
книги / Технология производства полимерных композитных материалов и конструкций на их основе
..pdfДля выбора эффективных методов я средств контроля качества необходимо учитывать: физико-механические свойства материалов, характерные особенности внутренней структуры и структурных де фектов, геометрические параметры изделий, особенности технологии изготовления изделий. Учитывая, что изготовление конструкций происходит в несколько этапов, необходимо проводить контроль ка чества на всех этапах с целью своевременного устранения, если это возможно, обнаруженных дефектов.
4.5. Прогнозирование п р о ч н о с т и
Показатели прочности материала и изделия являются основными при оценке несущей способности или работоспособности изделия. По казатель прочности материала характеризует предельное напряжение, выдерживаемое образцом при его нагружении. Показатель прочности изделия характеризует предельную нагрузку, при которой произошла потеря несущей способности или работоспособности. Потеря несущей способности возникает, когда действующее напряжение превосходит предельное (прочность) материала, что приводит к нарушению сплош ности и разрушению изделия.
В настоящее время диагностика прочностных характеристик ма териала развивается в следующих основных направлениях:
1)по однопараметровой эмпирической корреляции между наибо лее информативным физическим параметром и прочностью материала;
2)по многопараметровой эмпирической корреляции между комп лексом физических характеристик (скорость, затухание УЗК, ди электрическая проницаемость, коэффициент тепло- и температуро проводности и др.) и прочностью материала;
3)по функциональным аналитическим зависимостям.
Анализ показал, что наиболее значительное влияние на проч ность изделий из ПКМ оказывают физико-механические свойства ма териала, их анизотропия, дефекты ПКМ. Современные методы оценки прочности изделия связаны с его разрушением предельной нагрузкой.
Из неразрушащих методов наиболее широкое распространение получили тензометрический, акустический, многопараметровый. Эти методы основаны на установлении эмпирических корреляционных со отношений между предельной разрушающей нагрузкой и комплексом физических параметров (скоростью ультразвука, теплопроводностью,
диэлектрической проницаемостью, относительной деформацией и др.).
Однако и это общий недостаток указанных |
методов, при прогнозиро |
|
вании прочности не учитываются критерий |
прочности материала и |
|
расчетная схема воздействующих эксплуатационных нагрузок. |
||
Таким образом, |
определяя при помощи неразрушающих методов |
|
значения толщины, |
радиуса, показатель анизотропии и прочности |
ПКМ, можно с достаточной для практики точностью оценить проч ность изделия. Прочность материала ( <о0 ) вдоль какого-либо структурного направления может быть определена путем установле ния эмпирической связи прочности ПКМ с комплексом физических параметров (скорости УЗК, деформации, коэффициента теплопроводно сти и др.), определяемых непосредственно в изделии.
Кроме того, (Зд можно определить из образцов-свидетелей, из готавливаемых одновременно с изделием.
Значительный интерес представляет ультразвуковой временной метод, который основан на измерении деформаций при нагрузках, ни же разрушающих, путем установления взаимосвязи между деформацией и прочностью изделия. Этот метод может быть реализован при усло вии постоянства предельной относительной деформации. Основные не достатки метода: низкая точность определения прочности изделий, большая длительность измерений и обработки результатов; кроме того, не учитываются структурные изменения материала, возникаю щие при нагружении и деформировании изделия.
Сущность ультразвукового временного метода заключается в том, что в изделии возбуждают упругие волны при помощи ультра звукового датчика, устанавливаемого нормально поверхности изде лия, и измеряют время их распространения перед нагружением в тангенциальном направлении, перемещая датчики вдоль оси изделия. В местах максимального времени распространения следует ожидать максимальных деформаций при нагружении изделия.
