
книги / Очистные механизированные комплексы ОКП70
..pdfверхностей электродуговой сваркой и последующей механической обработкой; вибродуговой наплавкой деталей с последующей ме ханической обработкой до размеров по чертежу; хромированием или осталиванием изношенных поверхностей с последующей допол нительной обработкой или без нее; правкой.
Наплавку поверхностей следует производить при условии, что не нарушаются размерность и механические качества других по верхностей и наплавка не вызывает неисправимой деформации детали.
Изношенные поверхности отверстий перед наплавкой следует' расточить до диаметра на 3—5 мм больше номинального. В наплав ленном металле трещины и шлаковые включения не допускаются.' На нетрущихся поверхностях допускаются отдельные раковины общей площадью не более 10% площади наплавленной поверхности. Восстановленная поверхность вне зависимости от метода восстанов ления должна иметь твердость не ниже указанной в чертеже или в карте браковочных признаков. Поверхности, подлежащие восста новлению хромированием, должны быть чисто отшлифованы и отпо лированы (местные поджоги при шлифовке не допускаются), обез жирены, тщательно промыты в горячей воде и очищены от окис лов. При восстановлении деталей наращиванием запрещается при менять многослойное хромирование. Хромирование производится только на основной металл. Наращенный слой хрома должен быть не более 0,25 мм, включая припуск на последующую механическую обработку.
Поверхности, восстанавливаемые осталиванием, должны быть’ предварительно механически обезжирены, промыты в горячей воде и протравлены в концентрированной соляной кислоте. Обезжири-* вание и травление должны производиться непосредственно перед завесом деталей в ванне. Восстановление осталиванием должно про изводиться при точно выдержанных режимах, обеспечивающих гладкую (беспористую) поверхность слоя. Толщина наращенного слоя после окончательной обработки должна быть в пределах 0,5—' 1 мм. После процесса осталивания детали должны быть промыты в горячей воде, нейтрализованы в 10%-ном растворе соды и терми чески обработаны до +300°С с выдержкой до 1 ч. Поверхность наращенного слоя должна быть гладкой, без наплывов, раковин, трещин, отслоений, светло-серебристого цвета. Поверхности, под вергшиеся осталиванию, можно термически обрабатывать, цемен тировать и хромировать.
Восстановление забитых или сорванных резьб в деталях разре шается производить в зависимости от степени износа следующими
методами:
прогонкой метчиков или плашкой; наплавкой или заплавкой с последующей нарезкой резьбы в со
ответствии с чертежом. При восстановлении наружных резьб из ношенная резьба должна быть сточена;
постановкой заглушек в рассверленное отверстие с обваркой по диаметру и последующим сверлением и нарезкой новой резьбы;
внутренних резьб — рассверливанием или расточкой под бли жайшую большую резьбу;
наружных резьб — обточкой под ближайшую меньшую резьбу; при условии обеспечения необходимого запаса прочности;
резьб на деталях сварных сборочных единиц — заменой деталей с неисправной резьбой и приваркой по рабочим чертежам.
Восстановление трубопроводов допускается вырезкой изогнутых и смятых участков с последующей вваркой трубы номинального се чения.
Восстановление изогнутых осей, пальцев, валов допускается их! распрямлением в холодном состоянии.
При наличии трещин и разрывов в сварных швах допустимо сварные швы разделывать иа всю длину трещин, а затем заварить вновь. При расположении трещин на конце сварного шва заварива ние производить в направлении оставшегося шва. При разделке трещины в середине шва заваривать следует от середины к концам.'
Восстановление сварных сборочных единиц с деформированный ми или разрушенными деталями следует производить выплавлением^ или заменой деталей с приваркой их по рабочему чертежу. При восстановлении ремонтируемых и при изготовлении новых сварных* сборочных единиц допускается применение ручной электродуговой сварки.
Перешлифовка и переточка поверхностей штоков, цилиндров й‘ т. п. на больший (или меньший) диаметр и применение дополнитель ных деталей допускаются в том случае, если это предусмотрено ремонтными чертежами. Обработка латунных поясков на втулках абразивным инструментом не допускается. Методы восстановления деталей должны соответствовать рекомендуемым методам в картах1 браковочных признаков. Технология восстановления деталей раз рабатывается ремонтным предприятием исходя из освоенных про грессивных методов восстановления деталей, наличия оборудования, оснастки, мерительного инструмента и т. п.
