
книги / Технология производства полимерных композитных материалов и конструкций на их основе
..pdf1)сматывание армирущего материала со шпулярника и подача его в ванну со связующим;
2)пропитка армирующего материала;
3)сушка пропитанного армирующего материала;
4)намотка препрега на катушку.
При производстве препрегов армирующий материал устанавлива ют на шпулярник, одновременно с которого могут сматывать до 1000 нитей, до 10 жгутов. При этом бобины с армирующим материалом ос таются неподвижными, а армирующий материал стягивают с их наруж ной поверхности в осевом направлении (рис.2 9 ).
Г7ТГТ77ТГГТ77ТГГ77777ГГ
Рис.29. Установка для получения препрега: / - бобины о армирующим материалом, установленные в шпулярника; 2 - пропиточная ванна о отжим ными валиками; S - раскладчик нитей, формиру ющий из них ленту; 4 - лента; 5 - цилиндри ческая камера сушки; Б - катушка с лентой препрега на намоточном устройстве; 7 - кало рифер; 8 - нагнетающий вентилятор; 9 - отса
сывающий вентилятор
Перед пропиточной ванной армирующий материал проходит через гребенку, где он формируется в однонаправленную ленту, пропуска ется через тормозное устройство с целью создания некоторого тех нологического натяжения, которое необходимо для улучшения усло вий формирования препрега. Полимерное связующее наносится на на полнитель в количестве 2 8 ...3 7 м ао .£ .
Сушка нанесенного связующего ведется при прохождения армярущ его материала через термокамеру, имеющую зоны с регулируемым температурным режимом, выбор которого связан с типом связующего я со скоростью движения наполнителя. По конструхтивноцу исполне нию термокамеры могут быть как вертикального, так и горизонталь ного типа с заданным внутренним объемом обогревательных секций. Длина пути препрега по секциям камеры зависит от температуры суш ки я скорости перемещения материала, которая может плавно регули роваться от 0 ,3 до 2 ,4 и/мин. Меньшие значения относятся к фенолоформальдегядным связующим, а большие - к эпоксидным. Длина пу ти препрега в распространенных четырехсекционных шахтных уста
новках достигает 16 м. |
В сушильных камерах температура сушки свя |
зующего изменяется по |
зонам и достигает 3 2 8 ...4 2 3 К. Использует |
ся электрический и газовый обогрев. Последний предпочтительнее, |
так как уменьшается пожароопасность. Остаточная концентрация ле
тучих продуктов после сумки составляет 1 ,2 -1 |
,5 %, однако |
дохо |
дит до 6-8 %. |
|
|
Готовый препрег наматывается на бобины диаметром до |
400 мм. |
|
В таком виде препрег хранится ж поступает на |
"сухую" намотку |
|
конструкции. |
|
|
Условия хранения и срок годности препрега регламентируются.
Хранить препрег |
до намотки можно не более |
10 суток при 291-305 К |
и относительной |
влажности до 70 % или до |
20 суток в холодильнике |
при 271-283 К. Оптимальное же время хранения препрега обычно рав но 3-4 суткам и редко превышает 5-7 суток.
Применение препрегов в технологическом процессе намотки кон струкций требует эффективного размягчения связующего и более зна чительных давлений формования наматываемого композитного матери ала, чем при "мокром" методе. Ограниченность относительного пере мещения нитей арматуры в препрега делает возможным применение его при намотке только относительно простых по форме конструкций. Применение препрегов позволяет повысить качество получаемых кон струкций и совершенствовать технологию намотки.
Для эффективного использования препрегов необходимо иметь достаточную информацию об их технологических свойствах по таким показателям, как текучесть, температура размягчения, содержание влаги я летучих, содержание растворимой частя связующего, ско рость отверждения я т .д .
Роль технологического натяжения армирующего материала при намотке очень велика. Натяжение определяет коэффициент армироваяня, который растет с увеличением натяжения. Однако превышение некоторого максимума технологического натяжения приводит к до полнительным повреждениям армирующего материала при движении по фопиточно-формущему тракту станка и к появлению участков, не смоченных связующим и создающих неоднородность композитного ма териала по толщине наматываемой оболочки.
Практически номинальные значения технологического натяжения чаще всего выражают в долях разрывной нагрузки применяемой арма туры ( Рр ). Для стеклянных нитей оптимальное натяжение варьирует
ся в пределах ( 0 ,1 2 ... |
О,5) Рр (иногда до 0 ,7 для |
прочных |
и вы |
сокомодульных волокон) |
и на практике составляет 2 |
,4 ... 5 ,9 |
Н/нять, |
хотя используются и значения 1 ,4 ... 3 4 Н/нить. |
|
|
Для препрегов натяжение обычно выбирается в интервале 0 , 2 . . .
