
книги / Технология производства полимерных композитных материалов и конструкций на их основе
..pdfновине технологические режимы изготовления на стадии проектирова ния, что позволит спрогнозировать более точно работоспособность конструкции с учетом реального технологического процесса ее из готовления*
2*6, Ко н т р о л ь натяжения армирующих материалов
Натяжение армирующего материала (жгуты, ленты, ткани) сущест венно влияет на качество готовых конструкций* Поэтому необходима разработка широкой гаммы устройств для непрерывного или периоди ческого измерения и регулирования натяжения.
По принципу действия натяжители делятся на три группы.
Рис*34. Принципиальные схемы натяжителей ленточного композитного материала: Q - пластинчатый; (Г - стержневой; в - роликовый; I - движущийся ленточный армирующий материал; 2,3 - неподвижная и подвижная пластины (гребни;; Ц - регулировочный груз; f - враща
ющиеся ролики
В первую группу входят устройства, в которых натяжение арми рующего материала (рис.34, а ) создается под действием трения при
перемещении его между двумя пластинами 2 , 3 , |
прижимаемыми друг |
к другу с некоторой силой Р . Эту силу можно |
создавать с помощью |
рычажной системы и груза 4 , или пружины, или магнита. В данной конструкции натяжение материала зависит от начального натяжения
Т0 , усилия Р и приведенного коэффициента трения / о поверх ность пластины: Г = Т0 + 2Р/ . Также пластинчатые натяжители об ладают почти линейной статической характеристикой, достаточно просты в конструктивном отношении, однако они нарушают поверх ность армирующего материала и поэтому нашли ограниченное приме нение в производстве конструкций.
Вторую группу натяжителей составляют устройства, обеспечива ющие натяжение армирующего материала за счет его скольжения по криволинейной поверхности, например, по неподвижным стержням или роликам (рис.34, S ) . В этих стержневых устройствах натяжение ли нейно зависит от начального натяжения и нелинейно - от суммарно
го угла охвата |
<£0 стержней армирующим материалом и коэффициен |
|||
та трения: Т = |
Т0 вхр (cC0f ) |
. Для изменения Т в стержневых на |
||
тяжителях варьируют угол оС0 |
перемещением подвижного |
гребня 3 |
||
с помощью силы тяжести груза |
4 |
или усилия от магнита |
(пружины). |
|
В третью группу входят устройства, обеспечивающие нужное на |
||||
тяжение путем торможения ролика |
5 , вращаемого движущимся мате |
|||
риалом (рис.34, i ). Для торможения ролика используют |
силу тяжес |
|||
ти груза 4 или усилие пружины |
(магнита). В подобных роликовых |
конструкциях натяжение линейно зависит от тормозного момента Мт ролика радиусом R: Т = Т0 + MT/R.
Натяжители 2-й и 3-й групп широко применяют в производстве конструкций из композитных материалов.
Качество сматывания арматуры со шпулярника и последующее формование технологической пряди определяются предварительным на тяжением. Для этого в шпулярнике предусмотрены индивидуальные на тяжные устройства для армирующего материала. Эту роль выполняют устройства механического, пневматического, гидравлического или электрического типов. Наиболее простыми являются натяжители, ис пользующие эффект трения армирующего материала по поверхности их деталей. Регулирование величины натяга осуществляется в этом слу чае за счет изменения угла обхвата армирующим материалом этих по верхностей и контактного давления на них.
Применяемое при намотке натяжение может быть проконтролиро
вано:
по силе отжатия подпружиненного валика; по стреле провисания армирующего материала;
по потребляемой мощности намоточного станка; по величинам сил и моментов взаимодействия армирующего мате
риала с технологической оправкой или оправки с ее опорами; по деформации наматываемых на оправку слоев наполнителя.
Первый способ является самым надежным и просто осуществимым, причем применяются как механические, так и электрические тензо метры.
Электроиндуктивные датчики типов ДНИ-ЗМ, ДЛ-2Л, ИНПЛ-IM и др. обеспечивают контроль натяжения нитей, ровницы, жгута, ленты до 2 кН с точностью ±(2,5-5,0) % при скоростях намотки 0,1-1,0 м/с.
Механические тензометры предназначены для контроля более значительных натягов, но точность замера у них меньше (* 10 %). Для контроля нитей наиболее известны линейный тензометр ТОН-1, а также датчик угловых перемещений МУ-65.
Контроль обрыва нитей осуществляется специальными датчика ми, представляющими собой двуплечные подпружиненные рычаги, ко торые при обрыве нити замыкают электрическую цепь, вследствие чего загорается лампа аварийной сигнализации. Целостность ленты контролируется сигнализатором ее движения СВ-2.