12.4. Прием сборочных единиц после ремонта
Все сборочные единицы гидрооборудования механизированной крепи должны подвергаться приемосдаточным испытаниям в соот-’ ветствии с Программой и методикой испытаний, которая должна поступать с ремонтной документацией на ремонтные предприятия. Приемку всех деталей и сборочных единиц, изготовленных при ремонте или признанных годными без ремонта, должен произво дить ОТК ремонтного предприятия на соответствие требованиям рабочих и ремонтных чертежей. Все детали и сборочные единицы прошедшие приемку, должны иметь клеймо ОТК. Место клеймение устанавливается чертежом. Допускается не клеймить детали метал локонструкции, входящие в неразъемные сборочные единицы, а так же детали, на которых нанесение клейма невозможно. Контроль качества сварных швов должен производиться в соответствии с ГОСТ 3242—79.
Кинематическое взаимодействие передач редуктора конвейера
проверяется прокручиванием вручную. Зубчатые колеса при этом должны обкатываться плавно, без заеданий. Подшипники коничес кой передачи редуктора должны быть отрегулированы так, чтобы коническая вал-шестерня и колесо не имели осевого люфта и легко вращались от руки. Размеры, форма и расположение пятна контак та на конических и цилиндрических зубьях передач при проверке их' по краске, а также боковые зазоры должны соответствовать нормам. Проверка пятна контакта по краске производится выборочно на двух редукторах, но не реже одного раза в месяц.
Испытаниям, совмещенным с обкаткой, подвергаются приводной блок в сборе (редуктор, гидромуфта с проставкой, электродвига* тель) и привод в сборе. До проведения испытаний необходимо за лить смазочные материалы в редуктор и гидромуфту. Испытаниям должен предшествовать пробный пуск. При обнаруженных дефек тах (стук, заклинивание передач и др.) испытания должны быть прекращены до устранения дефектов. Приводной блок в сборе ис пытывается на испытательном стенде вхолостую и под погрузкой. Обкатка должна производиться на каждой ступени в обе стороны, включая и обкатку вхолостую. Продолжительность обкатки в каж дую сторону должна быть равна половине времени обкатки на дан ной ступени. Испытания приводного блока считаются удовлетвори тельными, если выполнены следующие требования:
рабочие поверхности зубьев не имеют сколов, трещин, задиров и приобрели гладкую блестящую поверхность пятен контакта;
пятна контакта в зубчатых передачах по размерам и располо* жению соответствуют нормам;
отсутствует течь масла через уплотнение и фланцевые соедине ния; 4
шум в передачах при испытании был ровным, низкого тона, без периодических нарастаний и убываний;
температура масла в редукторе в период испытаний не превы шала 60°С, в подшипниках 80°С сверх температуры окружающего воздуха.
Привод конвейера в сборе должен быть обкатан вхолостую в течение 15 мин в обоих направлениях вращения. Перед обкаткой привода должен производиться пробный пуск. Перед пробным пус ком необходимо проверить надежность крепления приводных бло ков к раме, правильность установки звездочек, съемников, козырь ка. Все выявленные нарушения должны быть устранены до начала испытаний. Привод должен плавно запускаться, работать без за еданий вращающихся частей, съемники цепи должны свободно' перемещаться в горизонтальной плоскости. Защитные ограждения (крышки проставок гидромуфты, кожухи вентиляторов на двига телях) должны быть надежно закреплены. Из каждой партии в 50 отремонтированных приводных блоков 1 блок испытывается на передачу максимального крутящего момента, развиваемого выход ным валом редуктора.
Все сборочные единицы и детали после ремонта должны быть подвергнуты окраске или консервации в соответствии с требовани-'
ями рабочих чертежей. Покрытие внешних необработанных по верхностей верхних и боковых листов, перекрытий, козырьков, верхняков и ограждений, контактирующих с кровлей, всех поверх ностей оснований, траверс рычагов, ограждающих щитов — лак! ВТ-577, ГОСТ 5631—79. Покрытие поверхностей сборочных единиц внутри крепи (кроме трущихся) — эмаль НЦ-132П, ГОСТ 6631—74* белого цвета, по грунту ГФ-0119, ТУ 6-10-1399—77. Допускаются цветные эмали светлого тона.