При неразрушающем контроле прочности изделий типа тел вра щения, например, цилиндрической или сферической оболочки, к из делию прикладывают внутреннюю осесимметричную нагрузку, величи на которой ниже предельной - разрушающей. В изделии возбуждают УЗК при помощи раздельного или совмещенного ультразвукового дат чика, устанавливаемого нормально поверхности изделия до приложе ния нагрузки и в процессе нагружения. Для эталонного изделия сни
мают диаграмму "нагрузка - относительное время УЗК" от нулевого значения нагрузки до разрушающей или в зависимости от вида диа граммы устанавливают расчетное уравнение для определения проч ности изделия. Испытательную нагрузку принимают такой, чтобы она была равна или меньше нагрузки, при которой изделие эксплуатиру ется, и значительно меньше разрушающей нагрузки. Оптимальная ис пытательная нагрузка составляет 0,4-0,7 от разрушающей.
Основное достоинство метода в том, что он повышает точ ность контроля прочности изделия вследствие взаимодействия упру гих волн с контролирующей средой и увеличивает производительность и надежность контроля в связи с отсутствием подготовительных опе раций.
4.6. Настройка а п п а р а т у р ы к о н т р о л я
Для настройки аппаратуры контроля предназначен стандартный образец. Он представляет собой имитатор конкретных параметров сборочных единиц изделий.
Стандартные образцы для выявления расслоения, неприклейки ТЗП и ПКМ к металлу должны представлять собой вырезки из нату ральных сборочных единиц с заложенными имитаторами дефектов. До пускается настройка дефектов на плоских стандартных образцах, если радиус кривизны контролируемой поверхности больше 350 мм. Допускается настройка дефектоскопов при контроле теневым мето дом по имитатору дефектов, накладываемому на поверхность контро лируемого изделия или образец, вырезанный из годного участка изделия.
Минимальные размеры искусственных дефектов устанавливают ис ходя из чувствительности применяемых методов контроля и требова ний конструкторской документации, установленных для ПКМ конкрет ных сборочных единиц.
Вкачестве имитаторов дефектов могут быть использованы:
1)пакеты из целлюлозной пленки;
2)пакеты из фторопластовой пленки;
3)зазор между дном углубления, высверленного в ПКМ, и проб кой из того же материала (рис.49);
4)углубление в дне углубления, высверленного в ПКМ, в кото-
рое установлена пробка, вмещая кольцевую проточку, заполненную излишками клея;
5) зазор между подложкой и покрытием, образованный нанесе нием на подложку вещества, разлагающегося при нагреве или легко плавкого материала, расплавляющегося при нагреве (рис.50);
6) регулируемый зазор, полученный высверливанием в подложке сквозного отверстия, в котором укрепляется полая втулка с бурти ком, во внутрь которой вставляется пробка с кольцевым буртиком (рис.51).
Рис.49. |
Схема высверленного де ж - |
Рис.50. Схема дефекта, раз |
та: А |
- диаметр дефекта; ао |
лагающегося при нагреве: / - |
|
диаметр пробки |
соль HHyNOi ; 2 - клей |
Рис.51. Схема дефекта с регули руемым зазором: f - полость де фекта; 2 - пробка; 3 - проклад
ка; 4 - буртик втулки
4.7. Классификация акустических методов к о н т р о л я
Согласно ГОСТ 23829-79 акустические методы делят на две боль шие группы: использующие излучение и прием акустических волн (ак тивные методы) и основанные только на приеме волн (пассивные мето-
ды). В кавдой из этих групп можно выделить методы, основанные на возникновении в объекте контроля бегущих и стоячих волн или ко лебаний.
Активные акустические методы, в которых применяют бегущие волны, делят на методы, использующие прохождение и отражение волн. Применяют как непрерывное, так и импульсное излучение.
4.7.1. Акустический метод отраженного излучения (эхо-импульсный метод)
Он выявляет расслоения в ПКМ на основании (металлическом и неметаллическом) и без основания (рис.52).
Рис.52. Схема эхо-импульс |
Рис.53. |
Импульсный теневой |
||
ного метода: / - излучаю |
метод: |
/ - генератор сиг |
||
щий пьезовибратор; |
1 |
- |
нала; 2 - приемный пьезо |
|
генератор сигнала; |
3 |
- |
вибратор; 3 - излучающий |
регистрирующая аппарату |
пьезовибратор; ^ - регист |
||
ра; |
4 - приемный пьезо |
рирующая аппаратура |
|
|
вибратор |
|
|
|
Метод осуществляется при одностороннем доступе со стороны из |
||
делия для материалов с плотностью больше 100 кг/м3. |
|
||
|
Минимальная глубина залегания |
выявленных дефектов |
3-5 мм. |
Можно |
выявить расслоения в покрытиях и ПКМ толщиной до |
200 мм. |
Контролируются выпуклые и вогнутые поверхности с радиусом кривиз ны 100-150 мм.
