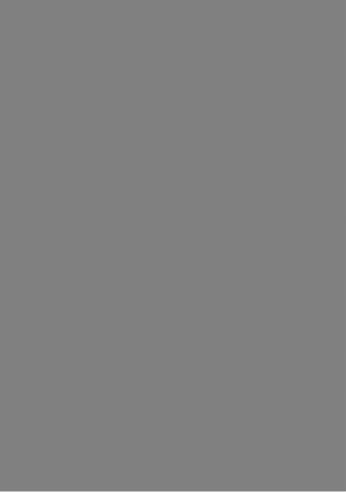
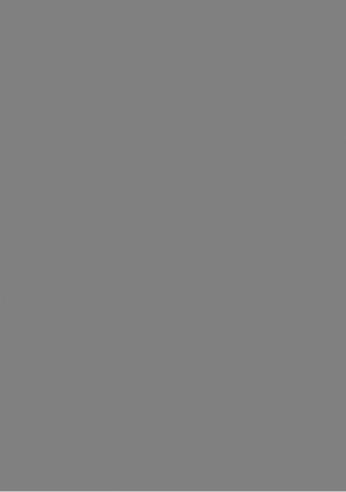