
книги / Нанотехнологии и специальные материалы
..pdfК преимуществам ГИП относятся получение заготовок с большим отношением длины к диаметру, а также изделий с рав номерной плотностью по всему объему и с малыми внутренними напряжениями.
6.5.4. ПРЕССОВАНИЕ ЗАГОТОВОК И ИЗДЕЛИЙ БОЛЬШОЙ ДЛИНЫ
Рассмотренные выше методы прессования основываются на дискретной подаче порошка в зону деформации, что позволяет получать заготовки и изделия относительно небольшой длины. При производстве длинных изделий (труб, прутков, лент и т. п.) прессование производят при непрерывной подаче порошка в очаг деформации. К таким процессам относятся экструзионное прес сование порошков и прокатка металлических порошков.
Экструзионное прессование. Это метод формообразования длинных изделий постоянной толщины или диаметра путем не прерывного прессования порошковой смеси в открытых прессформах. Сущность метода состоит в том, что подготовленная для прессования смесь, содержащая до 10 % пластификатора, непре рывно проталкивается под большим давлением через конус и матрицу прессформы (рис. 6.2), где за счет трения о стенки ко нуса и матрицы происходит обжатие и уплотнение порошка.
Достоинством экструзионного прессования является возмож ность получения изделий большой длины с равномерной плотно стью не только из пластичных и хорошо прессующихся порош ков, но и из порошков твердых и тутоплавких металлов, интер металлических соединений, а также из материалов на основе оксидов металлов.
Методом экструзионного прессования из готавливают трубы, стержни, ленты, тавры и т. п.
Прокатка. Прокатка порошков, схема ко торой изображена на рис. 6.3, по-сравнению с обычным прессованием имеет ряд преиму ществ: она позволяет получать однородные по плотности изделия любых размеров по длине и ширине при очень малой толщине. При прокатке для получения изделий боль шой площади не требуется мощного прессо вого оборудования (как это имеет место при
Рис. 6.2. Схема экструзионного прессования:
/ —плунжер пресса; 2 —пуансон; 3 —стальная гильза; 4 —конус; 5 — матрица; 6 — спрессованная заготовка; 7 —порошок
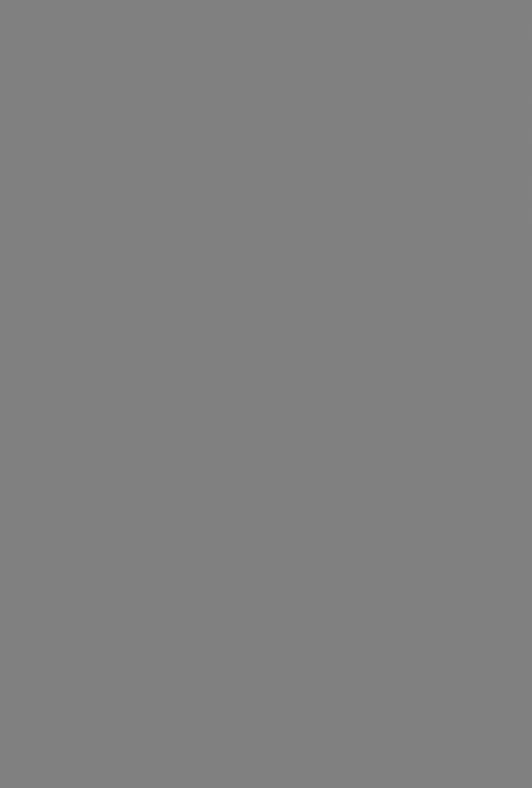
нах частиц и на ’’свободных, активных” поверхностях пора —ме талл. При этом кинетика и механизм спекания зависят от геомет рии частиц, их структурного состояния и характеризуются боль шой скоростью изменения формы частиц от неправильной к рав ноосной, что сопровождается большой скоростью усадки.
На втором этапе спекания поры могут рассматриваться как совокупность непзомерных включений пустот, следовательно, уменьшение объема каждой поры на этом этапе может происхо дить независимо, и пористая матрица в процессе спекания ведет себя как вязкая среда.