0,4 Рр , что составляет от 19 до 245 Н/см ширины и даже до 390 Н/см ширины. При этом большие значения натяжения соответству
ют окружной укладке арматуры на оболочку, а меньшие - продольной. Выбор в каждом конкретном случае оптимальной величины натя
жения зависит от многих обстоятельств. Наличие дополнительных спрессовывающих устройств, которые могут создавать контактные давления 2 0 ...4 0 0 Н/см ширины или до 4 . . . 5 МПа, снижают величи ну требуемого технологического натяжения.
Величина натяжения может быть связана с достижением оптимума одной или нескольких характеристик материала. Так, например, ус тановлено, что наибольшую однородность материала по толщине стен
ки удается получить при натяжении |
0 ,1 ...0 ,2 5 |
Рр , э то зремя как |
|
для получения минимума пористости |
требуется |
натяжение менее 10 |
|
или более 20 % от |
Рр . |
|
|
Выбор номинального значения натяжения при намотке связан так |
|||
ие с характером его изменения как |
по толщине, так и во времени. В |
||
процессе намотки |
с постоянным натяжением происходит выдавливание |
связующего и "просадка" нижележащих слоев в радиальном направлении, что приводит к уменьшению предварительно заданной величины натяже ния от верхних слоев материала к нижним.
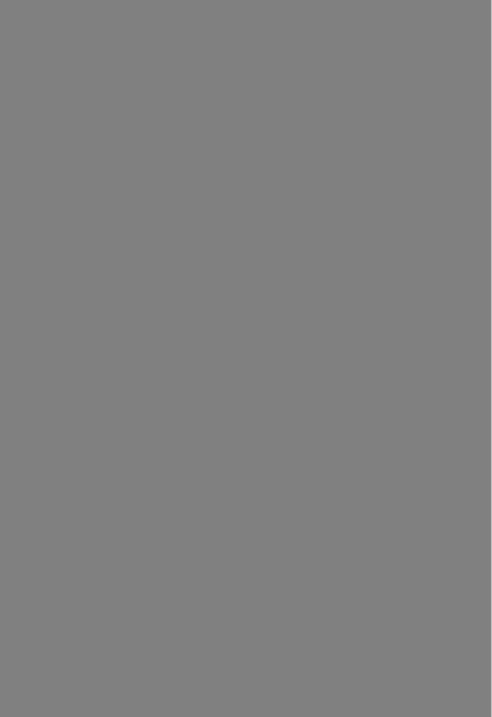
няться от слоя к слою по определенной программе) ленты ллл поло сы армирующего материала, предварительно пропитанной жидким свя зующим. Полагаем, что уоллле латяхевня воспрляямается только сис темой волокон армирующего матерлала, которые наделяется свойст вами линейной упругости н анизотропии. Полимерная матрица счита ется изотропной сжимаемой вявкопластичвой жидкостью, которая з а нимает все пространство между волокнами армирующего материала.
Намотку моделировали последовательным |
надеванием с |
натягом |
тон |
ких анизотропных колец. Под действием |
контактного |
давления |
ф0 = |
» Т0 /г ( Г - радиус, по которому укладывается лента) происхо |
дит сжатие |
полуфабриката в радиальном направления я миграция свя |
|
зующего из |
внутренних слоев во внешние. |
|
Система уравнений, описывающая фильтрационные процессы во |
||
время намотки |
полуфабриката, будет включать: |
|
- закон |
фильтрации сжимаемой вязкопластичной жидкости: |
где |
X |
- |
коэффициент фильтрации, |
MV H* C , |
Х^~ |
|
< К - про- |
|||
ницаемость |
армирующего материала, |
м2 ; ju - |
вязкость |
полимерной |
||||||
матрицы, |
Н 'с/м2 ); |
Pfr,'P) |
- поровое |
давление, |
являющееся функ |
|||||
цией текущего радиуса конструкции л |
и времени |
'Р , |
параметры |
|||||||
л |
, 't |
опущены, |
Н/м2 ; |
=<^Т0/\Гк |
(где |
- |
некоторая посто |
|||
янная « I ; |
Т 0 - |
предельное напряжение сдвига, |
значения которого |
