
книги / Технология автоматизированного производства лопаток газотурбинных двигателей
..pdf-отклонения по шагу одного зуба относительно другого ± 0,01 мм;
-отклонение по углу профиля в пределах ± 0,15';
-смещение одной стороны профиля "елки" относительно другой (длина до базовой линии) ± 0,01 мм.
Столь высокая точность обработки достигается благодаря ис пользованию при обработке хвостовиков специальных способов резания.
Так, металлорежущие станки, используемые при обработке хвосто виков лопаток турбины, осуществляют процесс резания в основном спо собом глубинного шлифования.
2.3.2.Глубинное шлифование - способ механической обработки
хвостовиков лопаток
Глубинное шлифование по своей кинематике существенно отлича ется от традиционного плоского. В условиях равной производительности, т.е. одинакового удельного съема металла в единицу времени, глубина резания на один-два порядка выше, чем при традиционном шлифовании, и, соответственно, величина подачи (скорость детали) во столько же раз меньше.
Такая кинематика процесса резания позволяет до 80 % теплоты, вы деляющейся при резании, направить в снимаемые слои металла. Это в конечном счете обеспечивает высокое качество поверхностного слоя де тали, поскольку при глубинном шлифовании формируется поверхност ный слой детали с остаточными напряжениями сжатия, что невозможно при традиционных способах шлифования.
Осуществление процесса глубинного шлифования гарантируется выполнением следующих технологических условий.
1. Характеристика инструмента: вид абразивного материала, зер нистость, твердость, структура, связка. Эти параметры должны обеспе чить максимальную производительность в случае бездефектного (бесприжогового) шлифования и в то же время сохранить высокую геометри ческую точность шлифуемого профиля.
При шлифовании сталей и жаропрочных сплавов на никелевой ос нове используют белые электрокорунды 24А, 25А, а при шлифовании титановых сплавов - карбиды кремния 54С, 63С. Зернистость определя ется в основном требованиями к точности шлифуемого профиля и усло виям бездефектного шлифования. Так, с уменьшением зернистости круга 2* увеличивается число режущих зерен, формирующих одну и ту же по верхность, т.е. возрастает геометрическая точность формообразования. Твердость круга Тк влияет на его износ и температуру шлифования, от
|
которых |
зависит вероятность |
появления |
|||
|
прижогов. Повышение твердости способст |
|||||
|
вует снижению размерного износа круга, а |
|||||
|
также уменьшению |
самозатачиваемости и |
||||
|
большей вероятности появления прижогов. |
|||||
|
При выборе твердости и зернистости |
|||||
|
круга учитывают сочетание этих характери |
|||||
|
стик, обеспечивающих период |
размерной |
||||
|
стойкости круга, равный (или несколько |
|||||
|
меньший) периоду его стойкости, ограни |
|||||
|
ченной |
появлением |
прижогов. Оптималь |
|||
|
ные сочетания ZK и |
Тк устанавливаются в |
||||
|
каждом |
конкретном |
случае |
эксперимен |
||
|
тально. |
|
|
|
|
|
|
Так, при шлифовании "елочного" про |
|||||
|
филя хвостовиков лопаток ГТД наибольшая |
|||||
|
размерная и бесприжоговая стойкость инст |
|||||
|
румента, |
определяемая длиной |
обработки |
|||
|
на выбранных режимах, обеспечивается при |
|||||
|
зернистости круга 8... 12 и твердости ВМ1, |
|||||
|
ВМ2, М1. |
|
|
|
||
Рис. 2.23. Схема врезной |
Структура кругов, используемых при |
|||||
глубинном шлифовании, должна обеспечи |
||||||
правки: |
||||||
вать свободное размещение |
и |
вымывание |
||||
1 - деталь; 2 - шлифовальный |
||||||
круг; 3 - алмазный ролик |
стружки из пор режущей поверхности кру |
|||||
га, а также перенос порами частиц жидко |
||||||
|
сти в зону контакта круга с деталью. Этими свойствами обладают круги зернистостью 9... 12, имеющие пористость ~ 80 %, т.е. структуры 11... 12.