Последний этап характеризуется ’’залечиванием” дефектов. При этом ’’залечивание” отдельной поры осуществляется путем ее диффузионного растворения в матрице, а между порами проис ходит диффузионное взаимодействие, которое приводит к коалесценции пор. Уменьшение поверхности пор в этом случае про исходит при неизменном их суммарном объеме.
Влияние среды спекания на структуру и свойства спечен ных изделий. Отличительной особенностью порошковых мате риалов является их высокая активность. В связи с тем что час тицы порошков всегда покрыты пленкой оксидов, а при спека нии их окислительная способность повышается, каждый процесс тепловой обработки порошковых изделий должен производиться в восстановительных или нейтральных средах. Выбор среды спекания определяется природой металла, режимом спекания (температурой и временем), назначением изделий. Если при спе кании компоненты порошковой смеси не склонны к окислению при высоких температурах (порошки благородных металлов), или частицы порошков покрыты устойчивой к окислению ок сидной пленкой (порошки алюминия), или, наконец, сами по рошки представляют собой оксиды, устойчивые при данных тем пературах спекания (порошки ферритов, силицидов и т. и.), то спекание может проводиться без применения специальных за щитных сред в обычной воздушной атмосфере. Во всех остать ных случаях спекание необходимо проводить в контролируемой (защитной) среде.
Наилучшей средой, обеспечивающей высокие свойства спе каемых изделий, является вакуум. При спекании в вакууме соз даются благоприятные условия для рафинирования порошковых компонентов (удаления газов, диссоциации оксидов и т. п.), 6о лее полного и быстрого спекания. По сравнению с другими сре дами при спекании в вакууме (особенно после низких давлений прессования) происходит значительное повышение плотности, в результате чего достигаются высокие механические свойства из делия. Однако промышленное использование вакуума связано с
некоторыми трудностями, поэтому спекание в вакууме применя ется тогда, когда газовые или другие защитные среды не обеспе чивают получения необходимых физико-химических или механи ческих свойств изделий.
Практика спекания порошковых материалов. Спекание — одна из наиболее трудоемких технологических операций в по рошковой металлургии. В связи с малой прочностью прессован ных заготовок все подготовительные операции перед спеканием производятся с большой осторожностью во избежание осыпания граней, разрушения тонких перемычек, резких переходов, а так же разрушения всего изделия. Производится спекание в любых печах, обеспечивающих необходимую температуру и среду спека ния. В зависимости от состава и назначения заготовки пересыпа ются слоем порошка прокаленного оксида алюминия, графитовой крупки, кварцевым песком. Применение засыпок не только пре дохраняет от припекания, но и способствует более равномерном}' прогреву изделий, а также защищает от окисления, выгорания углерода и легирующих элементов. Для усиления защитной спо собности часто к ним добавляют активные вещества — геттеры (губку или порошок титана, порошки хрома, феррохрома, фер росилиция и т. п.), которые, окисляясь, предохраняют от окис ления спекаемые изделия.
6.7. МАТЕРИАЛЫ, ПОЛУЧЕННЫЕ МЕТОДАМИ ПОРОШКОВОЙ МЕТАЛЛУРГИИ
В зависимости от плотности и назначения порошковые мате риалы подразделяются на две группы. К первой относятся плот ные материалы, обладающие минимальной пористостью, изготов ленные на базе порошков железа, меди, никеля, гитана, алюми ния и их сплавов. Ко второй — пористые материалы, в которых после окончательной обработки сохраняется свыше 10—15 % пор по объему. Первая группа материалов нашла широкое примене ние в машино- и приборостроении при изготовлении аппаратов низкотемпературной и пищевой промышленности, в автомобиль ной и авиационной технике и других отраслях оборонного и об щегражданского производства. Высокая пористость материалов второй группы обеспечивает приобретение ими специальных свойств и позволяет применять их для изготовления специальных изделий (изделий антифрикционного назначения, фильтров, де талей охлаждения и т. п.). При производстве этой группы дета лей применяются железографитовые материалы, бронзы, нержа веющие стали.
Особое значение имеют инструментальные порошковые мате риалы. К их числу относятся порошковые быстрорежущие стали, карбндостали, твердые сплавы, материалы на основе сверхтвер дых соединений (нитридов, борндов и т. д.) и алмазные мате риалы.