В систему регулирования технологического натяжения армирую щего материала на станке входят индивидуальные натяжные устрой ства для нитей в шпулярнике, а также индивидуальные и общие на тяжные устройства в конструкции пропиточно-формирующего тракта станка. В намоточных станках применяются системы регулирования натяжения типа УНПЛ-IM, САРН-2, АСПТ-1, ИНБВ-1 и др.
Совершенные натяжители обеспечивают коэффициент неравномер ности натяжения отдельных нитей в технологической пряди около 0,6-0,75, т.6, не менее 60 % нитей пряди имеют натяг в пределах заданного допуска. Минимально допустимый диаметр тормозного ба рабана <Z0fr зависит от диаметра и свойств армирующего материала:
где ЕАм - модуль упругости |
армирующего материала; d - диаметр |
|||
волокна; |
<?АМ- растягивающие |
напряжения в армирующем материале. |
||
Для |
стекловолокна |
значение <Юр должно быть не менее |
2,5 мм |
|
а для высокомодульных |
- 15-30 мм. Обычно применяемые на практике |
|||
в натяжном тракте барабаны и |
ролики натяжного устройства |
имеют |
диаметр около 50 мм и более. Материалом для их изготовления ча ще всего служат полиамид, фторопласт и сталь.
2.7. Формование к о н с т р у к ц и и
В комбинированных схемах намотку целесообразно начинать с укладки спирального слоя, который позволяет при уменьшенном сило
вом воздействии на наружные слои оправки получить более качест венный первый слой композитного материала с минимальным коли чеством дефектов (защипов и пузырей) на резиновом или другом поверхностном слое оправки. Допустимые зазоры и нахлесты техно логических прядей при намотке крупных конструкций в тангенциаль ных слоях могут составлять от 10 до 3 мм соответственно, а в спи ральных слоях от 20 до 5 мм. У небольших конструкций зазоры мень ше: 0,5-1,0 мм в тангенциальных и 1,5-3,0 мм в спиральных слоях. Обрыв нити при намотке должен быть устранен в течение 5 минут. Намотка при наличии 5 оборванных нитей в любой момент времени должна быть прекращена. Технологическим регламентом допускается не более 10 спутанных мест арматуры на один намотанный слой обо лочки, оговаривается также количество недопустимых посторонних включений в слоях. Любой слой намотанной стенки, кроме первого, признанный дефектным, подлежит отмотке с оболочки.
Концы оборванных лент (жгутов) склеиваются пленочным клеем БК-3 и обжимаются при 393 К в течение 1-2 мин. Разрешаются ос тановки в процессе намотки, связанные с установкой новых бобин, катушек и рулонов с армирующим материалом и устранением его об рывов, заливкой связующего в ванночку, изменением кинематики дви жения и т.п. Суммарное время остановок в процессе намотки ответ ственных конструкций должно быть менее 30 мин и в любом случае не превышать 6,5-8 ч (в зависимости от срока жизнеспособности связующего). В случае необходимости возобновления намотки после остановки большей длительности нужно предусмотреть адгезионную обработку поверхности наматываемой оболочки. При прекращении на мотки на время более 10 мин отключается обогрев пропиточной ван ночки или устройств размягчения препрега.
Продолжительность намотки средних по размерам оболочек сос
тавляет 50-70 мин, а крупногабаритных конструкций |
- 48 ч и более. |
В цехах должна поддерживаться температура 291-308 |
К, относитель |
ная влажность до 80 %и освещенность не менее 300 |
лк. |
По окончании процесса намотки основной оболочки часто быва ет необходимо осуществить подмотку дополнительного материала для сопряжения конструкции со смежными конструкциями комплекса. И, наконец, намотка может завершаться технологическими операциями обмотки свеженамотанной оболочки слоями для дренажа или капсули-
рования с целью дополнительного уплотнения намотанной структуры. Эти слои после выполнения их функций удаляются с конструкции об ратной размоткой или механической обработкой.
Для осуществления последующего контроля свойств намотанного композитного материала на наматываемых конструкциях предусматри вается "прибыльная часть", из которой и изготавливаются образцы для контроля.
Если в наматываемой конструкции невозможно получить "при быльную часть", то изготавливают намоткой специальные кольцевые образцы, часть из которых выполняют до начала намотки конструк ции, а часть - после ее окончания. Кольцевые образцы изготавли вают в тех же условиях, что и сами оболочки, не допуская отклоне ний от принятых режимов технологии. В последующем эти образцы совместно с намотанной конструкцией подвергают отверждению.