Размер пор в кругах, применяемых при глубинном шлифовании, формируется не только в результате их укладки, но и вследствие приме нения различных порообразующих веществ, выгораемых или выплав ляемых в процессе изготовления кругов. В качестве порообразующих наполнителей используют перлит, синтетический полистирол, мелкозер нистый нефтекокс и др. Связка абразивных кругов для глубинного шли фования должна выдерживать высокие термодинамические нагрузки, быть водостойкой и обладать высокой химической стойкостью. Эти свойства инструменту придают только керамические связки КЗ, К5, Kl 1 и др. Круги, наиболее оптимально отвечающие этим рекомендациям, вы пускают по ТУ 2-036-022450-015-86 в ОАО "Ильич" (Санкт-Петербург) [1,9].
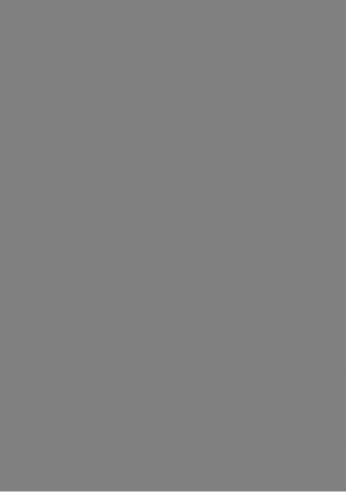
Рис. 2.25. Схемы правки с дискретной (а) и непрерывной (б)
компенсацией износа
МААС, представляющий собой гетерогенную систему, элементами кото рой являются зерна алмазов в металлической матрице. Сплав, связываю щий зерна, относится к дисперсионно-упрочненным и обладает высокой адгезией к алмазу. Стойкость таких роликов составляет 20...30 тыс. пра вок [15].
Круги обычно правят методом врезания, обеспечивающим более вы сокую геометрическую точность профиля. Метод требует точного пози ционирования алмазного ролика и круга, совпадения осей симметрии. Правка может проводиться с определенной периодичностью или непре рывно. В последнем случае профилирование шлифовального круга осу ществляется в процессе обработки. Абразивный круг и правящий ролик во время всего цикла обработки находятся в постоянном контакте. Ком пенсация износа круга выполняется дискретно или непрерывно (рис. 2.25).
При дискретной компенсации износа формируемая поверхность приобретает некоторую волнистость, допустимое значение которой не должно превышать 5 мкм. Шаг между вершинами зависит от подачи на правку 5пр, определяемую интенсивностью съема металла при шлифова нии. При непрерывной компенсации износа данный недостаток отсутст вует. Для этого алмазный ролик, вращающийся с частотой пр и находя
щийся в контакте с кругом, имеет подачу на врезание 5вр, которая ком
пенсируется такой же подачей всей шлифовальной бабки 5К. Непрерыв ная правка позволяет вести шлифование при одном и том же состоянии режущей поверхности круга, стабилизировать его режущие свойства.
Современные системы управления дают возможность совершать пе ремещения на правку и компенсацию круга абсолютно синхронно, ис ключая появление волнистости на обработанной поверхности. При этом подача на правку изменяется в пределах 0,1.. Л мкм/об. круга. Непрерыв ная правка наиболее эффективна при обработке материалов с низкой теп лопроводностью, например жаропрочных сталей и никелевых сплавов, а также материалов, склонных к адгезионному схватыванию с режущей поверхностью круга, например титановых сплавов.
Режимы правки определяют следующие характеристики:
- отношение скоростей правящего алмазного ролика и круга
-направление их вращения;
-толщину абразивного слоя h, снимаемого с круга при правке;
-длительность выхаживания круга без врезания ролика тв.