получают экспериментально). Движение жидкости начинается тогда,
когда перепад давления д Р /<5 Л |
достигает |
критического значе |
н и я^ . При выполнении условия |
I Э Р /Э г \ |
i ft течения не про |
исходит; - уравнения состояния для учета сжимаемости армирующего ма
териала и полимерной матрицы:
m = % * СА М ( р - Р0 ] >
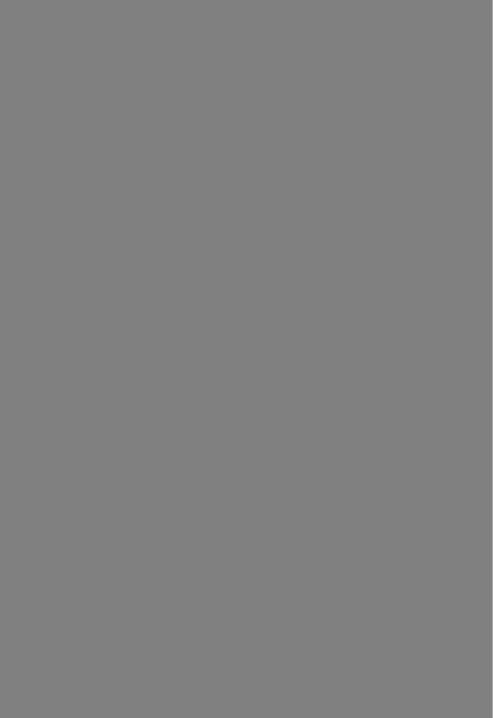
фильтрационные процессы, результатом которых является перемеще ние слоев армирупцего материала к центру. При этом происходит из менение коэффициента армирования по толщине стенки конструкции.
В просадку слоев на стадии намотки вносит свой вклад и упругое обжатие полуфабриката под действием контактного давления при на
ложении |
очередного слоя. |
|
|
|
|
J. -м слое |
|
|
||
|
Касательное напряжение при намотке в |
определим |
||||||||
по формуле |
|
|
|
|
|
|
|
|
||
|
|
|
= |
|
|
Ev |
l t |
|
|
III) |
где |
7V |
- начальное натяжение |
j |
-го слоя; |
h - толщина |
слоя |
||||
наполнителя; |
Е^- модуль упругости в окружном направлении; |
|||||||||
U■ |
- полное перемещение J. -го слоя; |
R- |
- радиус J |
-го |
слоя. |
|||||
^ |
Радиальное напряжение найдем из уравнения равновесия эле |
|||||||||
мента наполнителя для полных напряжений: |
|
|
|
|||||||
|
|
|
вл* — в |
л^ 1 + |
<32 |
|
|
( 12) |
||
|
|
|
|
|
|
|||||
Расчет радиальных напряжений удобно вести |
с внешнего |
слоя, где |
||||||||
(V |
= 0. |
|
|
|
|
|
|
|
|
|
|
Полное перемещение будет состоять из смещения в результате |
|||||||||
фильтрации US |
и смещения из-за упругого |
обжатия |
и*п |
|
||||||
|
|
|
Ы = |
uL |
+ |
иi |
|
|
|
|
|
|
|
и |
ир |
|
ыуп |
|
|
|
Просадку J. -го слоя наполнителя от фильтрации можно вычис лить через изменение толщины прослоек связующего в нижележащих слоях:
u<t |
Z Z |
A S-L |
(14) |
р |
t -1 |
L |
|
|
|
ASi можно определить из скорости фильтрации в крайних точках слоев наполнителя, прилегающих к 1-А прослойке:
Так как в результате решения уравнения (7) при условиях (8)- (10) станет известно поле давлений, то по (4) можно перейти к рассмотрению скоростей фильтрации. Таким образом, можно опреде
лить |
величину |
U * . |
|
|
|
|
|
|
|
|
|
|
Величину |
u ja можно определить |
следующим путем. Перемеще |
||||||||
ние от надеваемого кольца, |
создающего давление |
(j,Q= ^о/ |
* |
||||||||
вызывает на радиусе Г' |
при учете податливости оправки радиальное |
||||||||||
перемещение |
|
|
|
|
|
|
|
|
|
||
|
|
|
|
|
|
|
|
|
|
|
' тг' |
|
|
|
|
|
|
t y y |
s |
t - -Pi |
> |
|
|
где |
°^АМ коэффициент анизотропии армирующего материала |
°°AM |
|||||||||
= Еы/ VС |
£ - модуль упругости в радиальном направлении; |
||||||||||
|
|
|
._ °^АН |
+АОП |
Р. = Л . |
|
Л |
|
|||
|
|
|
<*АМ ~$0П |
Л |
р. |
|
/ а т |
|
|||
|
|
|
|
|
|
|
|||||
fan ~ параметр, характеризующий жесткость |