Намотанная оболочка вместе с оправкой поступает на отверж дение. Время от начала намотки до начала термической обработки не должно превышать сутки. Иногда, в частности при намотке на эластичные оправки, процесс ведут последовательно, раздельной намоткой нескольких слоев оболочки, каждый из которых по оконча нии его намотки подвергают частичному отвездению. В этом случае длительность перерывов в процессе намотки определяется условиями л требуемой степенью отверждения слоя. Обычно между операцией намотки и термической обработки существует небольшой (2-3 ч) разрыв во времени, необходимый для выполнения вспомогательных технологических операций. Этот разрыв, как показывает практика, может быть и полезен, так как позволяет углубить процесс пропит ки и снизить содержание воздушных включений в материале готовой
конструкции. Этому же способствует вакуумирование намотанных кон струкций.
2.8. Определение технологических
ремчоа ртвэрддеадя
Основными технологическими параметрами процесса отверждения являются температура я время. Температуре принадлежит главенству ющая роль, так как она решающим образом влияет на свойства полу чаемого материала. Высокая температура отверждения (для эпоксид
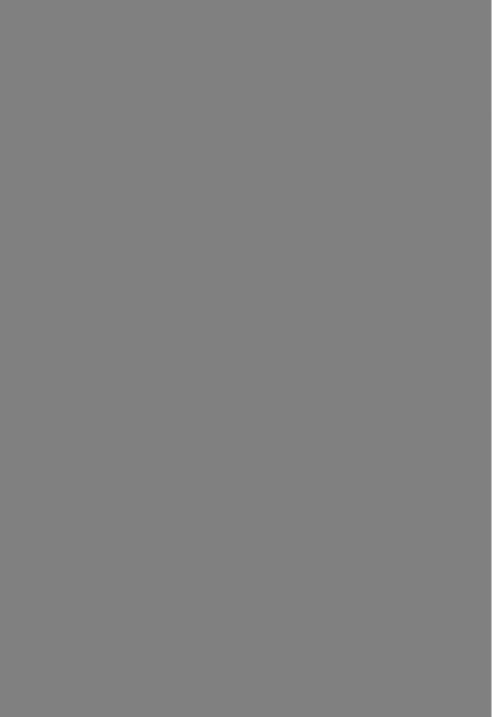
жет быть получен материал с оптимальными структурно-механически ми свойствами. Число таких ступеней в зависимости от габаритов конструкции может достигать 3-4, что приводит в увеличение дли тельности режима отверждения, приводя, с одной стороны, к улуч шение механических характеристик, а с другой, - к увеличению себестоимости производства ввиду высокой стоимости операции от
верждения за счет повышенного расхода электроэнергии, который |
|
может достигать 7000-12000 кЭ г/ч. |
|
|
Время отверждения конструкции может быть рассчитано на ос |
новании теории нестационарной теплопроводности. |
|
|
В качестве математической модели рассматривается отвержде |
ние в |
кольцевой области с заданными внешним ( Rz) и внутренним |
( R j) |
радиусами композитной оболочки, находящейся на цилиндри |
ческой оправке с внутренним радиусом ( R0). Процесс описывается сопряженной системой уравнений переноса тепловой энергии в кине тики отверждения:
|
|
|
|
* * » |
= |
<7, * * Г |
» |
* |
Cz |
* |
|
|
(17) |
||
|
|
|
|
дъ |
|
е |
|
|
|
d r |
|
|
|||
|
|
|
|
о j |
|
|
„ |
|
Ко9(л)е |
-EalRT(® |
(18) |
||||
|
|
|
|
|
= |
D V * * |
* |
|
|
||||||
|
|
7 * |
- оператор |
Лапласа, |
|
|
|
|
|
|
|
|
|||
|
|
|
|
» £ _ |
|
/ |
д / д ) |
|
1 |
д 2 |
|
|
|||
I |
- |
индекс |
соответственно для материалов оправки и композита, |
||||||||||||
I ж1 ,2 ; |
V |
- время; |
Л , <р - |
радиальная и окружная координаты; |
|||||||||||
a, |
D |
- |
коэффициенты температуропроводности |
и диффузии; |
- |
||||||||||
скрытая теплота полимеризации; |
С - |
массовая |
теплоемкость; |
К0 - |
|||||||||||
предэкспоненциальный множитель; |
|
Е а |
- |
энергия |
активации; R |
- г а |
|||||||||
зовая постоянная; |
(р (Л) |
- функция, |
выражающая закон протекания |
||||||||||||
(порядок) |
химической реакции. |
|
|
|
|
|
|
|
|
||||||
|
Степень отверждения определяется через плотности связующего |
||||||||||||||
в жидком |
|
и твердом |
j0 |
состояниях |
по формуле |
|
■ Р ~& к,
оС =
•Рг~Ям