Для кругов, используемых при глубинном шлифовании, твердостью ВМ1...М1 направление вращения ролика по отношению к кругу должно быть только попутным, так как в этом случае обеспечивается наиболь ший градиент плотности режущих зерен по толщине слоя инструмента, измененного правкой. Недопустимо, чтобы при этом соотношение частот их вращения было равно целому числу, поскольку все дефекты рабочей поверхности ролика или погрешности его установки в этом случае копи руются на рабочую поверхность круга. Отношение V p/vK должно быть в пределах 0,8...0,9, при других значениях наблюдается повышенное из нашивание алмазного ролика.
Толщина h абразивного слоя, снимаемого при правке, не должна превышать зернистости круга. Существенно влияет на шероховатость обработанной поверхности длительность выхаживания тв, которая обыч но колеблется в интервале 1...5 с. Дальнейшее увеличение тв не снижает шероховатость на обработанной поверхности и экономически нецелесо образно.
3. СОЖ и техника их подачи. Выбор СОЖ определяет характер тем пературно-деформационной напряженности шлифования. При глубинном шлифовании СОЖ должна обладать высокой смазывающей, моющей и проникающей способностью, обеспечивать наиболее полный отвод теп лоты из зоны шлифования. Оптимальное сочетание этих свойств достига ется в случае применения синтетических и полусинтетических водных СОЖ.
Наибольшее применение получил (1,5...2)%-ный водный раствор эмульсола Аквол-2 (ТУ 38 УССР 2-01-220-79). Он представляет собой
смесь композиции ЭК-1 (40 %) в минеральном масле И-12А (35...41 %). Эта смесь содержит противозадирные присадки: хлорированный парафин (10...15 %), осерненное жировое масло (5... 10 %), полисульфид ЛЗ-301.
Синтетическая смесь серных и хлорных присадок обеспечивает снижение интенсивности адгезионных и диффузионных явлений при об работке труднообрабатываемых материалов. Наличие в СОЖ большого количества воды (98 %) гарантирует высокую эффективность отвода теп лоты.
Недостатком эмульсола Аквол-2 является необходимость ее частой замены (не менее 1 раза в 3 мес), что обусловлено разложением СОЖ по мере истечения срока годности. Эти недостатки исключаются при ис пользовании жидкостей Аквол-6, Аквол-ЮМ, Аквапол, Ротан-Солюбль и др.
Транспортирование СОЖ в зону резания должно обеспечивать эф фективное использование моющих средств жидкости, отвод шлама и от ходов шлифования из зоны обработки, доставку жидкости в зону контак та круга с деталью. Перечисленные требования удовлетворяются в случае подачи СОЖ напорной струей. При глубинном шлифовании этот способ реализуется, если расход подаваемой жидкости 120...200 л/мин на один круг и давление составляет 0,6... 1,2 МПа.
Однако соблюдение этих условий не гарантирует получения тре буемого качества поверхностного слоя на обрабатываемой поверхности. Это объясняется тем, что диаметр круга в процессе его эксплуатации по стоянно изменяется, поэтому точка попадания охлаждающей жидкости может оказаться вне зоны резания. Вследствие этого практически все станки для глубинного шлифования оснащены механизмами наладки по ложения сопла, через который подается охлаждающая жидкость. Подна ладка осуществляется в автоматическом цикле, синхронно с уменьшени ем диаметра круга при правке. Кроме того, система подачи СОЖ на мно гих станках содержит специальные сопла для очистки режущей поверх ности круга. Существует много конструкций таких устройств. Одно из них, использующее метод ультразвуковой очистки, приведено на рис. 2.26 [9].
Здесь проникновение жидкости в поры круга обеспечивается при попадании охлаждающей жидкости из клиновой полости насадки в зазор между ней и кругом. При наложении на насадку ультразвуковых колеба ний (УЗК) в жидкости возникают явления кавитации (образования и за хлопывания микропустот). При захлопывании микропустот наблюдается ударная волна, проталкивающая жидкость в поры круга. Если межзерен-
-2 2 0 В
Рис. 2.26. Принципиальная схема наладки для подачи охлаждающей жидкости через торец круга с наложением УЗК:
1 - торцовая насадка; 2 - пьезокерамические шайбы; 3 - корпус; 4 - крышка; 5 - штуцер; б - токоподвод; 7 - гайка
ное пространство круга (пора) заполнено шламом (стружкой), то при от рицательном давлении (образовании микропустоты) частицы стружки удаляются с режущей поверхности.