6.7.1. КОНСТРУКЦИОННЫЕ МАТЕРИАЛЫ
Конструкционные порошковые материалы на основе ж елеза.
Все материалы на основе железа делятся на:
—стали малоуглеродистые, углеродистые и медистые; —стали никельмолибденовые, медноникелевые, медноникель-
молибденовые; —стали хромистые, марганцовистые, хромоникельмарганцо-
вистые; —стали коррозионностойкие.
Конструкционные порошковые стали — это спеченные мате риалы, используемые для замены литых и кованых сталей при изготовлении деталей машин и приборов методами порошковой металлургии. Условное обозначение таких материалов состоит из букв и цифр, например: сталь порошковая конструкционная мед ноникелевая со средней массовой долей углерода 0,4 °/ никеля 2 %, меди 2 % и минимальной плотностью 6,4 г/см3 в соответ ствии с ГОСТ 28378—89 будет иметь следующее обозначение: ПК40Н2Д2-64.
Буквы в марке стали указывают: П —на принадлежность ма териала к порошковому, К — на назначение материала (конст рукционный), остальные буквы и цифры — на содержание тех или иных легирующих элементов (Д — медь, X — хром, Ф — фосфор, К —сера, М —молибден, Г —марганец, Т —титан, Н — никель). Основу материала — железо — в обозначении марок не указывают. Цифры, стоящие за буквами Г1К, указывают на сред нюю массовую долю углерода в сотых долях процента. Массовую долю углерода, равную 1 %, в обозначении марки материала также не указывают. Цифры, стоящие за остальными буквами, означают содержание легирующих элементов в процентах; отсут ствие цифры указывает на то, что массовая доля легирующего элемента не превышает одного процента.
Основой порошковых сталей служит железо, свойства кото рого при спекании оказывают большое влияние на формирование структуры и свойств стали. Наряду с порошковыми сталями по рошковые изделия могут изготавливаться на основе одного же лезного порошка, а также железа, легированного другими эле ментами.
Применение в качестве исходного материала чистого железно го порошка при изготовлении конструкционных деталей ограни чено из-за низких прочностных свойств спеченного железа. В ос новном оно применяется для изготовления ненагруженных дета лен, различных уплотнительных изделии и т. п. Свойства таких изделий зависят от их плотности, величины и характера межчас тичных границ, метода получения порошка, гранулометрическо го состава, удельной поверхности частиц, внутренней их рых лости, технологии прессования (величины давления и скорости прессования), кратности прессования, температуры и времени спекания.
Для получения практически беспористых изделий с повышен ными механическими свойствами применяют горячее изостатическое прессование — экструзию, динамическое горячее прес сование.
В связи с низкой прочностью и твердостью спеченного железа для повышения его механических свойств в железный порошок при приготовлении порошковой смеси вводят легирующие добав ки (фосфор, медь, хром, никель, молибден), а спеченные изделия подвергают химико-термической обработке: азотированию, суль фидированию, хромированию.
Широкое применение нашли железоникелевые и железоникельмедные сплавы. Присадка к чистому железу 5 % никеля по вышает прочность и твердость материала, оставляя его пластич ность практически без изменений. При одновременном легирова нии никелем и медью (Ni — 4 % и Си — 2 %) прочность на разрыв образцов с пористостью 10 % достигает 400—420 МПа, удлинение 7—8 %, твердость 120—127 НВ.
Для повышения прочности и твердости спеченных железных изделий основная масса порошковых материалов на базе железа дополнительно легируется углеродом, под действием которого спеченное железо приобретает способность закаливаться и во много раз повышать свою твердость и прочность. В железный порошок углерод вводят в виде графита, сажи или чугунного по рошка.
Основные марки порошковых конструкционных сталей при ведены в табл. 6.5.