Система уравнений (17) - (18) замыкается краевыми условиями, включающими начальное распределение температуры в степени от верждения:
|
|
Т (е)( ? = 0 ) = Т „ |
|
сС(? = 0) = 0 , |
(19) |
|||
Граничные |
условия конвективного теплообмена: |
|
|
|||||
|
|
|
|
|
|
|
|
( 20) |
|
|
|
|
|
|
|
|
( 21) |
где |
J - |
коэффициент теплоотдачи; |
Л |
- коэффициент теплопровод |
||||
ности; Тп , Тс - температура |
поверхности л |
окружающей среды со |
||||||
ответственно. |
|
|
|
|
|
|
||
|
Граничные условия контактного теплообмена с учетом теплово |
|||||||
го |
сопротивления контакта |
R K \ |
|
|
|
|
||
|
|
г з г Ц _ |
. |
2 Т ® |
|
Т<« -т р |
(22) |
|
|
|
л 1 д г |
Л1 |
Э г |
~ |
RK |
, Л = £, , |
|
|
|
|
|
|||||
условия для степени отверждения: |
|
|
|
|
||||
|
|
С/d |
0. |
г |
|
i |
= 1,2 |
(23) |
|
|
d r = |
|
|||||
|
|
|
|
|||||
|
Тепловое сопротивление контакта |
RK определяется из |
зависи |
|||||
мости |
|
|
|
|
|
|
|
|
|
|
|
|
|
|
|
|
(24) |
где S - толщина материала на границе композит - оправка; Лк - коэффициент теплопроводности материала на границе композит - оправка.
Иопользуя подстановку
d * |
_ d c c |
|
d T Ю |
|
d v |
|
d T (e) |
d v |
|
запишем уравнение (17) |
в |
виде |
|
|
* & |
= W |
T |
* , |
|
Эт |
|
|
|
|
где |
|
|
|
|
|
|
1 - |
^ |
dT™ |
|
|
|
Сг |
|
Особенностью дифференциальных уравнений (1 8 ), (25) является |
их нелинейность. Она обусловлена не только наличием конвективных членов, но и неоднородностью теплофизических свойств композитно го материала при изменении агрегатного состояния в процессе от верждения. Другой особенностью является сопряженность, предпола
гающая совместное решение системы уравнений. |
|
Система дифференциальных уравнений (1 7 ),(1 8 ) вместе |
с крае |
выми условиями дает математическую формулировку задачи. |
Постав |
ленная задача нелинейна не только в уравнениях переноса |
и хими |
ческой кинетики, но и в граничных условиях. Сопряженность и не линейность существенно затрудняют решение краевой задачи и пред полагают использование численного метода.
Основная идея численной реализации поставленной задачи ме тодом сеток состоит в замене исходных дифференциальных уравнений и краевых условий их конечно-разностными аналогами и последующем решении сеточных уравнений. Для численного решения задачи область разбивается на регулярные ячейки сеткой (рис.35):
где |
h^, |
h<p - шаги сетки в направлении соответственно осей Z , |
(р ; L |
, |
N , М - числа разбиений в направления координат соответ- |
ственно г , л , </>; L |
, J. |
- |
номера узловых точек; |
vK - |
конечное |
||
время отверждения. При разбиении |
области |
по радиусу |
г ввели сгу |
||||
щающуюся к внутреннему радиусу сетку, используя подстановку: |
|||||||
|
Z |
= |
Спг' |
|
|
|
|
Тогда для композита, |
ограниченного радиусами Rf и |
R% |
получим |
||||
Zj |
- |
tn Rt |
Z2 = tn R z |
|
|
||
|
/ |
|
|
tn |
R jR i |
|
|
|
пг |
|
N |
~ |
N |
|
|
Для оправки |
|
|
_ |
|
|
|
|
|
|
U |
Rf/Rg |
|
|
|
|
|
|
П1 ----- p |
; |
|
|
где p - число разбиение по радиусу в оправке.
С
Рис.35. Схема разбивки
При дискретизации уравнений использовали право- я левосторон ние разности, исходя из схемы расщепления (рис.36):
k n = Ъ г Ч = ^ ' - ^ |
= |
|
кл = |
= |
zli -eZrkz= eZi( f - i / e k2) |
ioo