оправки, которая счи- |
||||||||||
тается изотропной с модулем упругости |
Еопр |
и коэффициентом Пу- |
|||||||||
ассона |
$0Пр |
|
|
|
2, |
п2 |
|
|
|
|
|
|
|
|
_ |
J* . |
|
|
|
|
|||
|
|
|
|
|
|
|
|
|
|||
|
|
|
*оа |
ЕопР \иг~и] |
опр) |
|
|
||||
|
Радиальное перемещение j |
-го слоя |
|
|
|
||||||
|
|
|
|
U* |
|
п |
|
|
|
|
|
|
|
|
|
= |
A U; |
|
|
|
|||
|
|
|
|
иуп |
|
|
|
|
|
|
|
где |
п - конечное число слоев наматываемой конструкции* |
|
|||||||||
|
Таким образом, определено радиальное перемещение каждого |
||||||||||
слоя. Подставляя (14), (16) в (13), а |
(13) в (II) и (12), можно |
||||||||||
получить вид распределения окружных и радиальных напряжений |
по |
||||||||||
толщине |
стенки конструкции. |
|
|
|
|
|
|
||||
|
Необходимо отметить,^что на стадии намотки происходит перио |
||||||||||
дическое |
(через время, |
равное |
времени прохождения ленты над |
од |
ной и той же точкой) изменение краевых условий в связи с тем, что происходит постепенное наращивание толщины конструкции. Счи таем, что намотка происходит в изотермических условиях, т.е. решаем задачу без учета переноса тепловой энергии. Для решения
уравнений (7) - (10) приняли явную конечно-разностную схему С ограничением на шаг по времени:
(лг!2
h„ * г х п
В качестве примера приведем расчет процесса намотки конст
рукции со |
следующими данными: |
h = 0 |
,2 5 ‘ Ю-3 |
м; начальная тол- |
|
кщна прослоек |
связующего SH = 0,125* К Г 3 м; |
Х^,= 10*^% *с/м ^; |
|||
Rf = 0 , 5 |
м; |
£ р = 2*Ю 4 МПа; |
= |
200 МПа; |
fg = 2 5 .I0 3 Н/м. |
На рис. 31 дано распределение порогового давления по толщи не полуфабриката в зависимости от количества слоев. Согласно на шим данным, давление монотонно изменяется по всей толщине нама тываемой конструкции* Здесь также видно, что граница между учас тком, где возникает упругий отпор, и участком, где сохраняется ''свободная" прослойка связущ его, размыта и з-за непостоянства норового давления, но она также смещается в сторону оправки с увеличением числа наматываемых слоев.
Рис. 31. Распределение порового |
Рис.32. Распределение |
коэффици |
|||
давления по толщине полуфабри |
ента армирования по толщине по |
||||
ката в зависимости от количест |
луфабриката в зависимости |
от |
|||
ва слоев. Цифры у кривых - |
зна |
времени, прошедшего после |
намот |
||
чение л |
|
ки последнего слоя. Цифры у кри |
|||
|
|
вых - значение времени в часах, |
|||
|
|
ж, - начальный коэффициент ар |
|||
|
|
мирования |
|
|
|
Анализ распределения коэффициента армирования |
уг |
по толщине |
|||
полуфабриката после окончания намотки ( п =» 80) показывает |
(ри с.32) |
||||
что после окончания намотки |
во |
внутренних слоях |
он |
составляет |
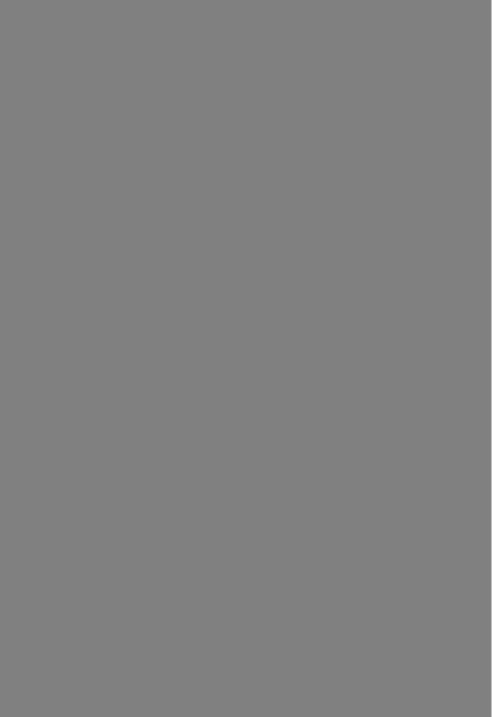