Наружные поверхности сборочных единиц гидрооборудования должны быть окрашены эмалью НЦ-132П (ГОСТ 6631—74) сле дующих цветов:
гидроцилиндры, магистральные трубы и отводы линейных сек ций — светло-серого;
отводы первой лавной секции (в крепи сопряжения конвейер-' ного штрека) — зелено-голубого;
отводы крепи вентиляционного штрека и концевых секций —1 золотисто-желтого.
Допускается замена цветов покрытий с сохранением различия' по перечисленным группам.
Все механически обработанные поверхности и поверхности, не имеющие лакокрасочного покрытия, должны быть подвергнуть! консервации нанесением консервационных масел в соответствии с: ГОСТ 9.014—78 при условиях хранения, указанных ниже, и обе спечивать срок защиты один год без переконсервации. В качестве консервационной смазки рекомендуется использовать К-17 (ГОСТ 10877—76) или ПВК (ГОСТ 19537—74).
Внутренние полости всех сборочных единиц гидрооборудования1 после сборки и испытания должны консервироваться смесью инду стриального масла И-20А (ГОСТ 20799—75) с 10% присадки КП-2 (ТУ 38-1019—80). Все полости сборочных единиц гидрооборудова-' ния после консервации должны быть заглушены во избежание по падания загрязнений.
12.5. Маркировка, упаковка, транспортирование и хранение
На каждой отремонтированной крепи на перекрытии первой лавной секции (рядом с табличкой завода-изготовителя) должна быть установлена табличка по ГОСТ 12971—67, содержащая:
товарный знак ремонтного предприятия; обозначение крепи;
номер крепи по системе нумерации ремонтного предприятия; год проведения ремонта.
Все отводы гидрооборудования, кроме отводов линейных сек ций, должны иметь маркировку согласно требованиям рабочих чер-? тежей. Резинотехнические и пластмассовые изделия (уплотнитель ные кольца, манжеты и т. д.) должны иметь маркировку на бир ках, в которых указаны соответствующие размеры или обозначение деталей.
Крупногабаритные сборочные единицы (основания, перекрытия'
в сборе, козырьки) транспортируются без упаковки. Допускается отгрузка секций, собранных в транспортное положение (рис. 12.1)
Траверсы рекомендуется упаковывать в проволочные связки.' Магистральные трубопроводы, гидроцилиндры, сборочные еди ницы механизмов удержания забоя упаковывают в брусковые5
связки.
Мелкие сборочные единицы и детали должны упаковывать в дощатые деревянные ящики, изготовляемые в соответствии с ГОСТ 2991—76 или ГОСТ 10198—78.
Мелкие детали (пружины, проволочные кольца, инструмент,* метизы) должны быть скомплектованы по типоразмерам и завер нуты в пакеты из парафинированной бумаги БП-б (ГОСТ 9569—79).
В каждый ящик должен быть вложен |
|
документ, |
содержащий |
|||
перечень и число упаковочных изделий. |
Эксплуатационная |
доку-] |
||||
ментация укладывается в пакет из |
полиэтиленовой |
пленки, по |
||||
|
Допускается |
по |
согласова |
|||
|
нию с потребителем отправ |
|||||
|
лять |
документацию |
почтой. |
|||
|
Оборудование, |
сборочные |
||||
|
единицы и детали крепи дол |
|||||
|
жны храниться |
в упаковоч |
||||
|
ном виде или |
(неупакован |
||||
|
ные) |
на деревянных |
брусь |
|||
|
ях |
в |
следующих условиях |
|||
Рис. 12.1. Транспортное положение секции |
хранения по ГОСТ 9.014—78; |
|||||
крепи |
|
сборочные |
единицы гид |
|||
|
рооборудования, |
в |
состав |
которых входят резинотехнические изделия и детали из пластмасс — в легких условиях (Л);
остальные сборочные единицы — в жестких условиях (Ж). Срок хранения до переконсервапии не более одного года. Транспортирование допускается любым видом транспорта. При
транспортировании обеспечиваются исправность и сохранность груза. На каждом грузовом месте должна быть маркировка с ука занием номера места, числа мест и заводского номера крепи.
Выполнение ремонта оформляется записью в разделе «Сведе ния о капитальном ремонте изделия» формуляра, поставляемого с крепью. При изменении конструкции составных частей крепи сведе ния об этом также записываются в разделе формуляра «Сведения об изменениях конструкции изделия и его составных частей, про изведенных в процессе эксплуатации и ремонта».