Стали порошковые высокопрочные конструкционного на значения. Методы порошковой металлургии позволяют получать высокопрочные мартеиситностареющие стали, не уступающие по прочности полученным традиционными методами. Введением в них повышенного содержания титана —до 2—3 % (мае.) можно увеличить их прочность до 2000 МПа при относительном уд лпнении 2—3 %. Все мартеиситностареющие порошковые стали
Химический состав (% мае.) конструкционных материалов на основе железа по ГОСТ 28378—89
Марка |
С |
Си |
|
Ni |
Mo |
Cr |
Другие |
|
плементьг |
||||||
|
|
|
|
|
|
|
|
Стали малоуглеродистые, углеродистые, медистые |
|||||||
п к ю |
<0,10 |
— |
|
— |
— |
— |
— |
ПК40 |
0,31-0,60 |
— |
|
— |
— |
— |
— |
Г1К70 |
0,61-0,90 |
— |
|
— |
— |
— |
— |
ПКЮФ |
<0,30 |
— |
|
— |
— |
— |
Р: 0,8 -1 ,2 |
|
|
|
|
||||
ПКЮДЗК |
<0,30 |
1 -4 |
|
— |
— |
— |
/VI: 0,15-0,40 |
ПКЮД5 |
<0,30 |
4 -6 |
|
— |
— |
— |
— |
ПК40ДЗ |
0,31-0,60 1 -4 |
|
— |
— |
— |
— |
|
ПК40ДЗК |
0,31-0,60 1-1,3 |
|
— |
— |
- |
Si: 0,15-0,40 |
|
Стали никельмолибденовые, медноникелевые, медноникельмолибденовые |
|||||||
ПКЮН2М |
<0,30 |
— |
1 -3 |
0 сос1 V i |
— |
— |
|
Г1КЮН2Д2 |
<0,30 |
1 -3 |
1 -3 |
— |
— |
— |
|
ПКЮН4Д4 |
<0,30 |
2 -6 |
2 -6 |
— |
— |
— |
|
11КЮН2Д6М |
<0,30 |
4 -8 |
1 -3 |
0,3 -0,7 |
— |
— |
|
ПК40НЗД2М |
0,31-0,60 1-3 |
1 -3 |
0,3 -0,7 |
— |
— |
||
ПК40Н4Д2М |
0,31-0,60 1 -3 |
3 - 5 |
0,3 -0,7 |
— |
— |
||
ПК70Н2Д2 |
0,61-0,90 1 -3 |
1 -3 |
— |
— |
— |
||
Стали хромистые, марганцовистые , хромникельмарганцовистые |
|||||||
ПК70ХЗ |
0,61-0,90 |
— |
1,0-3,0 2,0-4,0 |
|
Мп: 1,0-3,0 |
||
ПКХ6 |
0,91-1,20 |
|
|
|
5,0-7,0 |
|
Мп: 0,5—1,5 |
ПК40Х2 |
0,31-0,60 |
|
|
|
1,0-3,0 |
|
Мп: 12,0-14,0 |
ЛК40Г2 |
0,31-0,60 |
|
|
|
0,5-1,5 |
|
— |
|
|
Стали нержавеющие |
|
|
|||
Г1КЮХ13М2 |
<0,10 |
— |
1,0-3,0 |
1,0-3,0 |
12,0-14,0 |
Ti: 0 ,5 -0 ,8 |
|
ПК20Х13 |
0,10-0,30 |
|
оо о |
р о |
1,0 -3,0 |
12,0-14,0 |
|
11К40Х13М2 |
0,30-0,50 |
|
14,0-16,0 |
|
12.0-14,0 |
|
|
ПКЮХ17Н2 |
<0,15 |
|
|
|
|
16,8-18,0 |
|
ПКЮХ18Н9Т |
<0,10 |
|
|
|
|
17,0-19,0 |
|
ПКЮХ18Н15 |
<0,10 |
|
|
|
|
17,0-19,0 |
|
характеризуются низким содержанием кремния и марганца (в сумме ие более 0,2 %, причем допустимое содержание каждого не должно превышать 0,12 %), низким содержанием серы и фосфо ра (не более 0,01 % каждого). Составы наиболее широко приме няемых порошковых мартенситностареюшнх сталей приведены в табл. 6.6.