При амплитуде А колебаний в пределах 5 мкм в жидкости возникает кавитационный процесс, обеспечивающий проникновение жидкости в круг на глубину до 30 мм. Это позволяет устанавливать такие насадки не только по нормали к режущей поверхности круга для ее очистки, но и по торцу круга для прокачки через него охлаждающей жидкости под дейст вием центробежных сил. Исследования эффективности применения по добной техники подачи СОЖ показали, что в дополнение к основному способу ее подачи напорной струей мощность шлифования уменьшается на 10... 15 %, высота микронеровностей по параметру Яа меньше на 20...30 %, прижогов и шлифовочных трещин не обнаружено.
4. Очистка охлаждающей жидкости. В процессе шлифования ох лаждающая жидкость постепенно загрязняется частицами абразивных зерен, связки, стружки, пылью, волокнистыми и смазочными материала ми. Вследствие этого уменьшается стойкость инструмента, ухудшается качество шлифуемой поверхности. Поэтому каждый станок для глубин ного шлифования оснащен специальной системой очистки, осуществ ляющей фильтрацию путем пропускания жидкости через пористые или щелевые перегородки; очистку в силовых полях; физико-механическую очистку.
Наиболее эффективная система очистки обеспечивает:
-слив жидкости в бак-отстойник через сетчатый фильтр (грубая очистка);
-оседание твердых частиц в баке-отстойнике, для чего он выполня
ется значительных объемов (1,5...2 м3);
-удаление осажденных частиц постоянно работающим скребковым конвейером;
-очистку жидкости с помощью центрифуг, куда она подается по средством специальных насосов (тонкая очистка);
-перекачку жидкости в чистовой бак объемом до 3,5...5 м3 и очист ку методом флотации (окончательная очистка).
Такая схема очистки обеспечивает наличие в системе подачи жидко сти загрязняющих частиц размером в пределах 10 мкм, что гарантирует нормальный процесс шлифования и отсутствие дефектов на обработан ной поверхности детали.
5.Режимы шлифования. Выбором технологической схемы обработ ки, характеристики режущего и правящего инструмента, метода правки, способов и техники подачи СОЖ можно обеспечить необходимую произ водительность процесса глубинного шлифования и требуемое качество обработки поверхности при оптимизации каждого из указанных техноло гических условий.
Отсутствие дефектов поверхностного слоя (прижогов и микротре щин) является обязательным условием осуществления глубинного шли фования. Гарантированное достижение бездефектной обработки обеспе чивается режимными параметрами и техникой подачи СОЖ, удовлетво ряющими следующим условиям:
I, |
(2.1) |
Ук/Уд = (1...600)102; а > (З,5...5)103 Вт/(м2 °С),
где уд - скорость движения детали, м/мин; Г)к - диаметр шлифовального круга, мм; / - глубина шлифования, мм; а - температуропроводность, м2/с; ук - скорость вращения круга, м/с; а - коэффициент теплопередачи.
При обработке жаропрочных сплавов, имеющих низкую теплопро водность, рекомендуется вести обработку при попутной подаче детали, что увеличивает производительность на 30 %. Вязкие теплопроводные сплавы и конструкционные стали наиболее целесообразно обрабатывать при встречной подаче детали, обеспечивающей по сравнению с попутной более высокое качество или повышение производительности на 30 %.
Материал детали 1
£
PQ
>.
VO
ё
S
0Q
>.