Неконтролируемые зоны - участки со сложным профилем металли ческого основания, фланцевые соединения, вшангоуты, элементы креп ления.
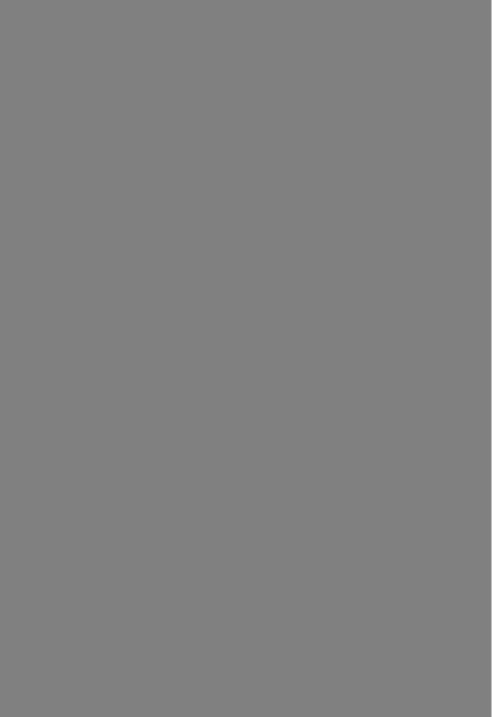
Блок-схема реверберационного дефектоскопа подобна блок-схе ме эхо-импульсного дефектоскопа и отличается лишь тем, что ь ре верберационном дефектоскопе используется недемпфированный (или слаб©демпфированный) пьезовибратор и более длительные разверт ки для наблюдения процесса реверберации.
Выявляются дефекты размером 15x15 мм и более. Толщина ТЗП и ПКМ и металлического основания не более 1/2 длины волны исполь зуемых при контроле акустических колебаний. Контролируются вы пуклые изделия с радиусом 100 мм и более и вогнутые с радиусом 200 мм и более.
Неконтролируемые зоны - участки со сложным профилем металли ческого основания и близлежащие к ним зоны, размер которых равен половине диаметра преобразователя. Шероховатость металла основа ния должна быть не более 40 мкм.
Применяется жидкая контактная смазка (глицерин, индустриаль ное масло, спирт, вода). Для повышения чувствительности метода при контроле сборочных единиц, имеющих тонкие или эластичные по крытия, нанесенные на внутреннюю поверхность, рекомендуется пе ред контролем вакуумировать полость сборки для увеличения рас крытия участков неприклея.
4.7.4. Радиационный метод
Радиационный метод позволяет выявить:
1)расслоения в ПКМ на основании (металлическом и неметалли ческом) и без основания;
2)неприклей ТЗП и ПКМ к основанию;
3)пазы и раковины в ПКМ.
При радиационном методе в качестве источника излучения ис пользуют ^-излучение с энергией частиц 0,2-0,4 МэВ. Этот метод допускает применение двух схем просвечивания: тангенциальной и нормальной. При тангенциальной схеме (рис.54) излучение направля ется перпендикулярно к радиусу по касательной между покрытием и изделием. Эта схема просвечивания позволяет определять глубину залегания дефектов, величину их раскрытия.
Плотность контролируемого материала более 300 кг/м3. На чувствительность метода влияет кривизна, отношение толщин мате риала и основания, плотность материалов. Тангенциальная схема
просвечивания позволяет выявить расслоения и непроклеи размерами более 16x16 мм, с раскрытием 0,2 % и более.
Рис.54. Радиационный метод (тангенциальная схема про свечивания): 1 - рентгенопленка; 2 - стандартный об разец чувствительности; 3 - покрытие; 4 - источник; 5 - изделие
При тангенциальном просвечивании максимально допустимый диа метр не более 2500 мм, эффективная толщина просвечивания 300 мм и менее. Производительность метода низка.