После окончания ремонта ремонтное предприятие производит запись о гарантийном сроке работы изделия в соответствии с дей ствующими в отрасли директивными документами в разделе фор муляра «Гарантии ремонтного предприятия горно-шахтного обо
рудования».
1. Комплексная механизация и автоматизация очистных работ в угольных шахтах. Под общей ред. Б. Ф. Братченко. М., Недра, И977.
2. |
Угледобывающий |
комплекс КМ87ДН / Я. С. Брук, В. И. Парамонов, |
A. В. |
Керов и др. М., |
Недра, 1975. |
3. Очистные механизированные комплексы О К П /Д . М. Орехов, Г. Г. Буров,
B.В. Вельтищев и др. М., Недра, 1981.
4.Гидрофицированная крепь очистных работ/В . Н, Хорин, Н. П. Бушуев,
C.М. Мамонтов, А. С. Архангельский. М., Недра, 1973.
5.Гидравлические системы механизированных крепей / В. Н. Хорин, С. В. Ма монтов, В. Я- Каштанова и др. М., Недра, 1971.
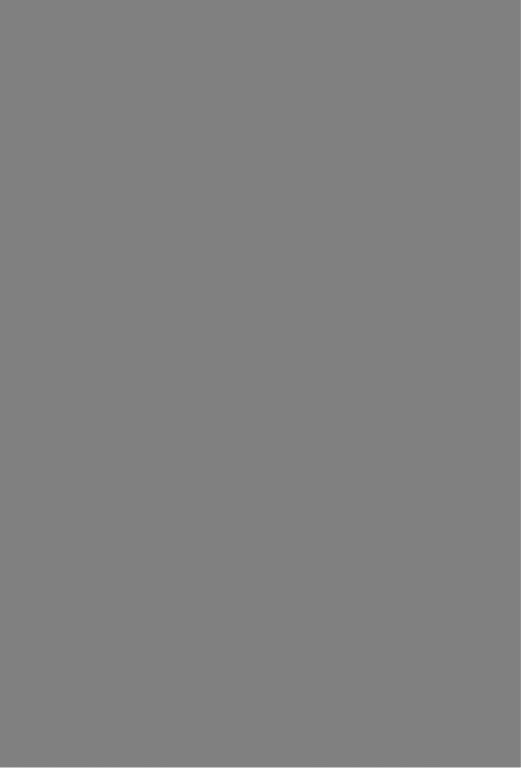
9.3. Хранение и подготовка к спуску в шахту |
|
88 |
|||||||||
9.4. Подготовка |
места монтажа |
комплекса . |
|
|
90 |
||||||
9.5. Спуск и доставка элементов |
комплекса |
|
|
92 |
|||||||
9.6. Монтаж комплекса |
. . . . |
|
|
93 |
|||||||
9.7. Подготовка и опробование комплекса |
|
|
96 |
||||||||
Г л а в а |
10. |
Эксплуатация |
комплексов |
|
|
|
101 |
||||
10.1. Порядок |
управления |
комплексом |
|
|
102 |
||||||
10.2. Особые |
виды |
работ |
|
|
|
|
|
105 |
|||
10.3. Окончание |
работ |
. |
. . . . |
. |
|
106 |
|||||
10.4. Демонтаж |
комплекса |
|
106 |
||||||||
10.5. Меры безопасности |
при |
эксплуатации |
комплекса |
|
109 |
||||||
Г л а в а |
11. |
Техническое |
обслуживание |
и текущий |
ремонт |
|
113 |
||||
11.1. Техническое обслуживание |
. . . |
|
113 |
||||||||
11.2. Текущий |
ремонт комплекса |
|
129 |
||||||||
11.3. Неполадки машин и механизмов комплекса и способы их устра |
146 |
||||||||||
нения |
|
|
|
|
|
|
|
ь |
|
||
Г л а в а |
12. |
Капитальный |
ремонт |
|
|
|
|
156 |
|||
12.1. |
Организация |
р е м о н т а ................................................................... |
156 |
||||||||
12.2. Разборка изделия, подготовка к дефектации,дефектация |
157 |
||||||||||
12.3. Ремонт деталей и неразъемных составных частей |
^ |
160 |
|||||||||
12.4. Прием сборочных единиц после ремонта |
. |
162 |
|||||||||
12.5. Маркировка, упаковка, транспортирование ихранение |
|
164 |
|||||||||
Список |
литературы |
|
|
|
|
|
|
|
|
166 |