(N
оо
и
гг
2.2. Расчетные режимы глубинного шлифования хвостовиков лопаток турбины
снимаемоВеличина ммприпуска,го |
проходовКоличество |
кругаСкоростьv, м/с |
Глуби |
Пода |
|
|
|
|
|
||
|
|
|
на ре |
|
|
|
|
|
ча S, |
Примечания |
|
|
|
|
зания t, |
||
|
|
|
мм/мин |
|
|
|
|
|
мм |
|
|
|
|
|
2,0 |
50 |
Ширина замка лопатки |
|
|
27 |
|
|
|
2,3 |
3 |
1,0 |
100 |
/ = 40 мм. |
|
|
|
|
0,05 |
50 |
Круг 24А10П 3H31...33 10К5 |
|
|
|
|
||
|
|
|
5,3; 2,5; |
|
|
и , |
|
|
2,0; 1,0; |
10 |
Ширина замка лопатки |
7 |
29 |
0,35; 0,1 |
|
/= 100 мм |
|
3 |
|
|
|
|
Круг 25А 1ОПЗИЗ1.. .33 12К5 |
|
|
|
0,05 |
50 |
|
|
|
|
|
Технологические расчеты режимов глубинного шлифования, вы полненные на основании условий (2.1), и опыт осуществления процесса шлифования лопаток турбины позволяют рекомендовать для жаропроч ных никелевых сплавов режимы резания, приведенные в табл. 2.2.
Анализ режимов резания при обработке двух различных видов ни келевых сплавов (марок ЖС и ЧС) показывает, что режимы резания на значаются технологом из следующих соображений.
1.Последний (чистовой) проход осуществляется с глубиной реза ния и подачей детали, которые обеспечивают требуемые геометрические размеры и шероховатость обрабатываемой поверхности.
2.Предпоследний (получистовой) проход выполняется с глубиной резания, гарантирующей удаление измененного слоя, возникающего по сле черновых проходов.
3.Предварительные (черновые) проходы осуществляются с целью снятия основного припуска. Здесь ограничением режимов является мощ
ность станка. Поэтому в зависимости от размеров шлифуемой поверхно
сти и глубины профиля, число проходов может быть разны в первом случае один проход; во втором - пять.
Отметим, что с каждым предварительным проходом глубина реза ния уменьшается. Это обусловлено тем, что при обработке "елочного" профиля фактическая ширина обработки постоянно увеличивается. По этому при одной и той же потребляемой мощности шлифования глубины резания отличаются друг от друга в широких пределах.
Поскольку на успешное выполнение процесса глубинного шлифова ния влияют много факторов, перед обработкой каждой новой партии де талей на установленных режимах обрабатывается образец, который аттестовывается в центральной измерительной лабораторией (ЦИЛ). Только после этого дается разрешение на обработку всей партии деталей.
После выполнения операции на рабочем месте проводится полны“ контроль замка лопатки. При этом проверяют:
-толщину замка по средней линии зуба в каждой вкладке;
-относительное смещение сторон профиля гребенок;
-высоту замка от оси ролика первого зуба до подошвы замка;
-высоту зуба по средней линии замка;
-шаг зубьев;
-радиусы при вершине и впадине зуба;
-углы в каждом пазе хвостовика.
Применяемые средства контроля различны и зависят от серийности обработки. Здесь могут использоваться микрометры для контроля разме ров по роликам, а также разнообразные индикаторные приспособления, компараторы и другие специальные средства контроля.
Внутренние и внешние дефекты поверхности хвостовика лопатки после обработки контролируют в основном люминесцентным методом. Он используется для выявления дефектов в виде трещин, волосовин, ра ковин, выходящих на поверхность детали. Этот капиллярный метод ос нован на способности некоторых жидкостей светиться при облучении ультрафиолетовым светом.
Контролируемую деталь после очистки и обезжиривания погружают в ванну с индикаторной жидкостью, проникающей в поры детали. Затем деталь очищают, сушат и покрывают краской с высокой поглощающей способностью. Индикаторная жидкость выступает из дефектных мест на поверхность пленки, образованной проявляющим составом. Наличие де фектов устанавливают, осматривая деталь в темном помещении при ультрафиолетовом освещении. При этом трещины выявляются в виде светящихся линий и пятен. Требования чертежа трещин на замке не до пускают. Детали с трещинами отбрасываются, остальные промываются ацетоном и переходят на последующие операции.