Нормальная схема просвечивания применяется только для выяв ления дефектов типа раковин и не позволяет определить глубину за легания дефектов (рис.55).
Рис.55. Радиационный метод (нормальная схема просвечи вания): / - изделие; 2 - покрытие; 3 - стандартный образец чувствительности;
if - источник; 5 - рентгенопленка
Подбор оптимальных режимов просвечивания производится с по мощью контрольного образца чувствительности, который изготовляет ся у каждого типа изделия, подлежащего контролю. Если невозможно установить стандартный образец, допускается просвечивание без не го. В этом случав выбор режимов просвечивания осуществляется с помощью контрольных образцов на изделии, геометрическая форма ко торого близка к геометрической форме контролируемого изделия.
4.8. Ультразвуковая дефектоскопия
Излучателем импульсов УЗК является пьезоэлектрический преоб разователь, возбуждаемый радиоимпульсами специального генератора. Отраженные эхо-импульсы принимаются тем же пьезопреобразователем, подаются в виде радиоимпульсов на экран индикатора.
Для контроля неприклеев используются приборы УД-22УМ (УД23УМ); преобразователи типа ДП1, ДКП с диаметром 40 мм (для луч-
руется качество приклея внутренних покрытий к металлической и неметаллической стенке (рис.56).
Рис.56. Схема контроля ультразву ковым дефектоскопом: 1 - прибор; 2 - преобразователи; 3 - конт ролируемое изделие; ^ - металл
Контроль проводится вручную, т.е. преобразователи перемеща ются по контролируемой поверхности контролером. Возможен контроль как цилиндрических, так и конических изделий. Контроль осуществ ляется по всей поверхности перемещением и вращением контролируе мого изделия вручную. Изделие во время контроля может быть уста новлено на стол или в специально предназначенные для данной опе рации приспособления.
В технологическом процессе производятся следующие записи: Контролировать з о н ы ..... . з о н ы ..... - неконтролируемые
(на схеме должны быть указаны данные зоны). Приспособление: имитатор дефектов НК-0120.
Процент контроля |
- 100. |
|
|
|
Особые указания: допускаются |
единичные дефекты площадью не |
|||
более 80 мм; общей площадью не |
болэе 350 мм^; дефекты |
по |
||
всей длине не допускаются. |
|
|
|
|
Время контроля: |
45 мин |
(время определяется отдельно |
по |
зонам).
Чувствительность: минимальный выявляемый дефект (20x20) мм. Если в результате контроля были выявлены дефекты, то в пас
порте на изделие заполняется схема расположения дефектов (рис.
57) и табл.12.
Отсчет координат производится от условно принятой начальной линии, которую проводят карандашом на наружной поверхности из делия.
Достоинство данного метода - простота и поэтому не требуется» высокой квалификации контролера.
Недостатки приведенного метода: преобразователи перемещаются
вручную, поэтому возможна несоосность их, в результате чего пока зания прибора оказываются неверны.
Таблица 12 Координаты залегания дефектов и их площадь
X , мм
У, мм
S, мм^
Рис.57. Схема рас положения дефектов
4.9. К о н т р о л ь п р о ч н о с т и (на примере стеклопластиков?
Стеклопластики являются ортотропными материалами, прочност ные и упругие свойства которых зависят от направления армирующих волокон.
Прочность стеклопластиков проверяют акустическим испульсным методом. При этом измеряют два параметра материала: скорость звука и коэффициент затухания.
Исходную прочность оценивают по формуле
* - т г г )
Излучающий и приемный преобра зователи устанавливают на очищен ную и смазанную маслом поверхность стеклопластика (рис.58).
Расстояние L0 между преобра зователями обычно составляет 200 мм. Скорость звука С = L0/1 . Для из мерения затухания один из преобразо
вателей устанавливают на расстоянии Lf= L0/2 . Измеряя с помощью аттенюатора изменение амплитуды принятого сигнала, находят значе ния оС .
Модуль Юнга вычисляют по полученным значениям С и плотности J). Коэффициенты А и В определяют на образце, изготовленном по