Получают высокопрочные мартенситностареющие стали спе канием при температуре 1200—1300 °С в течение 3—4 ч. Дальней шее повышение механических свойств может достигаться путем
Состав наиболее распространенных мартенситностареющих порошковых сталей
Марка стали |
|
Химический состав, %(мае.) |
|
||||
Ni |
Со |
|
другие элементы |
||||
|
|
||||||
СПН10ТЮ |
9,5—10,5 |
_ |
Al: 0,6 |
-0,9; |
Tî: 0,8-2,1 |
|
|
СПН1Ш5ТЮ |
10,5-11,5 |
4,8-5,1 |
Mo: 4,5 |
-5,1; |
Ti: 0,8-1,1: AI: 0 ,6 -0 ,9 |
||
СПН12К5М5Г4ТЮ |
11,5-12,5 |
4,8-5,1 |
Mo: 4,5 |
-5,1; AI: 0,6-0,9; Ti: 0,8-1,1; |
|||
|
1 |
|
Mn: 3,4-4,5 |
|
|
|
|
СПН12Х5МЗТ |
1,5—12,5 |
15,5—16,5 Mo: 2,8-3,1; |
Ti: 0,8 |
-1,1; |
Cr: 4,5-5,5; |
||
|
12,5-13,5 |
6,7-7.5 |
Mn: 9,5-10,5 |
|
|
|
|
СПН13К16МЮ |
Mo: 4,8-5,1; |
Ti: 0,8 |
-1,1 |
|
|||
СПН14К7М5Т |
13,5-14,5 |
4,8-5,1 |
Mo: 4,8-5,1; |
Ti: 2,5-3,5 |
|
||
СПН14К7М5ТЗ |
13,5-14,5 |
4.8-5,1 |
Mo: 4,8-5,1; Ti: 0,8-1,1; Mn: 1,2-2,1 |
||||
СПН14К5М5Г2Т |
13,5-14,5 |
4,8-5,1 |
Mo: 4,8 |
-5,1; |
Ti: 0,8 |
-1,1 |
|
СПН17К5М5Т |
16,5-17,5 |
5,5—6,5 |
Mo: 4,8-5,1; |
Ti: 0,8-1,1; |
Al: 0 ,6 -0 ,9 |
холодной пластической деформации (степень деформации 80— 90 %) с последующим старением при 400—500 °С, а также сочета нием закалки, пластической деформации и старения.
Среда при спекании, термическая обработка (закалка, ста рение) определяются составом стали. Стали, содержащие ти тан, могут обрабатываться только в очищенном аргоне или ва кууме.
Материалы конструкционные порошковые на основе цвет ных металлов. Из цветных порошковых сплавов наибольшее зна чение имеют полученные на основе меди, алюминия и титана; реже применяют материалы на основе циркония, бериллия, ура на, тория и других металлов.
Цветные порошковые материалы различаются по плотности, составу, структуре и методу производства. Они могут быть ком пактными и пористыми; по химическому составу — идентичны ми литым и такими, производство которых возможно только ме тодами порошковой металлургии. Изделия из этих материалов получают методами холодного статического прессования и спе кания, горячим прессованием или горячей штамповкой. В зави симости от состава и структуры эти материалы обладают высо кой тепло- и электропроводностью, коррозионной стойкостью, могут быть немагнитными, хорошо обрабатываются резанием и давлением. Марки и химический состав конструкционных по рошковых материалов на основе цветных металлов приведены в табл. 6.7
Марки этих материалов обозначаются сочетанием букв и цифр. Первый буквенный индекс указывает на класс материала: Ал —алюминий, Бе —бериллий, В —вольфрам, Г —марганец,
Д—медь, Ж —железо, Л —латунь, М —молибден, Н —никель,
О— олово, П —фосфор, С — кремний, Св — свинец, Ср — се ребро, Т —титан, Ф —ванадий, X —хром, Ц —цинк, Цр —цир коний. Второй буквенный индекс (П) означает, что материал по лучен методом порошковой металлургии. Следующие после этого индексы-буквы соответствуют легирующим компонентам, а циф ры после них — среднему содержанию компонента в процентах. Отсутствие цифр означает, что содержание компонента составля ет не более 1 %. Число после дефиса —плотность материала.
ТАБЛИЦА 6.7
Марки и составы основных конструкционных порошковых материалов на основе цветных металлов
|
|
|
Химический состав, % (мае.) |
|
||
материала |
А1 |
Си |
Mg |
Мп |
Zn |
другие элементы |
|
||||||
АлП |
Основа |
_ . |
_ |
_ |
_ |
_ |
АлПД2-12 |
Основа |
1,5-2,5 |
0,3-0,6 |
0,3-0,7 |
— |
— |
АлПЖ2-12 |
Основа |
— |
— |
0,3-0,7 |
|
Fe: 9,8-12,8 |
АлПМгб |
Основа |
— |
5,8-6,8 |
— |
— |
— |
БеП |
— |
— |
— |
0,5-0,8 |
— |
Be —основа |
БрШО |
— |
Основа |
— |
— |
— |
Sn: 9,5—10,5 |
БрПОЮЦЗ |
— |
Основа |
— |
— |
2,8-3,2 |
— |
ВП |
— |
— |
— |
— |
— |
W —основа |
д п |
— |
Основа |
— |
— |
— |
— |
ЛП58Г2 |
— |
Основа |
— |
— |
39-41 |
— |
ЛП59 |
— |
Основа |
— |
1,0-2,0 40-42 |
— |
|
ЛП59Св |
— |
Основа |
— |
— |
40-42 |
Pb: 0,8 -1,8 |
ЛП62 |
— |
Основа |
— |
— |
37-39 |
— |
ЛП65Н5 |
— |
Основа |
— |
— |
29-31 |
Ni: 5,0-6,5 |
ЛП68 |
— |
Основа |
— |
— |
31-33 |
— |
ЛП80 |
— |
Основа |
— |
— |
19-21 |
— |
ЛП90 |
— |
Основа |
— |
— |
9-11 |
— |
МП |
— |
— |
— |
— |
— |
Mo —основа |
МгП |
— |
— |
Основа |
— |
— |
— |
МгПАл5 |
4,5-5,5 |
— |
Основа |
— |
— |
— |
НП |
— |
— |
— |
— |
— |
Ni - основа |
СрП |
— |
— |
— |
— |
— |
Ag —основа |
тп |
— |
— |
— |
— |
— |
Ti —основа |
ТПАл2М |
1,8-2,2 |
— |
— |
— |
— |
Mo: 0,5 -0,8 |
ТПАл4 |
3,8-4,4 |
— |
— |
— |
— |
— |
Изделия из порошковых бронз и латуней нашли широкое применение в электротехнической промышленности в качестве электроконтактных изделий, в узлах трения —антифрикционных изделии.
6.7.2. ФИЛЬТРУЮЩИЕ ПОРИСТЫЕ МАТЕРИАЛЫ
Порошковые проницаемые материалы занимают особое место в общей номенклатуре изделий порошковой металлургии. Они применяются для фильтрации газов и жидкостей при низких и повышенных температурах, в устройствах для капиллярного транс порта жидкостей —тепловых трубах, при испарительном охлаж дении, в гидравлических уплотнениях затворов, при уплотнении различного рода соединений.
Особенностью этой группы материалов является возможность получения строго заданной регулируемой пористости, так как ее величина, размеры и форма пор, их распределение определяют эффективность использования изделий из таких материалов.
В зависимости от области применения пористые материалы могут быть разделены на четыре основные группы:
1) высокопористые декоративные, используемые для изготов ления медалей, монет, бижутерии, прокладок, шайб, уплотнений
итермоизоляции;
2)газо- и жидкостнопроницаемые, используемые для сепара ции и разделения газов и жидкостей, смешивания и распыления жидкостей, суспензий твердой и жидкой фаз;
3)фильтрующие, способные частично или полностью отфильт ровагь твердые частицы различных размеров в газах и жидко
стях; 4) антифрикционные, способные удерживать жидкость в по
рах.
Форма пор в подобных изделиях может быть самой разнооб разной —от глобулярной равноосной до щелевидной с различны ми соотношениями осей и неправильной с разветвленными края ми. Определение размеров пор и их распределения по объему изделия может производиться как металлографическим способом, так и ртутной порометрией.
Металлонорошковые фильтры лучше задерживают мелкие частицы, не горят, не рвутся, более прочны и эластичны, лучше сопротивляются механическим и термическим ударам, воздейст вию взрывной волны. К числу положительных сторон их исполь зования также относятся простота эксплуатации, возможность бы строй регенерации фильтра. Основные рекомендации по примене нию порошковых фильтрующих материалов даны в табл. 6.8.